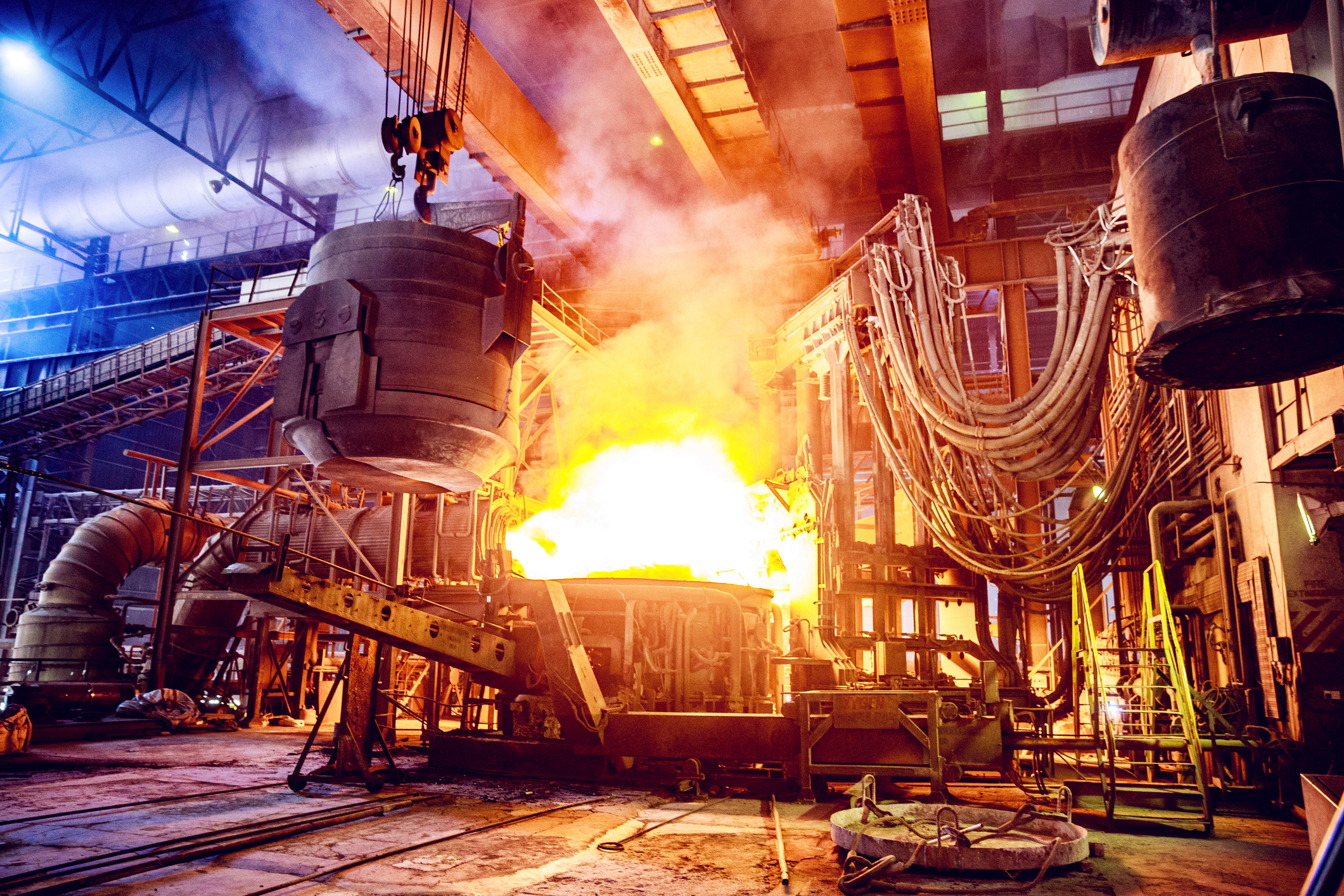
PET Plastic (Polyethylene Terephthalate) Selection Guide
PET (Polyethylene Terephthalate) is a widely used thermoplastic polymer known for its versatility, transparency, and recyclability. In this web page, we will explore the different types of PET, its numerous advantages and disadvantages, and the diverse industrial applications where PET plays a crucial role.
PET (Polyethylene Terephthalate) rapid manufacturing, & custom molded parts are available now!
Check with one of Canyon’s helpful product engineers for an expert material and manufacturing recommendation.
Common names include: PET (Polyethylene Terephthalate), Trade Names: Rynite®, Arnite®, Impet®, Hostaphan®, Valox®, Laser+®, Ensitep®, Ertaltyte®.
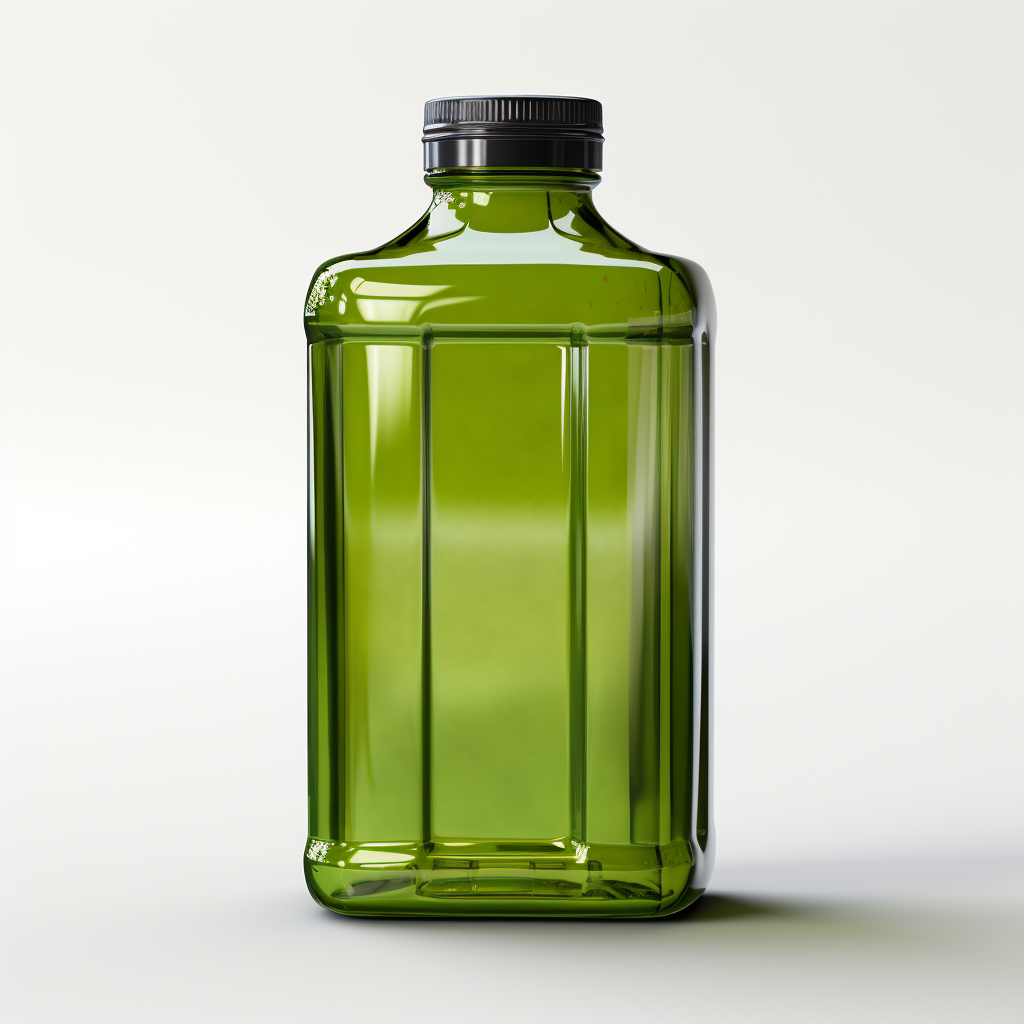
Advantages
- Clarity: PET offers exceptional optical clarity, making it ideal for packaging applications where product visibility is essential.
- Recyclability: PET is highly recyclable, and rPET is widely used to create sustainable packaging and textiles.
- Lightweight: PET is lightweight, which is particularly advantageous in packaging for reduced shipping costs and improved fuel efficiency.
- Chemical Resistance: PET is resistant to many chemicals, ensuring its stability in various environments.
- Durability: PET containers are shatter-resistant, reducing the risk of breakage during transportation and handling.
- Barrier Properties: PET can be coated or laminated to provide enhanced barrier properties, making it suitable for food and beverage packaging.
Disadvantages
- Not Suitable for High-Temperature Applications: PET has a lower heat resistance compared to some other engineering plastics. It may soften or deform at elevated temperatures.
- Limited UV Resistance: PET is sensitive to UV radiation and may degrade when exposed to prolonged sunlight. UV stabilizers can be added to mitigate this issue.
- Environmental Concerns: Although PET is recyclable, it can persist in the environment for a long time if not properly managed, contributing to plastic waste.
Common Applications of PET
- Medical Devices: PET is used in medical device packaging and components due to its biocompatibility and resistance to chemicals used in healthcare settings.
- Electronics: PET is used for manufacturing electronic components and device enclosures due to its electrical insulating properties.
- Automotive: PET is employed in automotive interiors, including headliners, seat upholstery, and door panels, thanks to its durability and versatility.
- Beverage Packaging: PET is widely used for bottling beverages, including water, soft drinks, and juices, due to its clarity, lightweight nature, and recyclability.
- Food Packaging: PET is used for various food packaging applications, such as containers for salads, fruits, and deli items, as well as blister packs and clamshell packaging.
- Textiles: rPET is used to create sustainable textiles for clothing, carpets, and accessories.
- Cosmetics and Personal Care: PET is commonly used for packaging cosmetics, lotions, and personal care products due to its clarity and durability.
- Construction: PET sheets are used in construction for glazing and interior applications due to their transparency and lightweight properties.
Please consult a Canyon Components Engineer about your specific application and we will use our decades of experience to formulate a solution that fits your need.
Types of PET
PET can come in different variations, depending on its composition and intended use. Some common types of PET include the following.
Canyon Components strives to meet all customer service requests. Feel free to contact Canyon Components engineering and let our knowledgeable staff help you design the perfect part for your needs.
PET-A (Amorphous PET)
PET-A is known for its clarity and versatility. Widely used in packaging, including bottles and food containers, it offers excellent barrier properties against moisture and gases. Its clarity makes it ideal for packaging where product visibility is key. PET-A is also recyclable, making it a popular choice for environmentally conscious applications.
PET-G (Glycol-Modified PET)
PET-G is favored for its ease of thermoforming and high impact resistance. It's commonly used in medical device packaging, 3D printing, and signage. Unlike standard PET, PET-G doesn’t crystallize when heated, making it highly workable and suitable for complex shapes and clear products.
PET-C (Crystalline PET)
Known for its strength and stiffness, PET-C is often used in engineering applications. It's suitable for high-strength mechanical parts, such as gears and bearings. PET-C offers excellent wear resistance and dimensional stability, even under mechanical stress and high temperature.
RPET (Recycled PET)
RPET is made by recycling PET products. It's used in textile fibers for clothing, containers, and packaging materials. RPET helps reduce waste and conserve resources, making it a sustainable choice. Although slightly less clear than virgin PET, it retains most of the key properties like strength and flexibility.
PET-E (Extruded PET)
PET-E is designed for extrusion processes and is often used in sheet and film applications. It offers excellent chemical resistance and barrier properties, making it suitable for protective coverings, food packaging, and industrial applications. PET-E maintains clarity and strength, similar to standard PET.
APET (Amorphous Polyethylene Terephthalate)
Similar to PET-A, APET is known for its high clarity and is commonly used in blister packaging and food containers. It is easily thermoformed and can be sealed with various materials. APET is resistant to impact, chemicals, and water, making it a versatile packaging material.
Please consult a Canyon Components Engineer about your specific application and we will use our decades of experience to formulate a solution that fits your need.
Manufacturing Options for PET
PET parts can be manufactured using several methods, each suitable for different applications and part complexities.
Each of these methods has its own advantages, limitations, and cost implications. The choice of manufacturing technique usually depends on factors like the complexity of the design, required precision, material properties, and production volume.
Canyon Components strives to meet all customer service requests. Feel free to contact Canyon Components engineering and let our knowledgeable staff help you design the perfect part for your needs.
Back to Plastics Hub
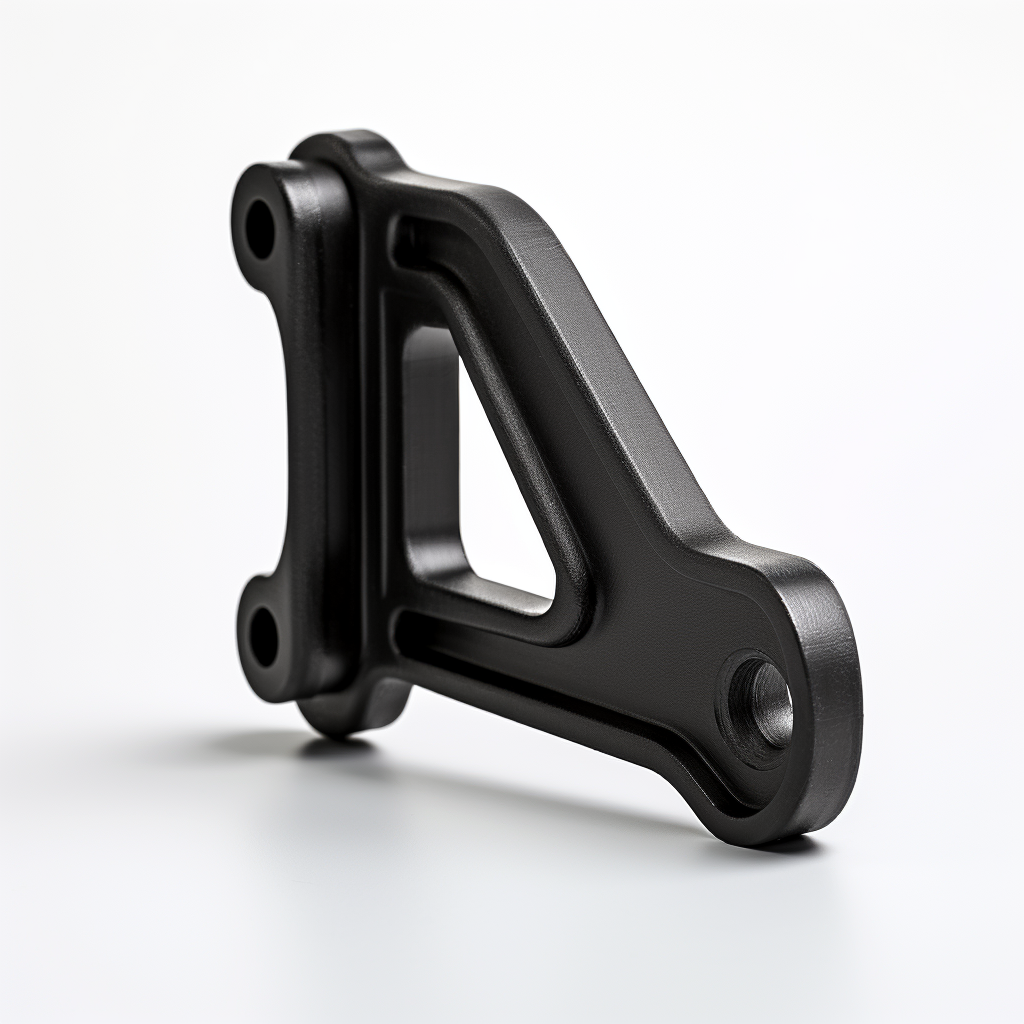
Get A Quote Now!
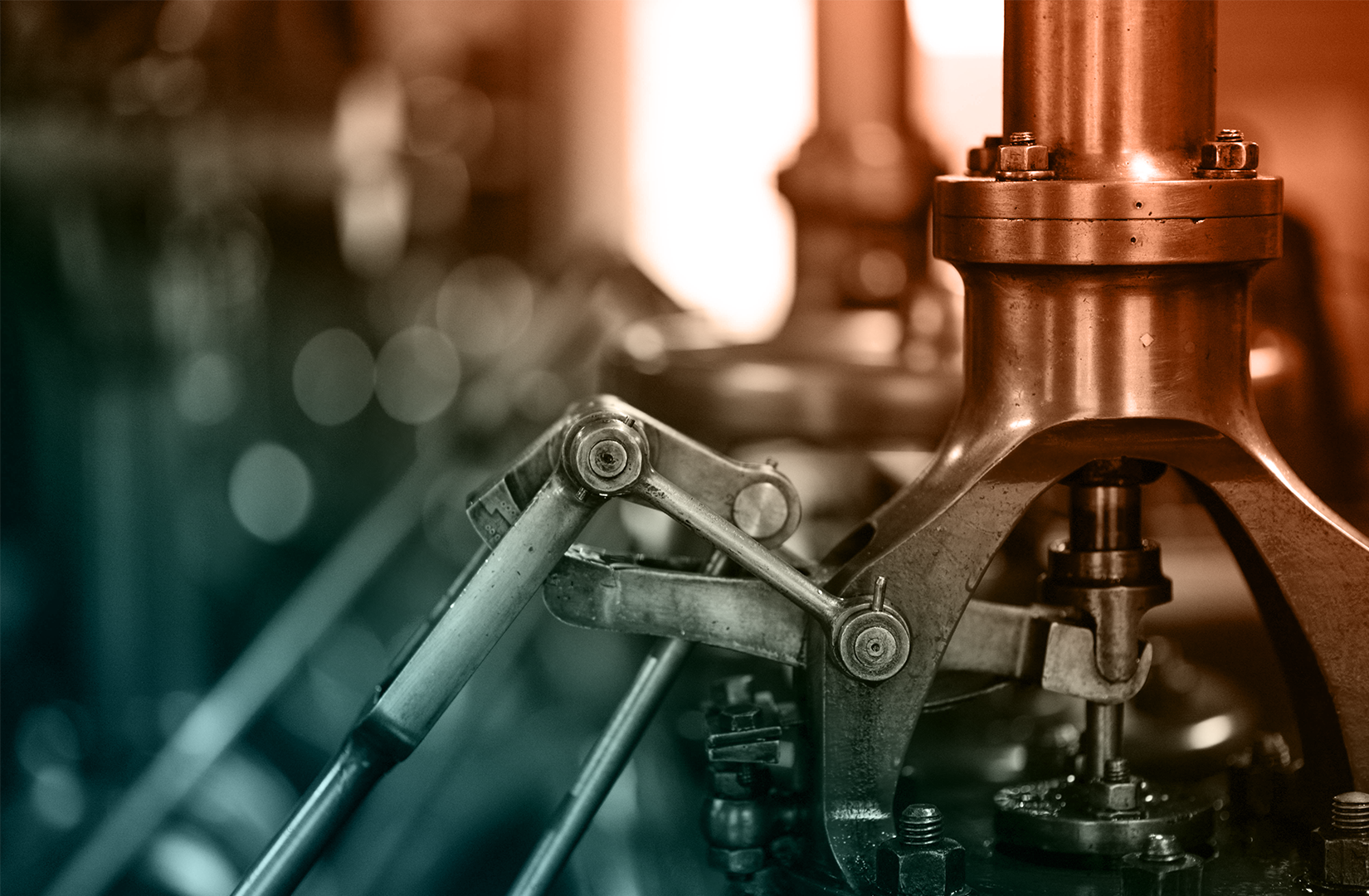
Groove Design References
Learn More
Coatings, Packaging, & Other Services
Learn More
Custom Parts & Custom O-rings
Learn More