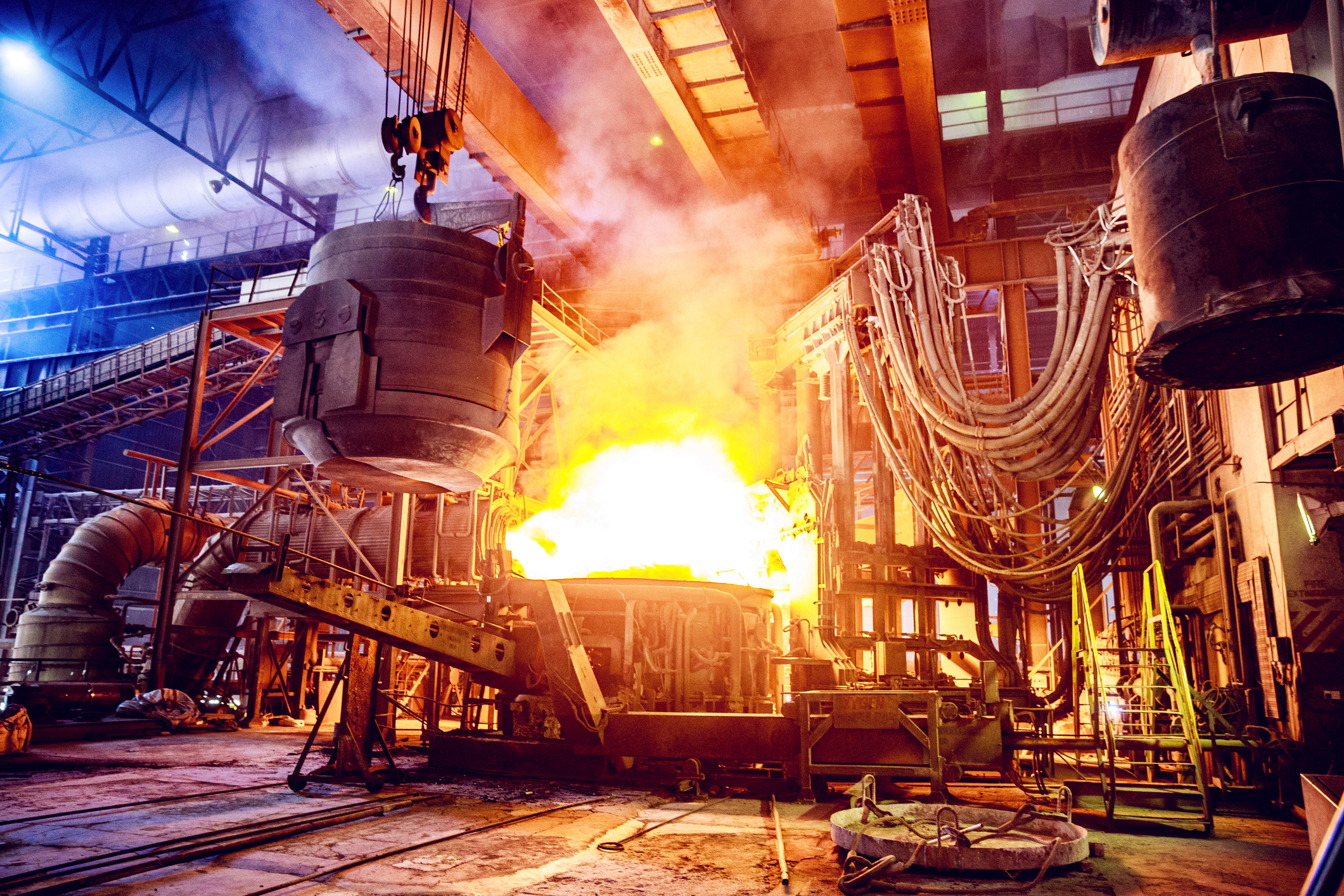
External Lubrication for O-Rings, Elastomers, and Plastics
External lubrication is essential for enhancing the performance and longevity of O-rings, elastomers, and plastics. Lubricants reduce friction, prevent wear, and improve sealing efficiency, especially in dynamic applications where movement is involved. This guide covers the types, features, common applications, and the pros and cons of external lubrication, with detailed information on popular lubricants such as O-Lube, silicone lubricant, Molykote, medical-grade lubricants, PTFE Teflon lubrication, and graphite.
External lubrication available for silicone, CanRez® FFKM and Kalrez® O-rings, gasket rapid manufacturing, & custom molded parts are available now!
Check with one of Canyon’s helpful product engineers for an expert material and manufacturing recommendation.
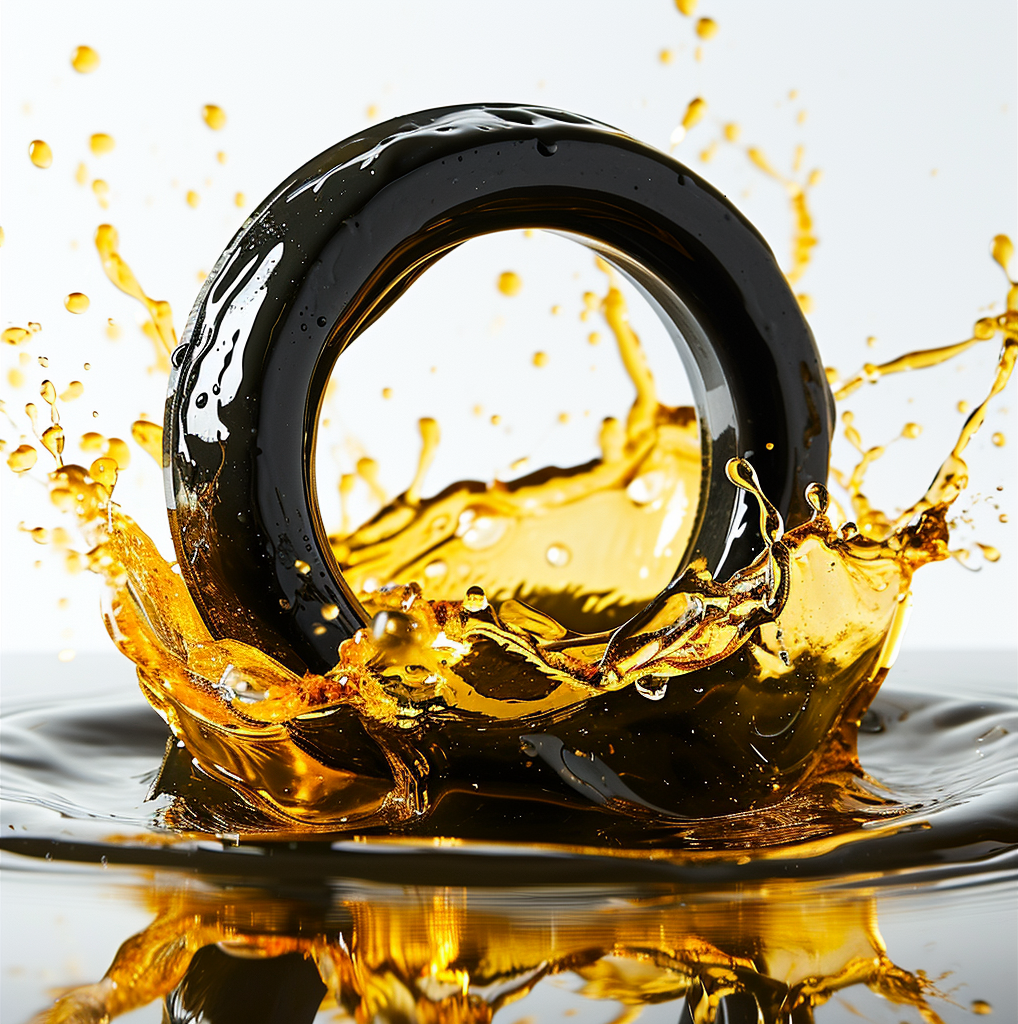
Types of External Lubrication
There are various types of external lubrication designed to meet specific needs for O-rings, elastomers, and plastics:
- O-Lube: O-Lube is a popular lubricant specifically designed for O-rings, providing long-lasting lubrication that enhances sealing and reduces friction in static and dynamic applications.
- Silicone Lubricant: Silicone lubricants offer excellent temperature stability and are ideal for use with rubber and plastic components, providing a non-reactive and non-toxic lubrication solution.
- Molykote: Molykote lubricants are high-performance solutions that often contain solid lubricants like MoS2 (Molybdenum Disulfide) to reduce wear and friction in high-load applications.
- Medical-Grade Lubricants: These lubricants are specifically formulated for use in medical devices and equipment, offering biocompatibility and safe use in sensitive environments.
- PTFE Teflon Lubrication: PTFE (Polytetrafluoroethylene) Teflon lubricants provide low friction and excellent chemical resistance, making them suitable for various industrial applications.
- Graphite: Graphite lubricants are dry lubricants that offer excellent lubrication in high-temperature environments, often used where liquid lubricants are not suitable.
Canyon Components strives to meet all customer service requests. Feel free to contact Canyon Components engineering and let our knowledgeable staff help you design the perfect part for your needs.
Features of External Lubrication
External lubricants offer several key features that enhance the performance of O-rings, elastomers, and plastics:
- Friction Reduction: Lubricants reduce surface friction, which is particularly important for elastomers in dynamic applications, preventing wear and tear and extending the life of the component.
- Temperature Resistance: Many lubricants are designed to withstand a wide range of temperatures, ensuring consistent performance in both high and low-temperature environments.
- Chemical Compatibility: Lubricants are available in formulations that are chemically compatible with various materials, preventing degradation and ensuring long-term effectiveness.
- Non-Toxic and Biocompatible Options: For medical and food-grade applications, lubricants are available that meet stringent safety and non-toxicity standards.
- Enhanced Sealing Efficiency: By reducing friction and wear, lubricants improve the sealing efficiency of O-rings and other elastomeric components, ensuring leak-free performance.
Common Applications of External Lubrication
External lubrication is used across a wide range of industries and applications to enhance the performance of O-rings, elastomers, and plastics:
- Automotive: Lubricants are used to reduce friction and wear in seals, gaskets, and other elastomeric components within engines, transmissions, and braking systems.
- Medical Devices: Medical-grade lubricants are applied to elastomers and plastics used in devices such as syringes, catheters, and seals, ensuring biocompatibility and smooth operation.
- Aerospace: In aerospace applications, lubricants help protect seals and gaskets from extreme temperatures and pressures, improving the reliability of critical components.
- Industrial Machinery: Lubricants are used to reduce wear and improve the lifespan of O-rings, seals, and plastic components in pumps, valves, and other industrial machinery.
- Consumer Electronics: Lubricants are applied to plastic components in consumer electronics to reduce friction and prevent wear, enhancing product durability.
Please consult a Canyon Components Engineer about your specific application and we will use our decades of experience to formulate a solution that fits your need.
Get a Quote Now!
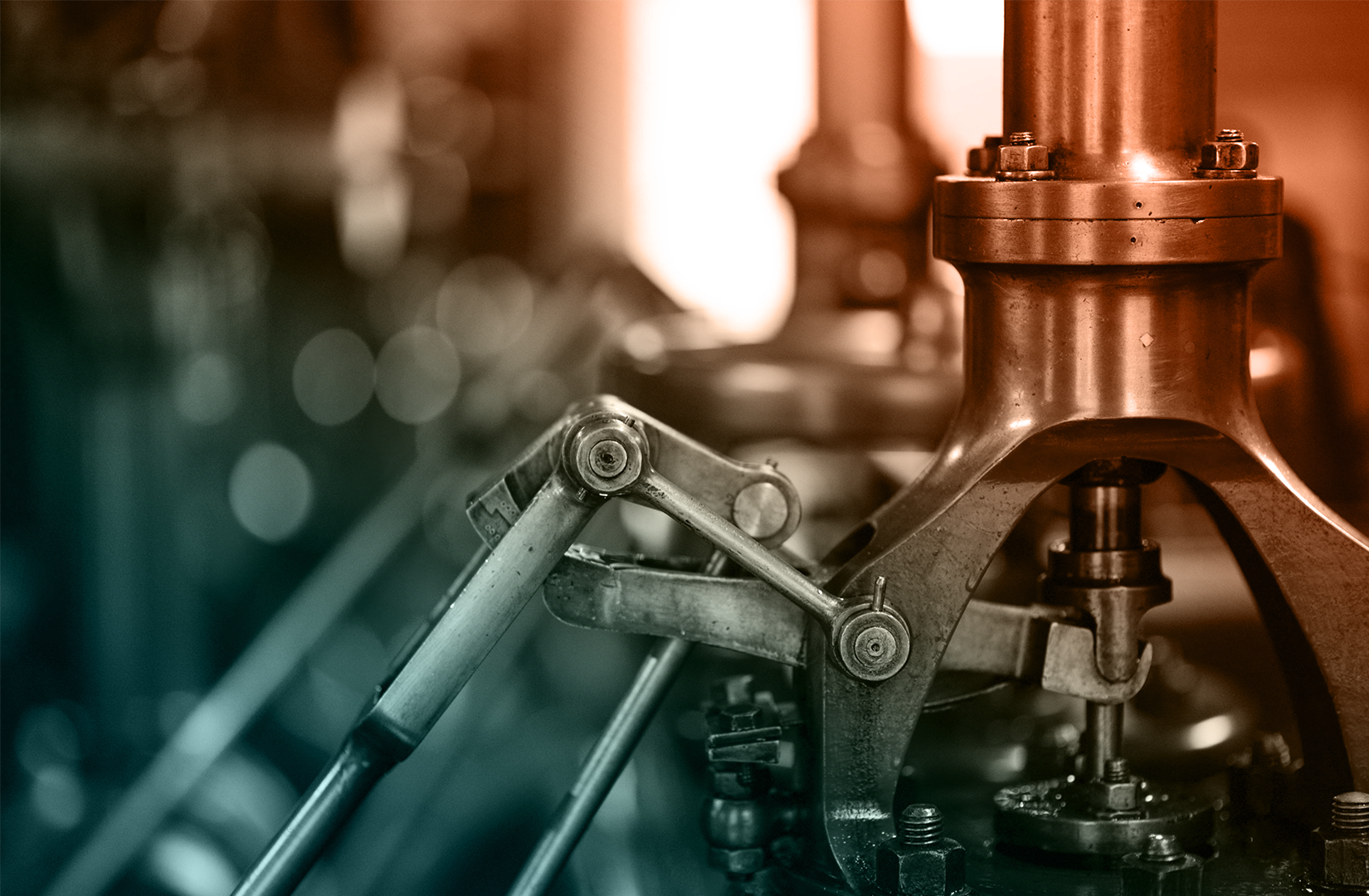
Lowered Surface Friction for Elastomers
For elastomers, particularly O-rings, reducing surface friction is crucial for extending the lifespan and improving performance in dynamic applications. Lubricants like PTFE Teflon and silicone can significantly reduce friction, preventing wear and tear during movement. This reduction in friction not only enhances sealing capabilities but also reduces the force required for installation, making it easier to fit elastomers into tight spaces without damage.
Canyon Components strives to meet all customer service requests. Feel free to contact Canyon Components engineering and let our knowledgeable staff help you design the perfect part for your needs.
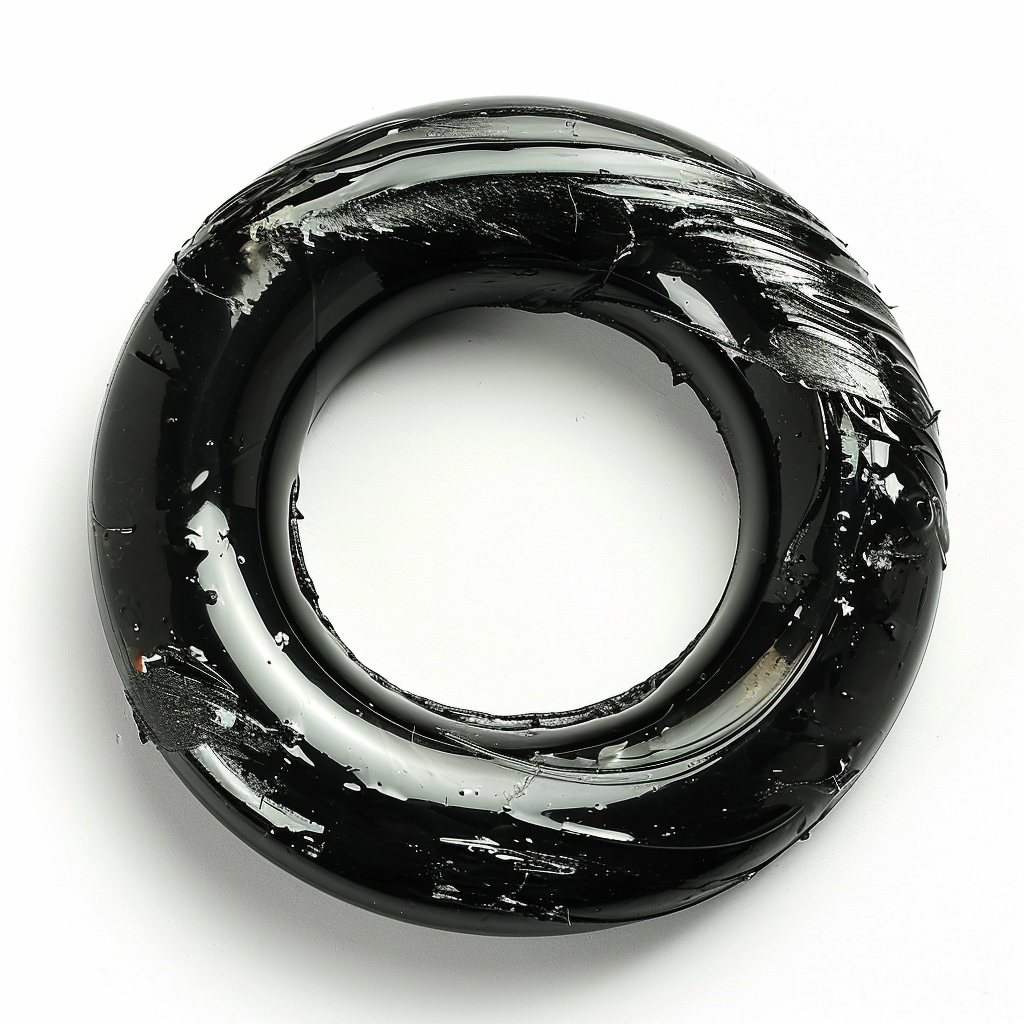
Specific Lubricants for O-Rings, Elastomers, and Plastics
O-Lube
- Features: O-Lube is specifically formulated for O-rings, providing long-lasting lubrication that enhances sealing and reduces friction. It is compatible with a wide range of elastomers and is ideal for both static and dynamic applications.
- Applications: Commonly used in hydraulic systems, pneumatic seals, and industrial machinery where reliable O-ring performance is critical.
- Pros: Easy to apply, long-lasting, enhances sealing performance.
- Cons: May not be suitable for use with all elastomers or in high-temperature environments.
Silicone Lubricant
- Features: Silicone lubricants are versatile, offering excellent temperature stability, non-toxicity, and compatibility with many rubber and plastic materials.
- Applications: Widely used in automotive seals, medical devices, and consumer electronics.
- Pros: Excellent temperature resistance, non-reactive, safe for use in sensitive environments.
- Cons: May attract dust and dirt over time, which can affect performance.
Molykote
- Features: Molykote lubricants often contain solid lubricants like MoS2, providing high-load carrying capacity and reducing wear in demanding applications.
- Applications: Used in heavy industrial machinery, automotive components, and aerospace applications where high performance is required.
- Pros: High load-bearing capacity, excellent wear protection.
- Cons: Can be more expensive than other lubricants, may require precise application.
Medical-Grade Lubricants
- Features: These lubricants are formulated to be biocompatible, non-toxic, and safe for use in medical devices and equipment.
- Applications: Commonly used in syringes, catheters, seals, and other medical components.
- Pros: Safe for use in sensitive environments, non-toxic, ensures smooth operation.
- Cons: Typically more expensive, may have limited temperature or chemical resistance.
PTFE Teflon Lubrication
- Features: PTFE Teflon lubricants provide a low-friction surface, excellent chemical resistance, and are non-reactive with most materials.
- Applications: Used in industrial machinery, automotive components, and electronics where low friction and chemical resistance are essential.
- Pros: Reduces friction, chemically inert, wide temperature range.
- Cons: Can be challenging to apply evenly, may not adhere well to some surfaces.
Graphite
- Features: Graphite is a dry lubricant that offers excellent lubrication in high-temperature environments and is ideal for applications where liquid lubricants are unsuitable.
- Applications: Used in high-temperature industrial processes, furnaces, and certain automotive applications.
- Pros: High-temperature resistance, excellent lubricating properties, does not attract dust or dirt.
- Cons: Limited to specific applications, may not provide sufficient lubrication in low-temperature or low-load situations.
Canyon Components strives to meet all customer service requests. Feel free to contact Canyon Components engineering and let our knowledgeable staff help you design the perfect part for your needs.
External Lubrication Pros & Cons
External lubrication plays a vital role in enhancing the performance and longevity of O-rings, elastomers, and plastics across various industries. With a range of lubricants available, including O-Lube, silicone, Molykote, medical-grade options, PTFE Teflon, and graphite, there's a solution for nearly every application. By understanding the types, features, and potential pros and cons of these lubricants, you can make informed decisions to ensure optimal performance and durability in your systems.
Canyon Components strives to meet all customer service requests. Feel free to contact Canyon Components engineering and let our knowledgeable staff help you design the perfect part for your needs.
Pros of External Lubrication
External lubrication offers several advantages that make it a valuable solution for many applications:
- Extended Component Life: By reducing friction and wear, lubricants help extend the lifespan of O-rings, elastomers, and plastic components.
- Improved Sealing Performance: Lubricants enhance the sealing efficiency of O-rings and gaskets, preventing leaks and ensuring reliable operation.
- Temperature and Chemical Resistance: Lubricants are available that can withstand extreme temperatures and harsh chemicals, ensuring consistent performance in challenging environments.
- Reduced Maintenance: Proper lubrication reduces the need for frequent maintenance and component replacement, lowering overall operating costs.
- Versatility: With a wide range of lubricant options available, there is a solution for nearly every application, from medical devices to heavy industrial machinery.
Cons of External Lubrication
While external lubrication offers many benefits, there are also some potential drawbacks to consider:
- Compatibility Issues: Not all lubricants are compatible with all materials, and using the wrong lubricant can cause degradation or failure of the component.
- Application Complexity: Proper application of lubricants is crucial for effectiveness, and incorrect application can lead to inadequate protection or even component damage.
- Cost: High-quality lubricants, especially those designed for specific applications like medical or aerospace, can be expensive.
- Potential for Contamination: In sensitive applications, such as medical devices or food processing, the risk of contamination from lubricants must be carefully managed.
Back to Products Hub
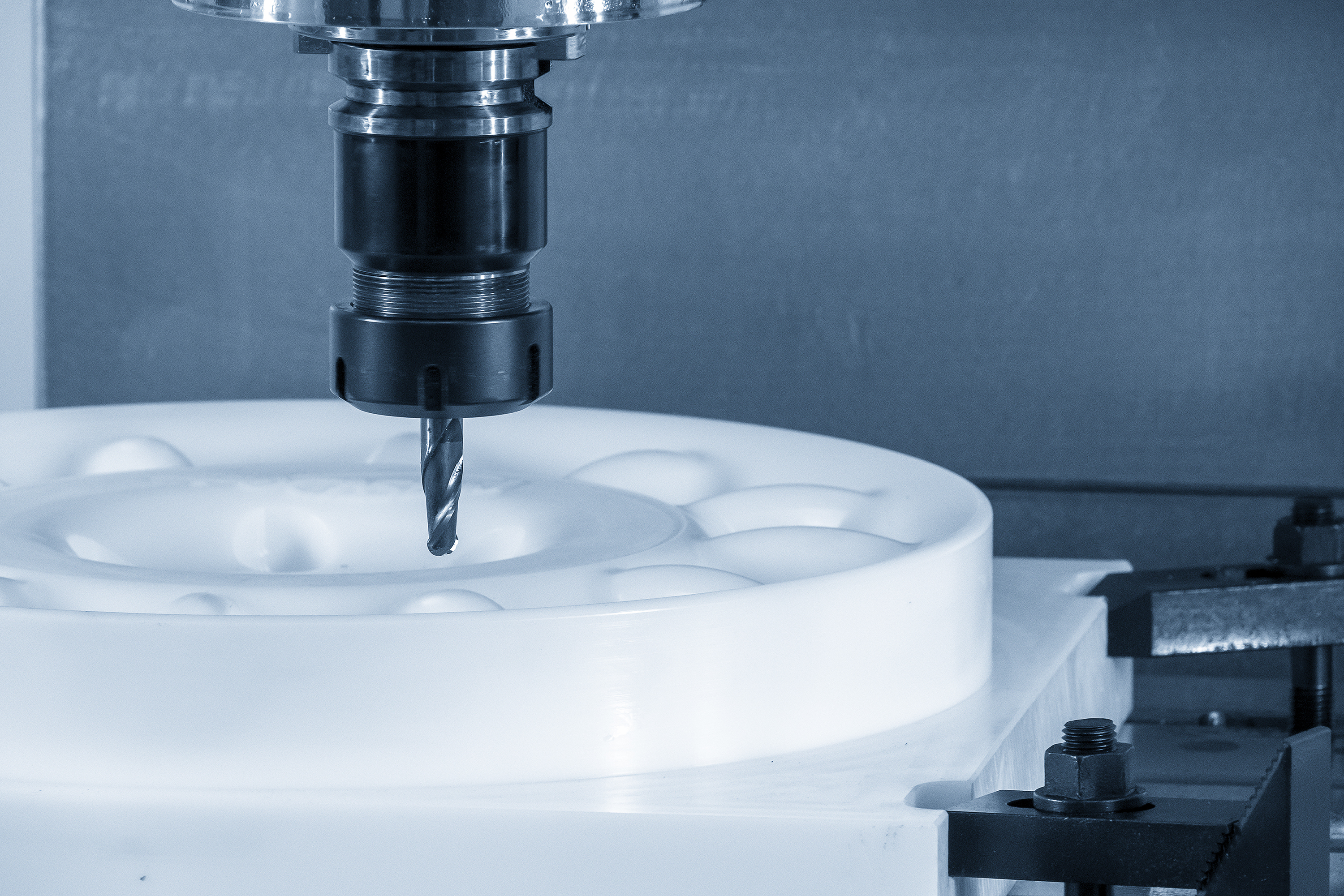
Get A Quote Now!
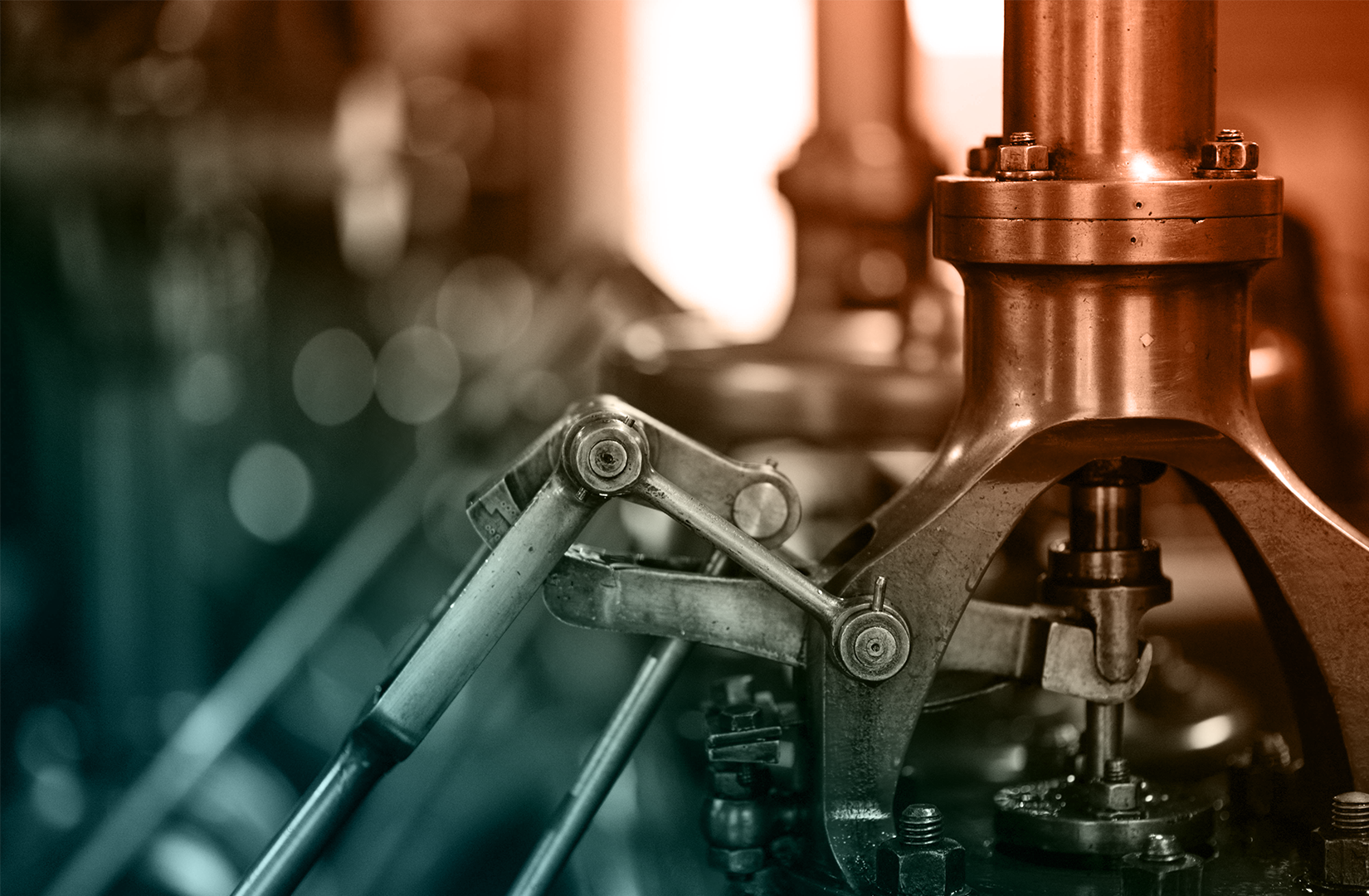