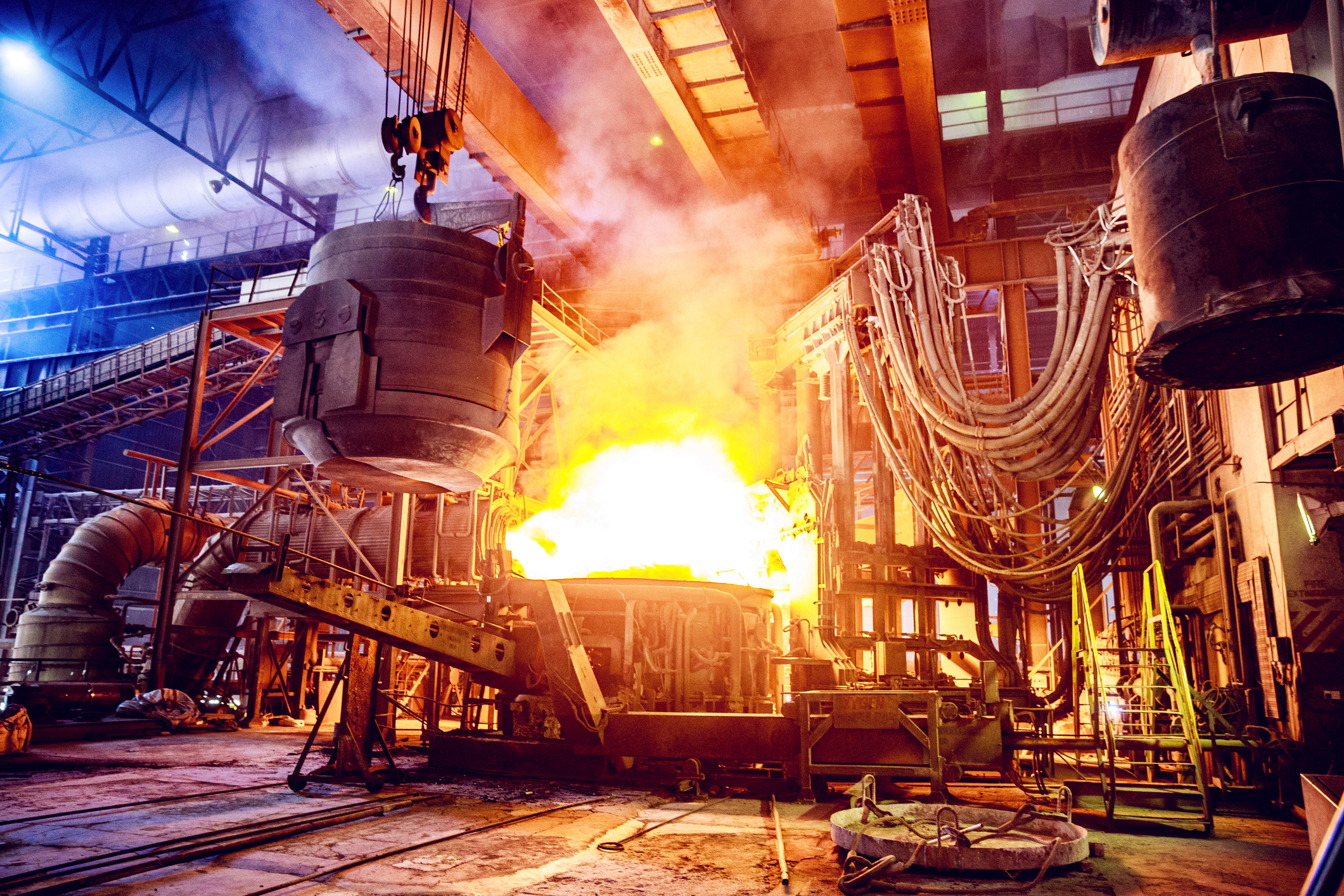
3D Printing
3D printing, also known as additive manufacturing, is a revolutionary process that constructs three-dimensional objects layer by layer from a digital model. It has transformed the way products are designed and fabricated across various industries. In this web page, we will explore the different types of 3D printing, their advantages and disadvantages, and the diverse industrial applications. Additionally, we'll provide a list of materials commonly used in 3D printing. Custom 3D Printed parts available now!
Check with one of Canyon’s helpful product engineers for an expert material and manufacturing recommendation.
Common terminology includes: Fused Deposition Modeling (FDM), Stereolithography (SLA), Selective Laser Sintering (SLS), Digital Light Processing (DLP), Multi Jet Fusion (MJF), Electron Beam Melting (EBM), Direct Metal Laser Sintering (DMLS), Binder Jetting, Material Jetting, Continuous Liquid Interface Production (CLIP).
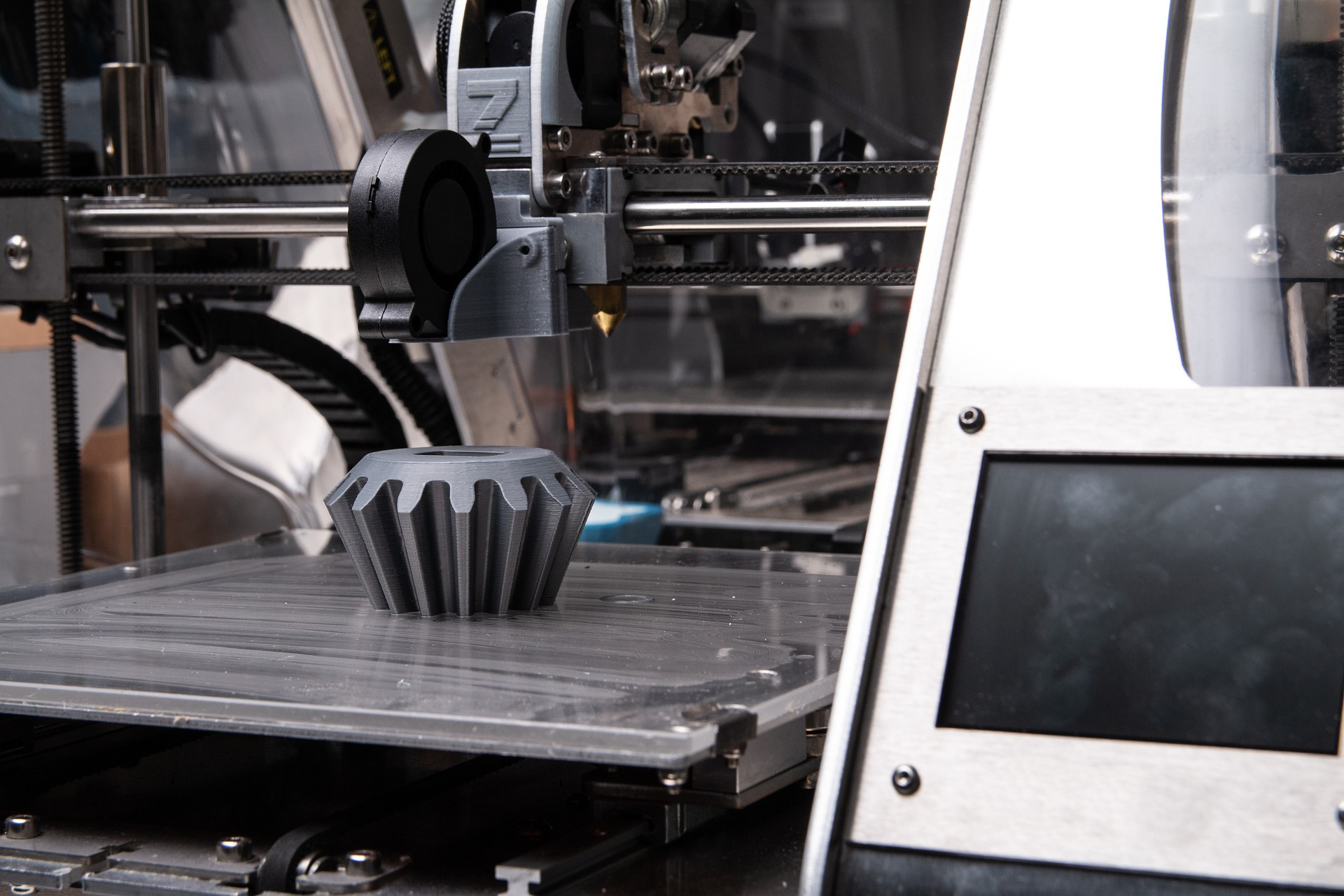
Advantages
- Rapid Prototyping: Enables quick and cost-effective design iterations.
- Complex Geometries: Creates intricate and customized parts that are challenging to manufacture using traditional methods.
- Material Efficiency: Minimizes waste, as only the necessary material is used.
- Customization: Ideal for producing one-off or low-volume customized parts.
- Reduced Lead Times: Significantly shortens production cycles compared to traditional manufacturing.
Disadvantages
- Material Limitations: Not all materials are suitable for 3D printing, and material properties may vary.
- Surface Finish: Achieving a smooth surface may require additional post-processing steps.
- Build Size Limitations: The size of objects that can be printed is constrained by the printer's build volume.
Common Applications of 3D Printing
- Aerospace: Manufacturing lightweight and complex aerospace components.
- Medical: Creating custom implants, prosthetics, and patient-specific surgical guides.
- Automotive: Prototyping, producing interior components, and customizing vehicles.
- Consumer Goods: Developing customized products, fashion items, and accessories.
- Architecture: Building scale models, creating intricate designs, and rapid prototyping.
Please consult a Canyon Components Engineer about your specific application and we will use our decades of experience to formulate a solution that fits your need.
Types of 3D Printing
3D Printing can be performed in a number of ways depending on the composition and intended use of the final product. Some variations available for 3D Printing include the following.
Canyon Components strives to meet all customer service requests. Feel free to contact Canyon Components engineering and let our knowledgeable staff help you design the perfect part for your needs.
Fused Deposition Modeling (FDM)
This popular 3D printing technique uses a thermoplastic filament, which is heated and extruded through a nozzle to build parts layer by layer. Advantages include ease of use and a wide range of material options. However, it often results in lower resolution and accuracy compared to other methods and has visible layer lines.
Stereolithography (SLA)
SLA uses a laser to cure liquid resin into solid plastic in a layer-by-layer fashion. It's known for high precision and smooth surface finishes, ideal for prototyping and detailed models. The downsides include the use of toxic resins, limited material options, and post-processing requirements.
Selective Laser Sintering (SLS)
SLS fuses small particles of polymer powder using a high-power laser. It offers strong parts with good complexity and does not require support structures. However, it has a limited color and finish range, and the post-processing can be extensive.
Digital Light Processing (DLP)
Similar to SLA, DLP cures liquid resin using projected light. It’s faster than SLA and produces parts with high accuracy. The main disadvantages are the brittle nature of the cured resin and limited size of the print area.
Multi Jet Fusion (MJF)
MJF spreads out a layer of powder and then selectively applies a detailing agent, which a heating element fuses. It’s fast and produces parts with consistent mechanical properties. However, it’s expensive and mostly limited to nylon material.
Direct Metal Laser Sintering (DMLS)
This technique uses a laser to fuse metal powder, ideal for complex, high-strength metal parts. Advantages include the ability to produce metal parts with complex geometries. The downsides are high costs, both in terms of machinery and materials, and the requirement for significant post-processing.
Please consult a Canyon Components Engineer about your specific application and we will use our decades of experience to formulate a solution that fits your need.
Request a Quote for 3D Printed Parts
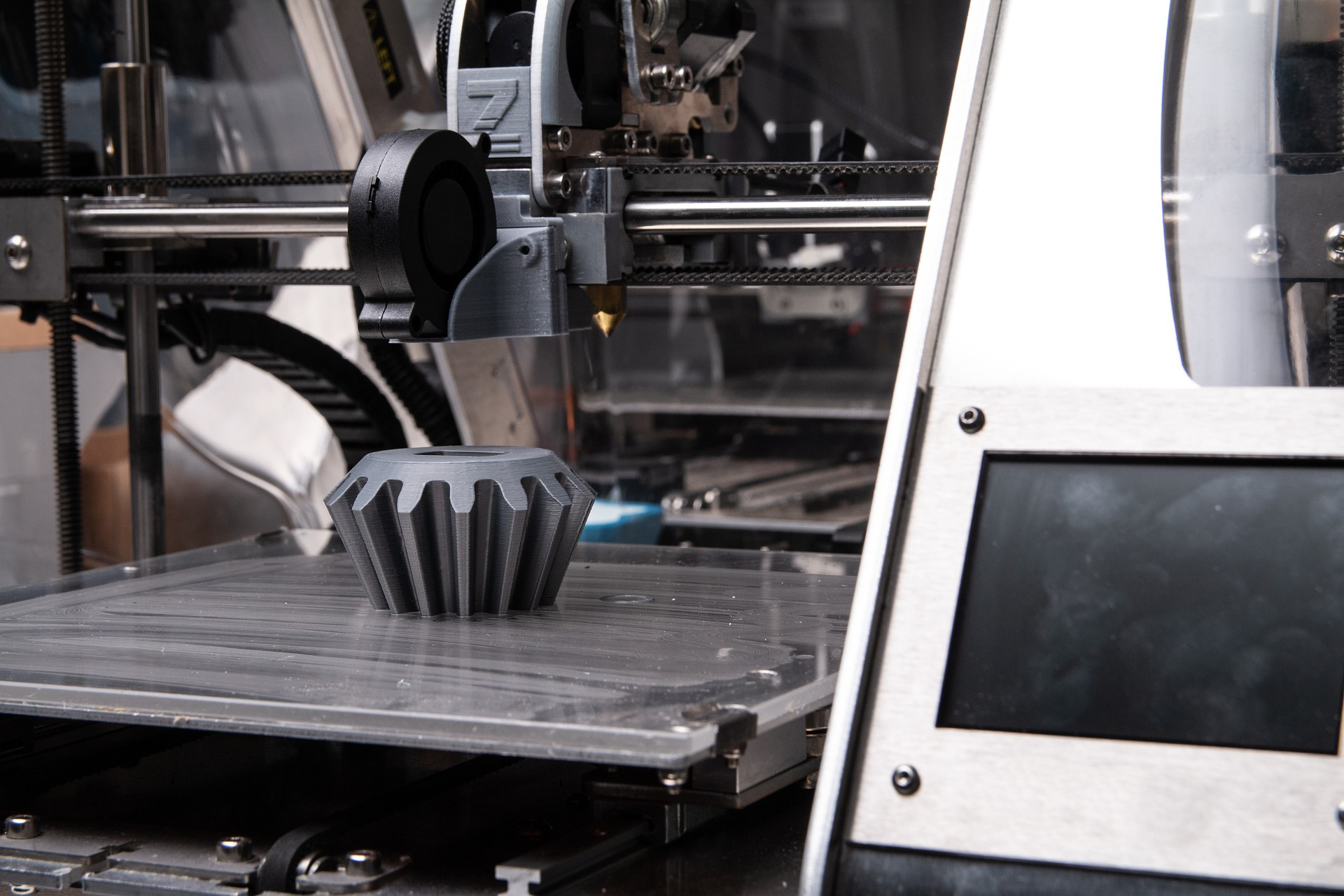
3D Printing Materials Available
3D Printing can be performed in a number of ways depending on the composition and intended use of the final product. Some common materials available for 3D Printing include the following.
Each of these materials has its own advantages, limitations, and cost implications. The choice of material and manufacturing technique usually depends on factors like the complexity of the design, required precision, material properties, and production volume.
Canyon Components strives to meet all customer service requests. Feel free to contact Canyon Components engineering and let our knowledgeable staff help you design the perfect part for your needs.
Plastics
Plastics are a broad class of synthetic or semi-synthetic materials known for their versatility and moldability. They are crucial in numerous applications due to their ability to be shaped, lightweight nature, and resistance to chemicals and moisture.
ABS (Acrylonitrile Butadiene Styrene)
ABS plastic, a thermoplastic polymer blend of acrylonitrile, butadiene, and styrene, is renowned for its toughness, impact resistance, and rigidity. It's easily machinable and ideal for automotive parts, consumer goods, and 3D printing due to its strength and versatility.
PEEK (Polyetheretherketone)
PEEK plastic, or polyether ether ketone, is a high-performance thermoplastic known for its exceptional heat resistance, chemical stability, and mechanical strength. It's widely used in aerospace, medical implants, and automotive industries for its durability and ability to withstand harsh environments.
PETG (Polyethylene Terephthalate Glycol)
PETG plastic, a glycol-modified version of polyethylene terephthalate, is valued for its clarity, excellent chemical resistance, and thermoformability. It's a popular choice for 3D printing, packaging, and medical devices due to its durability, impact resistance, and ease of fabrication.
PC (Polycarbonate)
Polycarbonate (PC) Plastic is a tough, transparent thermoplastic with exceptional impact resistance, heat tolerance, and optical clarity. Its versatility makes it ideal for bulletproof glass, eyewear lenses, medical devices, and protective gear, offering a unique balance of strength and lightweight properties.
Elastomers
Elastomers (also referred to as rubber) are a class of materials known for their unique ability to stretch, deform, and return to their original shape, making them essential in a wide range of applications.
Polyurethane (PU, AU)
Polyurethane O-rings, gaskets, & custom molded parts generally have two or three times greater tensile strength and wear resistance than Nitrile and comparable polymers. Polyurethane also provides excellent permeation resistance when compared to most rubbers.
Silicone (VMQ, PVMQ)
Silicone seals, O-rings, gaskets, & custom molded parts are excellent for extreme temperatures in static applications. Canyon Components carries a range of silicone materials, and we are happy to custom tailor a seal to meet your application requirements!
Metals
Metals are a class of materials distinguished by their conductive, malleable, and ductile properties. They are fundamental in various applications due to their ability to conduct electricity and heat, resist corrosion, and form alloys with other metals.
Titanium
Titanium is a lightweight, strong metal with a silvery-white appearance, known for its exceptional corrosion resistance and high strength-to-density ratio. Widely used in aerospace, medical implants, and sporting equipment, it forms alloys with elements like aluminum and vanadium.
Alloy Steel
Alloy steel is a robust metal composed of iron mixed with various elements like chromium, nickel, molybdenum, and vanadium. This combination enhances properties such as strength, hardness, durability, and corrosion resistance, making it ideal for diverse industrial applications.
Copper
Copper is a reddish-brown, highly ductile and conductive metal, renowned for its thermal and electrical conductivity. It's naturally antimicrobial and corrosion-resistant, extensively used in electrical wiring, plumbing, coinage, and as a component in various metal alloys.
Back to Manufacturing Hub
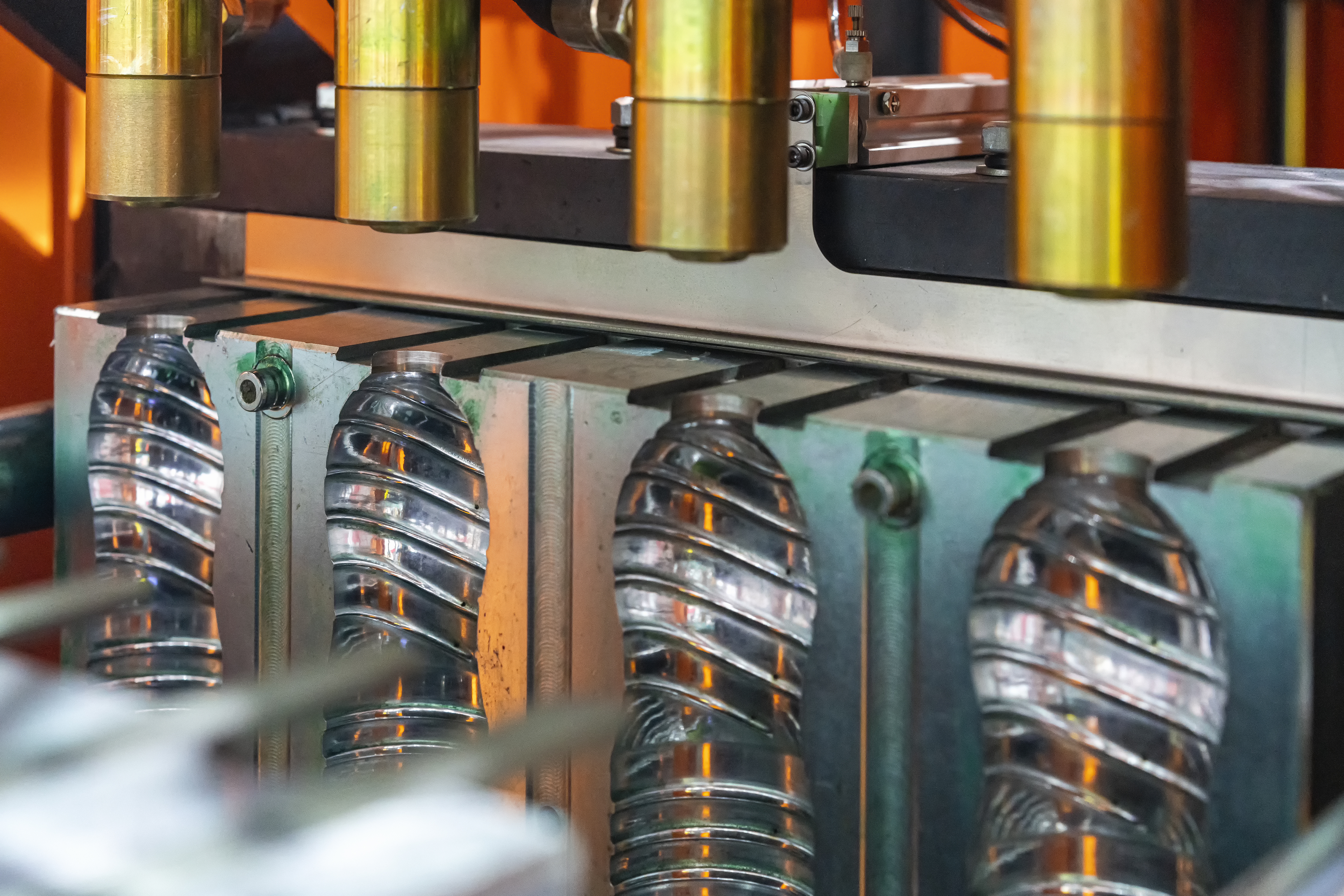
Get A Quote Now!
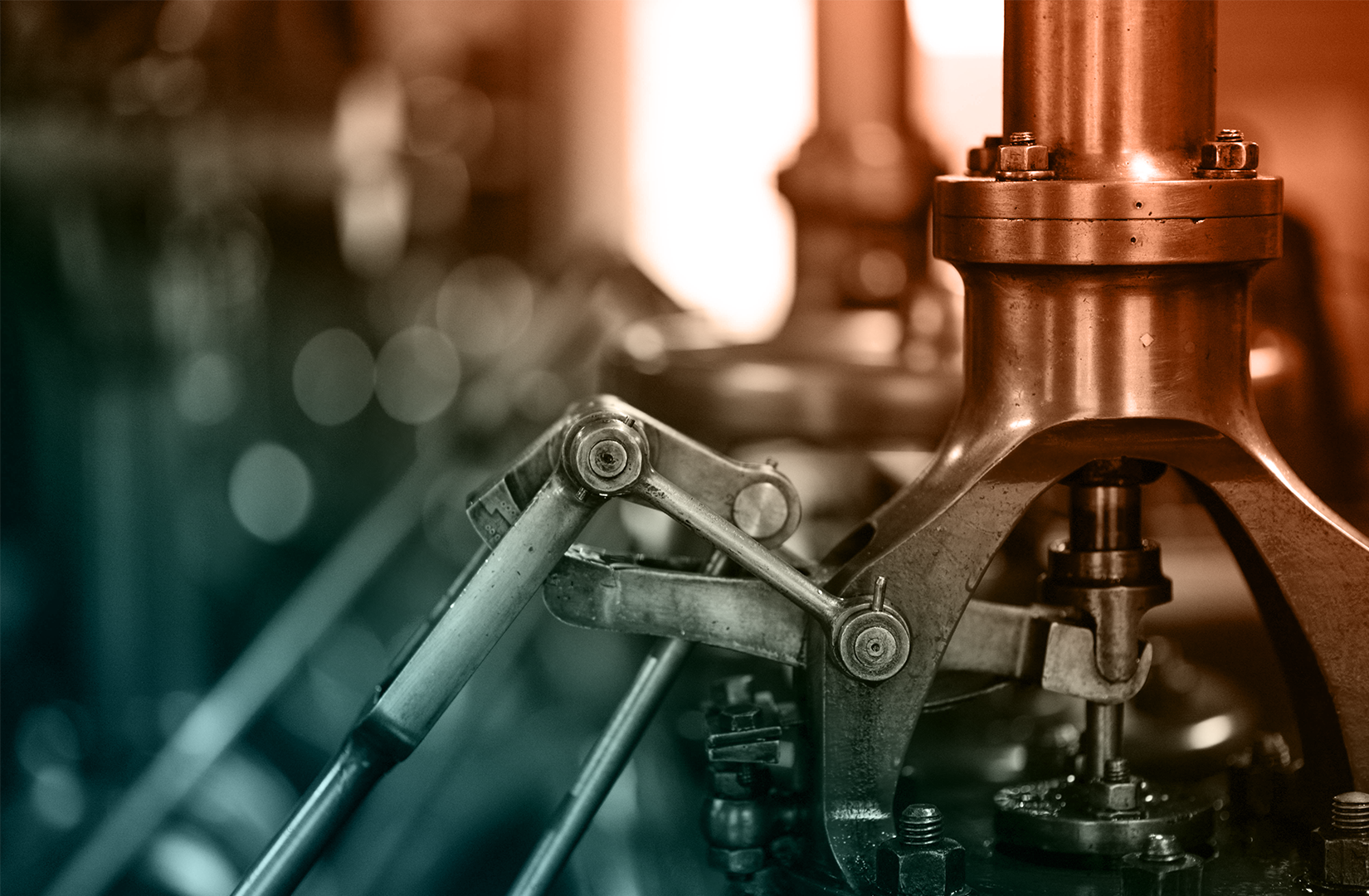
Groove Design References
Learn More
Coatings, Packaging, & Other Services
Learn More
Custom Parts & Custom O-rings
Learn More