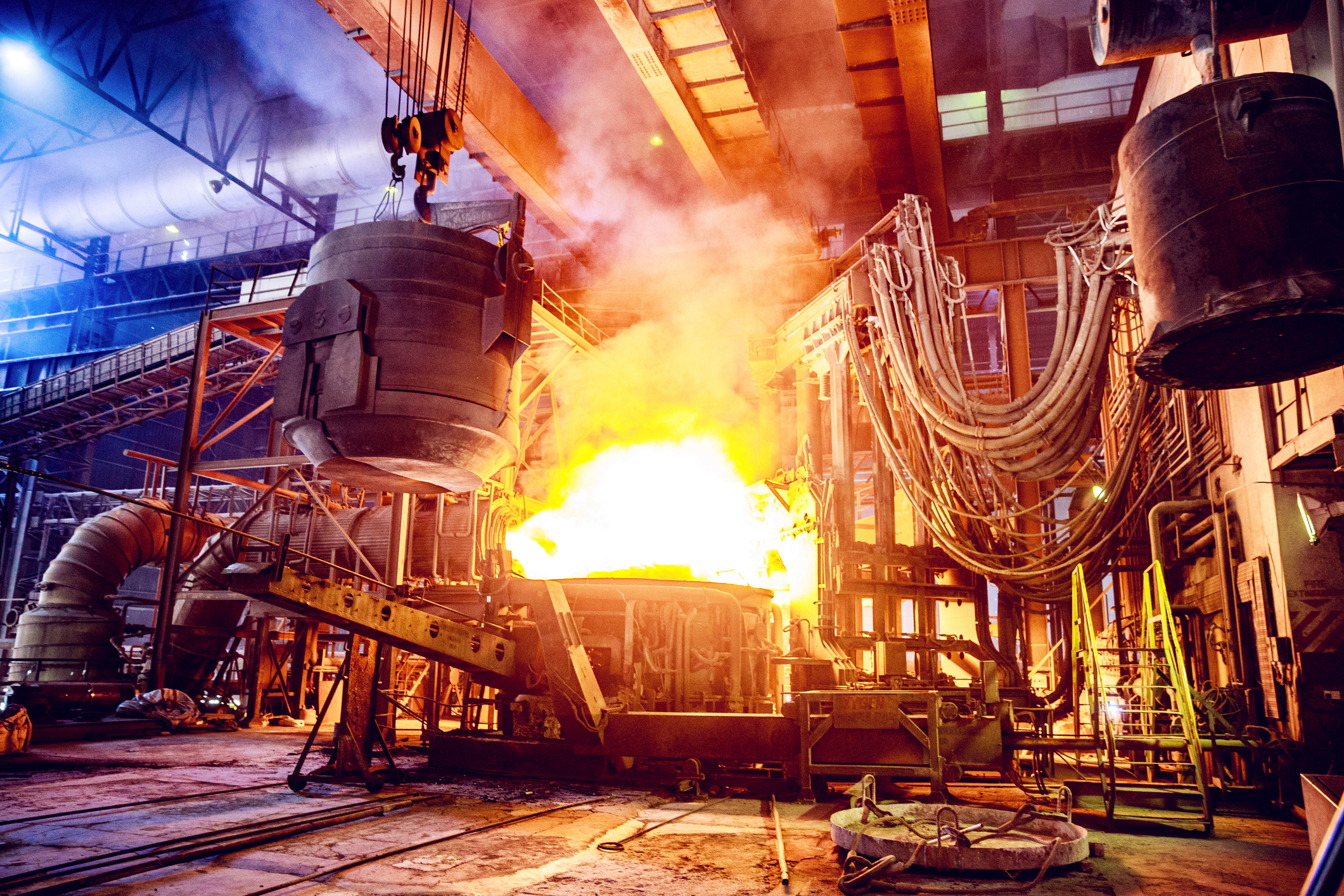
Braided Packing: Features, Applications, and Reliable Sealing Solutions
Braided packing seals are essential components used in a wide range of industries to provide reliable sealing in pumps, valves, and other equipment. These seals are constructed by weaving or braiding various materials into a durable and flexible form, offering excellent sealing performance in dynamic and static applications. This guide covers the types, features, common applications, and materials used in braided packing seals, including PTFE, fiberglass, graphite filament, flexible graphite, Grafoil, and various graphite/PTFE blends like GFO. We’ll also discuss the pros and cons of using braided packing seals in your systems.
CanRez® FFKM and Kalrez® grommets, O-rings, gasket rapid manufacturing, & custom molded parts are available now!
Check with one of Canyon’s helpful product engineers for an expert material and manufacturing recommendation.
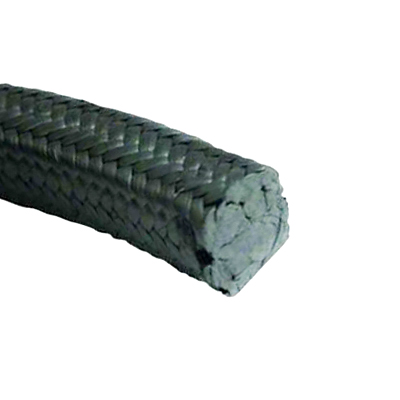
Features of Braided Packing Seals
Braided packing seals offer several features that make them suitable for a wide range of sealing applications:
- Excellent Sealing Performance: Braided packing provides effective sealing in both dynamic and static applications, preventing leakage of fluids and gases.
- High Durability: Braided packing seals are designed to withstand harsh operating conditions, including high pressures, extreme temperatures, and abrasive materials.
- Flexible and Resilient: The braided construction allows the packing to conform to irregular surfaces, ensuring a reliable seal even in challenging environments.
- Chemical Resistance: Depending on the material, braided packing seals can resist a wide range of chemicals, making them suitable for use in chemical processing, oil and gas, and industrial applications.
- Low Friction Options: Materials like PTFE and graphite are used to reduce friction, minimizing wear and extending the life of the seal.
Common Applications of Braided Packing Seals
Braided packing seals are used across various industries due to their versatility and reliability:
- Pumps: Braided packing is commonly used in centrifugal and reciprocating pumps to seal the shaft and prevent fluid leakage.
- Valves: In valve applications, braided packing provides a tight seal around the stem, preventing leaks of gases and fluids.
- Mixers and Agitators: Braided packing is used in mixers and agitators to seal rotating shafts, ensuring smooth operation and preventing product contamination.
- Chemical Processing: In chemical plants, braided packing seals are used to handle aggressive chemicals and high temperatures, ensuring leak-free operation.
- Oil and Gas: Braided packing is used in oilfield equipment, including valves, pumps, and compressors, where sealing performance and durability are critical.
Please consult a Canyon Components Engineer about your specific application and we will use our decades of experience to formulate a solution that fits your need.
Get a Quote Now!
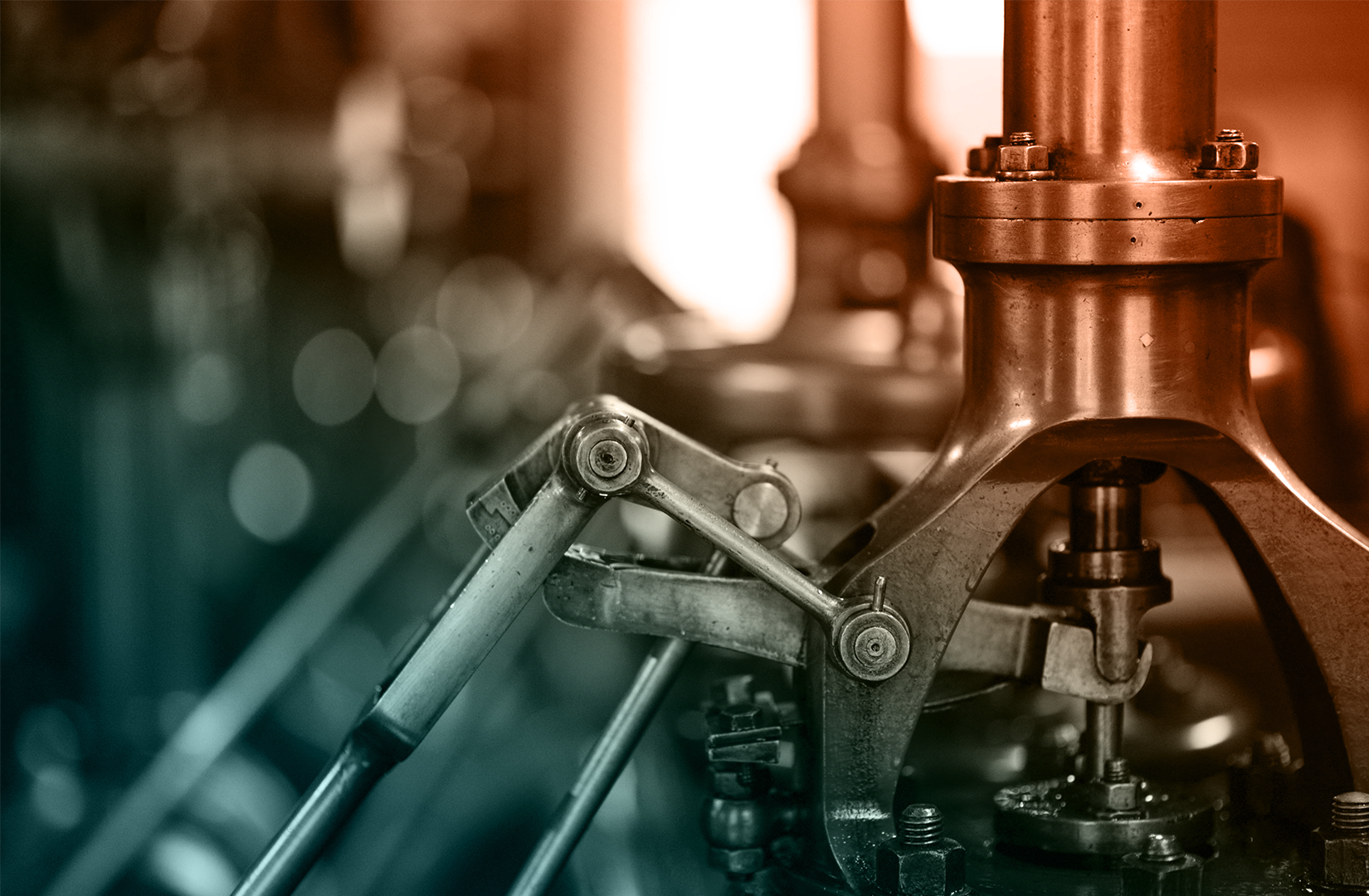
Types of Braided Packing Seals
Braided packing seals come in different types, each designed for specific applications and conditions:
- Square Braided Packing: This is the most common type of braided packing, used in pumps and valves to provide a reliable seal. The square cross-section allows it to fit snugly in the sealing cavity.
- Round Braided Packing: Round braided packing is used for special applications where round cavities are required, ensuring a perfect fit and even distribution of pressure.
- Interlocking Braided Packing: Interlocking braided packing offers enhanced durability and resistance to fraying, making it ideal for high-pressure applications.
- Lubricated Braided Packing: Lubricants such as PTFE or graphite are incorporated into the packing to reduce friction and heat, extending the life of the seal.
Canyon Components strives to meet all customer service requests. Feel free to contact Canyon Components engineering and let our knowledgeable staff help you design the perfect part for your needs.
Materials Used in Braided Packing Seals
PTFE (Polytetrafluoroethylene)
- Features: PTFE is known for its excellent chemical resistance, low friction, and high temperature tolerance. PTFE braided packing seals offer long-lasting performance in aggressive environments.
- Applications: PTFE braided packing is ideal for use in chemical processing, food and beverage, and pharmaceutical industries, where contamination and chemical resistance are critical.
- Pros: Excellent chemical resistance, low friction, non-reactive.
- Cons: Limited mechanical strength in high-pressure applications.
Fiberglass
- Features: Fiberglass is heat-resistant and strong, making it suitable for high-temperature applications. It is often used in conjunction with lubricants like PTFE or graphite to reduce wear.
- Applications: Fiberglass braided packing is commonly used in steam applications, boilers, and other high-temperature systems.
- Pros: High heat resistance, durable, cost-effective.
- Cons: Can be brittle under mechanical stress, limited chemical resistance.
Graphite Filament
- Features: Graphite filament provides excellent heat and chemical resistance, with low friction. It is suitable for use in high-temperature environments where traditional materials may fail.
- Applications: Graphite filament packing is used in high-pressure steam valves, pumps, and compressors in power generation and petrochemical industries.
- Pros: High temperature and chemical resistance, low friction.
- Cons: More expensive than other materials, can be prone to oxidation at extreme temperatures.
Flexible Graphite
- Features: Flexible graphite is compressible and highly resistant to chemicals, temperature, and pressure. It provides excellent sealing performance in extreme conditions.
- Applications: Flexible graphite packing is used in valves, pumps, and other critical applications in the chemical processing and oil and gas industries.
- Pros: Excellent thermal stability, chemical resistance, flexible.
- Cons: Can be susceptible to oxidation, higher cost.
Grafoil
- Features: Grafoil is a specific form of flexible graphite known for its high temperature and chemical resistance. It offers superior sealing capabilities in extreme conditions.
- Applications: Grafoil is used in high-temperature steam systems, chemical processing, and nuclear applications, where reliable performance is critical.
- Pros: Exceptional heat resistance, good for high-pressure and high-temperature environments.
- Cons: Expensive, may require additional coatings or treatments for extended life.
Graphite/PTFE Blends (Including GFO)
- Features: GFO is a patented blend of graphite, PTFE, and other materials designed to provide low friction, chemical resistance, and durability. These blends offer enhanced performance in demanding applications.
- Applications: GFO and similar graphite/PTFE blends are used in pumps, mixers, and valves where reduced friction and chemical resistance are required.
- Pros: Low friction, good chemical resistance, excellent performance in dynamic applications.
- Cons: Higher cost compared to standard PTFE or graphite packing.
Canyon Components strives to meet all customer service requests. Feel free to contact Canyon Components engineering and let our knowledgeable staff help you design the perfect part for your needs.
Product Types
Custom Parts
Here at Canyon Components, we make sure to offer our customers any manufacturing technique they desire. Whether your O-rings, gaskets, & custom molded parts be rubber, plastic, or metal, rest assured that Canyon Components can make it!
Gaskets & Custom Cutting
Whether your custom cut parts be rubber, plastic, sponge, composite, or metal, rest assured that Canyon Components can make it! Canyon Components strives to meet all customer service requests. If you need something that isn't listed, feel free to contact a Canyon Components product and application consultant.
Infinite "Giant" Diameter O-Rings
By either Continuous Molding O-rings, or Splice & Vulcanizing O-rings, Canyon can provide mold-less, infinitely large O-rings at competitive prices!
Specialty Compliances
Canyon have materials available for O-rings, gaskets, & custom parts with compliances ranging from USP Class VI <87> & <88> for medical applications, to FDA CFR 21.177.2600 grades A through F for different food types, to the various drinking water specifications like KTW and NSF. Whether it's metal, rubber, or plastic, Canyon can meet your needs!
Braided Packing Seals Pros & Cons
Braided packing seals are a versatile and reliable sealing solution for a wide range of industries and applications. With materials such as PTFE, fiberglass, graphite filament, flexible graphite, and graphite/PTFE blends like GFO, these seals provide excellent performance in extreme conditions, including high temperatures, chemical exposure, and dynamic environments. While they require regular maintenance and careful installation, the cost-effectiveness and durability of braided packing seals make them a valuable choice for pumps, valves, and other critical equipment. Understanding the features, applications, and potential drawbacks of braided packing seals will help you make informed decisions to ensure optimal performance in your systems.
Canyon Components strives to meet all customer service requests. Feel free to contact Canyon Components engineering and let our knowledgeable staff help you design the perfect part for your needs.
Pros of Braided Packing Seals
Braided packing seals offer several advantages that make them a preferred choice in many applications:
- Versatility: Braided packing can be used in a wide range of applications, from low-pressure pumps to high-temperature valves.
- Durability: These seals are designed to withstand extreme conditions, providing long-lasting performance.
- Customizable: With various materials available, braided packing seals can be tailored to meet specific needs, such as chemical resistance or temperature tolerance.
- Cost-Effective: Braided packing is generally more affordable than other sealing technologies, such as mechanical seals, while still offering reliable performance.
Cons of Braided Packing Seals
While braided packing seals are highly effective, there are also some potential drawbacks to consider:
- Maintenance Requirements: Braided packing seals may require more frequent maintenance and adjustment than other sealing technologies.
- Friction and Wear: Depending on the material, braided packing can generate friction and wear, potentially leading to energy losses and shorter service life in some applications.
- Installation Challenges: Proper installation is critical to ensuring the effectiveness of braided packing, and improper installation can lead to leaks or reduced performance.
Back to Products Hub
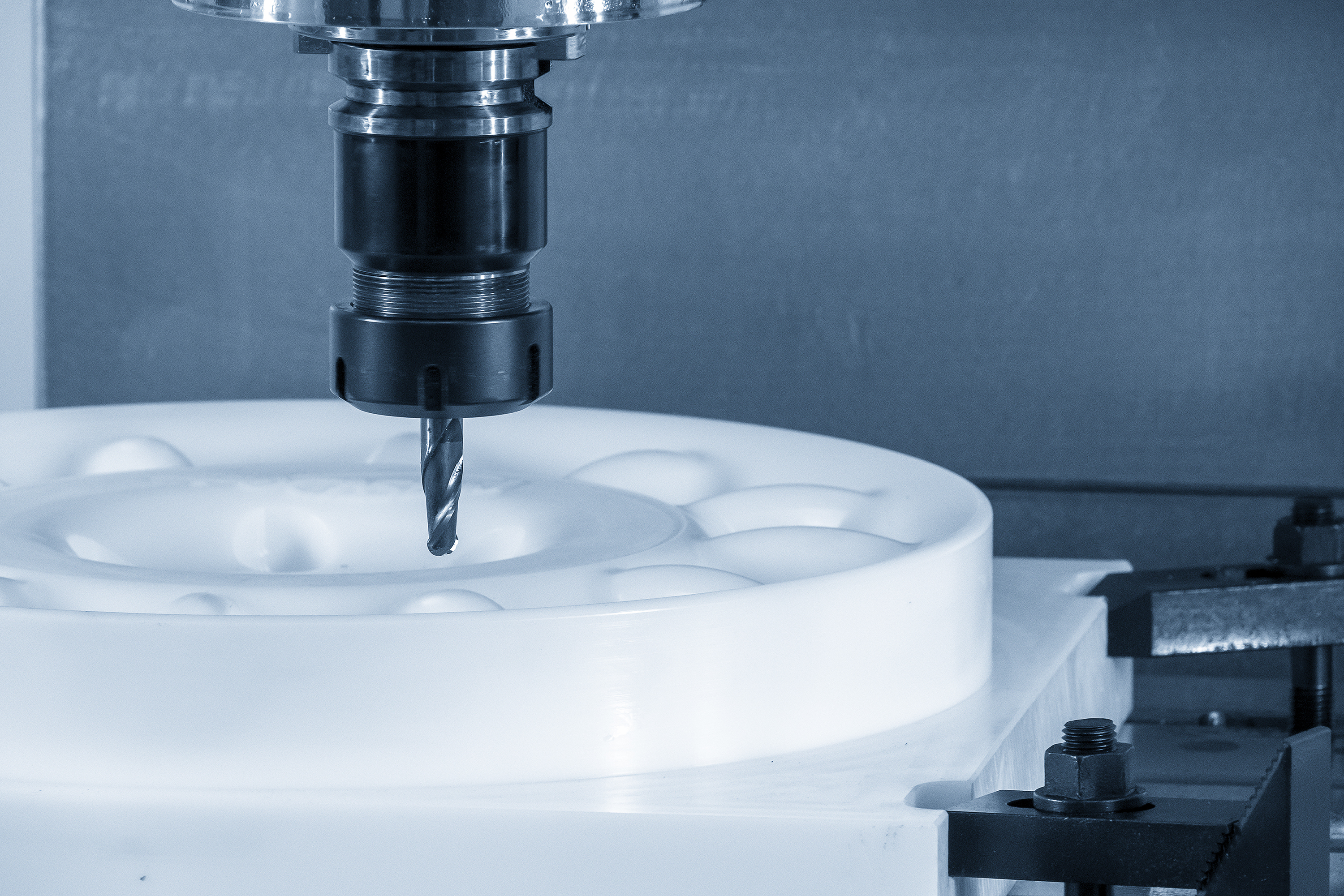
Get A Quote Now!
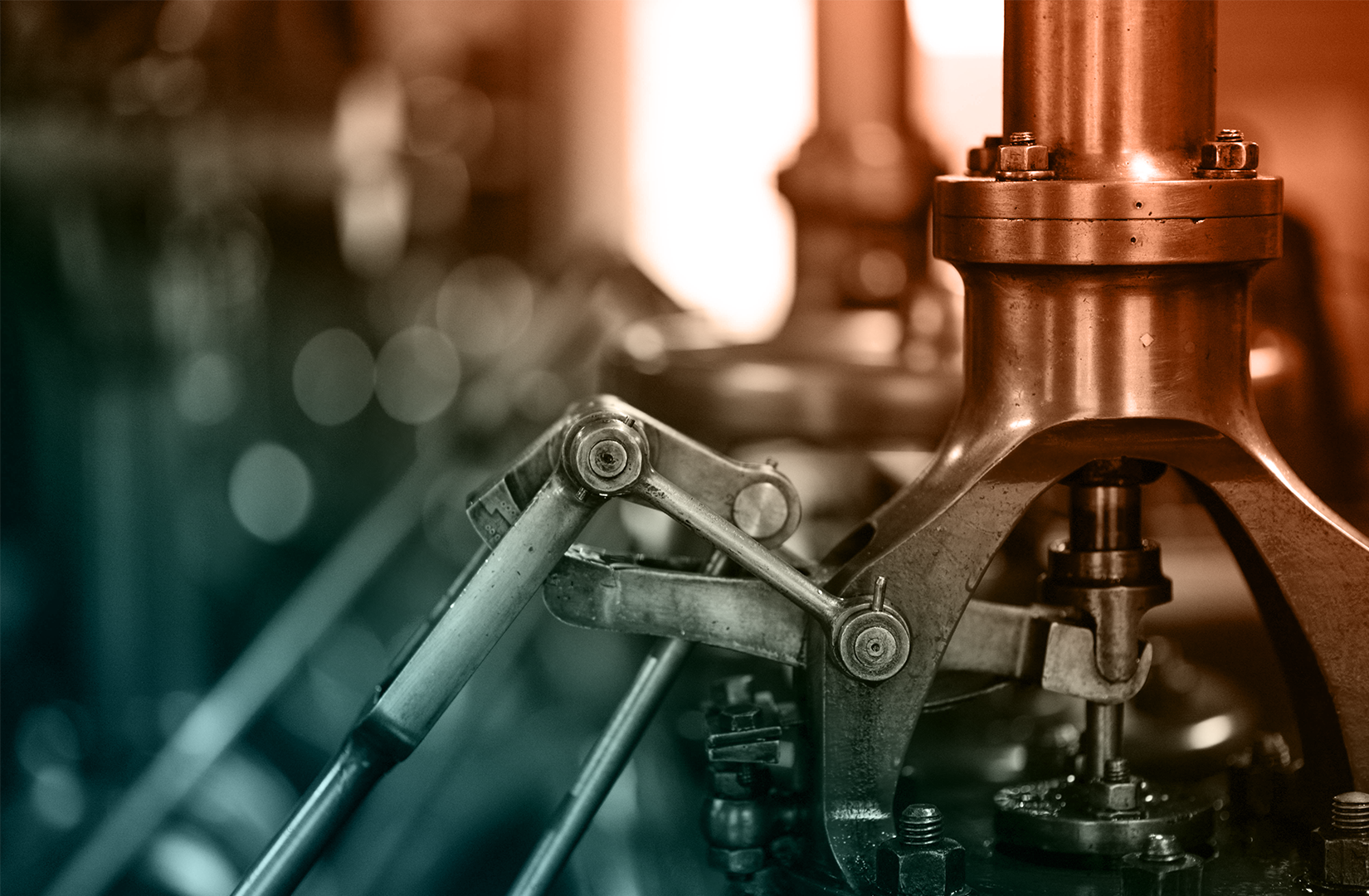