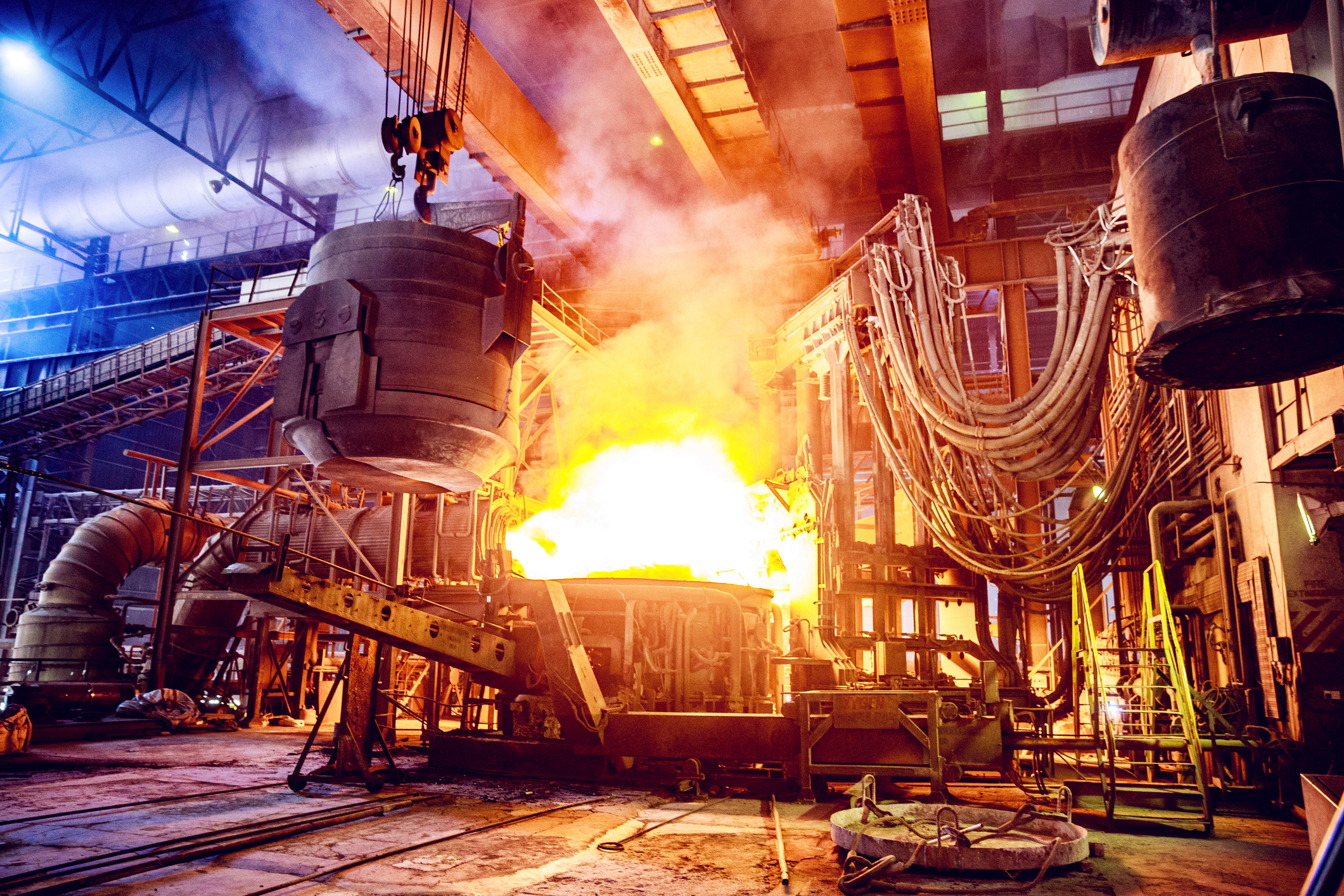
Internal Lubrication for O-Rings and Elastomers
Internal lubrication is a crucial aspect of enhancing the performance and longevity of O-rings and elastomers. By incorporating lubricants directly into the material during the manufacturing process, internal lubrication reduces friction, wear, and heat generation, which are critical factors in dynamic sealing applications. This guide covers the types, features, common applications, and the pros and cons of internal lubrication for O-rings and elastomers, with detailed information on sulfur bloom, silicone lubricant, medical-grade lubricants, PTFE Teflon lubrication, and graphite.
CanRez® FFKM and Kalrez® O-rings, gasket rapid manufacturing, & custom molded parts are available now!
Check with one of Canyon’s helpful product engineers for an expert material and manufacturing recommendation.
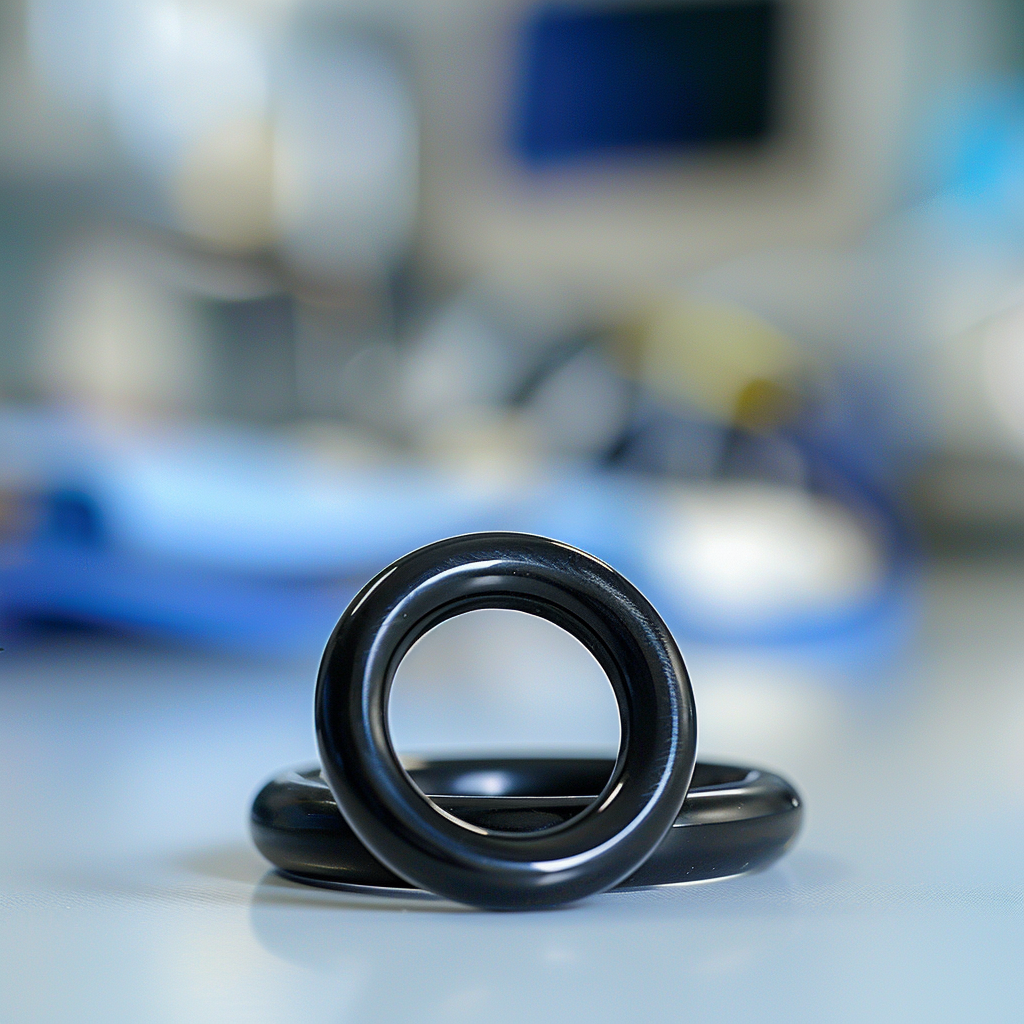
Features of Internal Lubrication
Internal lubrication offers several key features that enhance the performance of O-rings and elastomers:
- Friction Reduction: By incorporating lubricants directly into the elastomer, internal lubrication reduces the coefficient of friction, leading to smoother operation and less wear in dynamic applications.
- Extended Service Life: Reduced friction and wear result in longer service life for O-rings and elastomers, reducing the frequency of replacements and maintenance.
- Temperature Stability: Many internal lubricants, such as silicone and PTFE, offer excellent temperature stability, ensuring consistent performance across a wide range of operating temperatures.
- Chemical Resistance: Internal lubricants like PTFE and graphite provide enhanced chemical resistance, protecting the elastomer from degradation in harsh environments.
- Compatibility: Internal lubricants are chosen based on their compatibility with the elastomer material and the application, ensuring that they do not adversely affect the performance of the seal.
Common Applications of Internal Lubrication
Internal lubrication is used in various industries to improve the performance of O-rings and elastomers in demanding applications:
- Automotive: Internal lubrication is commonly used in automotive seals and gaskets to reduce friction and wear in engines, transmissions, and braking systems.
- Medical Devices: Medical-grade lubricants are used in elastomers for medical devices, such as seals in syringes and valves, ensuring smooth operation and compliance with biocompatibility standards.
- Aerospace: In aerospace applications, internally lubricated elastomers are used in critical seals and gaskets, where reduced friction and enhanced wear resistance are essential for reliable performance.
- Industrial Machinery: Internal lubrication is used in O-rings and seals for industrial machinery, reducing wear and extending the service life of components in pumps, valves, and hydraulic systems.
- Chemical Processing: Elastomers with internal PTFE or graphite lubrication are used in chemical processing applications, where resistance to aggressive chemicals and high temperatures is required.
Please consult a Canyon Components Engineer about your specific application and we will use our decades of experience to formulate a solution that fits your need.
Internally Lubricated Materials Available
Filter by
Temperature Search (°C)
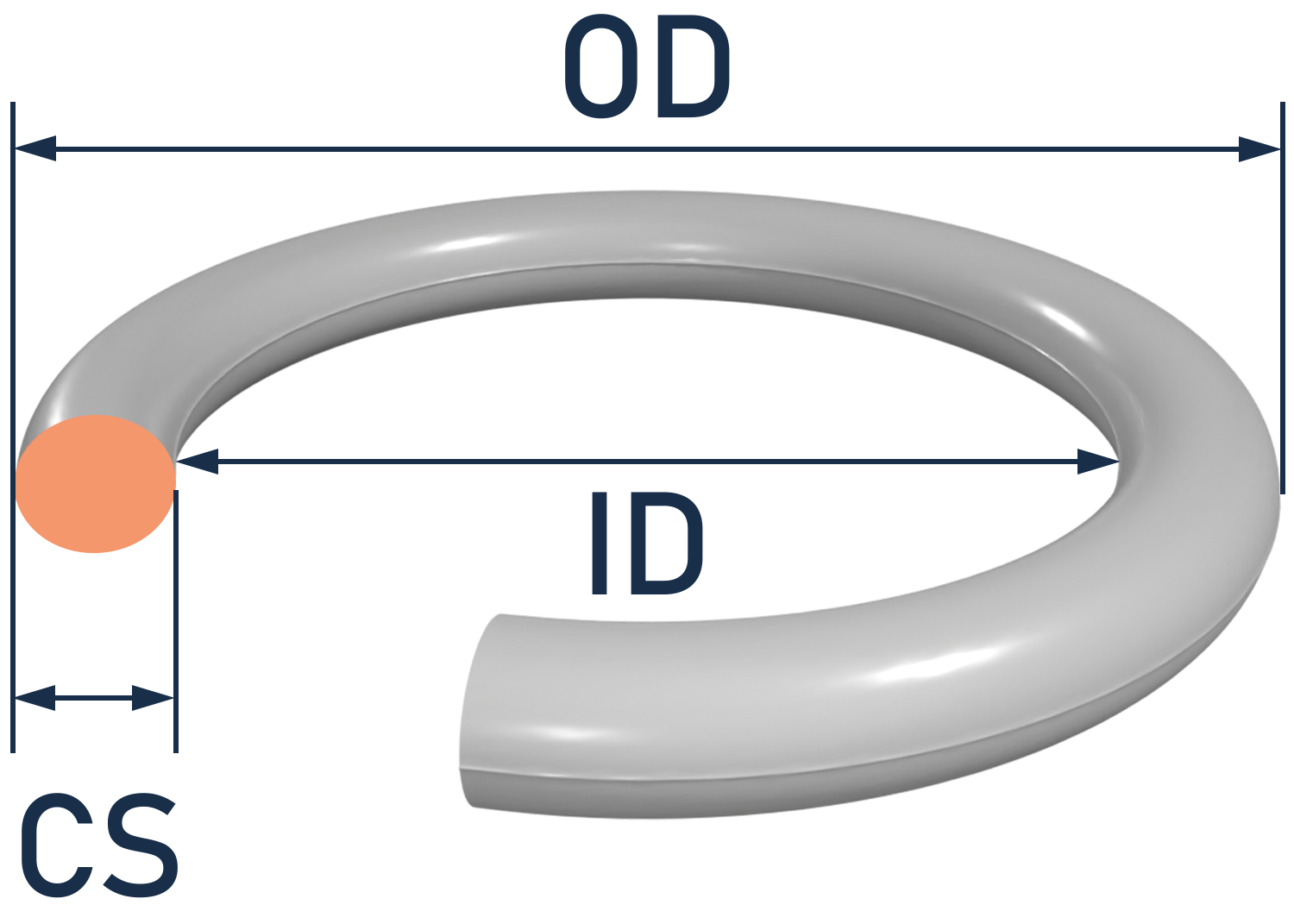
Get a Quote Now!
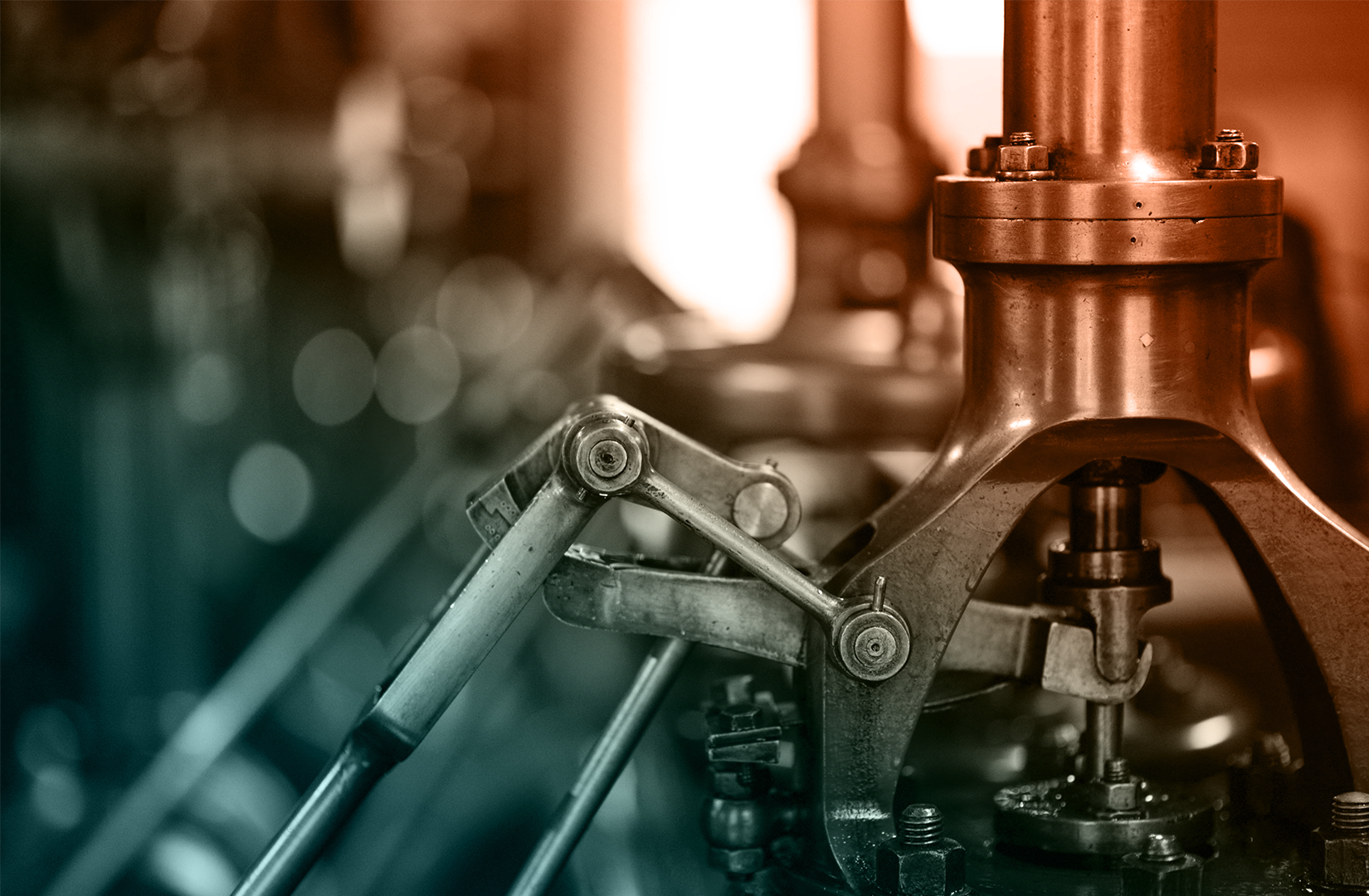
Types of Internal Lubrication
Internal lubrication can be achieved using various types of lubricants, each offering specific benefits depending on the application:
- Sulfur Bloom: A natural phenomenon where sulfur migrates to the surface of certain types of rubber, providing a limited amount of lubrication. While not an intentional internal lubricant, sulfur bloom can impact the performance of O-rings and elastomers.
- Silicone Lubricant: Silicone is widely used as an internal lubricant due to its excellent temperature stability and compatibility with a wide range of elastomeric materials.
- Medical-Grade Lubricants: These lubricants are biocompatible and safe for use in medical applications, ensuring that the elastomers do not release harmful substances during use.
- PTFE Teflon Lubrication: PTFE (Polytetrafluoroethylene) is known for its low friction and excellent chemical resistance, making it an ideal internal lubricant for demanding applications.
- Graphite: Graphite is a solid lubricant that can be incorporated into elastomers to reduce friction and enhance wear resistance, particularly in high-temperature applications.
Canyon Components strives to meet all customer service requests. Feel free to contact Canyon Components engineering and let our knowledgeable staff help you design the perfect part for your needs.
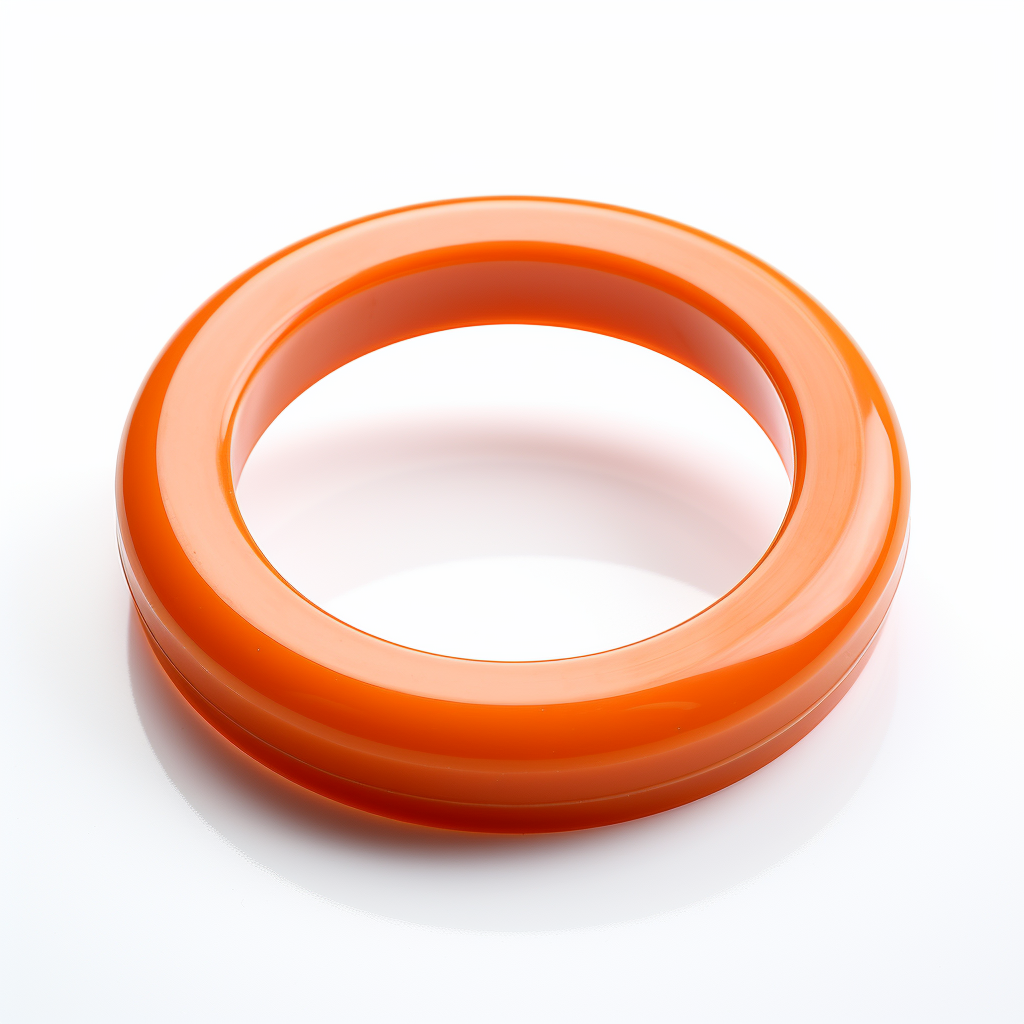
Internal Lubrication Pros & Cons
Internal lubrication is a powerful tool for enhancing the performance and longevity of O-rings and elastomers in a wide range of applications. By reducing friction, improving wear resistance, and enhancing chemical and temperature stability, internally lubricated elastomers provide significant benefits in industries such as automotive, aerospace, medical devices, and chemical processing. However, it is essential to consider the compatibility of the lubricant with the elastomer material and the specific application requirements to ensure optimal performance. Understanding the features, applications, and potential drawbacks of internal lubrication will help you make informed decisions to achieve the best results for your sealing solutions.
Canyon Components strives to meet all customer service requests. Feel free to contact Canyon Components engineering and let our knowledgeable staff help you design the perfect part for your needs.
Pros of Internal Lubrication
Internal lubrication offers several advantages that make it a valuable solution for many applications:
- Improved Performance: Internal lubrication reduces friction and wear, leading to smoother operation and longer service life for O-rings and elastomers.
- Consistency: Because the lubricant is incorporated into the elastomer, it provides consistent lubrication throughout the life of the part, unlike external lubricants that may wear off over time.
- Enhanced Chemical and Temperature Resistance: Lubricants like PTFE and graphite improve the chemical and temperature resistance of elastomers, making them suitable for more demanding environments.
- Reduced Maintenance: Internally lubricated elastomers require less frequent maintenance and replacement, reducing downtime and operational costs.
Cons of Internal Lubrication
While internal lubrication offers many benefits, there are also some potential drawbacks to consider:
- Material Compatibility: Not all lubricants are compatible with all elastomer materials, and choosing the wrong combination can lead to degradation or reduced performance.
- Cost: The process of incorporating internal lubricants can increase the cost of the elastomer, making it more expensive than standard, non-lubricated options.
- Limited Lubrication: Internal lubrication may not provide as much friction reduction as external lubricants, especially in applications with very high dynamic loads.
- Sulfur Bloom: While sulfur bloom can provide some lubrication, it can also lead to surface contamination, which may affect the performance of the elastomer in certain applications that require high cleanliness.
Back to Products Hub
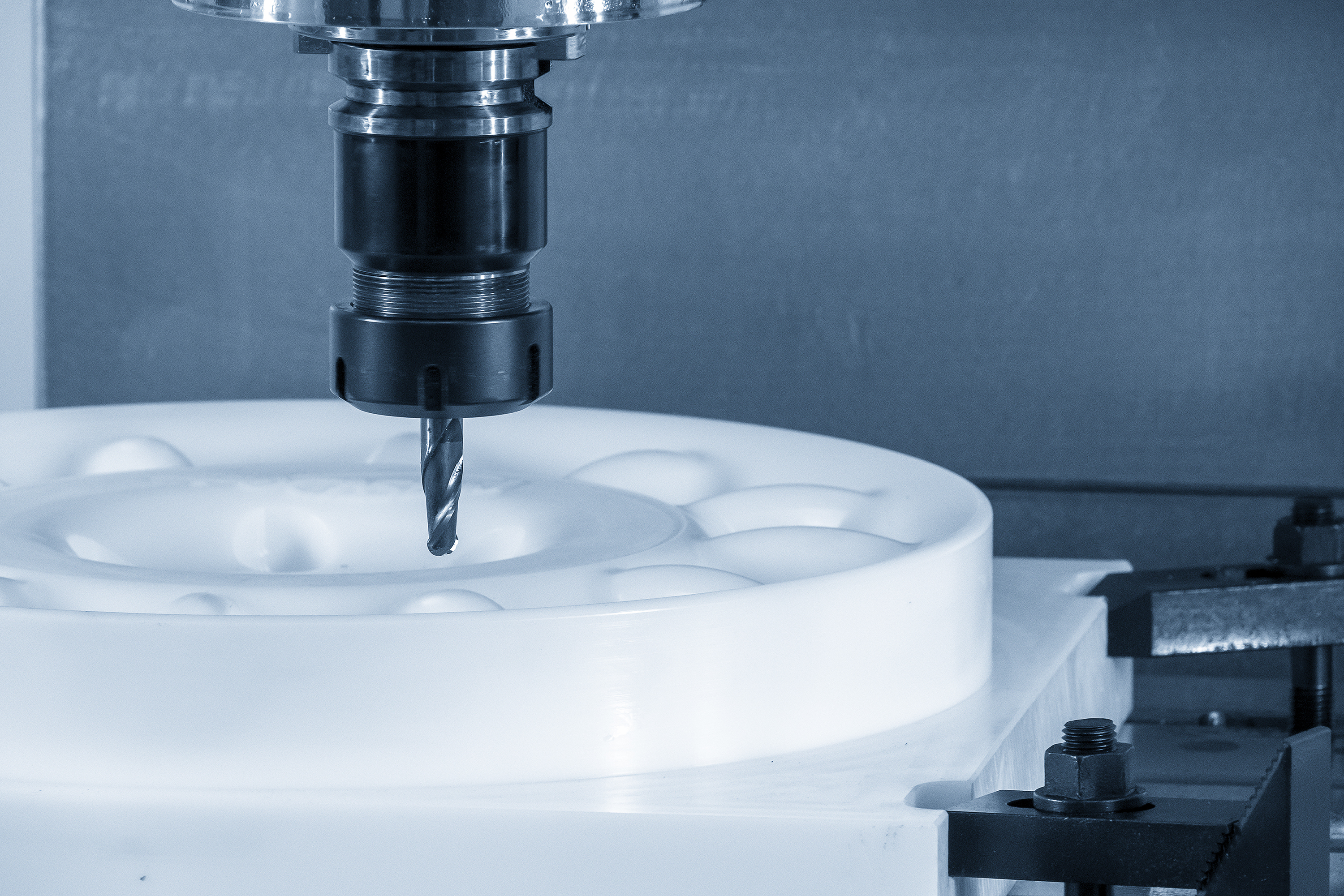
Get A Quote Now!
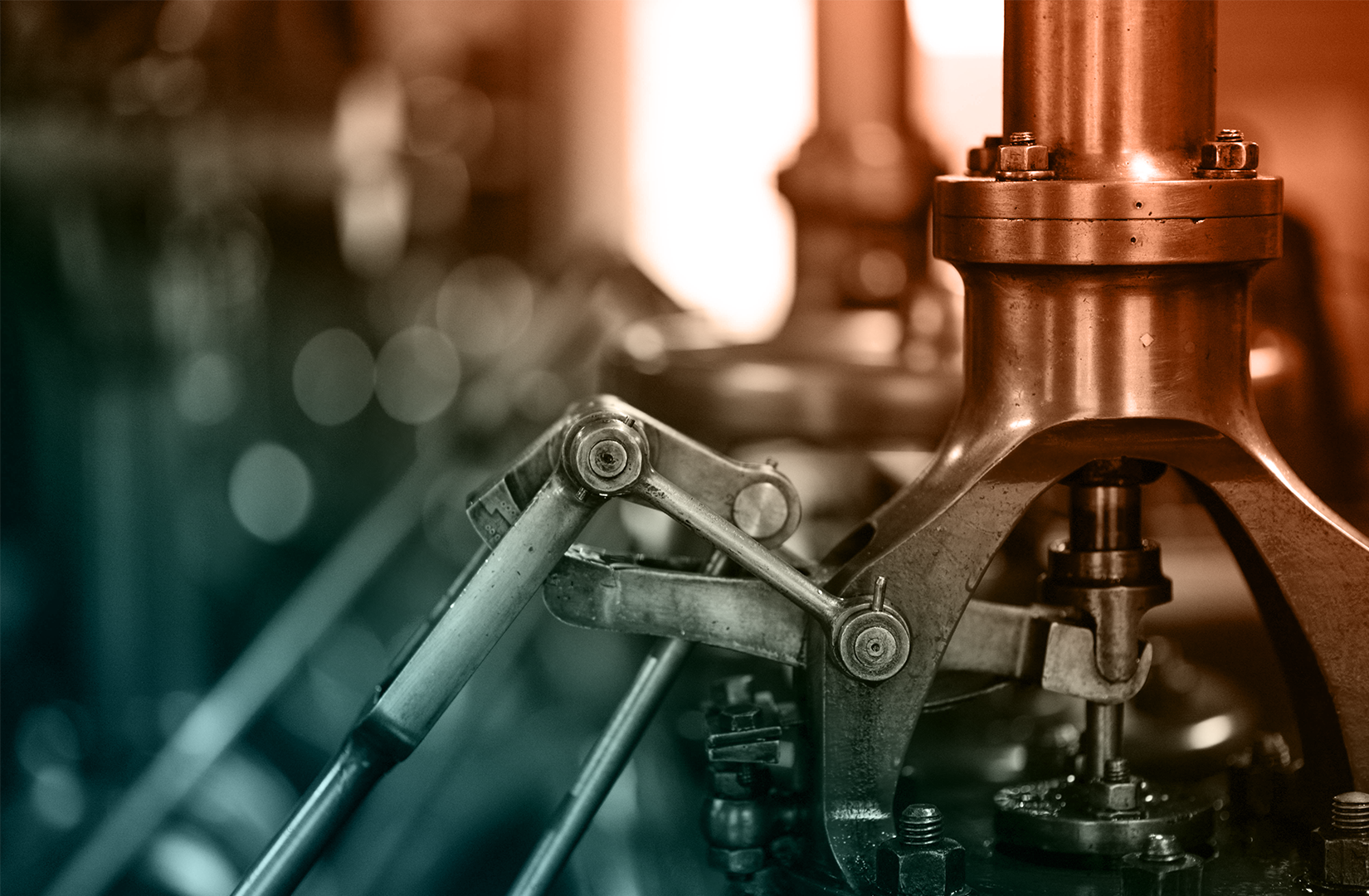