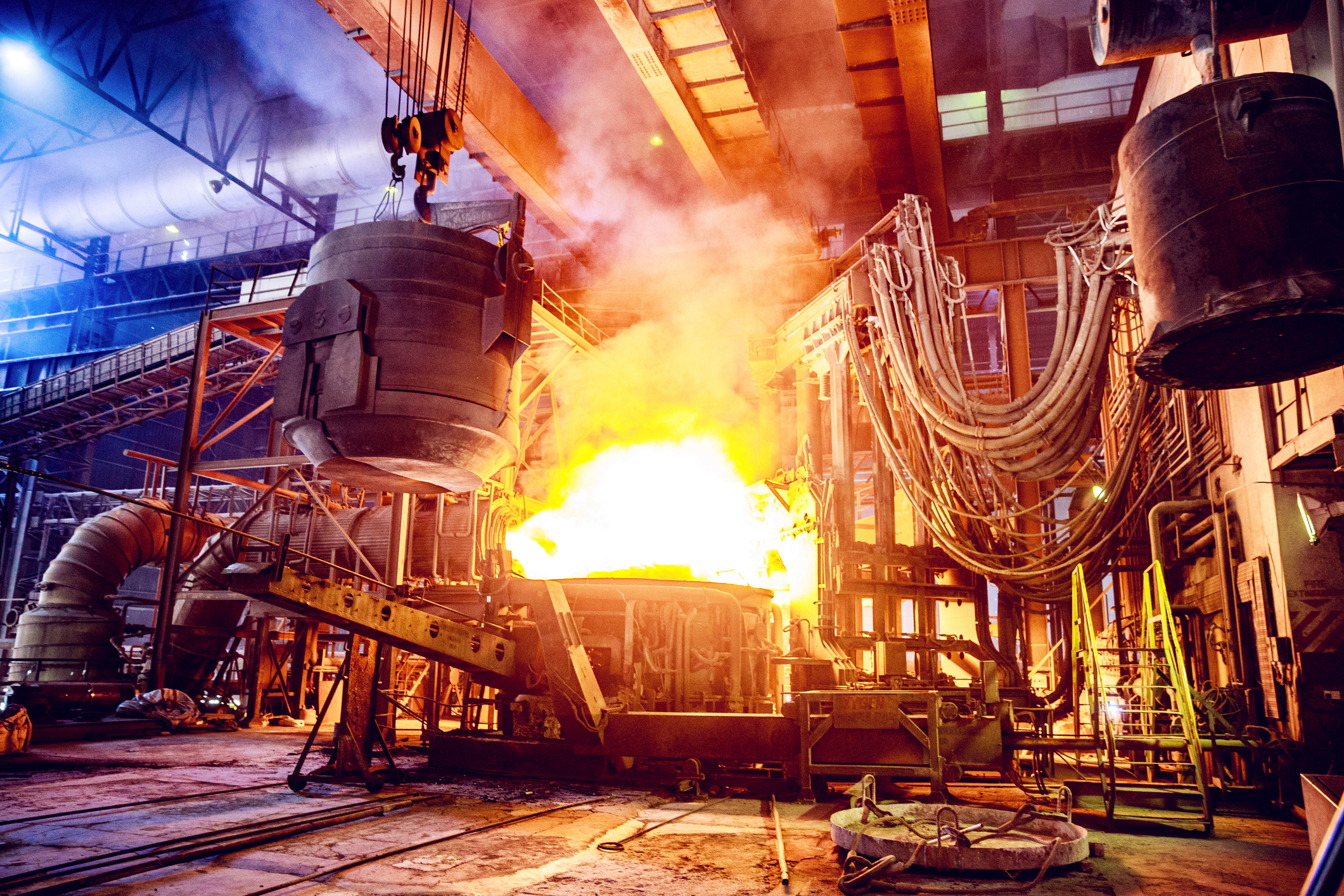
Clean Room Manufacturing and Packaging
Clean room manufacturing and packaging are critical processes used to ensure that O-rings, gaskets, and custom parts made from rubber, plastic, and metal meet the highest standards of cleanliness and quality. These processes are essential for industries where contamination control is paramount, such as semiconductor manufacturing and medical devices. This guide covers the types, features, common applications, and the pros and cons of clean room manufacturing and packaging, with references to USP Class VI materials, parts for semiconductor manufacturing, and parts for medical devices.
Cleanroom manufacturing and packaging available for USP Class VI silicone, CanRez® FFKM and Kalrez® O-rings, gasket rapid manufacturing, & custom molded parts are available now!
Check with one of Canyon’s helpful product engineers for an expert material and manufacturing recommendation.

Features of Clean Room Manufacturing and Packaging
Clean room manufacturing and packaging offer several key features that ensure the highest standards of cleanliness and quality:
- Contamination Control: Clean rooms are designed to minimize the presence of airborne particles, microbes, and other contaminants that could compromise the quality of the parts being produced.
- Strict Environmental Controls: Clean room environments are tightly controlled for temperature, humidity, and air pressure, ensuring consistent conditions that prevent contamination and material degradation.
- Use of USP Class VI Materials: For applications in the medical and pharmaceutical industries, clean room manufacturing often involves the use of USP Class VI materials, which are certified for biocompatibility and safety.
- Advanced Packaging Techniques: Parts produced in clean rooms are packaged using specialized materials and methods to maintain cleanliness during transportation and storage.
Common Applications of Clean Room Manufacturing and Packaging
Clean room manufacturing and packaging are used in industries where maintaining product purity and preventing contamination are critical:
- Semiconductor Manufacturing: O-rings, gaskets, and custom parts used in semiconductor manufacturing must be free of contaminants to ensure the purity of wafers and chips. Clean room manufacturing ensures that these components meet the stringent requirements of the industry.
- Medical Devices: Components used in medical devices, such as seals, gaskets, and custom parts, must be manufactured and packaged in clean rooms to ensure they are free of contaminants and safe for patient use. USP Class VI materials are often used in these applications to meet regulatory standards.
- Pharmaceuticals: Clean room manufacturing is essential for producing components used in pharmaceutical processing and packaging, where contamination could compromise product safety and efficacy.
- Aerospace: In aerospace applications, clean room manufacturing is used to produce components that must meet strict cleanliness standards to ensure the reliability and performance of aircraft and spacecraft systems.
Please consult a Canyon Components Engineer about your specific application and we will use our decades of experience to formulate a solution that fits your need.
Clean Room Manufactured Materials Available
Filter by
Temperature Search (°C)
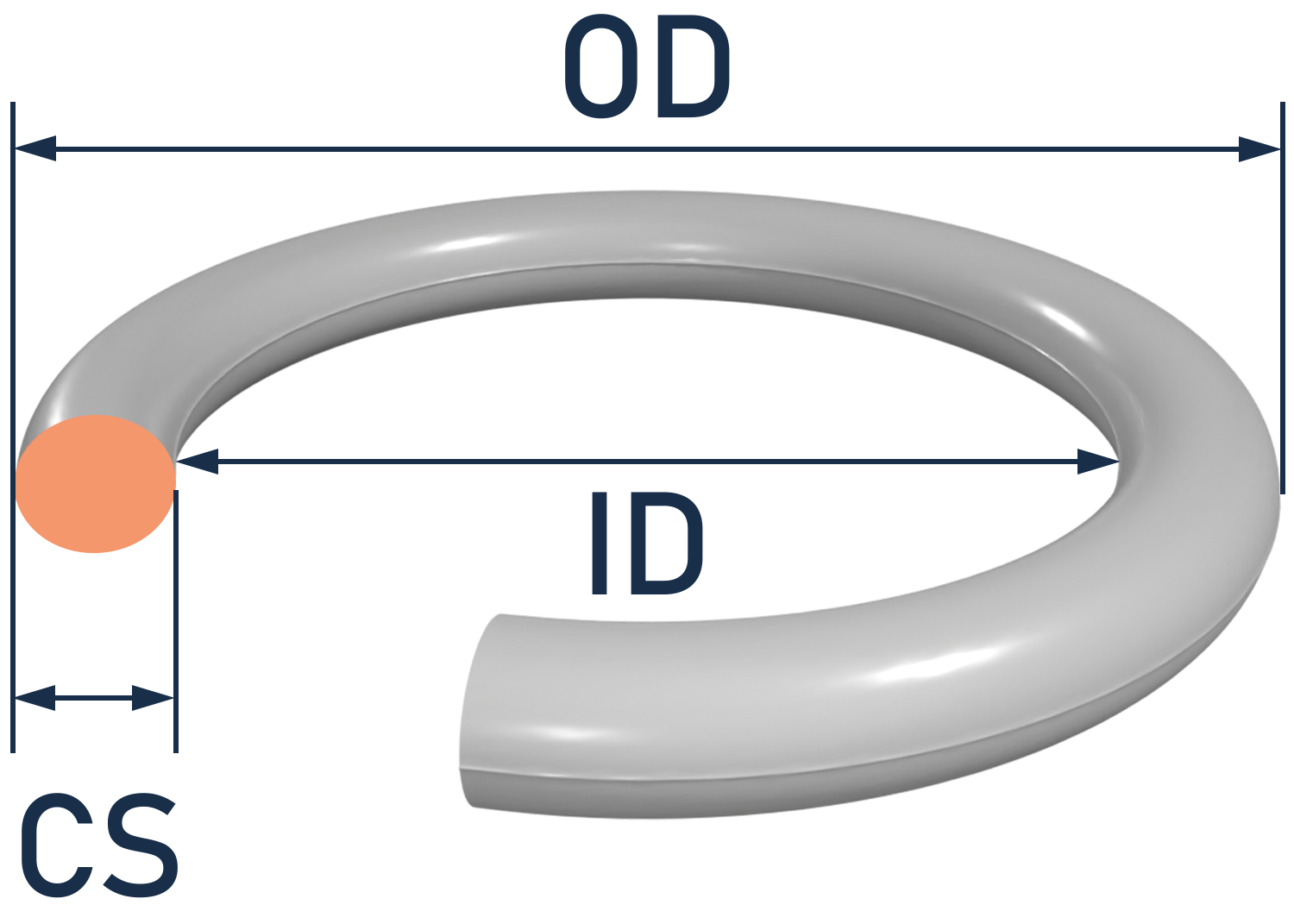
Get a Quote Now!
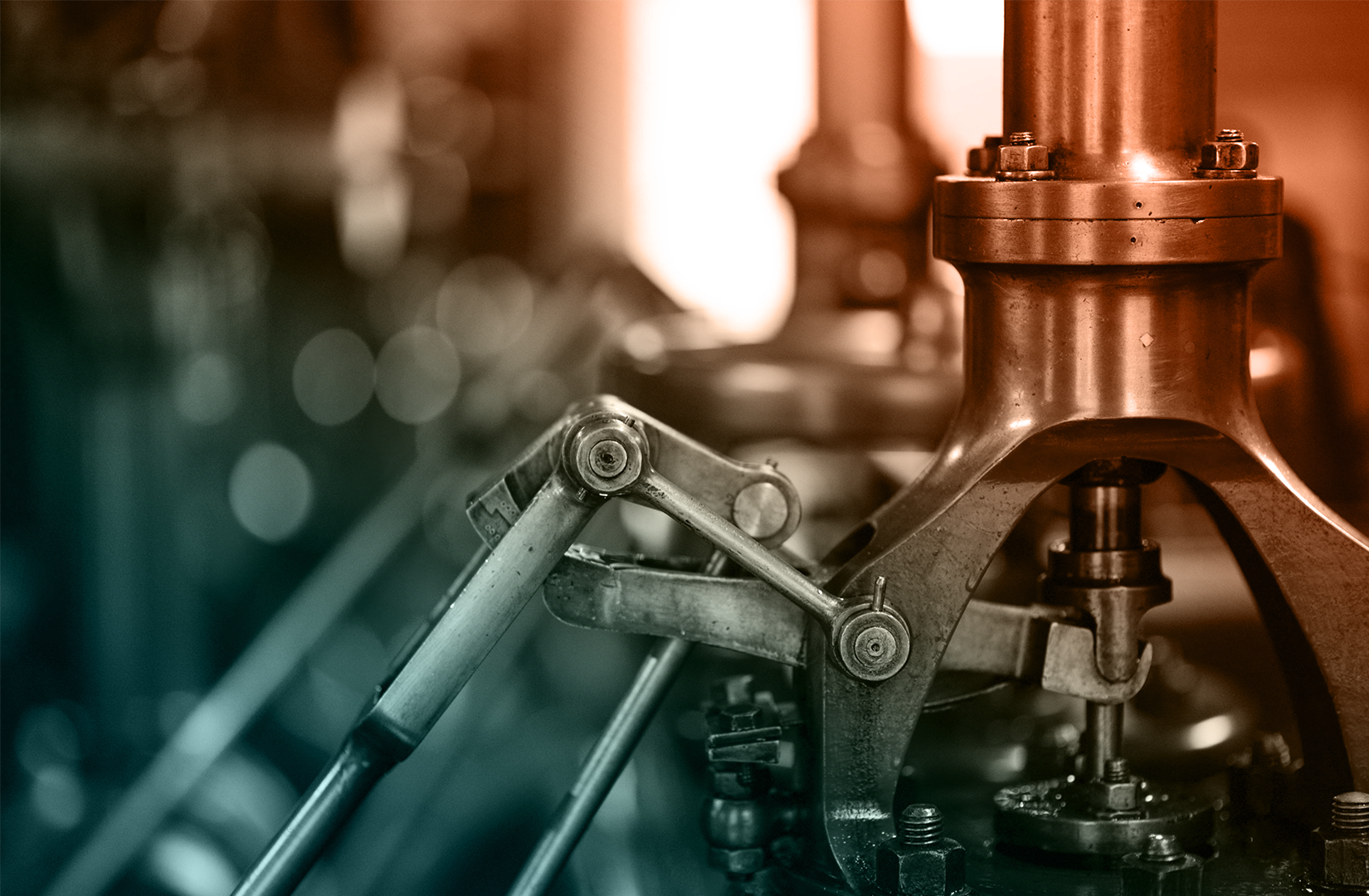
Types of Clean Room Manufacturing and Packaging
Clean room manufacturing and packaging processes are designed to meet specific cleanliness standards and are categorized based on the level of control required:
- ISO Class 5 (Class 100) Clean Rooms: These clean rooms provide the highest level of contamination control, with strict limits on the number of particles per cubic meter of air. They are used for manufacturing and packaging critical components such as medical devices and semiconductor parts.
- ISO Class 7 (Class 10,000) Clean Rooms: These clean rooms offer a lower level of particle control, suitable for less critical applications where a moderate level of cleanliness is required.
- ISO Class 8 (Class 100,000) Clean Rooms: Used for manufacturing and packaging parts that do not require extreme cleanliness but still need protection from airborne contaminants.
Canyon Components strives to meet all customer service requests. Feel free to contact Canyon Components engineering and let our knowledgeable staff help you design the perfect part for your needs.
Clean Room Manufacturing and Packaging Pros & Cons
Clean room manufacturing and packaging are essential processes for producing high-quality, contamination-free components used in critical industries such as semiconductor manufacturing and medical devices. By utilizing advanced environmental controls, USP Class VI materials, and specialized packaging techniques, clean room operations ensure that O-rings, gaskets, and custom parts meet the highest standards of cleanliness and performance. While these processes can be more costly and complex, the benefits of ensuring product purity, regulatory compliance, and enhanced performance make clean room manufacturing and packaging an invaluable service for industries where quality cannot be compromised.
Canyon Components strives to meet all customer service requests. Feel free to contact Canyon Components engineering and let our knowledgeable staff help you design the perfect part for your needs.
Pros of Clean Room Manufacturing and Packaging
Clean room manufacturing and packaging offer several advantages that make them essential for high-purity applications:
- High Product Quality: By controlling the manufacturing environment, clean room processes ensure that parts are produced to the highest quality standards, free from contamination and defects.
- Compliance with Regulatory Standards: Clean room manufacturing is necessary for producing parts that meet industry-specific regulatory standards, such as USP Class VI for medical devices.
- Enhanced Product Performance: Components manufactured in clean rooms are less likely to experience performance issues related to contamination, resulting in greater reliability and longer service life.
- Protection During Transportation: Specialized clean room packaging ensures that parts remain contaminant-free during transportation and storage, preserving their quality until they are ready for use.
Cons of Clean Room Manufacturing and Packaging
While clean room manufacturing and packaging offer many benefits, there are also some potential drawbacks to consider:
- Higher Costs: The stringent controls and specialized equipment required for clean room manufacturing can lead to higher production costs compared to standard manufacturing processes.
- Complexity: Clean room operations require strict adherence to protocols and procedures, which can increase the complexity of the manufacturing process and require specialized training for personnel.
- Limited Production Capacity: Due to the controlled environment and the need to minimize contamination, clean room manufacturing may have lower production capacity compared to traditional manufacturing methods.
- Longer Lead Times: The additional steps involved in clean room manufacturing and packaging, including stringent quality control and testing, can lead to longer lead times for product delivery.
Back to Products Hub
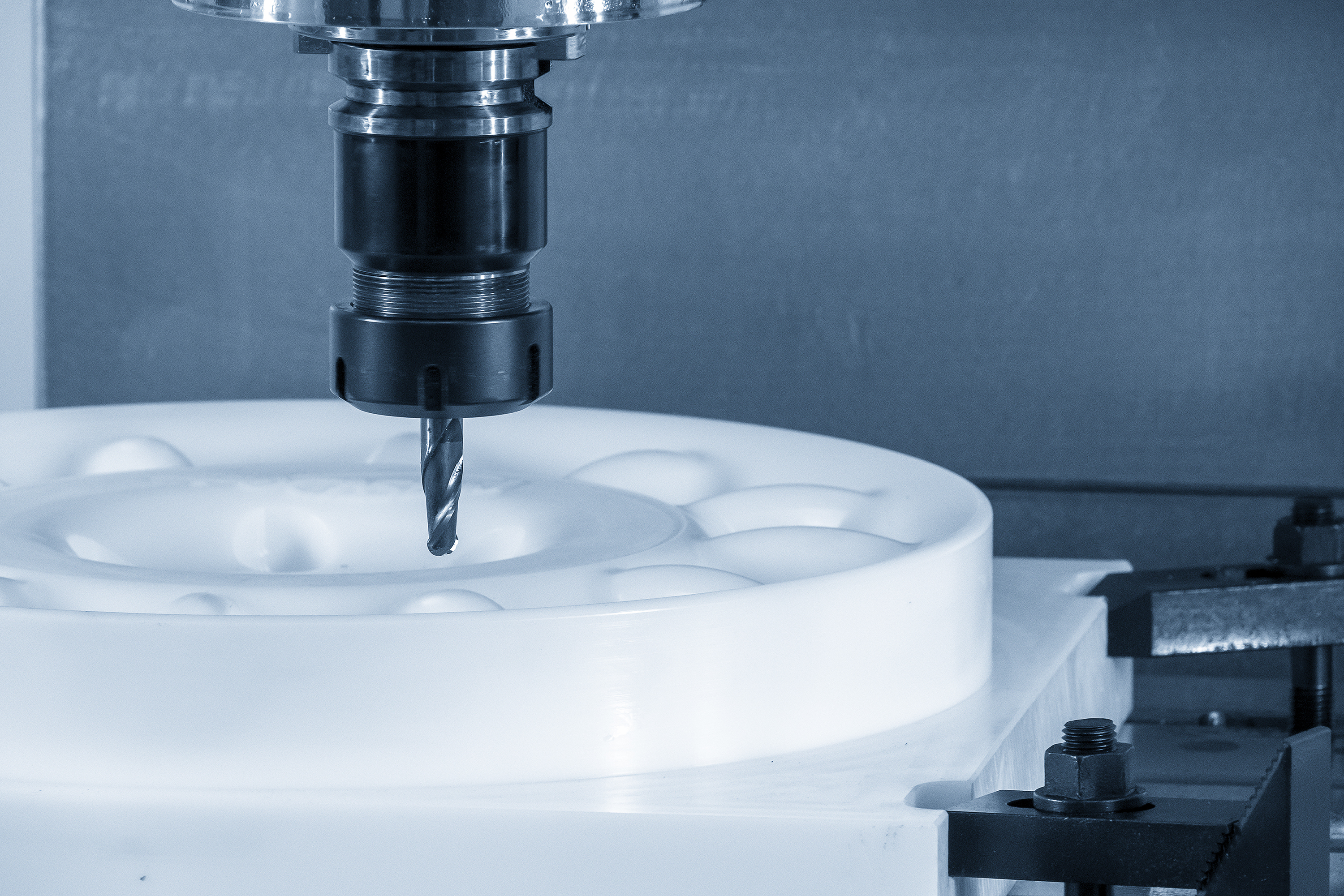
Get A Quote Now!
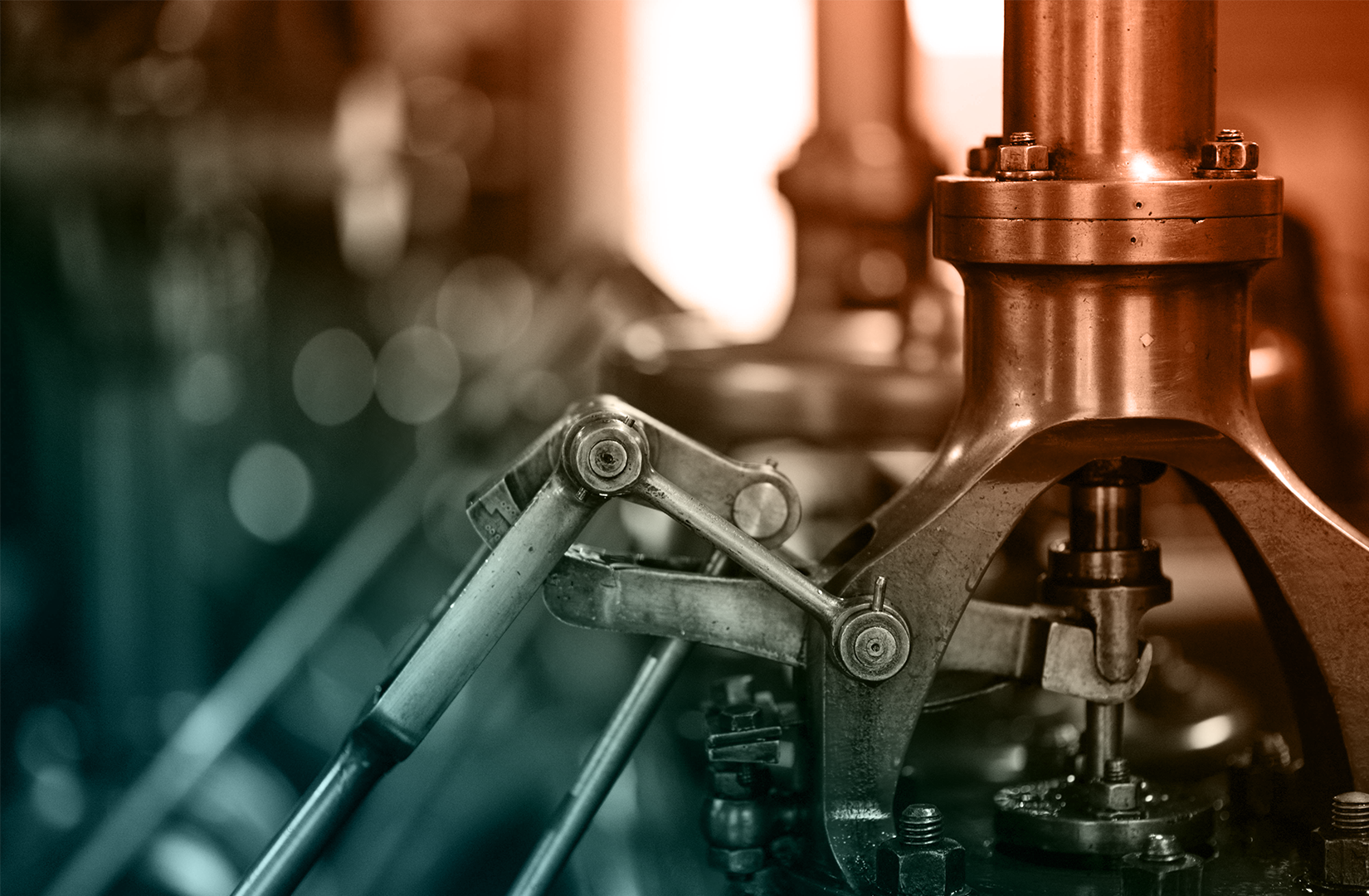