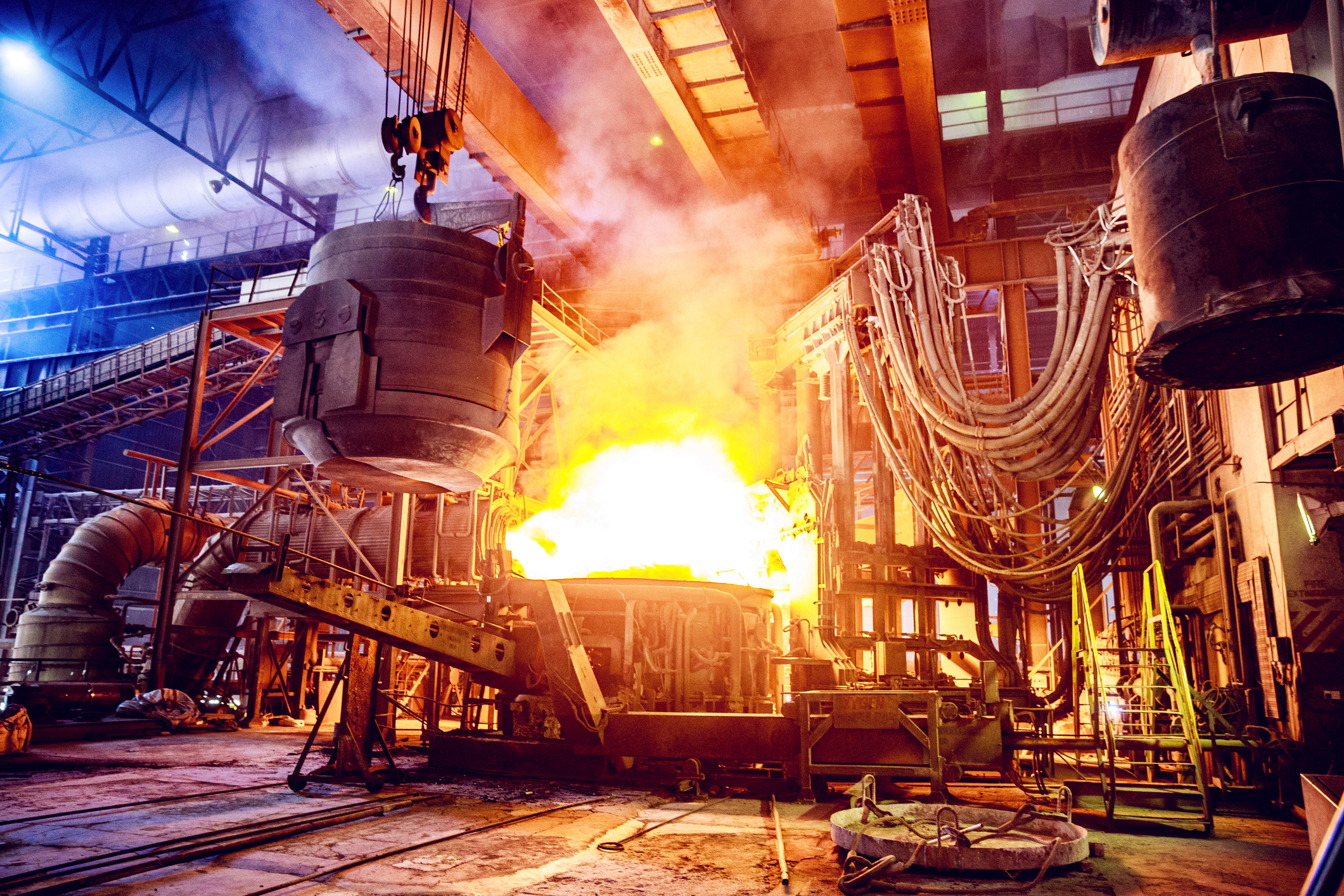
PEEK Plastic (Polyetheretherketone) Selection Guide
PEEK (Polyether Ether Ketone) is a high-performance thermoplastic polymer known for its exceptional mechanical properties, chemical resistance, and thermal stability. In this web page, we will explore the different types of PEEK, its numerous advantages and disadvantages, and the diverse industrial applications where PEEK plays a crucial role.
PEEK (Polyether Ether Ketone) rapid manufacturing, & custom molded parts are available now!
Check with one of Canyon’s helpful product engineers for an expert material and manufacturing recommendation.
Common names include: PEEK (Polyether Ether Ketone), Trade Names:
Victrex® PEEK, Ketron® PEEK, TECAPEEK®, Vestakeep®, Semitron® PEEK, KetaSpire® PEEK, SustaPEEK.
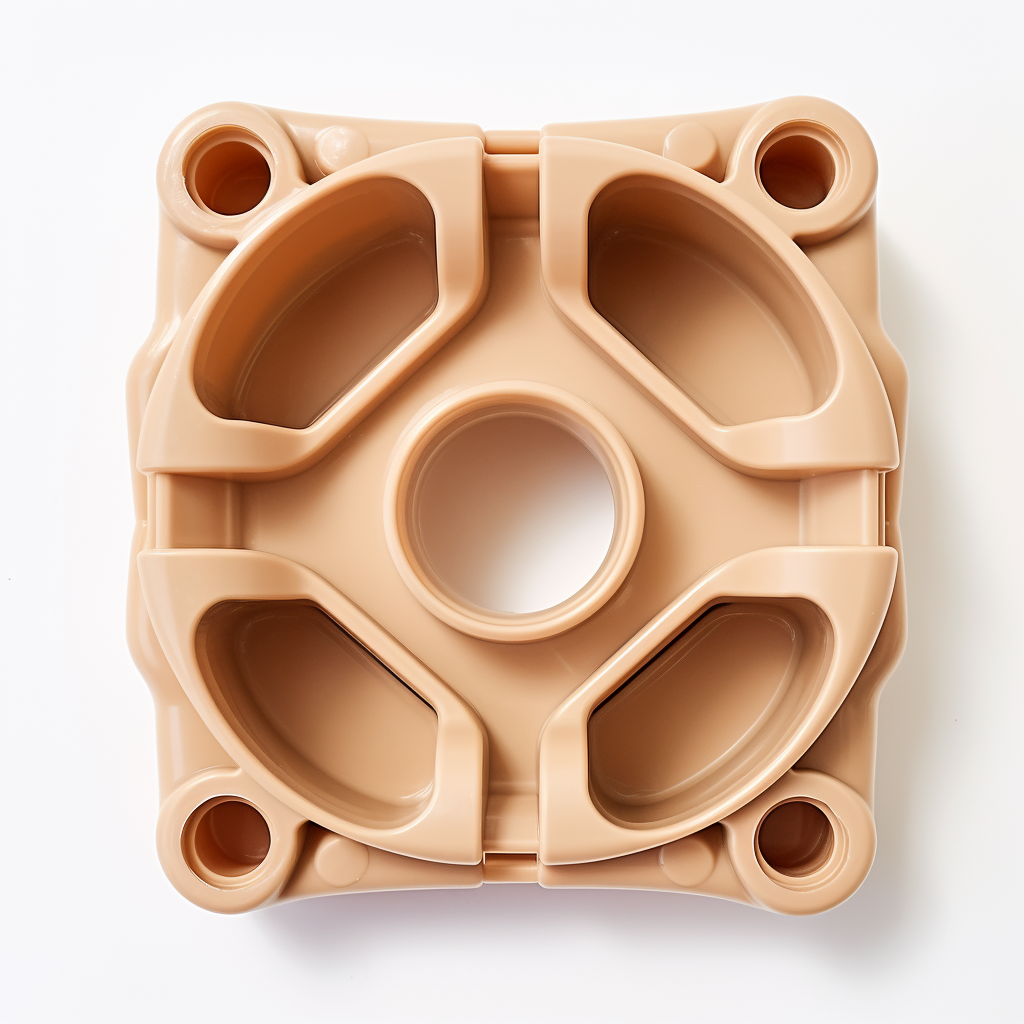
Advantages
- High Temperature Resistance: PEEK can withstand high temperatures, maintaining its properties even at temperatures above 250°C (482°F).
- Mechanical Strength: PEEK has exceptional mechanical properties, including high tensile strength, stiffness, and fatigue resistance.
- Chemical Resistance: PEEK is highly resistant to a wide range of chemicals, including acids, bases, and organic solvents.
- Electrical Insulation: PEEK is an excellent electrical insulator, making it suitable for electrical and electronics applications.
- Low Friction: PEEK has a low coefficient of friction, making it useful for applications where reduced wear and friction are important.
- Biocompatibility: PEEK is biocompatible and often used in medical implants and devices.
Disadvantages
- Cost: PEEK is relatively expensive compared to many other thermoplastics, which can limit its use in cost-sensitive applications.
- Processing Challenges: PEEK can be challenging to process due to its high melting point and high viscosity, requiring specialized equipment and expertise.
- Not Suitable for High-Radiation Environments: PEEK may degrade when exposed to high levels of ionizing radiation.
Common Applications of PEEK
- Aerospace: PEEK is used in aerospace applications for components like engine parts, seals, and aircraft interiors due to its lightweight nature and high temperature resistance.
- Medical: PEEK is employed in medical devices and implants, such as spinal implants and dental instruments, because of its biocompatibility and chemical resistance.
- Oil and Gas: PEEK is used in the oil and gas industry for downhole equipment, seals, and connectors due to its chemical resistance and high pressure/temperature capabilities.
- Automotive: PEEK is used in automotive components like bushings, bearings, and seals due to its mechanical strength and wear resistance.
- Electronics: PEEK is used for manufacturing electrical connectors, insulators, and semiconductor equipment due to its electrical insulating properties.
- Chemical Processing: PEEK is employed in chemical processing equipment, including pumps, valves, and gaskets, due to its chemical resistance.
- Food and Beverage: PEEK is used in food processing equipment, such as seals, bearings, and conveyor components, due to its low friction and resistance to food-related chemicals.
- Mechanical Engineering: PEEK is used for precision mechanical components like gears, bearings, and thrust washers due to its low friction and wear resistance.
Please consult a Canyon Components Engineer about your specific application and we will use our decades of experience to formulate a solution that fits your need.
Types of PEEK
PEEK can come in different variations, depending on its composition and intended use. Some common types of PEEK include the following.
Canyon Components strives to meet all customer service requests. Feel free to contact Canyon Components engineering and let our knowledgeable staff help you design the perfect part for your needs.
Unfilled PEEK
This pure form of PEEK (Polyether Ether Ketone) offers excellent mechanical and chemical resistance. It's widely used in demanding applications like aerospace, automotive, and medical implants due to its high strength, thermal stability, and biocompatibility. Unfilled PEEK is also known for its ease of machining and insulation properties.
Glass-Filled PEEK
Reinforced with glass fibers, Glass-Filled PEEK provides enhanced mechanical and thermal properties. It's ideal for industrial components requiring high rigidity and dimensional stability, such as precision bearings, piston parts, and pump housings. The glass fibers also improve its load-bearing capacity.
Carbon-Filled PEEK
Infused with carbon fibers, this variant offers increased strength and stiffness, along with superior wear and thermal resistance. Suitable for high-performance applications like aerospace components and high-stress mechanical parts, Carbon-Filled PEEK is also known for its lightweight and fatigue resistance.
Bearing Grade PEEK
Specifically designed for high-wear and friction applications, Bearing Grade PEEK includes additives like graphite, PTFE, or carbon fibers to enhance its bearing and wear properties. It's commonly used in high-speed bearings, seals, and gears where low friction and long service life are crucial.
Electrically Conductive PEEK
This type is modified to provide electrical conductivity, making it suitable for applications in the electronics industry, where static dissipation is essential. Electrically Conductive PEEK is used in semiconductor manufacturing, electronic packaging, and anti-static components.
Medical Grade PEEK
Meeting stringent biocompatibility requirements, Medical Grade PEEK is used in medical and dental applications. It's ideal for implants, surgical instruments, and orthopedic devices due to its radiolucent properties, compatibility with medical imaging, and resistance to sterilization processes.
Please consult a Canyon Components Engineer about your specific application and we will use our decades of experience to formulate a solution that fits your need.
Manufacturing Options for PEEK
PEEK parts can be manufactured using several methods, each suitable for different applications and part complexities.
Each of these methods has its own advantages, limitations, and cost implications. The choice of manufacturing technique usually depends on factors like the complexity of the design, required precision, material properties, and production volume.
Canyon Components strives to meet all customer service requests. Feel free to contact Canyon Components engineering and let our knowledgeable staff help you design the perfect part for your needs.
Back to Plastics Hub
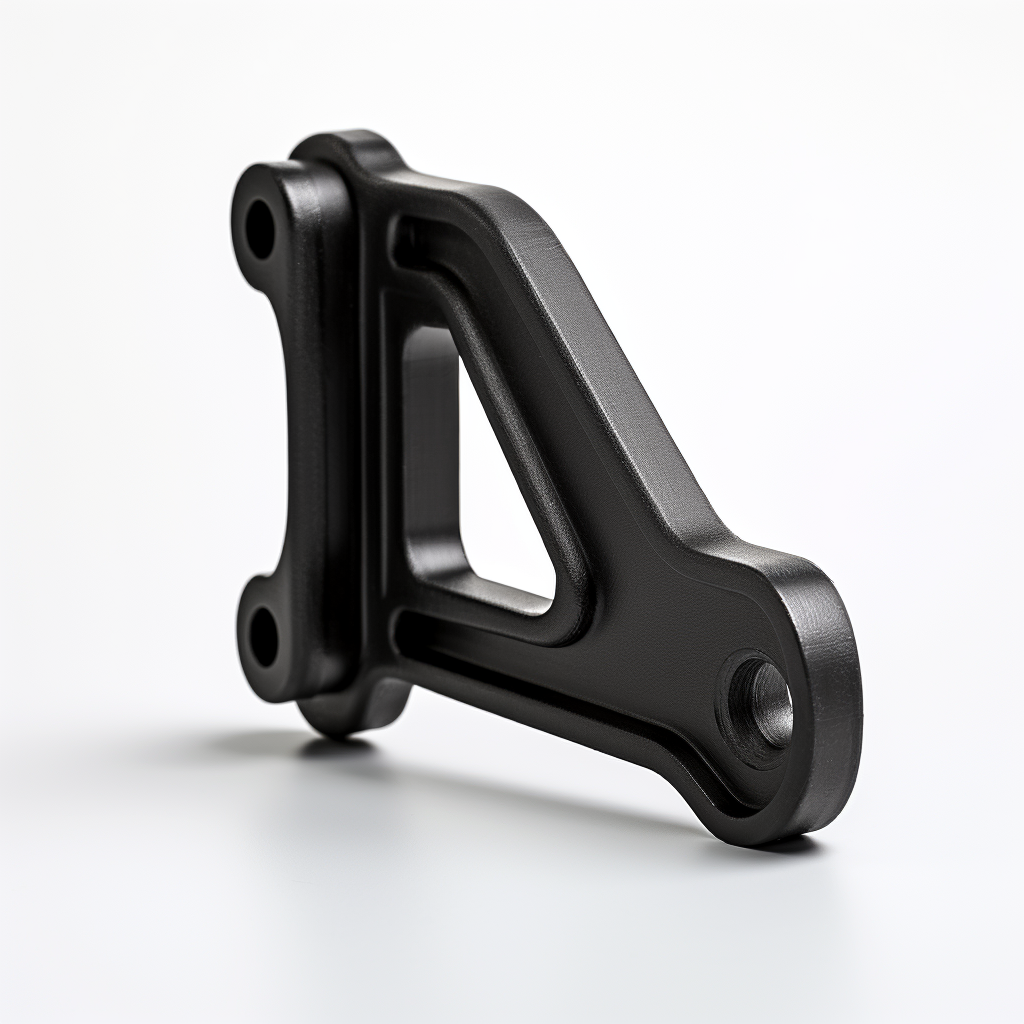
Get A Quote Now!
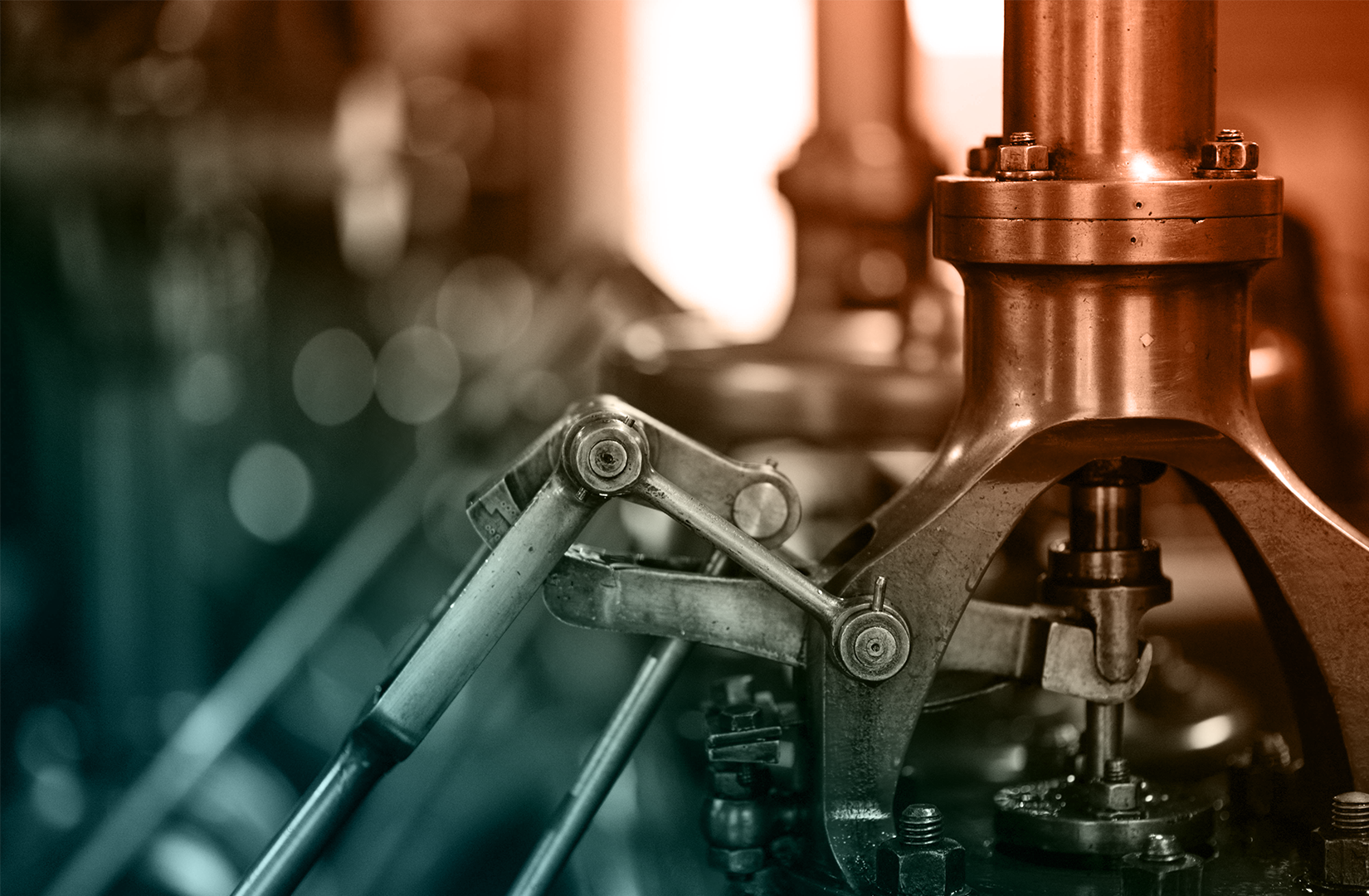
Groove Design References
Learn More
Coatings, Packaging, & Other Services
Learn More
Custom Parts & Custom O-rings
Learn More