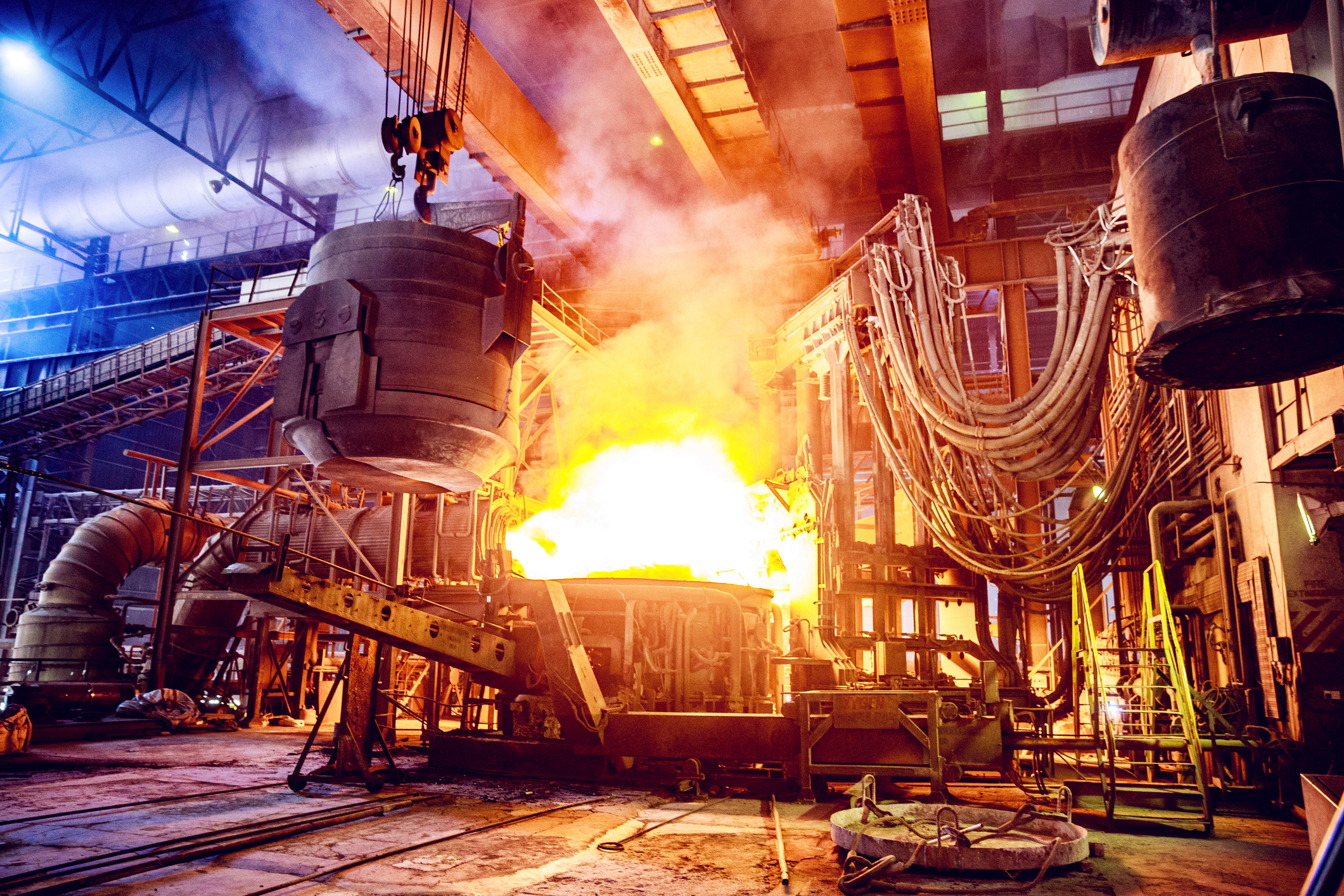
Blow Molding
Blow molding is a popular manufacturing process used to create hollow, three-dimensional objects such as bottles, containers, and automotive parts. It involves inflating a heated plastic or glass material inside a mold to form the desired shape. In this web page, we will explore the different types of blow molding, their advantages and disadvantages, and the wide array of industrial applications. Additionally, we'll provide a list of materials commonly used in blow molding manufacturing. Custom Blow Molded parts available now!
Check with one of Canyon’s helpful product engineers for an expert material and manufacturing recommendation.
Common terminology includes: Extrusion blow molding, injection blow molding, stretch blow molding, injection-stretch blow molding, accumulator blow molding, continuous blow molding, intermittent blow molding, co-extrusion blow molding, multilayer blow molding, 3D blow molding.
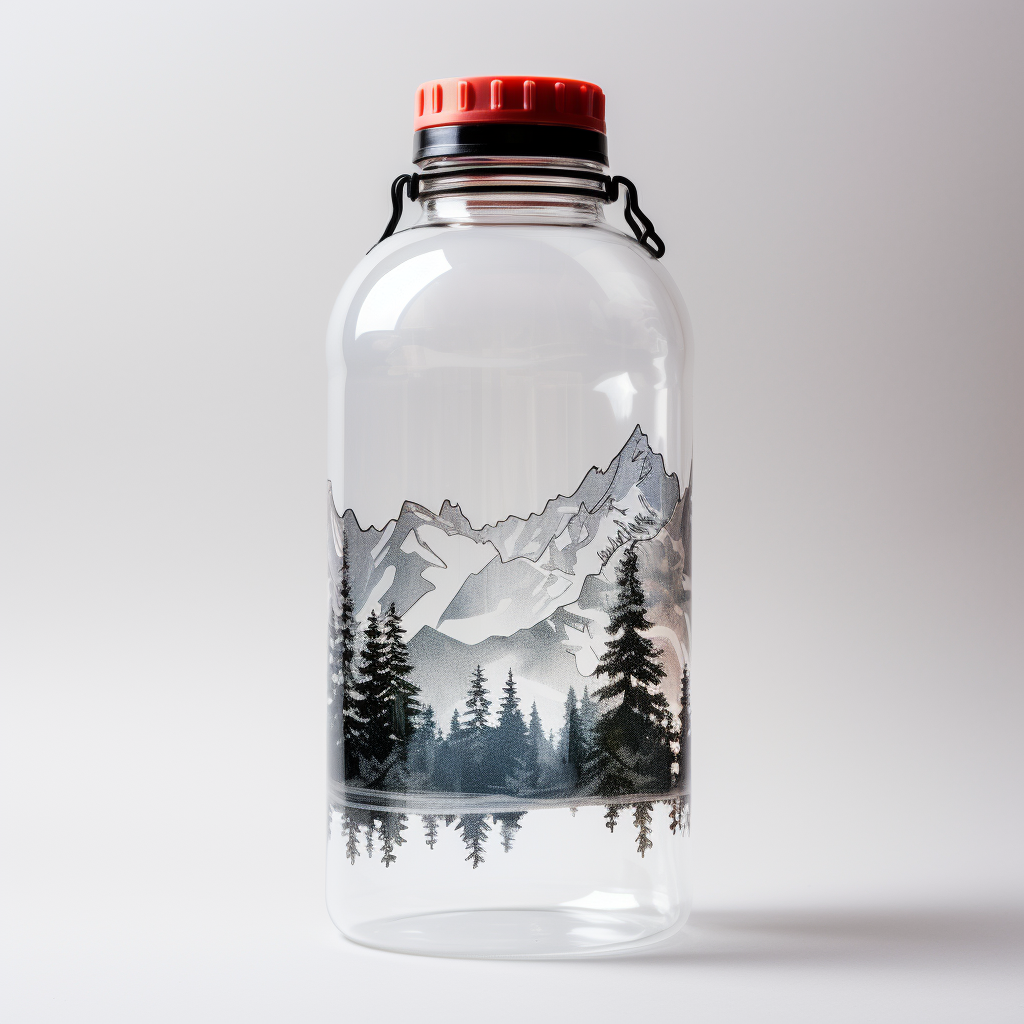
Advantages
- Cost-Effective: Suitable for high-volume production, reducing per-unit costs.
- Variety of Shapes: Versatile in producing a wide range of shapes and sizes.
- Material Efficiency: Minimizes waste, as excess material can be recycled.
- Strength and Durability: Provides strong and durable parts.
- Customization: Allows for customization through various types of blow molding.
Disadvantages
- Limited Material Compatibility: Not all materials are suitable for blow molding.
- Complex Tooling: Creating molds for intricate shapes can be expensive.
- Cycle Times: Longer cycle times compared to some other manufacturing methods.
Common Applications of Blow Molding
- Packaging: Manufacturing bottles, containers, and packaging materials.
- Automotive: Producing air ducts, fuel tanks, and interior components.
- Consumer Goods: Creating toys, sporting goods, and household items.
- Medical: Making medical vials, containers, and devices.
- Construction: Fabricating pipes, fittings, and construction components.
Please consult a Canyon Components Engineer about your specific application and we will use our decades of experience to formulate a solution that fits your need.
Types of Blow Molding
Blow Molding can be performed in a number of ways depending on the composition and intended use of the final product. Some variations available for Blow Molding include the following.
Canyon Components strives to meet all customer service requests. Feel free to contact Canyon Components engineering and let our knowledgeable staff help you design the perfect part for your needs.
Extrusion Blow Molding
This process involves extruding a hollow tube of molten plastic and blowing it into a mold. It's ideal for making hollow products like bottles. Advantages include cost-effectiveness for high-volume production and the ability to produce complex shapes. However, it can result in variable wall thickness and may have limitations in achieving tight tolerances.
Injection Blow Molding
Involves injecting plastic into a mold to form a preform, then blowing it into the final shape. This method is known for producing precise, high-quality containers. The advantage is excellent control over wall thickness. The downside is the higher cost of tooling and machinery, making it less economical for small runs.
Stretch Blow Molding
Commonly used for PET bottles, it stretches the preform both axially and radially during blowing. This enhances material strength and barrier properties. The advantage is the production of lightweight, strong bottles, but it requires specialized machines and preforms, increasing initial costs.
Injection-Stretch Blow Molding
Combines injection and stretch blow molding for high-clarity, high-strength containers. It's highly efficient for large-scale production. The advantage is superior container quality, but the process involves complex machinery and higher energy consumption.
Accumulator Blow Molding
Best for making large industrial containers, it accumulates a large amount of molten plastic before blowing. It allows for larger part production and has a faster cycle time for big parts. However, it’s not suitable for small items and can be more energy-intensive.
Continuous Blow Molding
Ideal for high-speed production of containers, this method continuously extrudes a parison. It's highly efficient and cost-effective for large runs. The main advantage is the high output rate. The disadvantage is less control over individual part quality, making it less suitable for complex or precision items.
Please consult a Canyon Components Engineer about your specific application and we will use our decades of experience to formulate a solution that fits your need.
Request a Quote for Blow Molded Parts
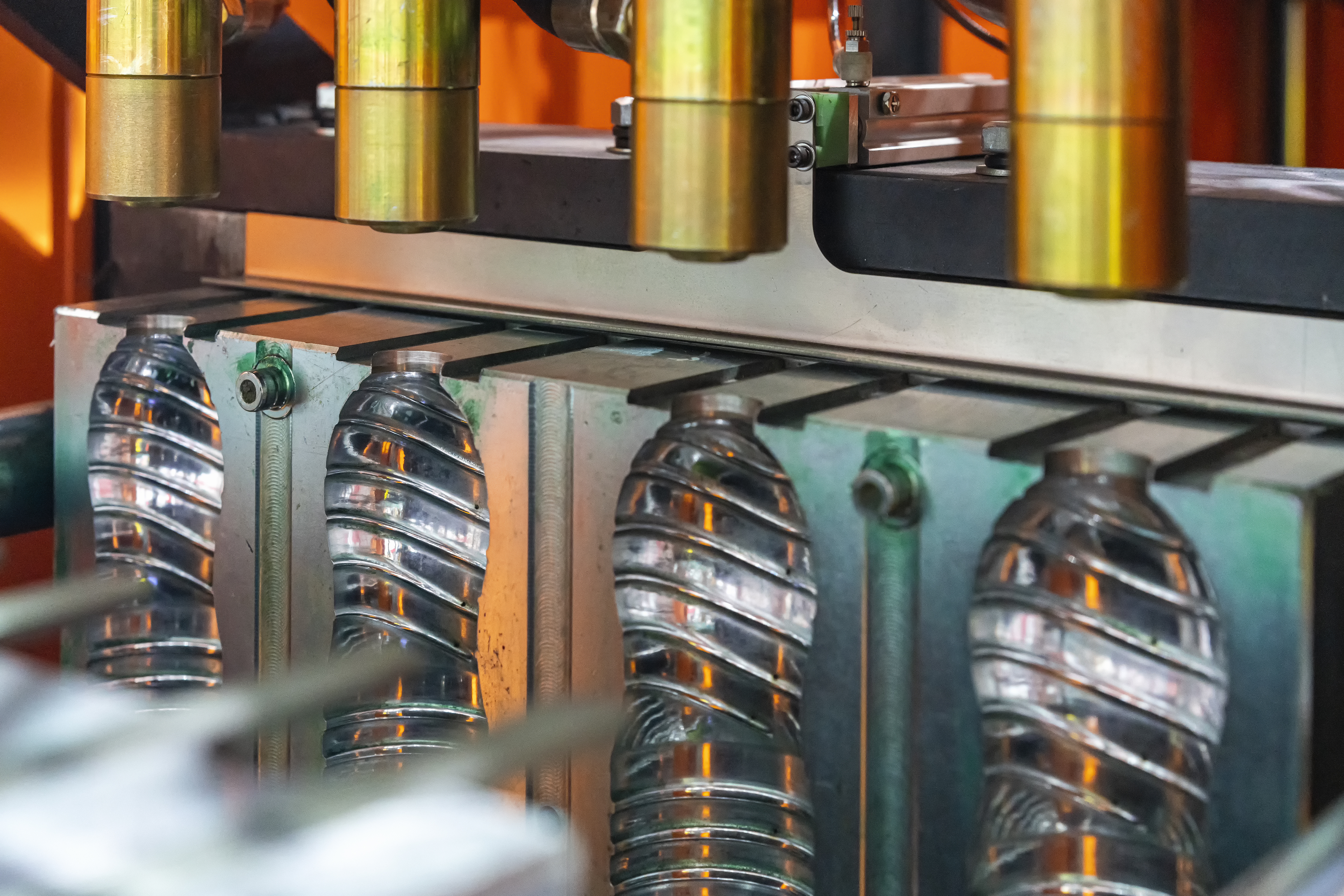
Blow Molding Materials Available
Blow Molding can be performed in a number of ways depending on the composition and intended use of the final product. Some common materials available for Blow Molding include the following.
Each of these materials has its own advantages, limitations, and cost implications. The choice of material and manufacturing technique usually depends on factors like the complexity of the design, required precision, material properties, and production volume.
Canyon Components strives to meet all customer service requests. Feel free to contact Canyon Components engineering and let our knowledgeable staff help you design the perfect part for your needs.
Plastics
Plastics are a broad class of synthetic or semi-synthetic materials known for their versatility and moldability. They are crucial in numerous applications due to their ability to be shaped, lightweight nature, and resistance to chemicals and moisture.
Specialty Compliances
Canyon have materials available for O-rings, gaskets, & custom parts with compliances ranging from USP Class VI <87> & <88> for medical applications, to FDA CFR 21.177.2600 grades A through F for different food types, to the various drinking water specifications like KTW and NSF. Whether it's metal, rubber, or plastic, Canyon can meet your needs!
PP (Polypropylene)
Polypropylene (PP) plastic, known for its exceptional chemical resistance and durability, is a lightweight thermoplastic. It's resilient against fatigue, has a high melting point, and is ideal for packaging, automotive parts, and textiles, thanks to its versatility and recyclability.
Polyethylene (PE)
Polyethylene (PE) plastic, renowned for its versatility, is a widely used thermoplastic. It's lightweight, impact-resistant, and has excellent chemical resistance. Commonly used in packaging, containers, and pipes, PE is available in varying densities for different applications, including high and low-density forms.
PC (Polycarbonate)
Polycarbonate (PC) Plastic is a tough, transparent thermoplastic with exceptional impact resistance, heat tolerance, and optical clarity. Its versatility makes it ideal for bulletproof glass, eyewear lenses, medical devices, and protective gear, offering a unique balance of strength and lightweight properties.
Nylon (Polyamide, PA)
Nylon, a synthetic thermoplastic polymer, is renowned for its high strength, elasticity, and abrasion resistance. It's versatile, easily dyeable, and used in a wide range of products from textiles and ropes to gears and automotive parts.
Polyurethane (PU, AU)
Polyurethane O-rings, gaskets, & custom molded parts generally have two or three times greater tensile strength and wear resistance than Nitrile and comparable polymers. Polyurethane also provides excellent permeation resistance when compared to most rubbers.
ABS (Acrylonitrile Butadiene Styrene)
ABS plastic, a thermoplastic polymer blend of acrylonitrile, butadiene, and styrene, is renowned for its toughness, impact resistance, and rigidity. It's easily machinable and ideal for automotive parts, consumer goods, and 3D printing due to its strength and versatility.
PVC (Polyvinyl Chloride)
Polyvinyl Chloride (PVC) plastic, a widely utilized thermoplastic, is celebrated for its durability, chemical resistance, and versatility. It's commonly used in construction for pipes and fittings, medical devices, and window frames, and can be made more flexible with the addition of plasticizers.
PET (Polyethylene Terephthalate)
Polyethylene Terephthalate (PET) is a durable, lightweight thermoplastic, renowned for its clarity, strength, and recyclability. Widely used in beverage bottles, food packaging, and textiles, PET is also food-safe, resistant to water and many chemical solvents, and easily formed into various shapes.
PETG (Polyethylene Terephthalate Glycol)
PETG plastic, a glycol-modified version of polyethylene terephthalate, is valued for its clarity, excellent chemical resistance, and thermoformability. It's a popular choice for 3D printing, packaging, and medical devices due to its durability, impact resistance, and ease of fabrication.
PPSU (Polyphenylsulfone)
Polyphenylsulfone (PPSU) Plastic is a high-performance thermoplastic known for its exceptional heat resistance, toughness, and stability under thermal stress. It's widely used in medical instruments, aerospace, and plumbing components due to its excellent chemical resistance and ability to withstand repeated sterilizations.
Back to Manufacturing Hub
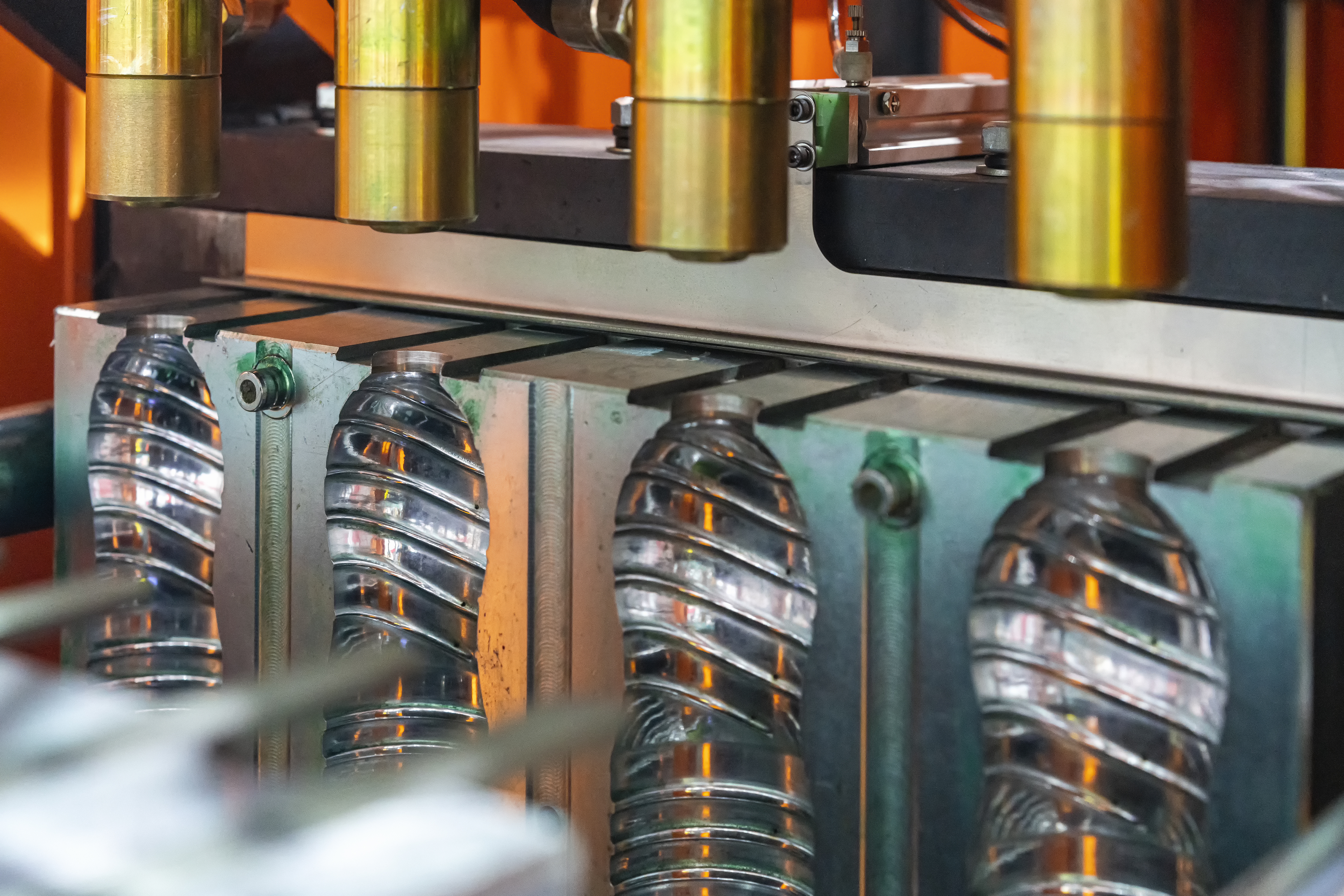
Get A Quote Now!
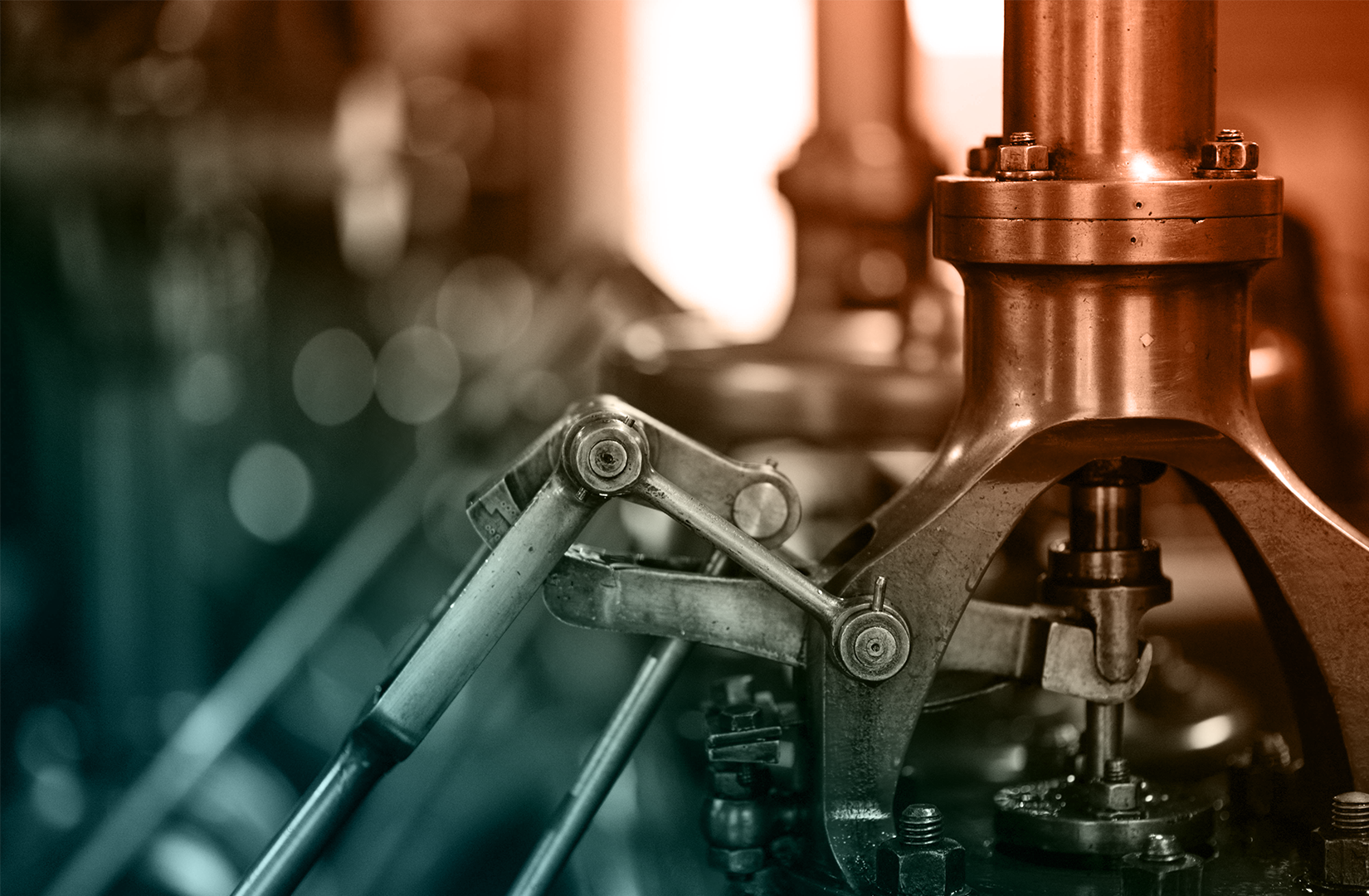
Groove Design References
Learn More
Coatings, Packaging, & Other Services
Learn More
Custom Parts & Custom O-rings
Learn More