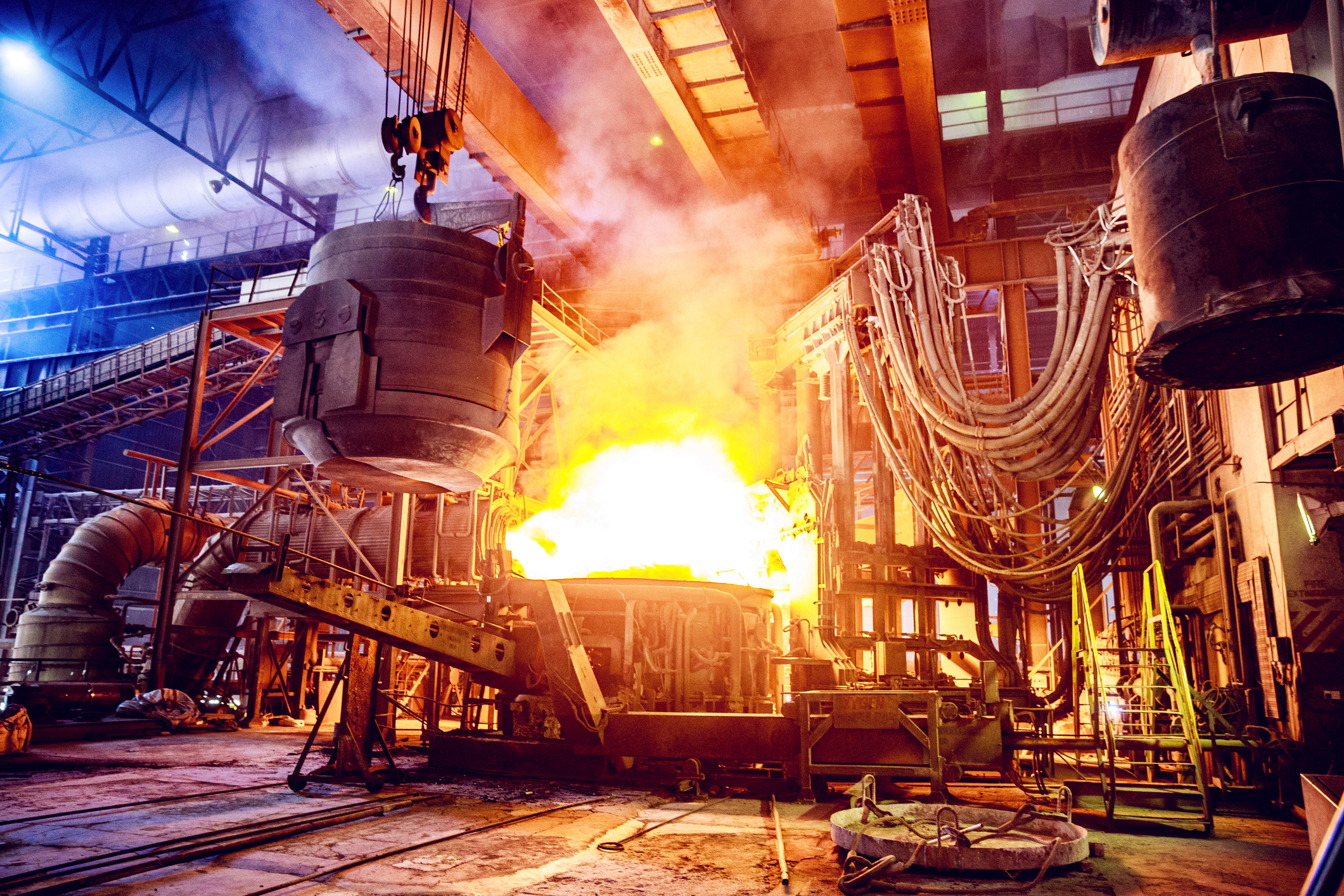
Parylene Coatings: Features, Applications, and Protective Benefits
Parylene coatings are ultra-thin, conformal coatings applied to various substrates to provide protection against moisture, chemicals, and environmental factors. Known for their excellent dielectric properties and biocompatibility, parylene coatings are widely used in industries ranging from electronics to medical devices. This guide covers the features, common applications, pros and cons of parylene coatings, with dedicated sections on their use for O-rings & elastomers, plastic & metal parts, and electronics.
Parylene coatings available for silicone, CanRez® FFKM and Kalrez® O-rings, gasket rapid manufacturing, & custom molded parts are available now!
Check with one of Canyon’s helpful product engineers for an expert material and manufacturing recommendation.
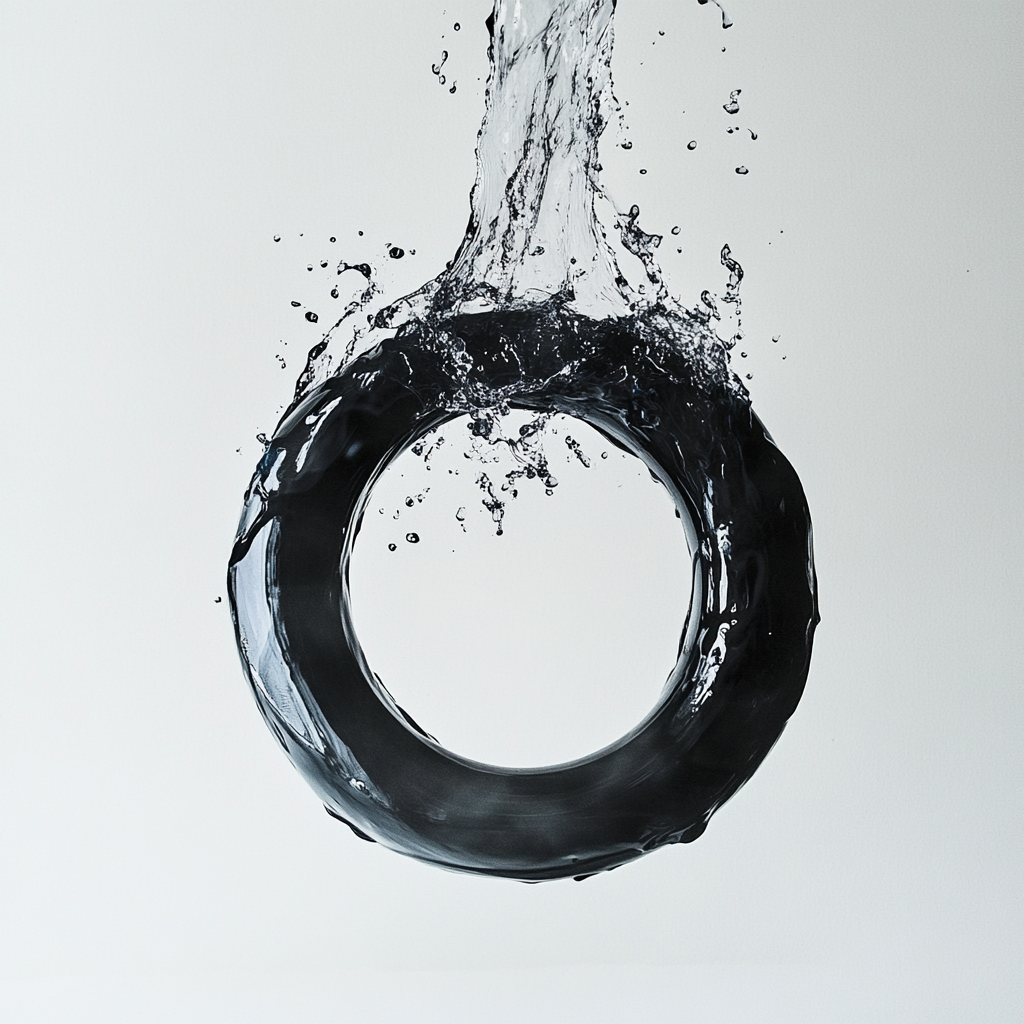
Features of Parylene Coatings
Parylene coatings offer several key features that make them ideal for protecting sensitive components and materials:
- Ultra-Thin Coating: Parylene coatings are applied in thicknesses ranging from a few microns to several tens of microns, providing a conformal coating that does not add significant weight or alter the dimensions of the substrate.
- Chemical Resistance: Parylene is highly resistant to a wide range of chemicals, making it suitable for use in harsh environments where exposure to corrosive substances is a concern.
- Moisture Barrier: Parylene provides an excellent moisture barrier, protecting sensitive components from water, humidity, and other environmental factors.
- Dielectric Properties: With its high dielectric strength, parylene is an excellent insulator, making it ideal for electronic applications where electrical insulation is required.
- Biocompatibility: Parylene is biocompatible and biostable, making it suitable for use in medical devices that come into contact with human tissue or fluids.
Common Applications of Parylene Coatings
Parylene coatings are used in a wide range of industries due to their protective and insulating properties. Common applications include:
- Medical Devices: Parylene is used to coat medical devices such as catheters, stents, and implants, providing a biocompatible, protective barrier that resists bodily fluids and reduces the risk of infection.
- Electronics: In the electronics industry, parylene coatings are applied to circuit boards, sensors, and other components to protect against moisture, dust, and chemicals, while also providing electrical insulation.
- Aerospace: Parylene is used in aerospace applications to protect sensitive components from harsh environmental conditions, including extreme temperatures, radiation, and corrosive chemicals.
- Automotive: In the automotive industry, parylene coatings are applied to electronic sensors, connectors, and other components to ensure reliability and longevity in challenging environments.
- Industrial Equipment: Parylene is used to coat various industrial components, such as seals, bearings, and valves, to protect them from wear, corrosion, and chemical exposure.
Please consult a Canyon Components Engineer about your specific application and we will use our decades of experience to formulate a solution that fits your need.
Get a Quote Now!
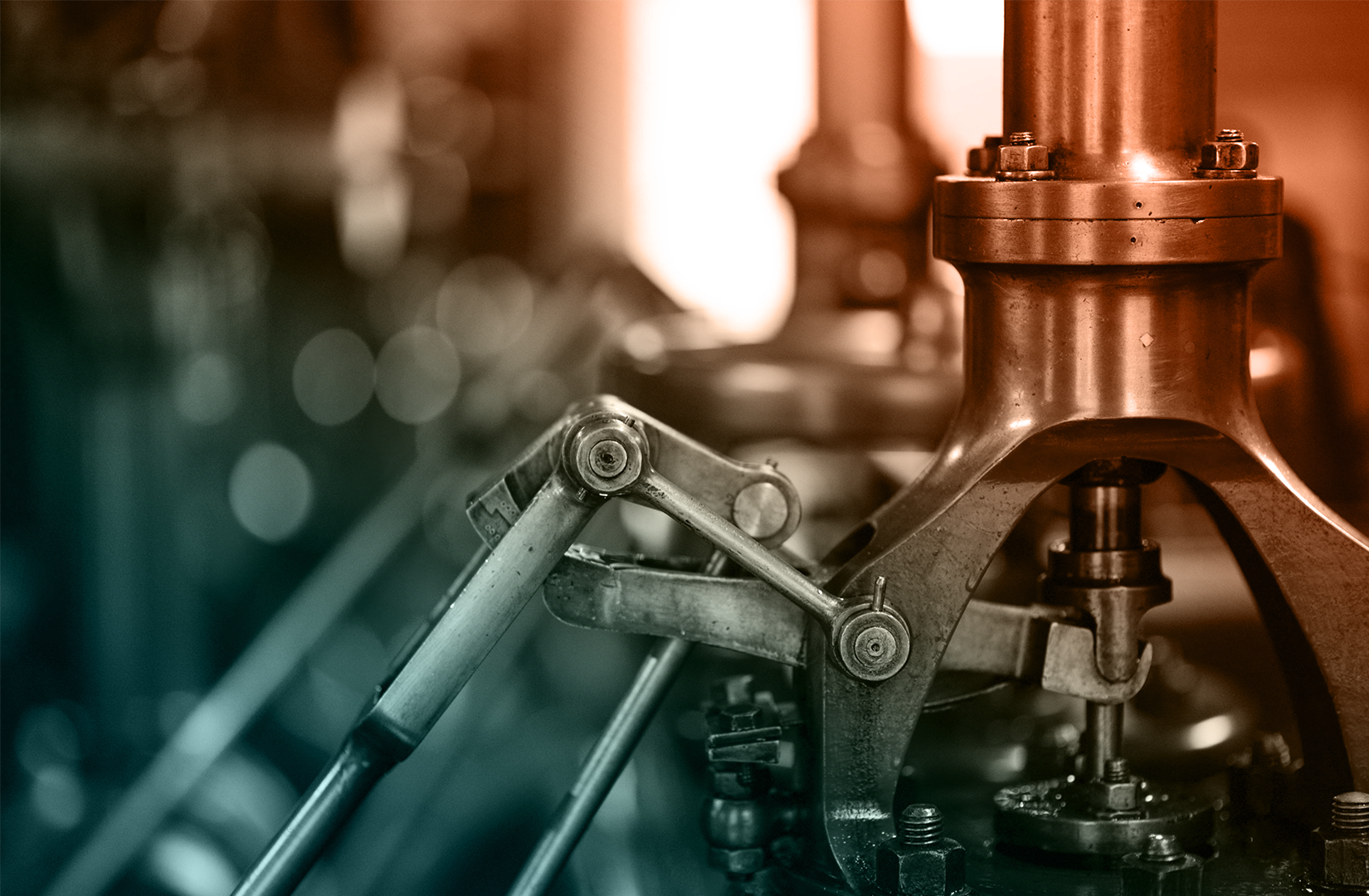
Parylene Coatings for O-Rings & Elastomers
Parylene coatings are particularly beneficial for O-rings and elastomers, providing enhanced protection and performance:
- Lowered Surface Friction: One of the significant advantages of applying parylene coatings to elastomers is the reduction of surface friction. This feature improves the performance of O-rings by reducing wear and tear, extending their service life, and enhancing their sealing capabilities in dynamic applications.
- Enhanced Chemical Resistance: Parylene coatings enhance the chemical resistance of elastomers, protecting them from aggressive chemicals, solvents, and gases that could otherwise degrade the material.
- Improved Durability: The coating helps protect elastomers from environmental factors such as UV radiation, ozone, and temperature fluctuations, further extending their lifespan.
- Uniform Coverage: Parylene provides a uniform coating that conforms to the shape of the elastomer, ensuring complete protection without compromising flexibility or performance.
Canyon Components strives to meet all customer service requests. Feel free to contact Canyon Components engineering and let our knowledgeable staff help you design the perfect part for your needs.
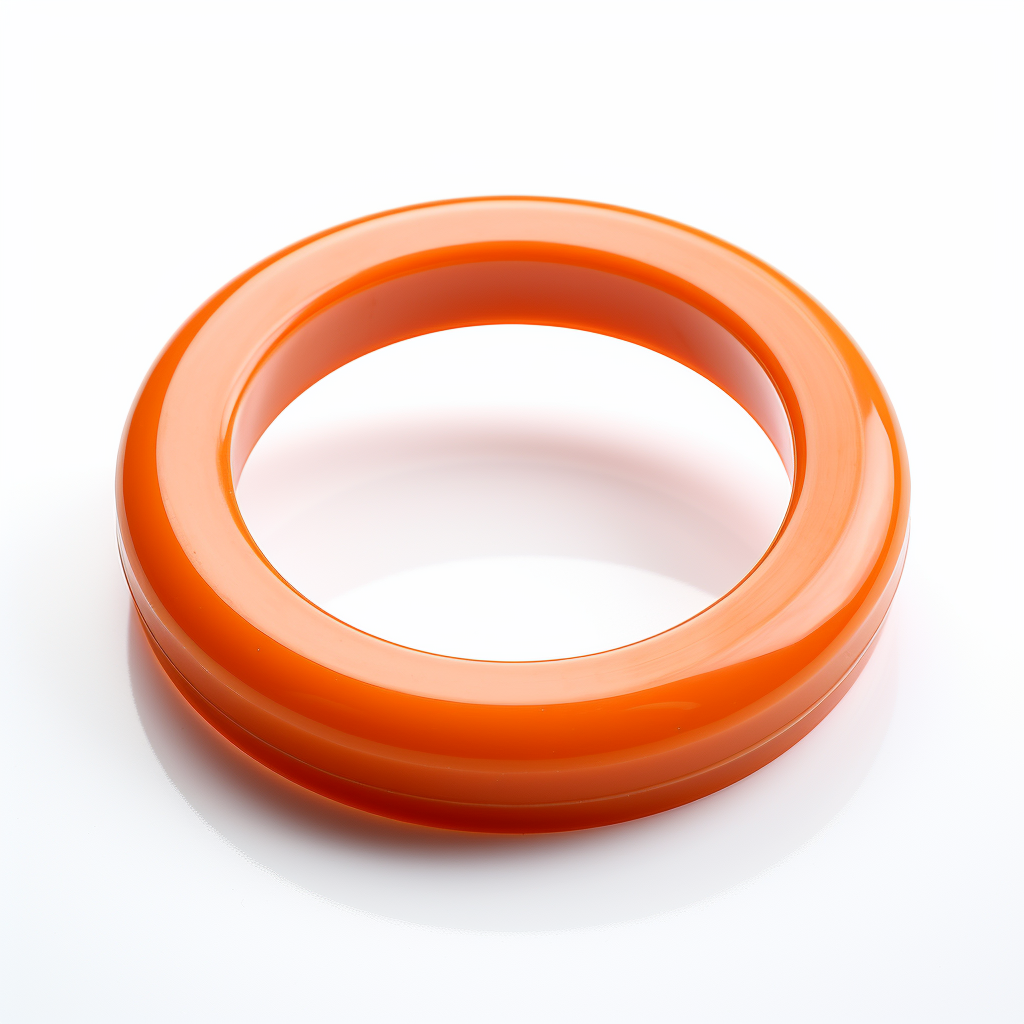
Parylene Coatings for Plastic & Metal Parts
Parylene coatings offer exceptional protection for plastic and metal parts used in various industries:
- Corrosion Protection: For metal parts, parylene provides a barrier against corrosion, protecting components from moisture, chemicals, and environmental exposure that could lead to degradation.
- Electrical Insulation: Parylene acts as an excellent electrical insulator, making it ideal for coating plastic and metal parts used in electronic and electrical applications.
- Enhanced Durability: By applying parylene to plastic parts, manufacturers can enhance the durability of components, protecting them from wear, abrasion, and chemical exposure.
- Adhesion and Compatibility: Parylene coatings adhere well to a wide range of substrates, including metals and plastics, providing a reliable protective layer that doesn’t peel or flake over time.
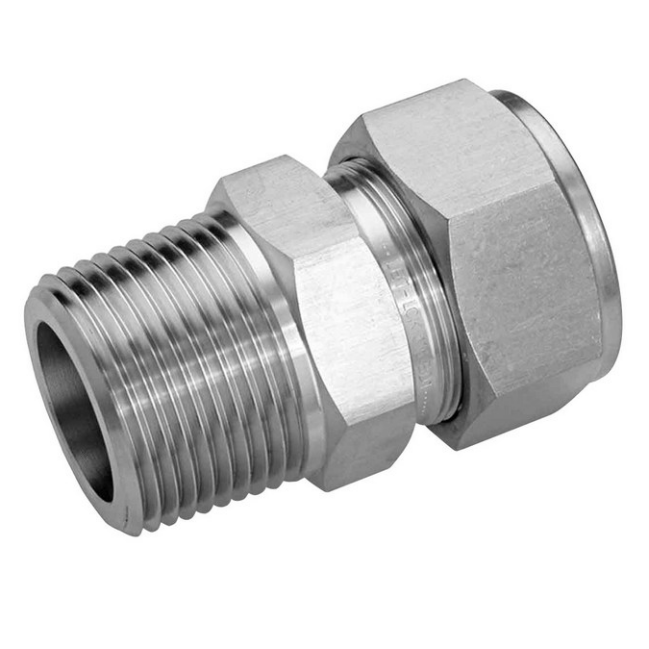
Parylene Coatings for Electronics
Parylene coatings are widely used in the electronics industry to protect delicate components from environmental damage:
- Moisture and Chemical Barrier: Parylene coatings provide a robust barrier against moisture, chemicals, and contaminants, protecting sensitive electronic components such as circuit boards, sensors, and microchips.
- Thermal Stability: The thermal stability of parylene ensures that electronic components remain protected even in environments with fluctuating temperatures.
- Minimized Corrosion: By protecting electronic components from moisture and corrosive elements, parylene coatings help prevent corrosion, which can lead to device failure.
- Enhanced Reliability: Parylene coatings increase the reliability and longevity of electronic devices by providing comprehensive protection against environmental factors.
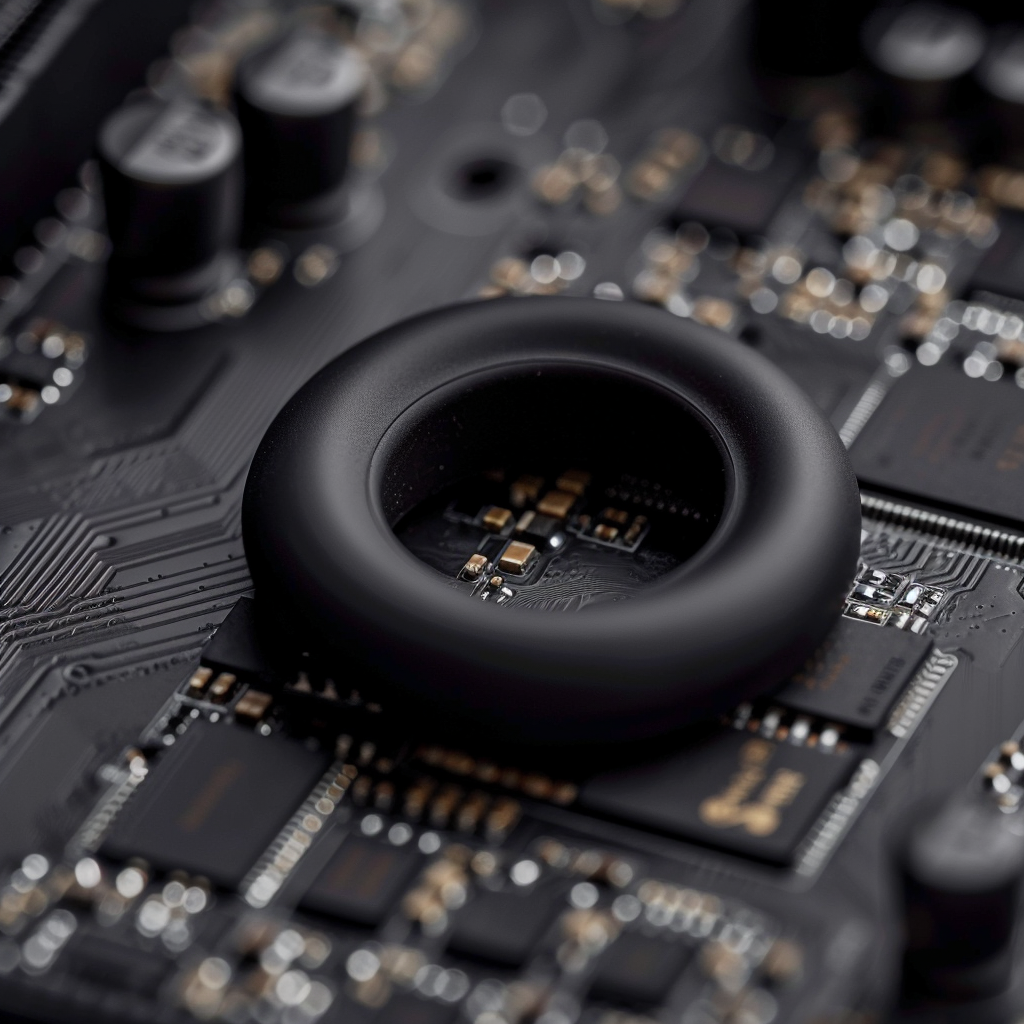
Parylene Coatings Pros & Cons
Parylene coatings offer a unique combination of protection, durability, and biocompatibility, making them an excellent choice for a wide range of applications, from medical devices to electronics and industrial components. Their ability to conform to complex geometries and provide a uniform, ultra-thin coating ensures that even the most sensitive components are fully protected. However, the potential challenges of cost, deposition time, and removal difficulty should be considered when selecting parylene coatings for specific applications. Understanding the features, applications, and potential drawbacks of parylene coatings will help you make informed decisions to ensure optimal performance in your systems.
Canyon Components strives to meet all customer service requests. Feel free to contact Canyon Components engineering and let our knowledgeable staff help you design the perfect part for your needs.
Pros of Parylene Coatings
Parylene coatings offer several advantages that make them a preferred choice for many applications:
- Excellent Protection: Parylene provides superior protection against moisture, chemicals, and environmental factors, ensuring the longevity and reliability of coated components.
- Conformal Coating: Parylene’s ability to conform to complex geometries ensures complete coverage and protection of intricate components.
- Biocompatibility: Parylene is safe for use in medical devices, offering a biocompatible coating that resists bodily fluids and reduces the risk of infection.
- Electrical Insulation: With its high dielectric strength, parylene is an ideal choice for insulating electronic components and preventing electrical shorts.
- Durability: Parylene coatings are long-lasting and resistant to wear, providing enduring protection in harsh environments.
Cons of Parylene Coatings
While parylene coatings offer many benefits, there are also some potential drawbacks to consider:
- Cost: Parylene coatings can be more expensive than other types of coatings, due to the specialized equipment and processes required for application.
- Deposition Process: The deposition process for parylene coatings is time-consuming, which may not be ideal for applications requiring quick turnaround times.
- Limited Thickness: While parylene coatings are effective at ultra-thin thicknesses, they may not be suitable for applications requiring thicker coatings for additional protection.
- Removal Difficulty: Parylene coatings are difficult to remove once applied, which can be a disadvantage in applications where rework or repairs may be necessary.
Back to Products Hub
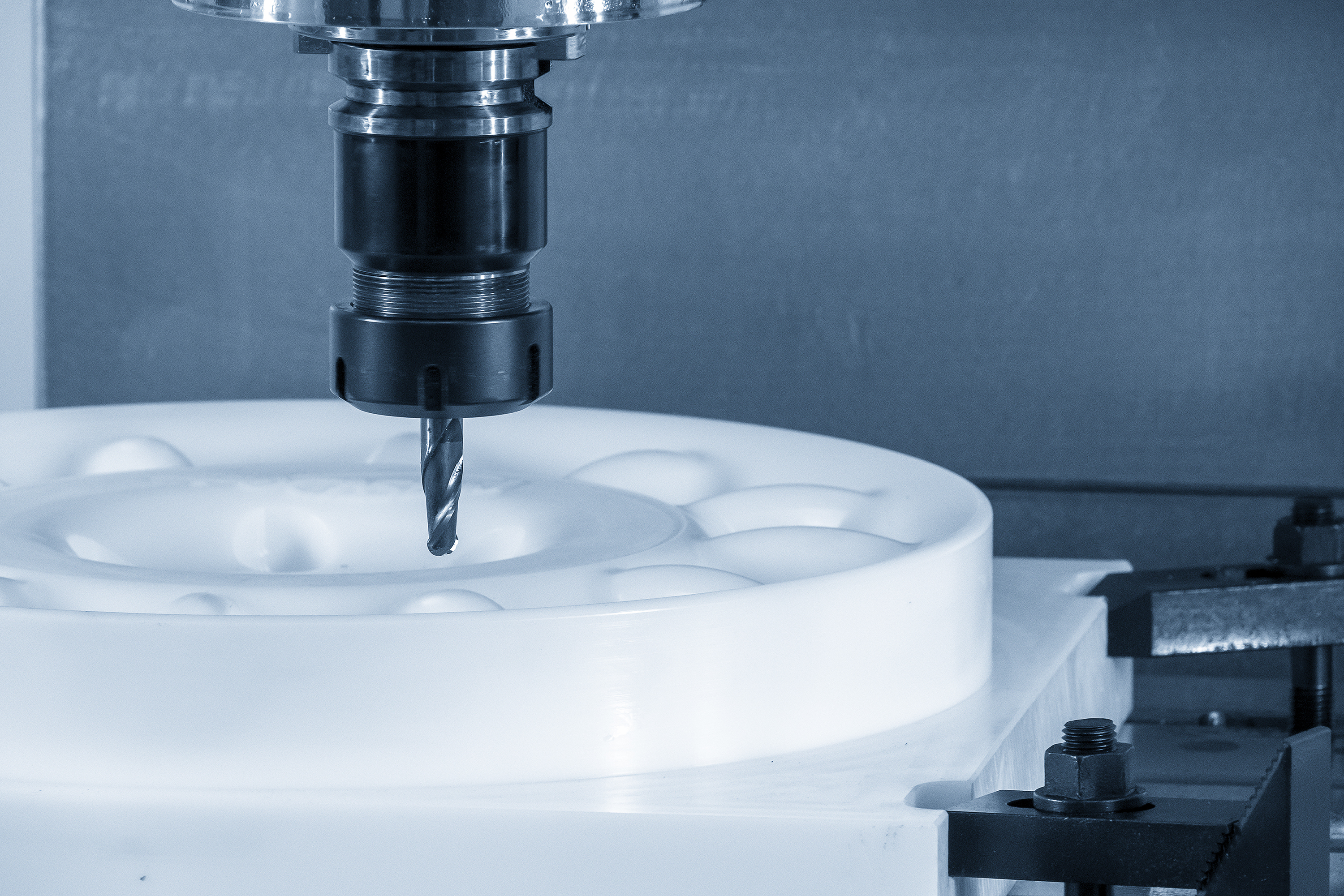
Get A Quote Now!
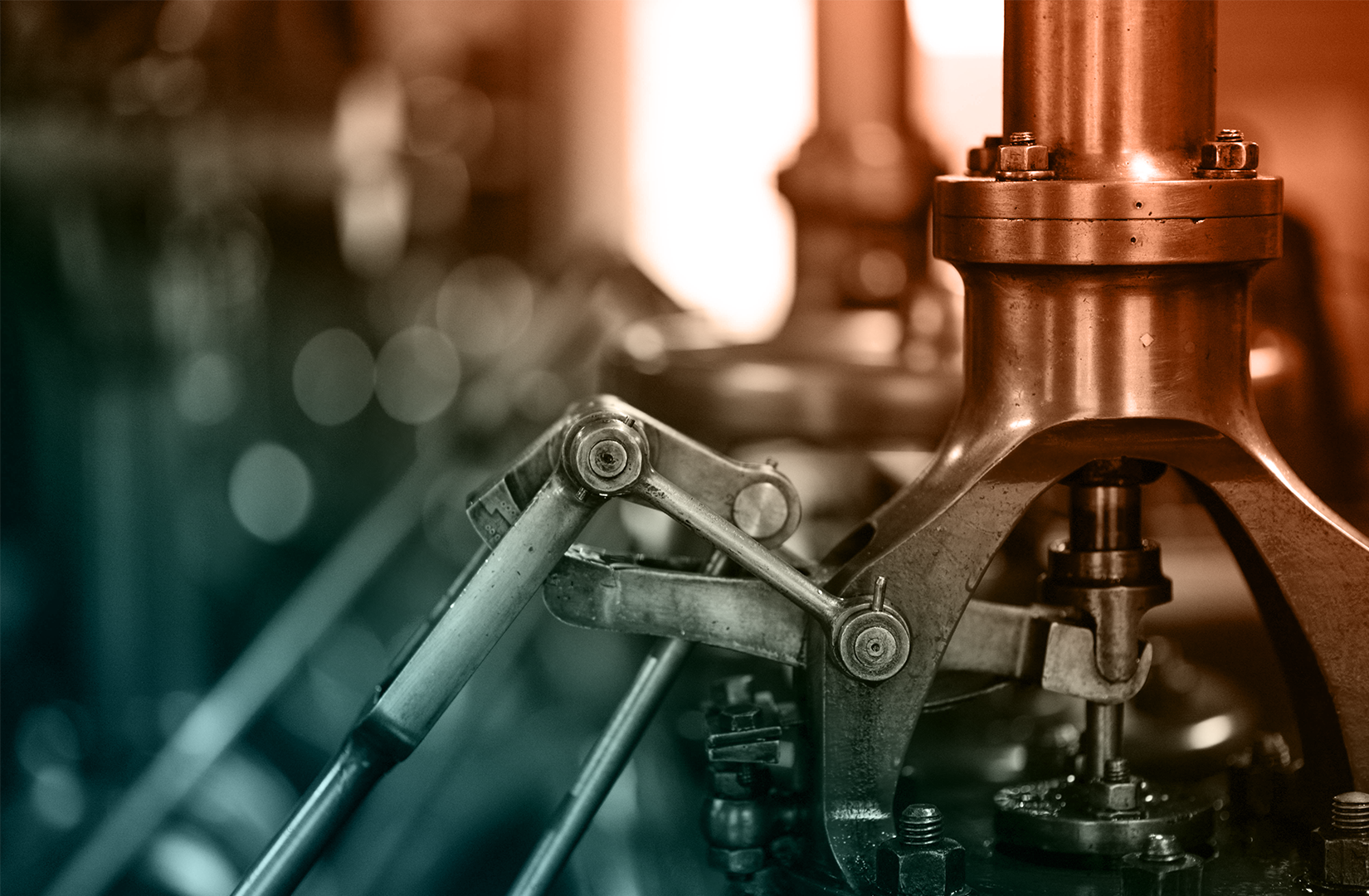