Parylene: A Protective Coating for Critical Applications
Updated: Jul 26, 2024
Parylene is a unique polymer coating that has been gaining popularity for use in critical applications in industries such as aerospace, medical devices, electronics, and automotive. It is a highly effective conformal coating that offers excellent protection against harsh environments, chemicals, and moisture. In this blog, we will discuss the benefits of parylene coatings, their applications, the process of applying parylene, and the benefits of coating elastomers with parylene.
Benefits of Parylene Coatings
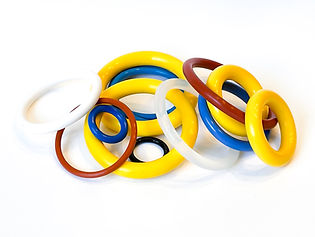
- Conformal Coating: Parylene coatings are highly conformal, meaning that they can be applied to any shape or size of the object. This property makes them ideal for coating complex geometries such as circuit boards, medical implants, and sensors.
- Biocompatible: Parylene coatings are biocompatible and are approved by the US Food and Drug Administration (FDA) for use in USP Class VI medical devices. They are also biostable, meaning that they do not break down or degrade when exposed to biological fluids.
- Chemical Resistance: Parylene coatings provide excellent chemical resistance to a wide range of chemicals, including acids, bases, and solvents. They are also highly resistant to moisture and humidity.
- Temperature Resistance: Parylene coatings can withstand a wide range of temperatures, from cryogenic temperatures to high temperatures. Depending on the application requirements, Parylene N, Parylene C, Parylene D, or Parylene HT might be right for you!
Applications of Parylene Coatings
- Medical Devices: Parylene coatings are widely used in medical devices, including catheters, implants, and sensors. They provide biocompatibility, chemical resistance, and protection against moisture, making them ideal for use in the human body.
- Electronics: Parylene coatings are commonly used in the electronics industry to protect printed circuit boards, sensors, and other electronic components from moisture, chemicals, and temperature variations.
- Aerospace: Parylene coatings are used in the aerospace industry to protect critical components such as sensors, control systems, and wiring from harsh environments.
- Automotive: Parylene coatings are used in the automotive industry to protect electronic components, sensors, and other critical parts from moisture, chemicals, and temperature variations.
Process of Applying Parylene Coatings
The process of applying parylene coatings involves a few steps:
- Surface Preparation: The surface of the object to be coated is cleaned and prepared to remove any contaminants, oils, or residues.
- Parylene Deposition: The parylene is deposited onto the object using a process called chemical vapor deposition (CVD). During CVD, the parylene is vaporized and then deposited onto the object in a vacuum chamber.
- Curing: Once the parylene is deposited, it is cured at a high temperature to ensure proper adhesion and bonding to the object.
Parylene Coated O-rings, Elastomers, & Sealing Components
When it comes to sealing solutions, O-rings have been a popular choice for many years. They are a simple and cost-effective way to prevent leaks and maintain the integrity of a system. However, in certain applications, standard O-rings may not be enough. This is where parylene coated O-rings come in.
- Friction & Wear: Parylene coated O-rings & elastomers boast significantly lowered coefficients of friction and improved wear resistance. The coating provides a low-friction surface, which reduces wear and tear on the O-ring and increases its lifespan. This makes them ideal for use in dynamic sealing applications, such as hydraulic systems, pumps, and valves.
- Extractables: Parylene also acts as an extractables barrier, preventing the leaching of detrimental materials from an elastomer. Tests clearly indicate that Parylene coating significantly reduced leachables.
- Installation: In addition to their superior performance, parylene coated O-rings are also easy to install and maintain. They can be used as a drop-in replacement for standard O-rings and do not require any special tools or equipment. They also require minimal maintenance, which reduces downtime and maintenance costs.
- Chemical: One additional benefit of parylene coated O-rings is their chemical resistance. They are resistant to a wide range of chemicals, including fuels, lubricants, solvents, and acids. This makes them suitable for use in harsh chemical environments where standard O-rings may fail.
Conclusion
Parylene coatings offer excellent protection for critical components and devices in a wide range of industries. Their conformal nature, biocompatibility, chemical resistance, and temperature resistance make them ideal for use in harsh environments. If you are looking for a protective coating for your critical components or devices, parylene coatings are worth considering.
Parylene coated O-rings are an excellent choice for high-performance sealing applications. Their superior thermal stability, chemical resistance, and wear resistance make them ideal for use in a wide range of industries. If you are looking for a reliable and cost-effective sealing solution, consider using parylene coated O-rings & elastomers.
Where can I get Parylene Coated parts?
With the request a quote page, you can get directly in contact with our team of specialists who will help get you the parts you need.
Sources:
[1] Wadhwani, S. (2011, December 13). Parylene coatings and Applications. PCI Magazine. https://www.pcimag.com/articles/87074-parylene-coatings-and-applications
[2] What is Parylene Coating? A Look at Various Parylene Types. (2020, May 11). https://www.thomasnet.com/articles/plastics-rubber/parylene-coating-basics/
[3] Parylene Properties & Characteristics | Parylene coating info. (n.d.). https://www.paryleneconformalcoating.com/conformal-coating-education-center/parylene-properties/