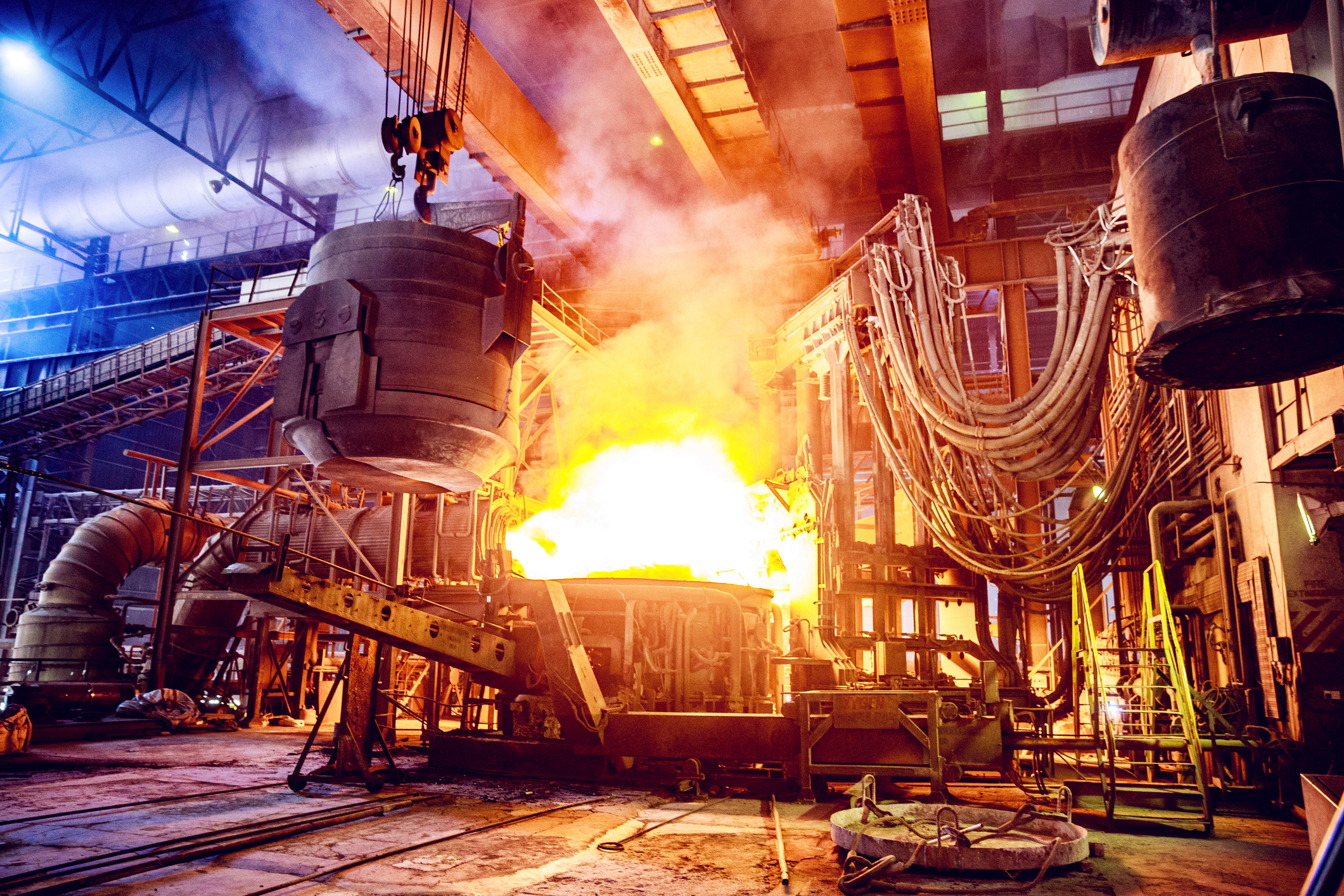
PETG Plastic (Polyethylene Terephthalate Glycol) Selection Guide
PETG (Polyethylene Terephthalate Glycol) is a popular and versatile thermoplastic polymer known for its clarity, durability, and ease of use. In this web page, we will delve into the different types of PETG, its numerous advantages and disadvantages, and the wide range of industrial applications where PETG plays a vital role.
PETG (Polyethylene Terephthalate Glycol) rapid manufacturing, & custom molded parts are available now!
Check with one of Canyon’s helpful product engineers for an expert material and manufacturing recommendation.
Common names include: PETG Plastic (Polyethylene Terephthalate Glycol), Trade Names: Vivak®, Spectar®, Ultradur®, Ultros®, Petgyl®, Lupoy®, Durapet®.
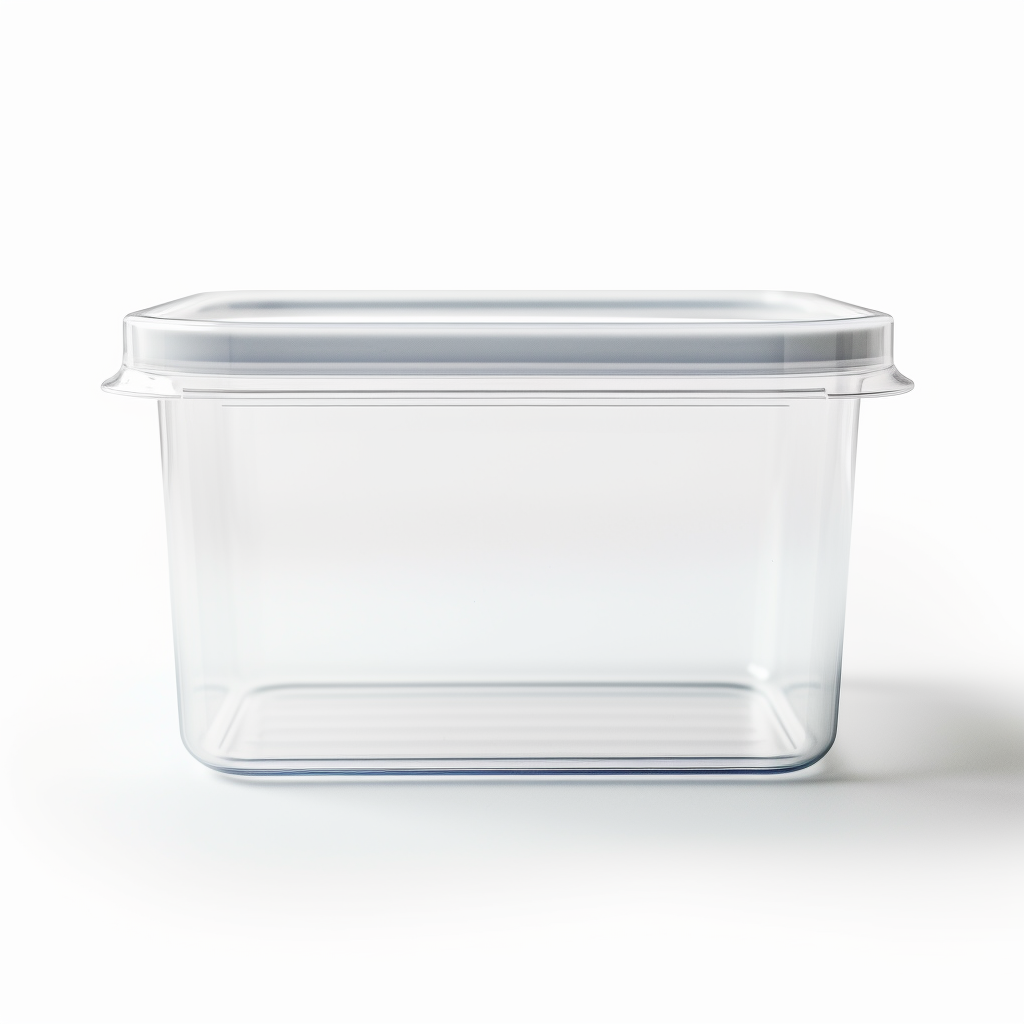
Advantages
- Transparency: PETG boasts exceptional clarity, making it an excellent choice for applications where visibility and aesthetics are important, such as retail displays and signage.
- Durability: PETG is impact-resistant and tough, making it suitable for products that need to withstand rough handling and potential falls.
- Chemical Resistance: It is resistant to a wide range of chemicals, ensuring its stability in various environments.
- Recyclability: PETG is recyclable, and the use of recycled PETG (rPETG) further promotes sustainability.
- Easy to Fabricate: PETG is easy to cut, shape, and form, making it a versatile material for custom fabrication projects.
- FDA Approval: Many PETG blends are FDA compliant for use in food contact applications, making it safe for packaging and food containers.
Disadvantages
- Lower Heat Resistance: PETG has a lower heat resistance compared to some other engineering plastics like PEEK or PPS. It may soften or deform at elevated temperatures.
- UV Sensitivity: PETG is sensitive to UV radiation and may degrade when exposed to prolonged sunlight. UV-stabilized variants are available to mitigate this issue.
- Not Suitable for High-Temperature Environments: PETG may not be suitable for applications that require exposure to high temperatures due to its lower heat resistance.
Common Applications of PETG
- Automotive: PETG is used for interior components like trim, dashboards, and door panels due to its impact resistance and clarity.
- Aerospace: In the aerospace industry, PETG may find use in applications such as windows, lighting covers, and cabin interior components.
- Medical: PETG is used for medical packaging, including blister packs and clamshell packaging, as well as for medical device components because of its biocompatibility.
- Food Packaging: PETG is utilized for food packaging containers, including trays, cups, and bottles, thanks to its transparency and FDA approval for food contact.
- 3D Printing: PETG is a popular filament material for 3D printing due to its ease of use, durability, and transparency.
- Cosmetics and Personal Care: PETG is commonly used for packaging cosmetics, lotions, and personal care products, where product visibility and protection are essential.
- Electronics: PETG is used for manufacturing electrical enclosures, covers, and protective components due to its durability and ease of customization.
- Retail and Display: PETG is extensively used for creating retail displays, signage, and product packaging due to its transparency and aesthetic appeal.
- Point-of-Purchase Displays: PETG is a favored material for creating attractive and durable point-of-purchase displays in retail environments.
Please consult a Canyon Components Engineer about your specific application and we will use our decades of experience to formulate a solution that fits your need.
Types of PETG
PETG can come in different variations, depending on its composition and intended use. Some common types of PETG include the following.
Canyon Components strives to meet all customer service requests. Feel free to contact Canyon Components engineering and let our knowledgeable staff help you design the perfect part for your needs.
Clear PETG
Known for its excellent clarity and high gloss, Clear PETG is ideal for applications where visibility is key, such as in packaging, medical devices, and display cases. It combines transparency with impact resistance, making it a durable alternative to glass and acrylic.
UV Resistant PETG
This type of PETG is treated to resist ultraviolet light, making it suitable for outdoor applications. It's used in signage, outdoor displays, and glazing where long-term exposure to sunlight is a factor. UV resistance helps in maintaining color and material integrity over time.
Anti-Static PETG
Specifically designed for static-sensitive environments, Anti-Static PETG is used in electronic packaging and cleanroom applications. It prevents the buildup of static electricity, protecting electronic components from static discharge.
Flame Retardant PETG
Incorporating flame-retardant additives, this variant is used in applications requiring high fire safety standards, such as public transportation, electronic housings, and industrial safety guards. It maintains the material's inherent properties while significantly reducing flammability.
FDA Compliant PETG
This form of PETG is certified for direct food contact, making it suitable for food and beverage packaging, kitchenware, and medical containers. Its safety for food-related applications is a key feature, ensuring no harmful substances leach into the contents.
Impact Modified PETG
Enhanced for superior impact resistance, this type is used in applications where durability and strength are critical, such as protective equipment, high-traffic displays, and industrial machinery guards. Despite its toughness, it maintains PETG's ease of fabrication and clarity.
Please consult a Canyon Components Engineer about your specific application and we will use our decades of experience to formulate a solution that fits your need.
Manufacturing Options for PETG
PETG parts can be manufactured using several methods, each suitable for different applications and part complexities.
Each of these methods has its own advantages, limitations, and cost implications. The choice of manufacturing technique usually depends on factors like the complexity of the design, required precision, material properties, and production volume.
Canyon Components strives to meet all customer service requests. Feel free to contact Canyon Components engineering and let our knowledgeable staff help you design the perfect part for your needs.
Back to Plastics Hub
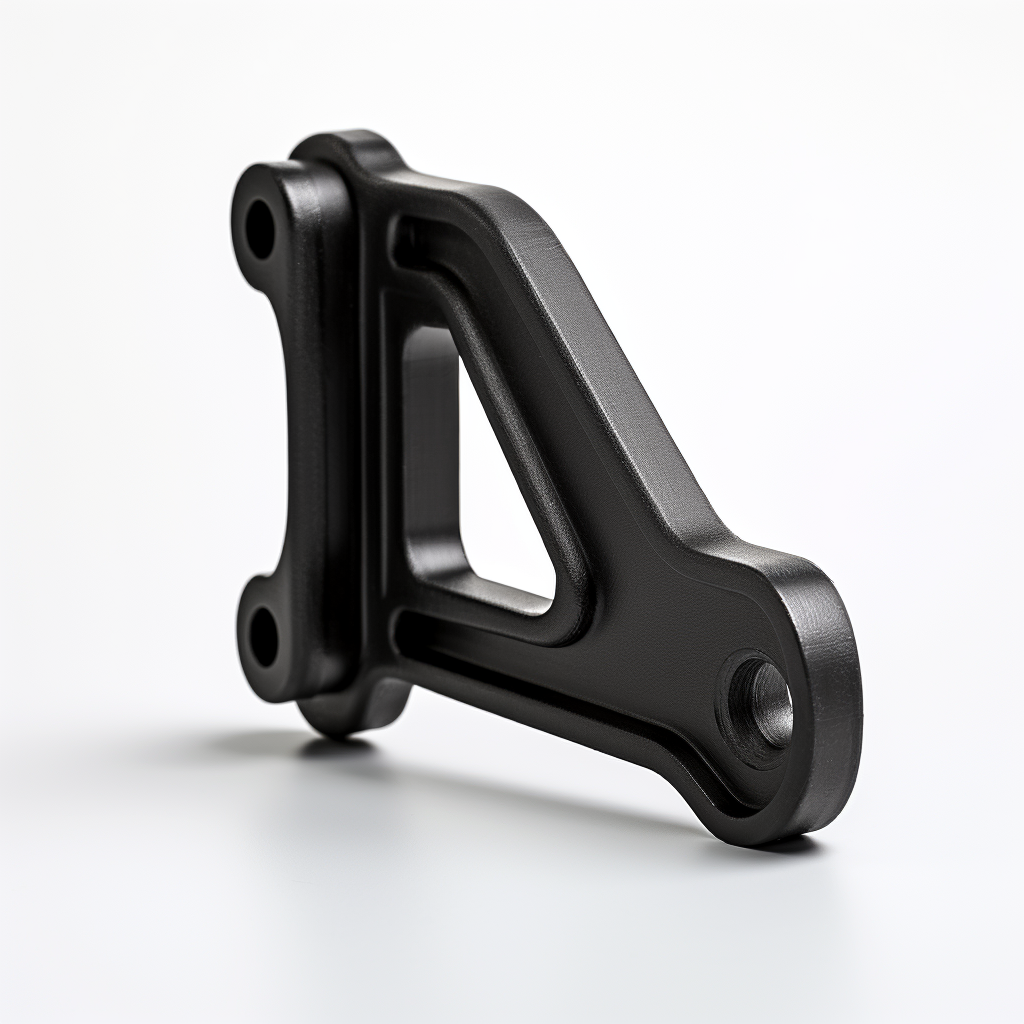
Get A Quote Now!
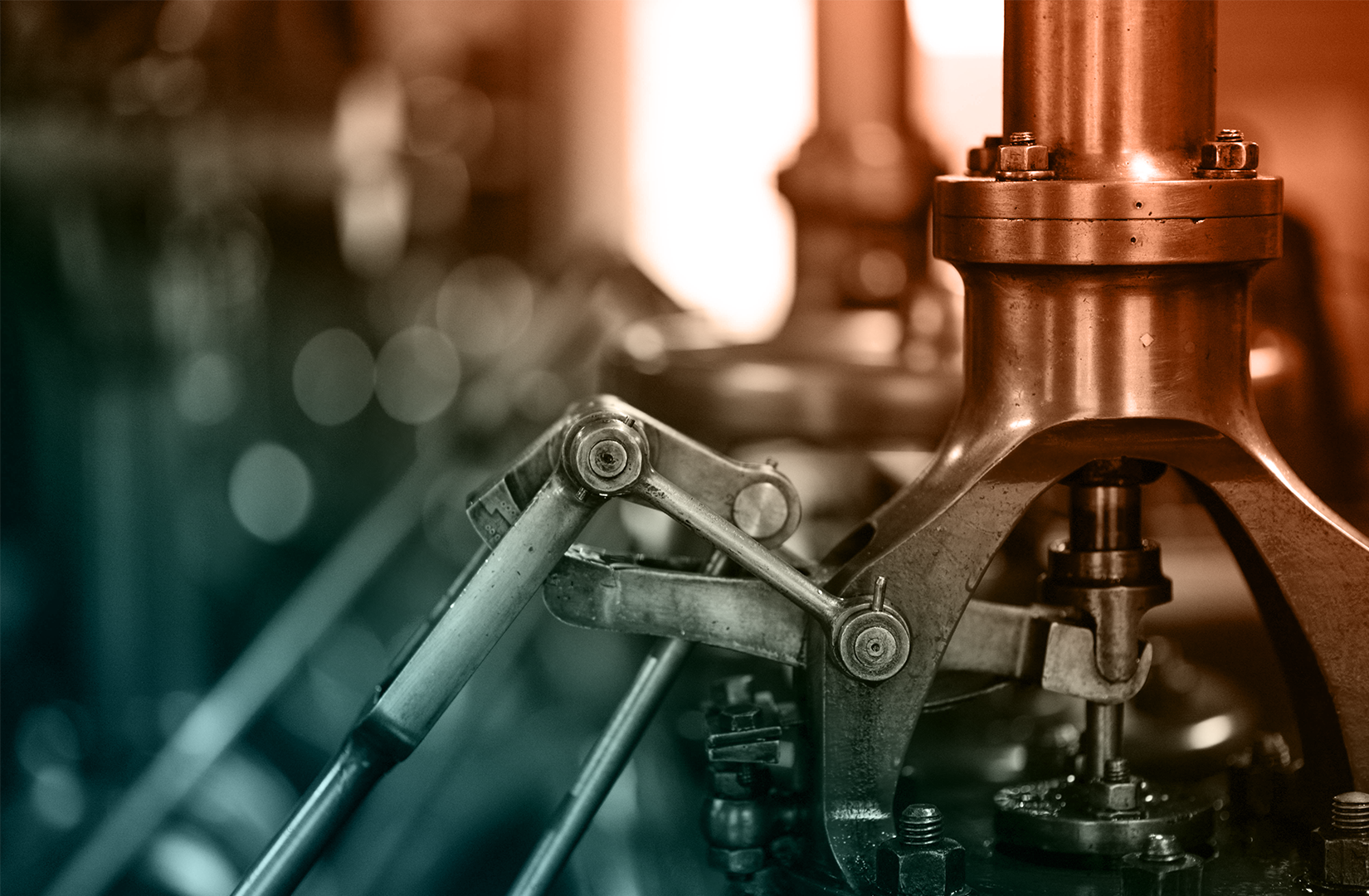
Groove Design References
Learn More
Coatings, Packaging, & Other Services
Learn More
Custom Parts & Custom O-rings
Learn More