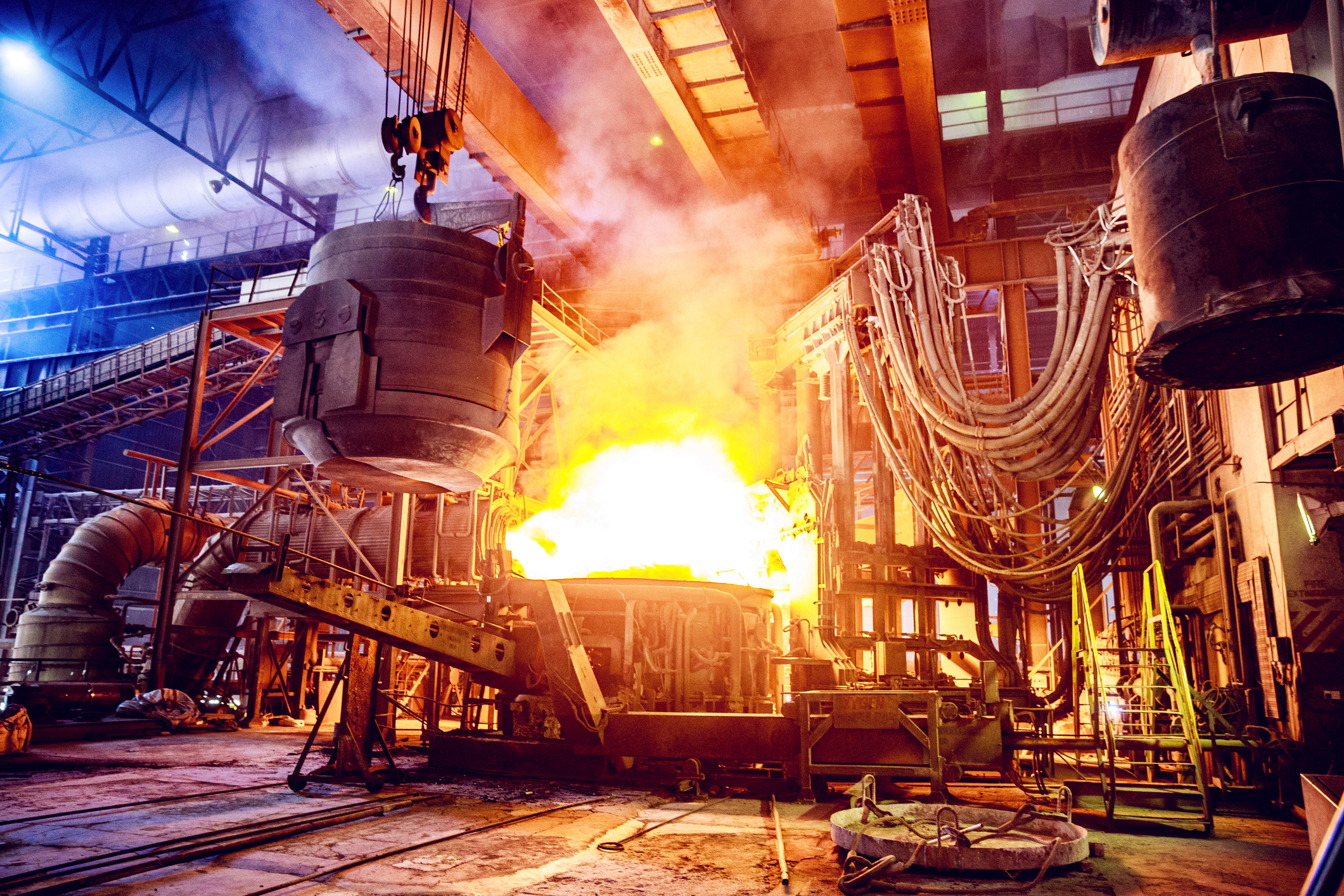
PS Plastic (Polystyrene) Selection Guide
Polystyrene (PS) is a versatile and widely used thermoplastic polymer known for its affordability, ease of processing, and insulation properties. In this web page, we will explore the different types of polystyrene, its numerous advantages and disadvantages, and the diverse industrial applications where polystyrene plays a significant role.
PS Plastic (Polystyrene) rapid manufacturing, & custom molded parts are available now!
Check with one of Canyon’s helpful product engineers for an expert material and manufacturing recommendation.
Common names include: PS Plastic (Polystyrene), HIPS (High Impact Polystyrene), Crystal PS, Trade Names: Styron®, Lustrex®, Styrolux®, NAS®
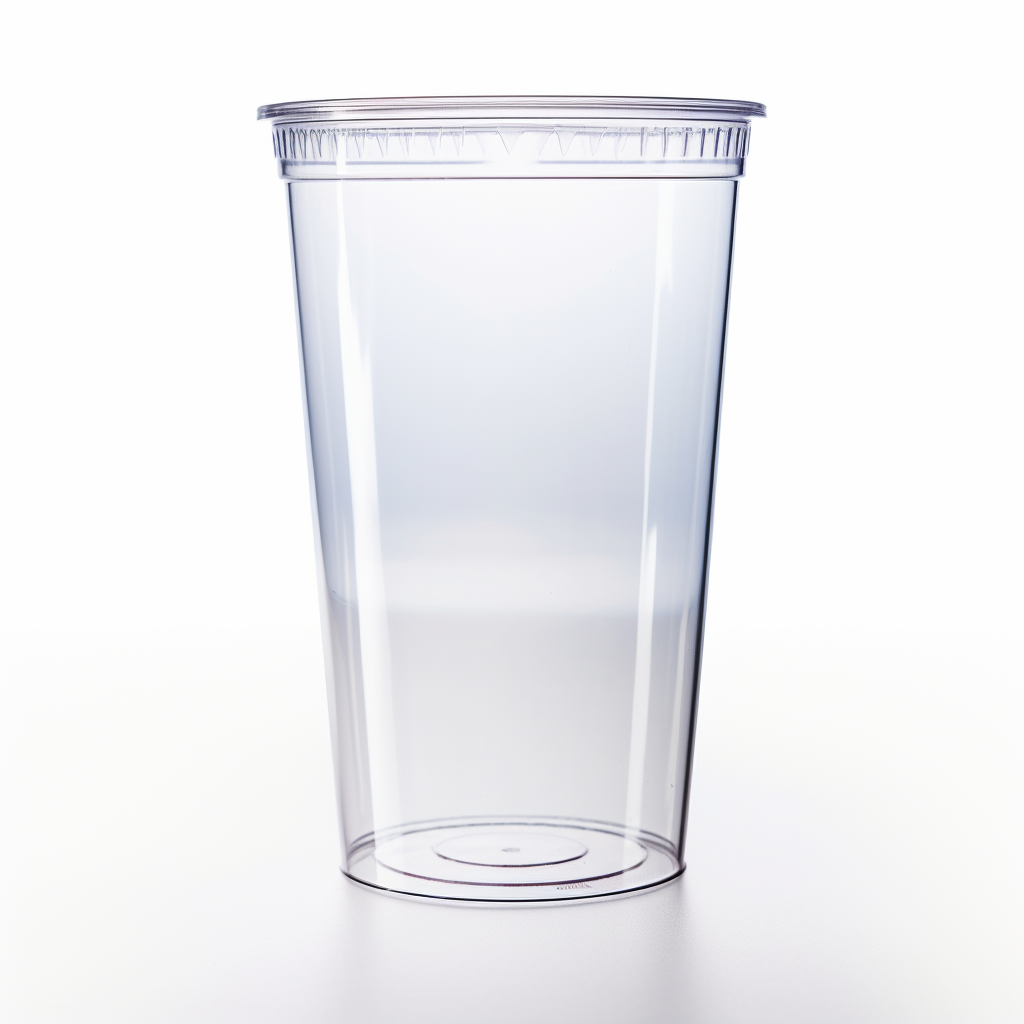
Advantages
- Affordability: Polystyrene is one of the most cost-effective plastics, making it a budget-friendly choice for many industries.
- Lightweight: It is lightweight, which is particularly advantageous in packaging and construction applications.
- Thermal Insulation: EPS and XPS foam variants provide excellent thermal insulation, helping to conserve energy in buildings.
- Ease of Processing: Polystyrene is easy to shape, mold, and cut, making it a versatile material for custom fabrication projects.
- Transparency: GPPS offers excellent transparency and optical clarity, making it suitable for applications where visibility is important.
- Chemical Resistance: Polystyrene is resistant to many chemicals, ensuring its stability in various environments.
Disadvantages
- Brittleness: GPPS can be brittle, making it susceptible to breakage, especially at low temperatures.
- Environmental Concerns: Polystyrene is not easily biodegradable and can persist in the environment for a long time. It is a source of environmental concern, especially in the form of single-use disposable items.
- Flammability: Polystyrene is flammable and can ignite easily. Flame-retardant additives are used to mitigate this issue in certain applications.
- Limited Heat Resistance: Polystyrene has a lower heat resistance compared to some other plastics, and it may soften or deform at elevated temperatures.
Common Applications of PS
- Medical Devices: Polystyrene is used in the production of various medical devices, including petri dishes and culture plates.
- Automotive: Polystyrene is used in automotive interior components like dashboard panels and trim due to its lightweight nature.
- Food Industry: Polystyrene is used for food packaging, including takeout containers, clamshell packaging, and disposable cutlery.
- Packaging: Polystyrene is commonly used for packaging materials, such as foam packaging for fragile items, food containers, and disposable cups and plates.
- Construction: EPS and XPS foam are used for thermal insulation in buildings, while HIPS is used for various construction applications like wall panels and decorative moldings.
- Electronics: Polystyrene is used for packaging electronic components due to its insulating properties.
- Toys and Novelties: HIPS is a popular choice for toy manufacturers due to its durability and ease of molding.
- Arts and Crafts: XPS foam is used in arts and crafts projects due to its rigidity and ease of cutting and shaping.
Please consult a Canyon Components Engineer about your specific application and we will use our decades of experience to formulate a solution that fits your need.
Types of PS
General Purpose Polystyrene (GPPS)
Known for its clarity and rigidity, GPPS is widely used in products like CD cases, laboratory ware, and various packaging materials. It's appreciated for its ease of processing, low cost, and good electrical properties, but lacks significant impact resistance.
High Impact Polystyrene (HIPS)
Enhanced with rubber additives for better durability, HIPS offers increased impact resistance compared to GPPS. Commonly used in appliance housings, toys, and automotive parts, it combines toughness with moldability and aesthetic appeal.
Expanded Polystyrene (EPS)
Lightweight and insulating, EPS is primarily used in packaging, disposable food containers, and insulation material. Its cellular structure provides excellent cushioning properties and thermal insulation, making it a popular choice for protective packaging and building applications.
Extruded Polystyrene (XPS)
Known for its strength, moisture resistance, and thermal insulation properties, XPS is commonly used in building insulation, models, and floatation devices. It's denser and more rigid than EPS, offering enhanced structural integrity.
Syndiotactic Polystyrene (SPS)
SPS is a high-performance variant with improved chemical and thermal resistance. It’s suitable for engineering applications, including electrical components and microwave cookware, where stability under heat and chemical exposure is necessary.
Atactic Polystyrene (aPS)
With a less ordered molecular structure, aPS is primarily used as an additive to improve the properties of other materials. It enhances the flexibility and impact resistance in blends, and is commonly used in the modification of bitumen for roofing and road construction.
Please consult a Canyon Components Engineer about your specific application and we will use our decades of experience to formulate a solution that fits your need.
Manufacturing Options for PS
Back to Plastics Hub
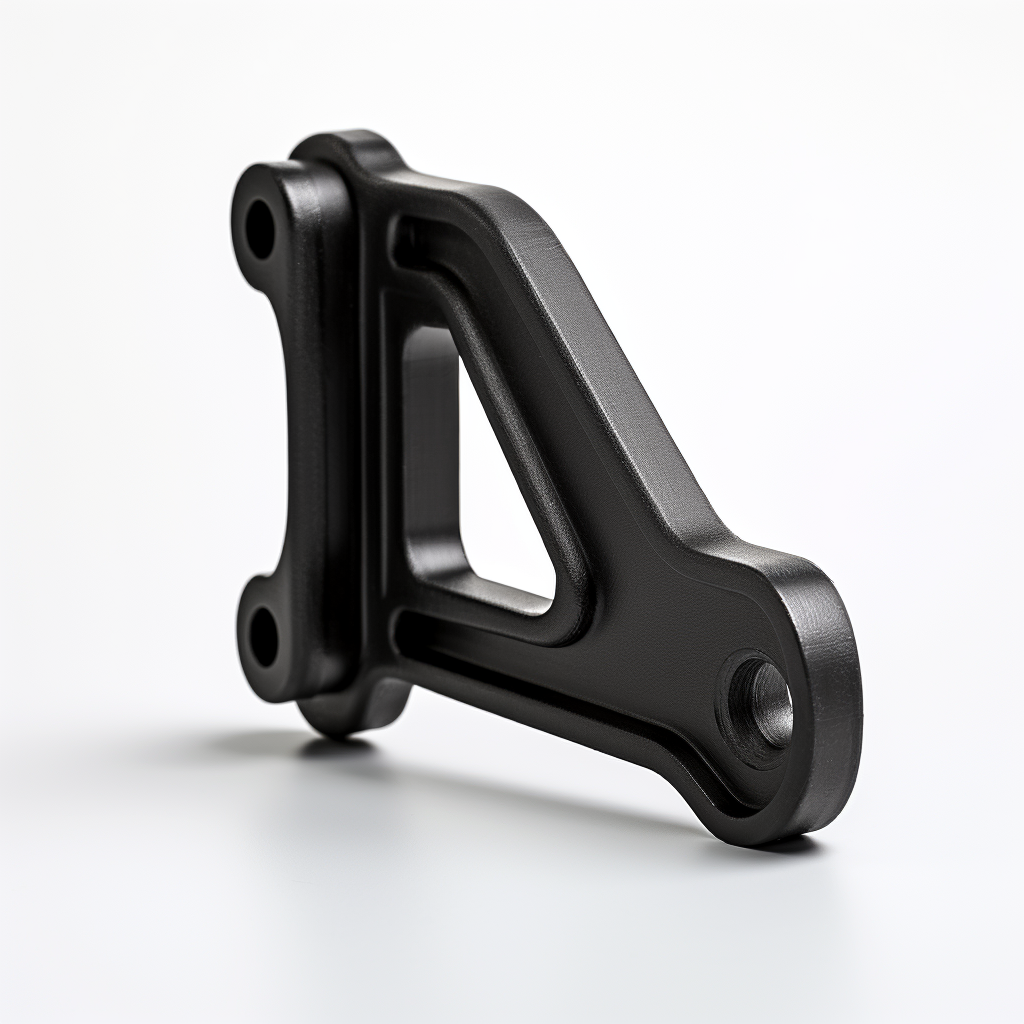
Get A Quote Now!
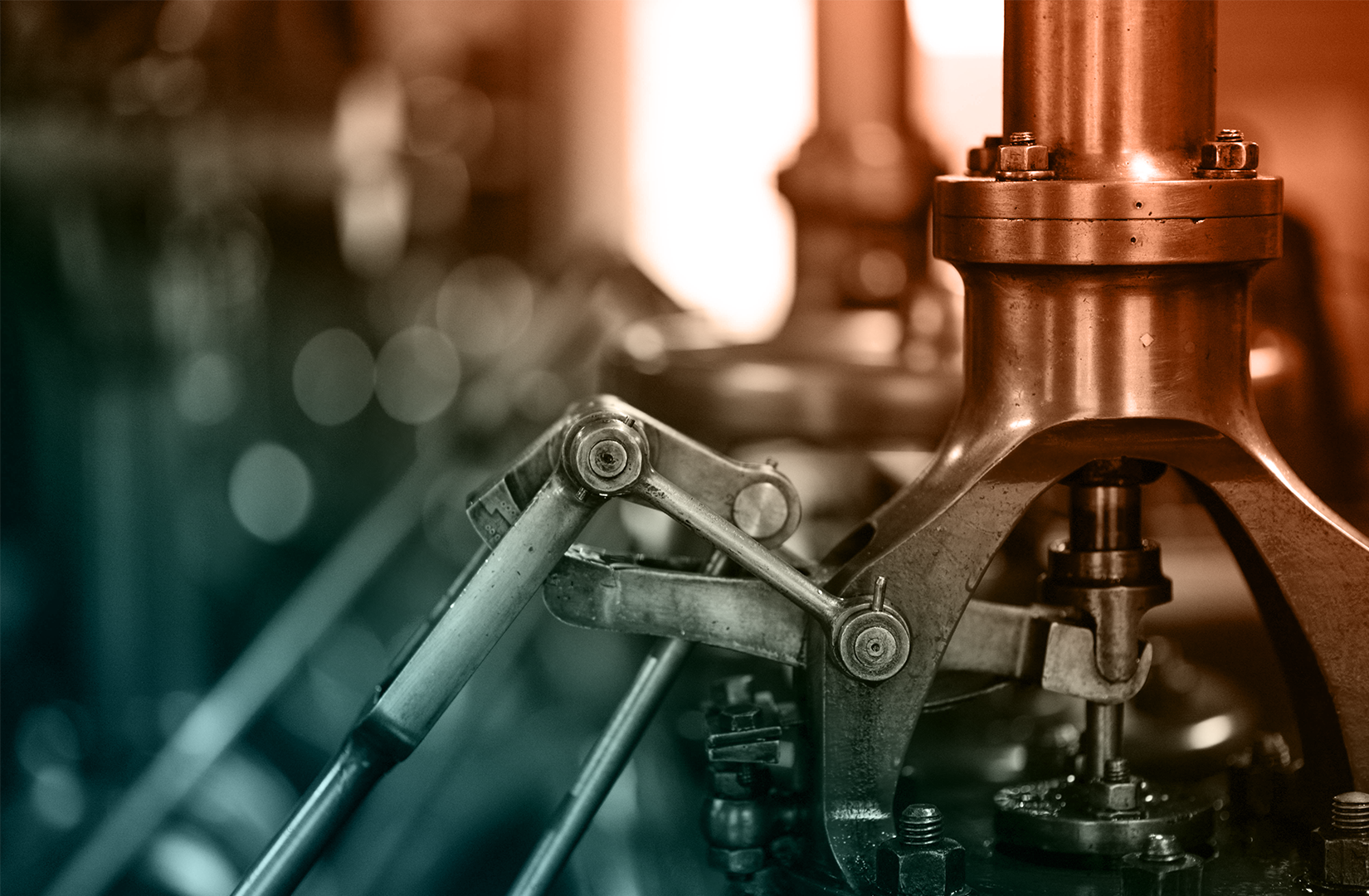