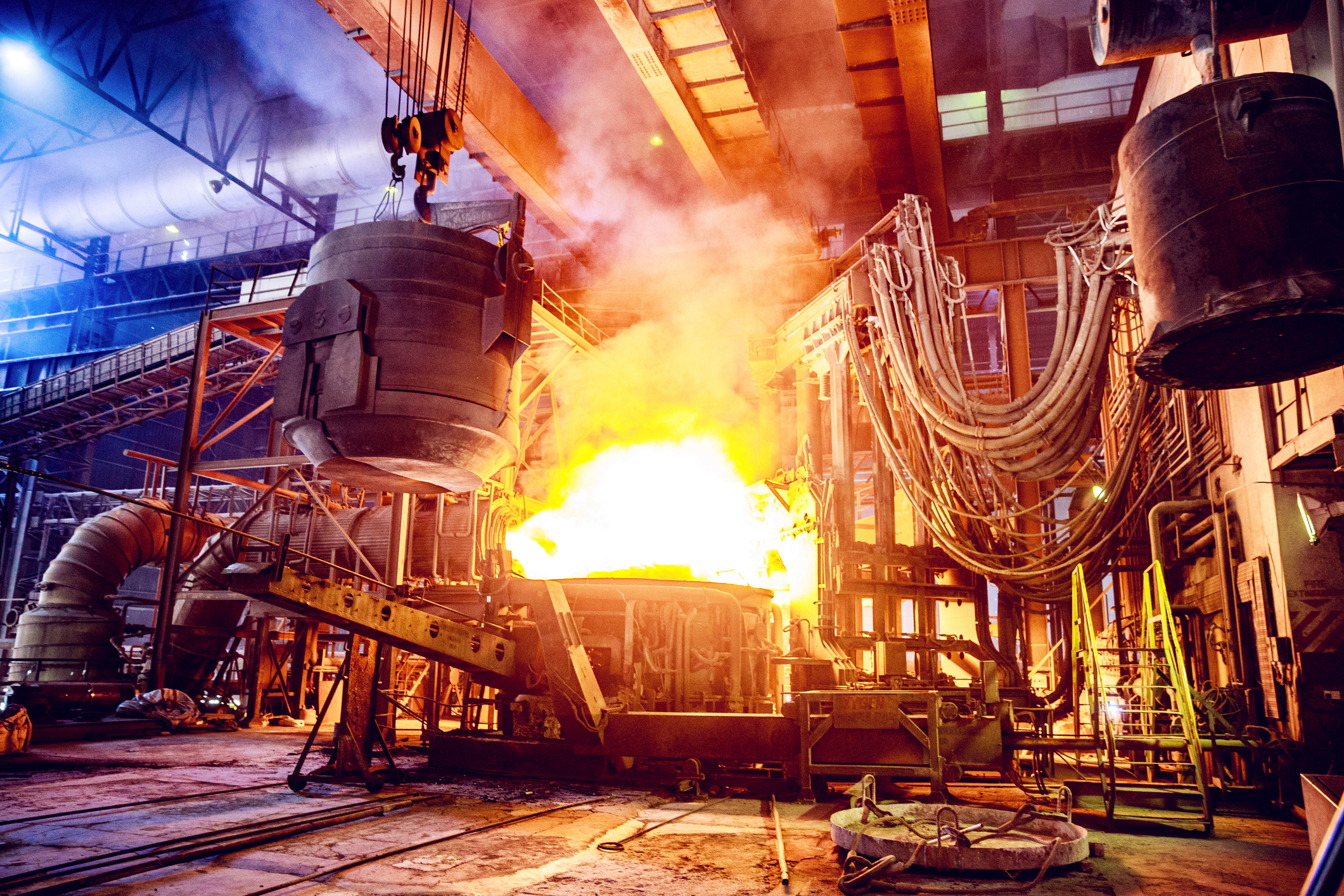
Shelf Life of Elastomers for O-Ring and Gasket Production
The shelf life of elastomers used in O-ring and gasket production is a critical factor that determines their long-term performance, reliability, and functionality. Proper storage and adherence to shelf life guidelines ensure that elastomeric materials maintain their properties, such as flexibility, elasticity, and sealing capability, over time. This guide explores the shelf life of various elastomers, with a focus on the SAE-ARP5316 standard, which provides comprehensive guidelines for storing and handling elastomeric components to maximize their longevity.
If you need additional context or have questions, feel free to get in touch with our engineers.
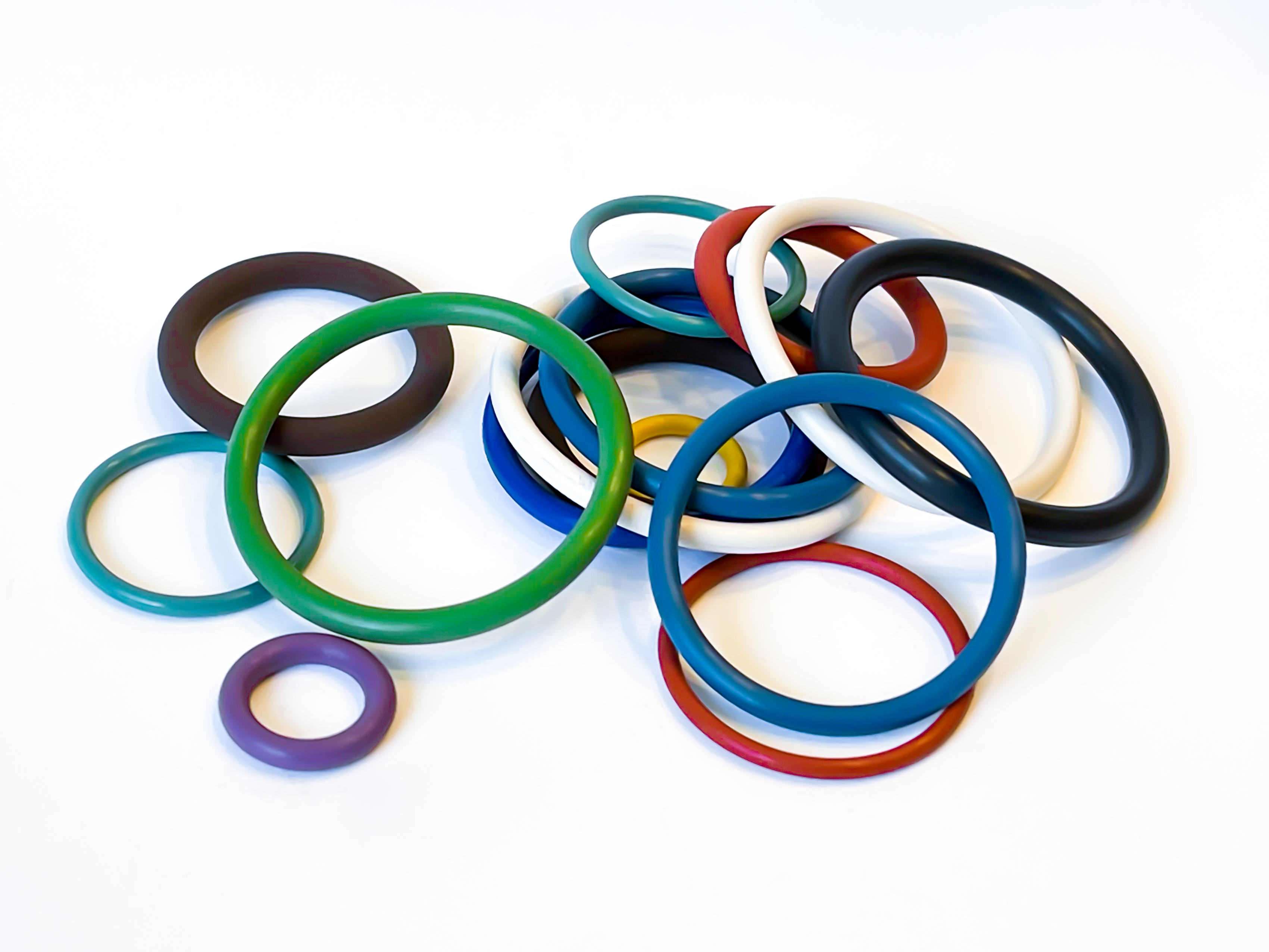
SAE-ARP5316: Shelf Life Guidelines
SAE-ARP5316 is the industry-standard document that outlines the recommended shelf life for elastomeric seals, such as O-rings and gaskets, used in aerospace, automotive, and industrial applications. It provides clear guidelines on how long different types of elastomeric materials can be stored before their properties begin to degrade. The standard aims to ensure that seals remain functional, preventing potential failures in critical applications.
According to SAE-ARP5316, the shelf life of elastomeric materials is determined based on factors such as polymer type, storage conditions, and the age of the product. The standard categorizes elastomers into various groups, each with a specified shelf life, ranging from 5 to 20 years or more, depending on the material. It also provides guidelines on how to identify, store, and handle elastomers to ensure they retain their performance characteristics.
- Identification: Elastomeric components should be labeled with the date of manufacture and batch number, making it easy to track their shelf life.
- Inspection and Testing: Regular inspection is recommended to check for signs of degradation, such as cracking, hardening, or discoloration.
- Revalidation: In cases where elastomeric components exceed their recommended shelf life, revalidation testing can be performed to determine if they still meet functional requirements.
Shelf Life of Common Elastomers
Here’s a breakdown of the typical shelf life for various elastomers, as outlined by SAE-ARP5316:
Unlimited
- Fluorocarbon (Viton®, FKM)
- Silicone (VMQ)
- EPDM (Ethylene Propylene)
- Butyl (IIR)
- Fluorosilicone (FVMQ)
- PTFE (Polytetrafluoroethylene)
15 Years
- Nitrile (NBR, Buna-N)
- Neoprene (CR)
5 to 10 Years
- Polyurethane (AU, EU)
3 Years
- SBR (Styrene-Butadiene)
Note: The shelf life listed here represents general guidelines. Actual shelf life may vary based on specific formulations, storage conditions, and handling practices.
Please consult a Canyon Components Engineer about your specific application and we will use our decades of experience to formulate a solution that fits your need.
Get a Quote Now!
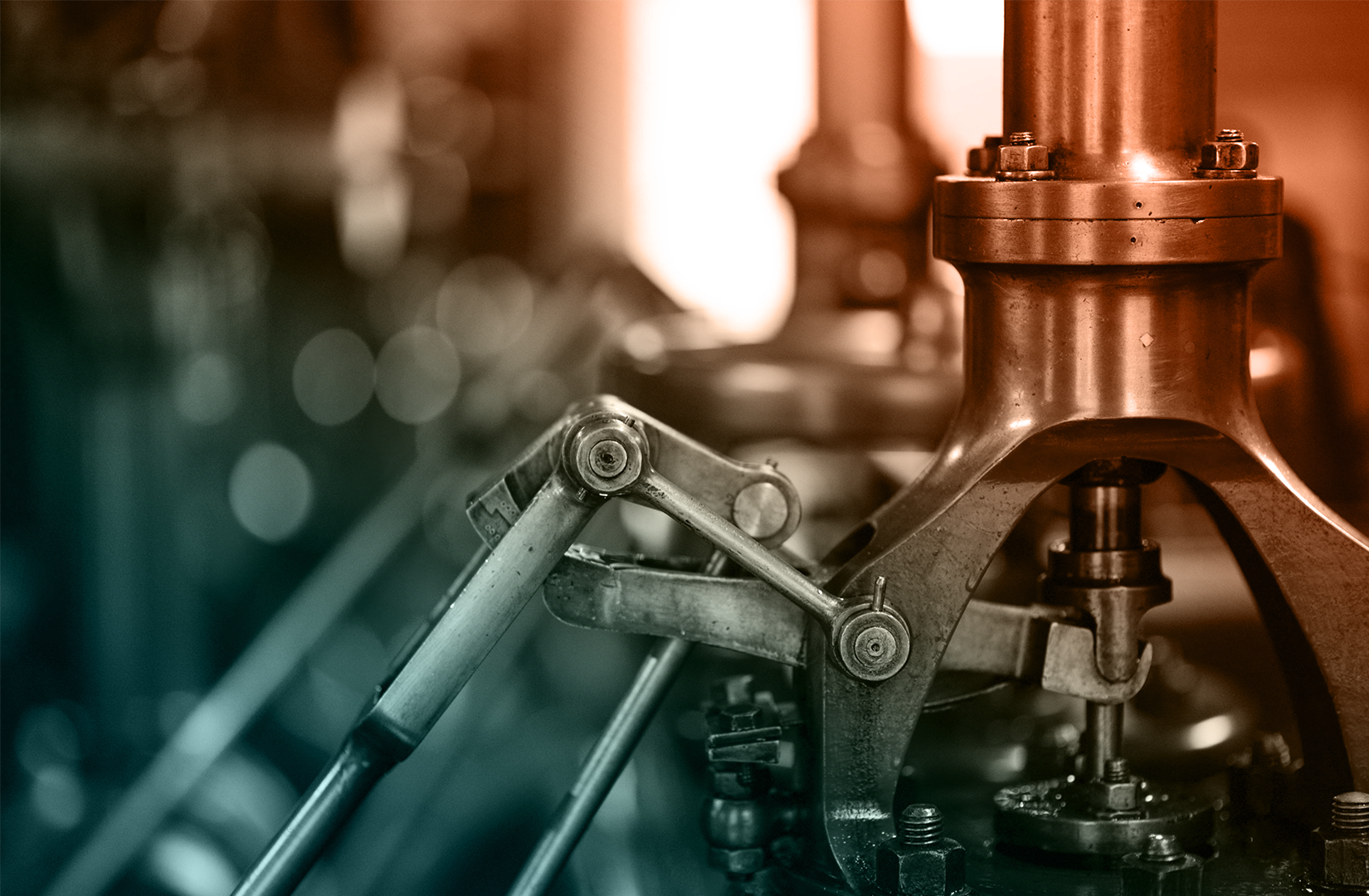
DEFINITIONS
ELASTOMER: A material that possesses elastic properties and has undergone vulcanization and/or conversion into a finished product.
SEAL: An elastomeric finished product or an assembly with an elastomeric element which prevents the excursion of media on one side of the product from migrating to the other side.
STORAGE LIFE: The maximum period of time, starting from the time of manufacture, that an elastomeric seal element, appropriately packaged, may be stored under specific conditions, after which time it is regarded as unserviceable for the purposes for which it was originally manufactured. The time of manufacture is the time of cure for thermoset elastomers or the time of conversion into a finished product for thermoplastic elastomers.
HARDWARE COMPONENT: The unit in which the elastomeric seal element is placed.
PACKAGING
PACKAGING: Unless otherwise specified by the customer at the time of order, the elastomeric seal or seal assembly shall be packaged:
- in individually sealed envelopes by the manufacturer, or
- in individually sealed packets in multiple envelopes by the manufacturer provided that individually packaged elastomeric seals or assemblies can be removed without affecting the seal integrity of the other packets.
The packaging shall be carried out in an atmosphere in which the relative humidity is not greater than 65%. Contamination by oil, grease, etc. shall be avoided. Seal assemblies (all components) shall be packaged in the same sealed envelope so that all elements of the assembly are present when the package is opened.
Packaging Materials: All packaging materials shall be free of copper naphthenates or creosote preservatives which can degrade rubber. Suitable materials include Kraft bags and polyethylene bags more than 0.075 mm thick and UV resistant. Opaque packaging is preferred but certified UV resistant materials can be used if available. Metal foil bags can be used provided they are salt free.
Labeling: Each package or container shall be labeled with the following information which shall be visible from the outside of the package without breaking the seal:
- Manufacturers' part number;
- Specification number and Revision level;
- Customer's part number and/or contract number (if requested);
- Quantity in package;
- Manufacturer's name and/or identity number (such as CAGE Code);
- Quarter and Year of cure or manufacturer of the rubber component (e.g., July to September 1997= 3Q97);
- Manufacturer's batch number;
- Rubber class designation per ASTM D 1418.
Expiration date will be added to the label for direct military procurement. It is not required to be on the label and will be added only when Purchaser specifically requests the addition because of direct military procurement.
STORAGE:
Temperature: The storage temperature shall be below 100 °F (38 °C), except when higher temperatures are caused by temporary climate changes, and articles shall be stored away from direct sources of heat such as boilers, radiators, and direct sunlight.
NOTE: If the storage temperature is below 59 °F (15 °C), care should be exercised during the handling of stored articles as they may have stiffened and become susceptible to distortion if not handled carefully.
The temperature of articles stored below 59 °F (15 °C) shall be raised to approximately 68 °F (20 °C) throughout their mass before being installed into a component.
Humidity: The relative humidity shall be such that given the variations of temperature in storage, condensation does not occur. In any event, if the elastomers are not stored in sealed moisture proof bags, the relative humidity of the atmosphere in storage shall be less than 75% r h, or if polyurethanes are being stored, shall be less than 65% r h.
Light: Elastomeric seals shall be protected from light sources, in particular direct sunlight or intense artificial light having an ultraviolet content. The individual storage bags offer the best protection as long as they are UV resistant.
NOTE: It is advisable that windows of storage rooms where elastomers are stored in bulk be covered with a red or orange coating or screen.
Radiation: Precautions shall be taken to protect stored articles from all sources of ionizing radiation likely to cause damage to stored articles.
Ozone: As ozone is particularly deleterious to some elastomeric seals, storage rooms shall not contain any equipment that is capable of generating ozone such as mercury vapor lamps, high voltage electrical equipment giving rise to electric sparks or silent electrical discharges. Combustion gases and organic vapor shall be excluded from storage rooms as they may give rise to ozone via photochemical processes.
Deformation: Elastomeric seals shall be stored free from superimposed tensions and compressive stresses or other causes of deformation. Where articles are packaged in a strain-free condition, they shall be stored in their original packaging. In case of doubt, the manufacturer's advise shall be sought. Rings of large inside diameter shall be formed into three equal superimposed loops so as to avoid creasing or twisting.
NOTE: It is not possible to achieve this condition by forming just two loops.
Contact With Liquid and Semi-Solid Materials: Elastomeric seals shall not be allowed to come into contact with liquid or semi-solid materials (for example, gasoline, greases, acids, disinfectants, cleaning fluids) or their vapors at any time during storage unless these materials are by design an integral part of the component or the manufacturer’s packaging. When elastomeric seals are received coated with their operational media, they shall be stored in this condition.
Contact With Metals: Certain metals and their alloys (in particular, copper, manganese, and iron) are known to have deleterious effects on elastomers. Elastomeric seals shall not be stored in contact with such metals (except when bonded to them) but shall be protected by individual packaging.
Contact With Dusting Powder: Dusting powders shall only be used for the packaging of elastomeric items in order to prevent blocking. In such instances, the minimum quantity of powder to prevent adhesion shall be used.
Contact Between Different Elastomers: Contact between different polymeric elastomers and elastomers of different seals shall be avoided. They shall not be packaged together in the same envelope.
Elastomeric Seals With Metal Parts Bonded to Them: The metal part of bonded elastomeric seals shall not come in contact with the elastomeric element of another seal. The bonded seal shall be individually packaged. Any preservative used on the metal shall be such that it will not affect the elastomeric element or the bond to such an extent that the seal will not comply with the product specification.
Stock Rotation: Elastomeric seal stock should be rotated on the FIFO principle (First In - First Out) so that the most recent manufactured parts remain in inventory.
History
Canyon Components strives to meet all customer service requests. Feel free to contact Canyon Components engineering and let our knowledgeable staff help you design the perfect part for your needs.
After World War II, age control was imposed on elastomers used in critical sealing devices of aircraft hydraulic, lubricating, and fuel systems. Several different requirements and specifications were implemented until 1958, when ANA Bulletin 438 was released. This bulletin's purpose was to consolidate all previous age control requirements into one document, making it easier for agencies and contractors to implement age control effectively. However, it led to confusion, cost increases, and inconsistently applied exceptions.
Numerous studies followed, summarized in the Air Force report AFML-TR-67-235. The conclusion was that elastomeric materials had improved over time, and age control should be less restrictive. As a result, MIL-STD-1523 was released in 1973, superseding ANA Bulletin 438. It introduced a cure date limitation of 12 quarters from the cure date to the acceptance of seals by the original procuring activity, intended to enforce First In - First Out (FIFO) warehousing procedures.
On February 1, 1984, MIL-STD-1523A was issued to replace MIL-STD-1523, aiming to eliminate previous ambiguities. It extended cure date requirements from 12 to 40 quarters, controlling elastomer age only at the time of acceptance by the government. Despite this, confusion persisted, and the need for age control continued to be debated.
EPRI NP-6608
In June 1989, Bruce Boyum and Jerral Rhoads presented the IEEE paper "Elastomer Shelf Life: Aged Junk or Jewels," concluding that age control limits were conservative and that shelf life could be extended with proper storage. This conclusion was further supported in May 1994 by EPRI NP-6608, "Shelf Life of Elastomeric Components," which determined that elastomer seals could have a shelf life of up to 32 years with appropriate storage.
AS1933A
Based on data from multiple studies on age control and shelf life, MIL-STD-1523A was canceled on January 30, 1995, without replacement. Instead, reference was made to AS1933A, “Age Controls for Hose Containing Age-Sensitive Elastomeric Materials.” This effectively released aerospace elastomers from age control. Since the cancellation, confusion has arisen, with contractors still insisting on age control and referring to AS1933A or MIL-HDBK-695C.
ARP5316
To address contractor needs and alleviate confusion after MIL-STD-1523A's cancellation, ARP5316 was issued. This recommended practice provides a control document for elastomeric seal components, offers traceability, and sets recommended shelf life limits consistent with age control studies. ARP5316 emphasizes proper storage and traceability, key elements for promoting long shelf life and ensuring compliance with specifications.
MIL-HDBK-695D
This recent revision directs readers to ARP5316 for questions concerning elastomer seal shelf life.
DOD 4141.27.M
The DOD Shelf Life Management Manual uses ARP5316 as its primary reference for elastomer seal shelf life.
Back to Reference Hub
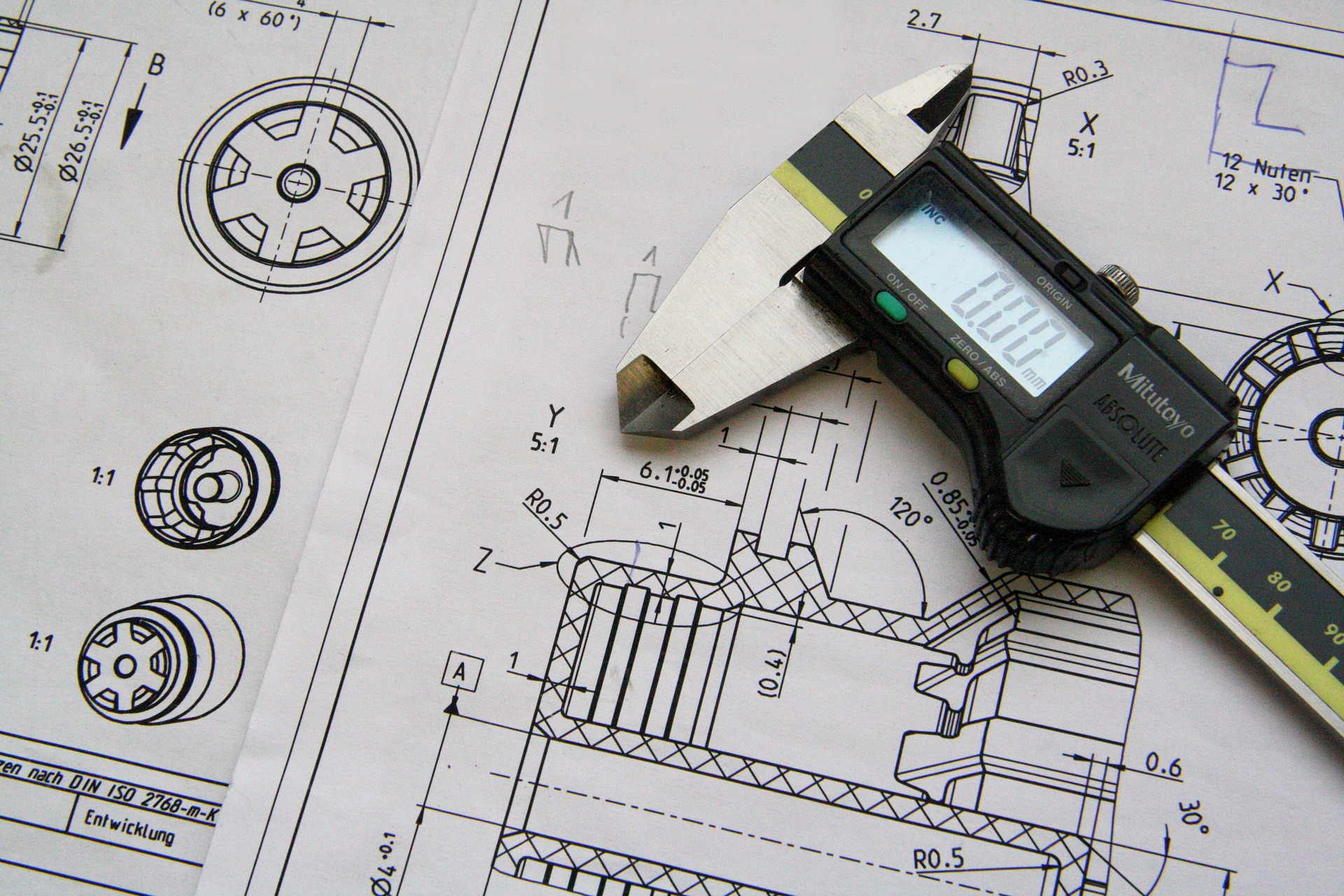
Get A Quote Now!
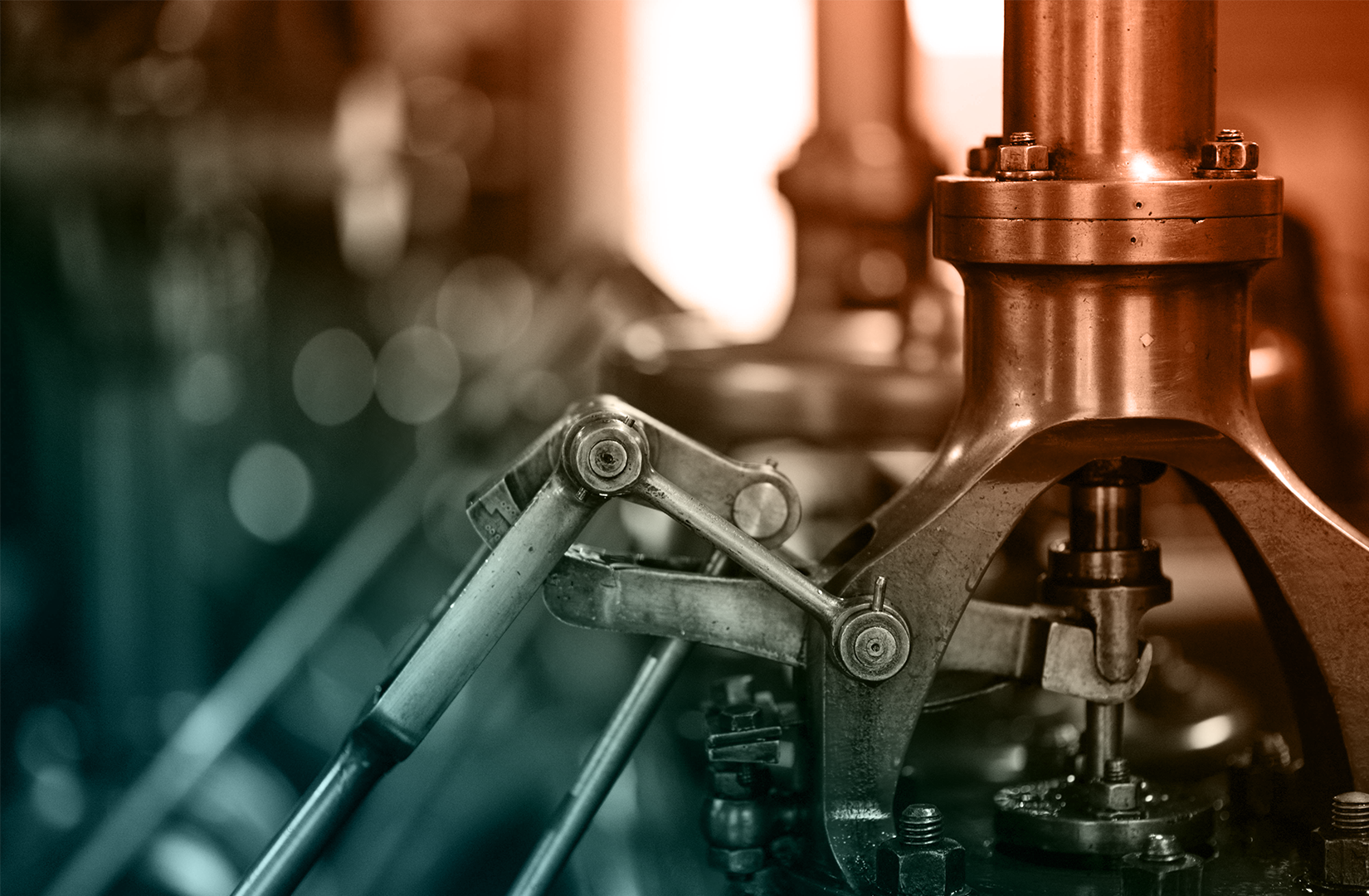