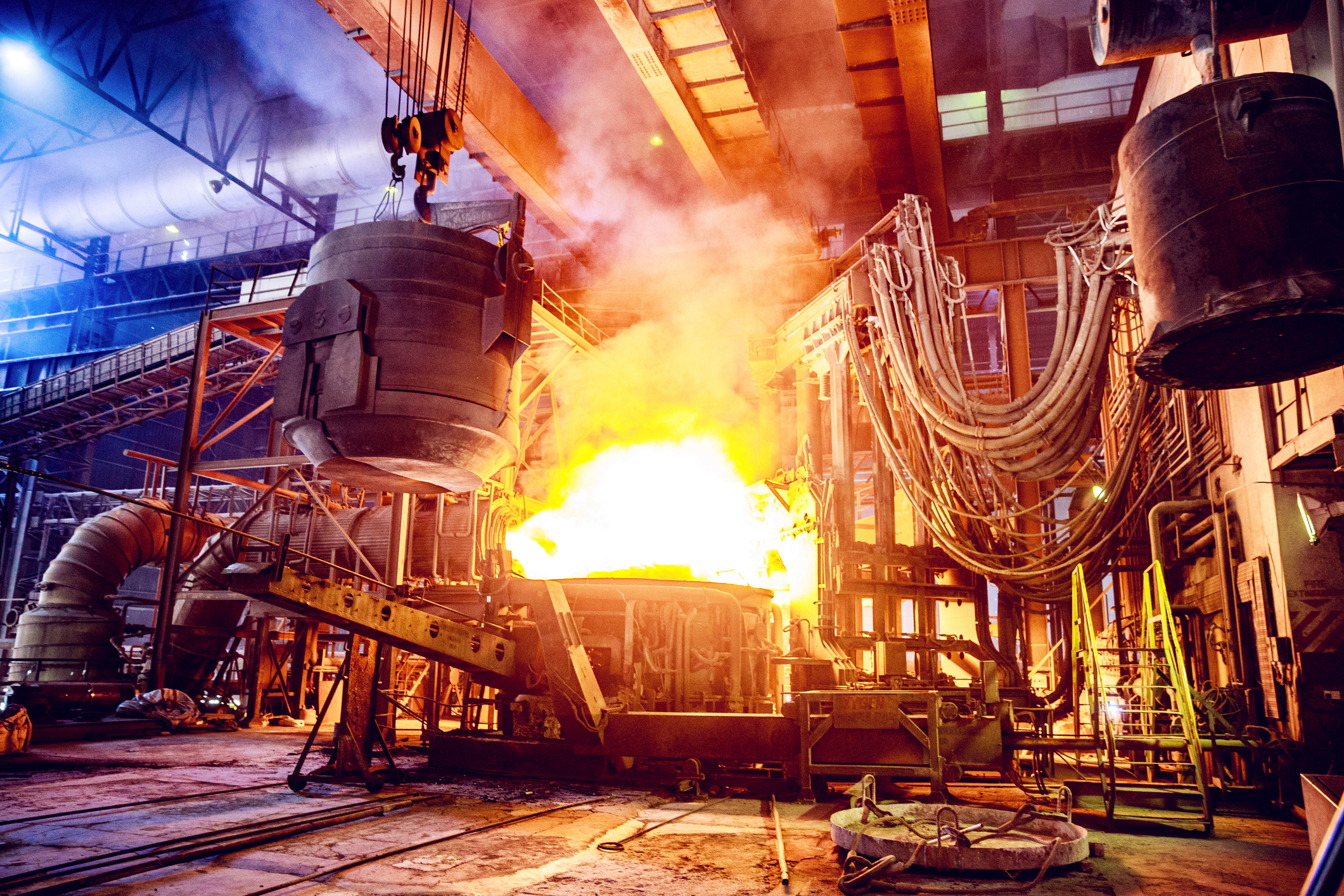
Compression Molding
Compression molding is a versatile manufacturing process used to create a wide range of composite and thermosetting plastic parts. It involves the application of pressure and heat to a material within a mold to form the desired shape. In this web page, we will explore the different types of compression molding, their advantages and disadvantages, and the diverse industrial applications. Additionally, we'll provide a list of materials commonly used in compression molding manufacturing. Custom Compression Molded parts available now!
Check with one of Canyon’s helpful product engineers for an expert material and manufacturing recommendation.
Common terminology includes: Vacuum forming, pressure forming, drape forming, twin-sheet thermoforming, plug and play thermoforming, match metal thermoforming, billow thermoforming, rotational thermoforming, mechanical thermoforming, blister forming.
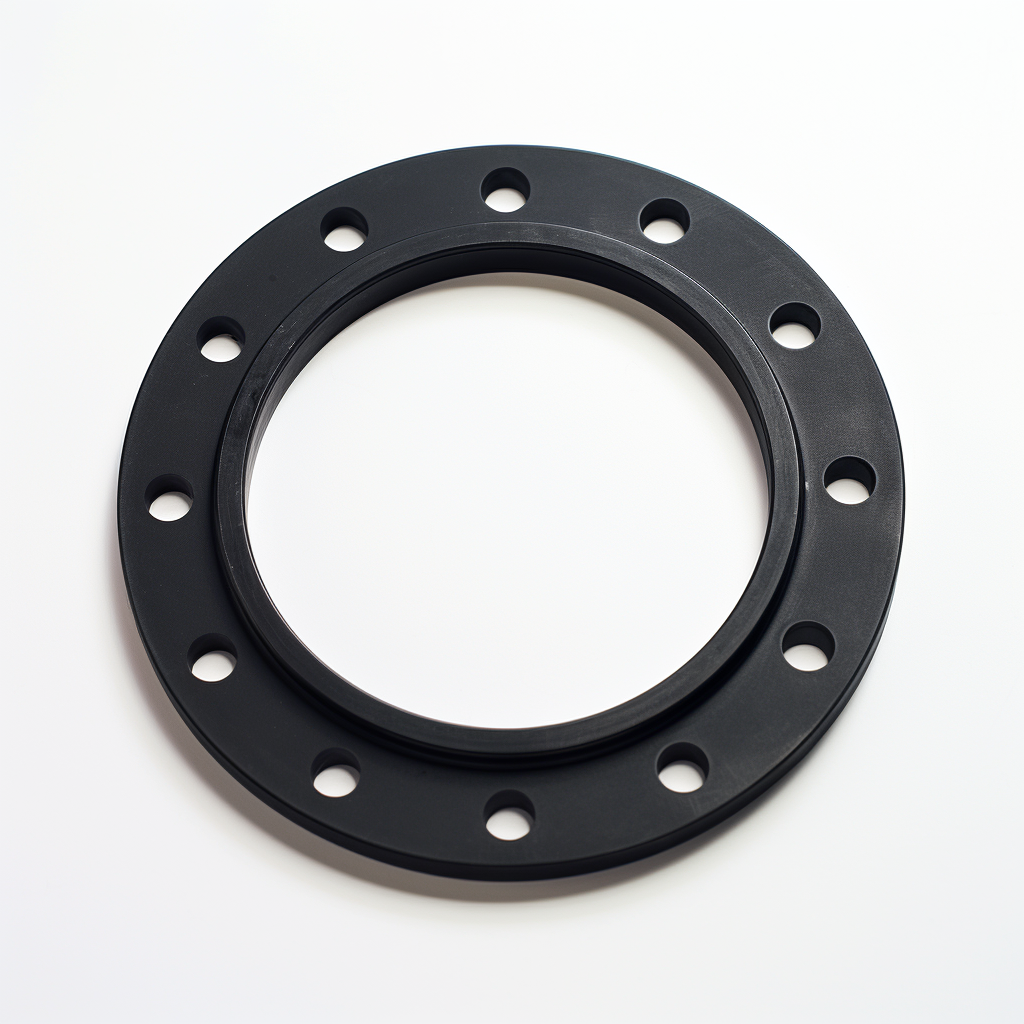
Advantages
- Cost-Effective: Suitable for both small and large-scale production runs.
- Material Efficiency: Minimizes waste, as excess material can be reused.
- Complex Shapes: Allows for the production of intricate parts with precise details.
- Consistent Quality: Ensures uniformity and reliability in product dimensions.
- Customization: Easily incorporates features like textures and inserts.
Disadvantages
- Limited Material Compatibility: Not all materials are suitable for compression molding.
- Cycle Times: Longer cycle times compared to some other manufacturing methods.
- Surface Finish: Achieving a smooth surface may require additional processing steps.
Common Applications of Compression Molding
- Automotive: Manufacturing engine gaskets, brake pads, and interior components.
- Aerospace: Producing electrical insulators, grommets, and aerospace seals.
- Electronics: Creating electrical connectors, insulators, and housing components.
- Medical: Fabricating medical device components, seals, and gaskets.
- Consumer Goods: Producing appliance parts, consumer electronics components, and packaging.
Please consult a Canyon Components Engineer about your specific application and we will use our decades of experience to formulate a solution that fits your need.
Types of Compression Molding
Compression Molding can be performed in a number of ways depending on the composition and intended use of the final product. Some variations available for Compression Molding include the following.
Canyon Components strives to meet all customer service requests. Feel free to contact Canyon Components engineering and let our knowledgeable staff help you design the perfect part for your needs.
Sheet Molding Compound (SMC) Compression Molding
Utilizes ready-to-mold fiberglass reinforced polyester material, providing high strength and light weight. Ideal for automotive and electrical industries. Advantages include excellent material strength and design flexibility. However, it involves higher material costs and longer cycle times compared to other molding processes.
Bulk Molding Compound (BMC) Compression Molding
Similar to SMC but in bulk form, suitable for smaller, intricate parts. It offers precise control over color and material properties. The downside is the potential for higher waste compared to other methods and requires precise control of pressure and heat.
Transfer Compression Molding
Involves transferring material from a separate chamber into the mold. This method is ideal for intricate designs and high-volume production. It allows for more consistent material distribution but can have higher tooling costs and increased waste material.
Wet Compression Molding
Utilizes a resin and fiber mixture, suitable for complex shapes and high-strength parts. Common in aerospace and automotive applications. The advantage is the ability to create parts with high fiber volume fractions. The downside includes longer cycle times and complexity in handling wet material.
Cold Compression Molding
Involves molding materials at room temperature, commonly used for rubber and plastic products. It’s energy-efficient and suitable for temperature-sensitive materials. However, the process may have longer cycle times and limited to simpler part geometries.
Flash Compression Molding
Excess material "flashes" out of the mold, ensuring proper material distribution and part consistency. Ideal for precise dimensional control. Advantages include high-quality surface finish and good detail. However, it results in material wastage and requires additional trimming processes.
Please consult a Canyon Components Engineer about your specific application and we will use our decades of experience to formulate a solution that fits your need.
Request a Quote for Compression Molded Parts
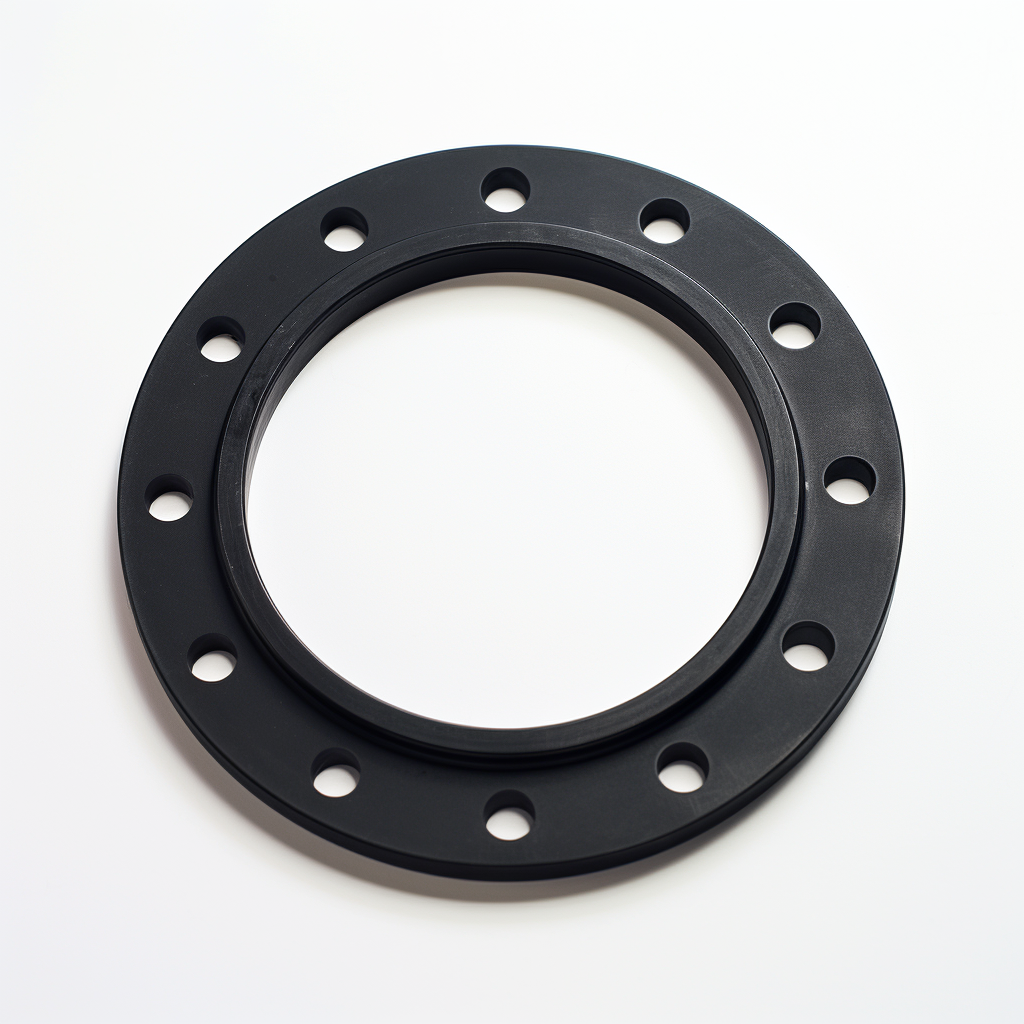
Compression Molding Materials Available
Compression Molding can be performed in a number of ways depending on the composition and intended use of the final product. Some common materials available for Compression Molding include the following.
Each of these materials has its own advantages, limitations, and cost implications. The choice of material and manufacturing technique usually depends on factors like the complexity of the design, required precision, material properties, and production volume.
Canyon Components strives to meet all customer service requests. Feel free to contact Canyon Components engineering and let our knowledgeable staff help you design the perfect part for your needs.
Elastomers
Elastomers (also referred to as rubber) are a class of materials known for their unique ability to stretch, deform, and return to their original shape, making them essential in a wide range of applications.
Perfluoroelastomers (FFKM, Kalrez, CanRez)
Extreme temperatures & chemicals require extreme solutions! CanRez™ FFKM materials offer extreme reliability where you need it most! Thousands of sizes in stock now!
FKM (Viton®, Fluorocarbon)
FKM compounds, O-rings, gaskets, & custom molded parts exhibit excellent mechanical attributes as well as excellent resistance to high temperatures, mineral oil, ozone, fuels, hydraulic fluids, and many other solvents and chemicals.
Silicone (VMQ, PVMQ)
Silicone seals, O-rings, gaskets, & custom molded parts are excellent for extreme temperatures in static applications. Canyon Components carries a range of silicone materials, and we are happy to custom tailor a seal to meet your application requirements!
Specialty Compliances
Canyon have materials available for O-rings, gaskets, & custom parts with compliances ranging from USP Class VI <87> & <88> for medical applications, to FDA CFR 21.177.2600 grades A through F for different food types, to the various drinking water specifications like KTW and NSF. Whether it's metal, rubber, or plastic, Canyon can meet your needs!
EPDM (Ethylene Propylene)
EPDM materials, O-rings, gaskets, & custom molded parts can operate over a wide temperature range, and are compatible with glycol fluids that cause problems for most typical elastomeric seals.
Aflas® (TFE/P)
TFE/P (Aflas) compounds, O-rings, gaskets, & custom molded parts gives high resistance to steam, hot water, atmospheric wear, and many chemicals. TFE/P compounds provide superior performance in water, steam and virtually all caustic chemicals.
NBR (Nitrile, Buna-N)
Nitrile O-rings, gaskets, & custom molded parts are very oil-resistant, have strong mechanical properties, are resistant to wear, and are relatively inexpensive. These properties make Nitrile the most commonly used general purpose O-ring, gasket, & custom molded part material.
Plastics
Plastics are a broad class of synthetic or semi-synthetic materials known for their versatility and moldability. They are crucial in numerous applications due to their ability to be shaped, lightweight nature, and resistance to chemicals and moisture.
PEEK (Polyetheretherketone)
PEEK plastic, or polyether ether ketone, is a high-performance thermoplastic known for its exceptional heat resistance, chemical stability, and mechanical strength. It's widely used in aerospace, medical implants, and automotive industries for its durability and ability to withstand harsh environments.
Polyethylene (PE)
Polyethylene (PE) plastic, renowned for its versatility, is a widely used thermoplastic. It's lightweight, impact-resistant, and has excellent chemical resistance. Commonly used in packaging, containers, and pipes, PE is available in varying densities for different applications, including high and low-density forms.
Polyurethane (PU, AU)
Polyurethane O-rings, gaskets, & custom molded parts generally have two or three times greater tensile strength and wear resistance than Nitrile and comparable polymers. Polyurethane also provides excellent permeation resistance when compared to most rubbers.
Back to Manufacturing Hub
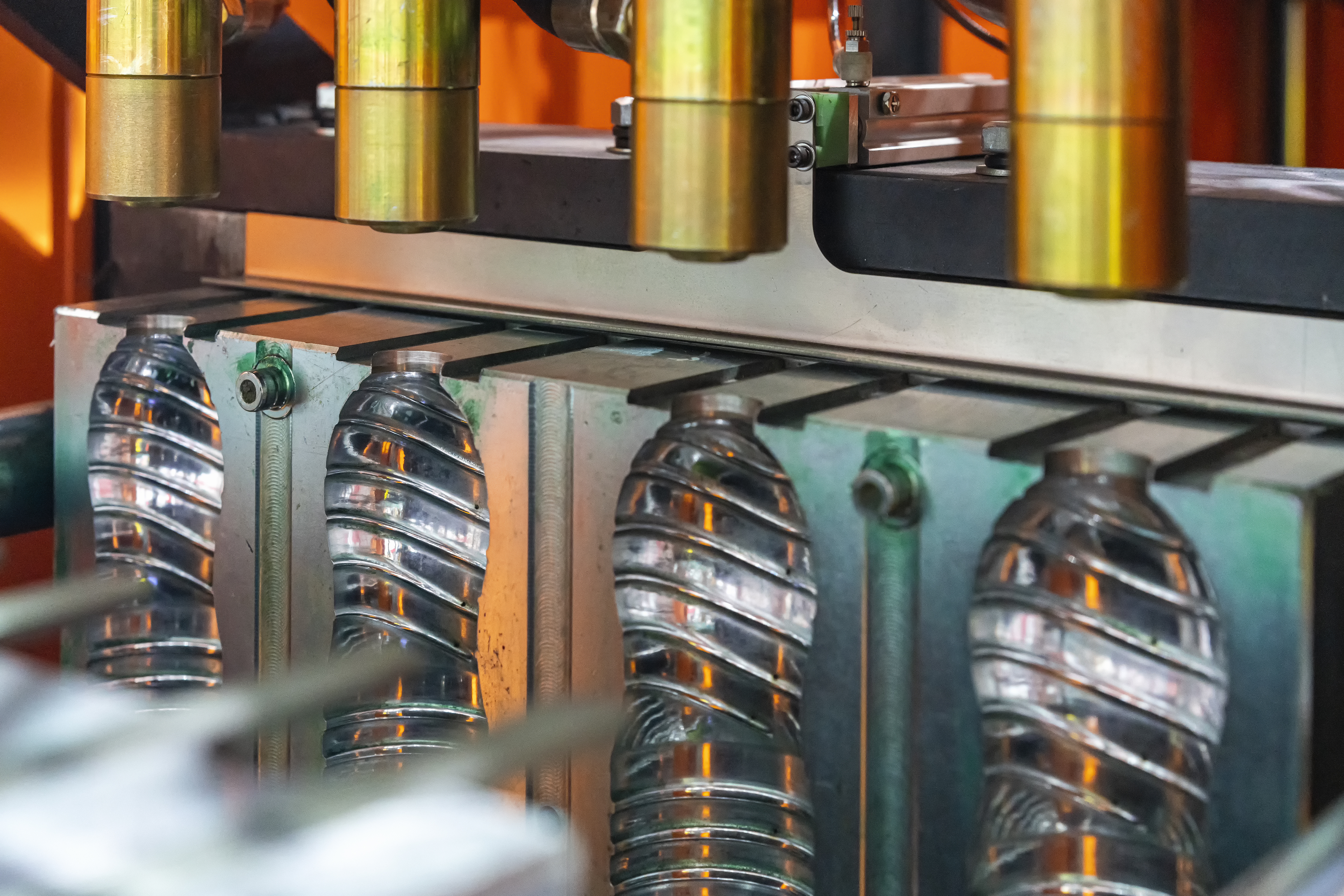
Get A Quote Now!
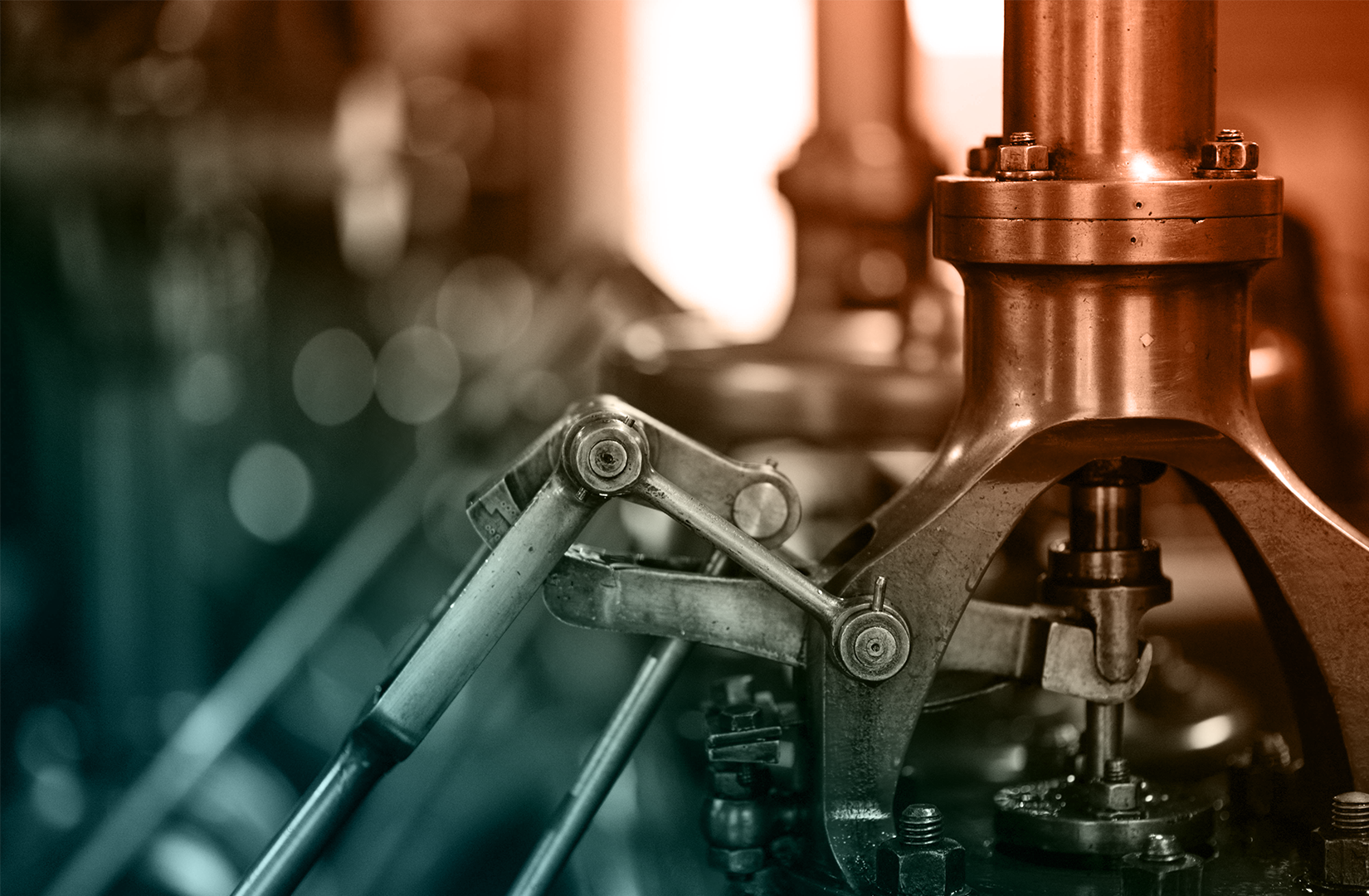
Groove Design References
Learn More
Coatings, Packaging, & Other Services
Learn More
Custom Parts & Custom O-rings
Learn More