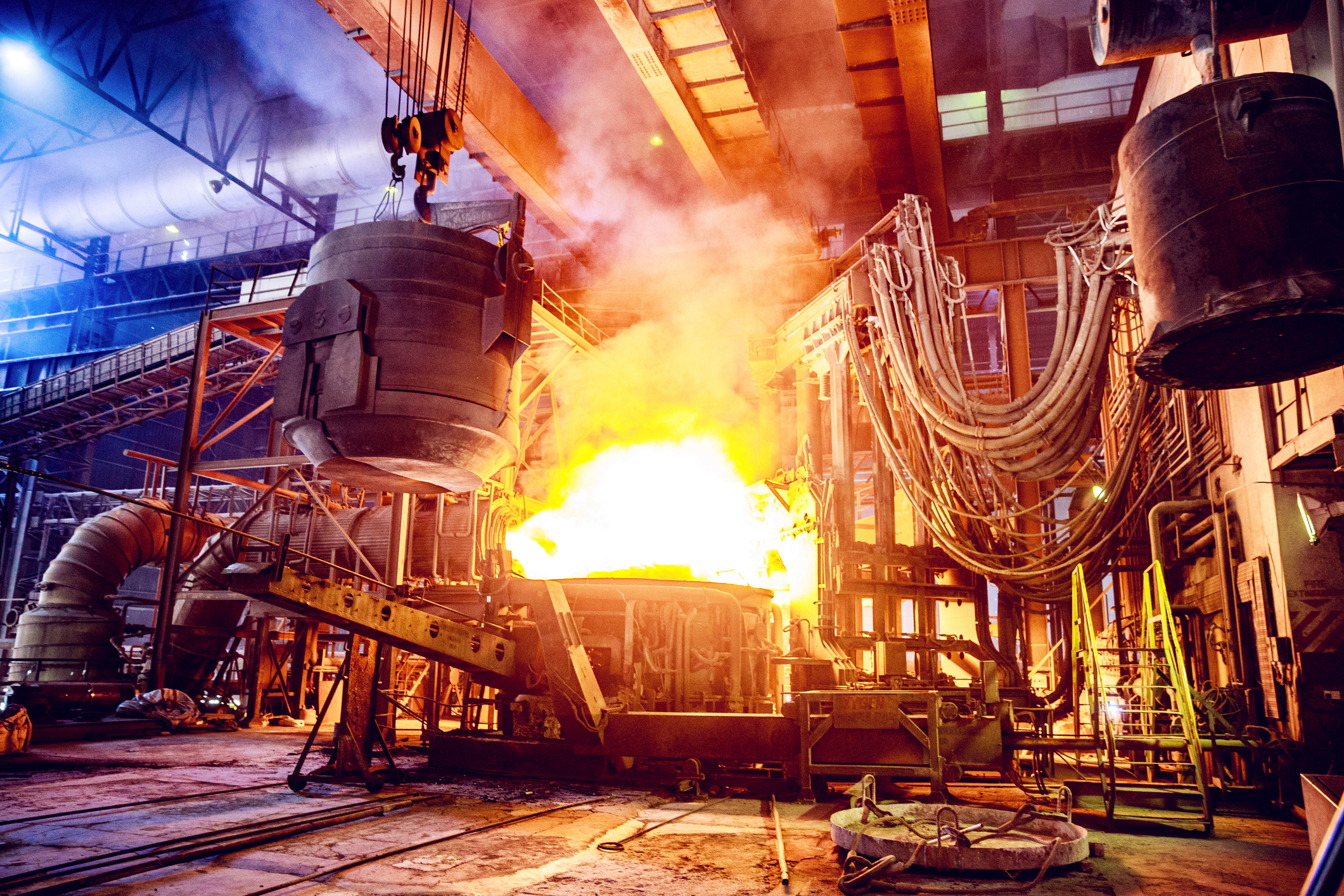
ABS Plastic (Acrylonitrile Butadiene Styrene) Selection Guide
ABS (Acrylonitrile Butadiene Styrene) is a versatile and widely used thermoplastic polymer known for its durability, impact resistance, and ease of processing. It has a wide range of applications across various industries due to its unique combination of properties. In this web page, we will explore the different types of ABS, its advantages and disadvantages, as well as its industrial uses. Additionally, we will provide a list of manufacturing methods available for ABS.
ABS plastic (Acrylonitrile Butadiene Styrene) rapid manufacturing, & custom molded parts are available now!
Check with one of Canyon’s helpful product engineers for an expert material and manufacturing recommendation.
Common names include: ABS plastic (Acrylonitrile Butadiene Styrene) Trade Names: Cycolac®, Lustran®, Royalite®, TECARAN™, Absylux®, Polystone®.
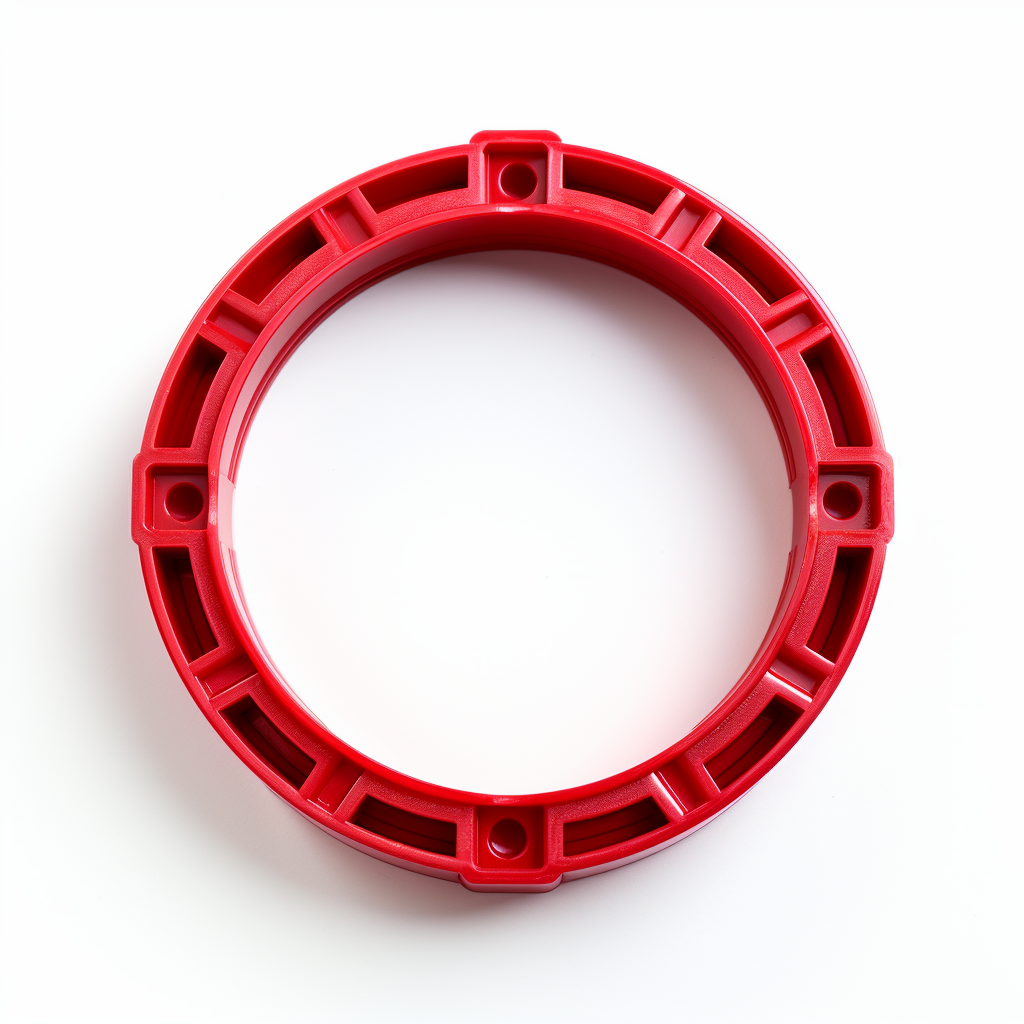
Advantages
- Impact Resistance: ABS is highly impact-resistant, making it ideal for products that need to withstand rough handling or potential falls.
- Versatility: It can be easily molded into various shapes, making it suitable for intricate and complex designs.
- Chemical Resistance: ABS is resistant to many chemicals, ensuring its stability in diverse environments.
- Good Thermal Stability: It retains its structural integrity in a wide range of temperatures, from -20°C to 80°C (-4°F to 176°F).
- Surface Finish: ABS can be easily sanded, painted, and post-processed to achieve the desired surface finish and appearance.
- Cost-Effective: ABS is relatively affordable compared to some other engineering plastics.
Disadvantages
- Limited UV Resistance: Standard ABS can degrade when exposed to prolonged sunlight, so it may not be suitable for long-term outdoor applications without UV stabilizers.
- Not Suitable for High-Temperature Environments: ABS has a lower heat resistance compared to some other plastics like PEEK or PPS. It may soften or deform at high temperatures.
- Potential for Warping: ABS has a tendency to warp during cooling, especially with larger parts. This can be mitigated with proper cooling techniques.
- Odor and Fumes: During processing, ABS can emit unpleasant odors and fumes, so adequate ventilation is necessary.
Common Applications of ABS
- Automotive: ABS is commonly used in automotive interiors and exteriors, including dashboards, bumpers, and trim components due to its impact resistance and ability to be molded into intricate shapes.
- Electronics: Many electronic devices and housings are made from ABS due to its electrical insulation properties and flame-retardant options.
- Consumer Goods: ABS is used for manufacturing a variety of consumer products such as toys, luggage, kitchen appliances, and sporting goods.
- Construction: ABS pipes and fittings are used in plumbing systems, and ABS sheets find use in architectural models and signage.
- Medical: ABS is employed in medical devices and equipment casings due to its biocompatibility and ease of sterilization.
Please consult a Canyon Components Engineer about your specific application and we will use our decades of experience to formulate a solution that fits your need.
Types of ABS
ABS can come in different variations, depending on its composition and intended use. Some common types of ABS include the following.
Canyon Components strives to meet all customer service requests. Feel free to contact Canyon Components engineering and let our knowledgeable staff help you design the perfect part for your needs.
General Purpose ABS
This type of ABS plastic offers a balanced combination of mechanical toughness, impact resistance, and ease of fabrication. Ideal for a wide range of applications, it is often used in automotive parts, consumer goods, and electronic casings. Its versatility makes it a popular choice for both prototyping and mass production.
Flame Retardant ABS
Specifically engineered for applications requiring enhanced fire resistance, Flame Retardant ABS contains additives that reduce its flammability. It is widely used in the electronics and automotive industries, especially in scenarios where parts must meet certain fire safety standards without sacrificing the material's inherent strength and rigidity.
Heat Resistant ABS
Designed to withstand higher temperatures, Heat Resistant ABS maintains its structural integrity and dimensional stability under thermal stress. This type makes it suitable for applications such as automotive under-hood components and household appliances that are exposed to elevated temperatures.
Transparent ABS
Offering a unique combination of clarity and high impact strength, Transparent ABS is used in applications where visibility of the inner workings is necessary, like in medical devices, transparent covers, and certain consumer products. It provides an aesthetically appealing see-through appearance while retaining the durability of standard ABS.
High Flow ABS
With its enhanced flow characteristics, High Flow ABS is specifically designed for intricate and complex molds. This type is ideal for producing thin-walled parts with a high level of precision and detail, commonly used in the manufacturing of intricate consumer goods and detailed automotive components.
High Impact ABS
Engineered for applications requiring superior toughness, High Impact ABS has an increased resistance to shock and stress. This type is especially useful in products that are prone to impacts or drops, such as protective gear, sporting goods, and durable consumer products, where maintaining structural integrity is crucial.
Please consult a Canyon Components Engineer about your specific application and we will use our decades of experience to formulate a solution that fits your need.
Manufacturing Options for ABS
ABS parts can be manufactured using several methods, each suitable for different applications and part complexities.
Each of these methods has its own advantages, limitations, and cost implications. The choice of manufacturing technique usually depends on factors like the complexity of the design, required precision, material properties, and production volume.
Canyon Components strives to meet all customer service requests. Feel free to contact Canyon Components engineering and let our knowledgeable staff help you design the perfect part for your needs.
Back to Plastics Hub
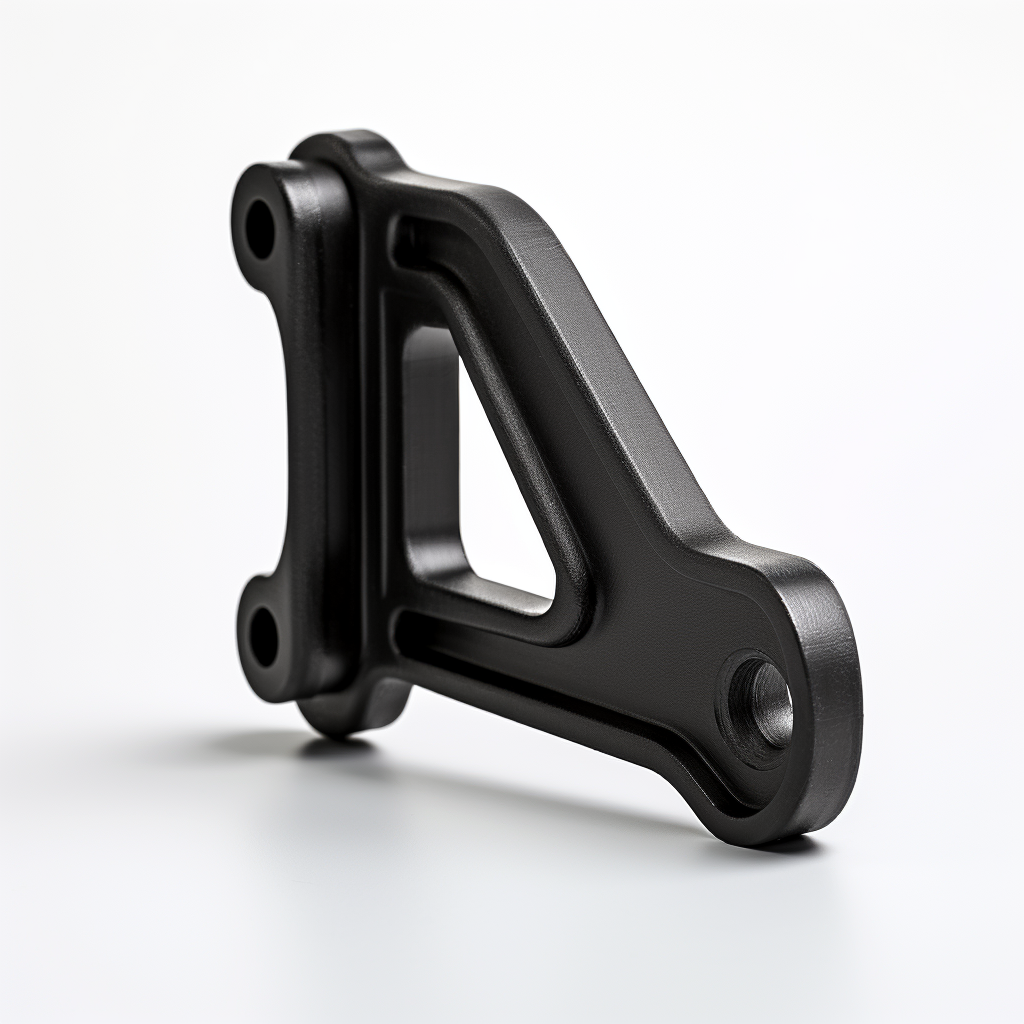
Get A Quote Now!
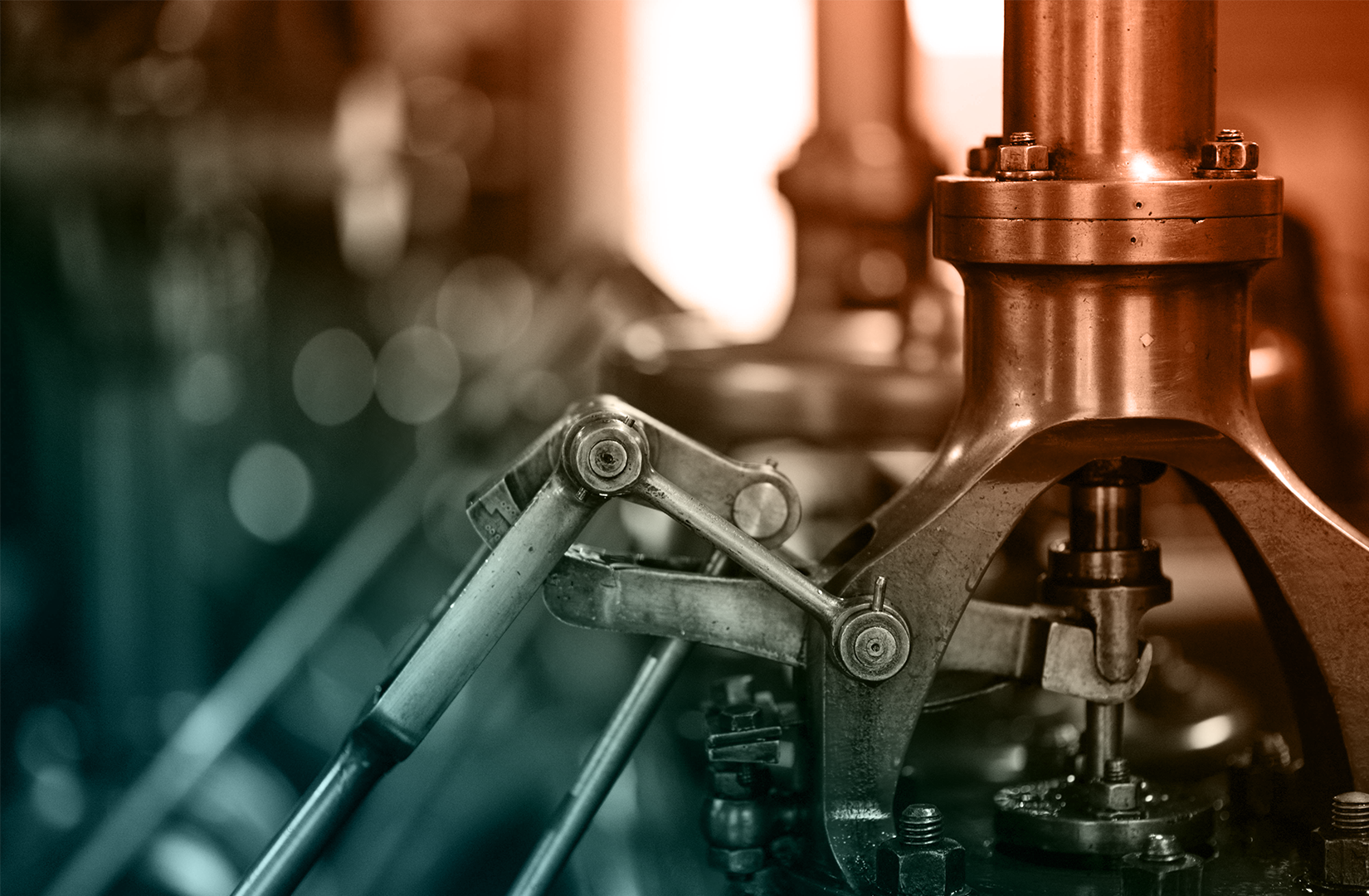
Groove Design References
Learn More
Coatings, Packaging, & Other Services
Learn More
Custom Parts & Custom O-rings
Learn More