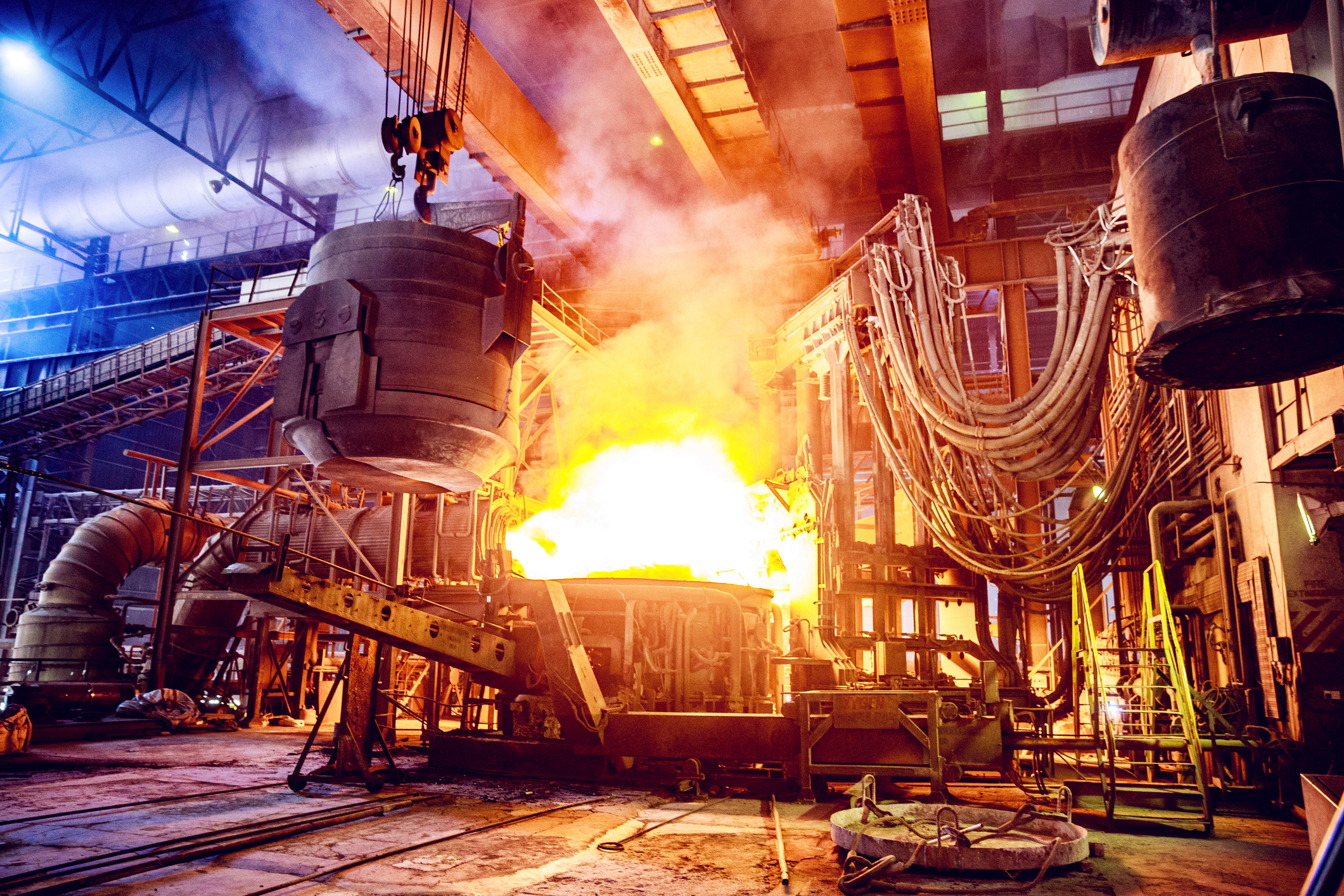
Manufacturing
Rubber, Plastic, and Metal parts can be manufactured using many methods, each suitable for different applications and part complexities. Here are some of the common manufacturing techniques that we offer, some of which may not be available for specific materials.
Each of these methods has its own advantages, limitations, and cost implications. The choice of manufacturing technique usually depends on factors like the complexity of the design, required precision, material properties, and production volume.
Canyon Components strives to meet all customer service requests. Feel free to contact Canyon Components engineering and let our knowledgeable staff help you design the perfect part for your needs.
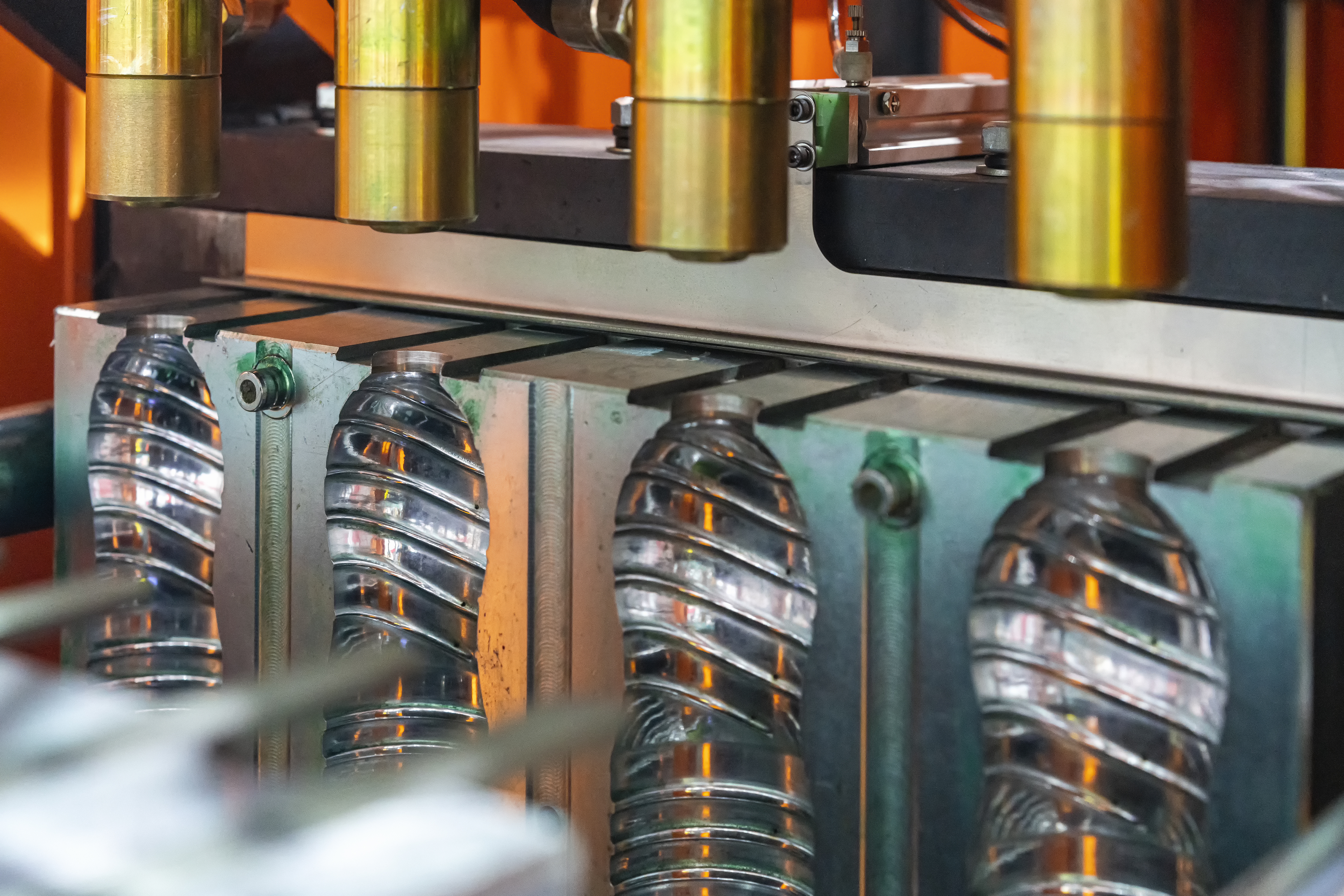
Manufacturing
Injection Molding
This is a popular method for producing high volumes of plastic or rubber parts. The plastic or rubber is injected in a molten form into a mold cavity where it cools and solidifies into the final shape. It's ideal for making complex shapes with high precision.
Extrusion
In this process, plastic, metal, or rubber, is forced through a die in a molten form to create long continuous shapes like pipes, tubing, sheets, or profiles. The extruded material is then cut to the desired length. It's excellent for producing products with a constant cross-sectional profile.
Thermoforming
In this process, a sheet of plastic is heated to a pliable forming temperature, formed to a specific shape in a mold, and trimmed to create a usable product. It's commonly used for packaging and larger parts like automotive door panels.
Micro-Extrusion
A specialized form of extrusion used to produce extremely small and precise plastic, metal, or rubber parts. It's ideal for medical devices and intricate components.
CNC Machining
This subtractive method involves starting with a solid block of plastic, metal, or rubber, and then cutting away material to create the desired shape. It's useful for prototypes and low-volume production of parts with high precision.
Blow Molding
This method is used to create hollow plastic parts such as bottles and containers. The plastic is melted and formed into a parison, which is then clamped into a mold. Air is blown into the parison, inflating it into the shape of the mold cavity.
Rotational Molding (Rotomolding)
Suitable for creating large, hollow parts. Plastic powder is placed inside a mold, which is then heated and rotated along two perpendicular axes. The plastic melts and coats the inside of the mold, forming the desired shape upon cooling.
Compression Molding
Plastic or rubber is placed in a heated mold cavity and then compressed to form a specific shape. This method is less common for many plastics, but can be used for large, fairly simple parts.
3D Printing (Additive Manufacturing)
3D printing can be used to produce complex geometries and bespoke parts. Specialized printers and filament types can be required when producing certain types of plastic, rubber, or metal.
Overmolding
This is a multistage process where a finished plastic, metal, or rubber part is inserted into a mold and another plastic or rubber is molded over it to create a composite part. It's used to add soft-touch surfaces or to combine rigid and flexible elements in a single component.
Casting
Involves pouring liquid plastic, rubber, or metal into a mold where it solidifies. This method is typically used for creating large, simple shapes or when a very smooth surface finish is required. It's less precise than injection molding but can be more cost-effective for small production runs or larger items. It can also be used for forming molten metal.
Cutting
Cutting manufacturing encompasses a range of processes that involve separating materials into desired shapes or sizes by removing excess material. It plays a crucial role in various industries, offering precision, speed, and versatility.
Back to Products Hub
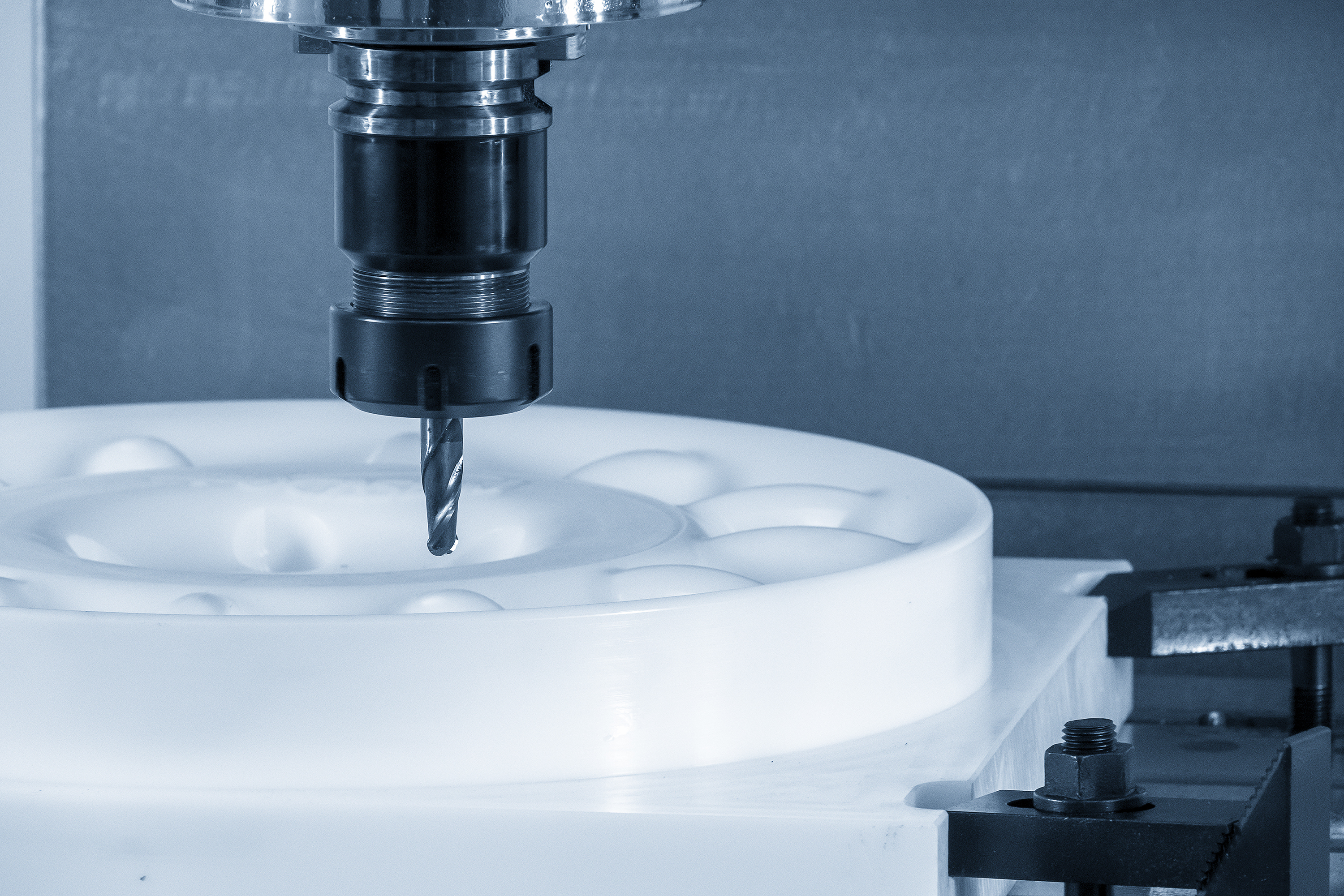
Get A Quote Now!
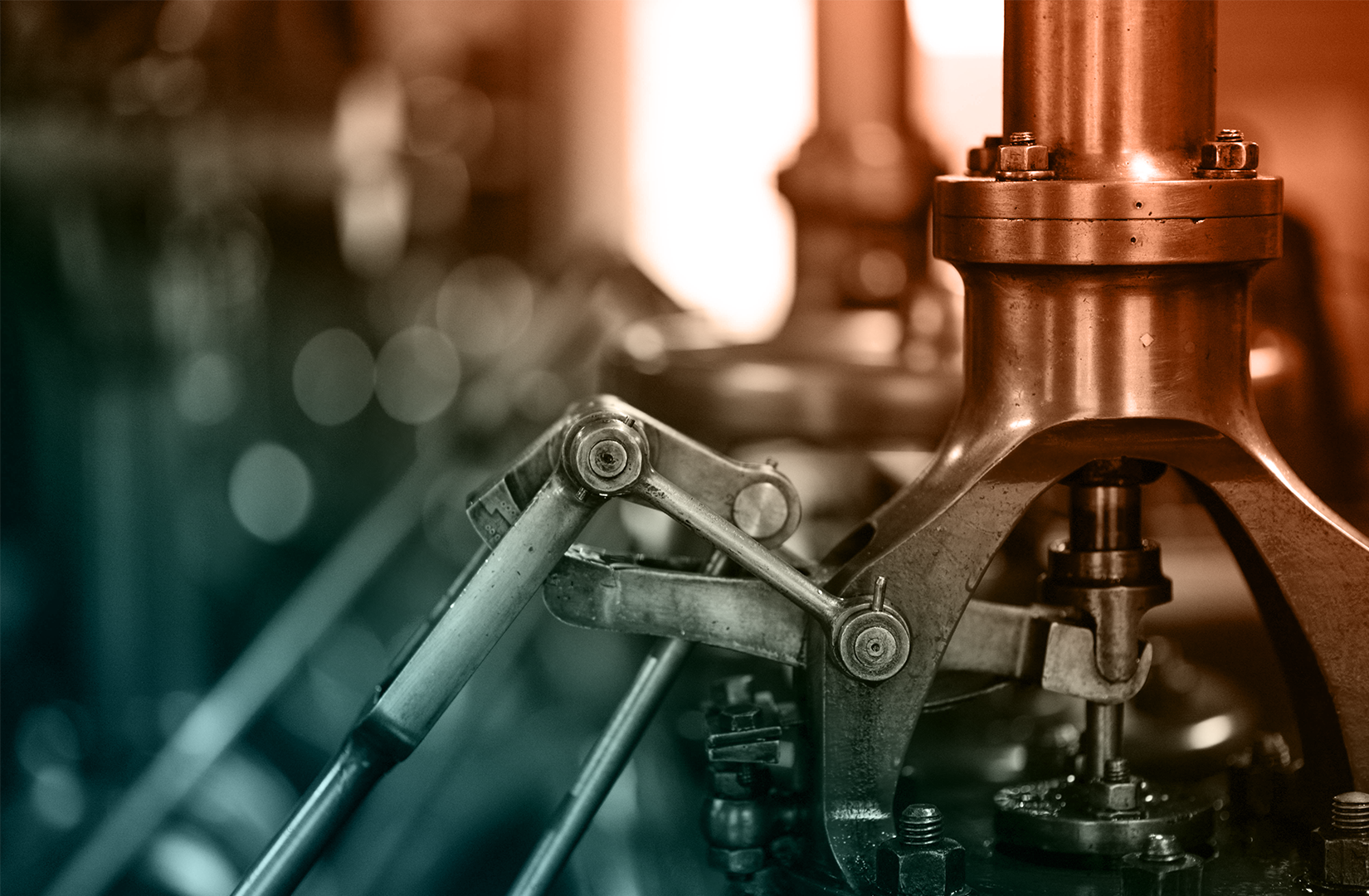
Groove Design References
Learn More
Coatings, Packaging, & Other Services
Learn More
Custom Parts & Custom O-rings
Learn More