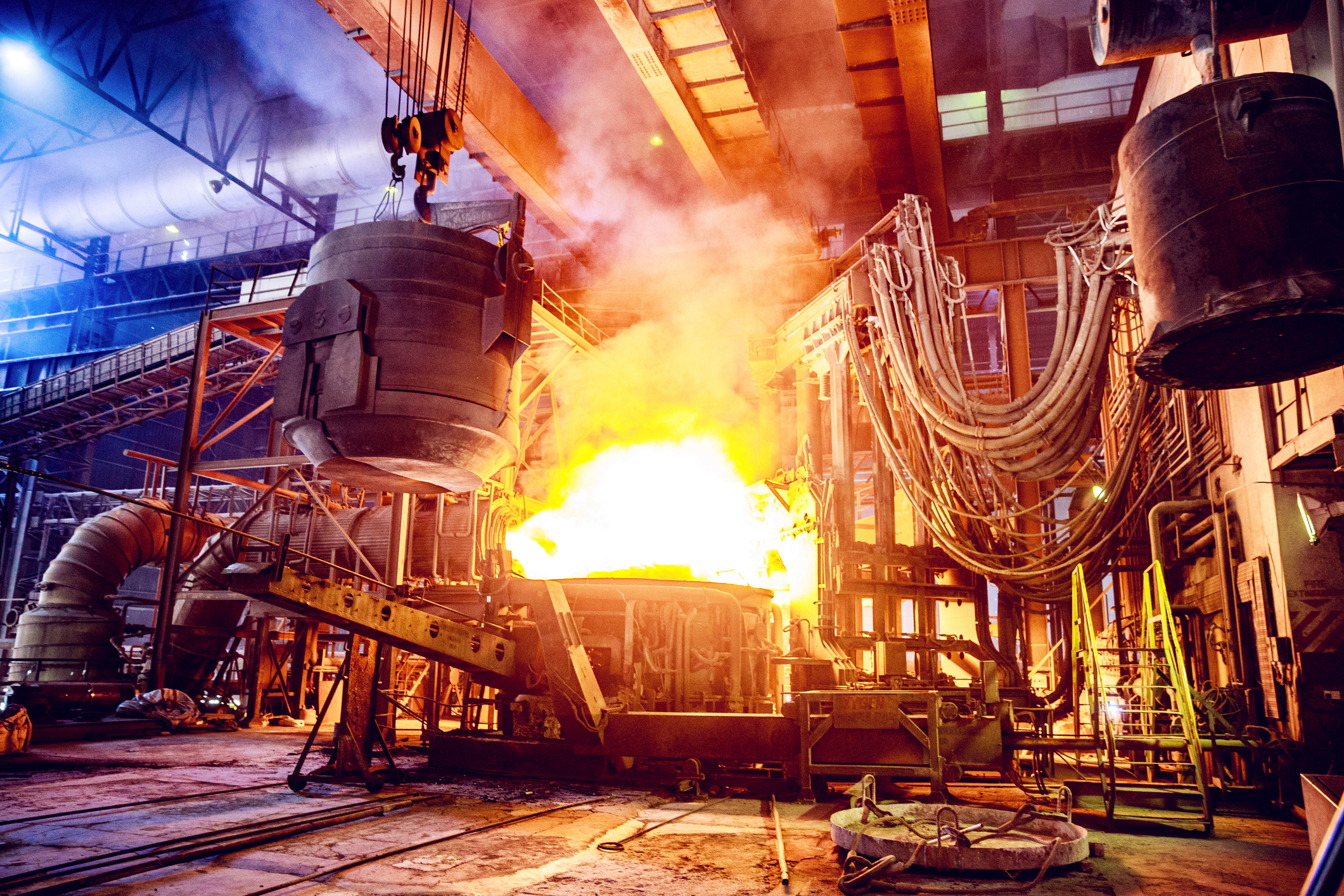
FKM (Viton™, Fluorocarbon) Selection Guide
Fluorocarbons are available in a wide range of elastomers, O-rings, gaskets, & custom molded parts, where the fluorine content greatly affects the physical and chemical properties of the material. In general, FKM compounds, O-rings, gaskets, & custom molded parts exhibit excellent mechanical attributes as well as excellent resistance to high temperatures, mineral oil, ozone, fuels, hydraulic fluids, and many other solvents and chemicals. FKM polymers, O-rings, gaskets, & custom molded parts are widely used in chemical, automotive, aerospace and industrial applications. The properties of Fluorocarbon compounds, O-rings, gaskets, & custom molded parts differ significantly based on their composition. Often increased fluid resistance for FKM O-rings, gaskets, & custom molded parts comes at the cost of a slight decrease in compression set or low temperature resistance.
The engineers and consultants here at Canyon Components take pride in finding the perfect seal to suit our customer’s needs. Contact our expert staff for assistance with any seal or application questions!
Common names include: FKM (Fluorocarbon), Fluoropolymer. Trade Names: Viton™, Fluorel®, Technoflon®, Dai-El®, FEPM.
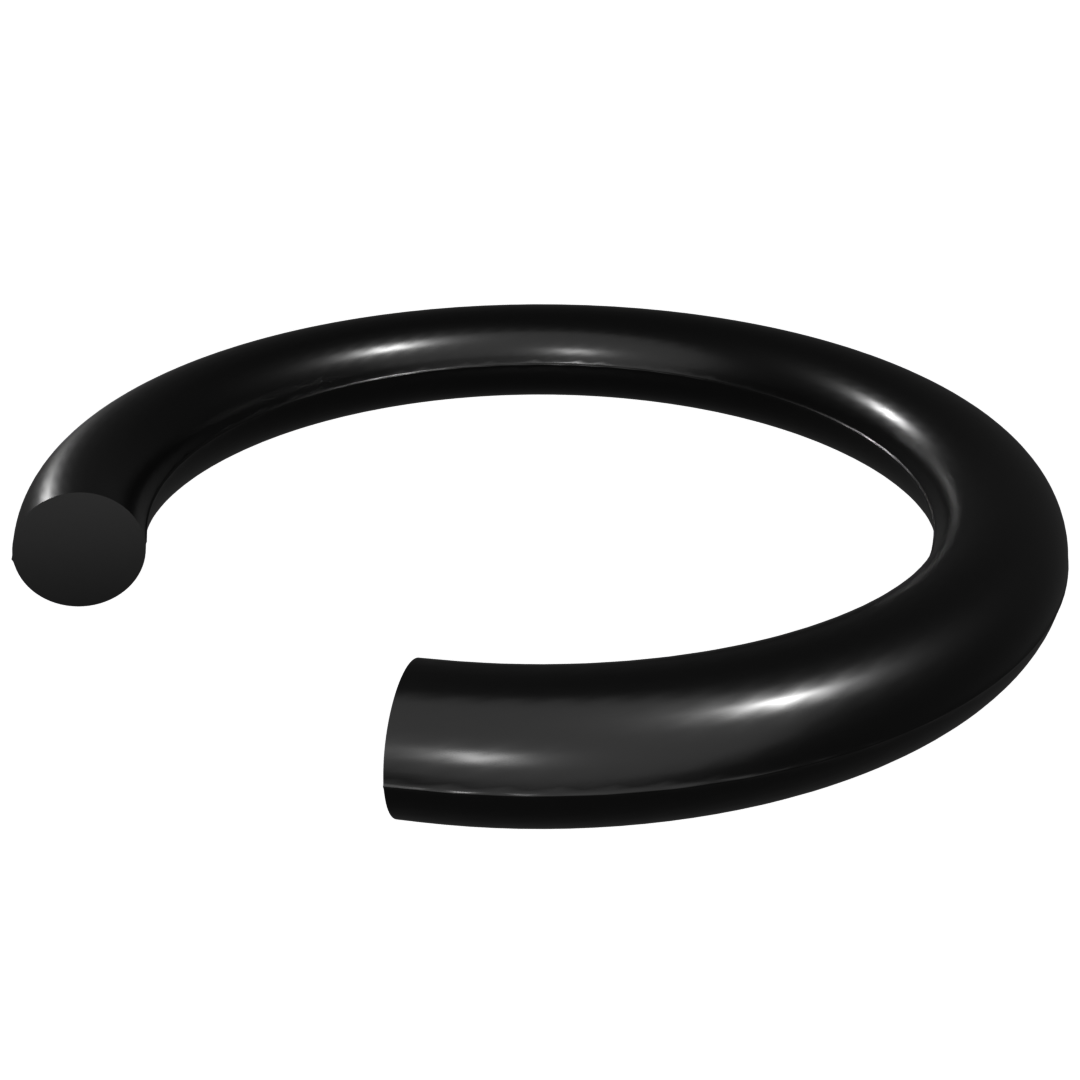
Features of FKM (Viton™)
- FKM O-rings, gaskets, & custom molded parts have excellent high temperature resistance
- FKM O-rings, gaskets, & custom molded parts have excellent resistance to acids, fuels, mineral and vegetable oils and greases, aliphatic, aromatic and chlorinated hydrocarbons, non-flammable hydraulic fluids (HFD) and many organic solvents and chemicals
- FKM O-rings, gaskets, & custom molded parts have low swelling in ASTM oil No. 1, and IRM 902 and IRM 903
- FKM O-rings, gaskets, & custom molded parts have excellent resistance to ozone, weather, and aging
- FKM O-rings, gaskets, & custom molded parts have low gas permeability
- FKM O-rings, gaskets, & custom molded parts have low compression set
- FKM O-rings, gaskets, & custom molded parts are available in multiple compounds to meet performance and cost requirements
Limitations of FKM (Viton™)
- FKM O-rings, gaskets, & custom molded parts have poor resistance to superheated steam or hot water
- FKM O-rings, gaskets, & custom molded parts have poor resistance to amines, polar solvents, low molecular weight organic solvents and glycol-based brake fluids. Learn more about Viton™ ETP for extreme chemical resistance.
- FKM O-rings, gaskets, & custom molded parts are not compatible with ammonia gas or low molecular weight organic acids
- FKM O-rings, gaskets, & custom molded parts have a Service Temperature Range of (varies with application): Typically 2°F to 400°F (-16°C to 204°C) *Specialty compounds allow range of -67°F to 432°F (-55°C to 222°C). Learn more about Low Temperature Viton™.
Please consult a Canyon Components Engineer about your specific application and we will use our decades of experience to formulate a solution that fits your need.
FKM & Viton™ High Performance Polymer Types
There are many types of FKM Polymer Types that Canyon Components offers.
This includes FKM Types A, B, F, GLT, GFLT, XLT, ULT, ETP, & TBR.
The table below is a Viton™ selection guide that lays out the pluses and minuses of each variation.
Key: 1 = Excellent 2 = Good 3 = Poor 4 = Not Recommended
Types of FKM | A | GF | GLT | GLT ED | GFLT | XLT | ETP | |||||||
---|---|---|---|---|---|---|---|---|---|---|---|---|---|---|
Canyon Compound Number | VT75BK00 | VT75BK20 | VT75BK30 | VT90BK31 | VT75BK40 | VT75BK50 | VT75BK60 | |||||||
Description | General Purpose | General Purpose High Fluorine |
Low Temp | Low Temp Resistant to Explosive Decompression |
Low Temp High Fluorine |
Extreme Low Temp High Fluorine |
Viton® Extreme High Fluorine FEPM |
|||||||
Cure Type | Bisphenol | Peroxide | Peroxide | Peroxide | Peroxide | Peroxide | Peroxide | |||||||
Typical Fluorine Content | 66 | 69.5 | 64 | 64 | 66.5 | 66.5 | 67 | |||||||
Typical High Temp Range °F (°C) | 437 (225) | 437 (225) | 437 (225) | 437 (225) | 437 (225) | 437 (225) | 437 (225) | |||||||
Typical Low Temp Range °F (°C) | -15 (-26) | -15 (-26) | -40 (-40) | -40 (-40) | -35 (-37) | -54 (-48) | -6 (-21) | |||||||
TR-10 °F (°C) | 1 (-17) | -6 (-21) | -22 (-30) | -22 (-30) | -11 (-24) | -40 (-40) | 12 (-11) | |||||||
Oxygenated Automotive Fuels (containing MeOH, EtOH, MTBE, etc.) | 4 | 1 | 4 | 4 | 1 | 1 | 1 | |||||||
Reciprocating Engine Lubricating Oils (SE-SF Grades) | 2 | 1 | 1 | 1 | 1 | 1 | 1 | |||||||
Aliphatic Hydrocarbon Process Fluids,Chemicals | 1 | 1 | 1 | 1 | 1 | 1 | 1 | |||||||
Aromatic Hydrocarbon Process Fluids, | 1 | 1 | 2 | 2 | 1 | 1 | 1 | |||||||
Aqueous Fluids: Water, Steam, Mineral Acids (H2SO4, HNO3, HCl, etc.) | 3 | 1 | 1 | 1 | 1 | 1 | 1 | |||||||
Amines, High pH Caustics | 4 | 4 | 4 | 4 | 4 | 4 | 1 |
FKM (Viton™) Materials Available
This table shows many of our standard materials and links out to our O-ring store. Get in touch with us if you need a custom gasket, custom molded part, or non-standard geometry!
Filter by
Temperature Search (°C)
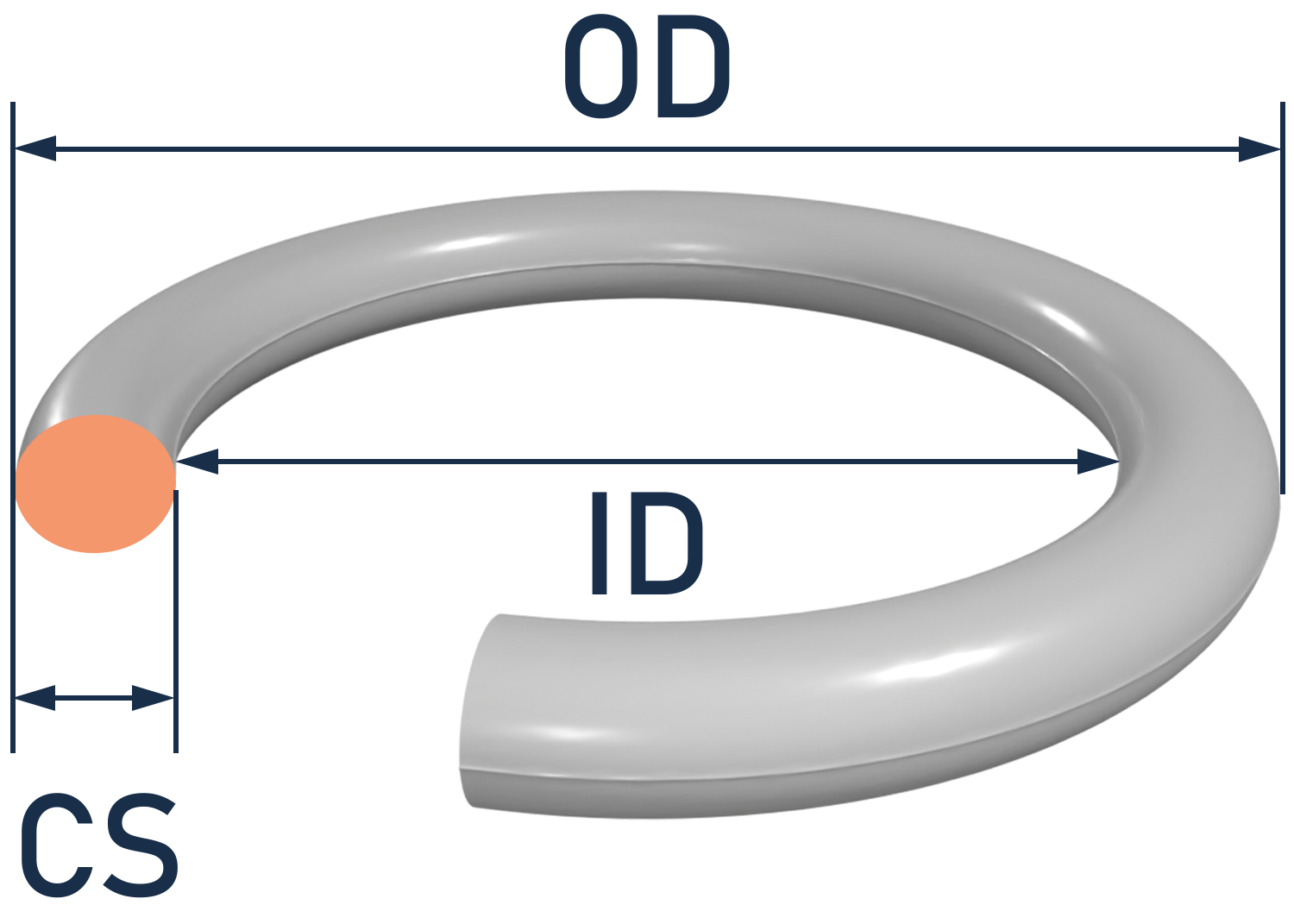
Many FKM Compound Variations
- Internal Lubrication with Silicone oil, Moly and Graphite FKM O-rings, gaskets, & custom molded parts
- High purity translucent FKM O-rings, gaskets, & custom molded parts
- UL Listed FKM O-rings, gaskets, & custom molded parts
- Conductive FKM O-rings, gaskets, & custom molded parts
- Surface free of silicone oil FKM O-rings, gaskets, & custom molded parts
- Talcum powder on surface to reduce sticking FKM O-rings, gaskets, & custom molded parts
- WRAS, KTW and NSF 51/61 Compliant FKM O-rings, gaskets, & custom molded parts
- USP class VI and 3A approved FKM O-rings, gaskets, & custom molded parts
- Explosive Decompression Resistant FKM O-rings, gaskets, & custom molded parts
- Metal and X-ray detectable FKM O-rings, gaskets, & custom molded parts
- PTFE or Parylene Coated in choice color FKM O-rings, gaskets, & custom molded parts
- Specific packaging requirements for FKM O-rings, gaskets, & custom molded parts
- Special bag and Label requirements for FKM O-rings, gaskets, & custom molded parts
- Increased steam resistance FKM O-rings, gaskets, & custom molded parts
- DuPont™ Chemours™ Viton™ specific FKM O-rings, gaskets, & custom molded parts
- Specific and Tight Tolerance FKM O-rings, gaskets, & custom molded parts
- Specific AQL Inspection requirement FKM O-rings, gaskets, & custom molded parts
- Special tumbling for complete flash removal FKM O-rings, gaskets, & custom molded parts
- Variety of colors available for FKM O-rings, gaskets, & custom molded parts
Please consult a Canyon Components Engineer about your specific application and we will use our decades of experience to formulate a solution that fits your need.
Back to Elastomers Hub
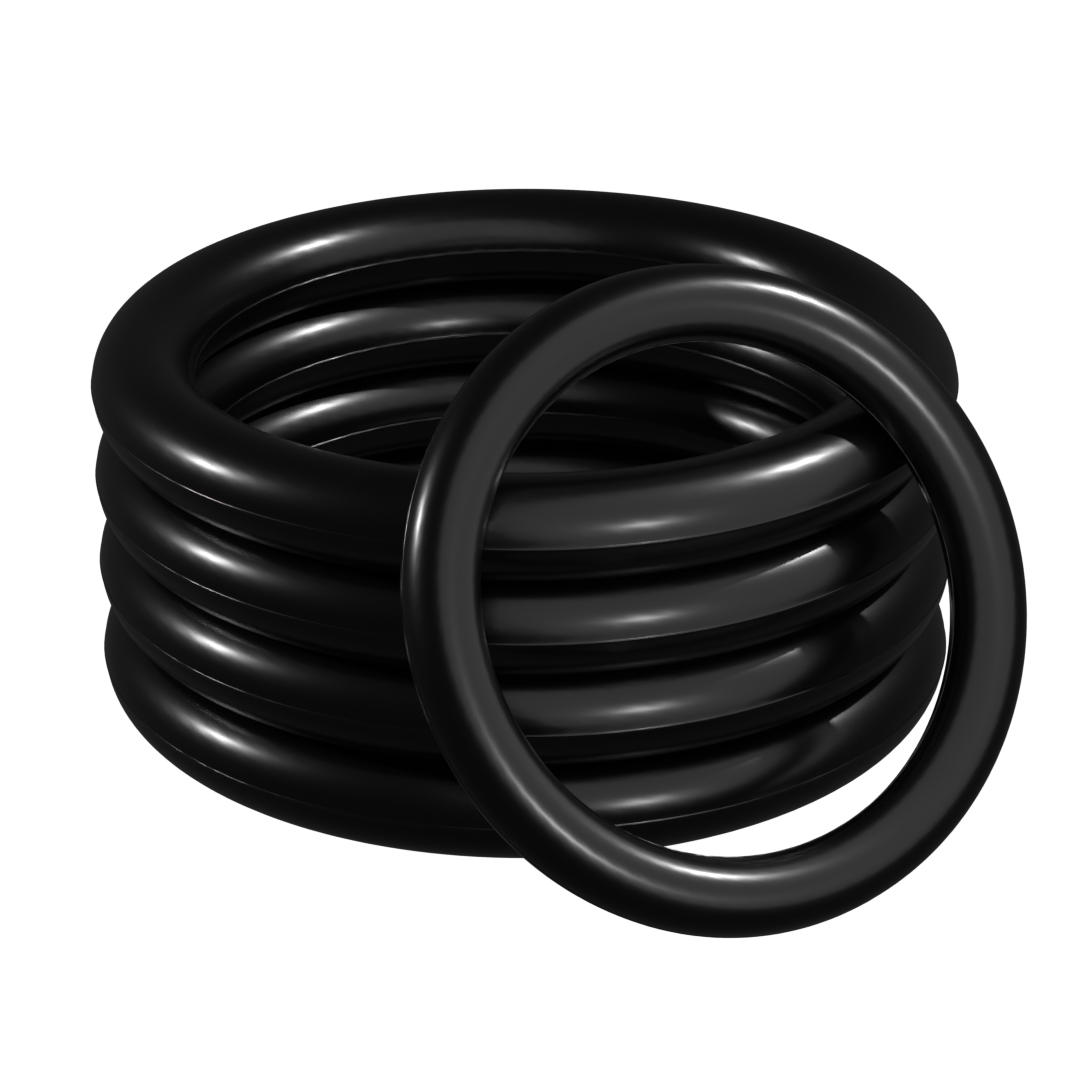
Get A Quote Now!
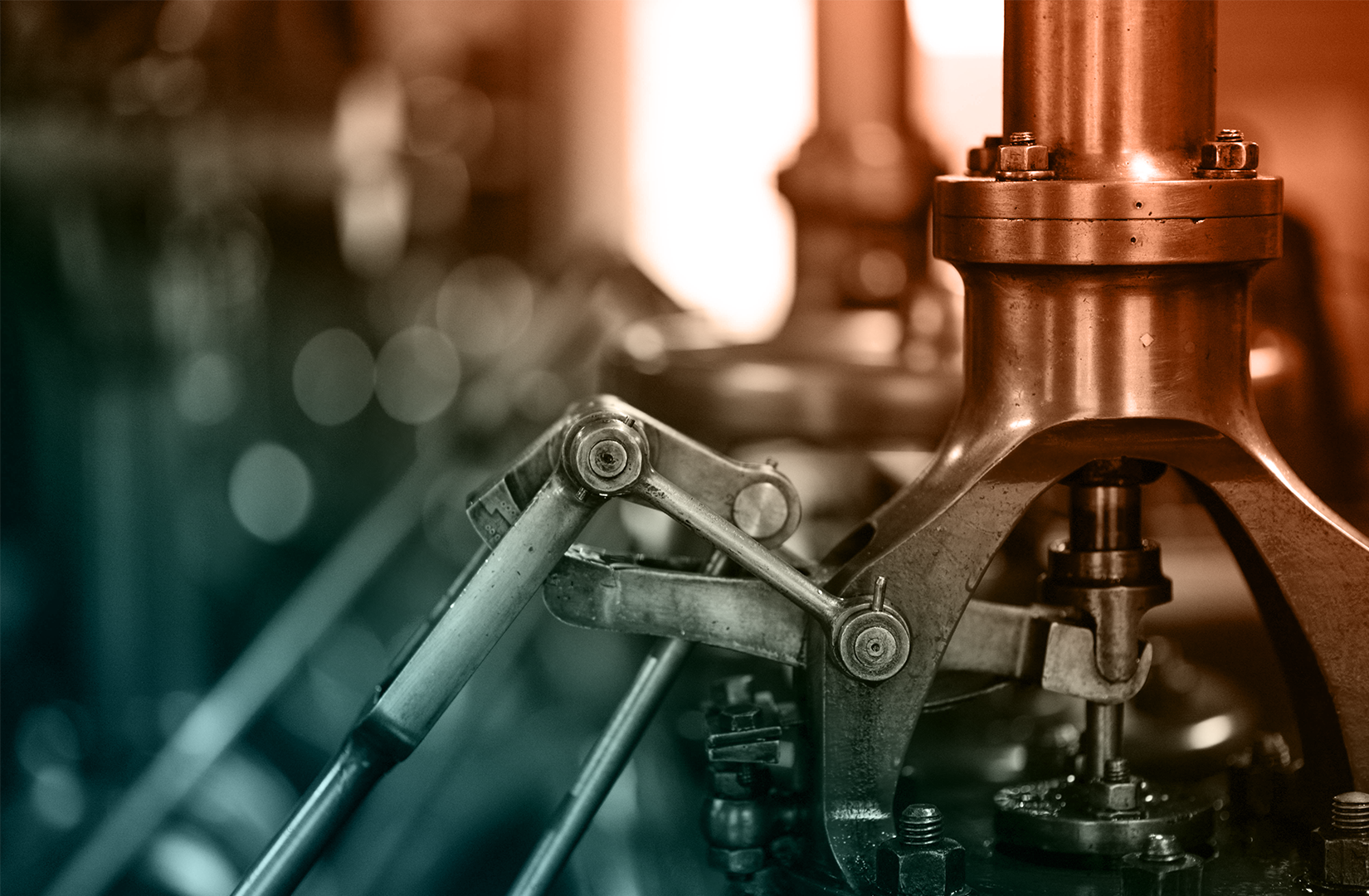
Groove Design References
Learn More
Coatings, Packaging, & Other Services
Learn More
Custom Parts & Custom O-rings
Learn More
Are green O-rings heat resistant?
The color of an O-ring does not necessarily indicate its heat resistance. O-rings are made from various elastomer materials, and their heat resistance depends on the specific material used rather than their color.
Heat resistance of O-rings is determined by the elastomer material's formulation and its ability to withstand elevated temperatures without losing its sealing properties or degrading. Common elastomer materials used for heat-resistant O-rings include:
The color of an O-ring doesn't inherently signify a specific characteristic or quality; rather, it's often used as a means to identify different materials or specifications. Here's a general guide to what different colored O-rings might indicate:
1. Black: The most common color for O-rings, typically made of nitrile (Buna-N), neoprene, EPDM, or other general-purpose materials. These are widely used in various applications due to their good resistance to oils, fuels, and certain chemicals. However, it should be noted that virtually any elastomeric material can be, and will frequently be manufactured in black colorations. This includes specialty materials like Aflas, FFKM Perfluoroelastomers, and silicone.
2. Blue: Fluorosilicone O-rings are typically manufactured in blue colorations. Also, blue is often associated with FDA-approved materials that are safe for food, water, and beverage contact. Blue O-rings are also easily detectable, which helps in maintaining safety standards in food processing industries.
3. Green: Commonly indicates the presence of hydrogenated nitrile (HNBR), which offers better heat and chemical resistance compared to standard nitrile. Viton® (fluorocarbon rubber) can also frequently be found in green colorations.
4. Brown: Typically signifies the use of Viton® (fluorocarbon rubber), known for its excellent resistance to high temperatures and chemicals, including petroleum products.
5. Red, Orange, or Pink: Frequently used for silicone O-rings, which are known for their heat resistance and use in food-grade applications.
6. White or Clear: Often indicates that the O-ring is made from silicone, Teflon (PTFE), or another material that is suitable for sanitary or medical applications.
7. Yellow: May indicate special compounds, such as polyurethane, which are known for their wear resistance and strength.
8. Metal Detectable O-rings: These O-rings are infused with metal detectable materials and are often blue. They are used in the food and pharmaceutical industries where contamination by foreign objects is a critical concern.
It's important to note that these color associations are not universal and can vary between manufacturers. The color alone should not be relied upon to determine the material or suitability of an O-ring for a specific application. Always refer to the manufacturer's specifications or consult with a Canyon Components engineer when selecting an O-ring for a particular use.
To determine the heat resistance of an O-ring, it is crucial to identify the material it is made from and consult the manufacturer's specifications or datasheets to ensure that it meets the temperature requirements of your specific application. The color alone should not be used as an indicator of heat resistance.
Are there different grades of Viton?
Yes, there are different grades of Viton, each formulated to meet specific performance requirements. Viton is a brand name for a type of fluoroelastomer made by Chemours (formerly DuPont). The different grades of Viton are tailored to offer varying levels of resistance to chemicals, temperatures, and other environmental factors. Here are some of the common grades:
1. Viton A: This is the general-purpose grade, offering excellent resistance to a wide range of chemicals and good mechanical properties. It's commonly used in automotive and aerospace fuel applications.
2. Viton B: This grade has better resistance to acids, and some fuels that are more aggressive to the general-purpose grade. It's often used in chemical processing applications.
3. Viton F: Designed for resistance to oxygenated automotive fuels and concentrated industrial chemicals, Viton F is often chosen for applications involving exposure to aggressive fluids.
4. Viton Extreme (ETP): This grade provides superior resistance to environments with acids, bases, and other aggressive chemicals. It's ideal for harsh chemical processing applications.
5. Viton GF: This grade is similar to Viton F but offers improved resistance to steam and higher temperature applications.
6. Viton GLT, GFLT: These grades are tailored for low-temperature applications. GLT-grade offers improved resistance to cold temperatures, while GFLT-grade combines low-temperature flexibility with fuel resistance.
Each grade of Viton fluoroelastomer has unique properties that make it suitable for different applications. The choice of grade depends on factors like the chemical environment, temperature extremes, and the specific requirements of the application, such as flexibility, compression set, and longevity. Always refer to manufacturer datasheets or consult with a Canyon Components materials specialist to select the appropriate grade of Viton for your specific needs.
Are Viton O-rings better than regular O-rings?
Viton O-rings and regular O-rings (typically made of materials like Nitrile, Silicone, or EPDM) have different properties and are better suited for different applications. The choice between them depends on the specific needs of your application. Here are some factors to consider:
1. Chemical Resistance: Viton O-rings have excellent resistance to a wide range of chemicals, including oils, fuels, lubricants, and most mineral acids. They perform better than regular O-rings in harsh chemical environments.
2. Temperature Resistance: Viton withstands high temperatures better than most common O-ring materials. It can be used in environments where temperatures clumb up to 437°F, making it suitable for high-temperature applications.
3. Durability and Longevity: Viton has excellent resistance to aging, weathering, ozone, oxygen, and sunlight. This makes Viton O-rings more durable and long-lasting in harsh environments compared to some regular O-rings.
4. Cost: Viton O-rings are generally more expensive than regular O-rings made from materials like Nitrile or Silicone. This is due to their superior performance characteristics.
5. Application Specific: The choice should be based on the specific requirements of the application, such as exposure to chemicals, temperature ranges, and mechanical wear and tear.
In summary, Viton O-rings are superior in terms of chemical and temperature resistance, durability, and longevity, but they are also more expensive. Regular O-rings may be sufficient for less demanding applications and are more cost-effective. Always consider the specific conditions of your application when choosing an O-ring material.
How do you identify a Viton O-ring?
Identifying a Viton O-ring involves a few steps, as there isn't a single definitive method. However, here are some common ways to identify if an O-ring is made from Viton:
1. Color and Appearance: Viton O-rings are often brown or black, but color alone is not a reliable indicator since O-rings made from other materials can also be colored similarly.
2. Manufacturer's Markings: Some Viton O-rings may have the manufacturer's name or the Viton brand name stamped on them. However, this is not always the case, especially for smaller O-rings.
3. Heat Resistance Test: Viton has excellent heat resistance. Heating a small section of the O-ring with a hot air gun and observing the response can give clues. Viton should withstand higher temperatures without melting compared to other elastomers like Nitrile.
4. Chemical Resistance Test: Viton is highly resistant to many chemicals and solvents. Immersing the O-ring in aggressive chemicals (like automotive fuel or hydraulic fluid) and checking for swelling or deterioration can help determine if it's made from Viton.
5. Flammability Test: When exposed to a flame, Viton does not easily ignite and should self-extinguish when the flame source is removed. This is in contrast to many other rubbers that continue to burn.
6. Density and Hardness: Viton tends to be denser and sometimes harder than many other types of rubber. Measuring the density and hardness can sometimes help, but this requires specific tools and knowledge.
7. Professional Analysis: For a definitive identification, a professional material analysis is recommended. This can be done through various methods, including spectroscopy, by a qualified lab or material specialist.
It's important to note that these methods can be destructive to the O-ring and may not always be conclusive. For critical applications, it's best to source O-rings from reputable suppliers and request certification or material specifications to ensure you are getting genuine Viton. Concact Canyon Components material specialists if you require material identification services.
Is Buna better than Viton?
Comparing Buna (often referred to as Nitrile or Buna-N) with Viton (a brand of fluoroelastomer) involves considering the specific requirements of the application, as each material has its strengths and weaknesses. Here’s a comparative analysis based on various factors:
1. Chemical Resistance:
- Viton: Exceptionally resistant to a wide range of chemicals, including oils, fuels, lubricants, and most mineral acids. It's superior in environments with harsh chemicals.
- Buna-N: Good resistance to oils and some chemicals, but not as broadly resistant as Viton, especially to strong acids and various solvents.
2. Temperature Resistance:
- Viton: Can withstand higher temperatures, generally between -15°F to 437°F (-26°C to 225°C), making it suitable for high-temperature applications.
- Buna-N: Has a decent temperature range but not as high as Viton, typically -40°F to 257°F (-40°C to 125°C).
3. Cost:
- Viton: Generally more expensive than Buna due to its superior performance in harsh environments and its more complex manufacturing process.
- Buna-N: More cost-effective, making it a preferred choice for applications where conditions do not demand Viton's high level of performance.
4. Physical Properties:
- Both materials have good physical properties like tensile strength and flexibility, but these can vary depending on the specific formulation.
5. Applications:
- Viton: Often used in automotive, aerospace, chemical processing, and industrial applications where high chemical and temperature resistance are required.
- Buna-N: Commonly used in automotive (particularly where oil resistance is needed), food handling, and general industrial applications where moderate resistance is sufficient.
6. Durability:
- Viton: Tends to have better longevity, especially in harsh chemical and thermal environments.
- Buna-N: While durable, it may not perform as well as Viton in extreme conditions but is sufficient for many standard applications.
In summary, whether Buna is "better" than Viton depends on the specific application requirements. Viton is superior in terms of chemical and temperature resistance, making it ideal for harsher environments, but it comes at a higher cost. Buna-N is a more cost-effective solution for applications that require good oil resistance and moderate temperature and chemical resistance. The decision should be based on balancing the performance requirements and budget constraints of your specific application.
Is EPDM or Viton better for acid?
When it comes to resistance against acids, the suitability of EPDM (Ethylene Propylene Diene Monomer) and Viton (a brand name for Fluorocarbon elastomers) largely depends on the type of acid and the concentration involved. Both materials have different levels of chemical resistance:
1. EPDM: It has good resistance to many mild acids, especially at lower concentrations. It is also resistant to bases, steam, and polar substances like ketones and alcohols. However, its resistance to strong and concentrated acids can be limited. EPDM is often chosen for its excellent resistance to weathering, ozone, UV radiation, and aging, rather than its chemical resistance.
2. Viton: Known for its exceptional resistance to a wide range of chemicals, Viton performs well against many acids, including some stronger and more corrosive ones. It's particularly resistant to sulfuric, nitric, hydrochloric, and phosphoric acids at varying concentrations. However, its resistance can vary with the concentration and temperature of the acid. Viton is also highly resistant to oils, fuels, and most mineral acids, making it suitable for harsher chemical environments.
Key Considerations:
- Type of Acid: The specific acid and its concentration play a crucial role. For instance, Viton is generally better for handling stronger acids.
- Concentration and Temperature: Both concentration and temperature can affect the material's resistance. Higher concentrations and temperatures generally require materials with higher resistance, like Viton.
- Application Environment: Consider factors like exposure to other chemicals, temperature ranges, and whether the seal will be used in dynamic or static applications.
Conclusion:
- For strong, corrosive acids, particularly in higher concentrations and temperatures, Viton is often the better choice due to its superior chemical resistance.
- For milder acids and lower concentrations, especially in environments where weathering and ozone resistance are also important, EPDM may be sufficient.
It's important to consult with material specifications and possibly conduct compatibility tests for the specific acid and conditions of your application to make the best choice.
Is FKM and Viton the same?
FKM and Viton refer to similar materials, but they are not exactly the same. FKM is a designation for a class of fluorinated, synthetic rubber materials, while Viton is a specific brand of FKM.
1. FKM (Fluoroelastomer): This term refers to the ASTM designation for a class of fluorinated, synthetic rubbers. FKM materials are known for their high resistance to heat, chemicals, and oils. They are used in a variety of applications, including automotive, aerospace, and industrial components.
2. Viton: This is a brand name of FKM produced by Chemours (formerly part of DuPont). Viton shares the properties common to the FKM class of materials, such as excellent resistance to heat, oil, and chemicals.
In summary, while all Viton products are a type of FKM, not all FKM products are Viton. Viton is a well-known and widely used brand of FKM, but there are other manufacturers and brands of FKM materials available in the market. Canyon Components provides hundreds of different formulations of FKM.
Is Fluorosilicone the same as Viton?
No, Fluorosilicone and Viton (a brand name for FKM, Fluoroelastomer) are not the same, although they both belong to the category of high-performance elastomers and share some similar properties. Here are the main differences between the two:
1. Chemical Structure:
- Fluorosilicone (FVMQ): This is a type of silicone rubber that has been modified with fluorine. It combines the beneficial properties of silicone (good flexibility, high temperature resistance) with the enhanced chemical resistance of fluorine.
- Viton (FKM): This is a fluoroelastomer, a special type of synthetic rubber, which is known for its excellent heat resistance and very good resistance to aggressive fuels and chemicals.
2. Temperature Resistance:
- Fluorosilicone: Typically effective in a temperature range of -75°C to +180°C.
- Viton (FKM): Can withstand higher temperatures, usually effective from -26°C to +225°C, with some special grades working even at extended temperature ranges.
3. Chemical Resistance:
- Both materials have excellent resistance to oils, fuels, and solvents, but FKM generally offers superior resistance to hydrocarbons and acids compared to Fluorosilicone.
4. Applications:
- Fluorosilicone: Often used in aerospace and automotive applications for fuel and oil systems, especially where exposure to aviation fuels, synthetic lubricants, or coolants is common.
- Viton (FKM): Widely used in the automotive, chemical processing, and energy industries due to its resistance to high temperatures and aggressive chemicals, especially hydrocarbons.
In summary, while both Fluorosilicone and Viton are used in high-performance applications requiring resistance to harsh chemicals and temperatures, they are distinct materials with different chemical structures and properties. The choice between them would depend on the specific requirements of the application, such as the type of chemicals involved, temperature range, and mechanical stress factors.
Is Viton a type of HNBR?
No, Viton (a brand of FKM, fluoroelastomer) is not the same as HNBR (Hydrogenated Nitrile Butadiene Rubber). These are two distinct types of synthetic rubber with different chemical compositions and properties:
1. Viton (FKM):
- Composition: Viton is a type of fluoroelastomer, which contains fluorine, carbon, hydrogen, and sometimes other elements. It is known for its excellent chemical resistance to a wide range of chemicals, including oils, fuels, acids, and solvents. Viton has a high-temperature resistance, typically up to 225°C (437°F).
- Applications: It is commonly used in industries where resistance to harsh chemicals and high temperatures is critical, such as the chemical processing, automotive, aerospace, and oil and gas industries.
2. HNBR (Hydrogenated Nitrile Butadiene Rubber):
- Composition: HNBR is a hydrogenated version of Nitrile Butadiene Rubber (NBR). It is produced by adding hydrogen to NBR, which improves its heat and ozone resistance, as well as its overall mechanical properties.
- Properties: HNBR combines the oil and fuel resistance of NBR with improved heat resistance. It can withstand temperatures higher than standard NBR, typically up to 165°C (329°F). It also has good resistance to various oils and chemicals.
- Applications: HNBR is commonly used in automotive and industrial applications where resistance to high temperatures and exposure to oils and fuels is required, such as in automotive engine components, seals, and gaskets.
While both Viton and HNBR have excellent chemical resistance properties, they are used in different applications due to their specific characteristics. Viton is known for its broader chemical resistance, especially to harsh solvents and aggressive chemicals, while HNBR is valued for its balance of oil and fuel resistance with improved heat resistance. The choice between them depends on the specific requirements of the application.
Is Viton an EPDM?
No, Viton and EPDM are not the same; they are two distinct types of synthetic rubber, each with its own unique properties and chemical composition.
1. Viton: This is a brand name for a type of synthetic rubber and fluoropolymer elastomer, typically known as Fluoroelastomers (FKM). Viton is known for its excellent resistance to high temperatures and a wide range of chemicals, including oils, fuels, lubricants, and most mineral acids. It is commonly used in environments where these resistances are crucial, such as in the automotive, aerospace, and chemical processing industries.
2. EPDM (Ethylene Propylene Diene Monomer): This is a type of synthetic rubber made from ethylene, propylene, and a diene monomer. EPDM is known for its excellent resistance to weathering, ozone, UV radiation, and aging. It is also resistant to water, steam, and some mild acids and alkalis. However, it does not have good resistance to oil and fuel, which is a stark contrast to Viton. EPDM is commonly used in outdoor applications, such as in automotive weather stripping and seals, roofing membranes, and window and door seals.
In summary, while both Viton and EPDM are valuable in their respective applications due to their specific properties, they are not interchangeable and are chosen based on the requirements of the application regarding chemical exposure, temperature range, and environmental conditions.
Is Viton stronger than EPDM?
The term "stronger" can mean different things in the context of material properties, such as tensile strength, tear resistance, or resilience under various conditions. When comparing Viton and EPDM, it's important to consider the specific aspects of strength relevant to your application:
Tensile Strength and Tear Resistance
- Viton: Generally has higher tensile strength compared to EPDM, although this can vary with different blends. This means it can withstand more stress or force before breaking. Viton also typically exhibits better resistance to tearing, especially in harsh chemical environments.
- EPDM: While EPDM has good tensile strength, it is generally lower than that of Viton. It's more valued for its flexibility and durability in extreme weather conditions rather than its raw strength.
Resistance to Chemicals and Temperature
- Viton: Has superior resistance to a wide range of chemicals, including oils, fuels, lubricants, and some acids. It also excels in high-temperature applications, maintaining its integrity and strength at temperatures where EPDM might degrade.
- EPDM: Excellent resistance to ozone, UV, and weathering makes it strong in outdoor applications. However, it lacks the chemical and oil resistance of Viton and is not as strong in high-temperature scenarios.
Durability in Different Environments
- Viton: Maintains its strength and resists degradation in environments that would adversely affect many other materials, such as automotive or industrial settings with exposure to hydrocarbons.
- EPDM: Exhibits strong durability in outdoor, UV-exposed, or weather-impacted applications but can weaken in the presence of oils, fuels, and high heat.
General Physical Strength
- Both materials are quite robust in their respective areas of application. However, the "strength" as in resistance to physical stress or deformation under load will vary depending on the specific formulation of the elastomer.
Conclusion
- Viton: Stronger in terms of chemical resistance, high-temperature performance, and tensile strength. Ideal for harsh industrial environments.
- EPDM: Strong in terms of weathering, UV resistance, and flexibility at low temperatures. Best suited for outdoor and water-based applications.
The choice between Viton and EPDM should be based on the specific environmental and chemical conditions they will face in their intended application. Each material has its strengths and weaknesses, making them suitable for different types of challenges.
Is Viton stronger than Nitrile?
Comparing the strength of Viton and Nitrile requires considering various factors, as "strength" can mean different things in the context of material properties. Here's a breakdown of how Viton and Nitrile compare in terms of common material strength characteristics:
1. Chemical Resistance: Viton is generally more resistant to a wide range of chemicals, especially hydrocarbons, oils, acids, and some solvents. Nitrile is also resistant to oils and some chemicals, but not as broadly or effectively as Viton.
2. Temperature Resistance: Viton has a higher temperature resistance than Nitrile. It can withstand temperatures from -54 to 437°F depending on the type, making it suitable for high-temperature applications. Nitrile typically handles temperatures from -40°F to 257°F.
3. Physical Strength: When it comes to physical strength, like tensile strength and tear resistance, Nitrile is generally considered strong and durable. However, Viton, while also strong, is often chosen more for its chemical and temperature resistance than its physical toughness.
4. Elasticity and Flexibility: Nitrile generally has better low-temperature flexibility than standard Viton. This means that in cold environments, Nitrile might maintain better elasticity and resistance to deformation, however some specialty blends of Viton can outperform Nitrile in cold temperature environments.
5. Durability: Both materials are durable, but Viton tends to have a longer service life in harsh environments due to its superior resistance to heat, chemicals, and aging.
6. Cost: Viton is typically more expensive than Nitrile. The choice between the two often comes down to whether the additional cost of Viton is justified by the need for higher performance in extreme conditions.
In summary, "stronger" can mean different things. If strength refers to resistance to chemicals and high temperatures, then Viton is stronger. If strength refers to physical toughness and elasticity, particularly in colder environments, then Nitrile might be considered stronger. The choice between the two depends on the specific requirements of your application.
Is Viton the same as HNBR?
No, Viton (a brand of FKM, fluoroelastomer) is not the same as HNBR (Hydrogenated Nitrile Butadiene Rubber). These are two distinct types of synthetic rubber with different chemical compositions and properties:
1. Viton (FKM):
- Composition: Viton is a type of fluoroelastomer, which contains fluorine, carbon, hydrogen, and sometimes other elements. It is known for its excellent chemical resistance to a wide range of chemicals, including oils, fuels, acids, and solvents. Viton has a high-temperature resistance, typically up to 225°C (437°F).
- Applications: It is commonly used in industries where resistance to harsh chemicals and high temperatures is critical, such as the chemical processing, automotive, aerospace, and oil and gas industries.
2. HNBR (Hydrogenated Nitrile Butadiene Rubber):
- Composition: HNBR is a hydrogenated version of Nitrile Butadiene Rubber (NBR). It is produced by adding hydrogen to NBR, which improves its heat and ozone resistance, as well as its overall mechanical properties.
- Properties: HNBR combines the oil and fuel resistance of NBR with improved heat resistance. It can withstand temperatures higher than standard NBR, typically up to 165°C (329°F). It also has good resistance to various oils and chemicals.
- Applications: HNBR is commonly used in automotive and industrial applications where resistance to high temperatures and exposure to oils and fuels is required, such as in automotive engine components, seals, and gaskets.
While both Viton and HNBR have excellent chemical resistance properties, they are used in different applications due to their specific characteristics. Viton is known for its broader chemical resistance, especially to harsh solvents and aggressive chemicals, while HNBR is valued for its balance of oil and fuel resistance with improved heat resistance. The choice between them depends on the specific requirements of the application.
What are the disadvantages of Viton?
Viton, a brand of synthetic rubber and fluoropolymer elastomer commonly used for O-rings, gaskets, and other molded or extruded goods, has several advantages like high temperature and chemical resistance. However, it also has some disadvantages:
1. Limited Cold Flexibility: Viton becomes quite hard and loses elasticity at low temperatures. This can be a significant disadvantage in applications where the material is exposed to cold environments. To solve this problem, low temperature Viton blends were developed, like GLT, GFLT, XLT, and ULT type Vitons.
2. Cost: Compared to other elastomers like nitrile or silicone, Viton is generally more expensive. This can be a limiting factor in applications where cost is a significant concern.
3. Not Suitable for Some Chemicals: While Viton is resistant to many chemicals and solvents, it is not suitable for use with ketones (like acetone) and organic acids (like acetic acid). This limits its applicability in some chemical environments. For better chemical performance, it is typically recommended to use an ETP type Viton or switch over to an FFKM like CanRez or Kalrez.
4. Poor Radiation Resistance: Viton has limited resistance to radiation, which can be a drawback in applications involving exposure to gamma rays or other forms of radiation.
5. Permeability to Gases: Viton is more permeable to gases than some other elastomers, which can be a disadvantage in applications where gas permeability is a critical factor.
6. Difficulty in Processing: Viton can be more difficult to process compared to other elastomers, requiring specialized equipment and expertise.
7. Environmental Impact: As with many synthetic rubbers, the production and disposal of Viton have environmental impacts. It is derived from petroleum products and is not biodegradable.
8. Swelling in Certain Solvents: While Viton has excellent resistance to many solvents, it can swell in certain solvents like acetone, methylethyl ketone, and amines.
These disadvantages should be considered alongside Viton's advantages to determine its suitability for a specific application. The choice of material will depend on the specific requirements of the application, including temperature range, chemical exposure, and cost considerations.
What do different colored O-rings mean?
The color of an O-ring doesn't inherently signify a specific characteristic or quality; rather, it's often used as a means to identify different materials or specifications. Here's a general guide to what different colored O-rings might indicate:
1. Black: The most common color for O-rings, typically made of nitrile (Buna-N), neoprene, EPDM, or other general-purpose materials. These are widely used in various applications due to their good resistance to oils, fuels, and certain chemicals. However, it should be noted that virtually any elastomeric material can be, and will frequently be manufactured in black colorations. This includes specialty materials like Aflas, FFKM Perfluoroelastomers, and silicone.
2. Blue: Fluorosilicone O-rings are typically manufactured in blue colorations. Also, blue is often associated with FDA-approved materials that are safe for food, water, and beverage contact. Blue O-rings are also easily detectable, which helps in maintaining safety standards in food processing industries.
3. Green: Commonly indicates the presence of hydrogenated nitrile (HNBR), which offers better heat and chemical resistance compared to standard nitrile. Viton® (fluorocarbon rubber) can also frequently be found in green colorations.
4. Brown: Typically signifies the use of Viton® (fluorocarbon rubber), known for its excellent resistance to high temperatures and chemicals, including petroleum products.
5. Red, Orange, or Pink: Frequently used for silicone O-rings, which are known for their heat resistance and use in food-grade applications.
6. White or Clear: Often indicates that the O-ring is made from silicone, Teflon (PTFE), or another material that is suitable for sanitary or medical applications.
7. Yellow: May indicate special compounds, such as polyurethane, which are known for their wear resistance and strength.
8. Metal Detectable O-rings: These O-rings are infused with metal detectable materials and are often blue. They are used in the food and pharmaceutical industries where contamination by foreign objects is a critical concern.
It's important to note that these color associations are not universal and can vary between manufacturers. The color alone should not be relied upon to determine the material or suitability of an O-ring for a specific application. Always refer to the manufacturer's specifications or consult with a Canyon Components engineer when selecting an O-ring for a particular use.
What is a very high temperature O-ring?
The choice of the best O-ring material for high-temperature applications depends on the specific temperature range and other environmental factors involved. Several elastomer materials are suitable for high-temperature sealing, and the selection should be based on the following considerations:
1. Silicone Rubber (VMQ):
- Temperature Range: Certain Silicone rubber blends can handle temperatures up to 600°F (315°C), however most are only rated for 400°F (205°C).
- Advantages: Excellent high-temperature resistance, good flexibility, and resistance to ozone and UV exposure.
- Applications: Suitable for a wide range of high-temperature applications, including aerospace, automotive, and food processing.
2. Fluorocarbon Rubber (FKM/Viton):
- Temperature Range: FKM can withstand temperatures up to 437°F (225°C).
- Advantages: Exceptional chemical resistance, high-temperature resistance, and durability.
- Applications: Commonly used in oil and gas, automotive, chemical processing, and aerospace industries.
3. Perfluoroelastomer (FFKM):
- Temperature Range: Certain FFKM CanRez blends can handle temperatures up to 635°F (335°C) and excursions to even higher temperatures.
- Advantages: Excellent high-temperature and ultimate chemical resistance, low outgassing, and low permeability.
- Applications: Used in demanding high-temperature and chemical environments, such as semiconductor manufacturing and oil and gas.
4. Fluorosilicone (FVMQ):
- Temperature Range: FVMQ materials can handle temperatures up to 356°F (180°C).
- Advantages: Good high-temperature resistance, flexibility, and resistance to oils and fuels.
- Applications: Suitable for aerospace, automotive, and other applications where a combination of temperature and chemical resistance is required.
The best O-ring material for high-temperature applications varies depending on the specific temperature range, chemical exposure, pressure, and other environmental factors. It's essential to consult with a material expert or O-ring manufacturer to select the most suitable material for your particular application to ensure optimal performance and longevity. Additionally, consider the specific grade and formulation of the elastomer material to match the requirements of your high-temperature application.
What is better, Nitrile or Viton?
Choosing between Buna-N (Nitrile rubber) and Viton (a brand of FKM, fluoroelastomer) depends on the specific requirements of your application. Each material has its advantages and limitations, so the choice should be based on factors like chemical resistance, temperature range, and cost. Here's a comparison:
1. Chemical Resistance:
- Buna-N: Buna-N is excellent for resistance to oils, fuels, and petroleum-based fluids. It performs well in applications where exposure to these substances is common.
- Viton: Viton is superior in terms of chemical resistance, especially for a broader range of chemicals, including more aggressive acids and solvents. It excels in applications with harsh chemical environments.
2. Temperature Range:
- Buna-N: Buna-N has a moderate temperature range, typically from -40°C to 108°C (-40°F to 226°F).
- Viton: Viton can handle higher temperatures, usually up to 200°C (392°F), making it suitable for high-temperature applications.
3. Cost:
- Buna-N: Generally more cost-effective compared to Viton. It provides good performance at a lower cost.
- Viton: Viton is more expensive due to its superior chemical resistance and higher temperature tolerance.
4. Applications:
- Buna-N: Commonly used in automotive, industrial, and manufacturing applications where exposure to oils, fuels, and petroleum-based fluids is frequent.
- Viton: Preferred in applications where a higher level of chemical resistance is required, such as in the chemical processing industry, aerospace, and situations involving aggressive chemicals.
5. Environmental Resistance:
- Buna-N: Better suited for applications involving oils and hydrocarbons.
- Viton: Better for applications involving a wider range of chemicals and high-temperature environments.
In summary, Buna-N is a cost-effective choice for applications involving oils and fuels, whereas Viton is preferred for applications with a broader range of chemicals and higher-temperature requirements. The specific choice depends on your application's needs, and it's essential to consider factors like chemical exposure, temperature extremes, and budget when making the decision.
What is Grade A Viton?
Grade A Viton is one of the various grades of Viton fluoroelastomers, which are high-performance synthetic rubber compounds used for their excellent resistance to high temperatures, chemicals, and other harsh conditions. Grade A specifically is known for its general-purpose applications and is characterized by the following properties:
1. Chemical Resistance: Grade A Viton is particularly resistant to a wide range of oils, fuels, lubricants, and most mineral acids. It maintains its integrity in harsh chemical environments, making it a popular choice for automotive, aerospace, and industrial applications.
2. Temperature Resistance: This grade can withstand temperature extremes, typically from -15°F to 437°F (-26°C to 225°C). It is suitable for applications where materials are exposed to high heat.
3. Physical Properties: Viton A has good mechanical properties, including high tensile strength and excellent resistance to compression set (the ability of a material to return to its original thickness after prolonged compressive stresses).
4. Applications: Due to its robustness against oils and chemicals, Grade A Viton is commonly used in the automotive industry for O-rings, gaskets, seals, and hoses in fuel systems. It's also used in the aerospace sector and in various industrial applications where resistance to aggressive chemicals is required.
5. Versatility: While it is very resistant to hydrocarbons and acidic substances, it's important to note that it may not be the best choice for some concentrated acids and bases, ketones, and amines, where other grades of Viton or different materials might be more appropriate.
Grade A Viton's blend of resistance to both chemical and temperature extremes, along with its physical durability, makes it a widely used material in environments where less robust elastomers would fail. When selecting a material for specific applications, it's crucial to consider the exact environmental conditions and chemical exposures it will face to ensure the chosen grade of Viton is appropriate.
What is the best O-ring for gasoline?
When selecting an O-ring for use with gasoline, the key factors to consider are the O-ring's resistance to gasoline (including any additives in the fuel), its ability to maintain integrity at various temperatures, and its compatibility with other environmental factors it may encounter. The most commonly recommended materials for O-rings used with gasoline are:
1. Viton (Fluorocarbon, FKM): Viton is often considered one of the best materials for gasoline applications due to its excellent resistance to hydrocarbons, including gasoline and its additives. It maintains its properties over a wide temperature range and offers good resistance to aging and weathering. This makes it a preferred choice for automotive fuel handling systems.
2. Nitrile (Buna-N, NBR): Nitrile rubber is another popular choice for gasoline applications, especially when cost is a consideration. It has good resistance to oils and fuels, including gasoline. However, it may not perform as well as Viton in high-temperature environments or when exposed to certain additives in modern fuels.
3. Ethylene Propylene Diene Monomer (EPDM): While EPDM has excellent resistance to weathering, ozone, and aging, its compatibility with gasoline is generally poor. It's not typically recommended for use with gasoline or petroleum-based fluids.
4. Neoprene (Chloroprene, CR): Neoprene has moderate resistance to gasoline but is generally less preferred than Viton or Nitrile for this application. It's more commonly used in environments where resistance to weathering and ozone is a priority.
5. Silicone: Silicone O-rings are not recommended for use with gasoline. They have poor resistance to petroleum-based fuels and oils.
Summary
- Best Overall: Viton is often considered the best choice for gasoline applications due to its superior resistance to hydrocarbons and high temperatures.
- Cost-Effective Alternative: Nitrile is a good, less expensive alternative with acceptable resistance to gasoline but may not perform as well in extreme conditions compared to Viton.
It's important to ensure that the O-ring material is compatible not only with gasoline but also with any fuel additives that may be present. Additionally, always check the specifications and recommendations from the O-ring manufacturer or supplier for your specific application.
What is the best O-ring material for high temperatures?
The choice of the best O-ring material for high-temperature applications depends on the specific temperature range and other environmental factors involved. Several elastomer materials are suitable for high-temperature sealing, and the selection should be based on the following considerations:
1. Silicone Rubber (VMQ):
- Temperature Range: Certain Silicone rubber blends can handle temperatures up to 600°F (315°C), however most are only rated for 400°F (205°C).
- Advantages: Excellent high-temperature resistance, good flexibility, and resistance to ozone and UV exposure.
- Applications: Suitable for a wide range of high-temperature applications, including aerospace, automotive, and food processing.
2. Fluorocarbon Rubber (FKM/Viton):
- Temperature Range: FKM can withstand temperatures up to 437°F (225°C).
- Advantages: Exceptional chemical resistance, high-temperature resistance, and durability.
- Applications: Commonly used in oil and gas, automotive, chemical processing, and aerospace industries.
3. Perfluoroelastomer (FFKM):
- Temperature Range: Certain FFKM CanRez blends can handle temperatures up to 635°F (335°C) and excursions to even higher temperatures.
- Advantages: Excellent high-temperature and ultimate chemical resistance, low outgassing, and low permeability.
- Applications: Used in demanding high-temperature and chemical environments, such as semiconductor manufacturing and oil and gas.
4. Fluorosilicone (FVMQ):
- Temperature Range: FVMQ materials can handle temperatures up to 356°F (180°C).
- Advantages: Good high-temperature resistance, flexibility, and resistance to oils and fuels.
- Applications: Suitable for aerospace, automotive, and other applications where a combination of temperature and chemical resistance is required.
The best O-ring material for high-temperature applications varies depending on the specific temperature range, chemical exposure, pressure, and other environmental factors. It's essential to consult with a material expert or O-ring manufacturer to select the most suitable material for your particular application to ensure optimal performance and longevity. Additionally, consider the specific grade and formulation of the elastomer material to match the requirements of your high-temperature application.
What is the difference between EPDM and Viton O-rings?
EPDM (Ethylene Propylene Diene Monomer) and Viton (a brand name for Fluorocarbon elastomers) are both types of synthetic rubber, but they have different chemical compositions and properties that make them suitable for different applications. Here's a comparison of their key characteristics:
Chemical Composition
- EPDM: It is a terpolymer made from ethylene, propylene, and a diene monomer. The diene component allows for vulcanization with sulfur and other curatives.
- Viton: It is made from fluoropolymer elastomers, which are a family of synthetic rubbers made from fluorocarbon-based compounds. This gives it a high degree of resistance to heat and chemicals.
Resistance to Chemicals and Fluids
- EPDM: Excellent resistance to ozone, weathering, and aging; good resistance to water, steam, alkalis, and mild acidic environments. However, it has poor resistance to petroleum-based oils and fuels.
- Viton: Outstanding resistance to oils, fuels, lubricants, and most mineral acids. It also has excellent resistance to high temperatures and can withstand a variety of chemicals.
Temperature Range
- EPDM: Generally effective in temperatures ranging from -67°F to 300°F (-55°C to 150°C), although certain specialty blends can perform well outside of this range. It performs well in outdoor applications due to its resistance to harsh weather conditions.
- Viton: Has a broader temperature range, typically from -15°F to 437°F (-26°C to 225°C), and can withstand higher temperatures for short periods. This makes it suitable for applications involving high temperatures. Certain blends are capable of low temperature performance down to -54°F (-48°C).
Applications
- EPDM: Commonly used in automotive weather stripping and seals, roofing membranes, electrical insulation, and other applications where resistance to weather and ozone is crucial. It's also used in the water and steam systems due to its excellent water resistance.
- Viton: Primarily used in situations requiring resistance to high temperatures and chemicals, such as in automotive fuel handling systems, chemical processing industries, and aerospace applications.
Cost
- EPDM: More cost-effective for applications where resistance to weathering and ozone is required but not in contact with oils and fuels.
- Viton: Generally more expensive due to its costly composition and superior resistance to chemicals & high temperatures.
Summary
- EPDM: Best for outdoor and water/steam applications due to its excellent weather, ozone, and water resistance but not suitable for use with oils or fuels.
- Viton: Ideal for applications requiring resistance to high temperatures and a wide range of chemicals, including oils and fuels, but more expensive.
The choice between EPDM and Viton O-rings depends largely on the specific requirements of the application, including the types of chemicals, temperatures, and environmental conditions they will be exposed to.
What is the most common type of O-ring?
The most common type of O-ring material used is Nitrile rubber, often referred to as NBR (Nitrile Butadiene Rubber) O-rings. NBR O-rings are widely used in various industries and applications due to their versatile properties and cost-effectiveness. Here are some reasons why NBR O-rings are commonly used:
1. Oil and Fuel Resistance: NBR O-rings exhibit excellent resistance to oils, fuels, and lubricants, making them ideal for sealing applications in automotive, machinery, and hydraulic systems.
2. Chemical Compatibility: NBR is compatible with a wide range of non-polar and polar chemicals, which makes it suitable for many industrial applications.
3. Temperature Range: NBR O-rings can perform effectively within a moderate temperature range, typically from -40°C (-40°F) to 125°C (257°F).
4. Cost-Effectiveness: NBR is relatively inexpensive compared to some other elastomer materials, making it a cost-effective choice for sealing solutions.
5. Availability: NBR O-rings are readily available in various sizes, shapes, and durometers, making them easy to source for a wide range of applications.
While NBR is the most common type of O-ring material, it's important to note that O-rings are available in a variety of materials, each with its own set of properties and suitability for specific applications. Depending on the requirements of the application, other types of O-ring materials, such as Viton (FKM), EPDM, silicone, and HNBR, may also be used to meet specific performance criteria such as temperature resistance, chemical compatibility, or durability. The choice of O-ring material should be based on the specific needs of the sealing application.
What is the shelf life of Viton O-rings?
The shelf life of Viton O-rings, like most elastomeric seals, depends on various factors including storage conditions and environmental factors. According to industry standards, particularly those set by the Society of Automotive Engineers (SAE) and the Aerospace Material Specifications (AMS), the shelf life for Viton (fluoroelastomer) O-rings is typically considered to be unlimited if stored properly.
However, proper storage is crucial to ensure that they maintain their quality over time. Here are some key storage guidelines for Viton O-rings:
1. Temperature: Store in a cool, dry place away from direct sunlight. The temperature should ideally be maintained between 59°F to 100°F (15°C to 38°C).
2. Humidity: The relative humidity should be controlled to prevent moisture-related degradation.
3. Lighting: Avoid exposure to direct sunlight and strong artificial light with a high ultraviolet content.
4. Ozone: Store away from electric motors, generators, or other ozone-generating equipment as ozone can rapidly degrade elastomers.
5. Deformation: Prevent deformation during storage. O-rings should be laid flat and not stretched, compressed, or otherwise distorted.
6. Contact with Materials: Avoid contact with solvents, fuels, lubricants, metals, or other materials that could cause degradation.
7. Packaging: Retain the original packaging if possible, as it is designed to protect the O-rings from environmental factors.
Following these storage conditions helps in maintaining the integrity and performance characteristics of Viton O-rings over time. Despite their robust nature and resistance to degradation, it's always a good practice to inspect O-rings for any signs of deterioration such as cracking, hardening, or brittleness before use, especially if they have been stored for an extended period.
What is the strongest O-ring material?
The term "strongest" when referring to O-ring materials can mean different things depending on the specific requirements of the application, such as resistance to chemicals, temperature extremes, pressure, or wear and tear. There is no single "strongest" O-ring material that suits all applications; instead, the best material depends on the specific conditions the O-ring will be exposed to. Here are some materials considered strong in various aspects:
1. FKM (Fluoroelastomer, e.g., Viton): Known for excellent chemical resistance, especially to oils, fuels, and some acids, and high-temperature tolerance (up to about 225°C or 437°F). It is often considered one of the strongest materials in terms of chemical and heat resistance.
2. FFKM (Perfluoroelastomer, e.g., CanRez, Kalrez, Chemraz): Offers even higher chemical and temperature resistance than standard FKM. It can withstand temperatures up to 335°C (635°F) and almost all chemicals. FFKM O-rings are often used in extremely harsh chemical and thermal environments.
3. Nitrile Rubber (NBR, Buna-N): Offers excellent resistance to oils and petroleum-based fluids. It's a strong choice for applications involving oil and fuel exposure.
4. EPDM (Ethylene Propylene Diene Monomer): Has outstanding resistance to weathering, ozone, UV rays, and aging, as well as good heat and steam resistance. It's a strong material for outdoor and water/steam applications.
5. Silicone: Exhibits excellent flexibility and is resistant to extreme temperatures, both hot and cold. It's a strong choice for applications requiring temperature resistance over a wide range.
6. Polyurethane: Known for its excellent wear and tear resistance, making it a strong material for high-pressure hydraulic systems and applications involving abrasion.
Each of these materials has its strengths in specific areas, and the choice of material should be based on the application's requirements, including exposure to chemicals, temperature, pressure, and wear. In some highly demanding applications, specialized O-ring materials like FFKM might be necessary due to their superior resistance qualities, despite their higher cost.
What temperature are Viton O-rings good for?
Viton O-rings, also known as fluoroelastomer O-rings, are known for their excellent high-temperature resistance. The specific temperature range at which Viton O-rings can perform effectively depends on the grade or formulation of the Viton material. However, as a general guideline:
FKM O-rings, gaskets, & custom molded parts have a Service Temperature Range of (varies with application): Typically 2°F to 400°F (-16°C to 204°C) *Specialty compounds allow range of -67°F to 432°F (-55°C to 222°C)
It's important to note that the actual temperature range for Viton O-rings can vary based on the specific grade, compound, and manufacturer. When selecting Viton O-rings for a particular application, it's crucial to consider the operating temperature range of the application and choose the appropriate grade of Viton that matches those temperature requirements.
Additionally, while Viton O-rings are known for their high-temperature resistance, other factors such as pressure, exposure to chemicals, and sealing gland design should also be considered when determining the suitability of Viton O-rings for a specific application. Consulting with O-ring manufacturers or suppliers can help in selecting the right material and grade for your specific needs.
Which is better, Buna-N or Viton?
Choosing between Buna-N (Nitrile rubber) and Viton (a brand of FKM, fluoroelastomer) depends on the specific requirements of your application. Each material has its advantages and limitations, so the choice should be based on factors like chemical resistance, temperature range, and cost. Here's a comparison:
1. Chemical Resistance:
- Buna-N: Buna-N is excellent for resistance to oils, fuels, and petroleum-based fluids. It performs well in applications where exposure to these substances is common.
- Viton: Viton is superior in terms of chemical resistance, especially for a broader range of chemicals, including more aggressive acids and solvents. It excels in applications with harsh chemical environments.
2. Temperature Range:
- Buna-N: Buna-N has a moderate temperature range, typically from -40°C to 108°C (-40°F to 226°F).
- Viton: Viton can handle higher temperatures, usually up to 200°C (392°F), making it suitable for high-temperature applications.
3. Cost:
- Buna-N: Generally more cost-effective compared to Viton. It provides good performance at a lower cost.
- Viton: Viton is more expensive due to its superior chemical resistance and higher temperature tolerance.
4. Applications:
- Buna-N: Commonly used in automotive, industrial, and manufacturing applications where exposure to oils, fuels, and petroleum-based fluids is frequent.
- Viton: Preferred in applications where a higher level of chemical resistance is required, such as in the chemical processing industry, aerospace, and situations involving aggressive chemicals.
5. Environmental Resistance:
- Buna-N: Better suited for applications involving oils and hydrocarbons.
- Viton: Better for applications involving a wider range of chemicals and high-temperature environments.
In summary, Buna-N is a cost-effective choice for applications involving oils and fuels, whereas Viton is preferred for applications with a broader range of chemicals and higher-temperature requirements. The specific choice depends on your application's needs, and it's essential to consider factors like chemical exposure, temperature extremes, and budget when making the decision.
Which is better, EPDM or Viton?
The choice between EPDM (Ethylene Propylene Diene Monomer) and Viton (a brand of FKM, fluoroelastomer) depends on the specific application and environmental conditions each material will be exposed to. Here's a comparison of the two:
1. Chemical Resistance:
- Viton: Excellent chemical resistance, particularly to oils, fuels, and hydrocarbons. It's also resistant to a wide range of other chemicals.
- EPDM: Good resistance to a variety of chemicals, but particularly strong against weathering, ozone, and UV rays. Not suitable for use with oils and fuels.
2. Temperature Range:
- Viton: Can handle higher temperature ranges than EPDM, typically up to 225°C (437°F), making it suitable for high-temperature applications.
- EPDM: Generally has a lower temperature range, up to around 150°C (302°F).
3. Cost:
- Viton: Generally more expensive than EPDM, due to its superior performance in harsh environments and expensive composition.
- EPDM: More cost-effective, making it a good choice for applications where its resistance properties are adequate.
4. Applications:
- Viton: Commonly used in automotive, aerospace, and industrial applications where chemical and temperature resistance is critical.
- EPDM: Often used in outdoor applications like roofing, seals in vehicles, and window and door seals due to its excellent weathering resistance.
5. Physical Properties:
- Viton: Typically harder and more resistant to compression set than EPDM.
- EPDM: More flexible and with better fatigue resistance.
6. Environmental Resistance:
- Viton: Better suited for harsh chemical environments.
- EPDM: Better for outdoor applications where weather and UV resistance are needed.
Ultimately, the choice depends on the specific requirements of your application, including exposure to chemicals, temperature ranges, and environmental conditions. It's always best to consult with a materials specialist or engineer to determine the most appropriate material for your specific needs.
Which is better, FKM or EPDM?
Choosing between FKM (Fluoroelastomer, with Viton being a well-known brand) and EPDM (Ethylene Propylene Diene Monomer) depends on the specific application requirements and environmental conditions. Both materials have unique properties that make them suitable for different uses. Here's a comparison to help determine which might be better for a given situation:
1. Chemical Resistance:
- FKM: Offers superior resistance to oils, fuels, lubricants, and most mineral acids. It also has good resistance to a variety of other chemicals.
- EPDM: Excellent resistance to ozone, weathering, and UV radiation. It also performs well with certain chemicals, especially ketones, hot water, steam, and alkalis. However, it is not suitable for use with oils, fuels, and hydrocarbons.
2. Temperature Resistance:
- FKM: Can handle higher temperatures, generally up to 225°C (437°F), and in some special formulations, even higher.
- EPDM: Has a lower temperature range, typically up to 150°C (300°F).
3. Environmental Conditions:
- FKM: Performs well in harsh chemical environments and where high heat resistance is needed.
- EPDM: Excellent for outdoor applications due to its superior resistance to weathering, ozone, and UV rays.
4. Cost:
- FKM: Generally more expensive, reflecting its advanced resistance capabilities, particularly in harsh chemical and temperature environments.
- EPDM: More cost-effective for applications where its properties are sufficient.
5. Applications:
- FKM: Common in automotive, aerospace, and industrial sectors for seals, O-rings, and gaskets, especially where oil and acid resistance is crucial.
- EPDM: Frequently used in automotive weather stripping and hoses, roofing membranes, and outdoor electrical insulation.
In summary, the choice between FKM and EPDM depends largely on the application's exposure to temperatures, chemicals, and environmental factors. FKM is typically better for applications involving oils, fuels, and high temperatures, while EPDM is more suitable for outdoor and water-based applications. Always consider the specific requirements of your application when choosing between these materials.
Which is better, Nitrile or Viton?
Comparing Buna (often referred to as Nitrile or Buna-N) with Viton (a brand of fluoroelastomer) involves considering the specific requirements of the application, as each material has its strengths and weaknesses. Here’s a comparative analysis based on various factors:
1. Chemical Resistance:
- Viton: Exceptionally resistant to a wide range of chemicals, including oils, fuels, lubricants, and most mineral acids. It's superior in environments with harsh chemicals.
- Buna-N: Good resistance to oils and some chemicals, but not as broadly resistant as Viton, especially to strong acids and various solvents.
2. Temperature Resistance:
- Viton: Can withstand higher temperatures, generally between -15°F to 437°F (-26°C to 225°C), making it suitable for high-temperature applications.
- Buna-N: Has a decent temperature range but not as high as Viton, typically -40°F to 257°F (-40°C to 125°C).
3. Cost:
- Viton: Generally more expensive than Buna due to its superior performance in harsh environments and its more complex manufacturing process.
- Buna-N: More cost-effective, making it a preferred choice for applications where conditions do not demand Viton's high level of performance.
4. Physical Properties:
- Both materials have good physical properties like tensile strength and flexibility, but these can vary depending on the specific formulation.
5. Applications:
- Viton: Often used in automotive, aerospace, chemical processing, and industrial applications where high chemical and temperature resistance are required.
- Buna-N: Commonly used in automotive (particularly where oil resistance is needed), food handling, and general industrial applications where moderate resistance is sufficient.
6. Durability:
- Viton: Tends to have better longevity, especially in harsh chemical and thermal environments.
- Buna-N: While durable, it may not perform as well as Viton in extreme conditions but is sufficient for many standard applications.
In summary, whether Buna is "better" than Viton depends on the specific application requirements. Viton is superior in terms of chemical and temperature resistance, making it ideal for harsher environments, but it comes at a higher cost. Buna-N is a more cost-effective solution for applications that require good oil resistance and moderate temperature and chemical resistance. The decision should be based on balancing the performance requirements and budget constraints of your specific application.
Which is better, Viton or Buna?
Choosing between Viton and Buna (also known as Nitrile rubber) depends on the specific application and environment in which the material will be used. Both have distinct properties that make them suitable for different purposes. Here's a comparison:
Viton (Fluorocarbon Elastomer)
1. Chemical Resistance: Excellent resistance to oils, fuels, lubricants, and most mineral acids. Also has good resistance to many aliphatic hydrocarbon fluids that act as solvents for other rubbers.
2. Temperature Range: Exceptionally good at high temperatures, withstanding temperatures up to about 437°F (225°C).
3. Aging/Weather Resistance: Excellent resistance to aging, ozone, sunlight, and weather.
4. Cost: Generally more expensive.
5. Applications: Ideal for automotive, aerospace, and industrial applications where resistance to high temperatures and chemicals is crucial.
Buna (Nitrile Rubber)
1. Chemical Resistance: Good resistance to oils, solvents, and greases. However, it is not recommended for use with highly polar solvents like acetone and methyl ethyl ketone, nor with chlorinated hydrocarbons.
2. Temperature Range: Good performance in temperatures ranging from -40°F to 257°F (-40°C to 125°C).
3. Aging/Weather Resistance: Good resistance to abrasion and aging, but inferior to Viton in terms of weather and ozone resistance.
4. Cost: Less expensive compared to Viton.
5. Applications: Commonly used in automotive applications (like fuel and oil handling hoses, seals, grommets), as well as in general industrial applications where fuel and oil resistance is needed.
Summary
- For High Temperature and Chemical Resistance: Viton is superior.
- For Cost-Effectiveness and General Oil Resistance: Buna is more suitable.
- Application Specific: Always consider the specific requirements of the application, including chemical exposure, temperature range, and budget constraints.
In conclusion, the better choice depends on the operational requirements of the application. Viton excels in extreme environments and with high chemical resistance needs, while Buna is more cost-effective for general industrial uses where extreme conditions are not a factor.
Which is better, Viton or HNBR?
Determining whether Viton or HNBR is better depends on the specific requirements of your application. Each material has its own set of properties and advantages, and the choice between them should be based on factors such as temperature resistance, chemical compatibility, and environmental conditions. Here's a comparison to help you decide:
Viton (Fluoroelastomer, FKM):
- Temperature Resistance: Viton excels in high-temperature applications, with the ability to withstand temperatures from -15°F to 400°F (-26°C to 204°C). It maintains its integrity at elevated temperatures.
- Chemical Resistance: Viton is highly resistant to a wide range of chemicals, including oils, fuels, lubricants, and most mineral acids. It is often chosen for applications involving aggressive chemicals.
- Ozone and UV Resistance: Viton exhibits good resistance to ozone and UV radiation, making it suitable for outdoor and exposed applications.
- Durability: Viton is known for its excellent durability and long service life, particularly in harsh environments.
- Applications: It is commonly used in industries such as automotive, aerospace, and chemical processing where extreme temperatures and chemical exposure are prevalent.
HNBR (Hydrogenated Nitrile Butadiene Rubber):
- Temperature Resistance: HNBR offers good temperature resistance, typically ranging from -40°F to 300°F (-40°C to 149°C). It is suitable for a wide range of temperature conditions.
- Chemical Resistance: HNBR has improved chemical resistance compared to standard Nitrile rubber (NBR). It is particularly resistant to oils, fuels, and some chemicals.
- Abrasion Resistance: HNBR exhibits good abrasion resistance, making it suitable for applications involving wear and tear.
- Applications: It is commonly used in automotive applications, including seals, belts, and hoses. It is also found in industrial applications where resistance to heat and chemicals is essential.
Summary:
- Viton is preferred for applications involving extremely high temperatures and aggressive chemicals. It is a top choice for the aerospace and chemical industries.
- HNBR is suitable for a wide range of applications, offering good temperature and chemical resistance. It is commonly used in automotive and industrial settings.
The choice between Viton and HNBR should be based on a detailed assessment of your specific application's requirements and conditions. Consult with material experts or engineers to ensure the most suitable material is chosen for your sealing needs.
Who invented Viton?
Viton, a type of fluoroelastomer, was invented by scientists at DuPont in 1957. This development was part of the company's significant contributions to the field of polymer and synthetic rubber research. Viton was created to meet the needs of the aerospace industry for a high-performance elastomer resistant to extreme temperatures and chemical conditions. Its invention marked a significant advancement in materials technology, particularly for applications requiring exceptional resistance to heat, oils, and chemicals. Since then, Viton has been widely adopted in various industries, including automotive, chemical processing, and more, due to its robust properties.
Why is Viton so expensive?
Viton, a brand of synthetic rubber and fluoropolymer elastomer (FKM) commonly used in O-rings, seals, and other moulded or extruded goods, tends to be expensive due to several key factors:
1. Material Composition: Viton is made from fluoropolymer elastomers (FKM), which are more complex and costly to produce than conventional rubbers. The process requires specialized chemicals and technology, contributing to its higher cost.
2. Performance Characteristics: Viton exhibits exceptional resistance to heat, chemicals, and oil, which makes it suitable for demanding industrial applications. Its ability to maintain integrity under harsh conditions justifies its higher price compared to less durable materials.
3. Production Costs: The manufacturing process of Viton is more intricate and requires stricter quality control than ordinary rubber production. This increases the overall production costs.
4. Market Demand: Viton's unique properties make it essential for specific industries, like aerospace, automotive, and chemical processing. The specialized demand for such high-performance material can drive up its price.
5. Brand Recognition: As a well-known brand under the Chemours Company (formerly a part of DuPont), Viton's established reputation can also be a factor in its pricing.
6. Durability and Longevity: Products made from FKM tend to last longer than those made from other materials, which can make them more cost-effective in the long run, despite the higher initial cost.
In summary, Viton's high price is a reflection of its superior quality, durability, and the specialized manufacturing process required to produce it.