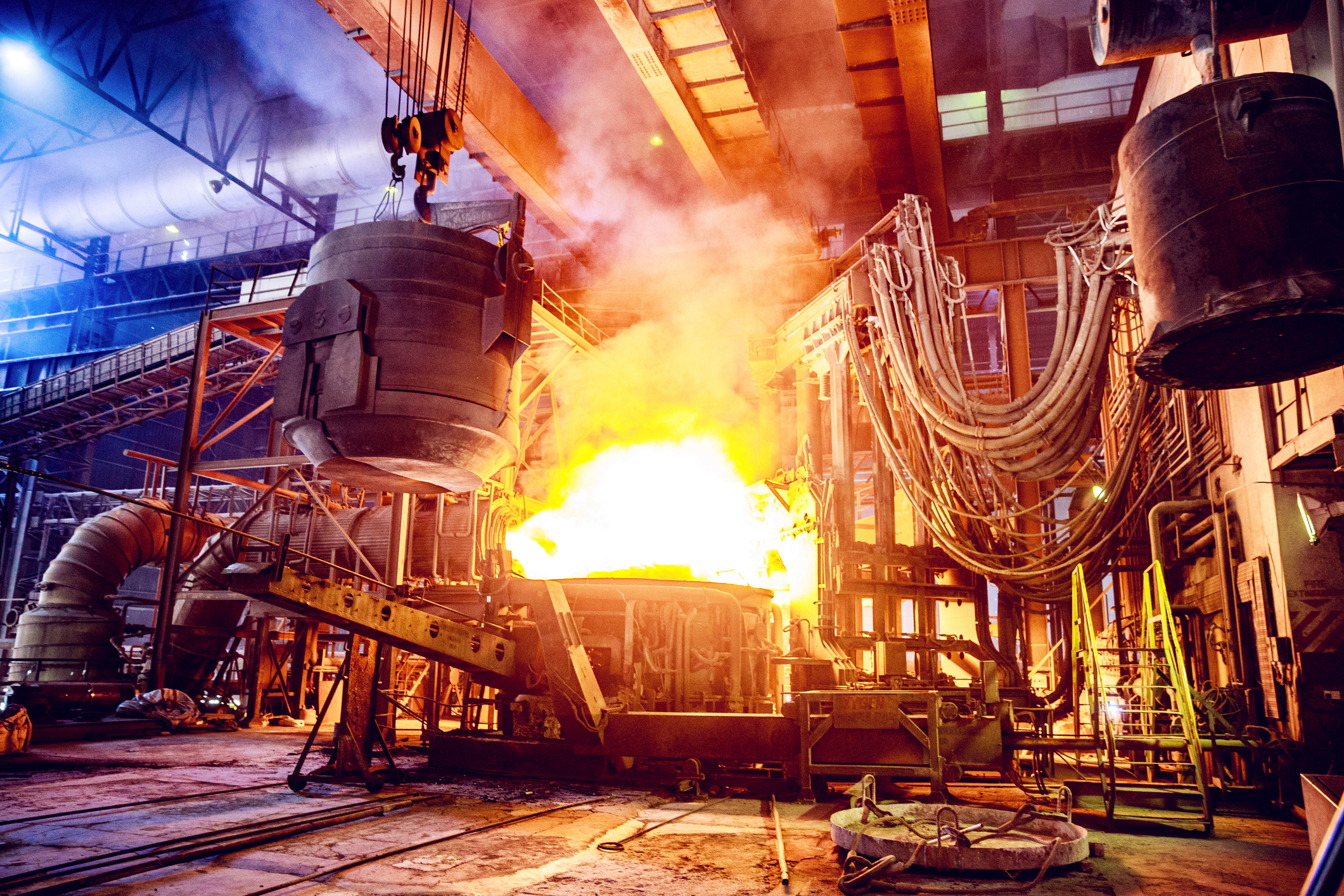
PVC Plastic (Polyvinyl Chloride) Selection Guide
PVC (Polyvinyl Chloride) is a versatile and widely used thermoplastic polymer known for its durability, chemical resistance, and ease of processing. In this web page, we will explore the different types of PVC, its numerous advantages and disadvantages, and the diverse industrial applications where PVC plays a significant role.
PVC (Polyvinyl Chloride) rapid manufacturing, & custom molded parts are available now!
Check with one of Canyon’s helpful product engineers for an expert material and manufacturing recommendation.
Common names include: PVC (Polyvinyl Chloride), Trade Names:
Vinnolit®, Koroseal®, Apex®, OxyVinyls®, Geon™, Solvin®, Benvic®, Corzan® CPVC, Flametec®, Seaboard® PVC, Versadur®, Teknor, Formolon®, Vintec®, Vintec® I, Vintec® II.
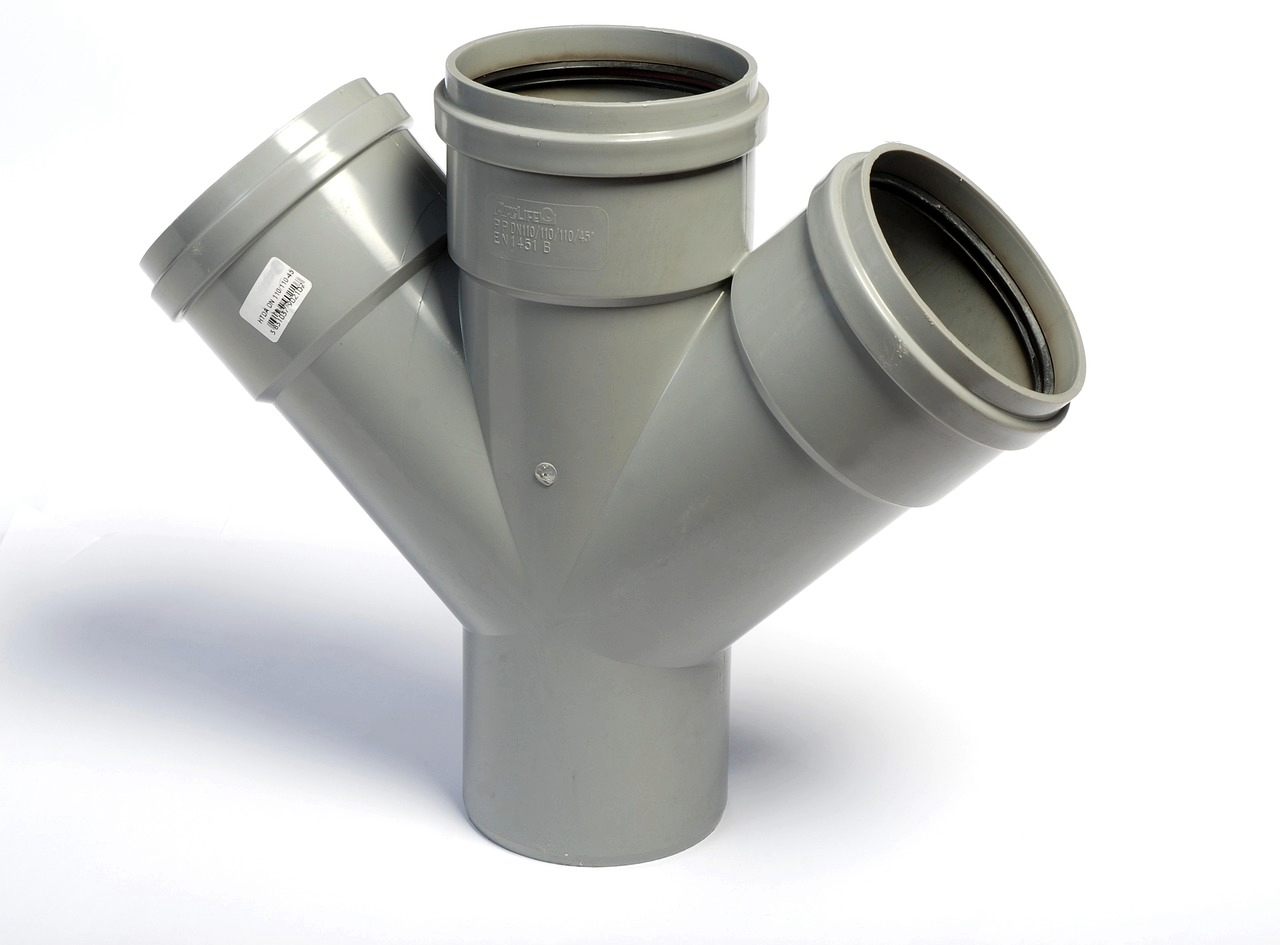
Advantages
- Chemical Resistance: PVC is highly resistant to many chemicals, acids, and bases, making it suitable for use in corrosive environments.
- Durability: PVC is durable and long-lasting, which is essential for applications requiring a prolonged lifespan.
- Low Maintenance: PVC products generally require minimal maintenance and are easy to clean.
- Cost-Effective: PVC is cost-effective compared to many other engineering plastics, making it a budget-friendly choice.
- Versatility: PVC can be formulated to be rigid or flexible, making it suitable for a wide range of applications.
- Recyclability: PVC is recyclable, and many PVC products can be repurposed into new materials.
Disadvantages
- Environmental Concerns: The production and disposal of PVC can have environmental impacts, including the release of chlorine gas when burned. Efforts have been made to mitigate these issues through recycling and safer disposal methods.
- Flammability: PVC is inherently flammable and can emit toxic gases when burned. Flame-retardant additives are often used to improve its fire resistance.
- Softening at High Temperatures: Rigid PVC can soften at elevated temperatures, limiting its use in high-temperature applications.
- Not Biodegradable: PVC is not biodegradable, and its disposal in landfills can contribute to plastic waste.
Common Applications of PVC
- Automotive: PVC is used in automotive applications for interior components, wire harnesses, and gaskets due to its durability and chemical resistance.
- Medical: Flexible PVC is used in medical devices such as IV bags, tubing, and catheters due to its biocompatibility and chemical resistance.
- Construction: PVC is extensively used in construction for pipes, profiles, window frames, roofing membranes, and flooring materials due to its durability and chemical resistance.
- Electrical and Electronics: PVC is used for electrical cable insulation, wire harnesses, and connectors due to its electrical insulating properties.
- Water Management: PVC pipes are widely used for water supply and drainage systems in both residential and industrial settings due to their corrosion resistance and long lifespan.
- Packaging: PVC is used for blister packaging, shrink wrap, and clamshell packaging for consumer goods and pharmaceutical products.
- Agriculture: PVC pipes and fittings are used in agricultural irrigation systems due to their resistance to chemical fertilizers and pesticides.
- Signage and Display: Foamed PVC is used for signage, display boards, and advertising materials due to its lightweight nature and versatility.
Please consult a Canyon Components Engineer about your specific application and we will use our decades of experience to formulate a solution that fits your need.
Types of PVC
PVC can come in different variations, depending on its composition and intended use. Some common types of PVC include the following.
Canyon Components strives to meet all customer service requests. Feel free to contact Canyon Components engineering and let our knowledgeable staff help you design the perfect part for your needs.
Rigid PVC (uPVC)
Unplasticized PVC, known for its strength and rigidity, is widely used in construction for pipes, window frames, and doors. It is durable, low maintenance, and resistant to chemicals and UV light, making it ideal for long-lasting applications.
Flexible PVC
By adding plasticizers, PVC becomes flexible and is used in applications like electrical cable insulation, inflatable products, and medical tubing. This type offers versatility while maintaining PVC’s inherent properties like chemical resistance and durability.
Chlorinated PVC (CPVC)
CPVC undergoes a chlorination process, enhancing its resistance to heat, chemicals, and corrosion. It's particularly suitable for hot water pipes, industrial liquid handling, and fire sprinkler systems due to its higher temperature tolerance compared to standard PVC.
Molecularly Oriented PVC (PVC-O)
This type is processed under controlled conditions to align the polymer chains, significantly enhancing its strength and impact resistance. PVC-O is primarily used in pressure pipes and fittings, offering higher durability and efficiency in water and wastewater infrastructure.
High Impact PVC (PVC-Hi)
Specifically formulated to have increased impact resistance, this variant is ideal for products that require toughness, such as outdoor applications, window profiles, and signage. It retains the general characteristics of PVC while being more resilient to physical stress.
PVC Blends
PVC is often blended with other polymers or additives to create materials tailored for specific applications, such as automotive interiors, consumer goods, and footwear. These blends offer a combination of properties like increased flexibility, UV stability, or lower density, expanding PVC’s range of applications.
Please consult a Canyon Components Engineer about your specific application and we will use our decades of experience to formulate a solution that fits your need.
Manufacturing Options for PVC
PVC parts can be manufactured using several methods, each suitable for different applications and part complexities.
Each of these methods has its own advantages, limitations, and cost implications. The choice of manufacturing technique usually depends on factors like the complexity of the design, required precision, material properties, and production volume.
Canyon Components strives to meet all customer service requests. Feel free to contact Canyon Components engineering and let our knowledgeable staff help you design the perfect part for your needs.
Back to Plastics Hub
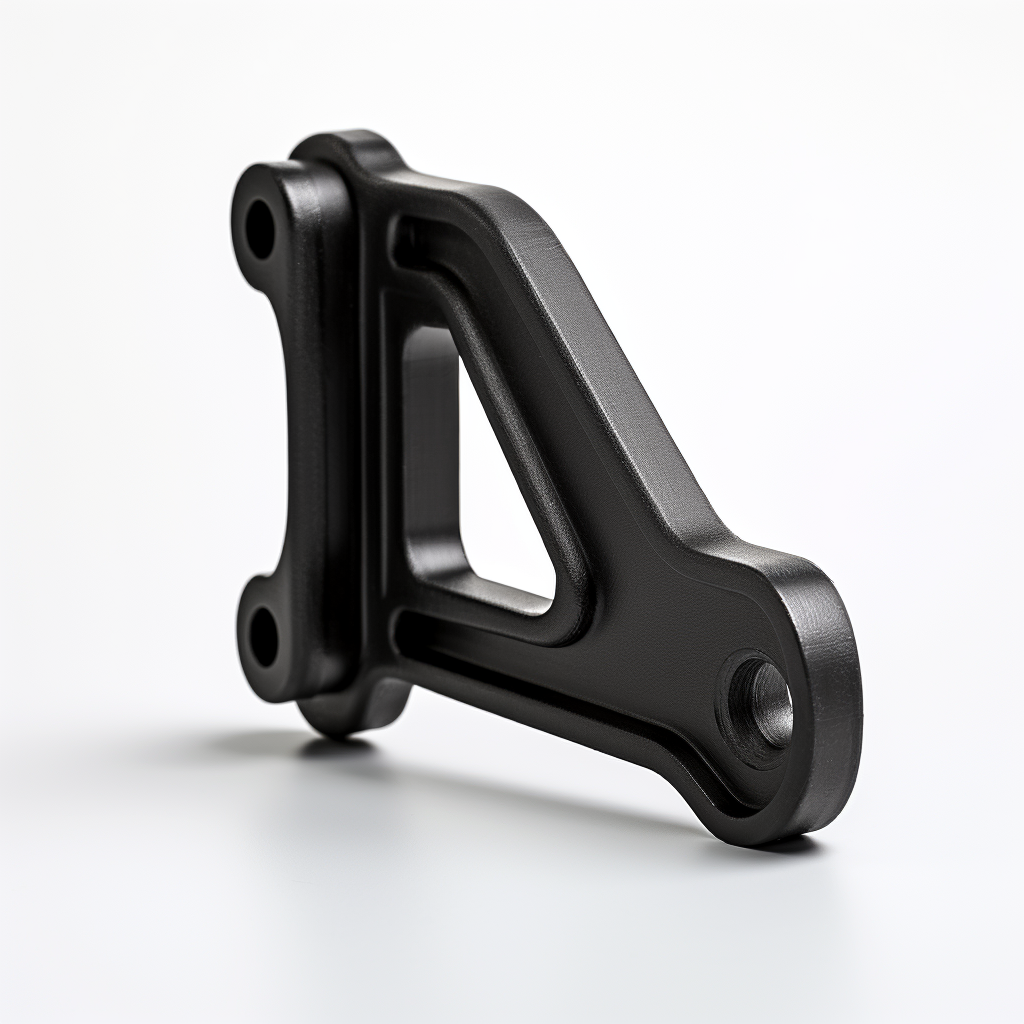
Get A Quote Now!
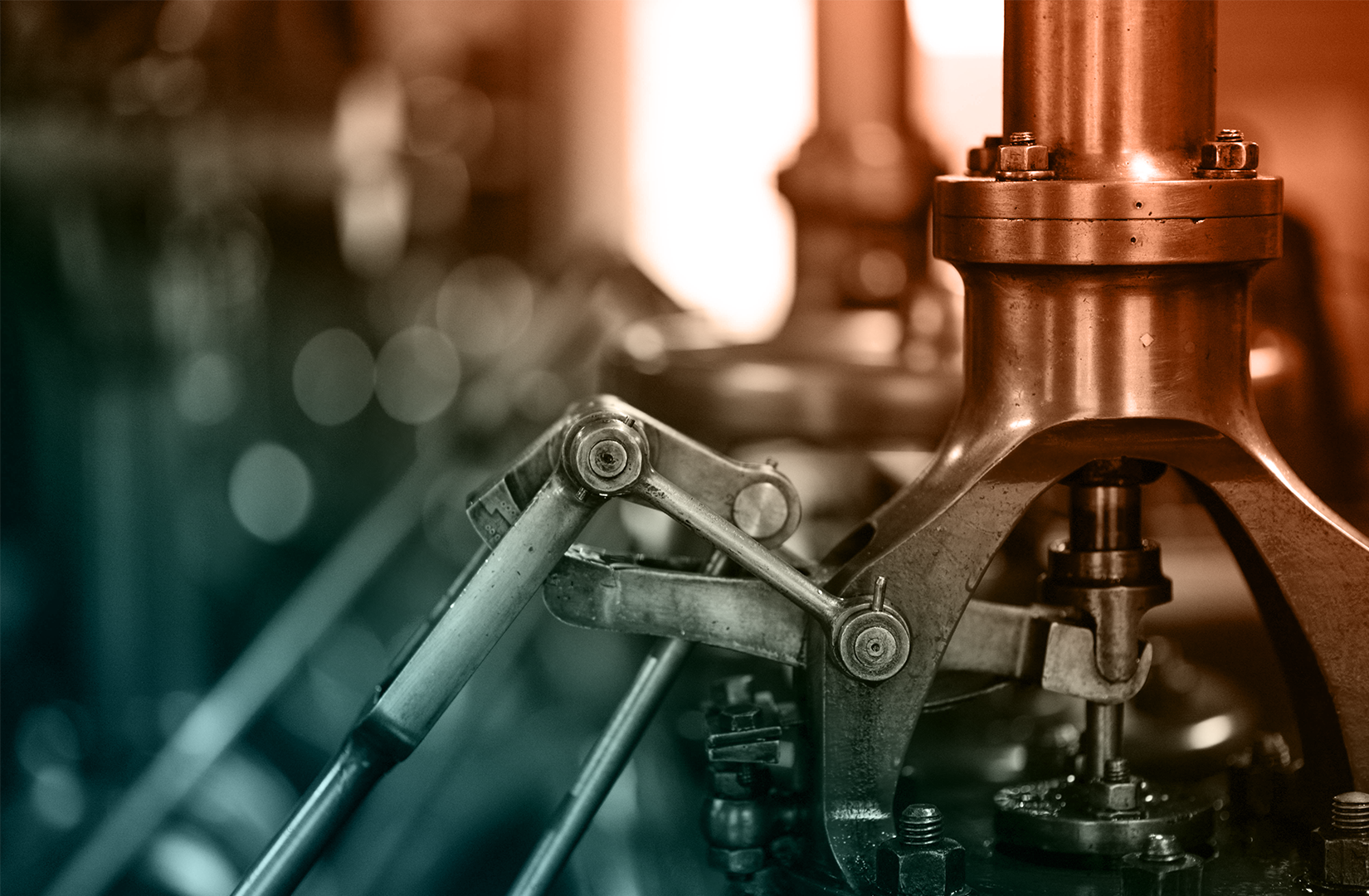
Groove Design References
Learn More
Coatings, Packaging, & Other Services
Learn More
Custom Parts & Custom O-rings
Learn More