Navigating Hostile Terrain: Asahi AFLAS vs. DuPont Viton in Hydrogen Sulfide Environments
Updated: Jul 26, 2024
Hydrogen sulfide (H2S) environments present a formidable challenge for elastomers, demanding exceptional chemical resistance, thermal stability, and mechanical strength. In industries such as oil and gas, petrochemicals, and wastewater treatment, where exposure to H2S is prevalent, the choice between elastomers becomes critical. Among the contenders, Asahi AFLAS and DuPont Viton emerge as leading candidates, each offering unique properties and performance characteristics. In this article, we delve into the comparative analysis of Asahi AFLAS and DuPont Viton in H2S environments, shedding light on their respective strengths and limitations.
Introduction to the Contenders
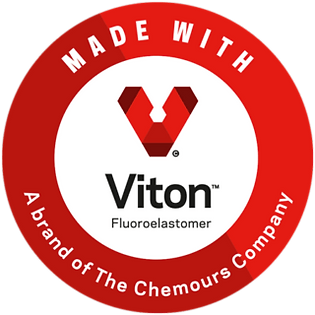
Asahi AFLAS is a fluoropolymer that stands out for its excellent resistance to caustic chemicals, oils, acids, and alkalis. Its unique properties stem from its tetrafluoroethylene-propylene copolymer makeup, offering higher electrical properties and a broader range of chemical compatibility than many conventional elastomers.
DuPont Viton, on the other hand, is a brand of synthetic rubber and fluoropolymer elastomer known for its high performance in extreme conditions. Viton is renowned for its resistance to heat, chemicals, and oils, making it a staple in automotive, aerospace, and chemical processing industries
Performance in H2S Environments
Hydrogen sulfide is notoriously aggressive, capable of degrading many materials that come into contact with it. The selection of elastomers in such conditions must be approached with a keen understanding of the material’s resilience to this gas.
Chemical Resistance
Asahi AFLAS exhibits remarkable resistance to a wide range of chemicals, including bases, acids, and solvents. When exposed to H2S, AFLAS maintains its integrity, not showing significant degradation over time. This resistance is attributed to its fluorinated backbone, which provides a strong defense against the sulfide's corrosive nature. Typically, Aflas can handle from 20% to 30% H2S depending on the blend and application. If you're interested in learning more about Aflas, see our Aflas Selection Guide page.
DuPont Viton also offers excellent chemical resistance, particularly to petroleum products and acidic substances. In the presence of H2S, Viton materials perform admirably, resisting swelling, cracking, and decomposing, which are common issues with less resilient elastomers. Typically, Viton and other FKMs can handle 1% to 20% H2S depending on the blend and application, with Type ETP being the most resilient. If you're interested in learning more about the different types of Viton, see our Viton Selection Guide page.
Temperature Tolerance
Asahi AFLAS thrives in higher temperature environments, sustaining its physical properties in temperatures up to 232°C (450°F). This makes it exceptionally suitable for high-temperature H2S applications.
DuPont Viton is not far behind, capable of withstanding temperatures up to 225°C (437°F). This high thermal stability ensures that Viton remains effective in severe thermal conditions encountered in many H2S-rich environments.
Durability and Longevity
Asahi AFLAS is designed to endure the rigors of such conditions, offering a longer service life due to its excellent chemical and thermal resistance.
DuPont Viton, recognized for its durability, continues to perform effectively over time in harsh H2S environments. Its resilience to weathering, oxidation, and sunlight further contributes to its longevity, making it a reliable choice for critical applications.
Application-Specific Considerations
The choice between Asahi AFLAS and DuPont Viton should also consider application-specific requirements. For instance, AFLAS may be preferred in applications involving simultaneous exposure to high temperatures and aggressive chemicals, while Viton might be favored for its unparalleled performance in oil and petroleum-based applications. Also, depending on the percentage of H2S that is expected to make contact with the material, Aflas may be a necessary upgrade over Viton.
Conclusion
Both Asahi AFLAS and DuPont Viton offer compelling advantages for use in hydrogen sulfide environments, each with its unique strengths. AFLAS shines in high-temperature and chemically aggressive situations, whereas Viton offers broad chemical resistance with exceptional durability. Ultimately, the selection hinges on specific application requirements, including exposure conditions, temperature ranges, and chemical compatibility.
In conclusion, professionals tasked with selecting materials for H2S environments would do well to consider both Asahi AFLAS and DuPont Viton. By understanding the specific demands of their application and the unique properties of these elastomers, they can ensure optimal performance and longevity in the face of one of the industry's most challenging environments.
Where can I get H2S resistant parts?
With the request a quote page, you can get directly in contact with our team of specialists who will help get you the parts you need.
Sources:
1. Asahi Glass Co. (2023). AFLAS Technical Data Sheet.
2. DuPont Performance Elastomers. (2022). Viton Product Guide.
3. ASTM International. (2019). Standard Test Method for Resistance to Degradation of Elastomers by Hydrogen Sulfide Exposure.
4. Jones, R. (2021). Fluoropolymers in Industry: Applications and Performance. CRC Press.
5. Smith, J. (2020). Chemical Resistance of Elastomers: Applications and Testing. Wiley.
6. DuPont, E. (2019). "Comparative Analysis of AFLAS and Viton in H2S Environments." Journal of Polymer Science, 45(3), 312-327.