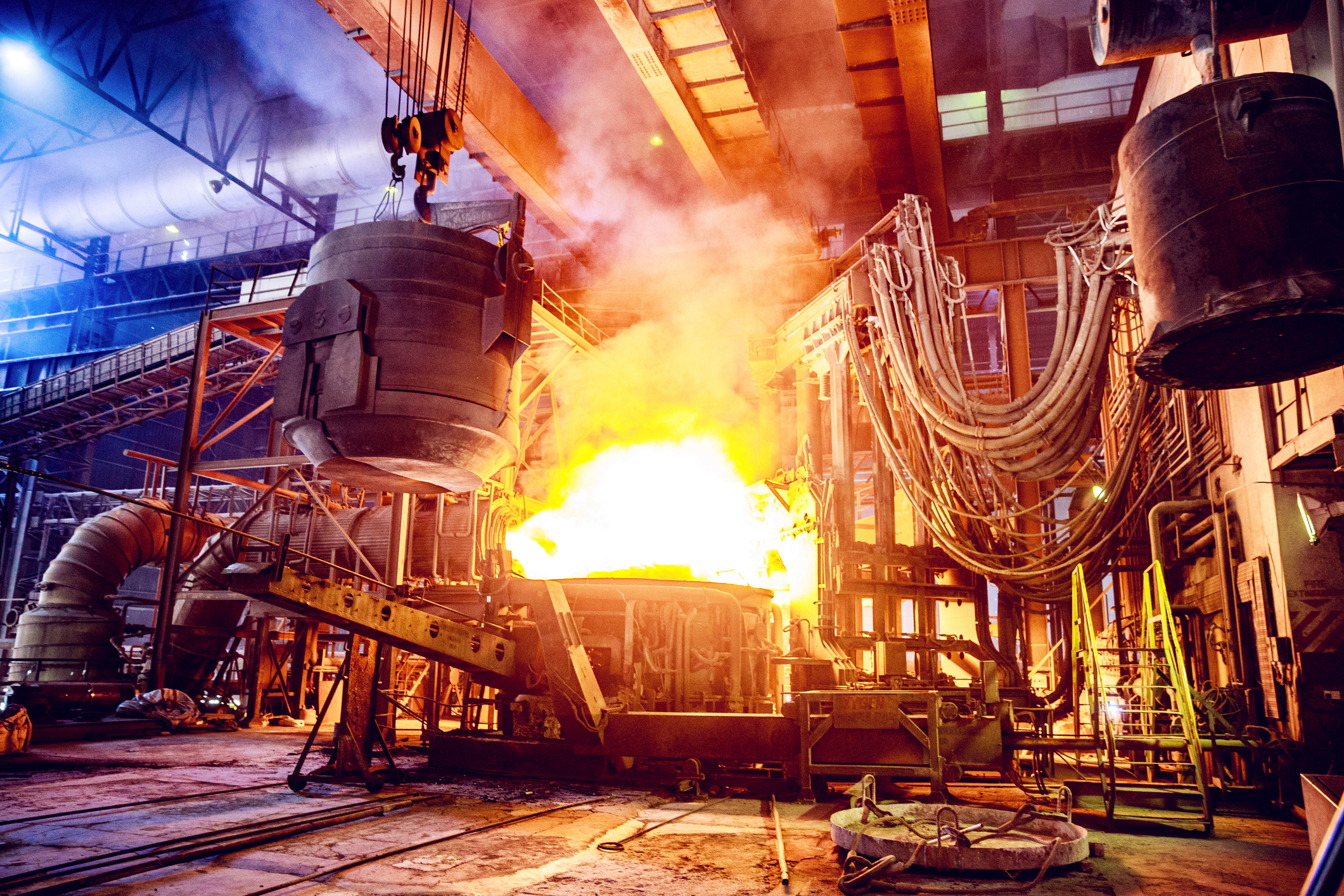
Deflashing Services for O-Rings and Custom Molded Parts
Deflashing is an essential finishing process for O-rings and custom molded parts, removing excess material (flash) created during molding. Flash can affect seal integrity, appearance, and the overall functionality of a part, especially in precision applications. Deflashing ensures clean, smooth edges and surfaces, making parts ready for use across a wide range of industries. This page covers the different deflashing methods available, key features, common applications, and the pros and cons of each technique, including cryogenic deflashing.
Deflashing services available for silicone, CanRez® FFKM and Kalrez® O-rings, gasket rapid manufacturing, & custom molded parts are available now!
Check with one of Canyon’s helpful product engineers for an expert material and manufacturing recommendation.
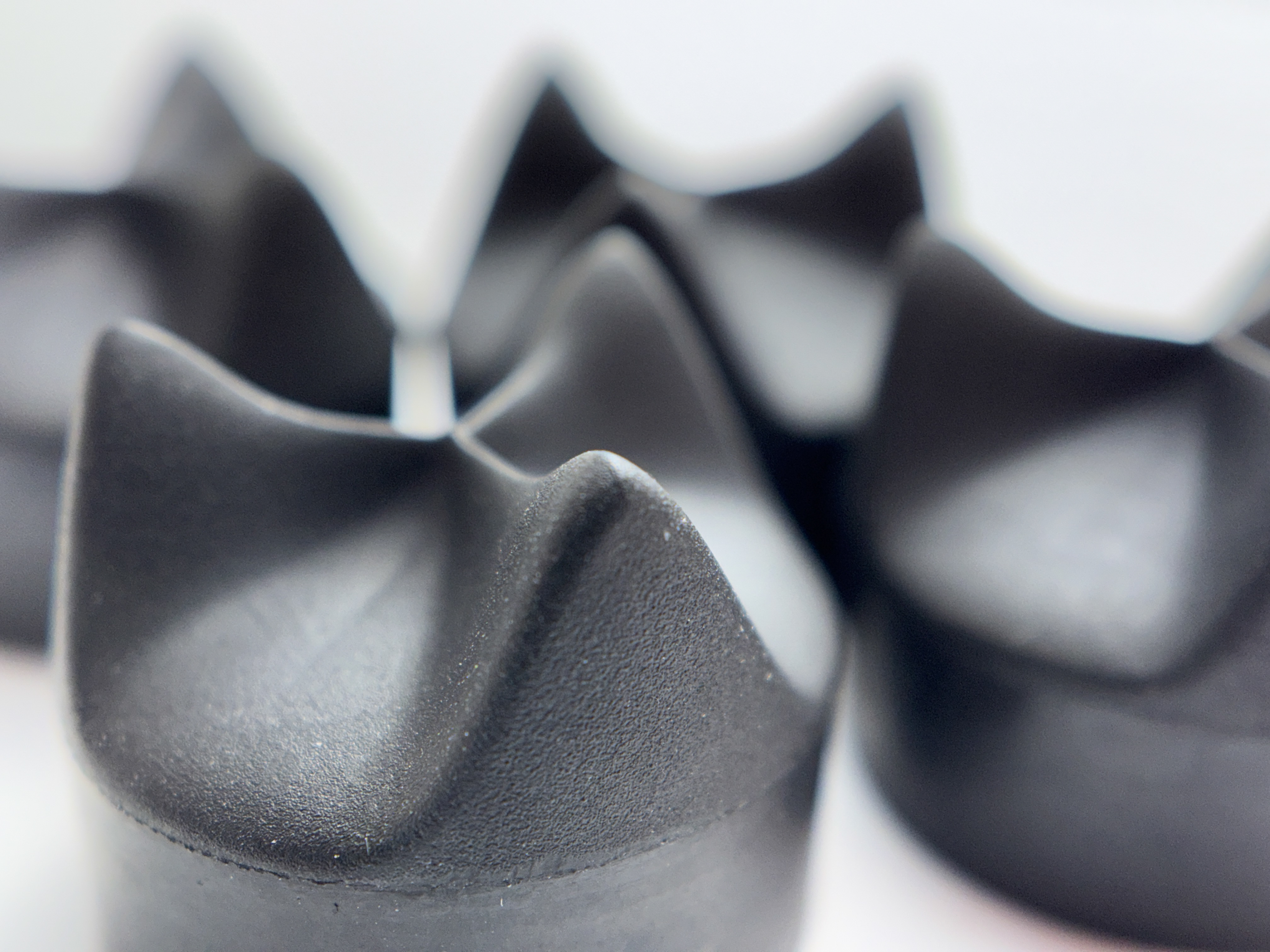
Types of Deflashing Services
- Cryogenic Deflashing: This process involves freezing parts to make flash brittle, then tumbling or blasting them with fine media to break off excess material. Cryogenic deflashing is highly precise, especially for intricate parts with tight tolerances, such as O-rings and complex molded components.
- Mechanical Deflashing: Mechanical deflashing uses abrasive materials, brushing, or tumbling to remove flash. While effective for general applications, mechanical deflashing may lack the precision needed for intricate parts and can lead to uneven results on smaller components.
- Hand Trimming: This method uses manual tools to trim flash from parts, often used for complex parts or prototypes where other deflashing methods might be impractical. Although highly controlled, hand trimming is labor-intensive and not ideal for high-volume production.
- Chemical Deflashing: Chemical deflashing involves submerging parts in a chemical bath to dissolve or soften flash for removal. Suitable for specific materials, it requires strict handling and disposal processes, often making it less practical than other methods.
Features of Deflashing Services
- Precision Finishing: Deflashing ensures smooth, uniform edges and surfaces, which are crucial for the performance of sealing components like O-rings.
- Versatile for Complex Geometries: Advanced deflashing methods, such as cryogenic deflashing, accommodate intricate designs and hard-to-reach areas, achieving consistent results on custom molded parts.
- Material-Specific Adaptability: Deflashing processes can be adapted for different elastomers, plastics, and rubber compounds to ensure material integrity is maintained.
- Efficiency for High-Volume Production: Automated deflashing methods, particularly cryogenic and mechanical, are highly efficient and cost-effective for large production runs, reducing labor and turnaround time.
Please consult a Canyon Components Engineer about your specific application and we will use our decades of experience to formulate a solution that fits your need.
Get a Quote Now!
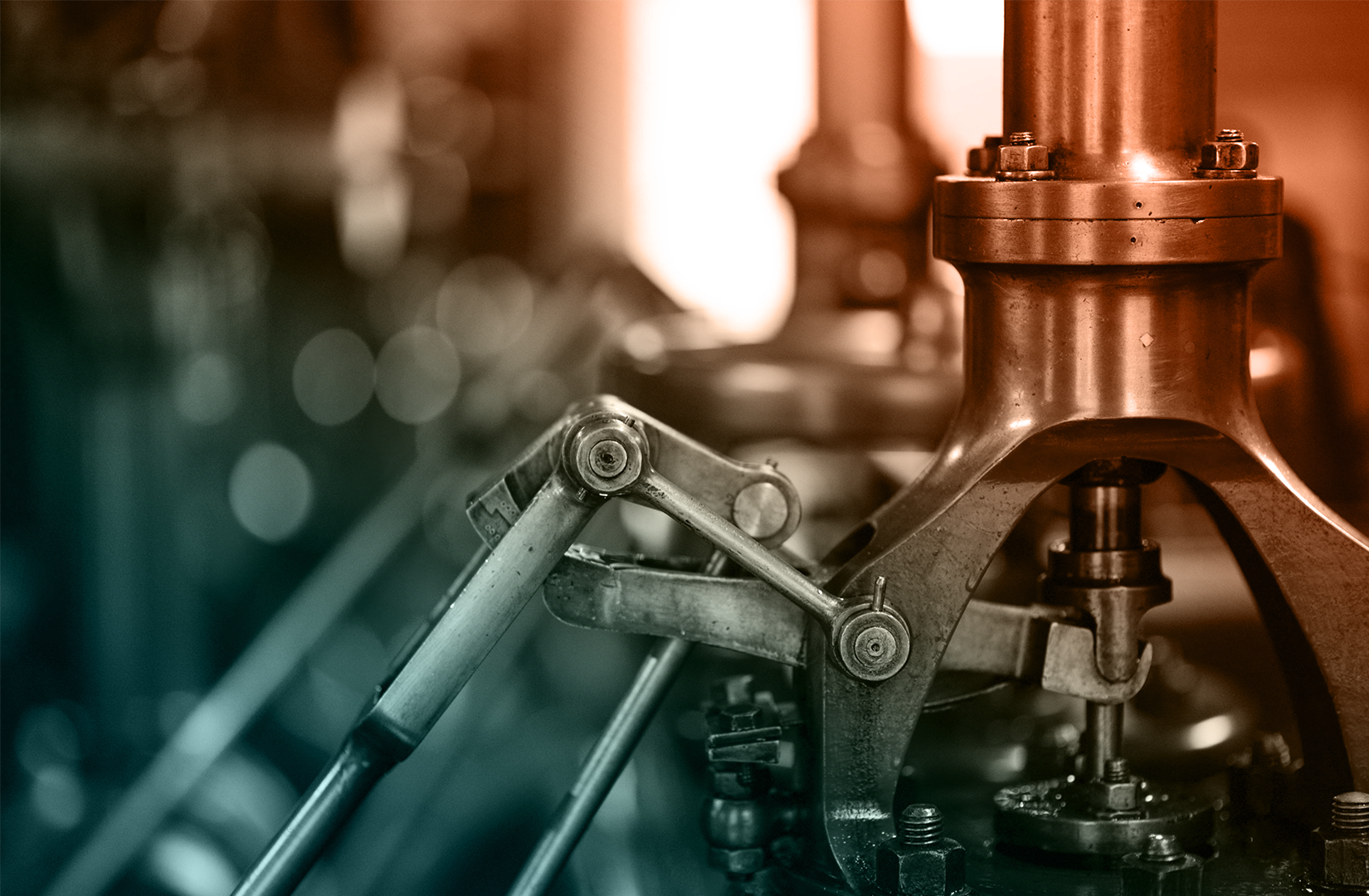
Common Applications
- Automotive Industry: Deflashing is essential for O-rings, gaskets, and custom-molded components used in automotive seals, gaskets, and other precision parts.
- Medical Devices: In medical applications, deflashing ensures that parts meet stringent cleanliness and precision standards, preventing contamination and ensuring a secure fit.
- Aerospace Components: Aerospace-grade O-rings and molded seals undergo deflashing to ensure reliable performance in high-stress environments.
- Industrial Equipment: Deflashing is used for seals, grommets, and custom parts in pumps, valves, and hydraulic systems where consistent sealing is critical.
- Electronics and Semiconductor: Clean, precise parts free from flash are essential in electronics to maintain component integrity and prevent interference in sensitive devices.
Canyon Components strives to meet all customer service requests. Feel free to contact Canyon Components engineering and let our knowledgeable staff help you design the perfect part for your needs.
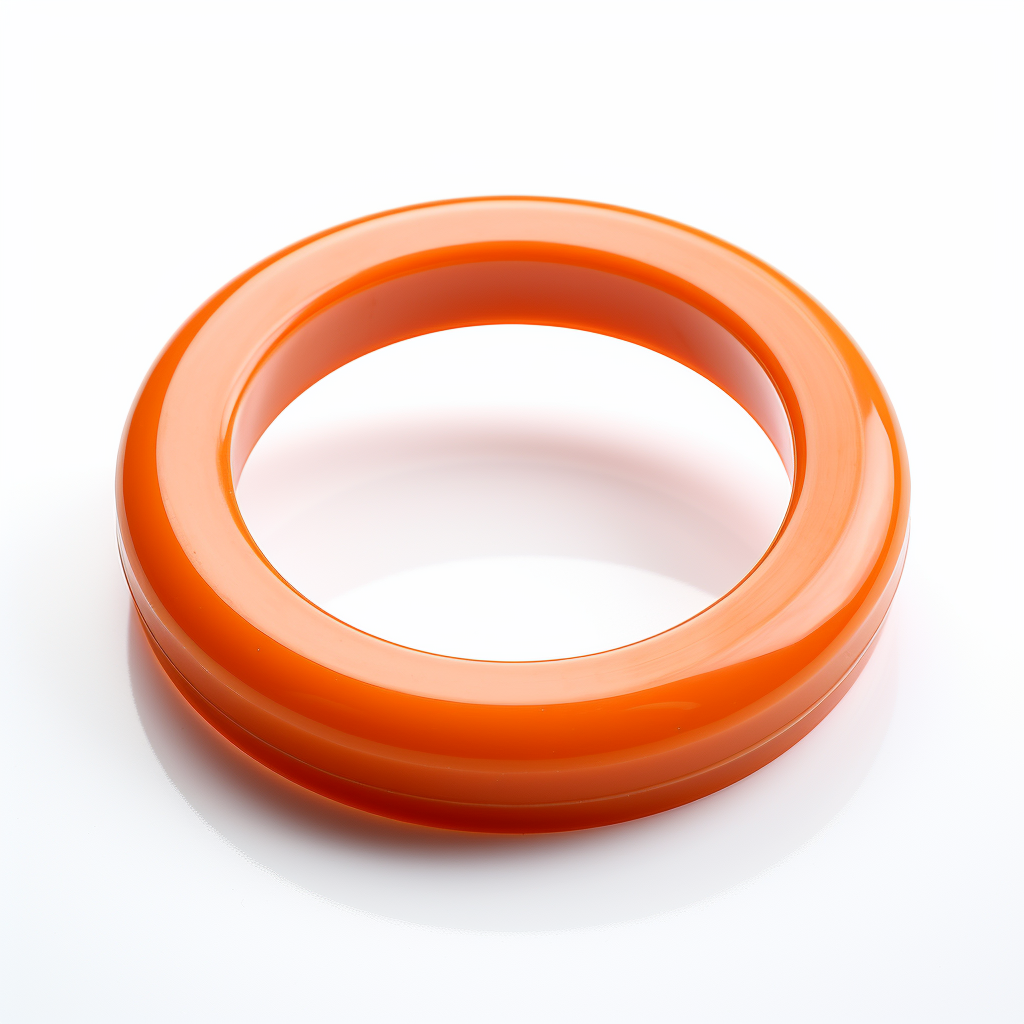
Pros and Cons of Deflashing Methods
Cryogenic Deflashing
- Pros: Extremely precise; ideal for complex geometries; highly efficient for large production volumes; preserves material integrity.
- Cons: Higher initial equipment cost; may not be suitable for parts sensitive to cold temperatures.
Mechanical Deflashing
- Pros: Cost-effective for larger, less intricate parts; versatile for different materials; fast for high-volume production.
- Cons: May cause surface roughness; less suitable for small or delicate parts; may leave inconsistent results on complex geometries.
Hand Trimming
- Pros: Highly controlled and customizable; ideal for low-volume production or prototypes; effective for intricate parts.
- Cons: Labor-intensive; slow and costly for high volumes; potential for inconsistent results based on operator skill.
Chemical Deflashing
- Pros: Can achieve high precision for specific materials; effective for hard-to-reach areas.
- Cons: Requires stringent handling and disposal of chemicals; limited applicability for certain materials; may impact material properties.
Back to Services Hub
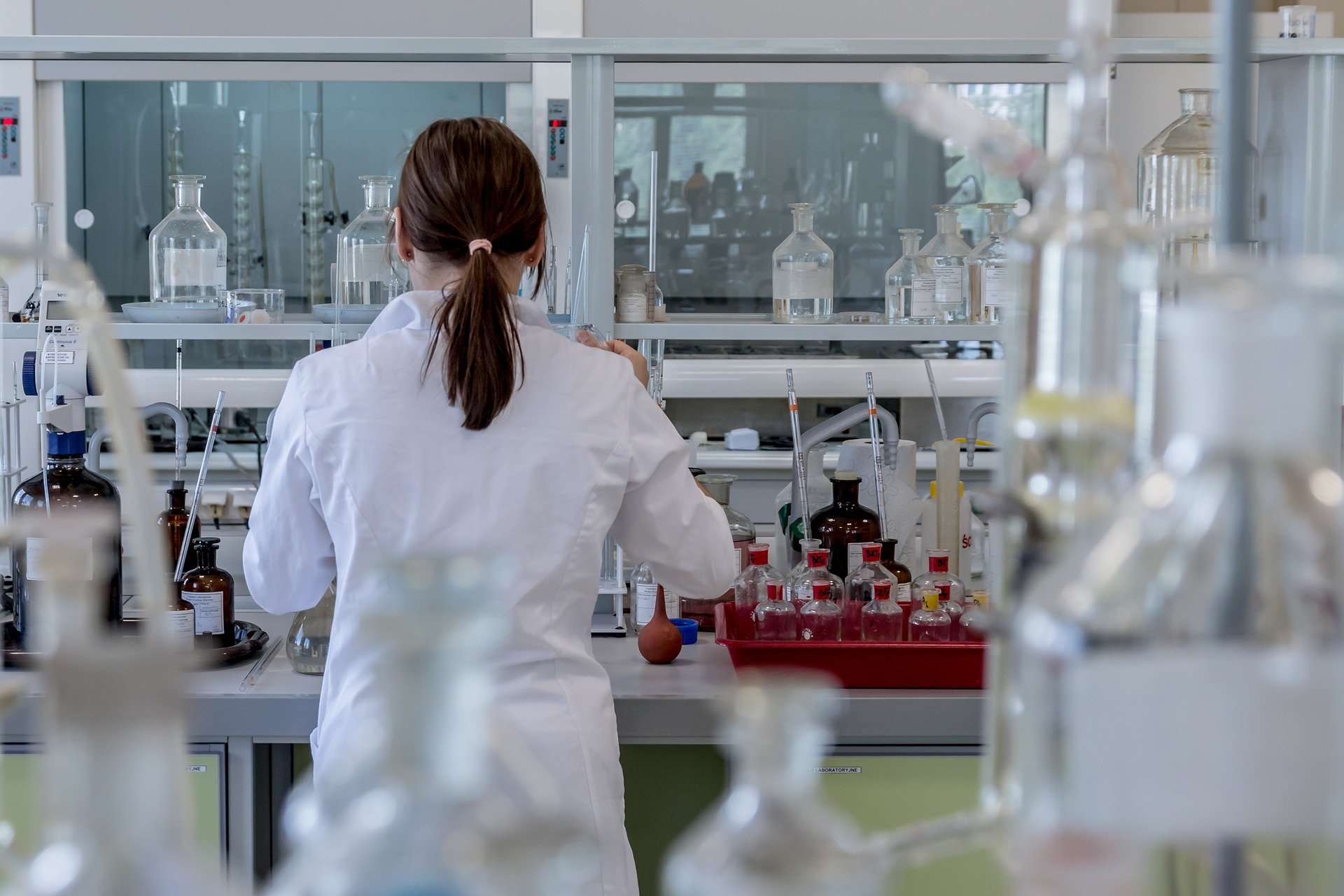
Get A Quote Now!
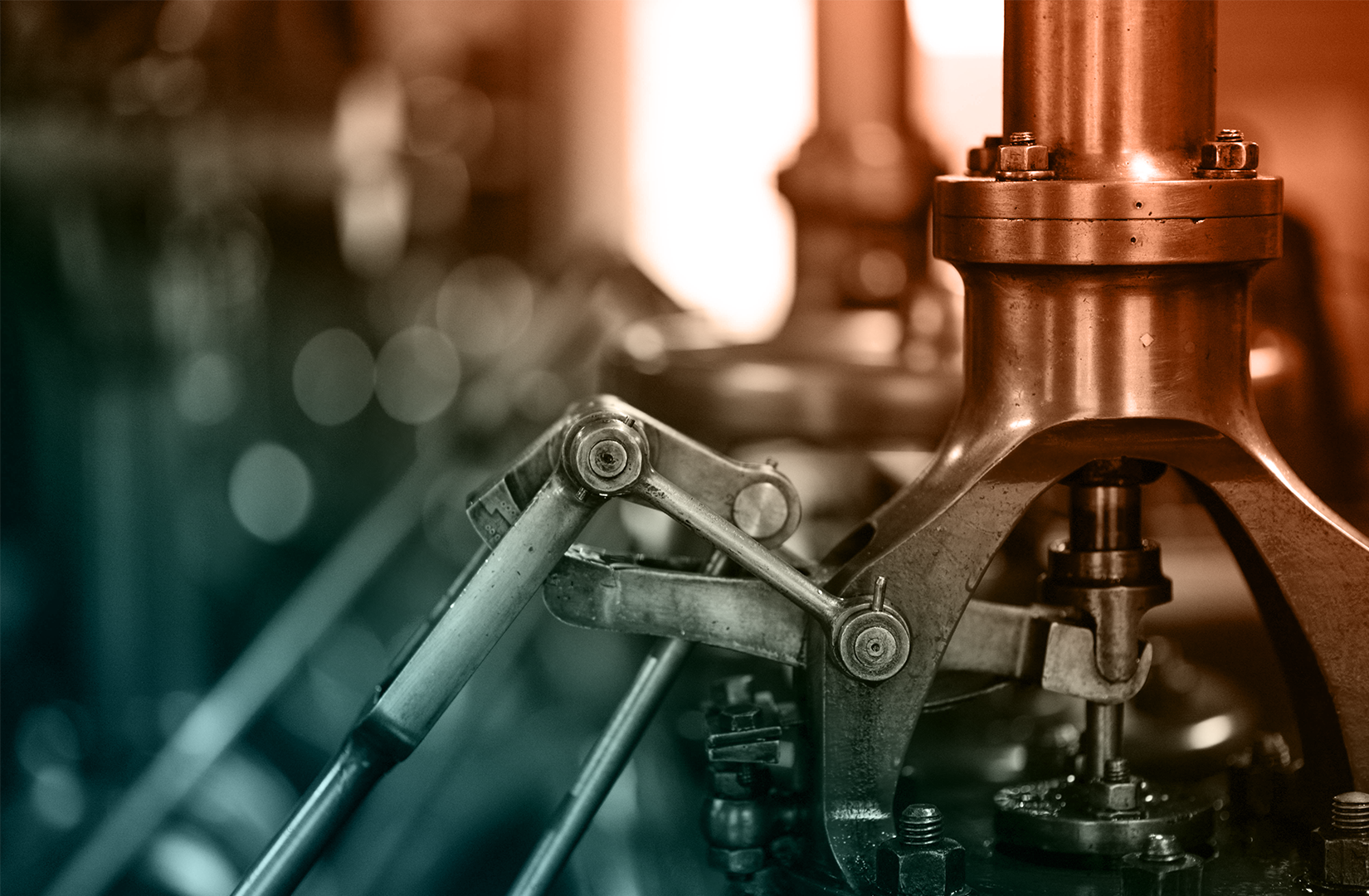