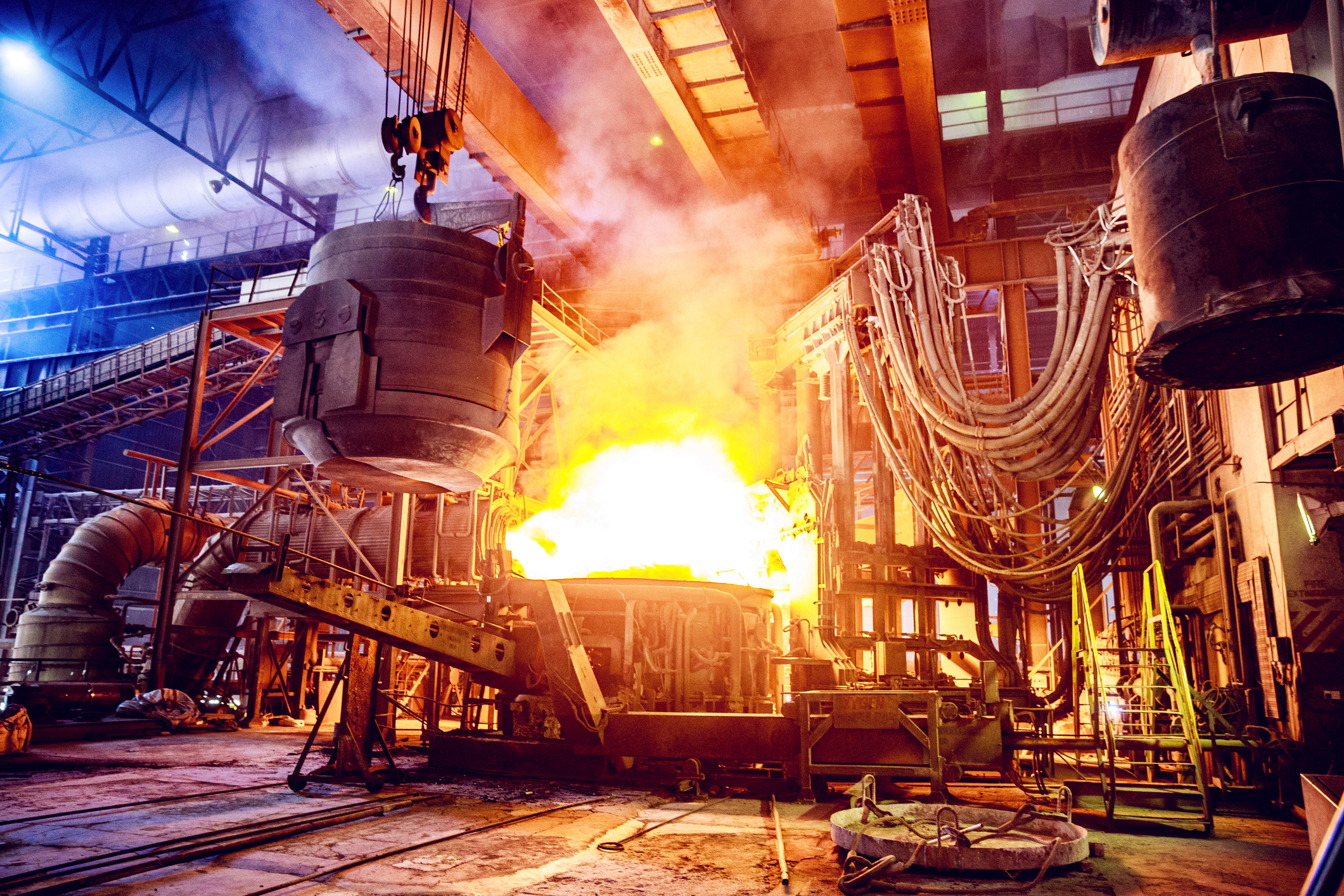
Plasma Nano-Coating for O-Rings, Elastomers, Plastics, & Metals
Plasma nano-coating is a cutting-edge surface treatment technology that applies a thin, uniform coating to O-rings, elastomers, plastics, and metals. This advanced coating process significantly enhances the surface properties of materials, offering benefits such as improved chemical resistance, reduced friction, and enhanced durability. This guide covers the features, common applications, and the pros and cons of plasma nano-coating, with a particular focus on how it lowers surface friction.
Plasma nano-coatings available for silicone, CanRez® FFKM and Kalrez® O-rings, gasket rapid manufacturing, & custom molded parts are available now!
Check with one of Canyon’s helpful product engineers for an expert material and manufacturing recommendation.
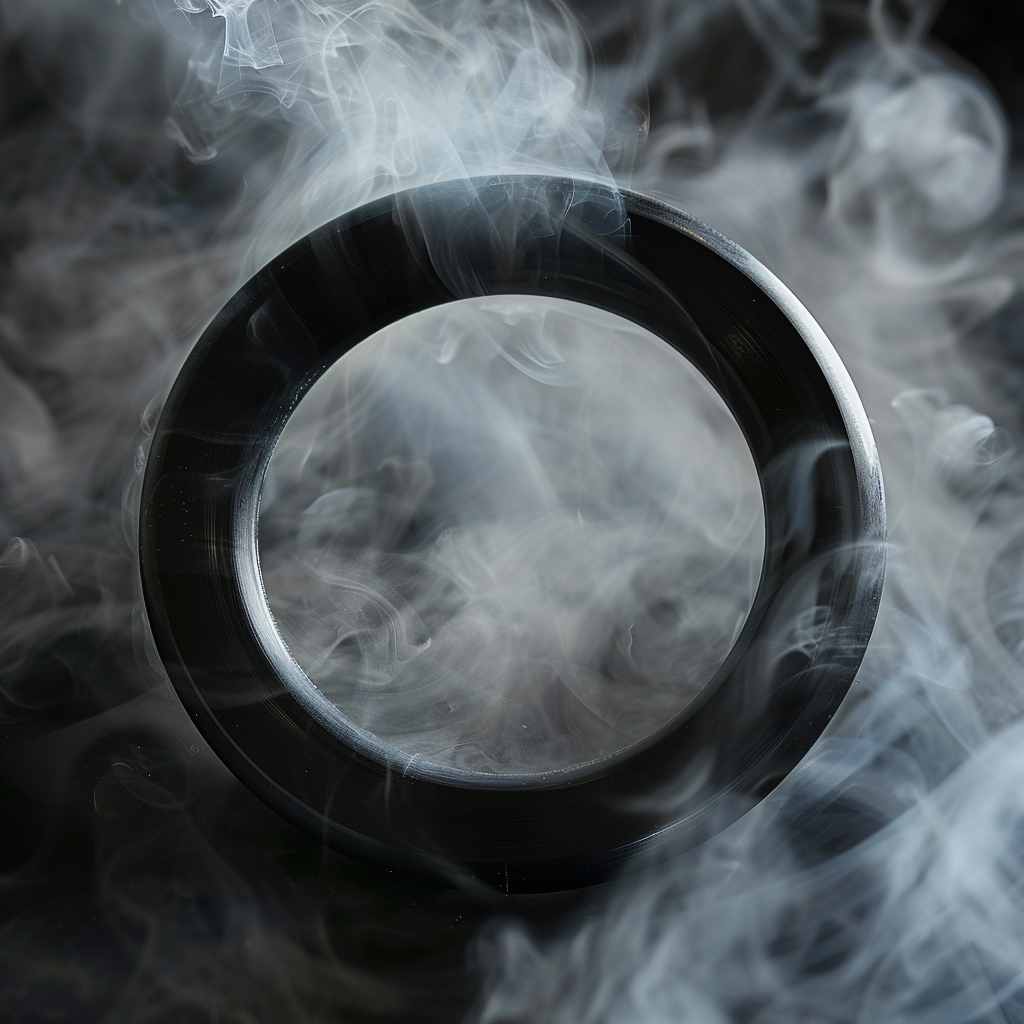
Features of Plasma Nano-Coating
Plasma nano-coating offers several key features that make it a valuable treatment for various materials:
- Reduced Surface Friction: One of the primary benefits of plasma nano-coating is the significant reduction in surface friction. This helps in minimizing wear and tear, particularly in dynamic applications where parts move relative to one another.
- Enhanced Chemical Resistance: The nano-coating creates a protective barrier that shields the underlying material from exposure to aggressive chemicals, solvents, and gases, extending the lifespan of the component.
- Uniform Coating: Plasma nano-coating is applied evenly across the surface of the material, ensuring consistent protection and performance without adding significant thickness.
- Improved Durability: The nano-coating increases the durability of the material by protecting it from environmental factors such as moisture, UV radiation, and temperature extremes.
- Biocompatibility: For medical and pharmaceutical applications, plasma nano-coatings can be tailored to be biocompatible, ensuring they meet the stringent requirements of these industries.
Common Applications of Plasma Nano-Coating
Plasma nano-coating is used in a wide range of industries due to its versatile benefits:
- Automotive: In the automotive industry, plasma nano-coating is applied to O-rings, gaskets, and metal components to reduce friction, improve fuel efficiency, and extend the life of seals and engine parts.
- Medical Devices: Plasma nano-coatings are used on medical elastomers and plastic components to improve biocompatibility, reduce friction, and prevent contamination, ensuring the safety and reliability of medical devices.
- Aerospace: The aerospace industry uses plasma nano-coating to protect metal and elastomeric components from extreme temperatures, corrosion, and wear, ensuring reliable performance in harsh environments.
- Electronics: In electronics, plasma nano-coating is applied to plastic and metal components to protect against moisture, dust, and chemical exposure, enhancing the durability and longevity of electronic devices.
- Industrial Machinery: Plasma nano-coating is used on seals, bearings, and other components in industrial machinery to reduce friction, minimize wear, and protect against chemical exposure.
Please consult a Canyon Components Engineer about your specific application and we will use our decades of experience to formulate a solution that fits your need.
Get a Quote Now!
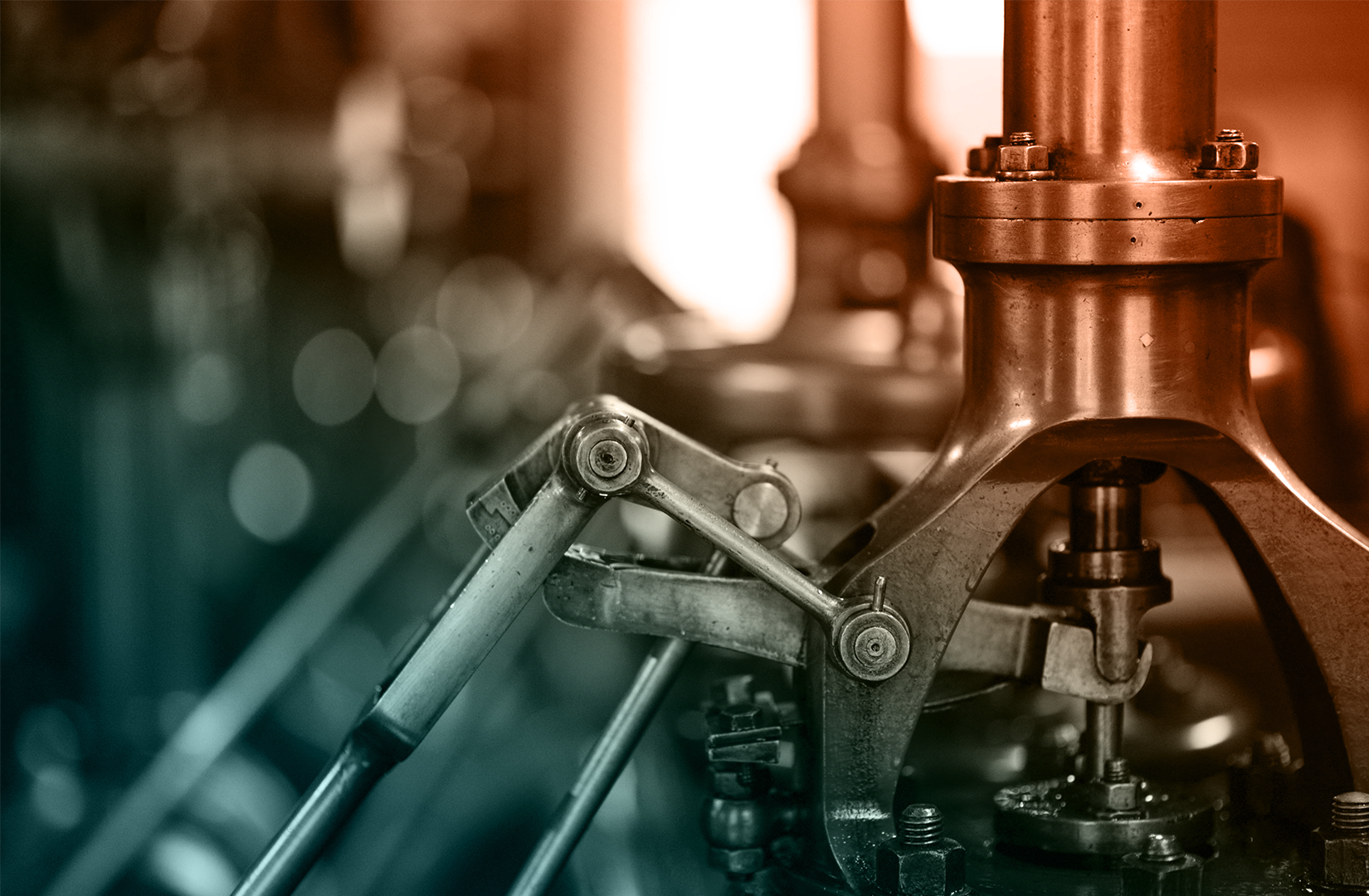
Plasma nano-coating Pros & Cons
Plasma nano-coating is a state-of-the-art surface treatment that offers significant benefits for O-rings, elastomers, plastics, and metals. By reducing surface friction, enhancing chemical resistance, and improving durability, this advanced coating process is ideal for applications in industries such as automotive, aerospace, medical devices, and electronics. While the process involves higher costs and requires specialized equipment, the enhanced performance and longevity provided by plasma nano-coating often justify the investment. Understanding the features, applications, and potential drawbacks of plasma nano-coating will help you make informed decisions to ensure optimal performance in your sealing and material solutions.
Canyon Components strives to meet all customer service requests. Feel free to contact Canyon Components engineering and let our knowledgeable staff help you design the perfect part for your needs.
Pros of Plasma Nano-Coating
Plasma nano-coating offers several advantages that make it an attractive option for enhancing the performance of various materials:
- Significant Friction Reduction: The coating drastically lowers surface friction, which reduces wear and extends the lifespan of components, especially in dynamic sealing applications.
- Enhanced Material Protection: Plasma nano-coating provides a robust barrier against chemicals, moisture, and environmental degradation, protecting the underlying material and improving overall durability.
- Versatile Application: Plasma nano-coating can be applied to a wide range of materials, including elastomers, plastics, and metals, making it a flexible solution for various industries.
- Uniform and Thin Coating: The application process ensures a uniform coating that does not significantly alter the dimensions of the component, making it ideal for precision parts.
- Environmentally Friendly: The plasma coating process is relatively eco-friendly, using less material and producing fewer emissions compared to traditional coating methods.
Cons of Plasma Nano-Coating
While plasma nano-coating offers many benefits, there are also some potential drawbacks to consider:
- Cost: Plasma nano-coating can be more expensive than traditional coating methods, which may not be justifiable for all applications, particularly those that do not require the advanced properties it provides.
- Specialized Equipment: The plasma coating process requires specialized equipment and expertise, which can increase production costs and lead times.
- Limited Thickness: While the thin nature of the coating is beneficial for many applications, it may not provide sufficient protection in environments requiring thicker barriers.
- Surface Preparation: Proper surface preparation is crucial for the success of plasma nano-coating, and any contaminants or irregularities on the surface can affect the coating's effectiveness.
Back to Products Hub
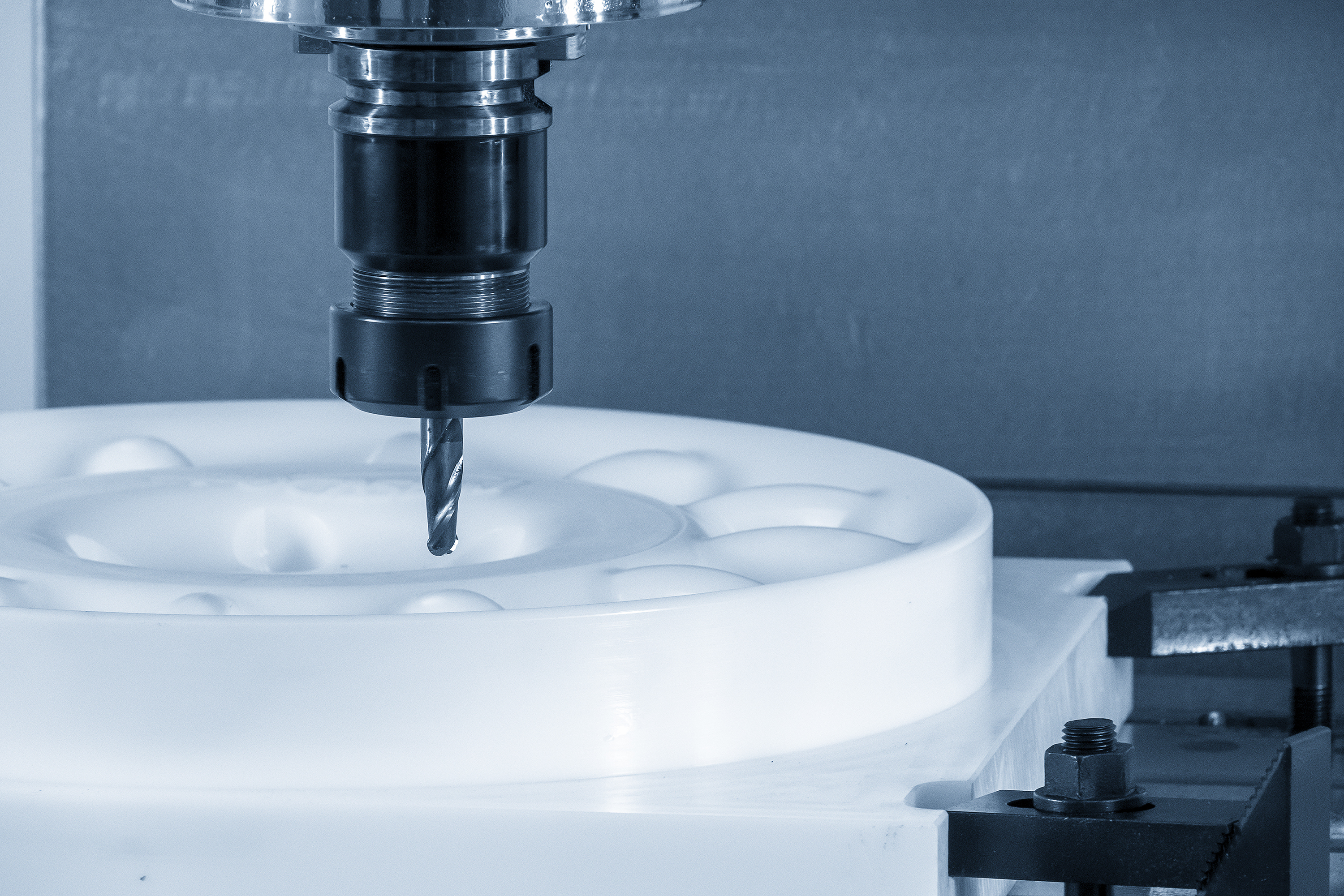
Get A Quote Now!
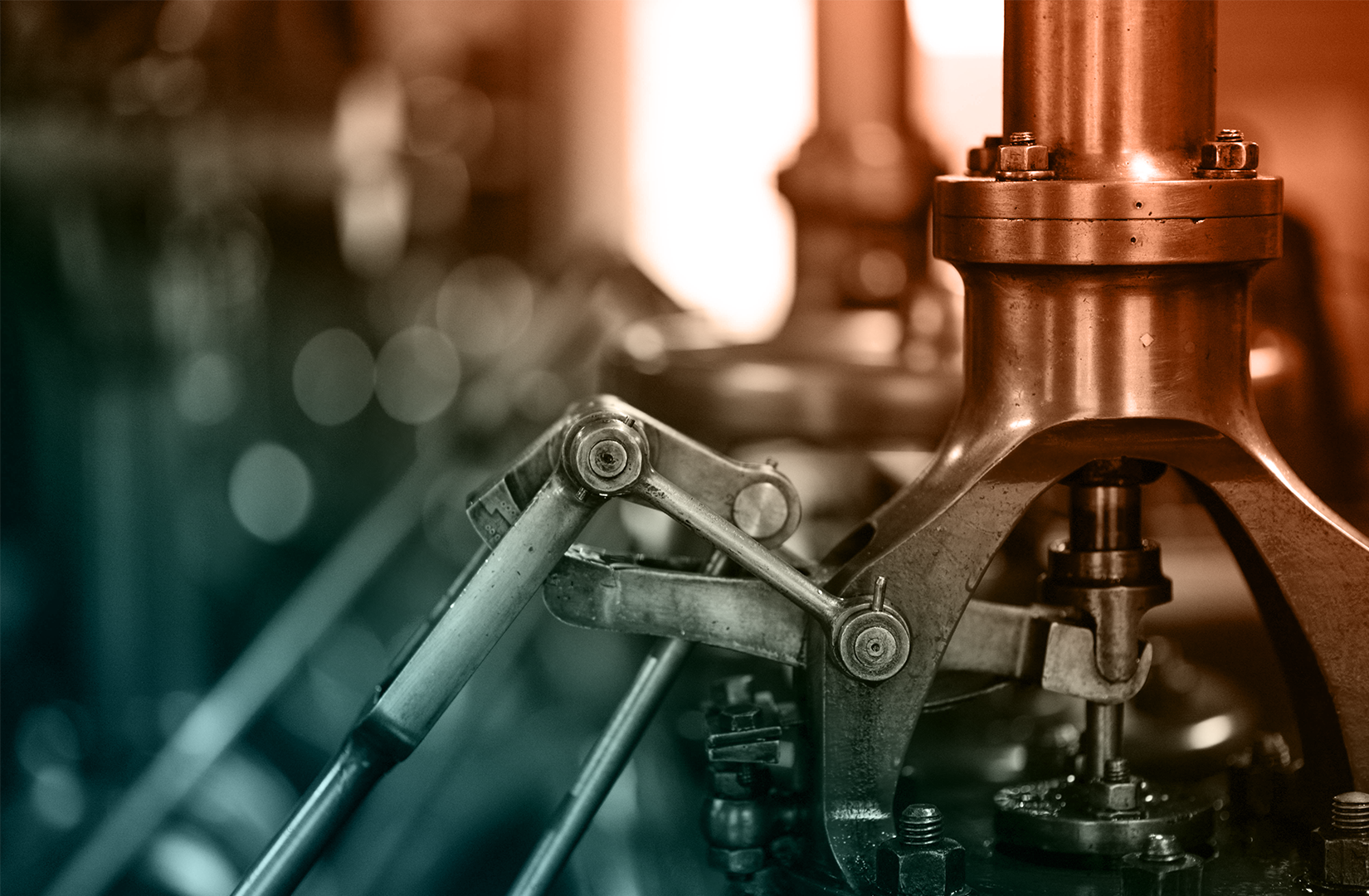