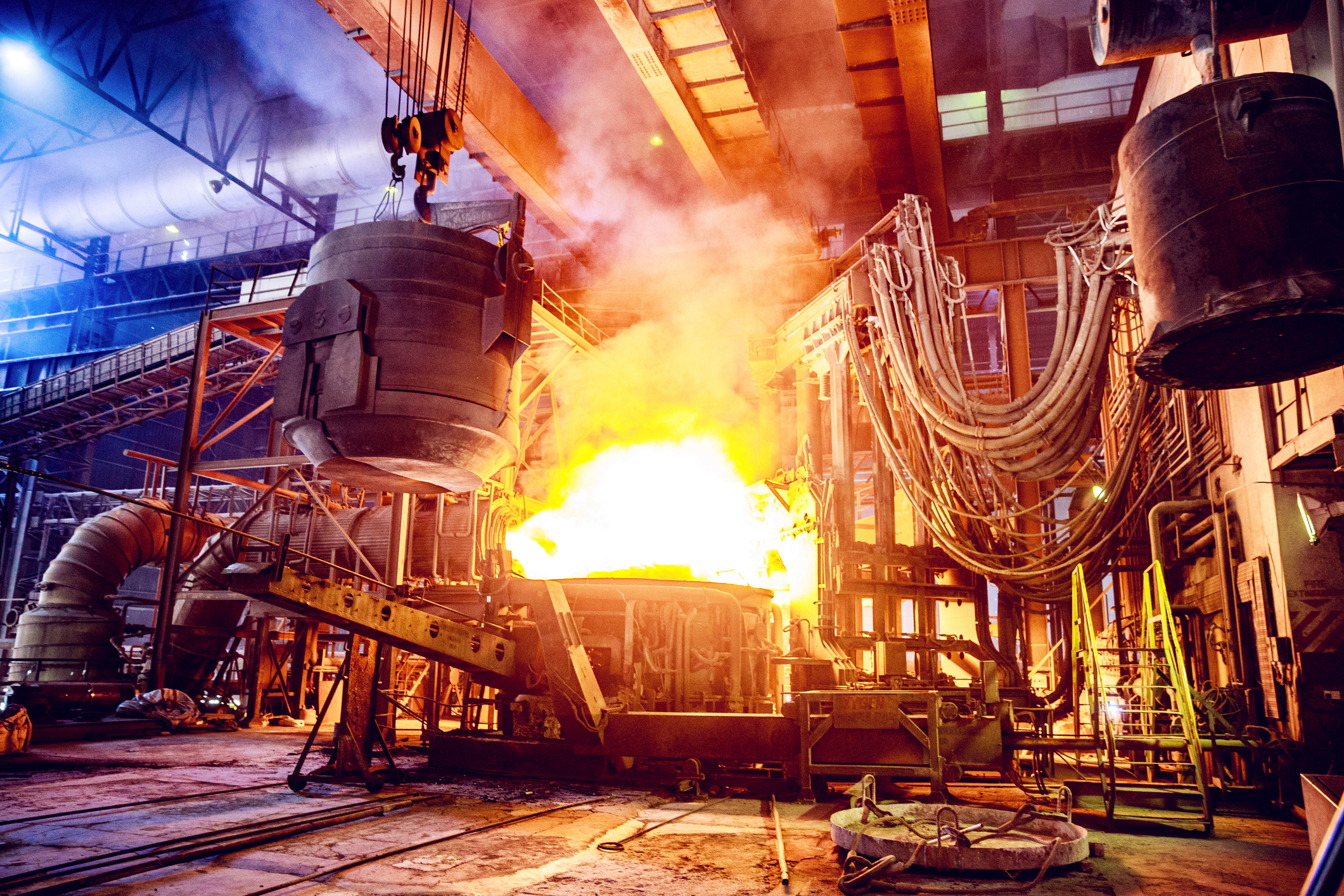
Nylon Plastic (Polyamide, PA) Selection Guide
Nylon (Polyamide, PA) is a family of synthetic polymers known for their exceptional strength, toughness, and wear resistance. In this web page, we will explore the different types of nylon, its numerous advantages and disadvantages, and the diverse industrial applications where nylon plays a crucial role.
Nylon (Polyamide, PA) rapid manufacturing, & custom molded parts are available now!
Check with one of Canyon’s helpful product engineers for an expert material and manufacturing recommendation.
Common names include: Nylon (Polyamide, PA), Trade Names: NYCAST®, NYLOIL, SUSTAMID®, TECAMID®, Nylon 6/6 DuPont Zytel®, Nylon 6 - BASF Ultramid®, Nylon 6/6 - Ascend Vydyne®, Ensilon®, Ertalon™, Hydlar® ZF, Nylon 6/12 - EMS Grivory®, Nylon 6 - Lanxess Durethan®, Nylon 6/6 - RadiciGroup Radilon®, NYMETAL®.
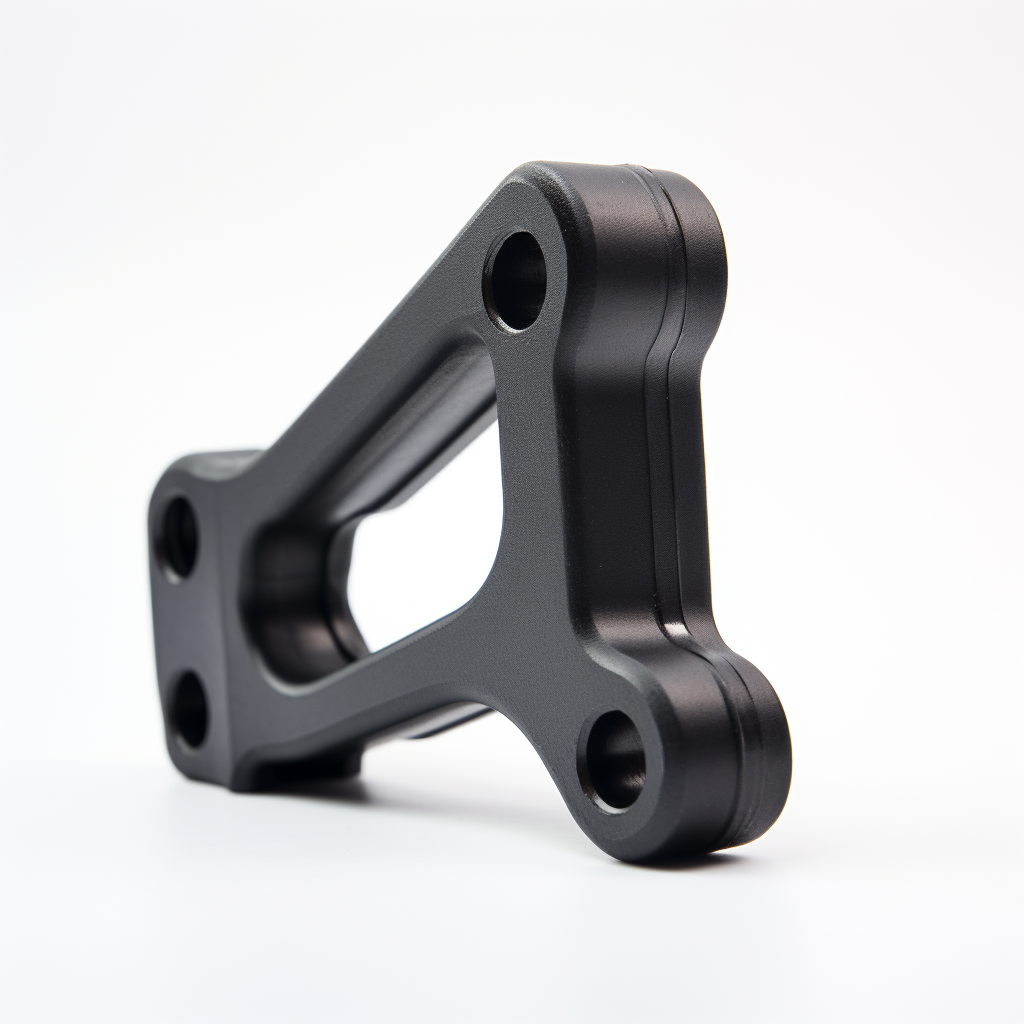
Advantages
- High Strength: Nylon is known for its exceptional tensile strength, making it suitable for load-bearing applications.
- Toughness: Nylon is highly resistant to impact and offers excellent toughness, even at low temperatures.
- Wear Resistance: Nylon exhibits excellent wear resistance, making it suitable for components subjected to friction and abrasion.
- Chemical Resistance: Nylon is resistant to many chemicals, oils, and solvents, ensuring its stability in various industrial environments.
- Low Friction: Nylon has a low coefficient of friction, reducing wear and enhancing its performance in sliding applications.
- Electrical Insulation: Nylon is an excellent electrical insulator, making it suitable for electrical and electronic applications.
- Self-Lubricating: Some nylon formulations contain internal lubricants, reducing the need for external lubrication in certain applications.
Disadvantages
- Moisture Absorption: Nylon absorbs moisture from the environment, which can affect its mechanical properties. This property should be considered in certain applications.
- High Processing Temperature: The high melting point of nylon may require specialized equipment for processing.
- UV Sensitivity: Nylon is sensitive to ultraviolet (UV) radiation and may degrade when exposed to prolonged sunlight. UV stabilizers can be added to mitigate this issue.
Common Applications of Nylon
- Medical Devices: Nylon is used in medical devices such as surgical sutures, catheters, and orthopedic implants due to its biocompatibility.
- Aerospace: Nylon can be used in aerospace applications for interior components, fasteners, and mechanical parts due to its lightweight and mechanical properties.
- Automotive: Nylon is used in automotive components such as gears, bushings, engine parts, and fuel lines due to its strength, wear resistance, and heat resistance.
- Textiles: Nylon is a key material in the textile industry, used to create fabrics for clothing, upholstery, and industrial applications.
- Electrical and Electronics: Nylon is used for electrical connectors, cable insulation, and circuit board hardware due to its electrical insulating properties.
- Machinery and Bearings: Nylon is used for manufacturing bearing and wear components, as well as gears and rollers in industrial machinery.
- Oil and Gas: Nylon is employed in oil and gas applications for tubing, seals, and connectors due to its resistance to oil and chemicals.
- Consumer Goods: Nylon is used in various consumer products, including sports equipment, kitchen appliances, and luggage due to its strength and durability.
Please consult a Canyon Components Engineer about your specific application and we will use our decades of experience to formulate a solution that fits your need.
Types of Nylon
Nylon can come in different variations, depending on its composition and intended use. Some common types of Nylon include the following.
Canyon Components strives to meet all customer service requests. Feel free to contact Canyon Components engineering and let our knowledgeable staff help you design the perfect part for your needs.
Nylon 6
This type is known for its strong mechanical properties and high impact resistance. It's widely used in automotive parts, industrial components, and consumer goods. Nylon 6 also has excellent wear resistance, making it ideal for gears and bearings. It absorbs moisture, which can affect its dimensions and mechanical properties.
Nylon 66
Renowned for its higher melting point and superior mechanical strength compared to Nylon 6, Nylon 66 is often used in high-performance applications such as automotive under-hood parts and electrical connectors. It also exhibits good resistance to wear and abrasion, making it suitable for heavy-duty mechanical parts.
Nylon 11
This bio-based nylon is known for its flexibility and impact resistance, even at low temperatures. Nylon 11 is used in applications requiring high-quality surface finishes, such as sports equipment and automotive interiors. Its low moisture absorption rate enhances stability and resistance to environmental conditions.
Nylon 12
Offering the lowest moisture absorption among nylons, Nylon 12 is ideal for applications requiring dimensional stability and resistance to chemicals. Its applications include medical devices, fuel lines, and pneumatic air brake tubing. It's also used in high-performance coatings due to its smooth finish and durability.
Nylon 6/10
Combining the properties of Nylon 6 and 10, this copolymer offers reduced moisture absorption and improved dimensional stability. It's typically used in tubing, electrical insulators, and automotive oil containers. Nylon 6/10 maintains good mechanical properties and chemical resistance.
Nylon 4/6
Known for its high heat deflection temperature, Nylon 4/6 is used in applications that require resistance to high temperatures and thermal aging, such as under-the-hood automotive components. It also has a higher melting point and maintains strength and stiffness over a wide temperature range.
Please consult a Canyon Components Engineer about your specific application and we will use our decades of experience to formulate a solution that fits your need.
Manufacturing Options for Nylon
Nylon parts can be manufactured using several methods, each suitable for different applications and part complexities.
Each of these methods has its own advantages, limitations, and cost implications. The choice of manufacturing technique usually depends on factors like the complexity of the design, required precision, material properties, and production volume.
Canyon Components strives to meet all customer service requests. Feel free to contact Canyon Components engineering and let our knowledgeable staff help you design the perfect part for your needs.
Back to Plastics Hub
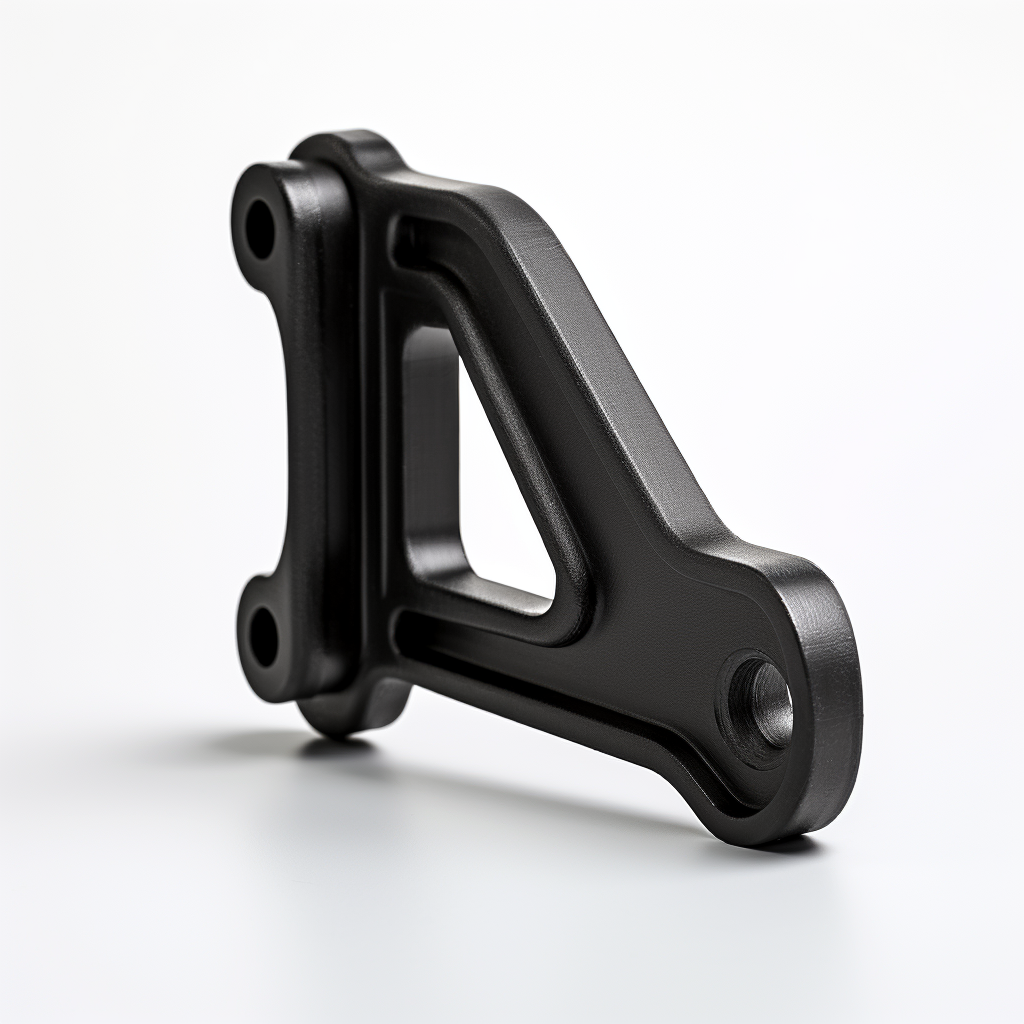
Get A Quote Now!
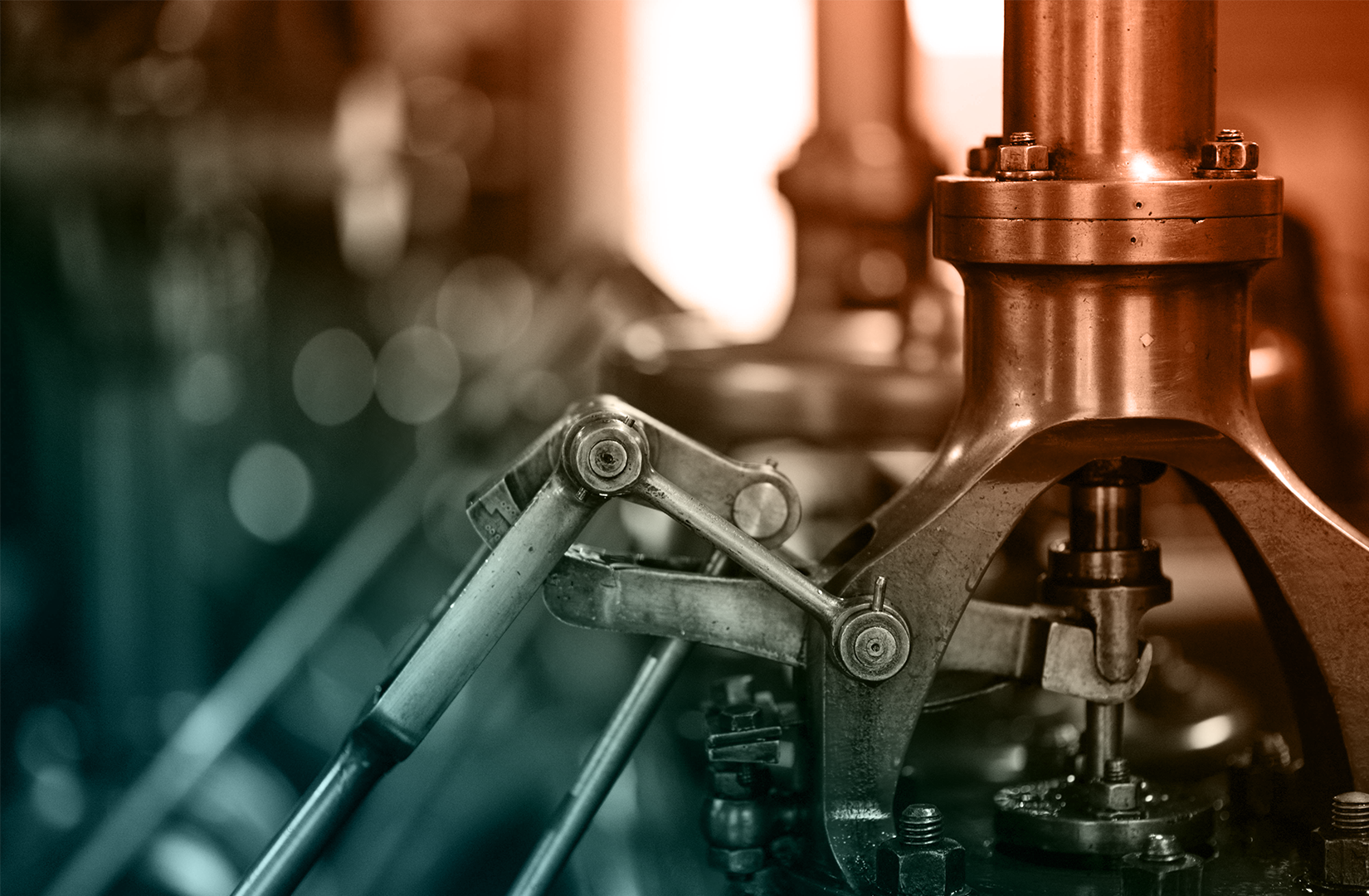
Groove Design References
Learn More
Coatings, Packaging, & Other Services
Learn More
Custom Parts & Custom O-rings
Learn More