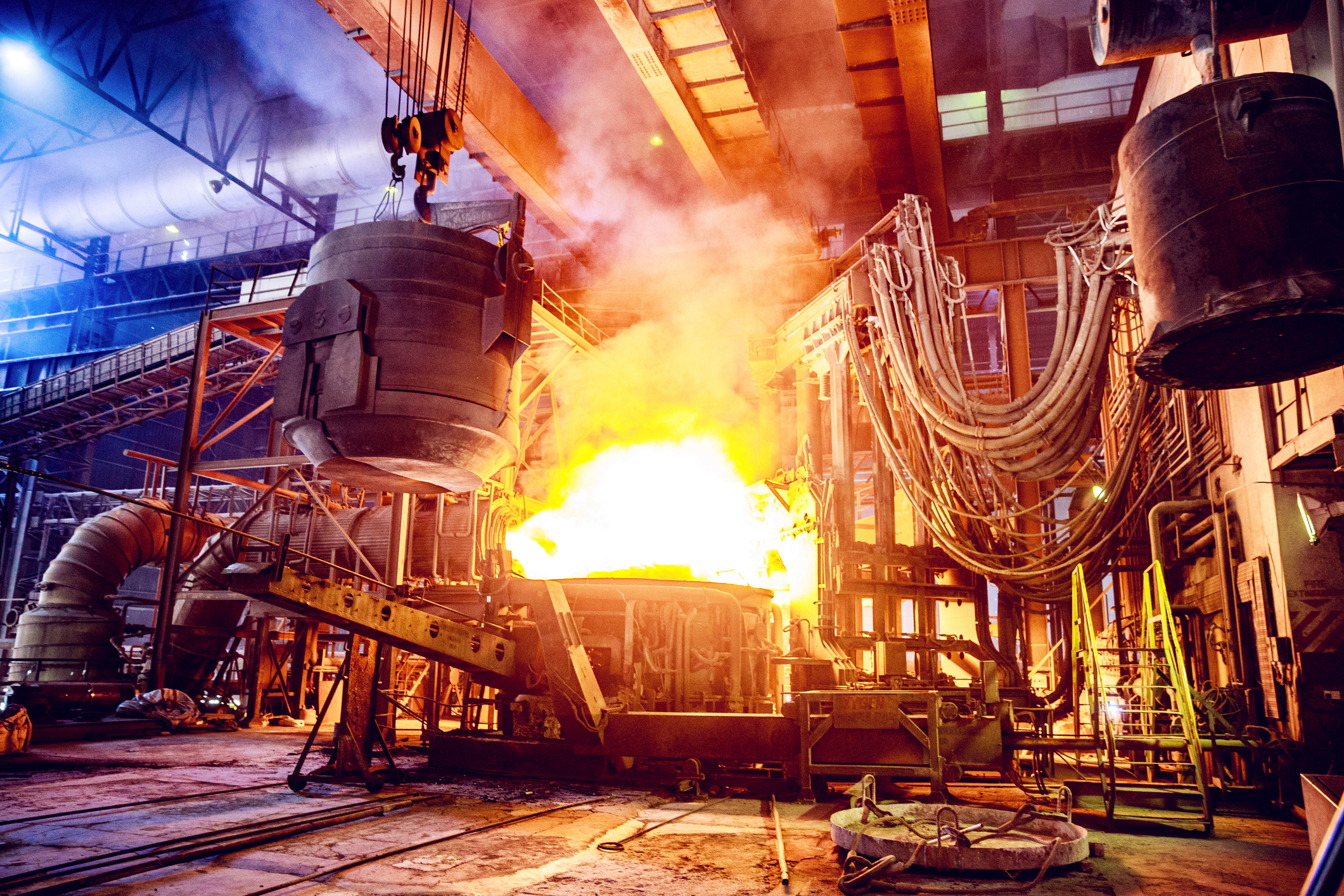
High-Performance Foam & Sponge Materials
High-performance foam and sponge materials are essential in various industries, offering versatile solutions for sealing, cushioning, insulation, and vibration damping. These materials are engineered to provide superior performance in demanding environments, making them ideal for applications where reliability and durability are crucial. This guide covers the features, common applications, and the pros and cons of high-performance foam and sponge materials, with a focus on EVA foam, silicone sponge, Viton sponge, and more.
Foam parts available now! CanRez® FFKM and Kalrez® grommets, O-rings, gasket rapid manufacturing, & custom molded parts are available now!
Check with one of Canyon’s helpful product engineers for an expert material and manufacturing recommendation.
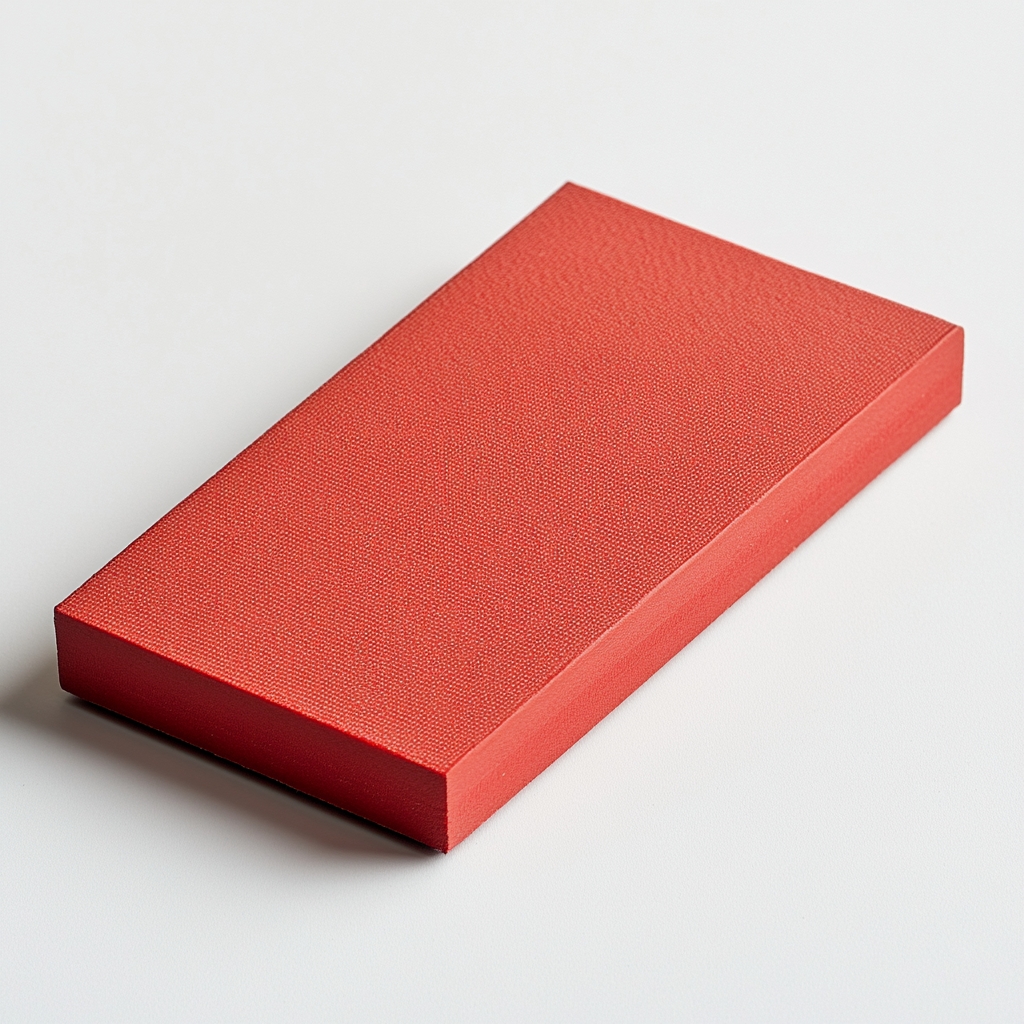
Features of High-Performance Foam and Sponge Materials
High-performance foam and sponge materials offer several key features that make them suitable for demanding applications:
- Excellent Compression Set Resistance: These materials maintain their shape and functionality even after prolonged compression, ensuring long-lasting performance in sealing and cushioning applications.
- High Temperature and Chemical Resistance: Many high-performance foams and sponges can withstand extreme temperatures and resist chemical degradation, making them ideal for harsh environments.
- Flexibility and Resilience: These materials are designed to provide excellent flexibility and resilience, allowing them to conform to irregular surfaces and return to their original shape after deformation.
- Lightweight and Low Density: High-performance foams and sponges are lightweight, reducing the overall weight of the final product while providing effective cushioning and insulation.
- Sound and Vibration Dampening: These materials are effective at absorbing sound and dampening vibrations, making them suitable for noise reduction and vibration control applications.
Common Applications of High-Performance Foam and Sponge Materials
High-performance foam and sponge materials are used in a wide range of industries and applications:
- Automotive: These materials are used for gaskets, seals, and insulation in vehicles, providing noise reduction, thermal insulation, and protection against dust and moisture.
- Electronics: Foam and sponge materials are used for cushioning and insulating electronic components, protecting them from shock, vibration, and environmental factors.
- Medical Devices: In the medical industry, these materials are used for seals, gaskets, and padding in devices and equipment, where biocompatibility and resilience are essential.
- Aerospace: High-performance foams and sponges are used in aerospace applications for insulation, sealing, and cushioning, where lightweight and high-temperature resistance are critical.
- Construction: These materials are used in construction for sealing, insulation, and soundproofing, providing long-lasting performance in harsh environments.
Please consult a Canyon Components Engineer about your specific application and we will use our decades of experience to formulate a solution that fits your need.
Get a Quote Now!
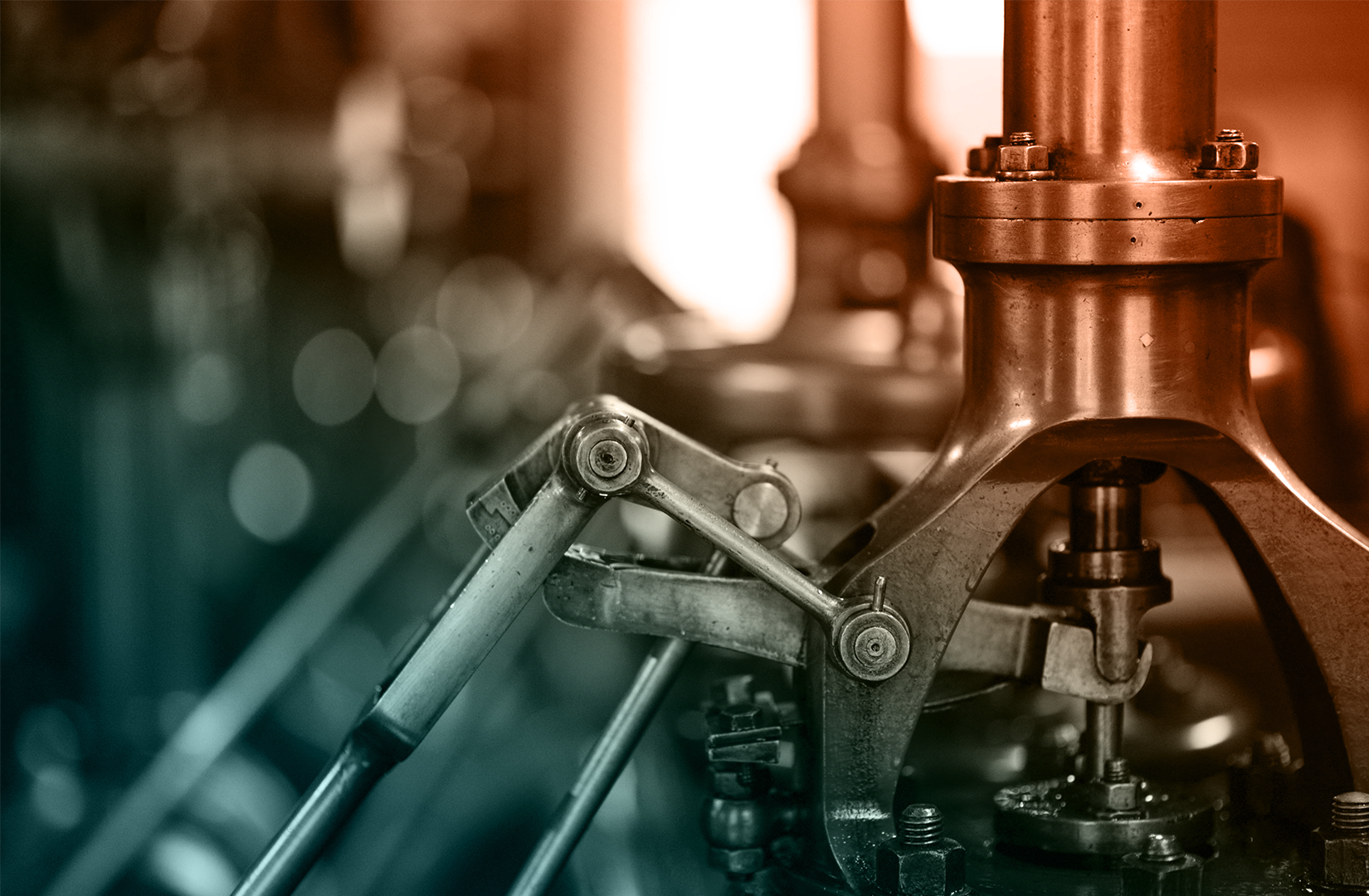
Materials Used in High-Performance Foam and Sponge Products
EVA Foam (Ethylene Vinyl Acetate)
- Features: EVA foam is known for its excellent cushioning properties, flexibility, and resistance to stress-cracking. It is also lightweight and has good shock absorption capabilities.
- Applications: EVA foam is used in sports equipment, footwear, automotive interiors, and packaging, where cushioning and impact resistance are important.
- Pros: Lightweight, flexible, good shock absorption, chemical resistance.
- Cons: Limited heat resistance, may degrade under prolonged UV exposure.
Silicone Sponge
- Features: Silicone sponge offers excellent temperature resistance, flexibility, and resilience. It is also highly resistant to UV, ozone, and chemicals, making it suitable for outdoor and high-temperature applications.
- Applications: Silicone sponge is used in automotive, aerospace, and medical applications for gaskets, seals, and insulation, where high performance under extreme conditions is required.
- Pros: High-temperature resistance, UV and ozone resistance, flexible and resilient.
- Cons: Higher cost compared to other materials, limited mechanical strength.
Viton Sponge
- Features: Viton FKM sponge is known for its exceptional chemical resistance, particularly to fuels, oils, and acids. It also offers good heat resistance and compression set properties.
- Applications: Viton sponge is used in the chemical processing, automotive, and aerospace industries for seals, gaskets, and insulation, where exposure to harsh chemicals is common.
- Pros: Excellent chemical resistance, good heat resistance, low compression set.
- Cons: High cost, limited availability, not suitable for low-temperature applications.
Neoprene Foam
- Features: Neoprene foam provides good thermal and moisture insulation, as well as resistance to weathering, ozone, and oil. It is also flexible and durable.
- Applications: Neoprene foam is commonly used in automotive, marine, and industrial applications for gaskets, seals, and insulation.
- Pros: Good weather and oil resistance, flexible, durable.
- Cons: Moderate chemical resistance, can be more expensive than standard foams.
EPDM Foam (Ethylene Propylene Diene Monomer)
- Features: EPDM foam is known for its excellent resistance to weathering, UV radiation, and ozone. It also offers good flexibility and resilience, making it suitable for outdoor applications.
- Applications: EPDM foam is used in automotive weatherstripping, HVAC systems, and outdoor equipment for sealing and insulation.
- Pros: Excellent weather and UV resistance, flexible, durable.
- Cons: Limited oil and fuel resistance, higher cost compared to standard rubber foams.
Product Types
Custom Parts
Here at Canyon Components, we make sure to offer our customers any manufacturing technique they desire. Whether your O-rings, gaskets, & custom molded parts be rubber, plastic, or metal, rest assured that Canyon Components can make it!
Gaskets & Custom Cutting
Whether your custom cut parts be rubber, plastic, sponge, composite, or metal, rest assured that Canyon Components can make it! Canyon Components strives to meet all customer service requests. If you need something that isn't listed, feel free to contact a Canyon Components product and application consultant.
Specialty Compliances
Canyon have materials available for O-rings, gaskets, & custom parts with compliances ranging from USP Class VI <87> & <88> for medical applications, to FDA CFR 21.177.2600 grades A through F for different food types, to the various drinking water specifications like KTW and NSF. Whether it's metal, rubber, or plastic, Canyon can meet your needs!
Open-Cell vs. Closed-Cell Foam
Open-Cell Foam
- Features: Open-cell foam has interconnected pores that allow air and liquids to pass through, making it breathable and soft. It is less dense and provides good cushioning and sound absorption.
- Applications: Open-cell foam is used in cushioning, acoustic panels, and insulation where breathability and sound absorption are important.
- Pros: Breathable, lightweight, good sound absorption.
- Cons: Less resistant to moisture and less durable than closed-cell foam.
Closed-Cell Foam
- Features: Closed-cell foam has sealed, non-interconnected cells that make it dense, water-resistant, and highly durable. It provides excellent insulation and buoyancy.
- Applications: Closed-cell foam is used in sealing, insulation, flotation devices, and protective padding where moisture resistance and durability are critical.
- Pros: Water-resistant, durable, excellent insulation.
- Cons: Less breathable, higher density, and potentially more expensive than open-cell foam.
Foam & Sponge Pros & Cons
High-performance foam and sponge materials are essential for a wide range of applications, offering excellent sealing, insulation, cushioning, and more. With materials like EVA foam, silicone sponge, and Viton sponge, these products provide superior performance in demanding environments. Understanding the differences between open-cell and closed-cell foams, as well as the pros and cons of each material, will help you make informed decisions to ensure optimal performance in your applications. Whether you need a solution for automotive, aerospace, medical, or industrial applications, high-performance foam and sponge materials offer the versatility and reliability you need.
Canyon Components strives to meet all customer service requests. Feel free to contact Canyon Components engineering and let our knowledgeable staff help you design the perfect part for your needs.
Pros of High-Performance Foam and Sponge Materials
High-performance foam and sponge materials offer several advantages that make them ideal for demanding applications:
- Versatility: Available in a wide range of materials and formulations, these products can be tailored to meet specific performance requirements.
- Durability: High-performance foams and sponges are designed to withstand harsh environments, providing long-lasting performance in sealing, insulation, and cushioning applications.
- Lightweight: These materials offer effective performance without adding significant weight to the final product, making them ideal for applications where weight is a concern.
- Customizability: Foam and sponge materials can be easily cut, shaped, and molded to fit precise specifications, ensuring a perfect fit for any application.
Cons of High-Performance Foam and Sponge Materials
While high-performance foam and sponge materials offer many benefits, there are also some potential drawbacks to consider:
- Cost: High-performance materials, especially specialized foams like Viton sponge or silicone sponge, can be more expensive than standard foam products.
- Material Limitations: Each material has its own set of limitations, such as limited chemical resistance or mechanical strength, which may make it unsuitable for certain applications.
- Processing Complexity: Some high-performance foams and sponges require specialized processing techniques, which can increase production time and cost.
Back to Products Hub
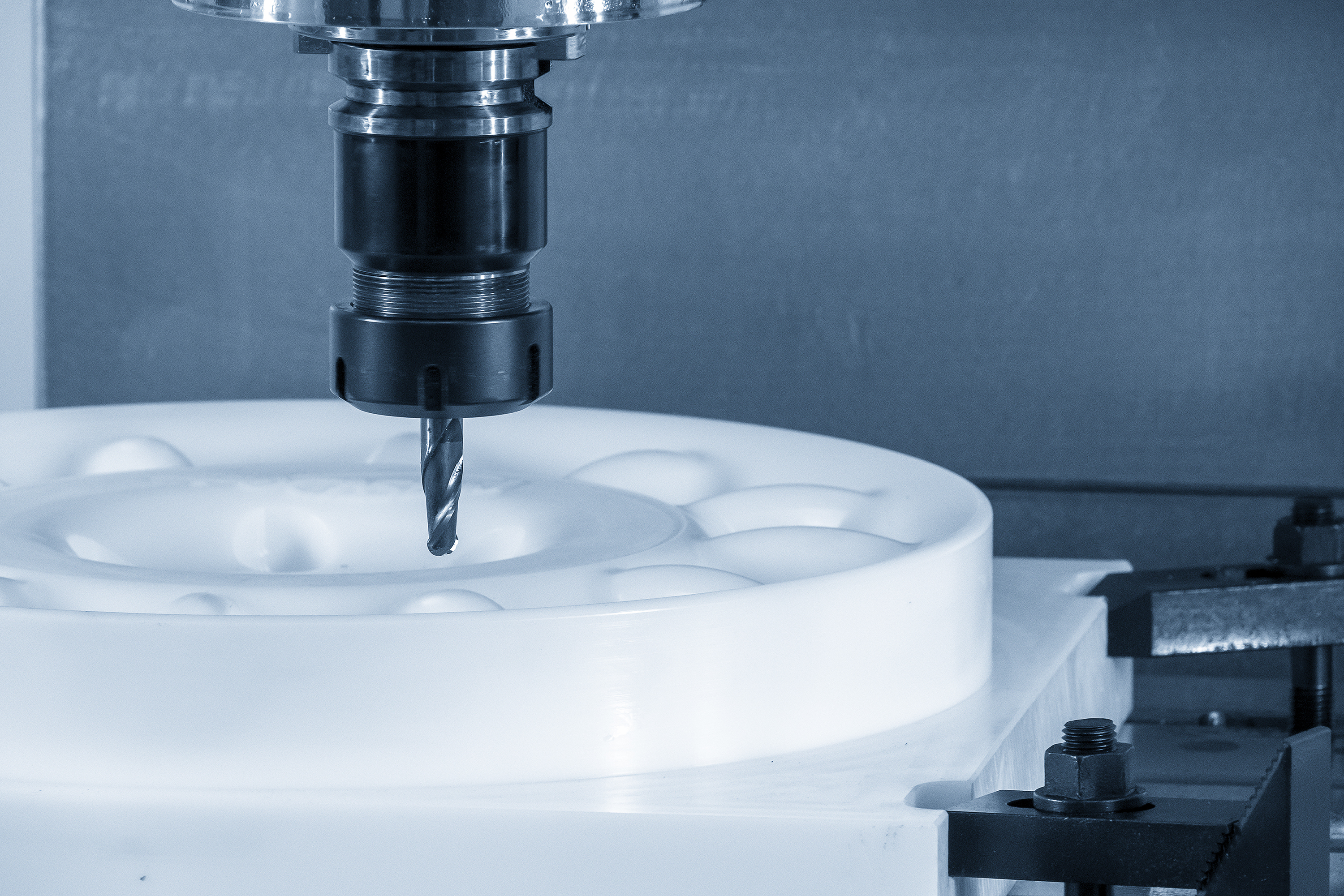
Get A Quote Now!
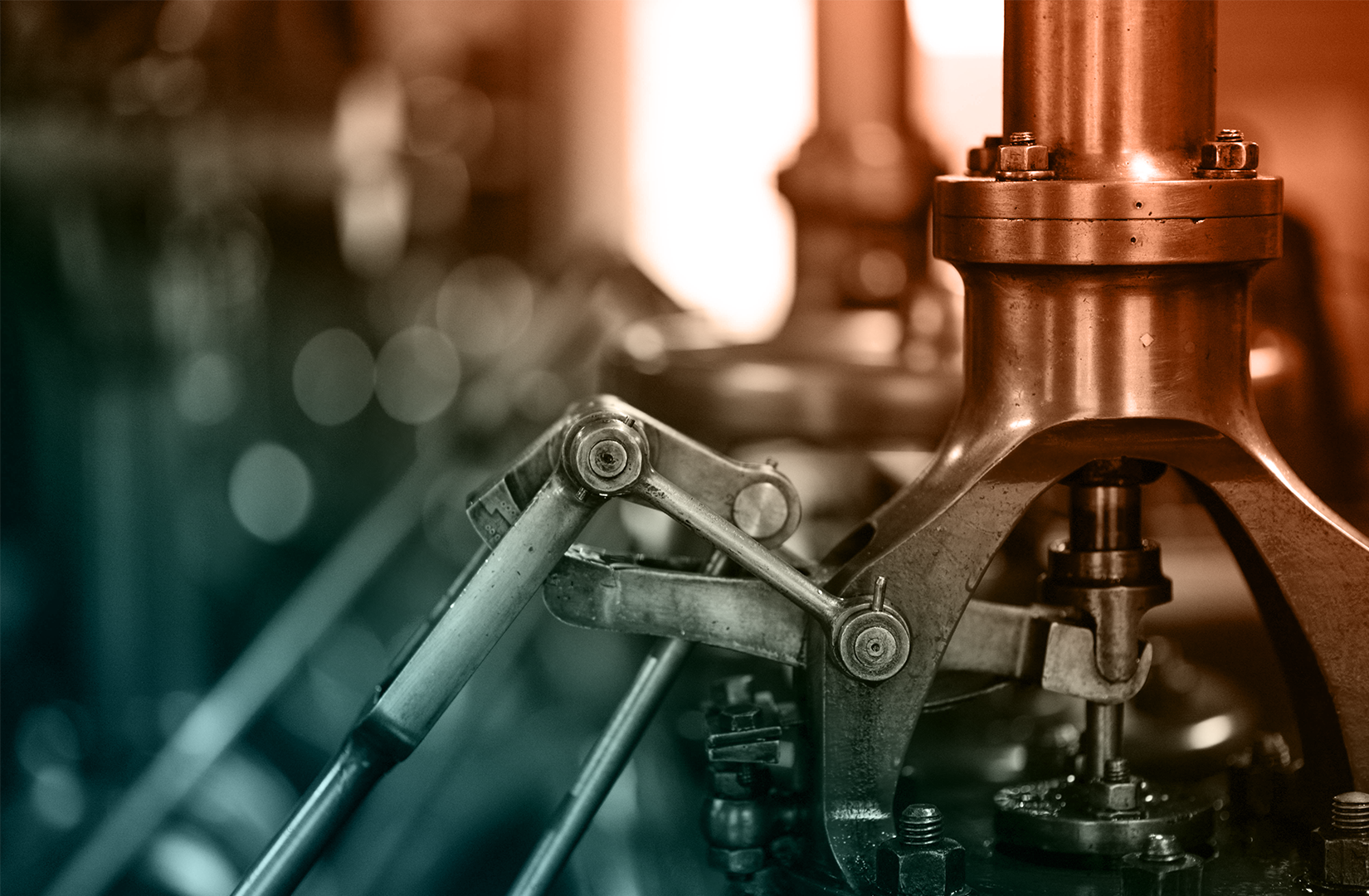