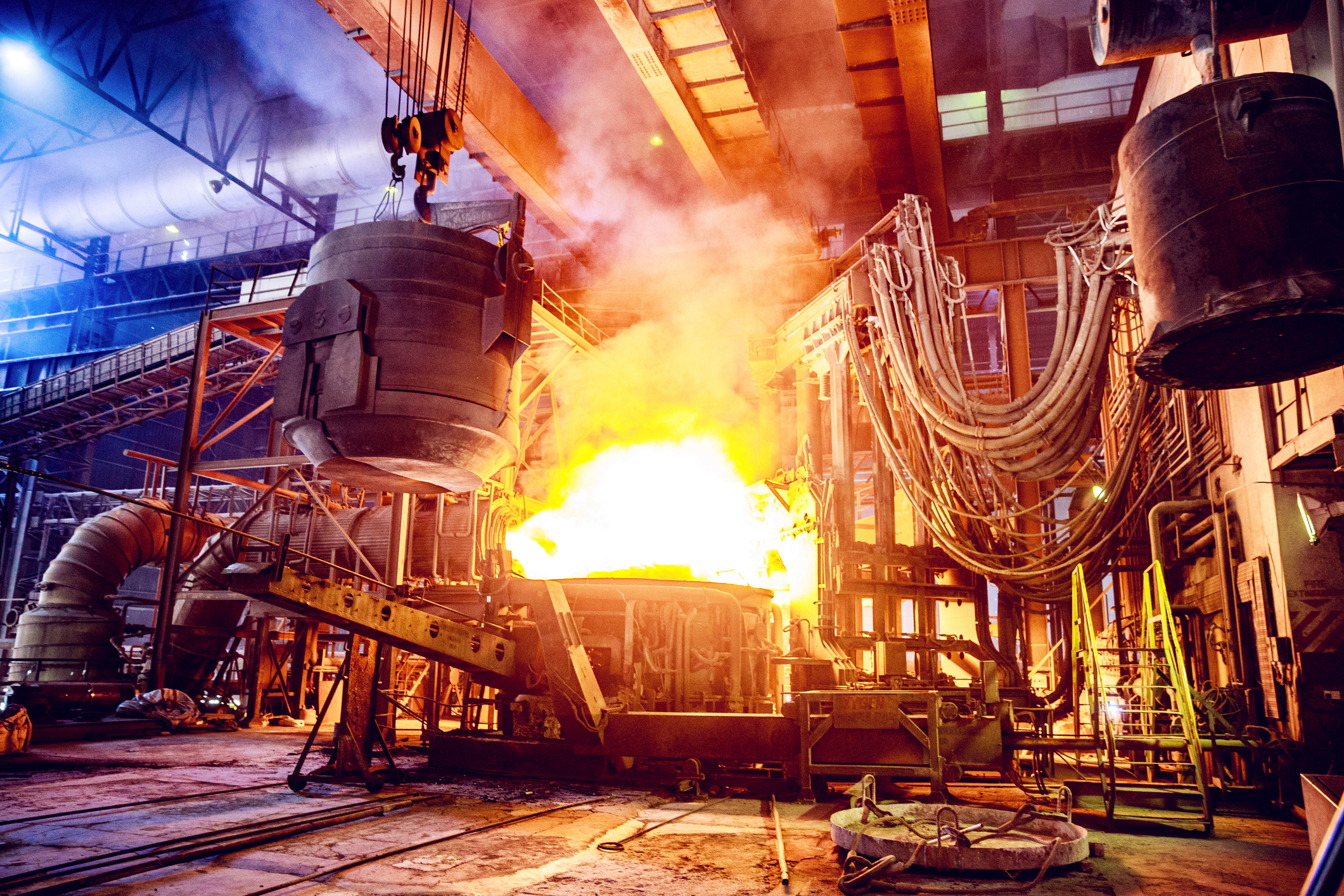
General Groove Guide
There are many variables that go into properly designing an O-ring groove. This page is intended to serve as a guide for how to use all of these variables to formulate the best O-ring sealing assembly possible.
Please keep in mind that every O-ring application is different and that there are always exceptions to rules. These are general considerations. When determining exact O-ring groove dimensions, it is also wise to see our more specific O-ring groove design tables.
If you have any questions or if you need assistance with engineering design, please feel free to get in touch with our engineering team.

Table of Contents
O-Ring Inside Diameter - Stretch & Interference
When O-rings are used in O-ring sealing applications, there will almost always be some stretch (the ID of the O-ring is smaller than the ID of the gland) or interference (the OD of the O-ring is larger than the OD of the gland).
Depending on the O-ring application, different levels of stretch and interference are recommended.
Relevant Equations


General Recommended Values *
- Face Seal (Internal Pressure): 0-3% Interference
- Face Seal (Internal Vacuum): 0-5% Stretch
- Rod (Static): 0-2% Interference
- Piston (Static): 0-5% Stretch
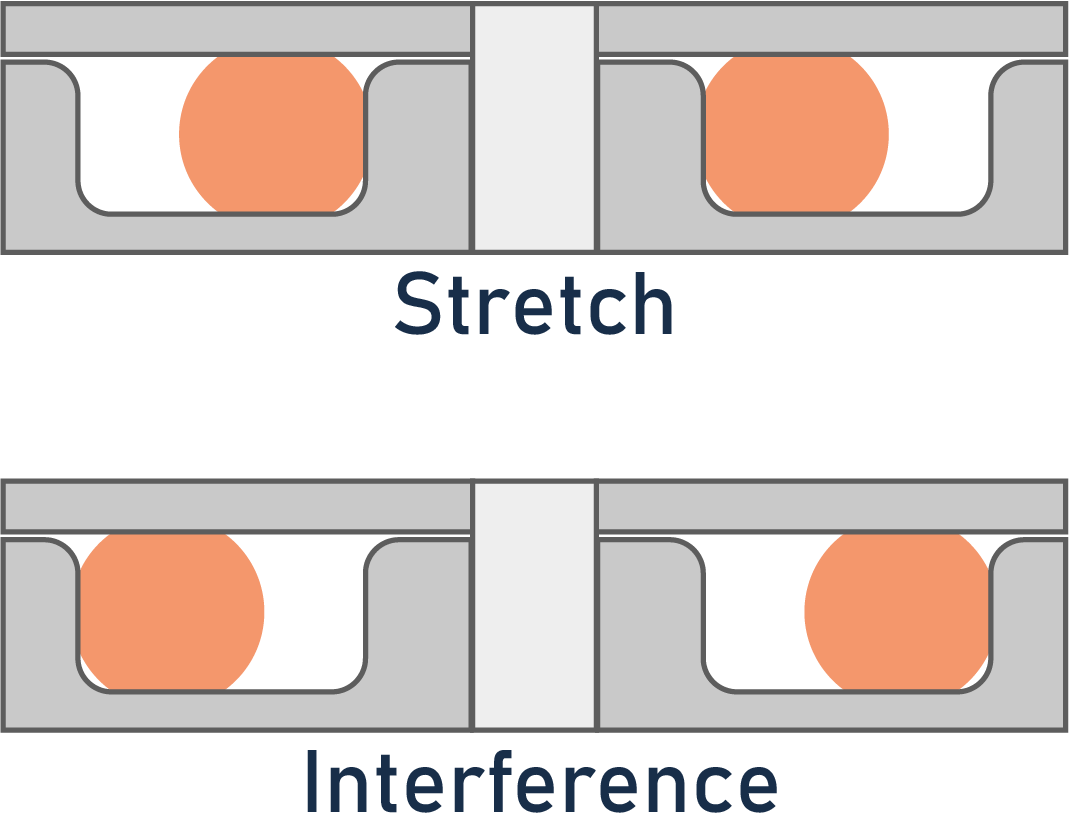
* Please keep in mind that recommended O-ring stretch and interference values can vary depending on the application. Please see our O-ring groove design tables for more specific recommendations, or get in touch with our engineering team.
O-Ring Cross Sectional Diameter - Small VS Large
Depending on the cross sectional diameter (CS) of an O-ring, the behavior of the seal can vary significantly.
Larger O-ring seals tend to be more effective in environments with frequent encounters with granular contaminants, such as dirt or dust.
Smaller O-ring seals tend to be more effective in environments that encourage explosive decompression.
Regardless of what O-ring size you need for your application, Canyon Components will be there to support your needs!

SMALLER CROSS SECTION | LARGER CROSS SECTION | |
---|---|---|
Dynamic Reciprocating Seals | ||
Less Stable | More Stable | |
Less Friction | More Friction | |
All Seals | ||
Requires Less Space | Requires More Space | |
Lower Weight | Higher Weight | |
Poorer Compression Set* | Better Compression Set* | |
More Volume Swell in Fluid | Less Volume Swell in Fluid | |
More Resistant to Explosive Decompression | Less Resistant to Explosive Decompression | |
Requires Tighter Gland Tolerances | Allows for Looser Gland Tolerances | |
More Likely to Leak From Dirt, Lint, Scratches, etc. | Less Likely to Leak From Dirt, Lint, Scratches, etc. | |
Better Physical Properties** | Poorer Physical Properties** | |
Lower Cost | Higher Cost | |
Higher Availability*** | Lower Availability*** |
* Particularly true for Fluorocarbon Elastomers & Nitrile Elastomers. Less applicable to EPDM and Silicones.
** Applies to the tensile strength and elongation of Nitrile Elastomers. Also applies to the elongation of Fluorocarbon Elastomers.
*** Can vary depending on O-ring sizing standard and popularity.
Please see our O-ring groove design tables for more specific recommendations, or get in touch with our engineering team.
Please consult a Canyon Components Engineer about your specific application and we will use our decades of experience to formulate a solution that fits your need.
Gland Corners
One of the most common O-ring failure modes is damage caused during installation. To avoid O-ring installation damage, it is important to eliminate burs or sharp surfaces that may interact with the O-ring seal.
By replacing any sharp corners with Chamfers or Fillets, most O-ring damage can be avoided.
Additionally, a lack of sharp corners will help prevent the O-ring from being damaged by the groove shifting during use or by high pressures.
Please see our O-ring groove design tables for more specific recommendations, or get in touch with our engineering team.
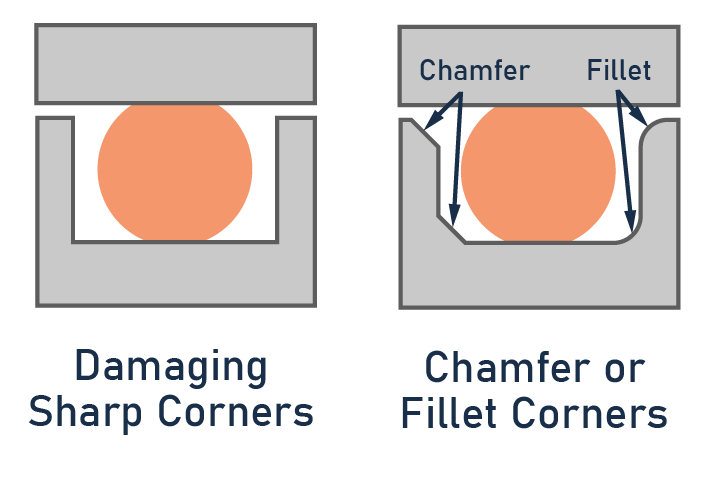
Friction
When designing dynamic O-ring sealing applications, Friction is often one of the most important variables. For example, if the friction is too high on the O-ring seal of a hand operated syringe, it may be too difficult for the user to actuate. Inversely, if the friction is too low on an O-ring valve assembly, it could mean that certain components don't hold together predictably while in motion.
TO DECREASE FRICTION | Factor | TO INCREASE FRICTION | ||
---|---|---|---|---|
Decrease | Unit Load (Squeeze) | Increase | ||
Decrease RMS | Surface Finish (Metal) | Increase RMS | ||
Decrease | Durometer | Increase | ||
Increase | Speed of Motion | Decrease | ||
Decrease | Cross Section of O-ring | Increase | ||
Decrease | Pressure | Increase | ||
Use Lubrication | Lubrication | Omit Lubrication | ||
Increase | Temperature | Decrease | ||
Increase | Groove Width | Decrease | ||
Decrease | Diameter of Bore or Rod | Increase | ||
Increase | Surface Finish (O-ring) | Decrease | ||
Increase Durometer | Coefficient of Friction* | Lower Durometer |
* This is a minor factor and should typically be ignored except for ultra high speed applications.
Please see our groove design tables for more specific recommendations, or get in touch with our engineering team.
Gland Surface Finish
When designing an O-ring sealing assembly, it is important that the sealing surfaces have the proper finish. If the finish is too rough, the O-ring sealing material might not be able to completely fill all surface voids which can lead to leaks. A lower durometer O-ring sealing material can help fix this problem by flowing more easily into surface voids.
Additionally, rough surfaces can damage O-ring seals, especially in dynamic O-ring applications. Sometimes it is best to use a harder, more abrasion resistant O-ring sealing material to help slow the effects of dynamic friction damage.
General Recommended Values *
- Static Seal (Liquids): 32 RMS
- Static Seal (Vacuum and Gases): 16 RMS
- Rod & Piston (Dynamic): 16 RMS
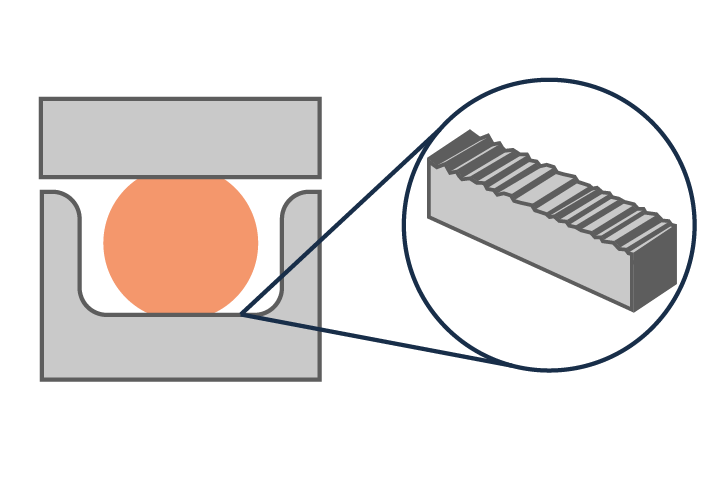
* Please keep in mind that recommended surface finish values can vary depending on the application. Please see our O-ring groove design tables for more specific recommendations, or get in touch with our engineering team.
O-Ring Compression
When O-rings are used in sealing applications, there will almost always be some compression. Without sufficient O-ring compression, the surfaces of the O-ring sealing material would not mate properly with the gland surfaces, likely causing loss of sealing performance.
Depending on the application, different levels of O-ring compression are recommended.
Relevant Equations

General Recommended Values *
- Face Seal: 10- 25 -35% Compression
- Rod & Piston (Static): 5- 20 -30% Interference
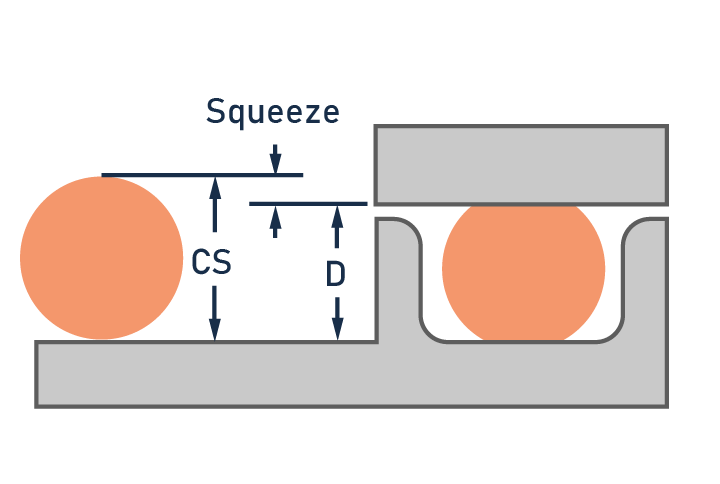
* Please keep in mind that recommended O-ring compression ratio values can vary depending on the application and O-ring materials used. Please see our O-ring groove design tables for more specific recommendations, or get in touch with our engineering team.
Gland Fill
When O-rings are compressed into closed glands, the O-ring sealing material deforms and fills a certain percentage of the volume of the groove. If the gland fill is too high, the O-ring can be damaged during assembly by the O-ring material swelling when contacting chemicals, or even by thermal expansion.
Depending on the application, different levels of O-ring gland fill are recommended.
Relevant Equations

General Recommended Values *
- Static Seal: 65- 75 -85% Gland Fill
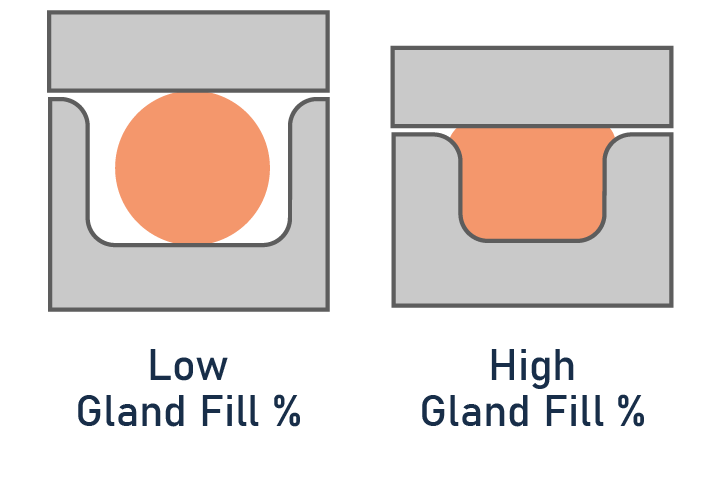
* Please keep in mind that recommended O-ring gland fill values can vary depending on the application and materials used. Please see our O-ring groove design tables for more specific recommendations, or get in touch with our engineering team.
O-Ring Gland Concentricity
When O-rings are used in pressurized or vacuum Rod & Piston O-ring sealing assemblies, it is important to maintain a relatively consistent seal compression across the entire O-ring.
In a perfectly Concentric sealing assembly, the clearance and O-ring seal compression would be constant across the entire assembly. In a Diametric sealing assembly, the compression of the O-ring seal and clearance would vary.
A diametric O-ring model is more realistic because it is technically impossible to achieve a perfectly concentric O-ring model. If a diametric O-ring sealing assembly is too unbalanced, it can cause leaks. If the Diametral Clearance is too large, the O-ring seal can experience extrusion.
Please see our O-ring groove design tables for more specific recommendations, or get in touch with our engineering team.
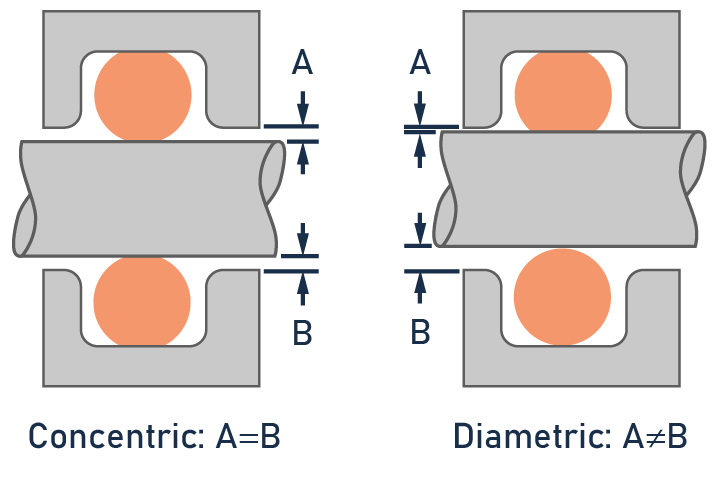
O-Ring Extrusion & High Pressure Applications
When O-rings are used in high pressure sealing applications, there is increased risk of extrusion. Without sufficient O-ring seal protection or proper O-ring gland design, the O-ring seal can be irreversibly damaged. Harder O-ring materials and Backup Rings typically produce a more extrusion resistant system.
Depending on the pressure levels, smaller O-ring clearance levels may be recommended.
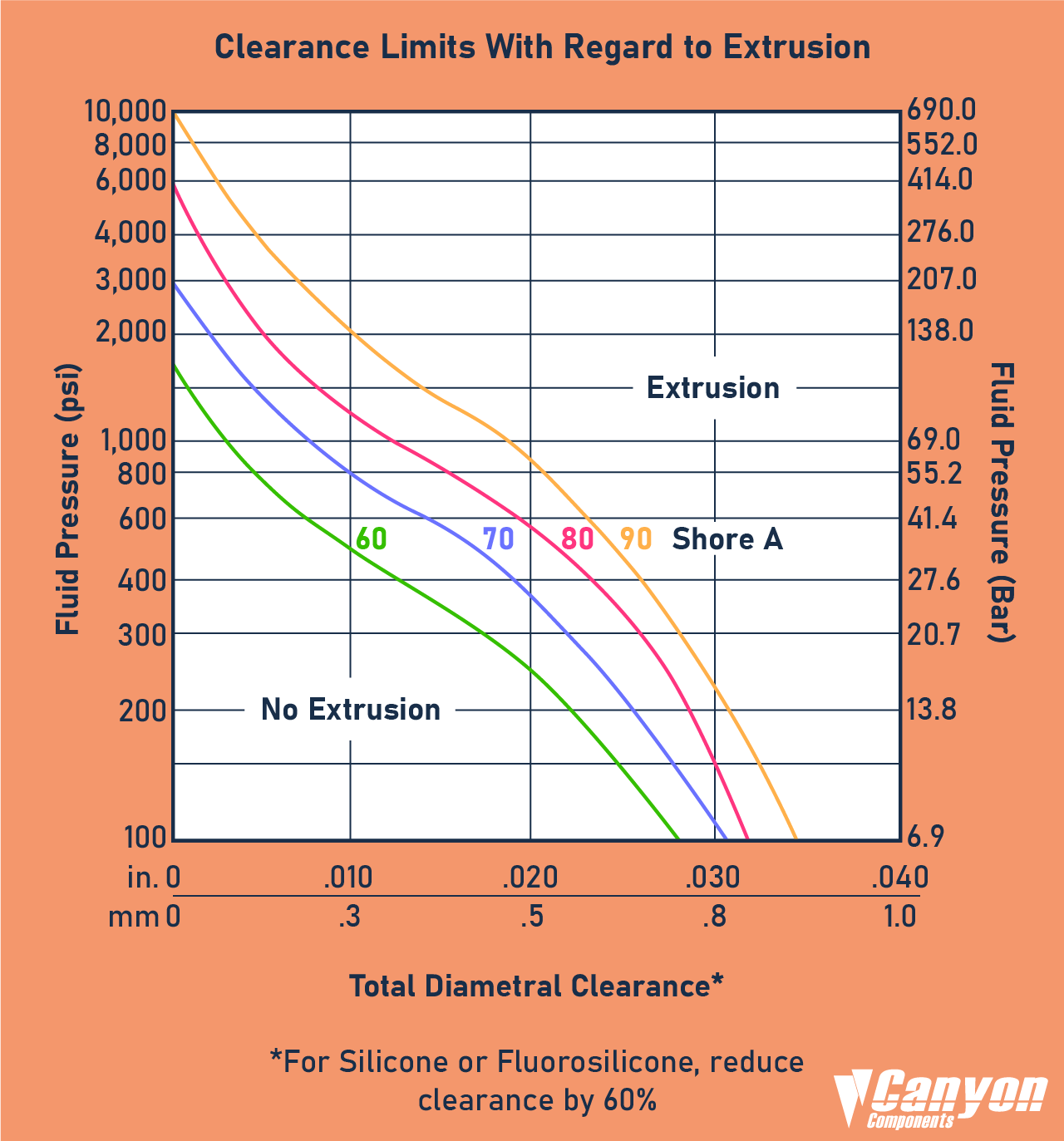
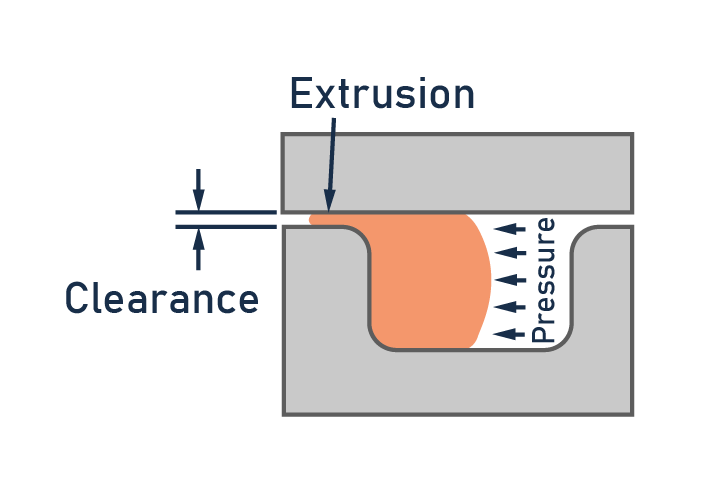

Please see our O-ring groove design tables for more specific recommendations, or get in touch with our engineering team.
Backup Rings
Backup rings are crucial components in O-ring sealing systems, providing enhanced support, reduced friction, and improved O-ring sealing capabilities. Backup rings prevent extrusion of the O-ring under high-pressure conditions and maintain a secure O-ring seal even at elevated pressures. In dynamic O-ring applications, backup rings reduce friction between the O-ring and mating surfaces, minimizing wear and ensuring longer-lasting O-ring sealing performance.
Additionally, backup rings help maintain the correct O-ring compression and ensure proper seating of the O-ring, optimizing O-ring sealing efficiency and preventing potential leaks. Using one backup ring on either side of the O-ring helps protect the seal against dynamic pressures in both directions. Overall, backup rings play a vital role in improving the reliability and efficiency of O-ring sealing systems in various applications, providing engineers with peace of mind in critical O-ring sealing environments.
Please see our O-ring groove design tables for more specific recommendations, or get in touch with our engineering team.
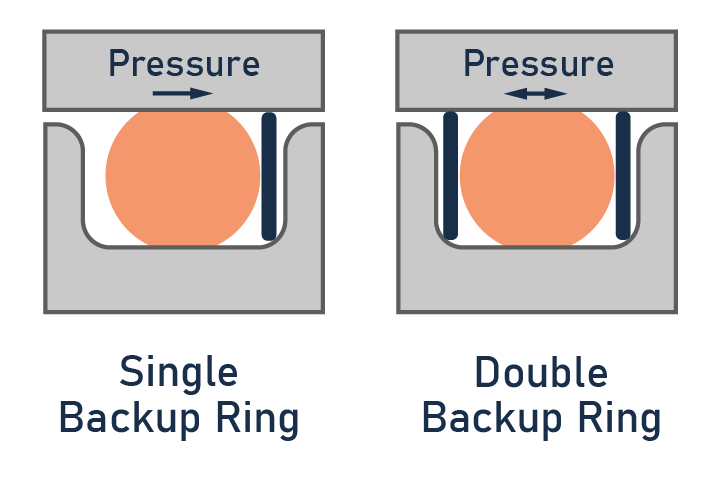
Back to Reference Hub
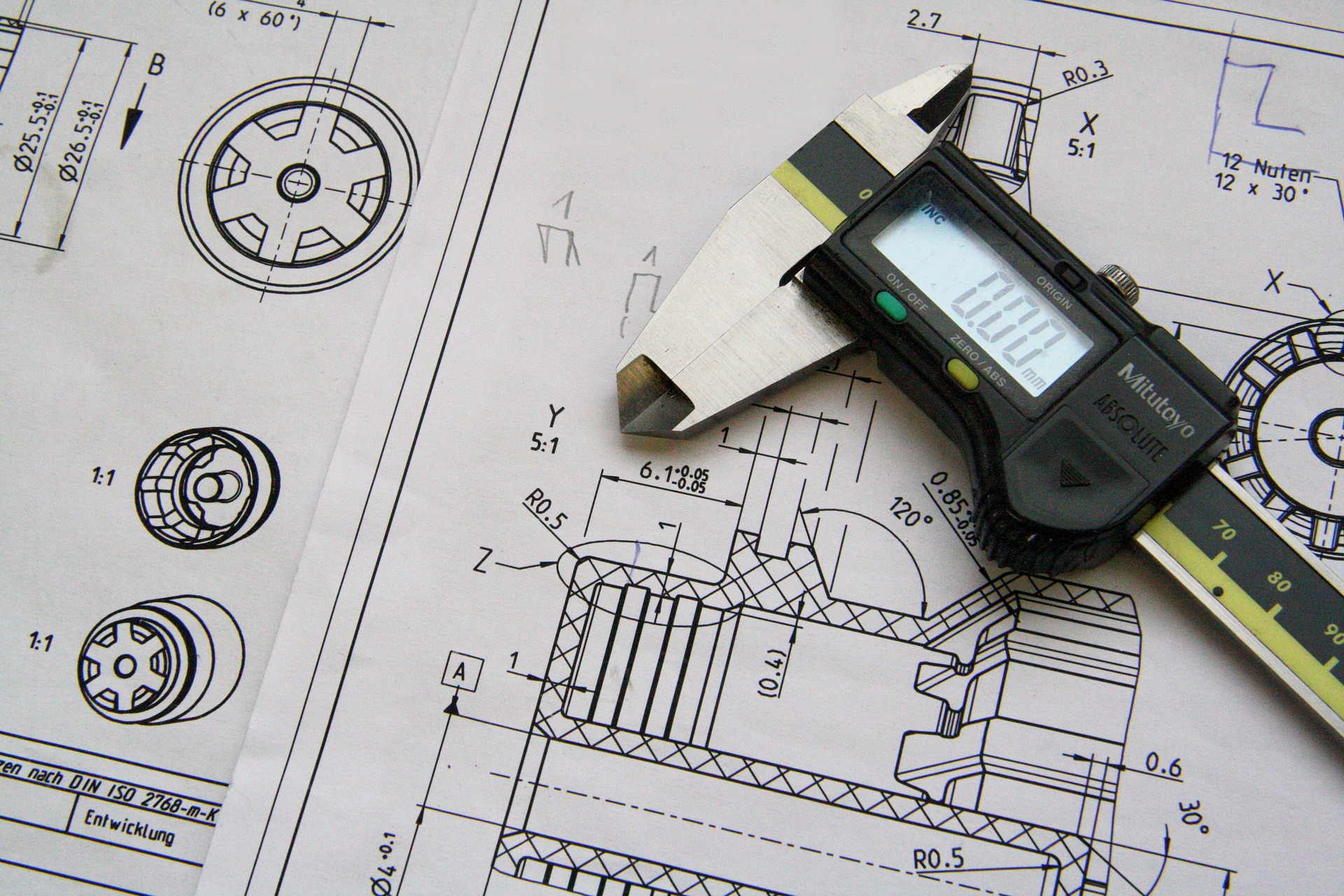
Get A Quote Now!
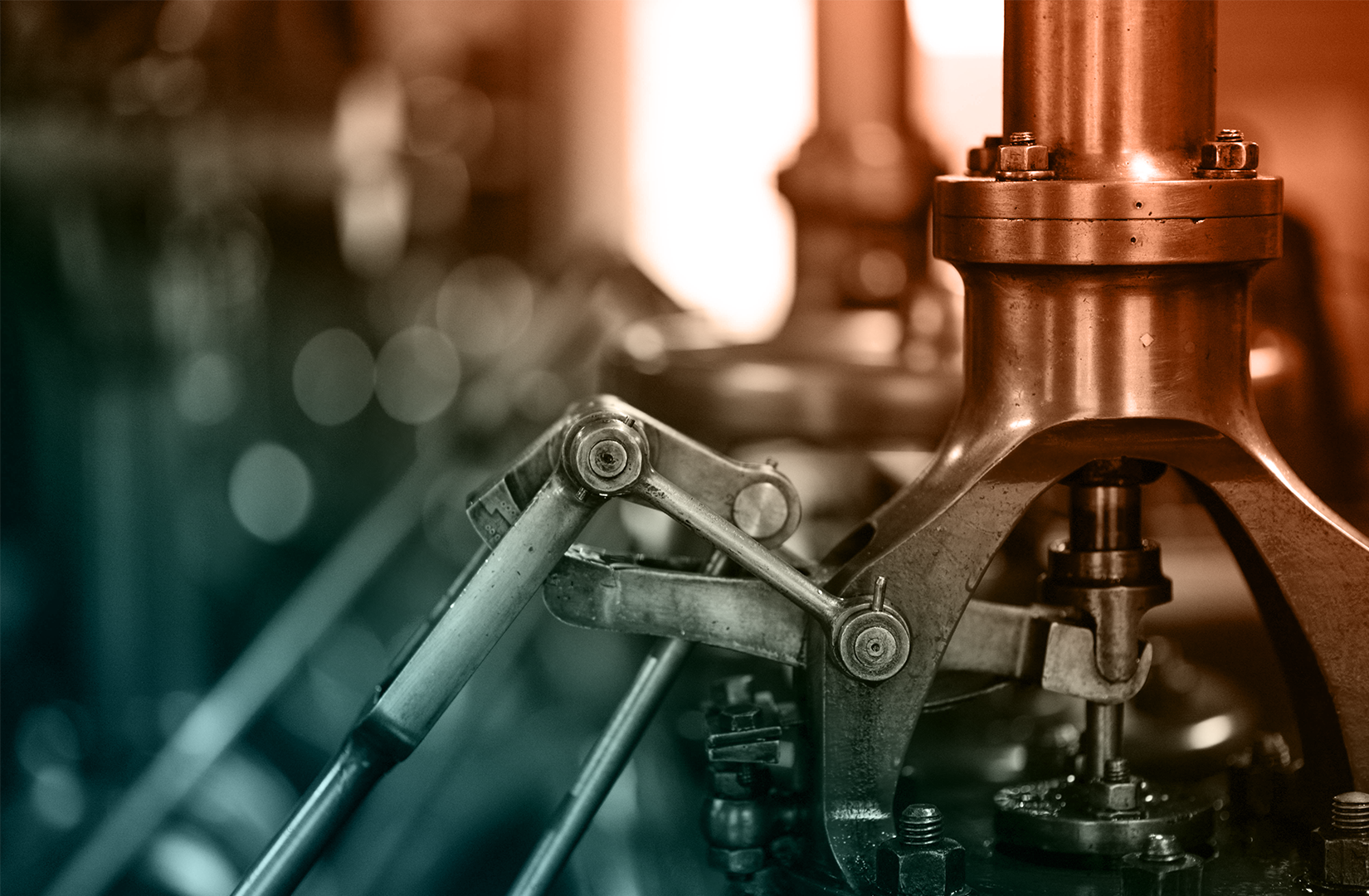
Groove Design References
Learn More
Coatings, Packaging, & Other Services
Learn More
Custom Parts & Custom O-rings
Learn More
Are thick or thin O-rings better?
Whether thick or thin O-rings are better depends on the specific requirements of the sealing application. Both thick and thin O-rings have their advantages and are suitable for different scenarios. Here's a comparison to help you decide:
Thick O-Rings:
1. Sealing Reliability: Thick O-rings provide a larger cross-sectional diameter (CS), which can improve sealing reliability, especially in applications where the sealing surface may have irregularities or imperfections.
2. Higher Pressure Resistance: The increased material volume in thick O-rings sometimes allows them to withstand higher pressures without deformation or failure, however it should be noted that thicker O-rings are less resistant to explosive decompression.
3. Enhanced Durability: Due to their larger size and cross-sectional diameter, thick O-rings may have a longer service life and better resistance to wear and tear.
Thin O-Rings:
1. Space Constraints: Thin O-rings are suitable for applications with limited space or tight clearances where a thicker O-ring may not fit.
2. Lower Friction: Thin O-rings can have lower friction compared to thicker O-rings, which can be advantageous in dynamic sealing applications.
3. Lower Compressive Force: Thin O-rings require less compressive force to achieve a seal, which can be important in delicate or lightweight assemblies.
4. Cost-Efficiency: Thin O-rings typically use less material and may be more cost-effective, especially in high-volume production.
In summary, the choice between thick and thin O-rings should be based on the specific sealing requirements of the application. Thick O-rings are generally preferred for certain types of high-pressure applications, applications with challenging sealing surfaces, and where durability is critical. Thin O-rings are suitable for space-constrained applications, situations where lower friction is beneficial, and when cost-effectiveness is a priority.
It's essential to consider factors such as pressure, temperature, space constraints, the condition of the sealing surface, and the desired level of sealing reliability when selecting the appropriate O-ring size and thickness.
Do O-rings have to be exact size?
O-rings do not have to be an exact size, but they should be selected and installed with careful consideration of the required size tolerances for the specific application. Here are some important points to understand:
1. Size Tolerances: O-rings are manufactured with size tolerances, which means that their actual dimensions may vary slightly from their nominal or specified dimensions. The tolerances are typically defined by industry standards such as AS568 (in the United States) or ISO 3601 (internationally). These standards provide a range of acceptable dimensions for O-rings.
2. Proper Fit: It is essential to select an O-ring size that fits properly within the sealing groove or gland of the application. The O-ring should be large enough to create an effective seal when compressed but not so large that it is excessively stretched or deformed during installation.
3. Compression: O-rings rely on compression to create a seal. When installed, the O-ring is compressed between two mating surfaces, which causes it to conform to the sealing surfaces and create a seal. The amount of compression required depends on the O-ring's material and the application requirements.
4. Material Elasticity: O-ring materials have a degree of elasticity, allowing them to deform under compression and return to their original shape when the pressure is released. This property enables them to maintain an effective seal.
5. Application Factors: Considerations such as temperature, pressure, and the type of fluid or gas being sealed are critical when selecting the appropriate O-ring size. These factors can affect the amount of compression needed and the O-ring material's compatibility with the application.
6. Custom Sizes: In some cases, custom-sized O-rings may be required to meet specific application needs. Manufacturers can produce O-rings with non-standard dimensions to fit unique sealing requirements.
In summary, while O-rings have size tolerances, selecting the right size within those tolerances and ensuring proper compression is crucial for effective sealing. It's important to follow industry standards, consult with Canyon Components engineers, and consider the specific application requirements to achieve a reliable and leak-free seal. Proper installation and maintenance are also essential for O-ring performance.
How do I choose an O-ring?
Choosing the right O-ring for your application is crucial to ensure a reliable seal. Here are the steps to help you choose the appropriate O-ring:
1. Identify the Application Requirements:
- Determine the operating conditions, including temperature, pressure, and exposure to chemicals.
- Consider whether the application is static (stationary) or dynamic (moving).
- Identify any specific industry or regulatory standards that must be met, such as FDA compliance for food-grade applications.
2. Material Selection:
- Select an O-ring material that is compatible with the operating conditions. Common materials include Nitrile (Buna-N), Viton, EPDM, Silicone, FFKM Perfluoroelastomers, and others.
- Consider the material's resistance to chemicals, temperature range, and compatibility with the fluids or gases involved.
3. Size and Dimensions:
- Measure the groove dimensions where the O-ring will be placed accurately.
- Determine the required O-ring size, including inner diameter (ID), outer diameter (OD), and cross-section (thickness).
- Ensure that the selected O-ring size will function properly when paired with the groove dimensions.
4. Temperature and Pressure Ratings:
- Check the temperature and pressure ratings of the selected O-ring material. Ensure that it can withstand the expected conditions without degradation or failure.
5. Chemical Compatibility:
- Verify that the O-ring material is compatible with the substances it will come into contact with, such as oils, fuels, chemicals, or gases.
- Consult chemical compatibility charts or databases to ensure the material's resistance to specific chemicals.
6. Hardness and Durometer:
- Consider the hardness or durometer of the O-ring material. Softer materials may be more flexible but less durable, while harder materials may be more durable but less flexible.
7. Installation and Maintenance:
- Follow proper installation procedures to ensure a secure and effective seal.
- Establish a maintenance schedule to inspect and replace O-rings regularly, as they can wear out over time.
8. Consult with Experts:
- If you have uncertainties or unique requirements, consult with Canyon Components O-ring experts who can provide guidance and recommend the best O-ring solution for your application.
Remember that choosing the right O-ring is essential for preventing leaks, maintaining equipment integrity, and ensuring safety in various industrial and mechanical systems. Taking the time to carefully assess your application's needs and selecting the appropriate O-ring material and design will contribute to the success and reliability of your sealing solution.
How do I know what size O-ring to buy?
To determine the correct size of O-ring to buy for your specific application, you'll need to consider several factors and follow a systematic approach:
1. Measure the Groove Dimensions:
- Measure the inside diameter (ID) and the groove width (cross-sectional diameter) of the groove where the O-ring will be installed. These measurements are crucial for selecting the appropriate O-ring size.
2. Check the O-ring Standard:
- Determine the O-ring standard or sizing system that is relevant to your application. The most common standards are AS568 (inch sizes) and metric sizes (ISO 3601). Ensure that you are using the appropriate standard for your region and industry.
3. Use O-ring Sizing Charts and Tables:
- Refer to O-ring sizing charts and tables provided by O-ring manufacturers or industry standards organizations. These resources will help you find the O-ring size that corresponds to your measured groove dimensions and standard.
4. Consider Tolerances:
- Take into account any tolerances or clearance requirements for your application. Depending on the application, you may need to select an O-ring size that provides a snug fit within the groove without excessive compression.
5. Check Material Compatibility:
- Ensure that the selected O-ring material is compatible with the fluids and environmental conditions in your application. Different elastomers (rubber compounds) have varying chemical resistance properties, so choose a material that can withstand the intended environment.
6. Temperature and Pressure Ratings:
- Verify that the selected O-ring material and size can handle the temperature and pressure conditions of your application. Consult the material's specifications and consider any temperature and pressure limitations.
7. Consider Dynamic vs. Static Sealing:
- Determine whether the O-ring will be used in a dynamic (moving) or static (non-moving) sealing application. Different O-ring sizes and materials may be suitable for each type of sealing.
8. Consult with Canyon Components Engineers:
- If you have any doubts or require assistance in selecting the right O-ring size, don't hesitate to consult with Canyon Components engineers. They can provide expert guidance based on your specific requirements.
9. Sample Testing:
- In critical applications, consider obtaining sample O-rings to test their fit and performance in the actual application before making a bulk purchase.
10. Safety Factors:
- Consider applying safety factors when selecting O-ring sizes. This can help ensure that the O-ring will perform reliably under varying conditions.
Remember that the correct O-ring size is essential for effective sealing and preventing leaks in your application. Taking the time to accurately measure and select the appropriate O-ring size will help ensure the success of your sealing solution.
How do you match an O-ring?
To determine the correct size of O-ring to buy for your specific application, you'll need to consider several factors and follow a systematic approach:
1. Measure the Groove Dimensions:
- Measure the inside diameter (ID) and the groove width (cross-sectional diameter) of the groove where the O-ring will be installed. These measurements are crucial for selecting the appropriate O-ring size.
2. Check the O-ring Standard:
- Determine the O-ring standard or sizing system that is relevant to your application. The most common standards are AS568 (inch sizes) and metric sizes (ISO 3601). Ensure that you are using the appropriate standard for your region and industry.
3. Use O-ring Sizing Charts and Tables:
- Refer to O-ring sizing charts and tables provided by O-ring manufacturers or industry standards organizations. These resources will help you find the O-ring size that corresponds to your measured groove dimensions and standard.
4. Consider Tolerances:
- Take into account any tolerances or clearance requirements for your application. Depending on the application, you may need to select an O-ring size that provides a snug fit within the groove without excessive compression.
5. Check Material Compatibility:
- Ensure that the selected O-ring material is compatible with the fluids and environmental conditions in your application. Different elastomers (rubber compounds) have varying chemical resistance properties, so choose a material that can withstand the intended environment.
6. Temperature and Pressure Ratings:
- Verify that the selected O-ring material and size can handle the temperature and pressure conditions of your application. Consult the material's specifications and consider any temperature and pressure limitations.
7. Consider Dynamic vs. Static Sealing:
- Determine whether the O-ring will be used in a dynamic (moving) or static (non-moving) sealing application. Different O-ring sizes and materials may be suitable for each type of sealing.
8. Consult with Canyon Components Engineers:
- If you have any doubts or require assistance in selecting the right O-ring size, don't hesitate to consult with Canyon Components engineers. They can provide expert guidance based on your specific requirements.
9. Sample Testing:
- In critical applications, consider obtaining sample O-rings to test their fit and performance in the actual application before making a bulk purchase.
10. Safety Factors:
- Consider applying safety factors when selecting O-ring sizes. This can help ensure that the O-ring will perform reliably under varying conditions.
Remember that the correct O-ring size is essential for effective sealing and preventing leaks in your application. Taking the time to accurately measure and select the appropriate O-ring size will help ensure the success of your sealing solution.
How long will an O-ring last?
The lifespan of an O-ring depends on various factors, and it can vary significantly based on the application and environment in which it is used. Here are the key factors that influence the longevity of an O-ring:
1. Material: Different materials have different resistances to wear, temperature, and chemicals. For example, O-rings made from Viton® (FKM) generally have a longer life in high-temperature and aggressive chemical environments compared to those made from Nitrile (NBR).
2. Operating Conditions: Exposure to extreme temperatures, aggressive chemicals, or constant mechanical stress can accelerate wear and degradation. O-rings used in harsh environments will generally have a shorter lifespan.
3. Installation and Fit: Proper sizing and correct installation are crucial. An improperly fitted O-ring can lead to excessive wear, extrusion, and early failure.
4. Lubrication: Adequate lubrication can significantly extend the life of an O-ring by reducing friction and wear.
5. Compression Set Resistance: This is the ability of the O-ring to return to its original shape after being compressed. A high resistance to compression set indicates a longer service life.
6. Quality of the O-Ring: Higher quality O-rings that meet specific industry standards tend to last longer than lower quality alternatives.
7. Maintenance and Inspection: Regular inspection and timely replacement of worn or damaged O-rings can prevent failures and extend the overall service life of the equipment.
In general, under normal operating conditions and with proper installation and maintenance, an O-ring can last several years. However, in demanding applications, such as those involving high temperatures, aggressive chemicals, or continuous mechanical motion, the lifespan might be significantly shorter.
It's important to regularly inspect O-rings in critical applications and replace them at the first sign of wear or degradation. For specific applications, consulting with a Canyon Components engineer who understands the operating environment can provide more precise estimates on the expected lifespan of an O-ring.
What are yellow O-rings used for?
Yellow O-rings are typically used as a visual indicator to distinguish them from O-rings made of other materials or colors. The color coding helps in identifying the specific material or application of the O-ring without the need for detailed inspection or testing. Here are a few common uses of yellow O-rings:
1. Food-Grade Applications: Yellow O-rings are sometimes used in food processing and pharmaceutical industries where hygiene and compliance with food safety regulations are critical. The yellow color may indicate that the O-ring is made of a food-grade material, such as FDA-compliant elastomers.
2. Chemical Compatibility: In some cases, yellow O-rings may be used in applications where they are exposed to specific chemicals or aggressive environments. The color can indicate that the O-ring is made of a material with enhanced chemical resistance or compatibility for that particular application.
3. High-Temperature Applications: Yellow O-rings may be used in high-temperature applications where the material is specially formulated to withstand elevated temperatures. The color coding helps in quickly identifying the O-rings suitable for high-temperature sealing.
4. Material Differentiation: Yellow can be used as a general color code to differentiate O-rings made of certain materials from others. For example, it may signify a specific type of elastomer or a proprietary material formulation used by a particular manufacturer.
5. Specialized Applications: In some cases, yellow O-rings may be used in specialized applications where they need to stand out or be easily identifiable due to specific performance characteristics, such as resistance to abrasion or extreme conditions.
It's important to note that the specific meaning of a yellow O-ring may vary between manufacturers or industries. Therefore, when using color-coded O-rings, it's essential to refer to the manufacturer's documentation or industry standards to ensure that the O-ring is being used appropriately for the intended application. Additionally, always follow safety and material compatibility guidelines when selecting O-rings for specific purposes.
What do different colored O-rings mean?
The color of an O-ring doesn't inherently signify a specific characteristic or quality; rather, it's often used as a means to identify different materials or specifications. Here's a general guide to what different colored O-rings might indicate:
1. Black: The most common color for O-rings, typically made of nitrile (Buna-N), neoprene, EPDM, or other general-purpose materials. These are widely used in various applications due to their good resistance to oils, fuels, and certain chemicals. However, it should be noted that virtually any elastomeric material can be, and will frequently be manufactured in black colorations. This includes specialty materials like Aflas, FFKM Perfluoroelastomers, and silicone.
2. Blue: Fluorosilicone O-rings are typically manufactured in blue colorations. Also, blue is often associated with FDA-approved materials that are safe for food, water, and beverage contact. Blue O-rings are also easily detectable, which helps in maintaining safety standards in food processing industries.
3. Green: Commonly indicates the presence of hydrogenated nitrile (HNBR), which offers better heat and chemical resistance compared to standard nitrile. Viton® (fluorocarbon rubber) can also frequently be found in green colorations.
4. Brown: Typically signifies the use of Viton® (fluorocarbon rubber), known for its excellent resistance to high temperatures and chemicals, including petroleum products.
5. Red, Orange, or Pink: Frequently used for silicone O-rings, which are known for their heat resistance and use in food-grade applications.
6. White or Clear: Often indicates that the O-ring is made from silicone, Teflon (PTFE), or another material that is suitable for sanitary or medical applications.
7. Yellow: May indicate special compounds, such as polyurethane, which are known for their wear resistance and strength.
8. Metal Detectable O-rings: These O-rings are infused with metal detectable materials and are often blue. They are used in the food and pharmaceutical industries where contamination by foreign objects is a critical concern.
It's important to note that these color associations are not universal and can vary between manufacturers. The color alone should not be relied upon to determine the material or suitability of an O-ring for a specific application. Always refer to the manufacturer's specifications or consult with a Canyon Components engineer when selecting an O-ring for a particular use.
What is better, Nitrile or Viton?
Choosing between Buna-N (Nitrile rubber) and Viton (a brand of FKM, fluoroelastomer) depends on the specific requirements of your application. Each material has its advantages and limitations, so the choice should be based on factors like chemical resistance, temperature range, and cost. Here's a comparison:
1. Chemical Resistance:
- Buna-N: Buna-N is excellent for resistance to oils, fuels, and petroleum-based fluids. It performs well in applications where exposure to these substances is common.
- Viton: Viton is superior in terms of chemical resistance, especially for a broader range of chemicals, including more aggressive acids and solvents. It excels in applications with harsh chemical environments.
2. Temperature Range:
- Buna-N: Buna-N has a moderate temperature range, typically from -40°C to 108°C (-40°F to 226°F).
- Viton: Viton can handle higher temperatures, usually up to 200°C (392°F), making it suitable for high-temperature applications.
3. Cost:
- Buna-N: Generally more cost-effective compared to Viton. It provides good performance at a lower cost.
- Viton: Viton is more expensive due to its superior chemical resistance and higher temperature tolerance.
4. Applications:
- Buna-N: Commonly used in automotive, industrial, and manufacturing applications where exposure to oils, fuels, and petroleum-based fluids is frequent.
- Viton: Preferred in applications where a higher level of chemical resistance is required, such as in the chemical processing industry, aerospace, and situations involving aggressive chemicals.
5. Environmental Resistance:
- Buna-N: Better suited for applications involving oils and hydrocarbons.
- Viton: Better for applications involving a wider range of chemicals and high-temperature environments.
In summary, Buna-N is a cost-effective choice for applications involving oils and fuels, whereas Viton is preferred for applications with a broader range of chemicals and higher-temperature requirements. The specific choice depends on your application's needs, and it's essential to consider factors like chemical exposure, temperature extremes, and budget when making the decision.
What is the best O-ring material for high temperatures?
The choice of the best O-ring material for high-temperature applications depends on the specific temperature range and other environmental factors involved. Several elastomer materials are suitable for high-temperature sealing, and the selection should be based on the following considerations:
1. Silicone Rubber (VMQ):
- Temperature Range: Certain Silicone rubber blends can handle temperatures up to 600°F (315°C), however most are only rated for 400°F (205°C).
- Advantages: Excellent high-temperature resistance, good flexibility, and resistance to ozone and UV exposure.
- Applications: Suitable for a wide range of high-temperature applications, including aerospace, automotive, and food processing.
2. Fluorocarbon Rubber (FKM/Viton):
- Temperature Range: FKM can withstand temperatures up to 437°F (225°C).
- Advantages: Exceptional chemical resistance, high-temperature resistance, and durability.
- Applications: Commonly used in oil and gas, automotive, chemical processing, and aerospace industries.
3. Perfluoroelastomer (FFKM):
- Temperature Range: Certain FFKM CanRez blends can handle temperatures up to 635°F (335°C) and excursions to even higher temperatures.
- Advantages: Excellent high-temperature and ultimate chemical resistance, low outgassing, and low permeability.
- Applications: Used in demanding high-temperature and chemical environments, such as semiconductor manufacturing and oil and gas.
4. Fluorosilicone (FVMQ):
- Temperature Range: FVMQ materials can handle temperatures up to 356°F (180°C).
- Advantages: Good high-temperature resistance, flexibility, and resistance to oils and fuels.
- Applications: Suitable for aerospace, automotive, and other applications where a combination of temperature and chemical resistance is required.
The best O-ring material for high-temperature applications varies depending on the specific temperature range, chemical exposure, pressure, and other environmental factors. It's essential to consult with a material expert or O-ring manufacturer to select the most suitable material for your particular application to ensure optimal performance and longevity. Additionally, consider the specific grade and formulation of the elastomer material to match the requirements of your high-temperature application.
What is the difference between NBR and HNBR O-rings?
NBR (Nitrile Butadiene Rubber) and HNBR (Hydrogenated Nitrile Butadiene Rubber) are both synthetic elastomers known for their excellent resistance to oil, fuel, and chemicals. However, they differ in their chemical structure and performance characteristics. Here are the key differences between NBR and HNBR:
1. Chemical Structure:
- NBR: NBR is a copolymer of butadiene and acrylonitrile. It contains a nitrile group in its chemical structure, which provides oil and fuel resistance. The acrylonitrile content in NBR can vary, affecting its overall properties.
- HNBR: HNBR is a modified version of NBR. It is also a copolymer of butadiene and acrylonitrile, but it undergoes hydrogenation, which involves the addition of hydrogen atoms to the polymer chain. This hydrogenation process enhances its resistance to heat, ozone, and chemicals.
2. Oil and Fuel Resistance:
- NBR: NBR offers good oil and fuel resistance and is commonly used in applications involving petroleum-based oils, fuels, and lubricants.
- HNBR: HNBR provides excellent oil and fuel resistance, often surpassing the performance of standard NBR. It is preferred in applications where exposure to automotive engine oils and transmission fluids is common.
3. Temperature Range:
- Buna-N (NBR) has a temperature range of approximately -40°F to 257°F (-40°C to 125°C), which is generally lower than HNBR.
- HNBR has a higher temperature resistance compared to standard NBR. It can typically handle temperatures ranging from -40°F to 329°F (-40°C to 165°C) or higher, depending on the specific grade.
4. Chemical Resistance:
- NBR: NBR exhibits good resistance to many chemicals but may not perform as well as HNBR in highly aggressive chemical environments.
- HNBR: HNBR offers excellent chemical resistance to a broader range of chemicals, acids, and solvents compared to NBR.
5. Ozone and Weathering Resistance:
- NBR: NBR is susceptible to ozone and weathering degradation over time.
- HNBR: HNBR has improved resistance to ozone and weathering due to its hydrogenated structure.
6. Applications:
- NBR: NBR is commonly used in automotive seals, O-rings, gaskets, and hoses, especially in applications involving petroleum-based fluids.
- HNBR: HNBR is preferred in automotive applications where exposure to engine oils and transmission fluids is significant. It is also used in chemical processing, oil and gas industry, and other applications requiring enhanced chemical and temperature resistance.
In summary, while both NBR and HNBR offer good oil and fuel resistance, HNBR provides superior performance in terms of temperature resistance, chemical resistance, and resistance to ozone and weathering. The choice between the two depends on the specific requirements of the application, with HNBR being the preferred choice in demanding environments.
What is the smallest O-ring?
The size of the smallest O-ring can vary depending on the material used and the manufacturing capabilities of O-ring manufacturers. O-rings come in a wide range of sizes, and the smallest O-rings are typically used in precision applications where a very tight seal is required. Here are some general guidelines:
1. Standard Sizes: O-rings are available in standard sizes based on industry standards such as AS568 (in the United States), JIS (Japanese), and ISO 3601 (internationally). These standards specify the dimensions of O-rings in terms of inside diameter (ID), outside diameter (OD), and cross-sectional diameter (thickness). The smallest standard O-rings are typically in the range of 0.74mm to 2mm in ID, with cross-sectional diameters as thin as 1mm or less.
2. Custom Sizes: In many cases, Canyon Components can produce custom O-rings with even smaller dimensions, including micro O-rings with extremely small ID's and cross sections. These custom O-rings are often used in specialized applications in industries such as medical devices, aerospace, and electronics.
3. Material Considerations: The choice of material is crucial for small O-rings, as the material must provide the necessary sealing properties while maintaining flexibility and durability. Materials like silicone, fluorocarbon (Viton), and PTFE (Teflon) are commonly used for small O-rings, depending on the application requirements.
4. Application Requirements: The size of the O-ring should be selected based on the specific requirements of the sealing application, including factors such as pressure, temperature, chemical compatibility, and the size of the sealing groove or gland in which the O-ring will be installed.
5. Manufacturing Precision: Producing small O-rings with high precision requires advanced manufacturing techniques and equipment. Canyon Components specializes in providing miniature and micro O-rings to meet the demands of specialized industries.
It's important to consult with Canyon Components engineers to determine the smallest O-ring size available for your specific application. They can provide guidance on material selection and manufacturing capabilities to ensure that the O-ring meets the required sealing performance in small and precision applications.
What size is a micro O-ring?
The term "micro O-ring" typically refers to O-rings that are very small in size, often with dimensions measured in millimeters or even fractions of a millimeter. The specific size of a micro O-ring can vary depending on the application and the manufacturer's requirements. Micro O-rings are commonly used in precision engineering, microfluidics, and miniature sealing applications.
To provide a general idea of the size range, micro O-rings may have:
1. Outer diameters (OD) as small as 0.5 mm or less.
2. Inner diameters (ID) in a similar range.
3. Cross-sectional diameters (thickness) ranging from 0.1 mm to 0.5 mm or less.
It's important to note that the exact size and dimensions of a micro O-ring can vary significantly based on the specific application and the precision required. When selecting a micro O-ring, it's essential to consider the sealing requirements, such as the pressure, temperature, and compatibility with the fluids involved, in addition to the size specifications. Manufacturers and suppliers of O-rings often provide detailed specifications for their products, including size measurements, to help customers choose the right O-ring for their needs.
What sizes do O-rings come in?
O-rings come in a wide range of sizes to accommodate various sealing and gasketing applications. The size of an O-ring is typically described using two key dimensions: the inside diameter (ID) and the cross-sectional diameter (CS). Here's how O-ring sizes are typically specified:
1. Inside Diameter (ID): This is the measurement of the inner circular diameter of the O-ring, which corresponds to the size of the opening it will seal. The ID is typically specified in millimeters (mm) or inches (in).
2. Cross-Sectional Diameter (CS): This is the measurement of the thickness or width of the O-ring when it is in a round cross-sectional shape. The CS is also specified in millimeters (mm) or inches (in).
O-rings are available in a wide range of ID and CS combinations to suit various applications. Common O-ring sizes include:
- Small O-rings with IDs in the range of a few millimeters to a few centimeters and CS ranging from fractions of a millimeter to a few millimeters.
- Medium-sized O-rings with IDs in the range of several centimeters to a few tens of centimeters and CS ranging from a few millimeters to a centimeter or more.
- Large O-rings with IDs measured in tens of centimeters or even meters and CS ranging from a few centimeters to several centimeters.
The specific size of an O-ring required for a particular application depends on factors such as the sealing requirements, the diameter of the sealing surface, the pressure, temperature, and the compatibility with the fluid being sealed. O-ring sizes are standardized to some extent, and industry standards like AS568 in the United States provide a range of standardized O-ring sizes with unique designations to simplify selection.
When selecting an O-ring size, it's important to consider the specific requirements of the sealing application and choose an O-ring size that provides an adequate seal while ensuring compatibility with the sealing surface and the surrounding environment.