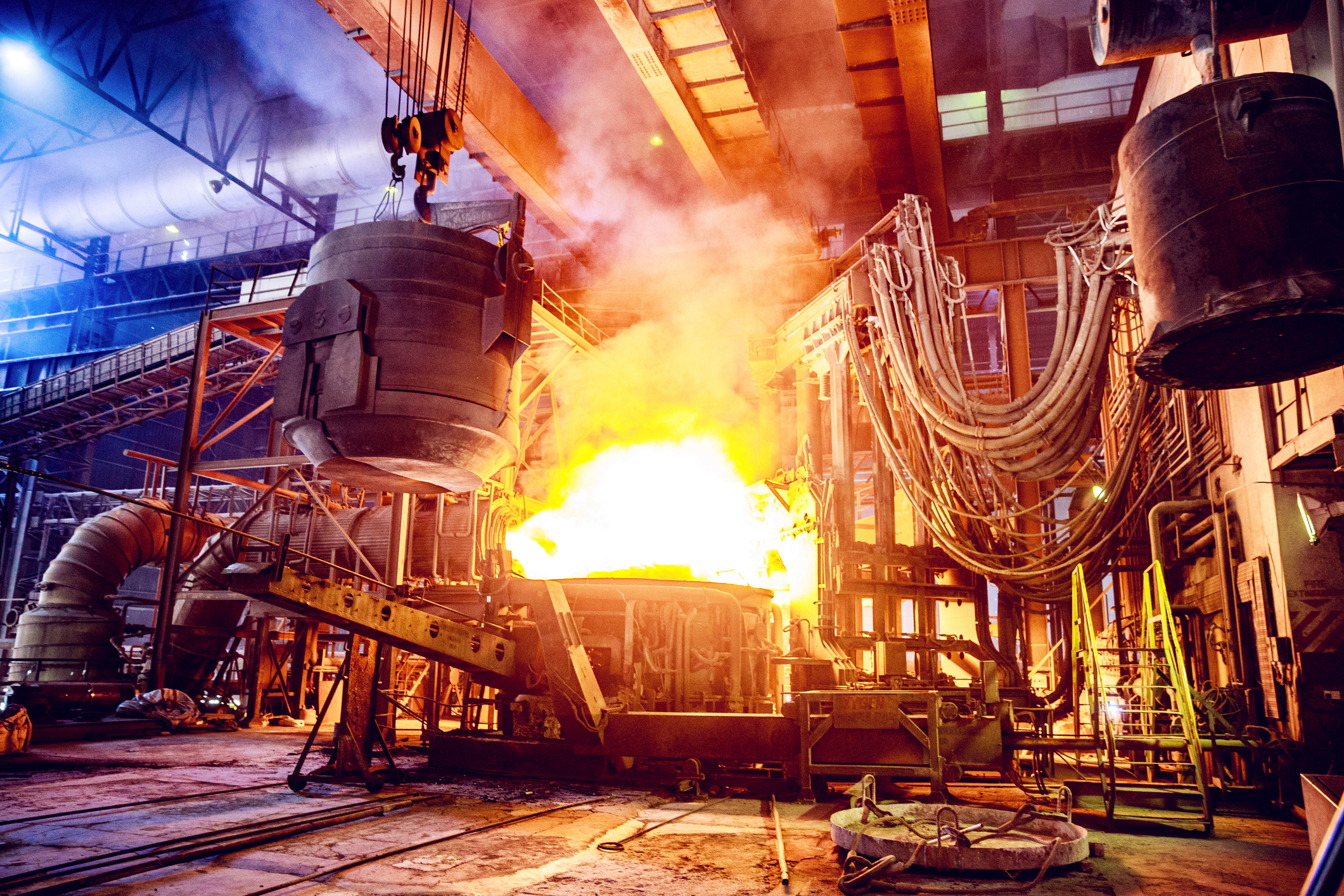
High Temperature Silicone (VMQ, PVMQ) Selection Guide
High temperature silicone is engineered to perform exceptionally well under extreme thermal conditions, making it an invaluable material in various demanding industries. This webpage delves into the different types of high temperature silicone, explores their benefits and limitations, and highlights their industrial applications, particularly focusing on O-rings, gaskets, and custom parts.
The engineers and consultants here at Canyon Components take pride in finding the perfect seal to suit our customer’s needs. Contact our expert staff for assistance with any seal or application questions!
Common names include: VQM (Silicone), PVMQ Trade Name: Silastic®, Elastosil®, Thermoflex®, Wacker, DOW Corning, DOWSIL.
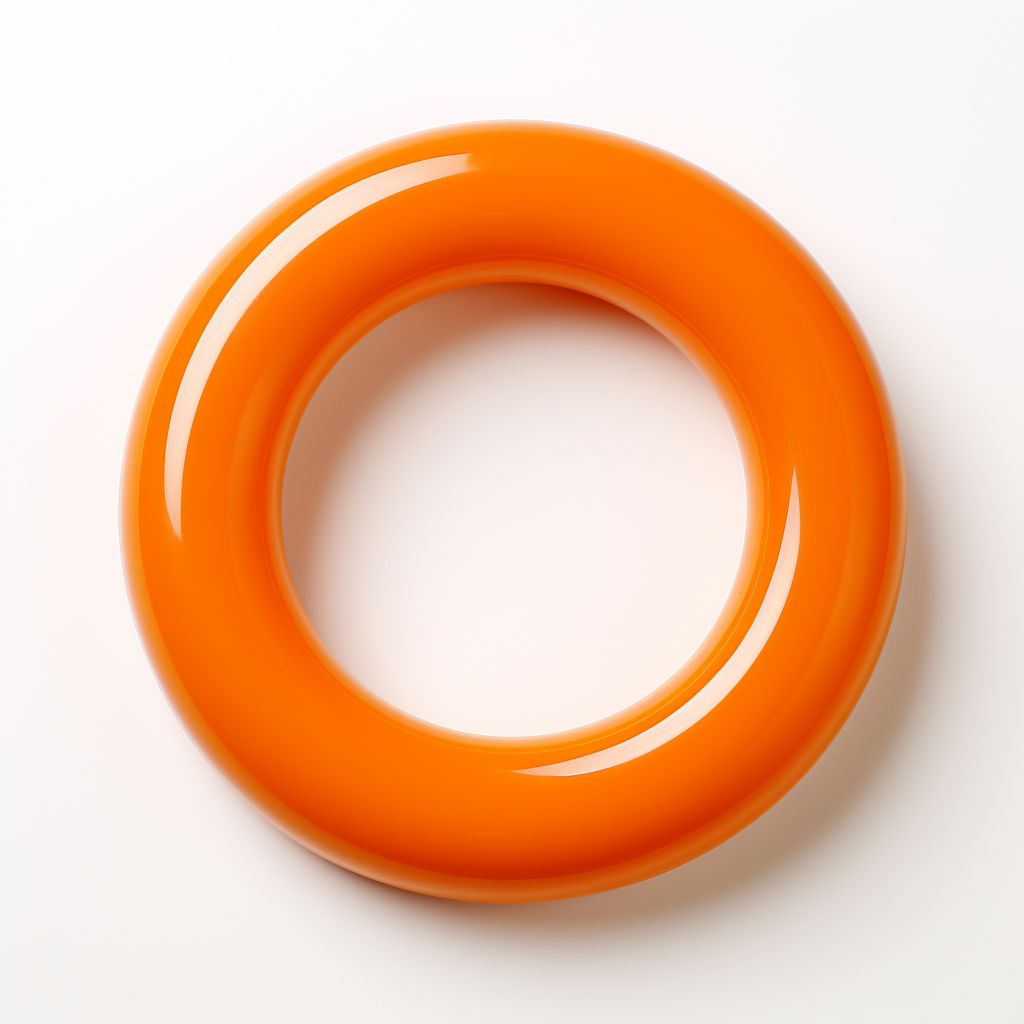
Request a Quote for High Temperature Silicone
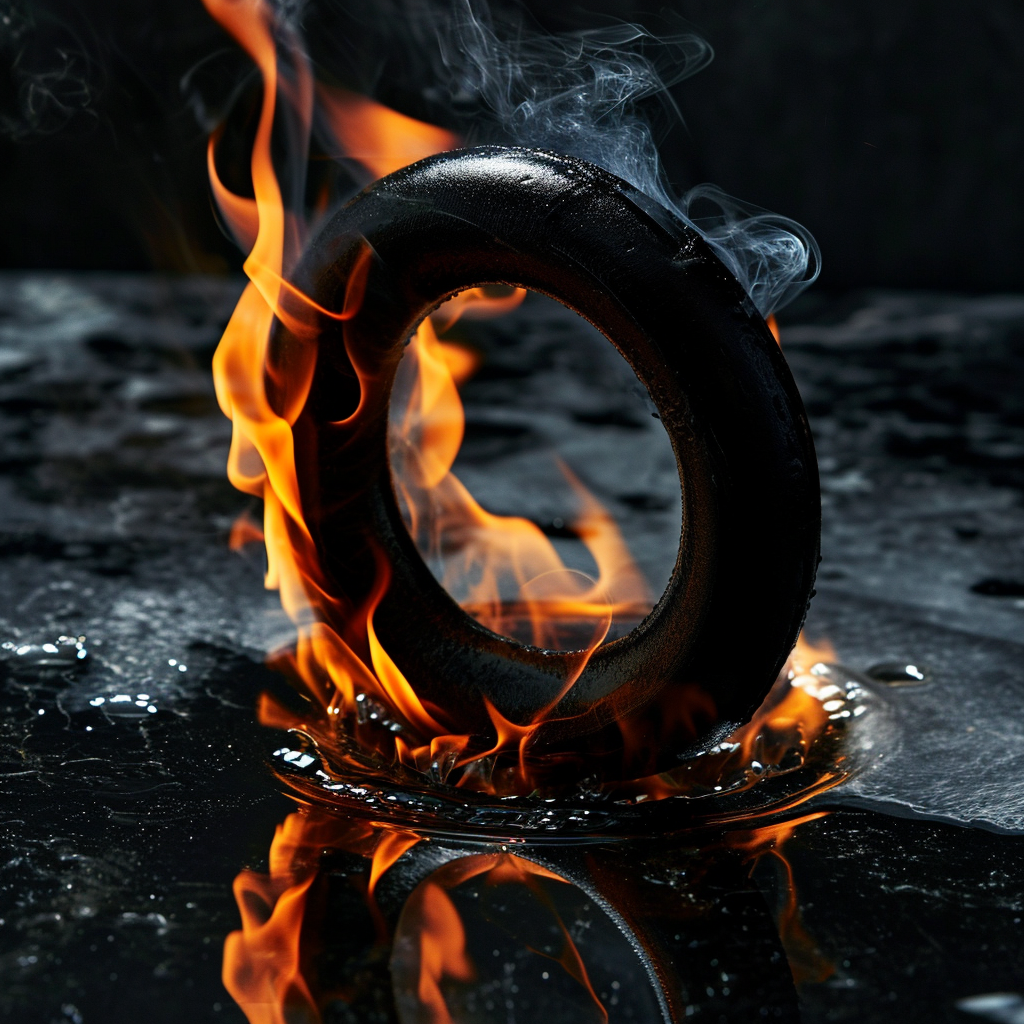
Please consult a Canyon Components Engineer about your specific application and we will use our decades of experience to formulate a solution that fits your need.
Features of High Temperature Silicone
- Thermal Stability: High temperature silicone, like Canyon Components SI80OR51, are capable of handling temperatures up to 600°F (315°C), while standard silicone is typically rated for temperatures up to 401°F (205°C).
- Chemical Resistance: Resistant to a variety of chemicals, making O-rings, gaskets, and custom parts made from this material highly durable in harsh environments.
- Electrical Insulation: Excellent insulator, suitable for use in electrical and electronic applications.
- Flexibility: Maintains its flexibility over a broad temperature range, ensuring a consistent seal in temperature-critical applications.
- Durability: Exhibits superior longevity and performance, reducing the need for frequent replacements.
Limitations of High Temperature Silicone
- Cost: Generally more expensive than regular silicone due to its enhanced properties.
- Tear Strength: While resistant to high temperatures, it often has lower tear strength and can be susceptible to mechanical damage.
- Limited Resistance: Not suitable for applications involving ketones, concentrated acids, and steam above certain temperatures.
High Temperature Silicone Materials Available
This table shows many of our standard materials and links out to our O-ring store. Get in touch with us if you need a custom gasket, custom molded part, or non-standard geometry!
Filter by
Temperature Search (°C)
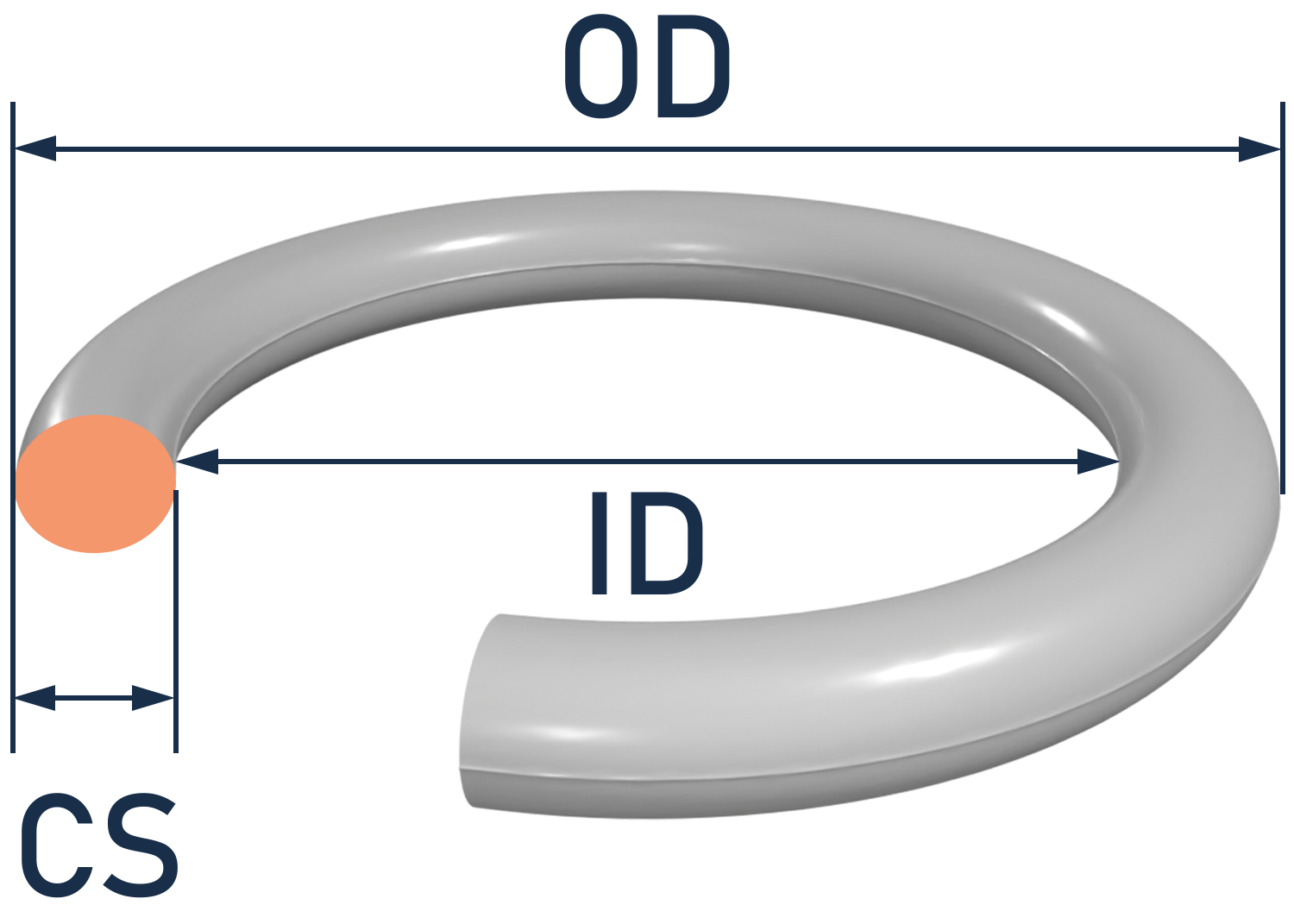
Industrial Usage of High Temperature Silicone
High temperature silicone is crucial for manufacturing O-rings, gaskets, and custom parts that can withstand extreme conditions without compromising performance. Its resilience in high temperature environments makes it a preferred material in industries where reliability under heat stress is critical. Despite its higher cost and some limitations, the benefits of using high temperature silicone in critical applications often outweigh these factors, underlining its value in demanding industrial settings.
Canyon Components strives to meet all customer service requests. Feel free to contact Canyon Components engineering and let our knowledgeable staff help you design the perfect part for your needs.
Energy Sector
In applications like oil and gas extraction and processing, where high temperature and chemical resistance are paramount, silicone components are essential for maintaining system integrity.
Food and Beverage
Silicone parts such as seals and tubing are used in food processing equipment, benefiting from silicone’s thermal stability and food-grade compliance.
Aerospace and Automotive
O-rings, gaskets, and custom parts within engines, fuel systems, and exhaust assemblies must resist high temperatures and chemical exposure.
Electronics
Used in O-rings, gaskets, custom parts, coatings and encapsulants for components that must endure high operating temperatures.
Manufacturing
High temperature silicone molds and parts are crucial in processes involving heated materials, ensuring that O-rings, gaskets, and custom parts do not degrade or lose shape.
Please consult a Canyon Components Engineer about your specific application and we will use our decades of experience to formulate a solution that fits your need.
Back to Elastomers Hub
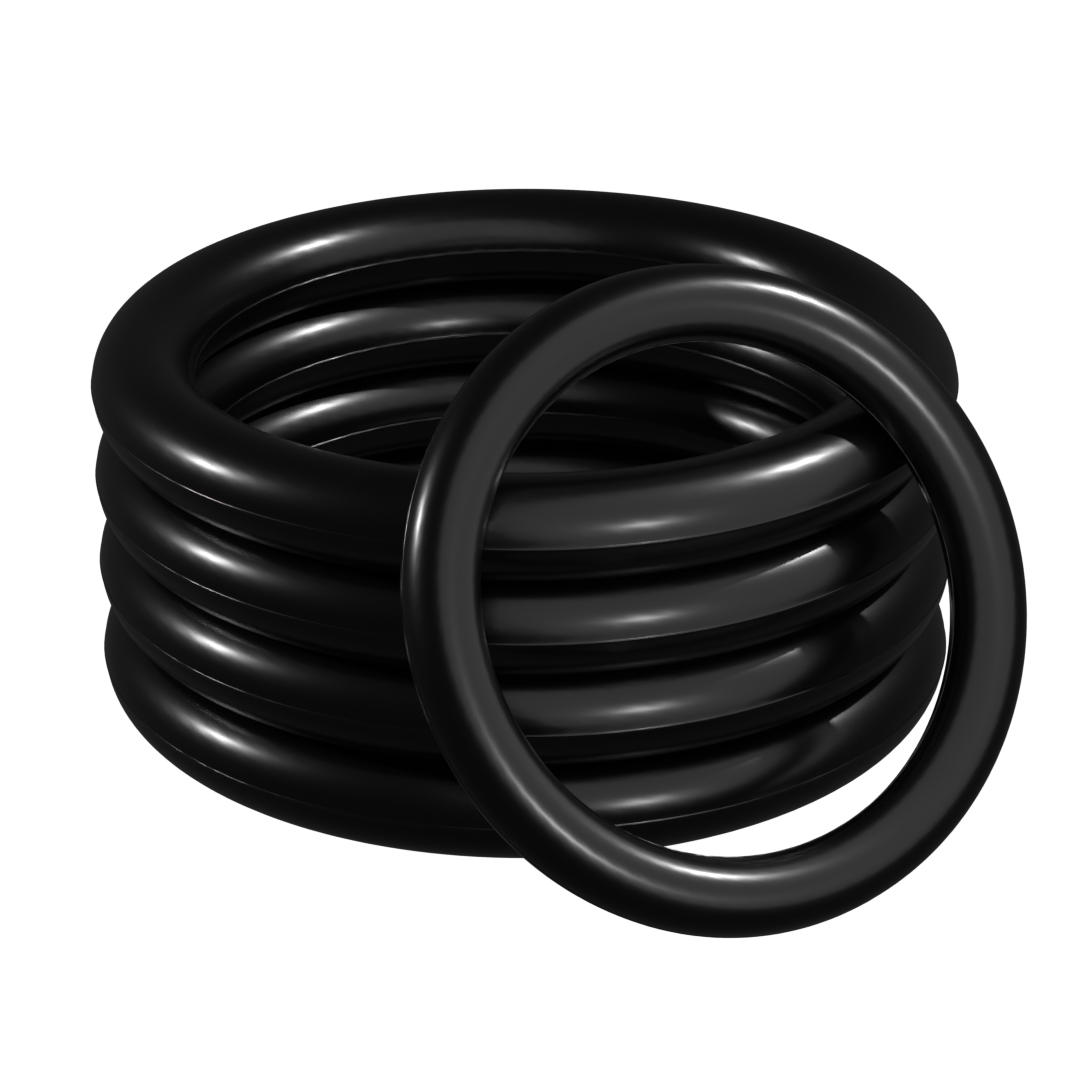
Get A Quote Now!
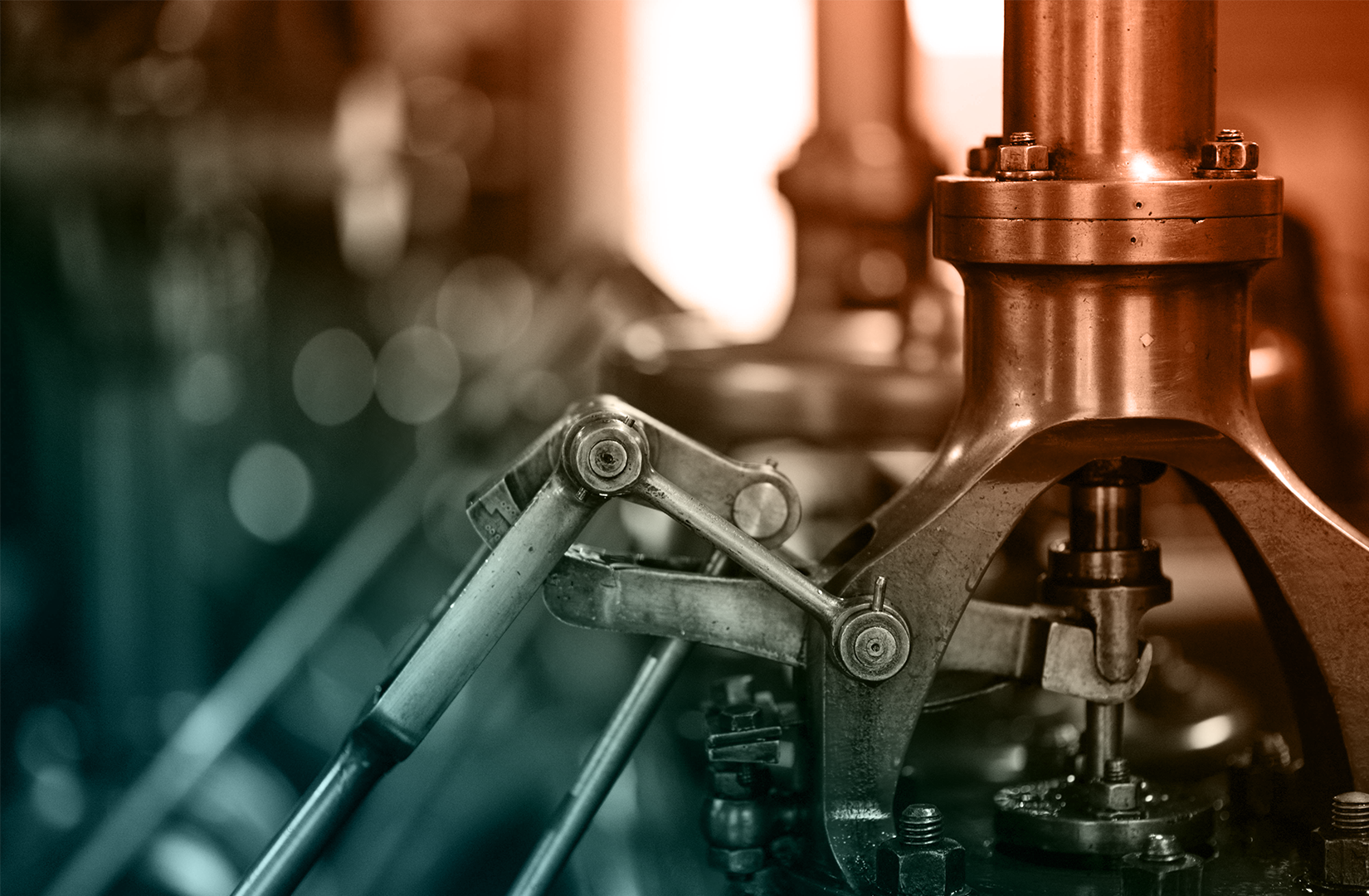
Groove Design References
Learn More
Coatings, Packaging, & Other Services
Learn More
Custom Parts & Custom O-rings
Learn More