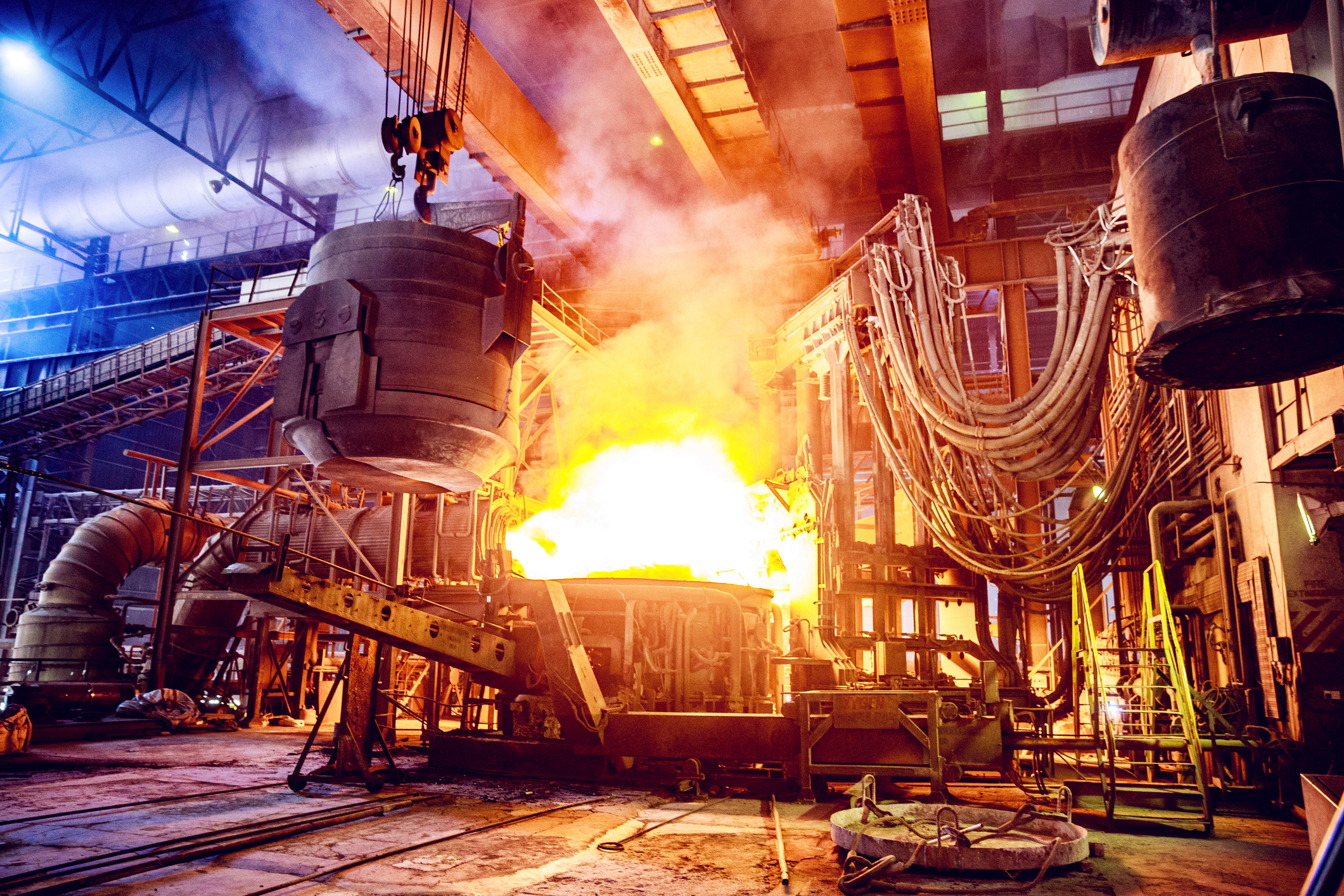
Isolation Gaskets: Electrical, Fire, & Thermal Insulation
Isolation gaskets are specialized sealing solutions designed to prevent galvanic corrosion, manage the flow of electricity, and maintain the integrity of pipeline systems. These gaskets are crucial in ensuring the longevity and safety of piping systems in industries such as oil and gas, chemical processing, and water treatment. This guide covers the features, common applications, materials, the differences between High Temp and Fire Safe gaskets, and the pros and cons of using isolation gaskets.
CanRez® FFKM and Kalrez® O-rings, gasket rapid manufacturing, & custom molded parts are available now!
Check with one of Canyon’s helpful product engineers for an expert material and manufacturing recommendation.
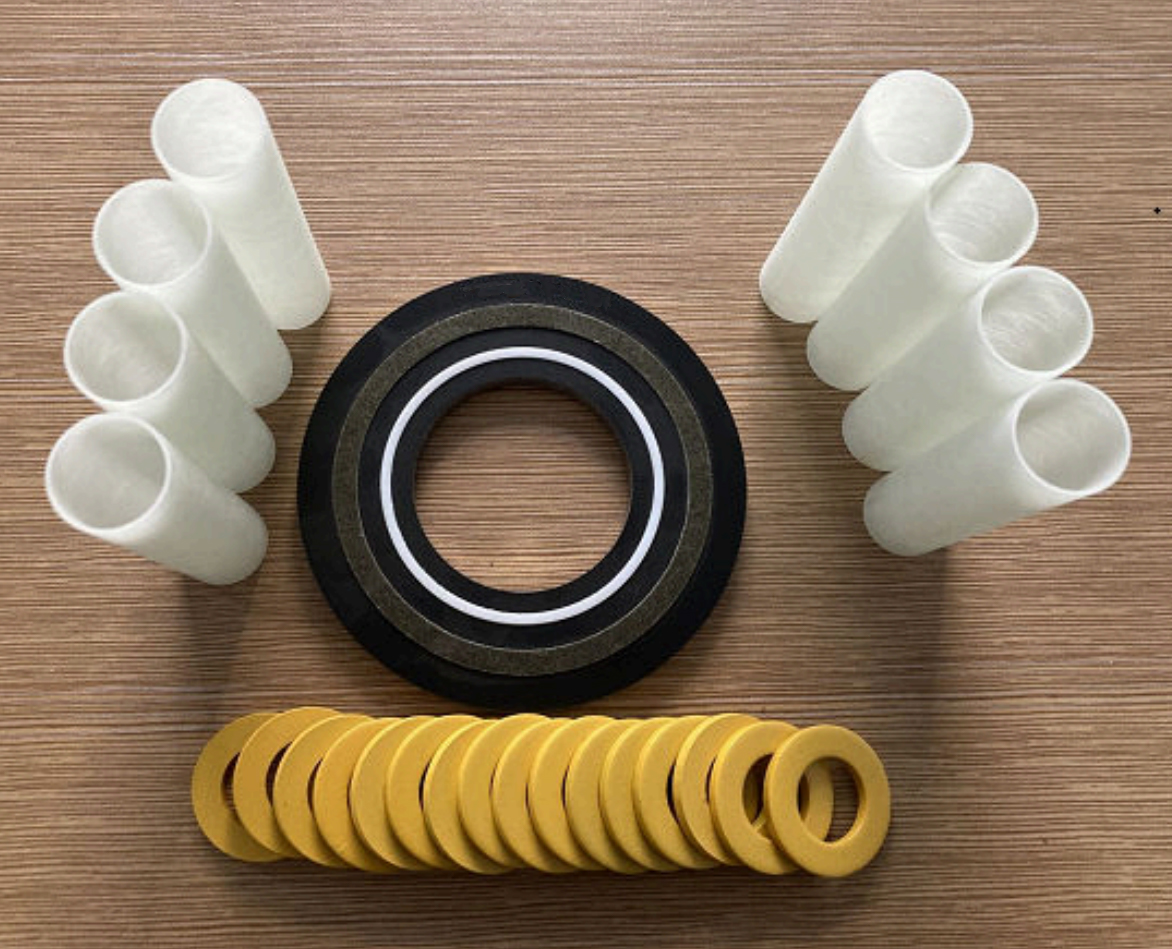
Features of Isolation Gaskets
Isolation gaskets offer several key features that make them essential in maintaining the safety and integrity of pipeline systems:
- Electrical Isolation: These gaskets provide a barrier that prevents the flow of electricity between dissimilar metals in a pipeline system, reducing the risk of galvanic corrosion.
- Corrosion Protection: By isolating different sections of a pipeline, these gaskets prevent the electrochemical reaction that leads to corrosion, extending the life of the system.
- Pressure and Temperature Resistance: Isolation gaskets are designed to withstand high pressures and temperatures, ensuring reliable sealing performance in demanding environments.
- Fire Safety: Certain isolation gaskets are engineered to maintain their integrity and sealing capabilities even in the event of a fire, providing an additional layer of safety in critical applications.
- Flexibility: Isolation gaskets are available in various designs and materials, making them adaptable to a wide range of applications and environmental conditions.
Common Applications of Isolation Gaskets
Isolation gaskets are used in a variety of industries where the prevention of galvanic corrosion and electrical isolation is critical:
- Oil and Gas: In the oil and gas industry, isolation gaskets are used in pipelines, flanges, and valves to prevent galvanic corrosion and ensure the integrity of the system in harsh environments.
- Chemical Processing: Isolation gaskets are employed in chemical plants to prevent corrosion and maintain the purity of chemical processes by isolating different sections of piping.
- Water Treatment: In water treatment facilities, these gaskets help prevent corrosion and ensure the longevity of the piping system, particularly in environments with aggressive water chemistries.
- Marine Industry: Isolation gaskets are used in marine applications to protect metal components from the corrosive effects of saltwater and to maintain the integrity of onboard piping systems.
Please consult a Canyon Components Engineer about your specific application and we will use our decades of experience to formulate a solution that fits your need.
Get a Quote Now!
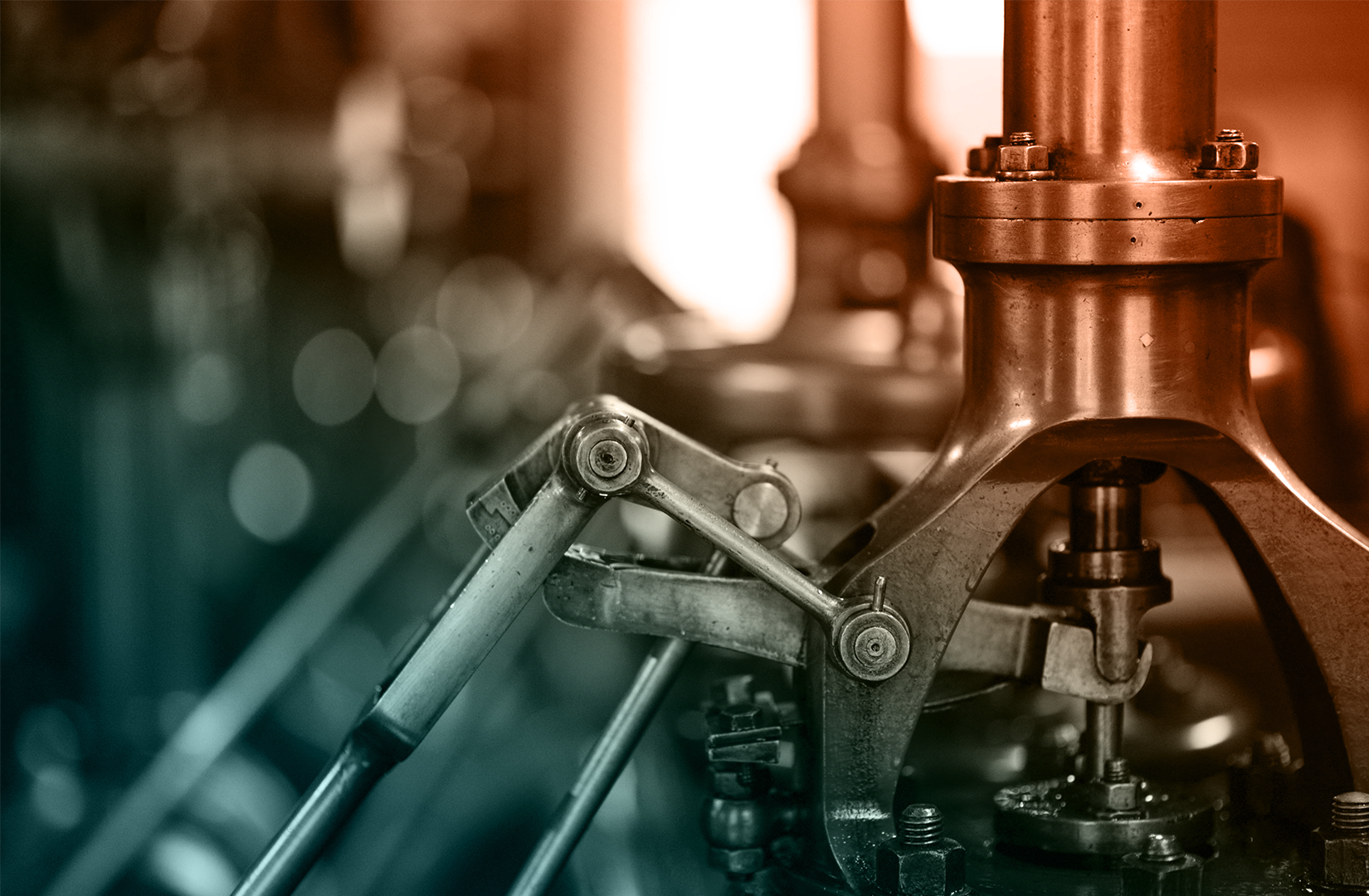
Materials Used in Isolation Gaskets
Isolation gaskets are made from a variety of materials, each chosen for its specific properties and suitability for different applications:
- Mica: Mica-based materials provide excellent high-temperature resistance and are often used in fire-safe gaskets.
- Phenolic Resin: Phenolic gaskets are widely used due to their excellent dielectric properties, making them effective at preventing electrical conductivity between flanges.
- Nitrile (NBR): Nitrile rubber is often used as the sealing element in isolation gaskets due to its good resistance to oils, fuels, and other chemicals.
- EPDM: EPDM rubber is chosen for its excellent resistance to water, steam, and weathering, making it ideal for water treatment and marine applications.
- PTFE: PTFE (Teflon) offers excellent chemical resistance and is used in gaskets that require a high degree of chemical inertness.
Canyon Components strives to meet all customer service requests. Feel free to contact Canyon Components engineering and let our knowledgeable staff help you design the perfect part for your needs.
High Temp vs. Fire Safe Isolation Gaskets
Isolation gaskets are available in both High Temp and Fire Safe versions, each designed to meet specific safety and performance requirements:
- High Temp Isolation Gaskets: These gaskets are engineered to withstand extremely high temperatures, making them suitable for use in environments where heat resistance is critical, such as in oil refineries and chemical plants. High Temp gaskets maintain their sealing integrity even at elevated temperatures, ensuring reliable performance in demanding conditions.
- Fire Safe Isolation Gaskets: Fire Safe gaskets are specifically designed to maintain their sealing capabilities during and after exposure to fire. These gaskets, often made with materials like mica, are essential in applications where fire safety is a priority, such as in offshore oil platforms and chemical processing facilities.
Isolation Gaskets Pros & Cons
Isolation gaskets are critical components in maintaining the integrity and safety of pipeline systems across various industries. With features such as corrosion prevention, electrical isolation, and adaptability to high-temperature and fire-safe requirements, these gaskets ensure reliable performance in demanding applications. While they offer many advantages, including long-term reliability and safety, it is important to consider their limitations, such as cost and installation complexity, when selecting the right gasket for your needs. Understanding the features, applications, and potential drawbacks of isolation gaskets, along with references to trusted brands, will help you make informed decisions to ensure optimal performance in your systems.
Canyon Components strives to meet all customer service requests. Feel free to contact Canyon Components engineering and let our knowledgeable staff help you design the perfect part for your needs.
Pros of Isolation Gaskets
Isolation gaskets offer several advantages that make them a preferred choice in critical sealing applications:
- Corrosion Prevention: By preventing galvanic corrosion, isolation gaskets extend the life of pipeline systems, reducing maintenance costs and downtime.
- Electrical Isolation: These gaskets effectively isolate sections of a pipeline, preventing the flow of electricity and protecting the system from electrical hazards.
- Adaptability: With a wide range of materials and designs available, isolation gaskets can be tailored to meet the specific needs of various industries and applications.
- Safety: Fire Safe gaskets provide an additional layer of protection in hazardous environments, ensuring that the sealing integrity is maintained even in the event of a fire.
- Reliability: Isolation gaskets are designed to provide long-lasting, reliable sealing performance, even in the most challenging environments.
Cons of Isolation Gaskets
While isolation gaskets offer many benefits, there are also some potential drawbacks to consider:
- Cost: High-performance isolation gaskets, particularly those that are Fire Safe or made from advanced materials, can be more expensive than standard gaskets.
- Installation Complexity: Proper installation is crucial for the effective performance of isolation gaskets. Incorrect installation can compromise the gasket's ability to isolate and seal, leading to potential failures.
- Material Limitations: The performance of isolation gaskets can be affected by the choice of material. For example, certain materials may not be suitable for highly corrosive environments or extreme temperatures.
- Pressure Limitations: While isolation gaskets are designed to withstand high pressures, they may not be suitable for applications that involve extremely high-pressure environments without proper reinforcement.
Back to Products Hub
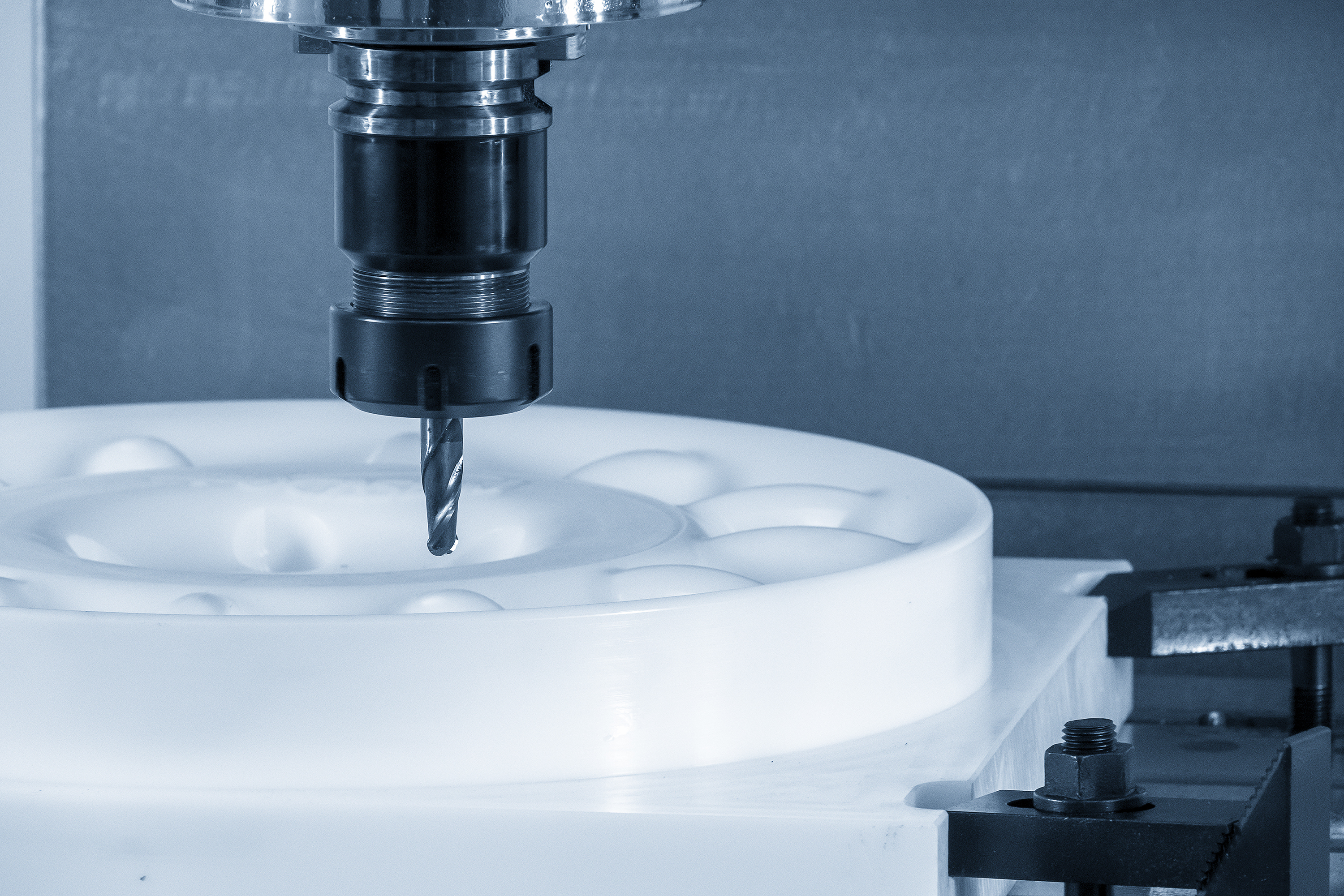
Get A Quote Now!
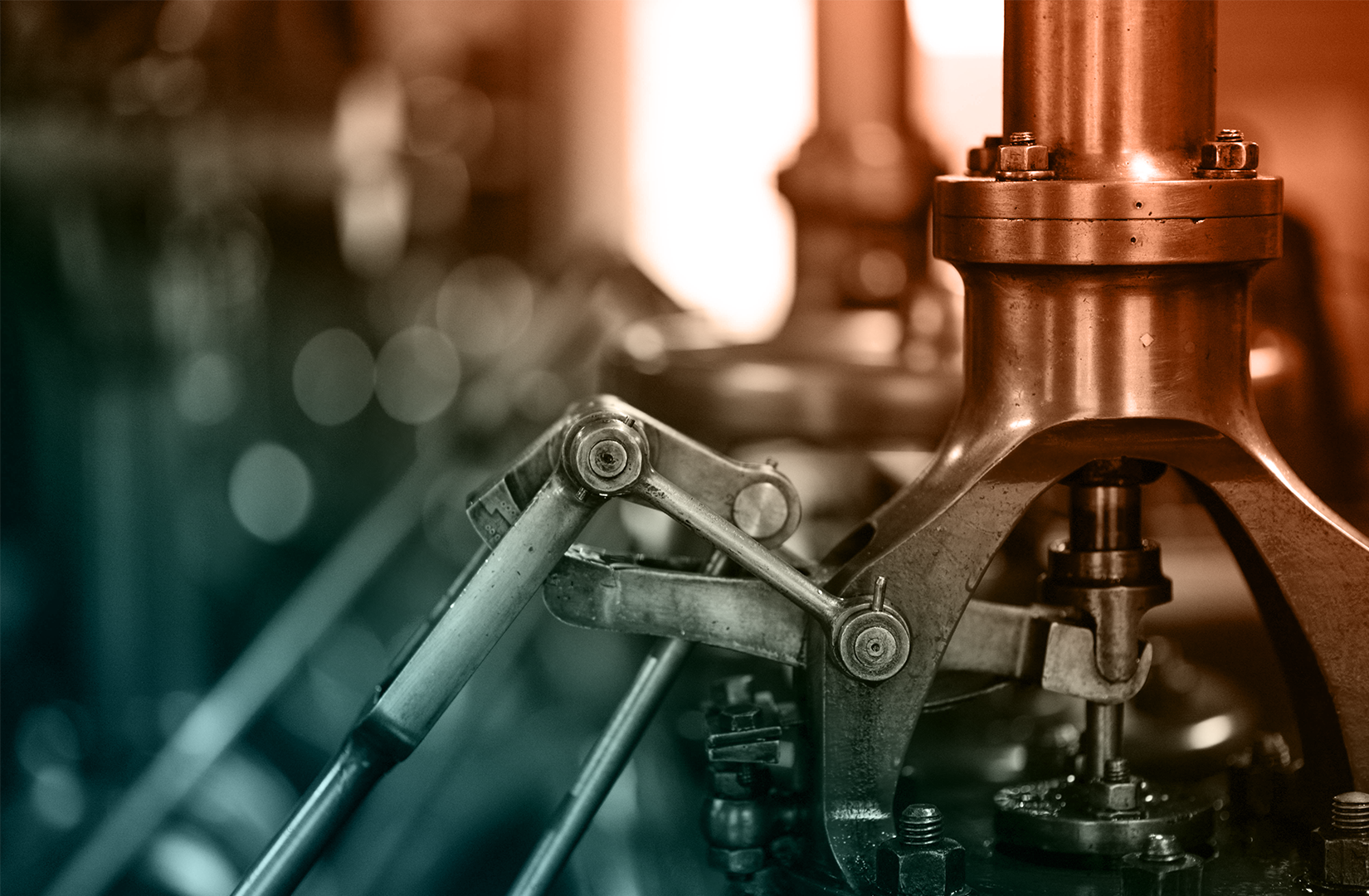