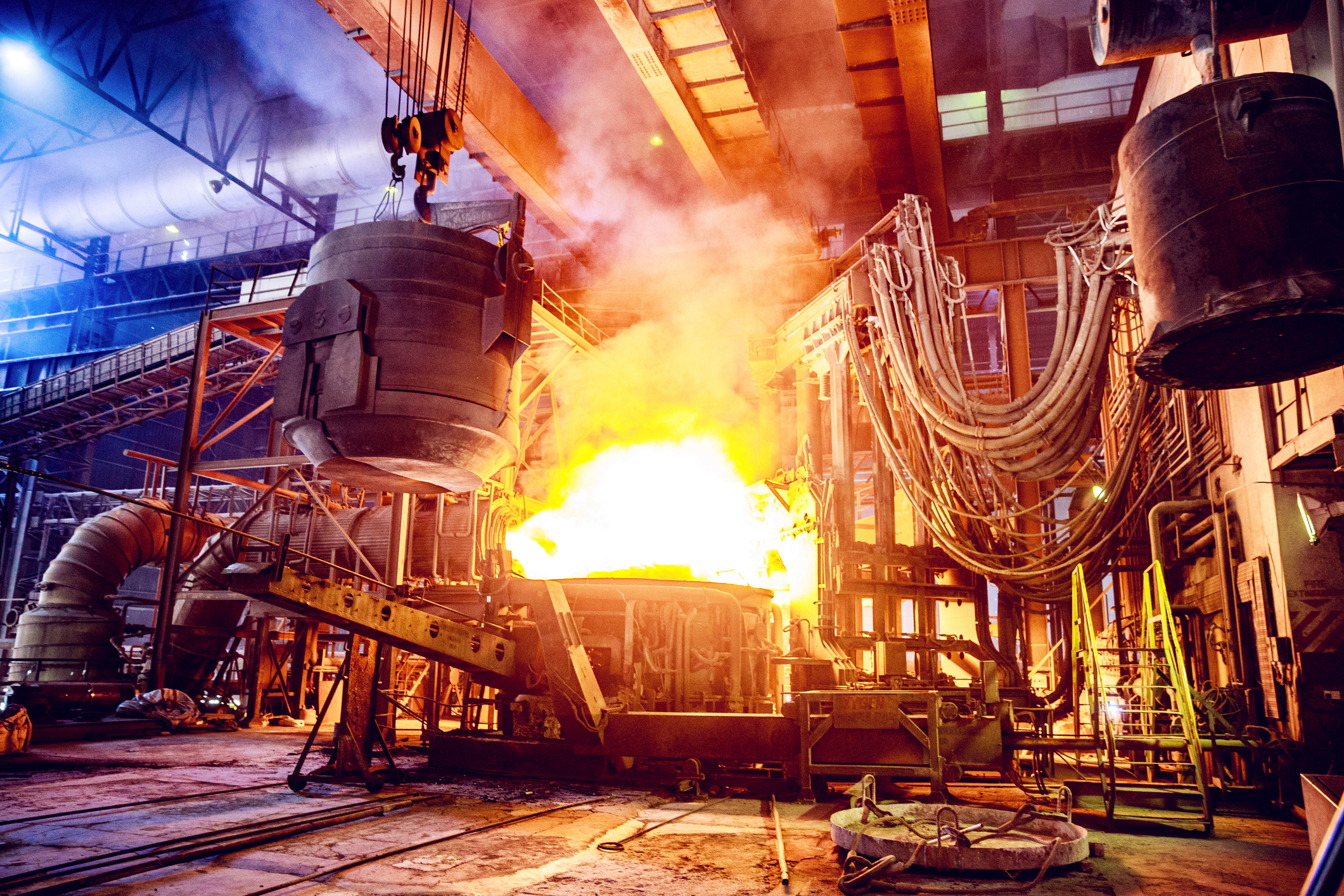
HNBR (Hydrogenated Nitrile) Selection Guide
HNBR O-rings, gaskets, & custom molded parts are formed by subjecting Nitrile rubber to a hydrogenation process. The resulting compound demonstrates increased temperature resistance and better compatibility with many fuels and chemicals. Hydrogenated Nitrile O-rings, gaskets, & custom molded parts also offer higher strength and reduced degradation at high temperatures compared to conventional Nitrile O-rings, gaskets, & custom molded parts. These properties make HNBR O-rings, gaskets, & custom molded parts popular in the oil and gas industry, as well as many applications in the chemical industry. Specific physical and chemical resistances vary by compound formulation.
Common names include: HNBR (Hydrogenated acrylonitrile butadiene rubber), Hydrogenated Nitrile Trade Names: Therban®, Zetpol®
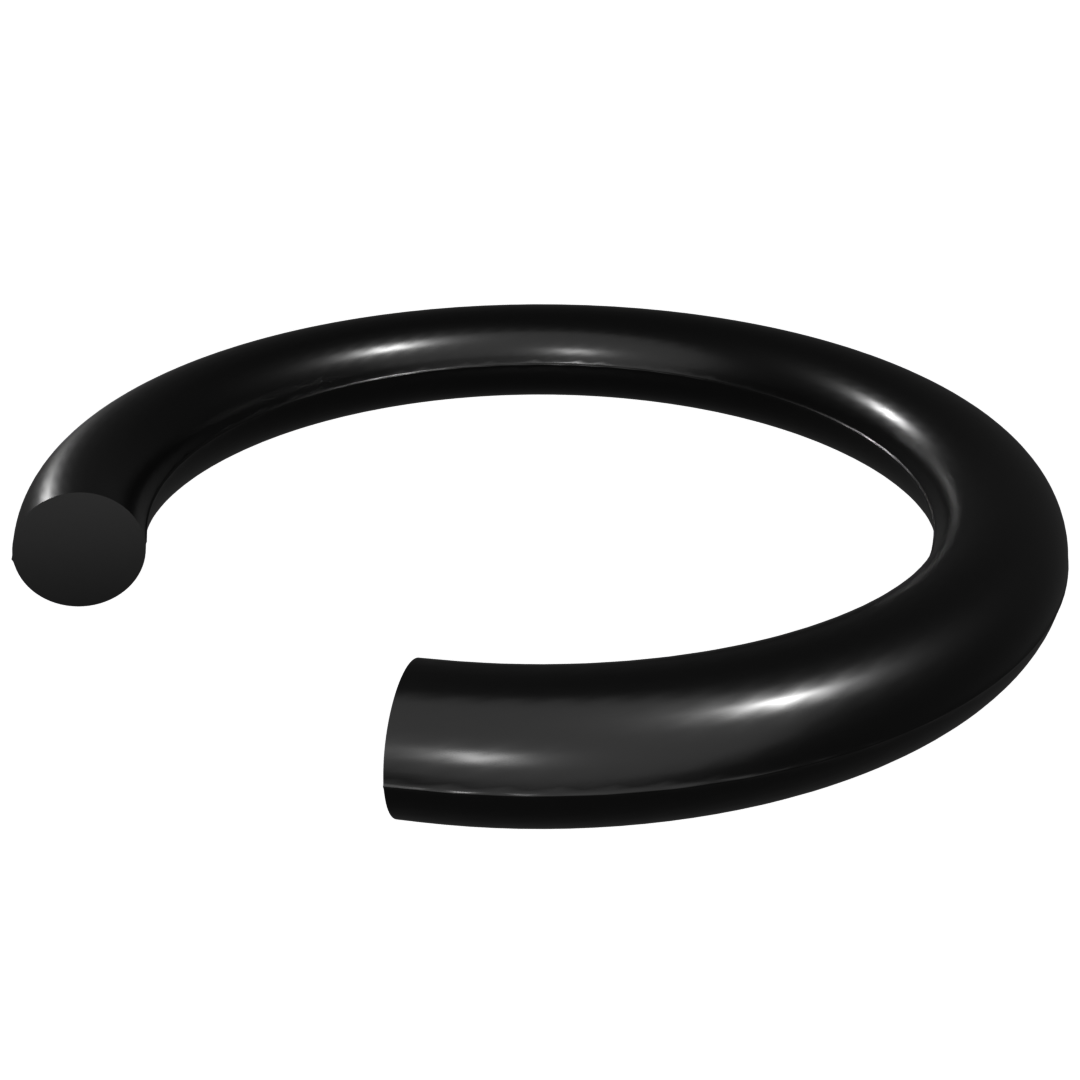
Features of HNBR
- HNBR O-rings, gaskets, & custom molded parts have a relative low cost
- HNBR O-rings, gaskets, & custom molded parts have enhanced chemical compatibility with many fuels
- HNBR O-rings, gaskets, & custom molded parts have increased resistance to ozone and weathering
- HNBR O-rings, gaskets, & custom molded parts have excellent resistance to compression set and tear/abrasion.
- HNBR O-rings, gaskets, & custom molded parts have excellent resistance to many fuels and aliphatic hydrocarbons (propane, butane, diesel fuel, fuel oils) as well as ethylene-glycol based fluids
- HNBR O-rings, gaskets, & custom molded parts are compatible with HFA, HFB and HFC fluids
- HNBR O-rings, gaskets, & custom molded parts are available in multiple compounds to meet performance and cost requirements
Limitations of HNBR
- HNBR O-rings, gaskets, & custom molded parts have poor resistance to polar solvents, aromatic/chlorinated hydrocarbons, and strong acids
- HNBR O-rings, gaskets, & custom molded parts have a Service Temperature Range of (varies with application): -40°F to 300° F (-40°C to 150°C)
Please consult a Canyon Components Engineer about your specific application and we will use our decades of experience to formulate a solution that fits your need.
HNBR (Hydrogenated Nitrile) Materials Available
This table shows many of our standard materials and links out to our O-ring store. Get in touch with us if you need a custom gasket, custom molded part, or non-standard geometry!
Filter by
Temperature Search (°C)
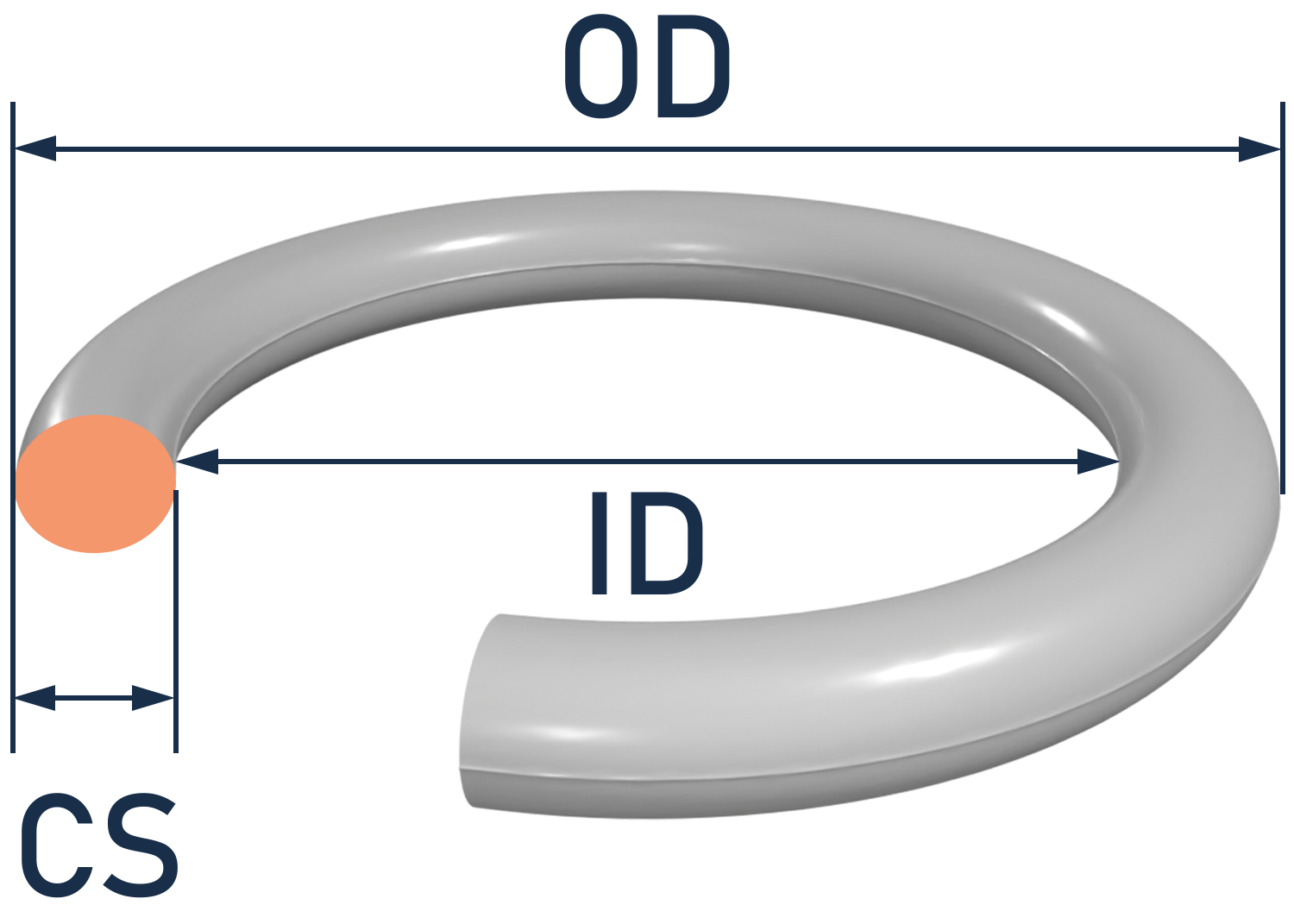
Back to Elastomers Hub
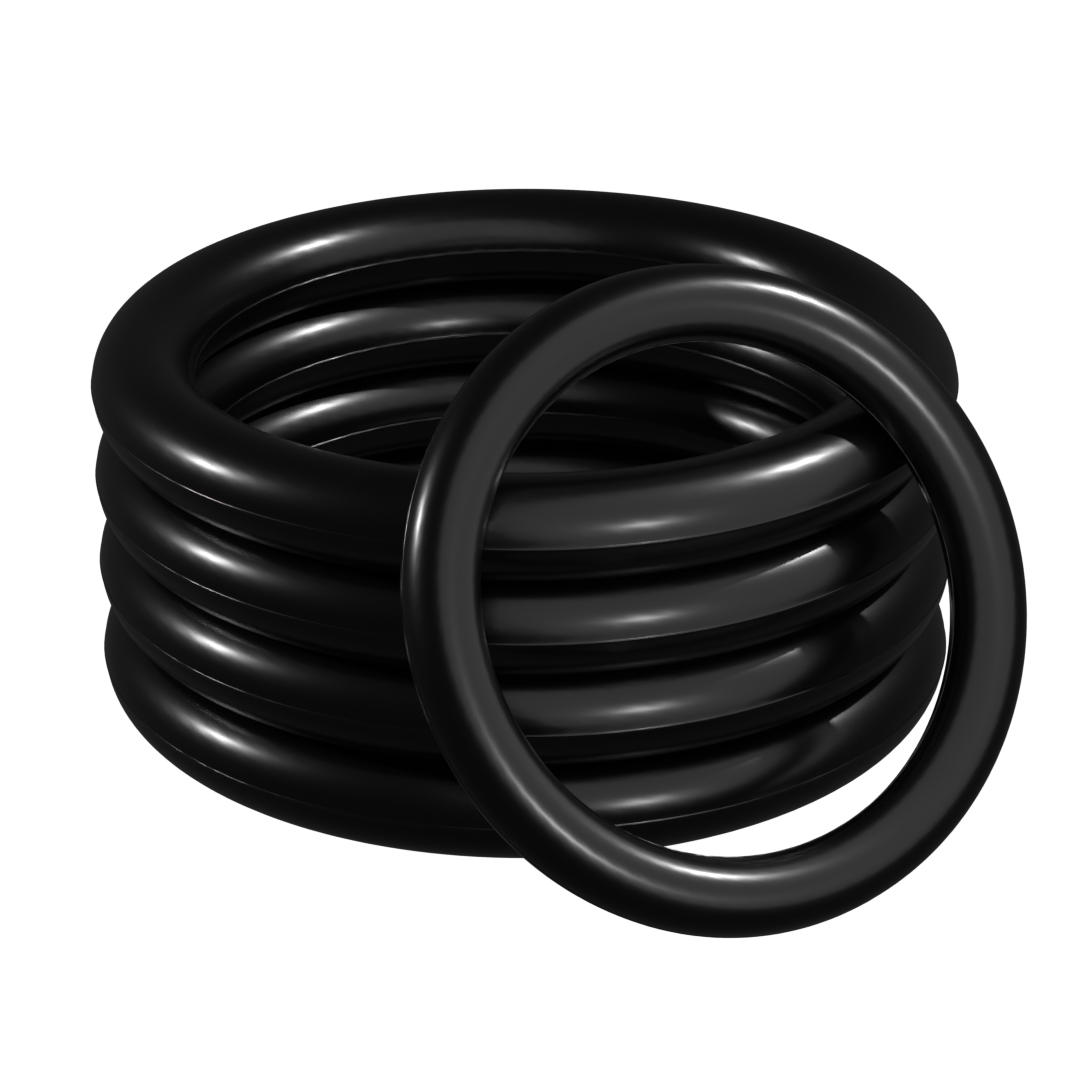
Get A Quote Now!
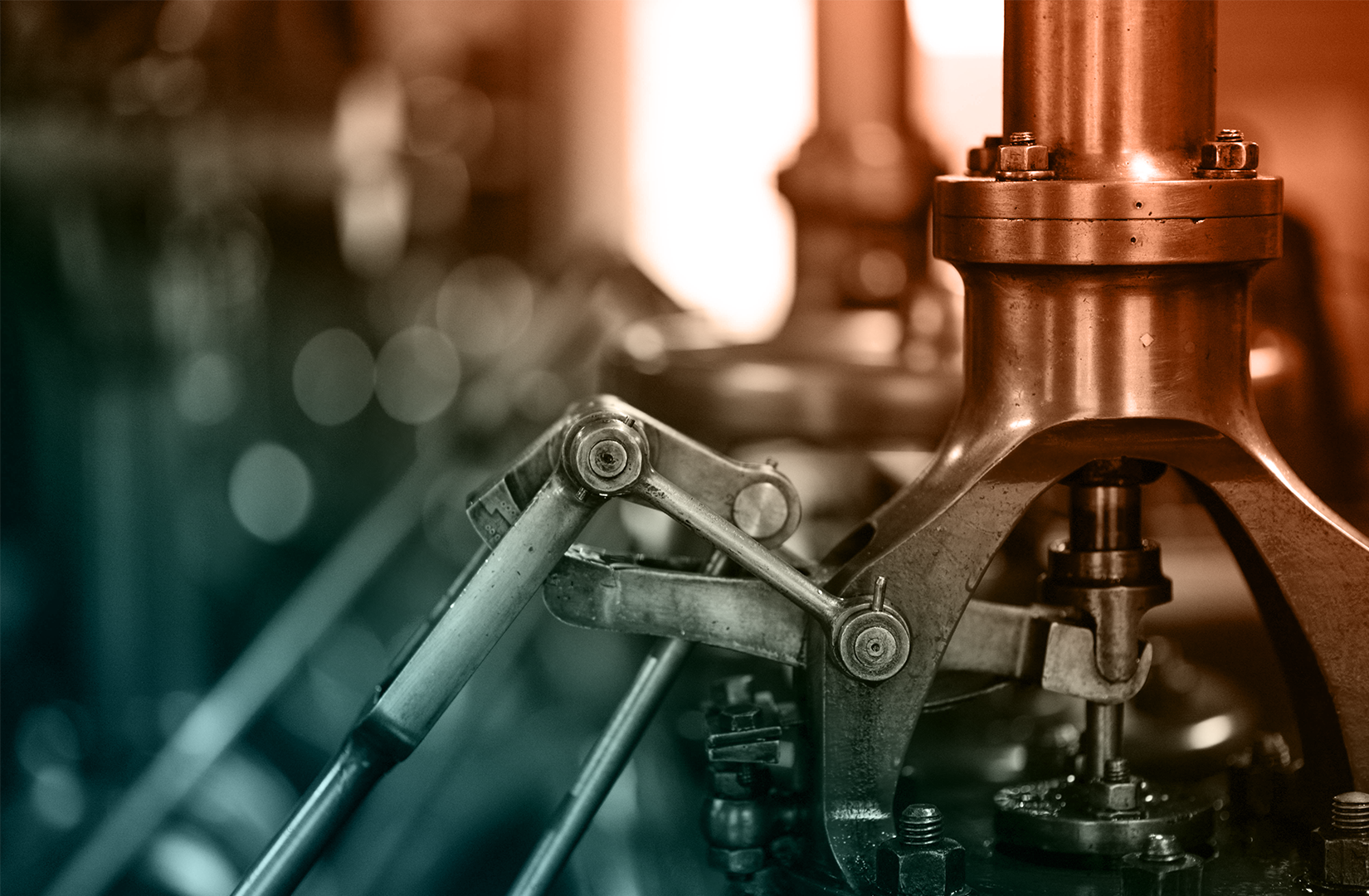
Groove Design References
Learn More
Coatings, Packaging, & Other Services
Learn More
Custom Parts & Custom O-rings
Learn More
Can you use HNBR O-rings for fuel?
HNBR (Hydrogenated Nitrile Butadiene Rubber) O-rings are suitable for certain fuel applications, but their compatibility with fuels depends on several factors, including the type of fuel, the concentration, and the specific formulation of the HNBR material. Here are some considerations:
1. Type of Fuel: HNBR O-rings are generally compatible with many hydrocarbon-based fuels, including gasoline (petrol), diesel fuel, biodiesel (B100), and some aviation fuels. They offer good resistance to these fuels and can maintain their sealing properties when in contact with them.
2. Fuel Concentration: The compatibility of HNBR with fuels can vary depending on the concentration of the fuel and the duration of exposure. HNBR is typically more resistant to intermittent or short-term exposure to fuels than long-term immersion.
3. Additives: Some fuels contain additives, such as ethanol in gasoline or various chemicals in aviation fuels. Compatibility with these additives may vary, and it's important to check whether the specific HNBR material used is resistant to them.
4. Temperature: The operating temperature of the fuel application should also be considered. HNBR has a temperature range of approximately -40°C (-40°F) to 165°C (329°F) or higher, making it suitable for many fuel-related applications.
5. Sealing Environment: The design of the sealing system and the conditions of use can impact the performance of HNBR O-rings in fuel applications. Factors such as pressure, vibration, and mechanical stresses should be taken into account.
It's important to consult with Canyon Components engineers to select the appropriate HNBR material that is specifically formulated for fuel applications. They can provide guidance on the compatibility of the HNBR material with the specific fuel and conditions of your application. Additionally, industry standards and regulations may have specific requirements for O-ring materials used in fuel systems, so it's essential to ensure compliance with such standards when selecting materials for critical applications.
Is HNBR an elastomer?
Yes, HNBR (Hydrogenated Nitrile Butadiene Rubber) is an elastomer. Elastomers are a class of polymers known for their excellent elasticity and flexibility. HNBR, like its base material Nitrile Butadiene Rubber (NBR), exhibits elastomeric properties.
Elastomers, including HNBR, have the following characteristics:
1. Elasticity: Elastomers can deform under stress and return to their original shape when the stress is removed. This property makes them suitable for sealing and gasket applications, where they can maintain a tight seal even under compression.
2. Flexibility: Elastomers are highly flexible, allowing them to accommodate movement and deformation without permanent damage.
3. High Resilience: Elastomers have a high resilience, meaning they can absorb and dissipate energy, making them suitable for shock-absorbing and damping applications.
HNBR, in particular, is a specialized elastomer known for its enhanced properties, including improved resistance to heat, chemicals, and ozone. It retains the elastomeric characteristics that make it suitable for sealing and gasket applications while offering additional benefits in demanding environments.
Is HNBR the same as Buna?
No, HNBR (Hydrogenated Nitrile Butadiene Rubber) is not the same as Buna (NBR). NBR (Nitrile Butadiene Rubber) and HNBR (Hydrogenated Nitrile Butadiene Rubber) are both synthetic elastomers known for their excellent resistance to oil, fuel, and chemicals. However, they differ in their chemical structure and performance characteristics. Here are the key differences between NBR and HNBR:
1. Chemical Structure:
- NBR: NBR is a copolymer of butadiene and acrylonitrile. It contains a nitrile group in its chemical structure, which provides oil and fuel resistance. The acrylonitrile content in NBR can vary, affecting its overall properties.
- HNBR: HNBR is a modified version of NBR. It is also a copolymer of butadiene and acrylonitrile, but it undergoes hydrogenation, which involves the addition of hydrogen atoms to the polymer chain. This hydrogenation process enhances its resistance to heat, ozone, and chemicals.
2. Oil and Fuel Resistance:
- NBR: NBR offers good oil and fuel resistance and is commonly used in applications involving petroleum-based oils, fuels, and lubricants.
- HNBR: HNBR provides excellent oil and fuel resistance, often surpassing the performance of standard NBR. It is preferred in applications where exposure to automotive engine oils and transmission fluids is common.
3. Temperature Range:
- Buna-N (NBR) has a temperature range of approximately -40°F to 257°F (-40°C to 125°C), which is generally lower than HNBR.
- HNBR has a higher temperature resistance compared to standard NBR. It can typically handle temperatures ranging from -40°F to 329°F (-40°C to 165°C) or higher, depending on the specific grade.
4. Chemical Resistance:
- NBR: NBR exhibits good resistance to many chemicals but may not perform as well as HNBR in highly aggressive chemical environments.
- HNBR: HNBR offers excellent chemical resistance to a broader range of chemicals, acids, and solvents compared to NBR.
5. Ozone and Weathering Resistance:
- NBR: NBR is susceptible to ozone and weathering degradation over time.
- HNBR: HNBR has improved resistance to ozone and weathering due to its hydrogenated structure.
6. Applications:
- NBR: NBR is commonly used in automotive seals, O-rings, gaskets, and hoses, especially in applications involving petroleum-based fluids.
- HNBR: HNBR is preferred in automotive applications where exposure to engine oils and transmission fluids is significant. It is also used in chemical processing, oil and gas industry, and other applications requiring enhanced chemical and temperature resistance.
In summary, while both NBR and HNBR offer good oil and fuel resistance, HNBR provides superior performance in terms of temperature resistance, chemical resistance, and resistance to ozone and weathering. The choice between the two depends on the specific requirements of the application, with HNBR being the preferred choice in demanding environments.
Is Nitrile a type of HNBR?
No, Nitrile (NBR) is not a type of HNBR (Hydrogenated Nitrile Butadiene Rubber). While both NBR and HNBR are synthetic rubber materials, they are distinct and have different chemical compositions and properties.
Here are the key differences between Nitrile (NBR) and Hydrogenated Nitrile (HNBR):
1. Chemical Structure:
- NBR: NBR is a copolymer of butadiene and acrylonitrile. It contains a nitrile group in its chemical structure, which provides oil and fuel resistance. The acrylonitrile content in NBR can vary, affecting its overall properties.
- HNBR: HNBR is a modified version of NBR. It is also a copolymer of butadiene and acrylonitrile, but it undergoes hydrogenation, which involves the addition of hydrogen atoms to the polymer chain. This hydrogenation process enhances its resistance to heat, ozone, and chemicals.
2. Oil and Fuel Resistance:
- NBR: NBR offers good oil and fuel resistance and is commonly used in applications involving petroleum-based oils, fuels, and lubricants.
- HNBR: HNBR provides excellent oil and fuel resistance, often surpassing the performance of standard NBR. It is preferred in applications where exposure to automotive engine oils and transmission fluids is common.
3. Temperature Range:
- Buna-N (NBR) has a temperature range of approximately -40°F to 257°F (-40°C to 125°C), which is generally lower than HNBR.
- HNBR has a higher temperature resistance compared to standard NBR. It can typically handle temperatures ranging from -40°F to 329°F (-40°C to 165°C) or higher, depending on the specific grade.
4. Chemical Resistance:
- NBR: NBR exhibits good resistance to many chemicals but may not perform as well as HNBR in highly aggressive chemical environments.
- HNBR: HNBR offers excellent chemical resistance to a broader range of chemicals, acids, and solvents compared to NBR.
5. Ozone and Weathering Resistance:
- NBR: NBR is susceptible to ozone and weathering degradation over time.
- HNBR: HNBR has improved resistance to ozone and weathering due to its hydrogenated structure.
6. Applications:
- NBR: NBR is commonly used in automotive seals, O-rings, gaskets, and hoses, especially in applications involving petroleum-based fluids.
- HNBR: HNBR is preferred in automotive applications where exposure to engine oils and transmission fluids is significant. It is also used in chemical processing, oil and gas industry, and other applications requiring enhanced chemical and temperature resistance.
In summary, HNBR is a modified and enhanced version of NBR that offers superior properties, particularly in terms of temperature and chemical resistance. Nitrile (NBR) and Hydrogenated Nitrile (HNBR) are distinct materials, and the choice between them depends on the specific requirements of the application.
Is Viton a type of HNBR?
No, Viton (a brand of FKM, fluoroelastomer) is not the same as HNBR (Hydrogenated Nitrile Butadiene Rubber). These are two distinct types of synthetic rubber with different chemical compositions and properties:
1. Viton (FKM):
- Composition: Viton is a type of fluoroelastomer, which contains fluorine, carbon, hydrogen, and sometimes other elements. It is known for its excellent chemical resistance to a wide range of chemicals, including oils, fuels, acids, and solvents. Viton has a high-temperature resistance, typically up to 225°C (437°F).
- Applications: It is commonly used in industries where resistance to harsh chemicals and high temperatures is critical, such as the chemical processing, automotive, aerospace, and oil and gas industries.
2. HNBR (Hydrogenated Nitrile Butadiene Rubber):
- Composition: HNBR is a hydrogenated version of Nitrile Butadiene Rubber (NBR). It is produced by adding hydrogen to NBR, which improves its heat and ozone resistance, as well as its overall mechanical properties.
- Properties: HNBR combines the oil and fuel resistance of NBR with improved heat resistance. It can withstand temperatures higher than standard NBR, typically up to 165°C (329°F). It also has good resistance to various oils and chemicals.
- Applications: HNBR is commonly used in automotive and industrial applications where resistance to high temperatures and exposure to oils and fuels is required, such as in automotive engine components, seals, and gaskets.
While both Viton and HNBR have excellent chemical resistance properties, they are used in different applications due to their specific characteristics. Viton is known for its broader chemical resistance, especially to harsh solvents and aggressive chemicals, while HNBR is valued for its balance of oil and fuel resistance with improved heat resistance. The choice between them depends on the specific requirements of the application.
Is Viton the same as HNBR?
No, Viton (a brand of FKM, fluoroelastomer) is not the same as HNBR (Hydrogenated Nitrile Butadiene Rubber). These are two distinct types of synthetic rubber with different chemical compositions and properties:
1. Viton (FKM):
- Composition: Viton is a type of fluoroelastomer, which contains fluorine, carbon, hydrogen, and sometimes other elements. It is known for its excellent chemical resistance to a wide range of chemicals, including oils, fuels, acids, and solvents. Viton has a high-temperature resistance, typically up to 225°C (437°F).
- Applications: It is commonly used in industries where resistance to harsh chemicals and high temperatures is critical, such as the chemical processing, automotive, aerospace, and oil and gas industries.
2. HNBR (Hydrogenated Nitrile Butadiene Rubber):
- Composition: HNBR is a hydrogenated version of Nitrile Butadiene Rubber (NBR). It is produced by adding hydrogen to NBR, which improves its heat and ozone resistance, as well as its overall mechanical properties.
- Properties: HNBR combines the oil and fuel resistance of NBR with improved heat resistance. It can withstand temperatures higher than standard NBR, typically up to 165°C (329°F). It also has good resistance to various oils and chemicals.
- Applications: HNBR is commonly used in automotive and industrial applications where resistance to high temperatures and exposure to oils and fuels is required, such as in automotive engine components, seals, and gaskets.
While both Viton and HNBR have excellent chemical resistance properties, they are used in different applications due to their specific characteristics. Viton is known for its broader chemical resistance, especially to harsh solvents and aggressive chemicals, while HNBR is valued for its balance of oil and fuel resistance with improved heat resistance. The choice between them depends on the specific requirements of the application.
What are the advantages of HNBR?
Hydrogenated Nitrile Butadiene Rubber (HNBR) is a highly saturated elastomer derived from nitrile rubber (NBR) through a hydrogenation process. This modification significantly enhances many of the material's properties, making HNBR a popular choice in various demanding applications. The key advantages of HNBR include:
1. Improved Temperature Resistance: HNBR can withstand higher temperatures compared to NBR. It typically operates effectively in the range of -40°C to +165°C, making it suitable for applications in hot environments.
2. Enhanced Chemical Resistance: HNBR offers excellent resistance to oils, fuels, and many other chemicals. This makes it ideal for use in the automotive and oil industries, where exposure to such substances is common.
3. Better Wear and Abrasion Resistance: The material exhibits superior durability and is less prone to wear and tearing. This property is particularly beneficial in dynamic sealing applications where components are in constant motion.
4. Strong Resistance to Atmospheric Conditions: HNBR is highly resistant to ozone, UV light, and other weathering elements, ensuring longevity and reliability in outdoor applications.
5. Excellent Mechanical Properties: It maintains high tensile strength, tear resistance, and compression set resistance, even under harsh conditions, making it suitable for high-stress applications.
6. Good Resistance to Heat Aging: HNBR is less likely to degrade over time when exposed to heat, which helps in maintaining its elasticity and sealing capabilities.
7. Compatibility with Various Additives: HNBR can be compounded with fillers and other additives to enhance its properties, such as flame retardancy or improved physical strength.
HNBR's combination of heat resistance, chemical resistance, and mechanical strength makes it a preferred choice for demanding applications, especially in the automotive, oil and gas, and heavy machinery industries. These advantages often outweigh its generally higher cost compared to other elastomers like NBR.
What are the disadvantages of HNBR?
Hydrogenated Nitrile Butadiene Rubber (HNBR) is a versatile elastomer with many advantages, but it also has some disadvantages and limitations that should be considered when choosing it for specific applications. Here are some disadvantages of HNBR:
1. Cost: HNBR tends to be more expensive than standard Nitrile Butadiene Rubber (NBR) due to the additional hydrogenation process required to produce it. This can make it less cost-effective for some applications.
2. Limited High-Temperature Resistance: While HNBR offers improved temperature resistance compared to NBR, it may not be suitable for extremely high-temperature applications. It typically has a temperature range of -40°C to 165°C (-40°F to 329°F), which is lower than some other high-temperature elastomers like Viton.
3. Not Ideal for Low-Temperature Applications: HNBR may become less flexible and more brittle at low temperatures. If your application involves extremely low temperatures, other elastomers like silicone may be more suitable.
4. Limited Chemical Compatibility: While HNBR offers improved resistance to oils, fuels, and many chemicals compared to NBR, it may still not be suitable for all chemical environments. In highly aggressive chemical applications, specialized elastomers like Viton or PTFE (Teflon) may be preferred.
5. Compression Set: HNBR can exhibit a moderate compression set, which means it may lose some of its sealing properties over time when subjected to constant compression or deformation.
6. Hardness Range: HNBR is available in a limited range of hardness levels. While it offers good mechanical properties, it may not provide the same level of flexibility or softness as some other elastomers.
7. Processing Difficulty: HNBR can be more challenging to process and fabricate than some other elastomers. Specialized equipment and expertise may be required for manufacturing HNBR components.
Despite these disadvantages, HNBR remains a valuable elastomer choice for many sealing and automotive applications due to its improved resistance to oils, fuels, and chemicals compared to standard NBR. The selection of HNBR or any other elastomer should be based on the specific requirements and operating conditions of the application to ensure optimal performance and durability.
What do different colored O-rings mean?
The color of an O-ring doesn't inherently signify a specific characteristic or quality; rather, it's often used as a means to identify different materials or specifications. Here's a general guide to what different colored O-rings might indicate:
1. Black: The most common color for O-rings, typically made of nitrile (Buna-N), neoprene, EPDM, or other general-purpose materials. These are widely used in various applications due to their good resistance to oils, fuels, and certain chemicals. However, it should be noted that virtually any elastomeric material can be, and will frequently be manufactured in black colorations. This includes specialty materials like Aflas, FFKM Perfluoroelastomers, and silicone.
2. Blue: Fluorosilicone O-rings are typically manufactured in blue colorations. Also, blue is often associated with FDA-approved materials that are safe for food, water, and beverage contact. Blue O-rings are also easily detectable, which helps in maintaining safety standards in food processing industries.
3. Green: Commonly indicates the presence of hydrogenated nitrile (HNBR), which offers better heat and chemical resistance compared to standard nitrile. Viton® (fluorocarbon rubber) can also frequently be found in green colorations.
4. Brown: Typically signifies the use of Viton® (fluorocarbon rubber), known for its excellent resistance to high temperatures and chemicals, including petroleum products.
5. Red, Orange, or Pink: Frequently used for silicone O-rings, which are known for their heat resistance and use in food-grade applications.
6. White or Clear: Often indicates that the O-ring is made from silicone, Teflon (PTFE), or another material that is suitable for sanitary or medical applications.
7. Yellow: May indicate special compounds, such as polyurethane, which are known for their wear resistance and strength.
8. Metal Detectable O-rings: These O-rings are infused with metal detectable materials and are often blue. They are used in the food and pharmaceutical industries where contamination by foreign objects is a critical concern.
It's important to note that these color associations are not universal and can vary between manufacturers. The color alone should not be relied upon to determine the material or suitability of an O-ring for a specific application. Always refer to the manufacturer's specifications or consult with a Canyon Components engineer when selecting an O-ring for a particular use.
What is HNBR used for?
HNBR (Hydrogenated Nitrile Butadiene Rubber) is a synthetic elastomer known for its excellent properties, making it suitable for various applications across different industries. Here are some common uses of HNBR:
1. Automotive Seals and Hoses: HNBR is widely used in the automotive industry for the manufacturing of seals, gaskets, O-rings, belts, and hoses. Its resistance to oils, fuels, and high temperatures makes it ideal for engine seals, transmission seals, and other critical automotive components.
2. Oil and Gas Industry: HNBR is employed in the oil and gas sector for applications such as seals, gaskets, and O-rings in downhole tools, drilling equipment, and pipeline components. Its resistance to hydrocarbons and chemicals is valuable in these harsh environments.
3. Aerospace: HNBR is used in the aerospace industry for various sealing applications, including gaskets, O-rings, and diaphragms. Its ability to withstand extreme temperatures and exposure to aviation fuels is essential in aircraft systems.
4. Industrial Machinery: HNBR finds applications in industrial machinery, including hydraulic systems, pumps, and compressors. Its resistance to hydraulic fluids and lubricants makes it suitable for these applications.
5. Chemical Processing: HNBR is utilized in chemical processing equipment for sealing applications where exposure to chemicals and elevated temperatures is common. It provides reliable sealing in pumps, valves, and reactors.
6. Seals for Refrigeration and HVAC: HNBR O-rings and seals are used in refrigeration and HVAC systems due to their resistance to refrigerants and exposure to temperature variations.
7. Food and Beverage Industry: In some cases, HNBR with FDA-compliant formulations is used in the food and beverage industry for seals and gaskets, particularly in applications where resistance to oils and high temperatures is required.
8. Medical Devices: HNBR can be used in medical devices where resistance to oils and chemicals is necessary. It is suitable for certain seals and components in medical equipment.
9. Consumer Products: HNBR can be found in consumer products like diving equipment, scuba regulators, and underwater cameras due to its resistance to saltwater and chemicals.
10. Power Generation: HNBR is used in power generation equipment, including seals for steam turbines, as it can withstand high-temperature steam and thermal cycling.
11. Pharmaceutical Manufacturing: In pharmaceutical manufacturing, HNBR seals can be used in equipment that handles chemicals and high-temperature processes.
12. Hydraulic Seals: HNBR is employed in hydraulic systems where it provides effective sealing in hydraulic cylinders, pumps, and valves.
Overall, HNBR's versatility, resistance to heat, chemicals, oils, and wear, as well as its durability, make it suitable for a wide range of demanding industrial applications. Its ability to maintain its properties in harsh conditions makes it a valuable material choice for many industries.
What is the ACN content of HNBR Rubber?
HNBR (Hydrogenated Nitrile Butadiene Rubber) is a synthetic elastomer known for its excellent resistance to heat, oil, and chemicals. The ACN (Acrylonitrile) content of HNBR rubber can vary depending on the specific formulation and application requirements. HNBR rubber typically has an ACN content ranging from 17% to 50%. The percentage of ACN in HNBR affects its physical properties, including its oil resistance, temperature resistance, and chemical resistance.
Here's a general overview of how ACN content can influence the properties of HNBR rubber:
1. Low ACN (26%-34%): HNBR with a lower ACN content tends to have better low-temperature flexibility but decreased resistance to automotive engine oils and transmission fluids.
2. Medium ACN (34%-40%): HNBR with a medium ACN content strikes a balance between low-temperature flexibility and resistance to oils and chemicals. It is often used in automotive seals, O-rings, and gaskets.
3. High ACN (40%-50%): HNBR with a higher ACN content offers excellent resistance to a wide range of chemicals, including acids, bases, and a variety of solvents. It is commonly used in applications where chemical resistance is critical, such as seals for downhole oil and gas equipment. It's low temperature performance tends to be worse.
The choice of HNBR with a specific ACN content depends on the intended application and the required combination of properties. Engineers and manufacturers select the appropriate ACN content to ensure that HNBR rubber performs optimally in their specific environments and conditions.
What is the difference between NBR and HNBR O-rings?
NBR (Nitrile Butadiene Rubber) and HNBR (Hydrogenated Nitrile Butadiene Rubber) are both synthetic elastomers known for their excellent resistance to oil, fuel, and chemicals. However, they differ in their chemical structure and performance characteristics. Here are the key differences between NBR and HNBR:
1. Chemical Structure:
- NBR: NBR is a copolymer of butadiene and acrylonitrile. It contains a nitrile group in its chemical structure, which provides oil and fuel resistance. The acrylonitrile content in NBR can vary, affecting its overall properties.
- HNBR: HNBR is a modified version of NBR. It is also a copolymer of butadiene and acrylonitrile, but it undergoes hydrogenation, which involves the addition of hydrogen atoms to the polymer chain. This hydrogenation process enhances its resistance to heat, ozone, and chemicals.
2. Oil and Fuel Resistance:
- NBR: NBR offers good oil and fuel resistance and is commonly used in applications involving petroleum-based oils, fuels, and lubricants.
- HNBR: HNBR provides excellent oil and fuel resistance, often surpassing the performance of standard NBR. It is preferred in applications where exposure to automotive engine oils and transmission fluids is common.
3. Temperature Range:
- Buna-N (NBR) has a temperature range of approximately -40°F to 257°F (-40°C to 125°C), which is generally lower than HNBR.
- HNBR has a higher temperature resistance compared to standard NBR. It can typically handle temperatures ranging from -40°F to 329°F (-40°C to 165°C) or higher, depending on the specific grade.
4. Chemical Resistance:
- NBR: NBR exhibits good resistance to many chemicals but may not perform as well as HNBR in highly aggressive chemical environments.
- HNBR: HNBR offers excellent chemical resistance to a broader range of chemicals, acids, and solvents compared to NBR.
5. Ozone and Weathering Resistance:
- NBR: NBR is susceptible to ozone and weathering degradation over time.
- HNBR: HNBR has improved resistance to ozone and weathering due to its hydrogenated structure.
6. Applications:
- NBR: NBR is commonly used in automotive seals, O-rings, gaskets, and hoses, especially in applications involving petroleum-based fluids.
- HNBR: HNBR is preferred in automotive applications where exposure to engine oils and transmission fluids is significant. It is also used in chemical processing, oil and gas industry, and other applications requiring enhanced chemical and temperature resistance.
In summary, while both NBR and HNBR offer good oil and fuel resistance, HNBR provides superior performance in terms of temperature resistance, chemical resistance, and resistance to ozone and weathering. The choice between the two depends on the specific requirements of the application, with HNBR being the preferred choice in demanding environments.
What is the difference between NBR and HNBR?
NBR (Nitrile Butadiene Rubber) and HNBR (Hydrogenated Nitrile Butadiene Rubber) are both synthetic elastomers known for their excellent resistance to oil, fuel, and chemicals. However, they differ in their chemical structure and performance characteristics. Here are the key differences between NBR and HNBR:
1. Chemical Structure:
- NBR: NBR is a copolymer of butadiene and acrylonitrile. It contains a nitrile group in its chemical structure, which provides oil and fuel resistance. The acrylonitrile content in NBR can vary, affecting its overall properties.
- HNBR: HNBR is a modified version of NBR. It is also a copolymer of butadiene and acrylonitrile, but it undergoes hydrogenation, which involves the addition of hydrogen atoms to the polymer chain. This hydrogenation process enhances its resistance to heat, ozone, and chemicals.
2. Oil and Fuel Resistance:
- NBR: NBR offers good oil and fuel resistance and is commonly used in applications involving petroleum-based oils, fuels, and lubricants.
- HNBR: HNBR provides excellent oil and fuel resistance, often surpassing the performance of standard NBR. It is preferred in applications where exposure to automotive engine oils and transmission fluids is common.
3. Temperature Range:
- Buna-N (NBR) has a temperature range of approximately -40°F to 257°F (-40°C to 125°C), which is generally lower than HNBR.
- HNBR has a higher temperature resistance compared to standard NBR. It can typically handle temperatures ranging from -40°F to 329°F (-40°C to 165°C) or higher, depending on the specific grade.
4. Chemical Resistance:
- NBR: NBR exhibits good resistance to many chemicals but may not perform as well as HNBR in highly aggressive chemical environments.
- HNBR: HNBR offers excellent chemical resistance to a broader range of chemicals, acids, and solvents compared to NBR.
5. Ozone and Weathering Resistance:
- NBR: NBR is susceptible to ozone and weathering degradation over time.
- HNBR: HNBR has improved resistance to ozone and weathering due to its hydrogenated structure.
6. Applications:
- NBR: NBR is commonly used in automotive seals, O-rings, gaskets, and hoses, especially in applications involving petroleum-based fluids.
- HNBR: HNBR is preferred in automotive applications where exposure to engine oils and transmission fluids is significant. It is also used in chemical processing, oil and gas industry, and other applications requiring enhanced chemical and temperature resistance.
In summary, while both NBR and HNBR offer good oil and fuel resistance, HNBR provides superior performance in terms of temperature resistance, chemical resistance, and resistance to ozone and weathering. The choice between the two depends on the specific requirements of the application, with HNBR being the preferred choice in demanding environments.
What is the difference between Nitrile and HNBR?
NBR (Nitrile Butadiene Rubber) and HNBR (Hydrogenated Nitrile Butadiene Rubber) are both synthetic elastomers known for their excellent resistance to oil, fuel, and chemicals. However, they differ in their chemical structure and performance characteristics. Here are the key differences between NBR and HNBR:
1. Chemical Structure:
- NBR: NBR is a copolymer of butadiene and acrylonitrile. It contains a nitrile group in its chemical structure, which provides oil and fuel resistance. The acrylonitrile content in NBR can vary, affecting its overall properties.
- HNBR: HNBR is a modified version of NBR. It is also a copolymer of butadiene and acrylonitrile, but it undergoes hydrogenation, which involves the addition of hydrogen atoms to the polymer chain. This hydrogenation process enhances its resistance to heat, ozone, and chemicals.
2. Oil and Fuel Resistance:
- NBR: NBR offers good oil and fuel resistance and is commonly used in applications involving petroleum-based oils, fuels, and lubricants.
- HNBR: HNBR provides excellent oil and fuel resistance, often surpassing the performance of standard NBR. It is preferred in applications where exposure to automotive engine oils and transmission fluids is common.
3. Temperature Range:
- Buna-N (NBR) has a temperature range of approximately -40°F to 257°F (-40°C to 125°C), which is generally lower than HNBR.
- HNBR has a higher temperature resistance compared to standard NBR. It can typically handle temperatures ranging from -40°F to 329°F (-40°C to 165°C) or higher, depending on the specific grade.
4. Chemical Resistance:
- NBR: NBR exhibits good resistance to many chemicals but may not perform as well as HNBR in highly aggressive chemical environments.
- HNBR: HNBR offers excellent chemical resistance to a broader range of chemicals, acids, and solvents compared to NBR.
5. Ozone and Weathering Resistance:
- NBR: NBR is susceptible to ozone and weathering degradation over time.
- HNBR: HNBR has improved resistance to ozone and weathering due to its hydrogenated structure.
6. Applications:
- NBR: NBR is commonly used in automotive seals, O-rings, gaskets, and hoses, especially in applications involving petroleum-based fluids.
- HNBR: HNBR is preferred in automotive applications where exposure to engine oils and transmission fluids is significant. It is also used in chemical processing, oil and gas industry, and other applications requiring enhanced chemical and temperature resistance.
In summary, while both NBR and HNBR offer good oil and fuel resistance, HNBR provides superior performance in terms of temperature resistance, chemical resistance, and resistance to ozone and weathering. The choice between the two depends on the specific requirements of the application, with HNBR being the preferred choice in demanding environments.
What is the trade name for HNBR?
The trade name for Hydrogenated Nitrile Butadiene Rubber (HNBR) can vary depending on the manufacturer or supplier, and there may not be a single universally recognized trade name for HNBR, similar to the way "Viton" is often used for fluoroelastomers (FKM).
However, some manufacturers and suppliers may have their own brand names or trade names for HNBR materials. These brand names are often used to distinguish their specific formulations or grades of HNBR. Some examples of trade names for HNBR include:
1. Therban: Therban is a trade name for HNBR products manufactured by ARLANXEO, a leading synthetic rubber producer.
2. Zetpol: Zetpol is another trade name for HNBR materials, often used by Zeon Corporation, a global elastomer manufacturer.
It's essential to check with the manufacturer or supplier of HNBR materials for the specific trade name associated with their product. Additionally, HNBR is often referred to simply by its acronym (HNBR) or its generic name, "hydrogenated nitrile butadiene rubber," in technical and industrial contexts.
What type of material is HNBR?
HNBR stands for "Hydrogenated Nitrile Butadiene Rubber." It is a synthetic elastomer or synthetic rubber that is derived from the polymerization of butadiene and acrylonitrile monomers, similar to Nitrile rubber (NBR or Buna-N). The key difference between HNBR and standard NBR lies in the hydrogenation process:
1. Nitrile Rubber (NBR): NBR is composed of butadiene and acrylonitrile monomers. It is known for its excellent resistance to oils, fuels, and lubricants, making it suitable for a wide range of industrial applications.
2. Hydrogenated Nitrile Butadiene Rubber (HNBR): HNBR is a modified version of NBR where additional hydrogen atoms are introduced into the polymer chain. This hydrogenation process enhances the material's overall properties, particularly its resistance to heat, chemicals, and ozone.
Key characteristics of HNBR include:
- Improved temperature resistance compared to standard NBR.
- Enhanced resistance to chemicals, including some aggressive fluids.
- Better resistance to ozone and UV exposure.
- Excellent mechanical properties, including good tensile strength and abrasion resistance.
- High resistance to automotive and industrial fluids, such as engine oils and transmission fluids.
HNBR is commonly used in automotive, aerospace, oil and gas, and industrial applications where durability, heat resistance, and chemical resistance are required. It is valued for its ability to maintain its properties in harsh environments and under high temperatures.
Which is better, Viton or HNBR?
Determining whether Viton or HNBR is better depends on the specific requirements of your application. Each material has its own set of properties and advantages, and the choice between them should be based on factors such as temperature resistance, chemical compatibility, and environmental conditions. Here's a comparison to help you decide:
Viton (Fluoroelastomer, FKM):
- Temperature Resistance: Viton excels in high-temperature applications, with the ability to withstand temperatures from -15°F to 400°F (-26°C to 204°C). It maintains its integrity at elevated temperatures.
- Chemical Resistance: Viton is highly resistant to a wide range of chemicals, including oils, fuels, lubricants, and most mineral acids. It is often chosen for applications involving aggressive chemicals.
- Ozone and UV Resistance: Viton exhibits good resistance to ozone and UV radiation, making it suitable for outdoor and exposed applications.
- Durability: Viton is known for its excellent durability and long service life, particularly in harsh environments.
- Applications: It is commonly used in industries such as automotive, aerospace, and chemical processing where extreme temperatures and chemical exposure are prevalent.
HNBR (Hydrogenated Nitrile Butadiene Rubber):
- Temperature Resistance: HNBR offers good temperature resistance, typically ranging from -40°F to 300°F (-40°C to 149°C). It is suitable for a wide range of temperature conditions.
- Chemical Resistance: HNBR has improved chemical resistance compared to standard Nitrile rubber (NBR). It is particularly resistant to oils, fuels, and some chemicals.
- Abrasion Resistance: HNBR exhibits good abrasion resistance, making it suitable for applications involving wear and tear.
- Applications: It is commonly used in automotive applications, including seals, belts, and hoses. It is also found in industrial applications where resistance to heat and chemicals is essential.
Summary:
- Viton is preferred for applications involving extremely high temperatures and aggressive chemicals. It is a top choice for the aerospace and chemical industries.
- HNBR is suitable for a wide range of applications, offering good temperature and chemical resistance. It is commonly used in automotive and industrial settings.
The choice between Viton and HNBR should be based on a detailed assessment of your specific application's requirements and conditions. Consult with material experts or engineers to ensure the most suitable material is chosen for your sealing needs.