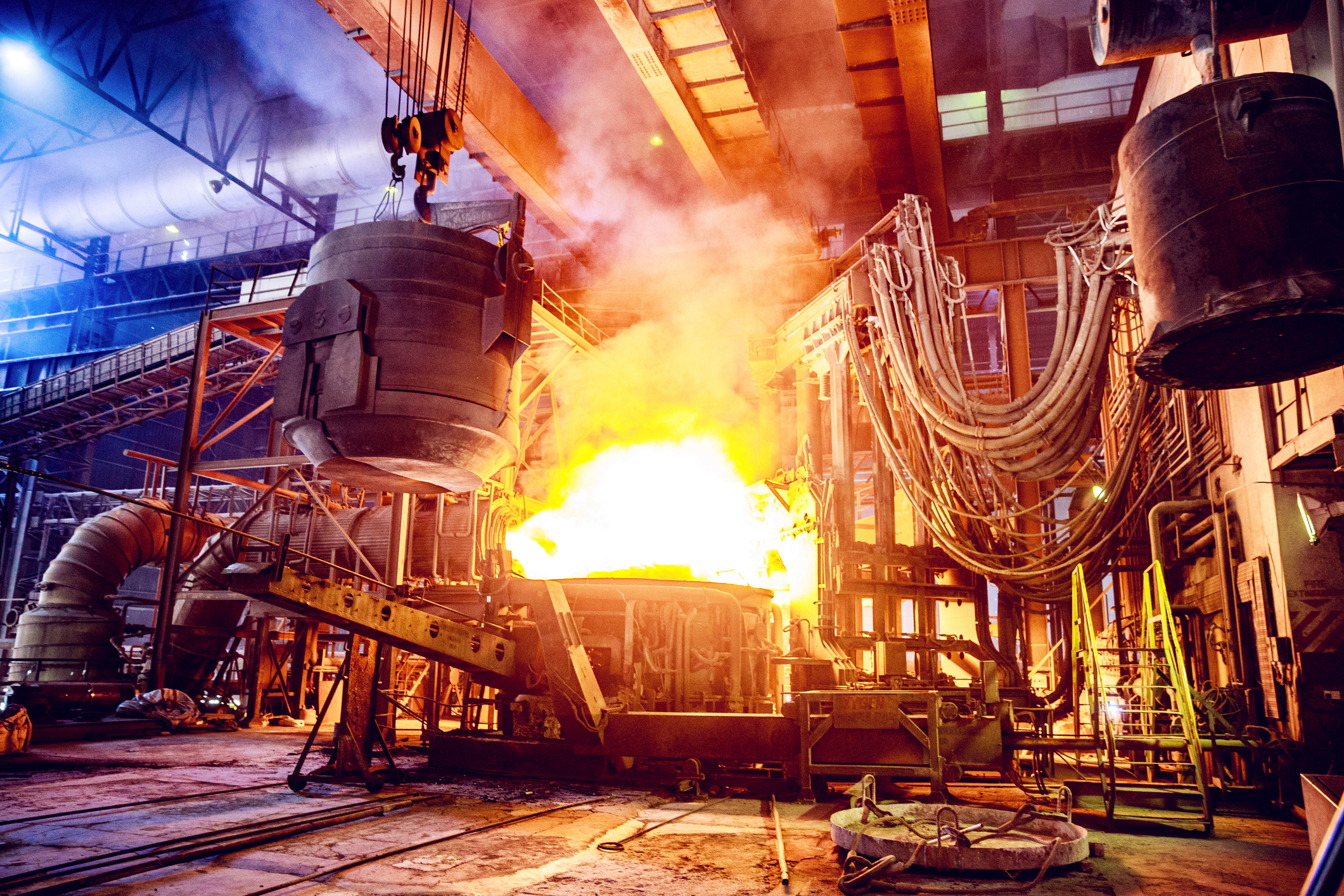
Extrusion
Extrusion manufacturing is a versatile process used to create objects of a fixed cross-sectional profile. It involves forcing a material through a die to produce continuous lengths of a specific shape. In this web page, we'll explore the different types of extrusion, their advantages and disadvantages, and the wide array of industrial applications. Additionally, we'll provide a list of materials commonly used in extrusion manufacturing. Custom Extruded parts available now!
Check with one of Canyon’s helpful product engineers for an expert material and manufacturing recommendation.
Common terminology includes: Plastic extrusion, aluminum extrusion, profile extrusion, sheet extrusion, tube extrusion, film extrusion, blow film extrusion, co-extrusion, cold extrusion, hot extrusion, twin-screw extrusion, single-screw extrusion.
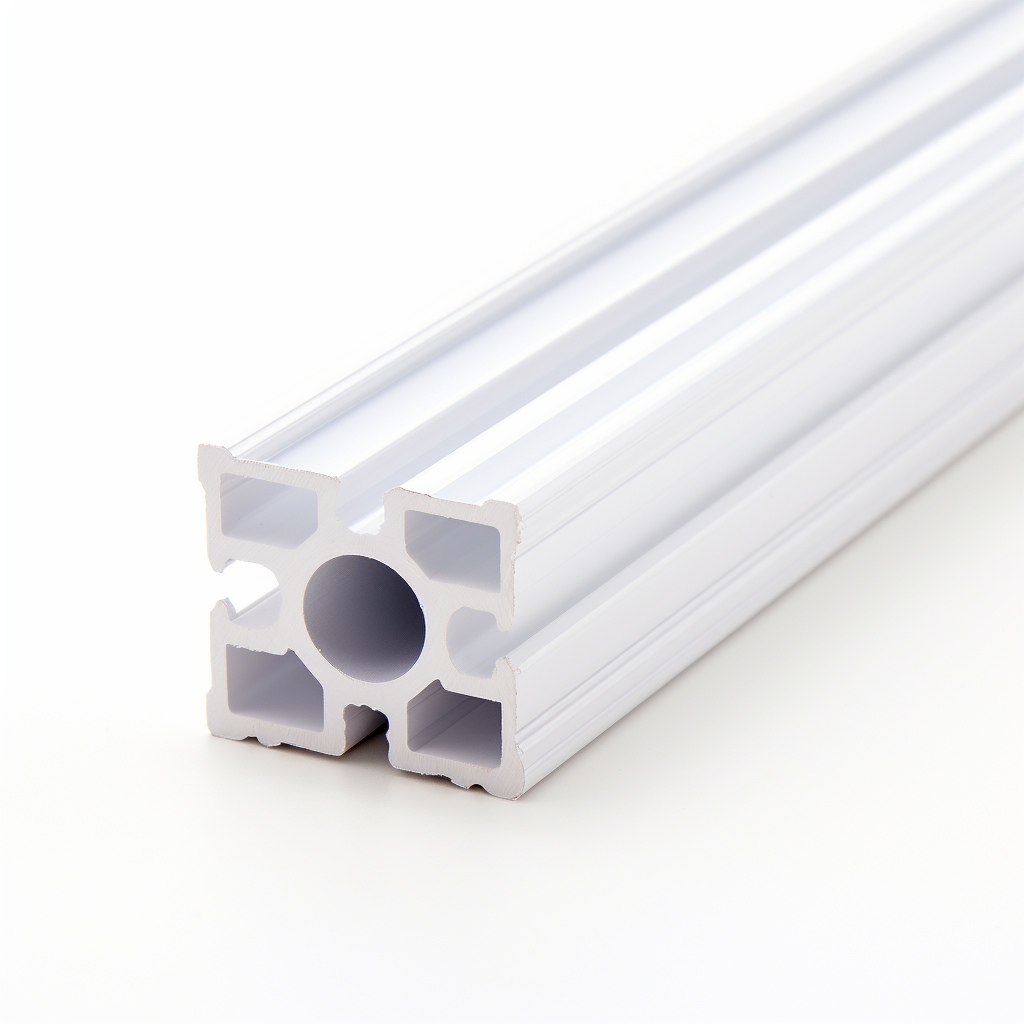
Advantages
- Complex Shapes: Extrusion allows for the creation of intricate profiles and cross-sections.
- Material Efficiency: Minimal waste as excess material can be recycled.
- Consistency: High precision and repeatability in product dimensions.
- High Production Rates: Well-suited for high-volume manufacturing.
- Improved Material Properties: Some materials experience enhanced mechanical properties after extrusion.
Disadvantages
- Setup Costs: Initial tooling and equipment costs can be high.
- Limited Material Compatibility: Not all materials are suitable for extrusion.
- Surface Finish: Achieving a smooth surface may require additional processing.
Common Applications of Extrusion
- Construction: Creating aluminum and PVC profiles for windows, doors, and structural components.
- Automotive: Producing complex aluminum and steel profiles for vehicle frames and parts.
- Aerospace: Manufacturing high-strength components for aircraft and spacecraft.
- Packaging: Extruding plastics for packaging materials like films, sheets, and containers.
- Electronics: Fabricating heat sinks, electrical enclosures, and connectors.
Please consult a Canyon Components Engineer about your specific application and we will use our decades of experience to formulate a solution that fits your need.
Types of Extrusion
Extrusion can be performed in a number of ways depending on the composition and intended use of the final product. Some variations available for Extrusion include the following.
Canyon Components strives to meet all customer service requests. Feel free to contact Canyon Components engineering and let our knowledgeable staff help you design the perfect part for your needs.
Plastic Extrusion
Involves melting and pushing plastic through a die to create continuous shapes like tubes and sheets. It's cost-effective for high-volume production. Advantages include versatility in shapes and materials and continuous output. However, it has limited precision compared to other manufacturing processes and can struggle with complex cross-sections.
Aluminum Extrusion
This process pushes heated aluminum through a die to create components for construction and automotive industries. Its advantages are strength, lightweight parts, and corrosion resistance. The downside is the initial cost of die design and limited to uniform cross-section profiles.
Sheet Extrusion
Produces flat plastic sheets used in packaging and building industries. The advantage is the ability to produce wide, continuous sheets with consistent thickness. However, it is less suitable for complex shapes and the material may warp if not cooled properly.
Profile Extrusion
Used to create complex cross-sectional profiles for window frames and pipes. Its advantage lies in producing intricate shapes with consistent quality. The main disadvantage is the limitation in producing only uniform cross-sectional shapes and the potential for variations in wall thickness.
Tube Extrusion
Creates hollow tubes used in medical, automotive, and plumbing applications. Advantages include the ability to create tubes with varying diameters and wall thicknesses. The drawback is difficulty in maintaining uniform wall thickness, especially in complex or very small tubes.
Film Extrusion
Produces thin plastic films, commonly used for packaging. This method is excellent for creating large volumes of product with good material efficiency. However, it's less capable of producing films with complex or irregular shapes, and film quality can be sensitive to process conditions.
Please consult a Canyon Components Engineer about your specific application and we will use our decades of experience to formulate a solution that fits your need.
Request a Quote for Extruded Parts
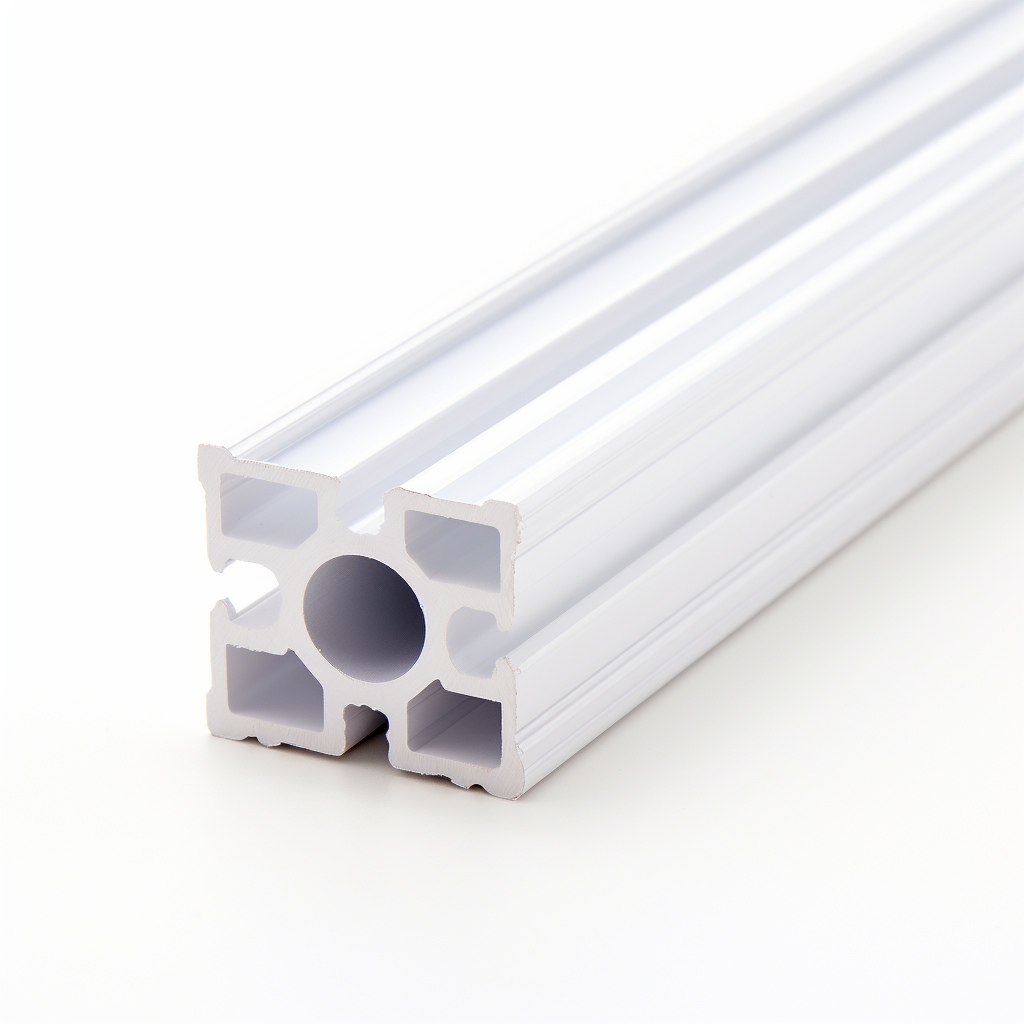
Extrusion Materials Available
Extrusion can be performed in a number of ways depending on the composition and intended use of the final product. Some common materials available for Extrusion include the following.
Each of these materials has its own advantages, limitations, and cost implications. The choice of material and manufacturing technique usually depends on factors like the complexity of the design, required precision, material properties, and production volume.
Canyon Components strives to meet all customer service requests. Feel free to contact Canyon Components engineering and let our knowledgeable staff help you design the perfect part for your needs.
Elastomers
Elastomers (also referred to as rubber) are a class of materials known for their unique ability to stretch, deform, and return to their original shape, making them essential in a wide range of applications.
Perfluoroelastomers (FFKM, Kalrez, CanRez)
Extreme temperatures & chemicals require extreme solutions! CanRez™ FFKM materials offer extreme reliability where you need it most! Thousands of sizes in stock now!
FKM (Viton®, Fluorocarbon)
FKM compounds, O-rings, gaskets, & custom molded parts exhibit excellent mechanical attributes as well as excellent resistance to high temperatures, mineral oil, ozone, fuels, hydraulic fluids, and many other solvents and chemicals.
Silicone (VMQ, PVMQ)
Silicone seals, O-rings, gaskets, & custom molded parts are excellent for extreme temperatures in static applications. Canyon Components carries a range of silicone materials, and we are happy to custom tailor a seal to meet your application requirements!
Plastics
Plastics are a broad class of synthetic or semi-synthetic materials known for their versatility and moldability. They are crucial in numerous applications due to their ability to be shaped, lightweight nature, and resistance to chemicals and moisture.
Nylon (Polyamide, PA)
Nylon, a synthetic thermoplastic polymer, is renowned for its high strength, elasticity, and abrasion resistance. It's versatile, easily dyeable, and used in a wide range of products from textiles and ropes to gears and automotive parts.
PEEK (Polyetheretherketone)
PEEK plastic, or polyether ether ketone, is a high-performance thermoplastic known for its exceptional heat resistance, chemical stability, and mechanical strength. It's widely used in aerospace, medical implants, and automotive industries for its durability and ability to withstand harsh environments.
PTFE (Polytetrafluoroethylene, Teflon)
Polytetrafluoroethylene (PTFE) Plastic, commonly known as Teflon, is a highly non-reactive and low-friction thermoplastic. Renowned for its outstanding chemical resistance, heat tolerance, and electrical insulation properties, it's extensively used in cookware coatings, electrical insulation, and various industrial applications.
Metals
Metals are a class of materials distinguished by their conductive, malleable, and ductile properties. They are fundamental in various applications due to their ability to conduct electricity and heat, resist corrosion, and form alloys with other metals.
Aluminum
Aluminum, a lightweight, silver-white metal, is known for its remarkable corrosion resistance and high strength-to-weight ratio. It's easily machinable, conducts heat and electricity well, and is widely used in aerospace, transportation, and packaging industries due to its versatility.
Stainless Steel
Stainless steel, an alloy of iron, chromium, and often nickel, is renowned for its corrosion resistance and lustrous appearance. Its durability, easy maintenance, and hygienic qualities make it a popular choice in kitchenware, medical equipment, and architectural structures.
Titanium
Titanium is a lightweight, strong metal with a silvery-white appearance, known for its exceptional corrosion resistance and high strength-to-density ratio. Widely used in aerospace, medical implants, and sporting equipment, it forms alloys with elements like aluminum and vanadium.
Back to Manufacturing Hub
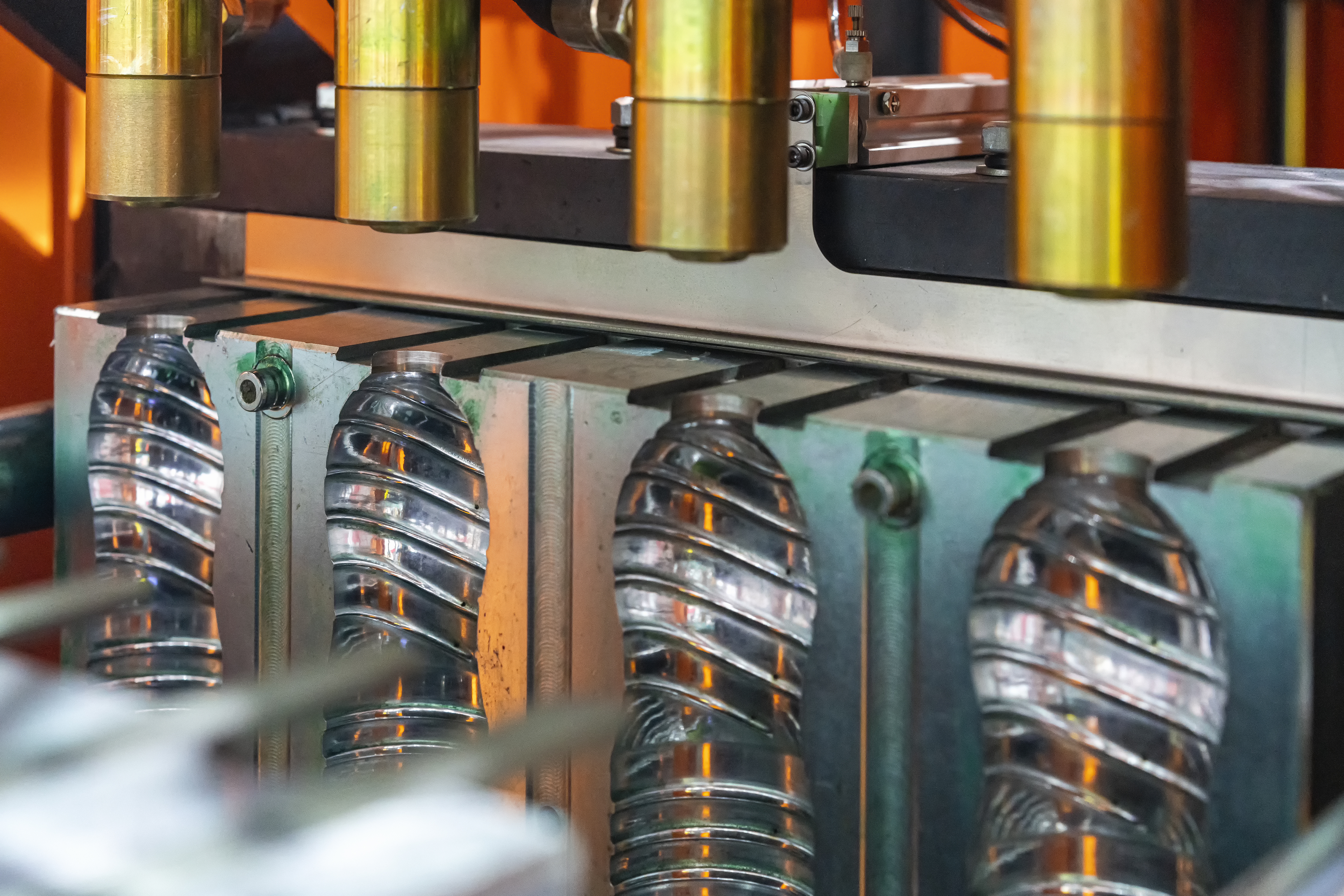
Get A Quote Now!
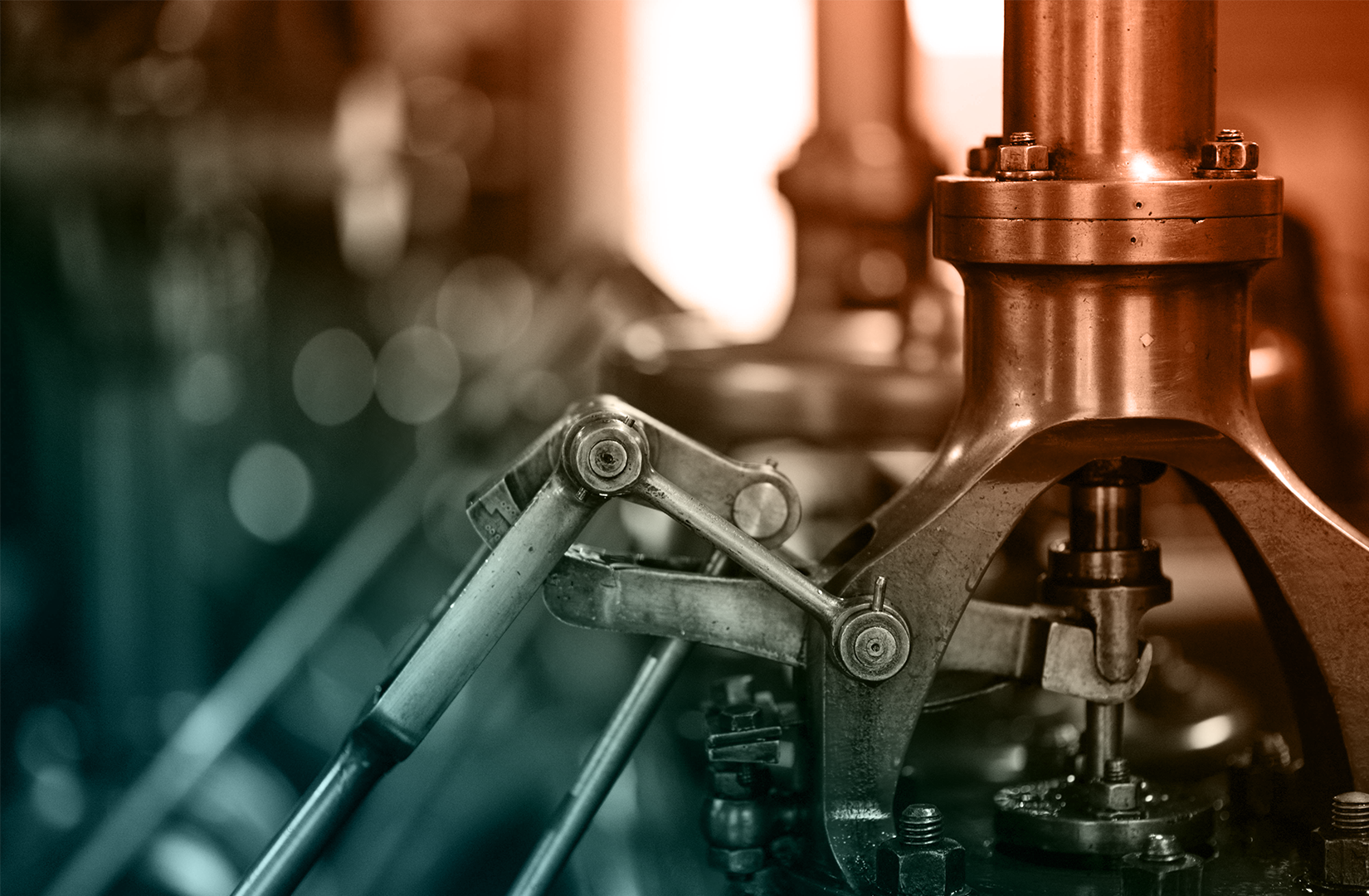
Groove Design References
Learn More
Coatings, Packaging, & Other Services
Learn More
Custom Parts & Custom O-rings
Learn More