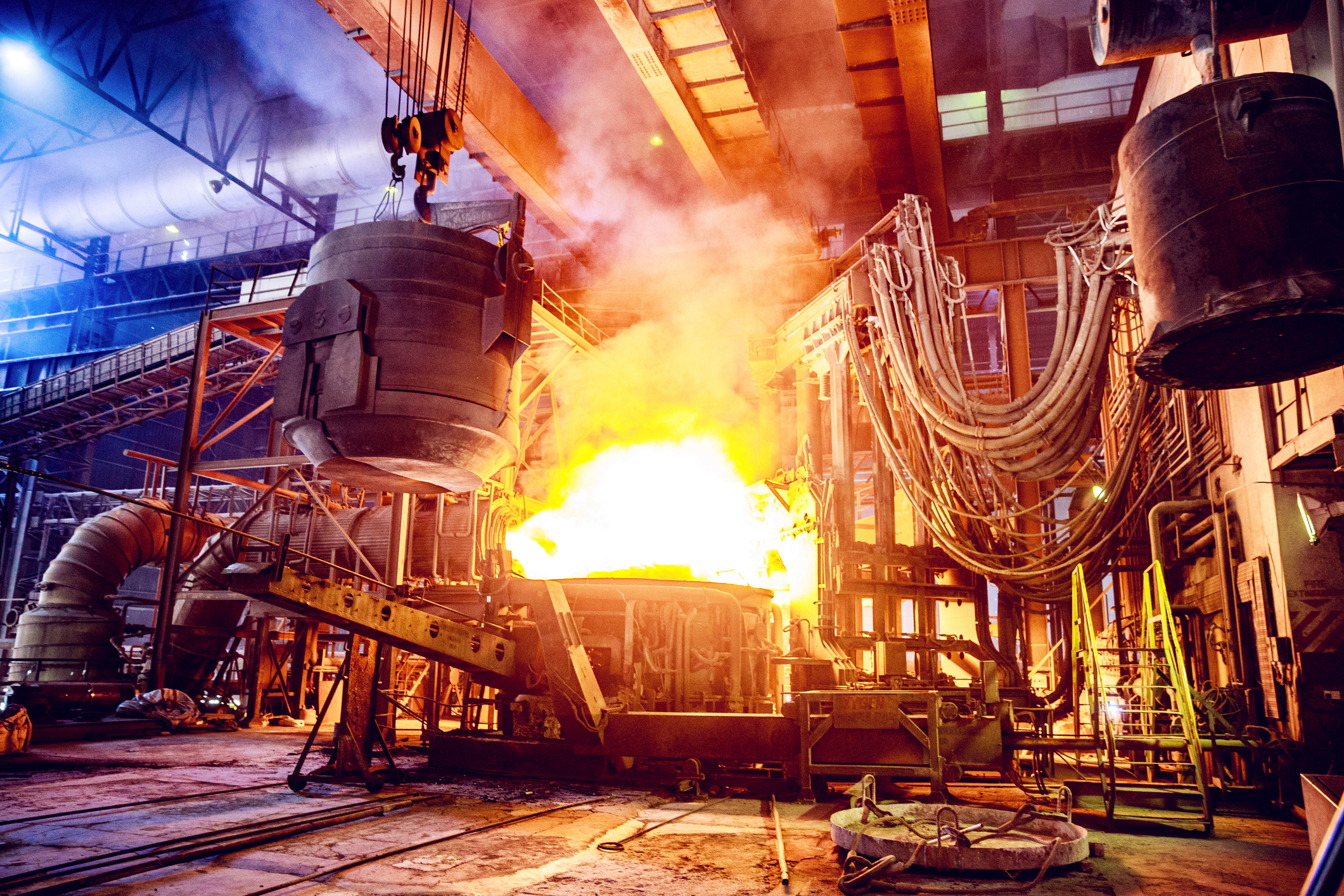
NBR (Nitrile, Buna-N) Selection Guide
Nitrile is the term used to describe a copolymer of acrylonitrile and butadiene. The amount of acrylonitrile used in the copolymer varies between compounds and has a profound effect on the mechanical and physical properties of the material, O-rings, gaskets, & custom molded parts. Generally, Nitrile O-rings, gaskets, & custom molded parts are very oil-resistant, have strong mechanical properties, are resistant to wear, and are relatively inexpensive. These properties make Nitrile the most commonly used general purpose O-ring, gasket, & custom molded part material. Canyon Components carries a huge variety of Nitrile based seals, O-rings, gaskets, & custom molded parts and supplies thousands of customers in a diverse range of industries.
Specific physical and chemical resistances vary by compound formulation. Basic NBR O-rings, gaskets, & custom molded parts are not resistant to weathering or ozone without special formulation. Hydrogenated versions of NBR (HNBR) O-rings, gaskets, & custom molded parts are more resistant to temperature, chemicals, and ozone.
Common names include: NBR (acrylonitrile butadiene rubber), Buna-N, Nitrile Trade Names: CHEMIGUM®, HYCAR®, PARACRIL® , PERBUNAN®, KRYNAC®, NYSYSN®
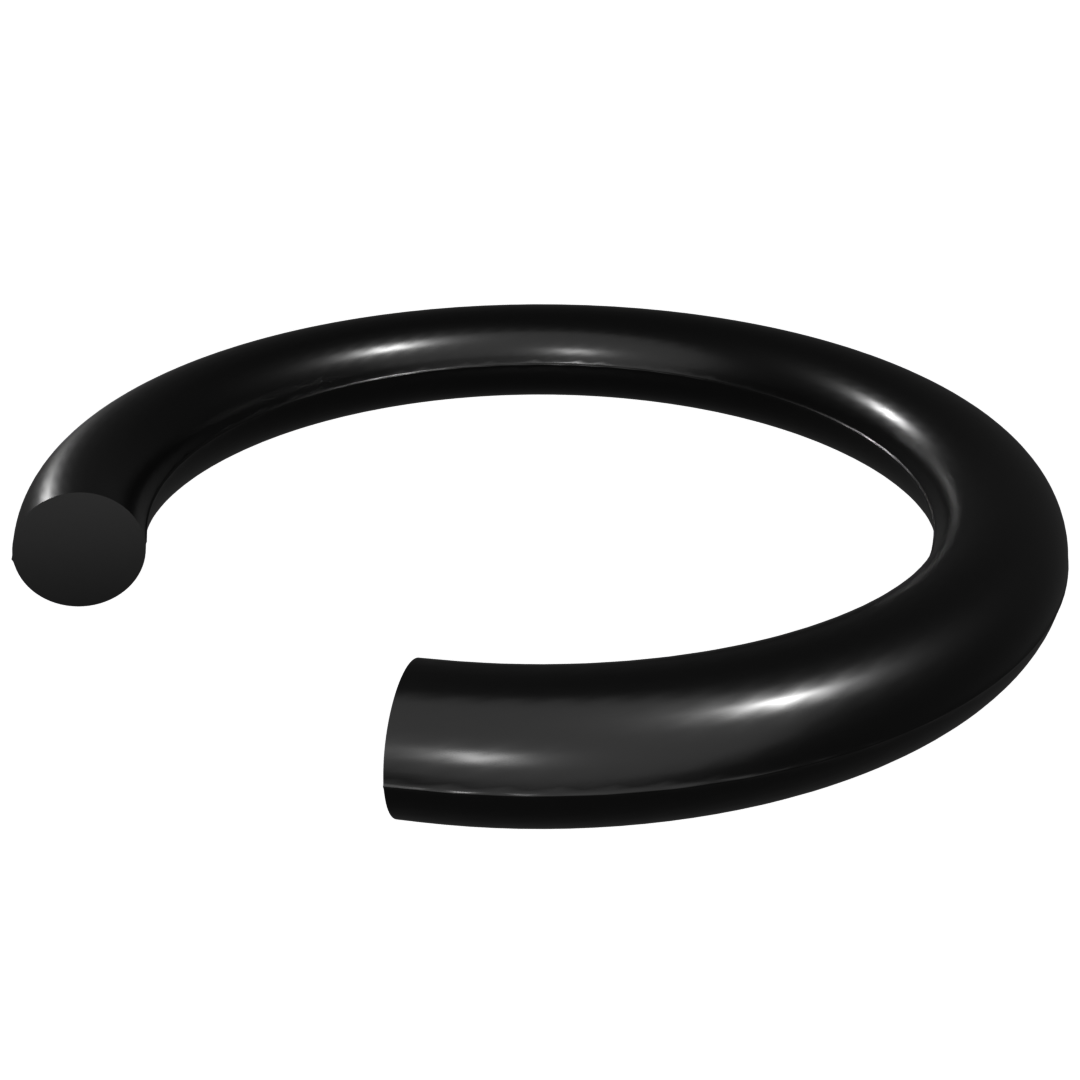
Features of NBR
- NBR O-rings, gaskets, & custom molded parts have a relative low cost
- NBR O-rings, gaskets, & custom molded parts have good resistance to compression set and tear/abrasion
- NBR O-rings, gaskets, & custom molded parts have good resistance to many petroleum oils/greases, hydraulic fluids, alcohol, ambient water, silicone greases, mineral oil and grease
- NBR O-rings, gaskets, & custom molded parts have good resistance to many fuels and aliphatic hydrocarbons (propane, butane, diesel fuel, fuel oils) as well as ethylene-glycol based fluids
- NBR O-rings, gaskets, & custom molded parts are compatible with HFA, HFB and HFC fluids
- NBR O-rings, gaskets, & custom molded parts are available in multiple compounds to meet performance and cost requirements
Limitations of NBR
- NBR O-rings, gaskets, & custom molded parts are not compatible with ozone, direct sunlight, UV, or weathering
- NBR O-rings, gaskets, & custom molded parts have poor resistance to aromatic fuels, glycol-based brake fluids, polar solvents, non-flammable hydraulic fluids (HFD), aromatic/chlorinated hydrocarbons, and strong acids
- NBR O-rings, gaskets, & custom molded parts have a 15 year shelf life
- NBR O-rings, gaskets, & custom molded parts have a Service temperature range of (varies with application) Typically -20°F to 200°F (-30°C to 100°C) *Special formulations allow range of -65°F to 275°F (-54°C to 135°C)
Please consult a Canyon Components Engineer about your specific application and we will use our decades of experience to formulate a solution that fits your need.
NBR (Nitrile, Buna-N) Materials Available
This table shows many of our standard materials and links out to our O-ring store. Get in touch with us if you need a custom gasket, custom molded part, or non-standard geometry!
Filter by
Temperature Search (°C)
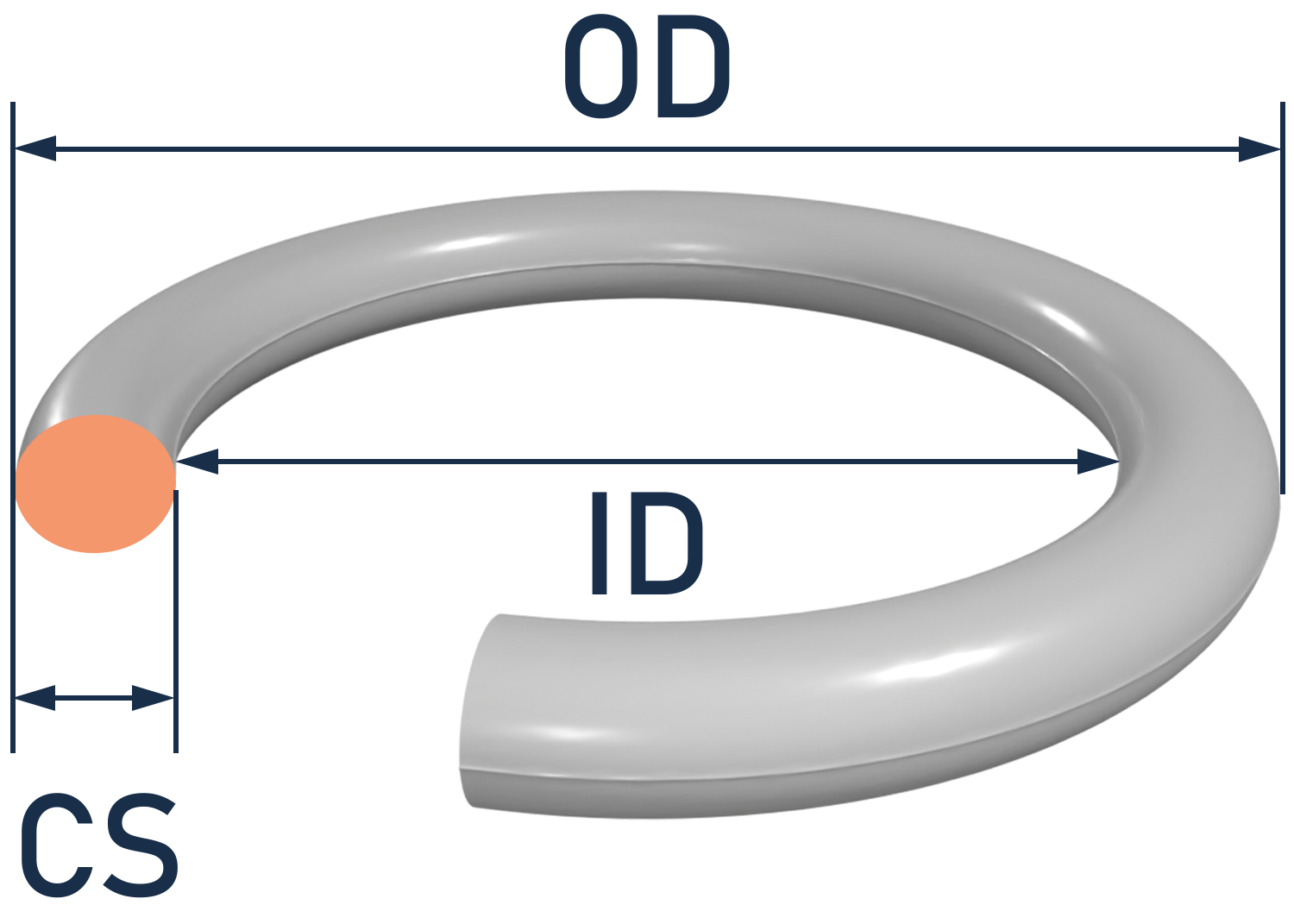
Back to Elastomers Hub
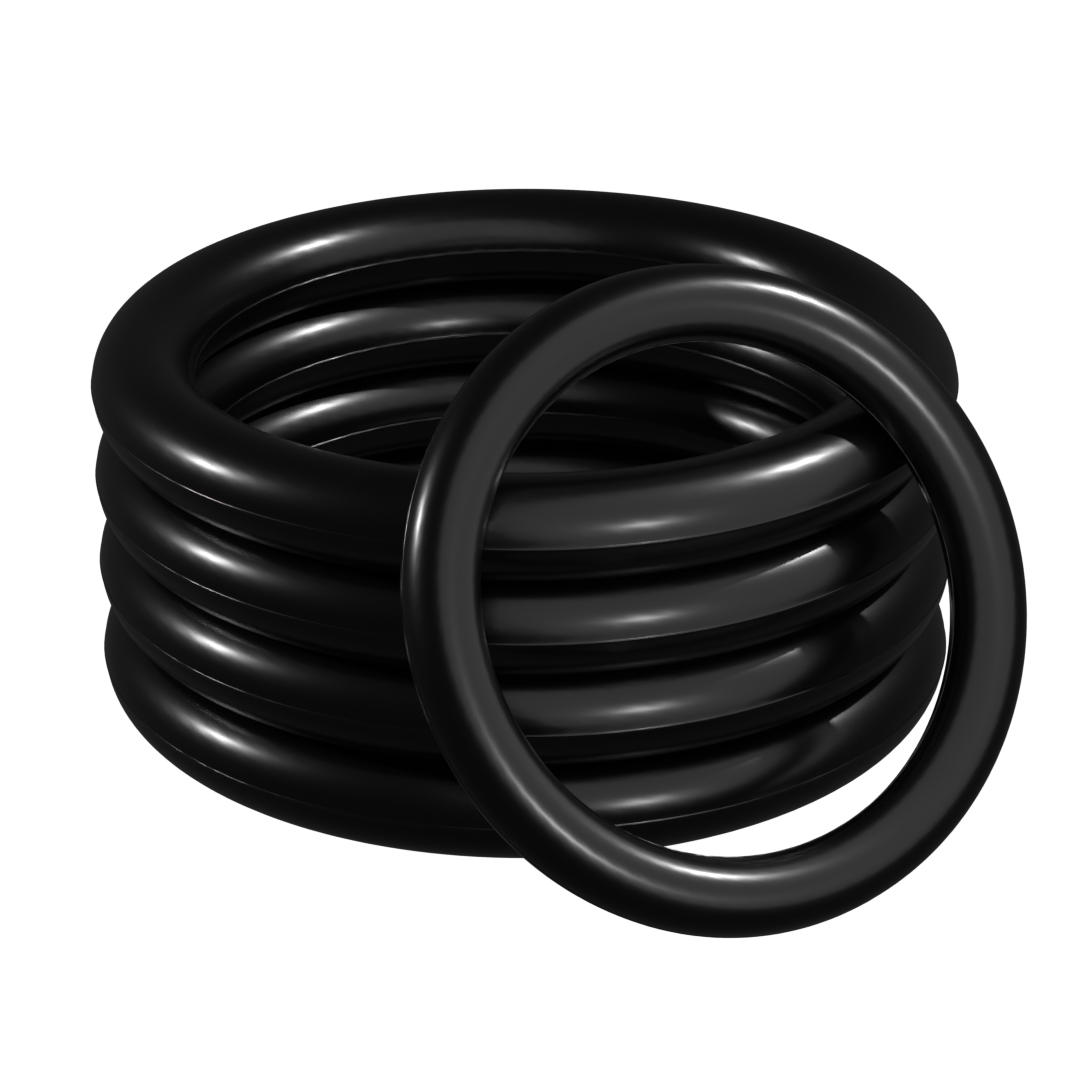
Get A Quote Now!
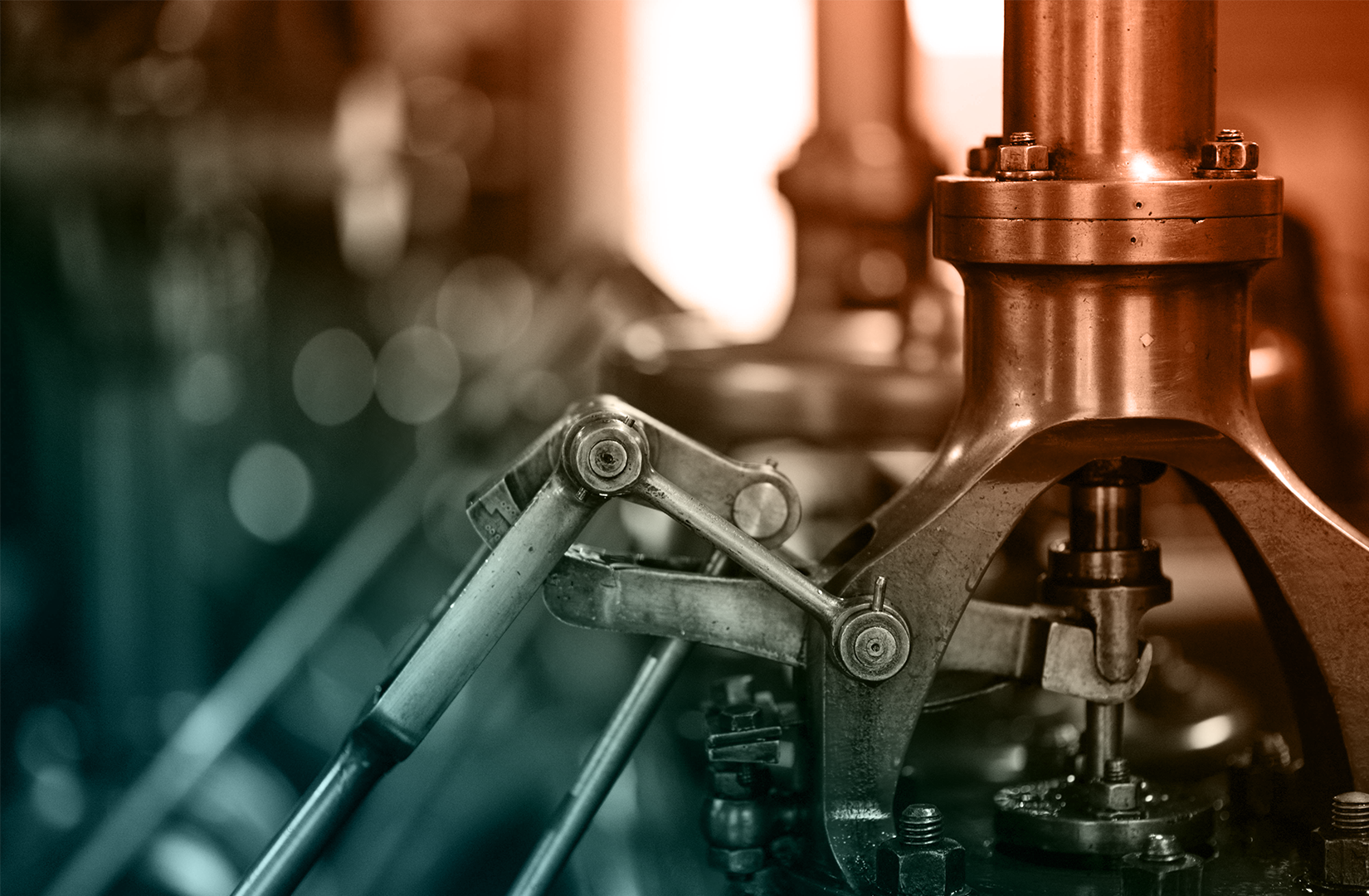
Groove Design References
Learn More
Coatings, Packaging, & Other Services
Learn More
Custom Parts & Custom O-rings
Learn More
Are silicone O-rings better than rubber?
Silicone and rubber O-rings (like EPDM, Viton, and NBR) each have unique properties, making them suitable for different applications. The choice between them depends on the specific requirements of your use case. Here are some key differences:
1. Temperature Resistance: Silicone O-rings generally have a wider temperature range compared to other rubber materials. They can operate effectively in more extreme temperatures, both hot and cold.
2. Chemical Resistance: Rubber O-rings, particularly those made from nitrile or other specialized compounds, often have better resistance to certain oils and fuels compared to silicone. However, silicone is generally more resistant to weathering, ozone, and UV radiation.
3. Durability: Other rubber materials are typically more durable and have better tear resistance than silicone. They're suited for applications involving high pressure or where mechanical wear is a concern.
4. Flexibility and Seal Quality: Silicone maintains its flexibility over a wider range of temperatures, which can be crucial in certain sealing applications. However, for dynamic applications where the O-ring is in constant motion, other rubber materials might provide better performance.
5. Cost and Availability: Other rubber materials are usually more cost-effective and widely available in a variety of sizes and specifications.
6. Food Safety and Medical Applications: Silicone is often preferred for food-grade and medical applications due to its inertness and ability to be sterilized.
In summary, if your application involves extreme temperatures, exposure to UV light, or requires FDA compliance for food or medical use, silicone O-rings might be the better choice. However, for general industrial applications, especially where oil and fuel resistance, durability, and cost are concerns, O-rings made from other rubber materials might be more suitable.
Are Viton O-rings better than regular O-rings?
Whether Viton O-rings are "better" than regular O-rings depends on the specific requirements of the application. Here's a comparison based on various factors:
1. Chemical Resistance:
- Viton O-rings have excellent resistance to a wide range of chemicals, including oils, fuels, lubricants, and most mineral acids. This makes them superior in harsh chemical environments.
- Regular O-rings (made from materials like Nitrile, Silicone, or EPDM) have varying levels of chemical resistance, but generally, they are not as broadly resistant as Viton.
2. Temperature Resistance:
- Viton withstands higher temperatures (ranging from -15°F to 437°F) better than most common O-ring materials. This makes it suitable for high-temperature applications. Some blends of Viton can even perform well outside of this range.
- Regular O-rings have a range of temperature tolerances depending on the material. For instance, Silicone can handle high temperatures well, but not as high as Viton.
3. Durability and Longevity:
- Viton has excellent resistance to aging, weathering, ozone, oxygen, and sunlight. This makes Viton O-rings more durable and long-lasting in harsh environments.
- Regular O-rings also have good durability, but their longevity will vary based on material and environmental conditions.
4. Cost:
- Viton O-rings are generally more expensive than regular O-rings due to their superior performance characteristics.
- Regular O-rings are more cost-effective and might be sufficient for less demanding applications.
5. Application Specific:
- The choice should be based on the specific requirements of the application, such as exposure to chemicals, temperature ranges, and mechanical wear and tear.
In summary, Viton O-rings are superior in terms of chemical and temperature resistance, durability, and longevity, but they are also more expensive. "Regular" O-rings made from materials like Silicone, EPDM, or Nitrile may be sufficient for less demanding applications and are more cost-effective. The choice of material should be based on the specific conditions and requirements of your application.
Can I use silicone instead of an O-ring?
Using silicone as a direct substitute for an O-ring depends on the specific application and the conditions under which the seal is required to function. Here are some considerations:
1. Sealing Requirements: O-rings are designed to create a very effective seal between two parts, especially in dynamic applications where parts may move or vibrate. Silicone in the form of a caulk or sealant may not provide the same level of sealing efficiency, especially under pressure.
2. Physical Properties: O-rings are made from materials that can withstand a range of pressures and temperatures while maintaining their shape and flexibility. Silicone sealants or sheets may not have the same level of durability or resilience under similar conditions.
3. Chemical Compatibility: While silicone has good chemical resistance, the specific formulation of an O-ring might be chosen for its resistance to particular chemicals. Replacing it with a different silicone material could lead to reduced chemical resistance.
4. Application Design: Many systems are specifically designed to use O-rings. Using a different material like silicone sealant could lead to improper fit or function, potentially causing leaks or mechanical failures.
5. Ease of Replacement and Maintenance: O-rings are generally easier to replace and maintain compared to silicone sealants, which may require removal and reapplication.
If you're considering using silicone as a substitute for an O-ring, it's important to carefully evaluate these factors. In some low-stress, low-pressure, and non-critical applications, silicone sealants might work as a temporary fix. However, for most industrial or mechanical applications, it's advisable to use the appropriate O-ring designed for the specific purpose. If in doubt, consulting with a mechanical engineer or the equipment manufacturer is recommended.
Is Buna better than Viton?
Comparing Buna (often referred to as Nitrile or Buna-N) with Viton (a brand of fluoroelastomer) involves considering the specific requirements of the application, as each material has its strengths and weaknesses. Here’s a comparative analysis based on various factors:
1. Chemical Resistance:
- Viton: Exceptionally resistant to a wide range of chemicals, including oils, fuels, lubricants, and most mineral acids. It's superior in environments with harsh chemicals.
- Buna-N: Good resistance to oils and some chemicals, but not as broadly resistant as Viton, especially to strong acids and various solvents.
2. Temperature Resistance:
- Viton: Can withstand higher temperatures, generally between -15°F to 437°F (-26°C to 225°C), making it suitable for high-temperature applications.
- Buna-N: Has a decent temperature range but not as high as Viton, typically -40°F to 257°F (-40°C to 125°C).
3. Cost:
- Viton: Generally more expensive than Buna due to its superior performance in harsh environments and its more complex manufacturing process.
- Buna-N: More cost-effective, making it a preferred choice for applications where conditions do not demand Viton's high level of performance.
4. Physical Properties:
- Both materials have good physical properties like tensile strength and flexibility, but these can vary depending on the specific formulation.
5. Applications:
- Viton: Often used in automotive, aerospace, chemical processing, and industrial applications where high chemical and temperature resistance are required.
- Buna-N: Commonly used in automotive (particularly where oil resistance is needed), food handling, and general industrial applications where moderate resistance is sufficient.
6. Durability:
- Viton: Tends to have better longevity, especially in harsh chemical and thermal environments.
- Buna-N: While durable, it may not perform as well as Viton in extreme conditions but is sufficient for many standard applications.
In summary, whether Buna is "better" than Viton depends on the specific application requirements. Viton is superior in terms of chemical and temperature resistance, making it ideal for harsher environments, but it comes at a higher cost. Buna-N is a more cost-effective solution for applications that require good oil resistance and moderate temperature and chemical resistance. The decision should be based on balancing the performance requirements and budget constraints of your specific application.
Is Buna the same as Buna-N?
Yes, "Buna" and "Buna-N" are often used interchangeably to refer to the same material. Both terms are common abbreviations for Nitrile rubber, which is also known as NBR (Nitrile Butadiene Rubber).
- Buna: This term originated from the names of the two primary monomers used in the production of Nitrile rubber, "Bu" from butadiene and "Na" from sodium. It was used historically but is still used colloquially to refer to Nitrile rubber.
- Buna-N: The "N" in "Buna-N" specifically stands for "Nitrile," emphasizing the material's composition.
Both terms refer to the same synthetic rubber material with excellent resistance to oils, fuels, lubricants, and many other petroleum-based products. It is widely used in sealing applications, such as O-rings, gaskets, seals, hoses, and more, in various industries.
Is EPDM better than rubber?
Whether EPDM (Ethylene Propylene Diene Monomer) is "better" than other types of rubber depends on the specific application and environment. EPDM is a type of synthetic rubber with particular properties that make it suitable for certain uses. Here's how EPDM compares to other rubbers in various aspects:
1. Resistance to Weathering and Ozone: EPDM excels in outdoor applications due to its superior resistance to UV radiation, ozone, and weathering. This makes it better than many other rubbers for applications exposed to harsh environmental conditions.
2. Temperature Resistance: EPDM has a wide operating temperature range and can perform well in both hot and cold environments, which is better than some types of rubber, like natural rubber, that don’t perform as well at higher temperatures.
3. Chemical Resistance: EPDM is resistant to many chemicals, particularly water-based and alkaline substances. However, it is not resistant to oil, gasoline, and hydrocarbons, where nitrile rubber or Viton would be better choices.
4. Electrical Insulation: EPDM is an excellent electrical insulator, making it preferable in applications where this property is required.
5. Flexibility and Durability: EPDM maintains its flexibility over a wide temperature range and has good tensile strength, but it may not be as flexible as some natural rubber compounds in certain applications.
6. Cost-Effectiveness: Generally, EPDM is more cost-effective than some specialized synthetic rubbers, like silicone or fluorocarbons (Viton), especially in applications where its specific resistance properties are required.
7. Water, Steam Resistance: EPDM is an excellent choice for applications involving water or steam, surpassing most other rubbers in this regard.
In summary, EPDM has advantages in environmental resistance, temperature range, and cost-effectiveness for specific applications. However, it is not suitable for use with oils or hydrocarbons, and other types of rubber may be better in those environments. The "best" rubber depends on the specific requirements of the application, including exposure to chemicals, temperature, and physical demands.
Is HNBR the same as Buna?
No, HNBR (Hydrogenated Nitrile Butadiene Rubber) is not the same as Buna (NBR). NBR (Nitrile Butadiene Rubber) and HNBR (Hydrogenated Nitrile Butadiene Rubber) are both synthetic elastomers known for their excellent resistance to oil, fuel, and chemicals. However, they differ in their chemical structure and performance characteristics. Here are the key differences between NBR and HNBR:
1. Chemical Structure:
- NBR: NBR is a copolymer of butadiene and acrylonitrile. It contains a nitrile group in its chemical structure, which provides oil and fuel resistance. The acrylonitrile content in NBR can vary, affecting its overall properties.
- HNBR: HNBR is a modified version of NBR. It is also a copolymer of butadiene and acrylonitrile, but it undergoes hydrogenation, which involves the addition of hydrogen atoms to the polymer chain. This hydrogenation process enhances its resistance to heat, ozone, and chemicals.
2. Oil and Fuel Resistance:
- NBR: NBR offers good oil and fuel resistance and is commonly used in applications involving petroleum-based oils, fuels, and lubricants.
- HNBR: HNBR provides excellent oil and fuel resistance, often surpassing the performance of standard NBR. It is preferred in applications where exposure to automotive engine oils and transmission fluids is common.
3. Temperature Range:
- Buna-N (NBR) has a temperature range of approximately -40°F to 257°F (-40°C to 125°C), which is generally lower than HNBR.
- HNBR has a higher temperature resistance compared to standard NBR. It can typically handle temperatures ranging from -40°F to 329°F (-40°C to 165°C) or higher, depending on the specific grade.
4. Chemical Resistance:
- NBR: NBR exhibits good resistance to many chemicals but may not perform as well as HNBR in highly aggressive chemical environments.
- HNBR: HNBR offers excellent chemical resistance to a broader range of chemicals, acids, and solvents compared to NBR.
5. Ozone and Weathering Resistance:
- NBR: NBR is susceptible to ozone and weathering degradation over time.
- HNBR: HNBR has improved resistance to ozone and weathering due to its hydrogenated structure.
6. Applications:
- NBR: NBR is commonly used in automotive seals, O-rings, gaskets, and hoses, especially in applications involving petroleum-based fluids.
- HNBR: HNBR is preferred in automotive applications where exposure to engine oils and transmission fluids is significant. It is also used in chemical processing, oil and gas industry, and other applications requiring enhanced chemical and temperature resistance.
In summary, while both NBR and HNBR offer good oil and fuel resistance, HNBR provides superior performance in terms of temperature resistance, chemical resistance, and resistance to ozone and weathering. The choice between the two depends on the specific requirements of the application, with HNBR being the preferred choice in demanding environments.
Is Nitrile a type of HNBR?
No, Nitrile (NBR) is not a type of HNBR (Hydrogenated Nitrile Butadiene Rubber). While both NBR and HNBR are synthetic rubber materials, they are distinct and have different chemical compositions and properties.
Here are the key differences between Nitrile (NBR) and Hydrogenated Nitrile (HNBR):
1. Chemical Structure:
- NBR: NBR is a copolymer of butadiene and acrylonitrile. It contains a nitrile group in its chemical structure, which provides oil and fuel resistance. The acrylonitrile content in NBR can vary, affecting its overall properties.
- HNBR: HNBR is a modified version of NBR. It is also a copolymer of butadiene and acrylonitrile, but it undergoes hydrogenation, which involves the addition of hydrogen atoms to the polymer chain. This hydrogenation process enhances its resistance to heat, ozone, and chemicals.
2. Oil and Fuel Resistance:
- NBR: NBR offers good oil and fuel resistance and is commonly used in applications involving petroleum-based oils, fuels, and lubricants.
- HNBR: HNBR provides excellent oil and fuel resistance, often surpassing the performance of standard NBR. It is preferred in applications where exposure to automotive engine oils and transmission fluids is common.
3. Temperature Range:
- Buna-N (NBR) has a temperature range of approximately -40°F to 257°F (-40°C to 125°C), which is generally lower than HNBR.
- HNBR has a higher temperature resistance compared to standard NBR. It can typically handle temperatures ranging from -40°F to 329°F (-40°C to 165°C) or higher, depending on the specific grade.
4. Chemical Resistance:
- NBR: NBR exhibits good resistance to many chemicals but may not perform as well as HNBR in highly aggressive chemical environments.
- HNBR: HNBR offers excellent chemical resistance to a broader range of chemicals, acids, and solvents compared to NBR.
5. Ozone and Weathering Resistance:
- NBR: NBR is susceptible to ozone and weathering degradation over time.
- HNBR: HNBR has improved resistance to ozone and weathering due to its hydrogenated structure.
6. Applications:
- NBR: NBR is commonly used in automotive seals, O-rings, gaskets, and hoses, especially in applications involving petroleum-based fluids.
- HNBR: HNBR is preferred in automotive applications where exposure to engine oils and transmission fluids is significant. It is also used in chemical processing, oil and gas industry, and other applications requiring enhanced chemical and temperature resistance.
In summary, HNBR is a modified and enhanced version of NBR that offers superior properties, particularly in terms of temperature and chemical resistance. Nitrile (NBR) and Hydrogenated Nitrile (HNBR) are distinct materials, and the choice between them depends on the specific requirements of the application.
Is Nitrile Rubber an EPDM?
No, Nitrile Rubber (often referred to as NBR, Buna-N, or Acrylonitrile Butadiene Rubber) is not the same as EPDM (Ethylene Propylene Diene Monomer). These are two distinct types of synthetic rubber, each with different chemical compositions and properties:
1. Nitrile Rubber (NBR):
- Composition: Made from acrylonitrile and butadiene.
- Properties: Known for its excellent resistance to oils, fuels, and other chemicals like aliphatic hydrocarbons, mineral oils, and greases.
- Temperature Range: Generally, NBR can withstand temperatures from -40°C to 125°C (-40°F to 257°F).
- Applications: Commonly used in the automotive and aeronautical industry to make fuel and oil handling hoses, gaskets, seals, and o-rings. It is also used in disposable gloves, especially in the medical field.
2. Ethylene Propylene Diene Monomer (EPDM):
- Composition: Made from ethylene, propylene, and a diene comonomer.
- Properties: Excellent resistance to weathering, ozone, UV, and aging; good heat and steam resistance; very good insulation properties. Not resistant to oils and fuels.
- Temperature Range: EPDM typically operates effectively in a range of -55°C to 150°C (-67°F to 300°F).
- Applications: Commonly used in automotive weather stripping and hoses, roofing membranes, outdoor electrical cable insulation, and waterproofing sheets.
In summary, while both Nitrile Rubber and EPDM are synthetic rubbers used in a variety of applications, they have different chemical resistances and are suitable for different environments. NBR is preferable in applications involving oils and hydrocarbons, while EPDM is better suited for outdoor, heat, and steam applications.
Is Viton stronger than Nitrile?
Comparing the strength of Viton and Nitrile requires considering various factors, as "strength" can mean different things in the context of material properties. Here's a breakdown of how Viton and Nitrile compare in terms of common material strength characteristics:
1. Chemical Resistance: Viton is generally more resistant to a wide range of chemicals, especially hydrocarbons, oils, acids, and some solvents. Nitrile is also resistant to oils and some chemicals, but not as broadly or effectively as Viton.
2. Temperature Resistance: Viton has a higher temperature resistance than Nitrile. It can withstand temperatures from -54 to 437°F depending on the type, making it suitable for high-temperature applications. Nitrile typically handles temperatures from -40°F to 257°F.
3. Physical Strength: When it comes to physical strength, like tensile strength and tear resistance, Nitrile is generally considered strong and durable. However, Viton, while also strong, is often chosen more for its chemical and temperature resistance than its physical toughness.
4. Elasticity and Flexibility: Nitrile generally has better low-temperature flexibility than standard Viton. This means that in cold environments, Nitrile might maintain better elasticity and resistance to deformation, however some specialty blends of Viton can outperform Nitrile in cold temperature environments.
5. Durability: Both materials are durable, but Viton tends to have a longer service life in harsh environments due to its superior resistance to heat, chemicals, and aging.
6. Cost: Viton is typically more expensive than Nitrile. The choice between the two often comes down to whether the additional cost of Viton is justified by the need for higher performance in extreme conditions.
In summary, "stronger" can mean different things. If strength refers to resistance to chemicals and high temperatures, then Viton is stronger. If strength refers to physical toughness and elasticity, particularly in colder environments, then Nitrile might be considered stronger. The choice between the two depends on the specific requirements of your application.
Is Viton the same as HNBR?
No, Viton (a brand of FKM, fluoroelastomer) is not the same as HNBR (Hydrogenated Nitrile Butadiene Rubber). These are two distinct types of synthetic rubber with different chemical compositions and properties:
1. Viton (FKM):
- Composition: Viton is a type of fluoroelastomer, which contains fluorine, carbon, hydrogen, and sometimes other elements. It is known for its excellent chemical resistance to a wide range of chemicals, including oils, fuels, acids, and solvents. Viton has a high-temperature resistance, typically up to 225°C (437°F).
- Applications: It is commonly used in industries where resistance to harsh chemicals and high temperatures is critical, such as the chemical processing, automotive, aerospace, and oil and gas industries.
2. HNBR (Hydrogenated Nitrile Butadiene Rubber):
- Composition: HNBR is a hydrogenated version of Nitrile Butadiene Rubber (NBR). It is produced by adding hydrogen to NBR, which improves its heat and ozone resistance, as well as its overall mechanical properties.
- Properties: HNBR combines the oil and fuel resistance of NBR with improved heat resistance. It can withstand temperatures higher than standard NBR, typically up to 165°C (329°F). It also has good resistance to various oils and chemicals.
- Applications: HNBR is commonly used in automotive and industrial applications where resistance to high temperatures and exposure to oils and fuels is required, such as in automotive engine components, seals, and gaskets.
While both Viton and HNBR have excellent chemical resistance properties, they are used in different applications due to their specific characteristics. Viton is known for its broader chemical resistance, especially to harsh solvents and aggressive chemicals, while HNBR is valued for its balance of oil and fuel resistance with improved heat resistance. The choice between them depends on the specific requirements of the application.
What are Buna O-rings made of?
Buna O-rings are made of a synthetic rubber known as Nitrile rubber or NBR (Nitrile Butadiene Rubber). This type of rubber is commonly referred to as "Buna" as a shorter name, which is derived from the original name of the material, "Bu" from butadiene and "Na" from sodium. Buna-N is widely used for its excellent resistance to oils, fuels, lubricants, and other petroleum-based products. It is a versatile material known for its durability and cost-effectiveness, making it a popular choice for O-rings, gaskets, seals, hoses, and other sealing applications in various industries.
What are cheap O-rings made of?
Cheap O-rings are typically made from less expensive elastomer materials compared to premium or specialized O-rings like Viton, specialty Silicone blends, Aflas, or FFKM. The choice of material depends on the cost-effectiveness required for the application. Here are some common inexpensive elastomers used for cheap O-rings:
1. Nitrile Rubber (NBR): Nitrile rubber, also known as Buna-N, is one of the most cost-effective elastomers. It offers good resistance to oils, fuels, and lubricants, making it a popular choice for many industrial applications. While it may not have the same level of performance as more expensive materials, it is suitable for many standard sealing applications.
2. EPDM (Ethylene Propylene Diene Monomer): EPDM is known for its excellent weather resistance and is often used in outdoor applications. It's more cost-effective than premium elastomers like Viton and Silicone and is suitable for sealing applications that don't require high-temperature or chemical resistance.
3. SBR (Styrene Butadiene Rubber): SBR is an economical elastomer often used in low-cost O-rings. It has good abrasion resistance but may not offer the same level of chemical resistance as Nitrile or EPDM.
4. Natural Rubber (NR): Natural rubber is another low-cost elastomer option. It offers good elasticity and low-temperature flexibility but may not perform well in environments with oils or certain chemicals.
5. Neoprene (CR): Neoprene is a moderately priced elastomer known for its resistance to weathering, ozone, and UV radiation. It's often used in outdoor applications where cost is a consideration.
While these materials are cost-effective, it's important to note that they have limitations compared to more expensive elastomers like Viton, specialty Silicone blends, Aflas, and FFKM. They may not perform well in extreme temperature or chemical environments. When choosing O-rings, it's essential to consider the specific requirements of your application and select the material that balances performance and cost-effectiveness to meet those needs.
What does Buna mean in O-rings?
"Buna" in the context of O-rings typically refers to a group of synthetic rubbers known as Nitrile rubber or NBR (Nitrile Butadiene Rubber). The term "Buna" originates from an earlier era of synthetic rubber development and is often used interchangeably with Nitrile rubber. Here's a brief overview:
1. Composition: Buna or Nitrile rubber is made from acrylonitrile and butadiene. The amount of acrylonitrile in the compound can vary, influencing the rubber's resistance to oils and fuels. Higher acrylonitrile content increases resistance to oils but can decrease the material's flexibility at lower temperatures.
2. Properties: Nitrile rubber is known for its excellent resistance to oils, fuels, and other petroleum-based products. It also has good mechanical properties, including resistance to abrasion and tearing.
3. Temperature Range: Buna O-rings can typically handle temperatures from -40°F to 257°F (-40°C to 125°C), making them suitable for a variety of industrial and automotive applications.
4. Applications: Commonly used in environments where resistance to oil and fuel is necessary, such as in fuel and oil handling hoses, seals, and gaskets. They are also used in automotive and aeronautical applications to make fuel and oil handling hoses, seals, grommets, and self-sealing fuel tanks.
5. Limitations: While Nitrile rubber is excellent for oil and fuel resistance, it is not recommended for applications involving exposure to ozone, strong acids, ketones, esters, and hydrocarbons with a high aromatic content.
In summary, when "Buna" is referred to in the context of O-rings, it typically means Nitrile rubber, a material well-suited for applications requiring resistance to oils and fuels.
What is a very high temperature O-ring?
The choice of the best O-ring material for high-temperature applications depends on the specific temperature range and other environmental factors involved. Several elastomer materials are suitable for high-temperature sealing, and the selection should be based on the following considerations:
1. Silicone Rubber (VMQ):
- Temperature Range: Certain Silicone rubber blends can handle temperatures up to 600°F (315°C), however most are only rated for 400°F (205°C).
- Advantages: Excellent high-temperature resistance, good flexibility, and resistance to ozone and UV exposure.
- Applications: Suitable for a wide range of high-temperature applications, including aerospace, automotive, and food processing.
2. Fluorocarbon Rubber (FKM/Viton):
- Temperature Range: FKM can withstand temperatures up to 437°F (225°C).
- Advantages: Exceptional chemical resistance, high-temperature resistance, and durability.
- Applications: Commonly used in oil and gas, automotive, chemical processing, and aerospace industries.
3. Perfluoroelastomer (FFKM):
- Temperature Range: Certain FFKM CanRez blends can handle temperatures up to 635°F (335°C) and excursions to even higher temperatures.
- Advantages: Excellent high-temperature and ultimate chemical resistance, low outgassing, and low permeability.
- Applications: Used in demanding high-temperature and chemical environments, such as semiconductor manufacturing and oil and gas.
4. Fluorosilicone (FVMQ):
- Temperature Range: FVMQ materials can handle temperatures up to 356°F (180°C).
- Advantages: Good high-temperature resistance, flexibility, and resistance to oils and fuels.
- Applications: Suitable for aerospace, automotive, and other applications where a combination of temperature and chemical resistance is required.
The best O-ring material for high-temperature applications varies depending on the specific temperature range, chemical exposure, pressure, and other environmental factors. It's essential to consult with a material expert or O-ring manufacturer to select the most suitable material for your particular application to ensure optimal performance and longevity. Additionally, consider the specific grade and formulation of the elastomer material to match the requirements of your high-temperature application.
What is ACN in a polymer?
ACN in a polymer stands for Acrylonitrile content. It is a key component of copolymers, particularly in the production of synthetic rubbers and elastomers. Acrylonitrile is a monomer that is polymerized with other monomers, such as butadiene or styrene, to create a wide range of polymers with different properties.
The Acrylonitrile content in a polymer affects its characteristics and performance. In the context of synthetic rubbers like Nitrile rubber (NBR), which is also known as Buna-N, the Acrylonitrile content plays a crucial role in determining the material's properties, including:
1. Chemical Resistance: Higher Acrylonitrile content in NBR results in better resistance to oils, fuels, and chemicals. This makes NBR with higher Acrylonitrile content suitable for applications where exposure to petroleum-based fluids is common.
2. Temperature Resistance: The Acrylonitrile content influences the temperature range over which the polymer can perform effectively. Higher Acrylonitrile content provides worse performance in low temperature applications.
3. Flexibility and Softness: Lower Acrylonitrile content results in softer and more flexible materials, while higher Acrylonitrile content makes the material stiffer.
4. Cost: The cost of the polymer may vary with the Acrylonitrile content, with higher Acrylonitrile content versions often being more expensive.
In summary, ACN in a polymer, especially in the context of NBR or other copolymers, is a critical factor in tailoring the material's properties to meet specific application requirements, particularly in terms of chemical resistance and temperature performance.
What is another name for Buna Rubber?
Buna rubber is commonly known as Nitrile rubber or NBR (Nitrile Butadiene Rubber). This synthetic rubber is a copolymer of acrylonitrile and butadiene. The name "Buna" originates from the first few letters of butadiene and natrium (sodium, in Latin), indicating the material's origins in sodium-catalyzed polymerization processes. Nitrile rubber is widely used in various applications due to its excellent resistance to oils, fuels, and certain chemicals. Some common trade names include: CHEMIGUM®, HYCAR®, PARACRIL® , PERBUNAN®, KRYNAC®, NYSYSN®.
What is better, EPDM or Buna?
Whether Nitrile or EPDM is "better" depends largely on the specific application and environmental conditions they are intended for. Both Nitrile and EPDM have distinct properties that make them suitable for different uses. Here's a comparison to help determine which might be more appropriate for a given situation:
1. Oil and Fuel Resistance:
- Nitrile: Excellent resistance to oils, fuels, and other hydrocarbons. This makes it a preferred choice for automotive and industrial applications involving oil and petroleum-based products.
- EPDM: Poor resistance to oil and fuel. It is not suitable for applications involving petroleum products.
2. Weather and UV Resistance:
- Nitrile: Good resistance to weather, but not as strong as EPDM. It can degrade with prolonged exposure to UV rays.
- EPDM: Outstanding resistance to weather, UV radiation, and ozone. Ideal for outdoor applications.
3. Heat Resistance:
- Nitrile: Generally good heat resistance, but typically not as high as EPDM. It can handle temperatures up to about 275°F (135°C).
- EPDM: Excellent heat resistance, often used in applications with temperatures up to 300°F (150°C) and sometimes higher.
4. Chemical Resistance:
- Nitrile: Good resistance to many chemicals, especially hydrocarbons, oils, and fats.
- EPDM: Excellent resistance to a wide range of chemicals, including certain acids, alkalis, and ketones, but not suitable for exposure to oils and fuels.
5. Application Examples:
- Nitrile: Often used in seals, gaskets, hoses, and O-rings in automotive, oil and gas, and mechanical applications.
- EPDM: Commonly used in weather seals, roofing membranes, electrical insulation, and automotive cooling systems.
6. Cost:
- The cost can vary, but generally, Nitrile is less expensive than EPDM, making it a cost-effective option for applications that don't require the superior weather and heat resistance of EPDM.
In summary, the choice between Nitrile and EPDM depends on the specific requirements of your application. For environments involving oils and fuels, Nitrile is the better choice. For applications that demand high weather, UV, and heat resistance, EPDM is preferable. Always consider the environmental conditions and chemical exposures that the material will face to make the most appropriate selection.
What is better, Nitrile or Viton?
Choosing between Buna-N (Nitrile rubber) and Viton (a brand of FKM, fluoroelastomer) depends on the specific requirements of your application. Each material has its advantages and limitations, so the choice should be based on factors like chemical resistance, temperature range, and cost. Here's a comparison:
1. Chemical Resistance:
- Buna-N: Buna-N is excellent for resistance to oils, fuels, and petroleum-based fluids. It performs well in applications where exposure to these substances is common.
- Viton: Viton is superior in terms of chemical resistance, especially for a broader range of chemicals, including more aggressive acids and solvents. It excels in applications with harsh chemical environments.
2. Temperature Range:
- Buna-N: Buna-N has a moderate temperature range, typically from -40°C to 108°C (-40°F to 226°F).
- Viton: Viton can handle higher temperatures, usually up to 200°C (392°F), making it suitable for high-temperature applications.
3. Cost:
- Buna-N: Generally more cost-effective compared to Viton. It provides good performance at a lower cost.
- Viton: Viton is more expensive due to its superior chemical resistance and higher temperature tolerance.
4. Applications:
- Buna-N: Commonly used in automotive, industrial, and manufacturing applications where exposure to oils, fuels, and petroleum-based fluids is frequent.
- Viton: Preferred in applications where a higher level of chemical resistance is required, such as in the chemical processing industry, aerospace, and situations involving aggressive chemicals.
5. Environmental Resistance:
- Buna-N: Better suited for applications involving oils and hydrocarbons.
- Viton: Better for applications involving a wider range of chemicals and high-temperature environments.
In summary, Buna-N is a cost-effective choice for applications involving oils and fuels, whereas Viton is preferred for applications with a broader range of chemicals and higher-temperature requirements. The specific choice depends on your application's needs, and it's essential to consider factors like chemical exposure, temperature extremes, and budget when making the decision.
What is Buna-N rubber less resistant to?
Buna-N rubber (Nitrile rubber or NBR) is an excellent elastomer with many valuable properties, including resistance to various substances. However, it has some limitations and is less resistant to certain materials and conditions. Here are some substances and factors to which Buna-N rubber is less resistant:
1. Low-Temperature Flexibility: While Buna-N has a relatively wide temperature range, it is less flexible at extremely low temperatures compared to elastomers like Silicone or EPDM.
2. Ozone and UV Exposure: Buna-N is less resistant to prolonged exposure to ozone and UV radiation compared to some other elastomers like EPDM. Over time, ozone and UV exposure can cause degradation and cracking of Buna-N rubber.
3. Acids: Buna-N is generally resistant to mild acids but is less resistant to strong acids, especially concentrated acids like sulfuric acid and nitric acid. It can experience swelling and degradation when exposed to certain aggressive acids.
4. Ketones: Buna-N is less resistant to ketones, which are organic compounds often found in solvents and industrial chemicals. Ketones can cause swelling and deterioration of Buna-N rubber.
5. Aromatic Hydrocarbons: Buna-N is less resistant to some aromatic hydrocarbons, such as benzene and toluene, which are found in certain fuels and chemicals. Prolonged exposure to these substances can cause deterioration of Buna-N.
6. Polar Solvents: Buna-N is less resistant to polar solvents like acetone and methyl ethyl ketone (MEK) compared to non-polar solvents. These solvents can cause swelling and reduced performance of Buna-N rubber.
7. High-Temperature Applications: While Buna-N can handle moderately high temperatures, it is less suitable for extremely high-temperature applications compared to elastomers like Viton, which can withstand higher temperature ranges.
It's essential to consider the specific requirements of your application and the substances or conditions it will be exposed to when selecting the appropriate elastomer material. In situations where Buna-N's limitations are a concern, alternative elastomers with better resistance to these specific factors may be preferred.
What is the ACN content of HNBR Rubber?
HNBR (Hydrogenated Nitrile Butadiene Rubber) is a synthetic elastomer known for its excellent resistance to heat, oil, and chemicals. The ACN (Acrylonitrile) content of HNBR rubber can vary depending on the specific formulation and application requirements. HNBR rubber typically has an ACN content ranging from 17% to 50%. The percentage of ACN in HNBR affects its physical properties, including its oil resistance, temperature resistance, and chemical resistance.
Here's a general overview of how ACN content can influence the properties of HNBR rubber:
1. Low ACN (26%-34%): HNBR with a lower ACN content tends to have better low-temperature flexibility but decreased resistance to automotive engine oils and transmission fluids.
2. Medium ACN (34%-40%): HNBR with a medium ACN content strikes a balance between low-temperature flexibility and resistance to oils and chemicals. It is often used in automotive seals, O-rings, and gaskets.
3. High ACN (40%-50%): HNBR with a higher ACN content offers excellent resistance to a wide range of chemicals, including acids, bases, and a variety of solvents. It is commonly used in applications where chemical resistance is critical, such as seals for downhole oil and gas equipment. It's low temperature performance tends to be worse.
The choice of HNBR with a specific ACN content depends on the intended application and the required combination of properties. Engineers and manufacturers select the appropriate ACN content to ensure that HNBR rubber performs optimally in their specific environments and conditions.
What is the ACN content of Nitrile Rubber?
The Acrylonitrile Content (ACN) of Nitrile Rubber (NBR) can vary depending on the specific formulation of the rubber. NBR is a copolymer of butadiene and acrylonitrile, and the ratio of these two monomers determines the ACN content in NBR.
Typically, NBR rubber can have ACN content ranging from approximately 18% to 50%. The ACN content is a critical factor that influences the properties of NBR, including its oil and fuel resistance. Generally, higher ACN content results in better resistance to oils and fuels, but it can reduce the rubber's flexibility and low-temperature performance.
The specific ACN content of a particular NBR compound is usually specified by the manufacturer or supplier of the rubber material. It's important to know the ACN content when selecting NBR for a specific application, as it helps determine the material's compatibility with the intended environment and the level of resistance it provides against various chemicals.
What is the best O-ring for gasoline?
When selecting an O-ring for use with gasoline, the key factors to consider are the O-ring's resistance to gasoline (including any additives in the fuel), its ability to maintain integrity at various temperatures, and its compatibility with other environmental factors it may encounter. The most commonly recommended materials for O-rings used with gasoline are:
1. Viton (Fluorocarbon, FKM): Viton is often considered one of the best materials for gasoline applications due to its excellent resistance to hydrocarbons, including gasoline and its additives. It maintains its properties over a wide temperature range and offers good resistance to aging and weathering. This makes it a preferred choice for automotive fuel handling systems.
2. Nitrile (Buna-N, NBR): Nitrile rubber is another popular choice for gasoline applications, especially when cost is a consideration. It has good resistance to oils and fuels, including gasoline. However, it may not perform as well as Viton in high-temperature environments or when exposed to certain additives in modern fuels.
3. Ethylene Propylene Diene Monomer (EPDM): While EPDM has excellent resistance to weathering, ozone, and aging, its compatibility with gasoline is generally poor. It's not typically recommended for use with gasoline or petroleum-based fluids.
4. Neoprene (Chloroprene, CR): Neoprene has moderate resistance to gasoline but is generally less preferred than Viton or Nitrile for this application. It's more commonly used in environments where resistance to weathering and ozone is a priority.
5. Silicone: Silicone O-rings are not recommended for use with gasoline. They have poor resistance to petroleum-based fuels and oils.
Summary
- Best Overall: Viton is often considered the best choice for gasoline applications due to its superior resistance to hydrocarbons and high temperatures.
- Cost-Effective Alternative: Nitrile is a good, less expensive alternative with acceptable resistance to gasoline but may not perform as well in extreme conditions compared to Viton.
It's important to ensure that the O-ring material is compatible not only with gasoline but also with any fuel additives that may be present. Additionally, always check the specifications and recommendations from the O-ring manufacturer or supplier for your specific application.
What is the difference between fluorocarbon O-rings and Nitrile O-rings?
Comparing Buna (often referred to as Nitrile or Buna-N) with Viton (a brand of fluoroelastomer) involves considering the specific requirements of the application, as each material has its strengths and weaknesses. Here’s a comparative analysis based on various factors:
1. Chemical Resistance:
- Viton: Exceptionally resistant to a wide range of chemicals, including oils, fuels, lubricants, and most mineral acids. It's superior in environments with harsh chemicals.
- Buna-N: Good resistance to oils and some chemicals, but not as broadly resistant as Viton, especially to strong acids and various solvents.
2. Temperature Resistance:
- Viton: Can withstand higher temperatures, generally between -15°F to 437°F (-26°C to 225°C), making it suitable for high-temperature applications.
- Buna-N: Has a decent temperature range but not as high as Viton, typically -40°F to 257°F (-40°C to 125°C).
3. Cost:
- Viton: Generally more expensive than Buna due to its superior performance in harsh environments and its more complex manufacturing process.
- Buna-N: More cost-effective, making it a preferred choice for applications where conditions do not demand Viton's high level of performance.
4. Physical Properties:
- Both materials have good physical properties like tensile strength and flexibility, but these can vary depending on the specific formulation.
5. Applications:
- Viton: Often used in automotive, aerospace, chemical processing, and industrial applications where high chemical and temperature resistance are required.
- Buna-N: Commonly used in automotive (particularly where oil resistance is needed), food handling, and general industrial applications where moderate resistance is sufficient.
6. Durability:
- Viton: Tends to have better longevity, especially in harsh chemical and thermal environments.
- Buna-N: While durable, it may not perform as well as Viton in extreme conditions but is sufficient for many standard applications.
In summary, whether Buna is "better" than Viton depends on the specific application requirements. Viton is superior in terms of chemical and temperature resistance, making it ideal for harsher environments, but it comes at a higher cost. Buna-N is a more cost-effective solution for applications that require good oil resistance and moderate temperature and chemical resistance. The decision should be based on balancing the performance requirements and budget constraints of your specific application.
What is the difference between NBR and HNBR O-rings?
NBR (Nitrile Butadiene Rubber) and HNBR (Hydrogenated Nitrile Butadiene Rubber) are both synthetic elastomers known for their excellent resistance to oil, fuel, and chemicals. However, they differ in their chemical structure and performance characteristics. Here are the key differences between NBR and HNBR:
1. Chemical Structure:
- NBR: NBR is a copolymer of butadiene and acrylonitrile. It contains a nitrile group in its chemical structure, which provides oil and fuel resistance. The acrylonitrile content in NBR can vary, affecting its overall properties.
- HNBR: HNBR is a modified version of NBR. It is also a copolymer of butadiene and acrylonitrile, but it undergoes hydrogenation, which involves the addition of hydrogen atoms to the polymer chain. This hydrogenation process enhances its resistance to heat, ozone, and chemicals.
2. Oil and Fuel Resistance:
- NBR: NBR offers good oil and fuel resistance and is commonly used in applications involving petroleum-based oils, fuels, and lubricants.
- HNBR: HNBR provides excellent oil and fuel resistance, often surpassing the performance of standard NBR. It is preferred in applications where exposure to automotive engine oils and transmission fluids is common.
3. Temperature Range:
- Buna-N (NBR) has a temperature range of approximately -40°F to 257°F (-40°C to 125°C), which is generally lower than HNBR.
- HNBR has a higher temperature resistance compared to standard NBR. It can typically handle temperatures ranging from -40°F to 329°F (-40°C to 165°C) or higher, depending on the specific grade.
4. Chemical Resistance:
- NBR: NBR exhibits good resistance to many chemicals but may not perform as well as HNBR in highly aggressive chemical environments.
- HNBR: HNBR offers excellent chemical resistance to a broader range of chemicals, acids, and solvents compared to NBR.
5. Ozone and Weathering Resistance:
- NBR: NBR is susceptible to ozone and weathering degradation over time.
- HNBR: HNBR has improved resistance to ozone and weathering due to its hydrogenated structure.
6. Applications:
- NBR: NBR is commonly used in automotive seals, O-rings, gaskets, and hoses, especially in applications involving petroleum-based fluids.
- HNBR: HNBR is preferred in automotive applications where exposure to engine oils and transmission fluids is significant. It is also used in chemical processing, oil and gas industry, and other applications requiring enhanced chemical and temperature resistance.
In summary, while both NBR and HNBR offer good oil and fuel resistance, HNBR provides superior performance in terms of temperature resistance, chemical resistance, and resistance to ozone and weathering. The choice between the two depends on the specific requirements of the application, with HNBR being the preferred choice in demanding environments.
What is the difference between NBR and HNBR?
NBR (Nitrile Butadiene Rubber) and HNBR (Hydrogenated Nitrile Butadiene Rubber) are both synthetic elastomers known for their excellent resistance to oil, fuel, and chemicals. However, they differ in their chemical structure and performance characteristics. Here are the key differences between NBR and HNBR:
1. Chemical Structure:
- NBR: NBR is a copolymer of butadiene and acrylonitrile. It contains a nitrile group in its chemical structure, which provides oil and fuel resistance. The acrylonitrile content in NBR can vary, affecting its overall properties.
- HNBR: HNBR is a modified version of NBR. It is also a copolymer of butadiene and acrylonitrile, but it undergoes hydrogenation, which involves the addition of hydrogen atoms to the polymer chain. This hydrogenation process enhances its resistance to heat, ozone, and chemicals.
2. Oil and Fuel Resistance:
- NBR: NBR offers good oil and fuel resistance and is commonly used in applications involving petroleum-based oils, fuels, and lubricants.
- HNBR: HNBR provides excellent oil and fuel resistance, often surpassing the performance of standard NBR. It is preferred in applications where exposure to automotive engine oils and transmission fluids is common.
3. Temperature Range:
- Buna-N (NBR) has a temperature range of approximately -40°F to 257°F (-40°C to 125°C), which is generally lower than HNBR.
- HNBR has a higher temperature resistance compared to standard NBR. It can typically handle temperatures ranging from -40°F to 329°F (-40°C to 165°C) or higher, depending on the specific grade.
4. Chemical Resistance:
- NBR: NBR exhibits good resistance to many chemicals but may not perform as well as HNBR in highly aggressive chemical environments.
- HNBR: HNBR offers excellent chemical resistance to a broader range of chemicals, acids, and solvents compared to NBR.
5. Ozone and Weathering Resistance:
- NBR: NBR is susceptible to ozone and weathering degradation over time.
- HNBR: HNBR has improved resistance to ozone and weathering due to its hydrogenated structure.
6. Applications:
- NBR: NBR is commonly used in automotive seals, O-rings, gaskets, and hoses, especially in applications involving petroleum-based fluids.
- HNBR: HNBR is preferred in automotive applications where exposure to engine oils and transmission fluids is significant. It is also used in chemical processing, oil and gas industry, and other applications requiring enhanced chemical and temperature resistance.
In summary, while both NBR and HNBR offer good oil and fuel resistance, HNBR provides superior performance in terms of temperature resistance, chemical resistance, and resistance to ozone and weathering. The choice between the two depends on the specific requirements of the application, with HNBR being the preferred choice in demanding environments.
What is the difference between Nitrile and HNBR?
NBR (Nitrile Butadiene Rubber) and HNBR (Hydrogenated Nitrile Butadiene Rubber) are both synthetic elastomers known for their excellent resistance to oil, fuel, and chemicals. However, they differ in their chemical structure and performance characteristics. Here are the key differences between NBR and HNBR:
1. Chemical Structure:
- NBR: NBR is a copolymer of butadiene and acrylonitrile. It contains a nitrile group in its chemical structure, which provides oil and fuel resistance. The acrylonitrile content in NBR can vary, affecting its overall properties.
- HNBR: HNBR is a modified version of NBR. It is also a copolymer of butadiene and acrylonitrile, but it undergoes hydrogenation, which involves the addition of hydrogen atoms to the polymer chain. This hydrogenation process enhances its resistance to heat, ozone, and chemicals.
2. Oil and Fuel Resistance:
- NBR: NBR offers good oil and fuel resistance and is commonly used in applications involving petroleum-based oils, fuels, and lubricants.
- HNBR: HNBR provides excellent oil and fuel resistance, often surpassing the performance of standard NBR. It is preferred in applications where exposure to automotive engine oils and transmission fluids is common.
3. Temperature Range:
- Buna-N (NBR) has a temperature range of approximately -40°F to 257°F (-40°C to 125°C), which is generally lower than HNBR.
- HNBR has a higher temperature resistance compared to standard NBR. It can typically handle temperatures ranging from -40°F to 329°F (-40°C to 165°C) or higher, depending on the specific grade.
4. Chemical Resistance:
- NBR: NBR exhibits good resistance to many chemicals but may not perform as well as HNBR in highly aggressive chemical environments.
- HNBR: HNBR offers excellent chemical resistance to a broader range of chemicals, acids, and solvents compared to NBR.
5. Ozone and Weathering Resistance:
- NBR: NBR is susceptible to ozone and weathering degradation over time.
- HNBR: HNBR has improved resistance to ozone and weathering due to its hydrogenated structure.
6. Applications:
- NBR: NBR is commonly used in automotive seals, O-rings, gaskets, and hoses, especially in applications involving petroleum-based fluids.
- HNBR: HNBR is preferred in automotive applications where exposure to engine oils and transmission fluids is significant. It is also used in chemical processing, oil and gas industry, and other applications requiring enhanced chemical and temperature resistance.
In summary, while both NBR and HNBR offer good oil and fuel resistance, HNBR provides superior performance in terms of temperature resistance, chemical resistance, and resistance to ozone and weathering. The choice between the two depends on the specific requirements of the application, with HNBR being the preferred choice in demanding environments.
What is the most common type of O-ring?
The most common type of O-ring material used is Nitrile rubber, often referred to as NBR (Nitrile Butadiene Rubber) O-rings. NBR O-rings are widely used in various industries and applications due to their versatile properties and cost-effectiveness. Here are some reasons why NBR O-rings are commonly used:
1. Oil and Fuel Resistance: NBR O-rings exhibit excellent resistance to oils, fuels, and lubricants, making them ideal for sealing applications in automotive, machinery, and hydraulic systems.
2. Chemical Compatibility: NBR is compatible with a wide range of non-polar and polar chemicals, which makes it suitable for many industrial applications.
3. Temperature Range: NBR O-rings can perform effectively within a moderate temperature range, typically from -40°C (-40°F) to 125°C (257°F).
4. Cost-Effectiveness: NBR is relatively inexpensive compared to some other elastomer materials, making it a cost-effective choice for sealing solutions.
5. Availability: NBR O-rings are readily available in various sizes, shapes, and durometers, making them easy to source for a wide range of applications.
While NBR is the most common type of O-ring material, it's important to note that O-rings are available in a variety of materials, each with its own set of properties and suitability for specific applications. Depending on the requirements of the application, other types of O-ring materials, such as Viton (FKM), EPDM, silicone, and HNBR, may also be used to meet specific performance criteria such as temperature resistance, chemical compatibility, or durability. The choice of O-ring material should be based on the specific needs of the sealing application.
What is the shelf life of Buna O-rings?
The shelf life of Buna-N (Nitrile) O-rings can vary depending on several factors, including storage conditions and the specific formulation of the material. However, in general, Buna-N O-rings have a recommended shelf life of approximately 15 years when stored properly. Here are some key considerations:
1. Storage Conditions: Proper storage is crucial to extending the shelf life of Buna-N O-rings. They should be stored in a cool, dry, and dark environment, away from direct sunlight and heat sources. Exposure to high temperatures, humidity, and UV radiation can accelerate the aging process and reduce shelf life.
2. Packaging: O-rings should be stored in their original packaging or in sealed containers to protect them from environmental factors. Avoid leaving them exposed to the air for extended periods.
3. Quality of the Material: The quality of the Buna-N material itself can impact its shelf life. Higher-quality formulations may have a longer shelf life compared to lower-quality materials.
4. Manufacturing Date: It's important to keep track of the manufacturing date of the O-rings and use a "first-in, first-out" inventory management system to ensure that older O-rings are used before newer ones.
5. Regular Inspection: Even if O-rings are within their recommended shelf life, it's a good practice to inspect them periodically for signs of deterioration, such as hardening, cracking, or changes in color. If any of these signs are observed, it's advisable to replace the O-rings.
6. Usage Conditions: The intended application and conditions of use can also impact the shelf life. O-rings used in demanding or high-stress applications may have a shorter effective shelf life than those used in less demanding environments.
It's important to note that the recommended shelf life is a general guideline, and the actual lifespan of Buna-N O-rings can vary. To ensure the reliability of O-rings in critical applications, it's advisable to consult with Canyon Components engineers for specific shelf life recommendations based on specific material formulations and to follow proper storage and handling practices.
What is the strongest O-ring material?
The term "strongest" when referring to O-ring materials can mean different things depending on the specific requirements of the application, such as resistance to chemicals, temperature extremes, pressure, or wear and tear. There is no single "strongest" O-ring material that suits all applications; instead, the best material depends on the specific conditions the O-ring will be exposed to. Here are some materials considered strong in various aspects:
1. FKM (Fluoroelastomer, e.g., Viton): Known for excellent chemical resistance, especially to oils, fuels, and some acids, and high-temperature tolerance (up to about 225°C or 437°F). It is often considered one of the strongest materials in terms of chemical and heat resistance.
2. FFKM (Perfluoroelastomer, e.g., CanRez, Kalrez, Chemraz): Offers even higher chemical and temperature resistance than standard FKM. It can withstand temperatures up to 335°C (635°F) and almost all chemicals. FFKM O-rings are often used in extremely harsh chemical and thermal environments.
3. Nitrile Rubber (NBR, Buna-N): Offers excellent resistance to oils and petroleum-based fluids. It's a strong choice for applications involving oil and fuel exposure.
4. EPDM (Ethylene Propylene Diene Monomer): Has outstanding resistance to weathering, ozone, UV rays, and aging, as well as good heat and steam resistance. It's a strong material for outdoor and water/steam applications.
5. Silicone: Exhibits excellent flexibility and is resistant to extreme temperatures, both hot and cold. It's a strong choice for applications requiring temperature resistance over a wide range.
6. Polyurethane: Known for its excellent wear and tear resistance, making it a strong material for high-pressure hydraulic systems and applications involving abrasion.
Each of these materials has its strengths in specific areas, and the choice of material should be based on the application's requirements, including exposure to chemicals, temperature, pressure, and wear. In some highly demanding applications, specialized O-ring materials like FFKM might be necessary due to their superior resistance qualities, despite their higher cost.
What type of rubber is Buna?
Buna, also known as Buna-N, is a type of synthetic rubber. It is a copolymer of acrylonitrile and butadiene, and its full name is "Nitrile Butadiene Rubber" (NBR). Buna-N is one of the most commonly used elastomers due to its excellent resistance to oils, fuels, lubricants, and a wide range of chemicals. It is known for its versatility and is widely used in various industrial and automotive applications where resistance to oil and fuel is essential.
Which is better, Buna-N or Viton?
Choosing between Buna-N (Nitrile rubber) and Viton (a brand of FKM, fluoroelastomer) depends on the specific requirements of your application. Each material has its advantages and limitations, so the choice should be based on factors like chemical resistance, temperature range, and cost. Here's a comparison:
1. Chemical Resistance:
- Buna-N: Buna-N is excellent for resistance to oils, fuels, and petroleum-based fluids. It performs well in applications where exposure to these substances is common.
- Viton: Viton is superior in terms of chemical resistance, especially for a broader range of chemicals, including more aggressive acids and solvents. It excels in applications with harsh chemical environments.
2. Temperature Range:
- Buna-N: Buna-N has a moderate temperature range, typically from -40°C to 108°C (-40°F to 226°F).
- Viton: Viton can handle higher temperatures, usually up to 200°C (392°F), making it suitable for high-temperature applications.
3. Cost:
- Buna-N: Generally more cost-effective compared to Viton. It provides good performance at a lower cost.
- Viton: Viton is more expensive due to its superior chemical resistance and higher temperature tolerance.
4. Applications:
- Buna-N: Commonly used in automotive, industrial, and manufacturing applications where exposure to oils, fuels, and petroleum-based fluids is frequent.
- Viton: Preferred in applications where a higher level of chemical resistance is required, such as in the chemical processing industry, aerospace, and situations involving aggressive chemicals.
5. Environmental Resistance:
- Buna-N: Better suited for applications involving oils and hydrocarbons.
- Viton: Better for applications involving a wider range of chemicals and high-temperature environments.
In summary, Buna-N is a cost-effective choice for applications involving oils and fuels, whereas Viton is preferred for applications with a broader range of chemicals and higher-temperature requirements. The specific choice depends on your application's needs, and it's essential to consider factors like chemical exposure, temperature extremes, and budget when making the decision.
Which is better, Nitrile or EPDM?
Whether Nitrile or EPDM is "better" depends largely on the specific application and environmental conditions they are intended for. Both Nitrile and EPDM have distinct properties that make them suitable for different uses. Here's a comparison to help determine which might be more appropriate for a given situation:
1. Oil and Fuel Resistance:
- Nitrile: Excellent resistance to oils, fuels, and other hydrocarbons. This makes it a preferred choice for automotive and industrial applications involving oil and petroleum-based products.
- EPDM: Poor resistance to oil and fuel. It is not suitable for applications involving petroleum products.
2. Weather and UV Resistance:
- Nitrile: Good resistance to weather, but not as strong as EPDM. It can degrade with prolonged exposure to UV rays.
- EPDM: Outstanding resistance to weather, UV radiation, and ozone. Ideal for outdoor applications.
3. Heat Resistance:
- Nitrile: Generally good heat resistance, but typically not as high as EPDM. It can handle temperatures up to about 275°F (135°C).
- EPDM: Excellent heat resistance, often used in applications with temperatures up to 300°F (150°C) and sometimes higher.
4. Chemical Resistance:
- Nitrile: Good resistance to many chemicals, especially hydrocarbons, oils, and fats.
- EPDM: Excellent resistance to a wide range of chemicals, including certain acids, alkalis, and ketones, but not suitable for exposure to oils and fuels.
5. Application Examples:
- Nitrile: Often used in seals, gaskets, hoses, and O-rings in automotive, oil and gas, and mechanical applications.
- EPDM: Commonly used in weather seals, roofing membranes, electrical insulation, and automotive cooling systems.
6. Cost:
- The cost can vary, but generally, Nitrile is less expensive than EPDM, making it a cost-effective option for applications that don't require the superior weather and heat resistance of EPDM.
In summary, the choice between Nitrile and EPDM depends on the specific requirements of your application. For environments involving oils and fuels, Nitrile is the better choice. For applications that demand high weather, UV, and heat resistance, EPDM is preferable. Always consider the environmental conditions and chemical exposures that the material will face to make the most appropriate selection.
Which is better, Nitrile or Viton?
Comparing Buna (often referred to as Nitrile or Buna-N) with Viton (a brand of fluoroelastomer) involves considering the specific requirements of the application, as each material has its strengths and weaknesses. Here’s a comparative analysis based on various factors:
1. Chemical Resistance:
- Viton: Exceptionally resistant to a wide range of chemicals, including oils, fuels, lubricants, and most mineral acids. It's superior in environments with harsh chemicals.
- Buna-N: Good resistance to oils and some chemicals, but not as broadly resistant as Viton, especially to strong acids and various solvents.
2. Temperature Resistance:
- Viton: Can withstand higher temperatures, generally between -15°F to 437°F (-26°C to 225°C), making it suitable for high-temperature applications.
- Buna-N: Has a decent temperature range but not as high as Viton, typically -40°F to 257°F (-40°C to 125°C).
3. Cost:
- Viton: Generally more expensive than Buna due to its superior performance in harsh environments and its more complex manufacturing process.
- Buna-N: More cost-effective, making it a preferred choice for applications where conditions do not demand Viton's high level of performance.
4. Physical Properties:
- Both materials have good physical properties like tensile strength and flexibility, but these can vary depending on the specific formulation.
5. Applications:
- Viton: Often used in automotive, aerospace, chemical processing, and industrial applications where high chemical and temperature resistance are required.
- Buna-N: Commonly used in automotive (particularly where oil resistance is needed), food handling, and general industrial applications where moderate resistance is sufficient.
6. Durability:
- Viton: Tends to have better longevity, especially in harsh chemical and thermal environments.
- Buna-N: While durable, it may not perform as well as Viton in extreme conditions but is sufficient for many standard applications.
In summary, whether Buna is "better" than Viton depends on the specific application requirements. Viton is superior in terms of chemical and temperature resistance, making it ideal for harsher environments, but it comes at a higher cost. Buna-N is a more cost-effective solution for applications that require good oil resistance and moderate temperature and chemical resistance. The decision should be based on balancing the performance requirements and budget constraints of your specific application.
Which is better, Viton or Buna?
Choosing between Viton and Buna (also known as Nitrile rubber) depends on the specific application and environment in which the material will be used. Both have distinct properties that make them suitable for different purposes. Here's a comparison:
Viton (Fluorocarbon Elastomer)
1. Chemical Resistance: Excellent resistance to oils, fuels, lubricants, and most mineral acids. Also has good resistance to many aliphatic hydrocarbon fluids that act as solvents for other rubbers.
2. Temperature Range: Exceptionally good at high temperatures, withstanding temperatures up to about 437°F (225°C).
3. Aging/Weather Resistance: Excellent resistance to aging, ozone, sunlight, and weather.
4. Cost: Generally more expensive.
5. Applications: Ideal for automotive, aerospace, and industrial applications where resistance to high temperatures and chemicals is crucial.
Buna (Nitrile Rubber)
1. Chemical Resistance: Good resistance to oils, solvents, and greases. However, it is not recommended for use with highly polar solvents like acetone and methyl ethyl ketone, nor with chlorinated hydrocarbons.
2. Temperature Range: Good performance in temperatures ranging from -40°F to 257°F (-40°C to 125°C).
3. Aging/Weather Resistance: Good resistance to abrasion and aging, but inferior to Viton in terms of weather and ozone resistance.
4. Cost: Less expensive compared to Viton.
5. Applications: Commonly used in automotive applications (like fuel and oil handling hoses, seals, grommets), as well as in general industrial applications where fuel and oil resistance is needed.
Summary
- For High Temperature and Chemical Resistance: Viton is superior.
- For Cost-Effectiveness and General Oil Resistance: Buna is more suitable.
- Application Specific: Always consider the specific requirements of the application, including chemical exposure, temperature range, and budget constraints.
In conclusion, the better choice depends on the operational requirements of the application. Viton excels in extreme environments and with high chemical resistance needs, while Buna is more cost-effective for general industrial uses where extreme conditions are not a factor.
Who makes Buna O-rings?
Canyon Components carries a huge variety of Nitrile based seals, O-rings, gaskets, & custom molded parts and supplies thousands of customers in a diverse range of industries. Nitrile is the term used to describe a copolymer of acrylonitrile and butadiene. The amount of acrylonitrile used in the copolymer varies between compounds and has a profound effect on the mechanical and physical properties of the material, O-rings, gaskets, & custom molded parts. Generally, Nitrile O-rings, gaskets, & custom molded parts are very oil-resistant, have strong mechanical properties, are resistant to wear, and are relatively inexpensive. These properties make Nitrile the most commonly used general purpose O-ring, gasket, & custom molded part material.
Why is Viton so expensive?
Viton, a brand of synthetic rubber and fluoropolymer elastomer (FKM) commonly used in O-rings, seals, and other moulded or extruded goods, tends to be expensive due to several key factors:
1. Material Composition: Viton is made from fluoropolymer elastomers, which are more complex and costly to produce than conventional rubbers. The process requires specialized chemicals and technology, contributing to its higher cost.
2. Performance Characteristics: Viton exhibits exceptional resistance to heat, chemicals, and oil, which makes it suitable for demanding industrial applications. Its ability to maintain integrity under harsh conditions justifies its higher price compared to less durable materials.
3. Production Costs: The manufacturing process of Viton is more intricate and requires stricter quality control than ordinary rubber production. This increases the overall production costs.
4. Market Demand: Viton's unique properties make it essential for specific industries, like aerospace, automotive, and chemical processing. The specialized demand for such high-performance material can drive up its price.
5. Brand Recognition: As a well-known brand under the Chemours Company (formerly a part of DuPont), Viton's established reputation can also be a factor in its pricing.
6. Durability and Longevity: Products made from FKM tend to last longer than those made from other materials, which can make them more cost-effective in the long run, despite the higher initial cost.
In summary, Viton's high price is a reflection of its superior quality, durability, and the specialized manufacturing process required to produce it.