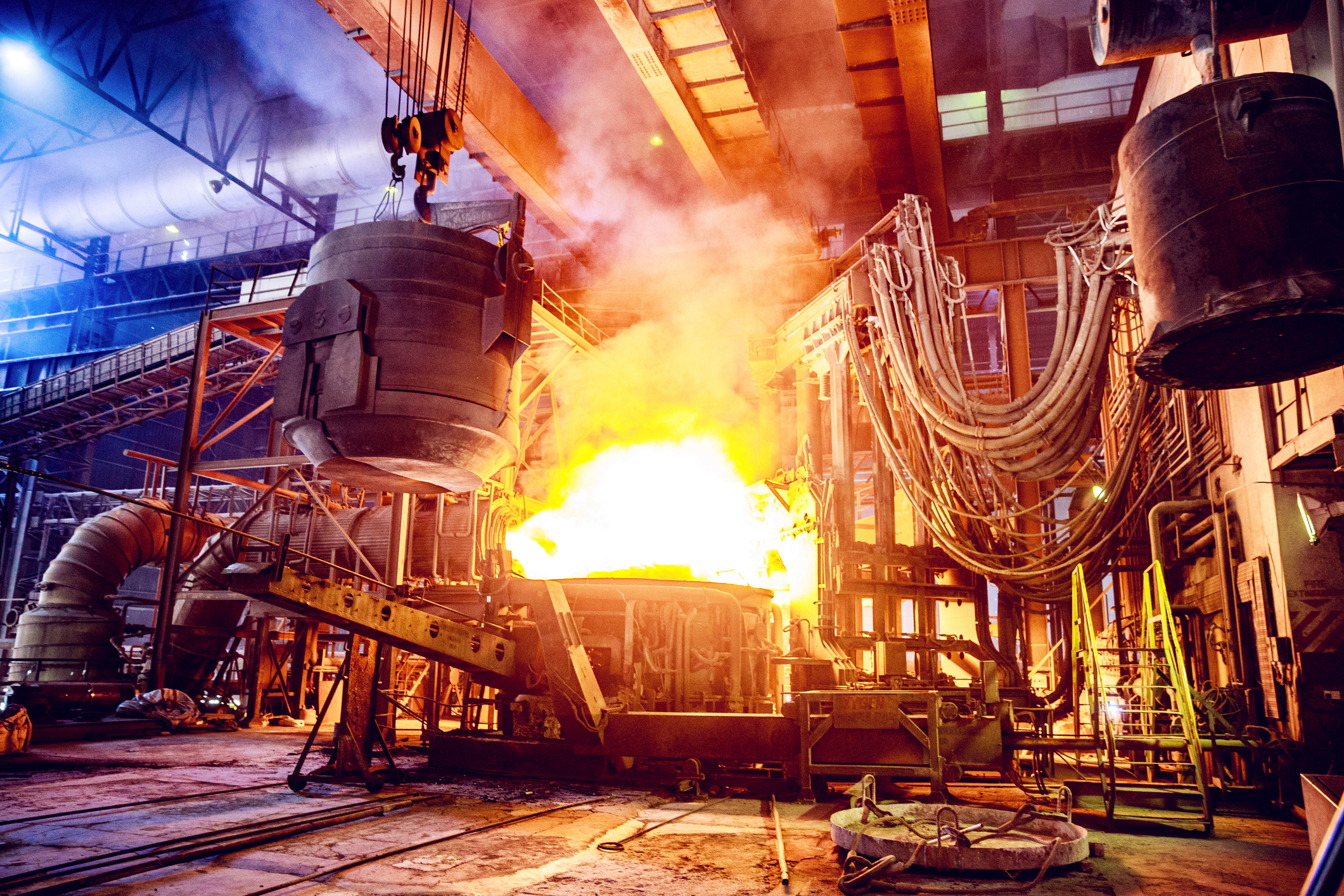
Aluminum Metal Selection Guide
Aluminum is a lightweight and versatile metal that is widely used in various industrial applications due to its excellent combination of properties. It is known for its low density, corrosion resistance, and good electrical conductivity. In this web page, we will explore the different types of aluminum, its numerous advantages and disadvantages, and the diverse industrial uses where aluminum plays a crucial role.
Aluminum rapid manufacturing, & machined parts are available now!
Check with one of Canyon’s helpful product engineers for an expert material and manufacturing recommendation.
Common names include: 1100 Aluminum, 2024 Aluminum, 3003 Aluminum, 5052 Aluminum, 6061 Aluminum, 7075 Aluminum, 6063 Aluminum, Alclad Aluminum.
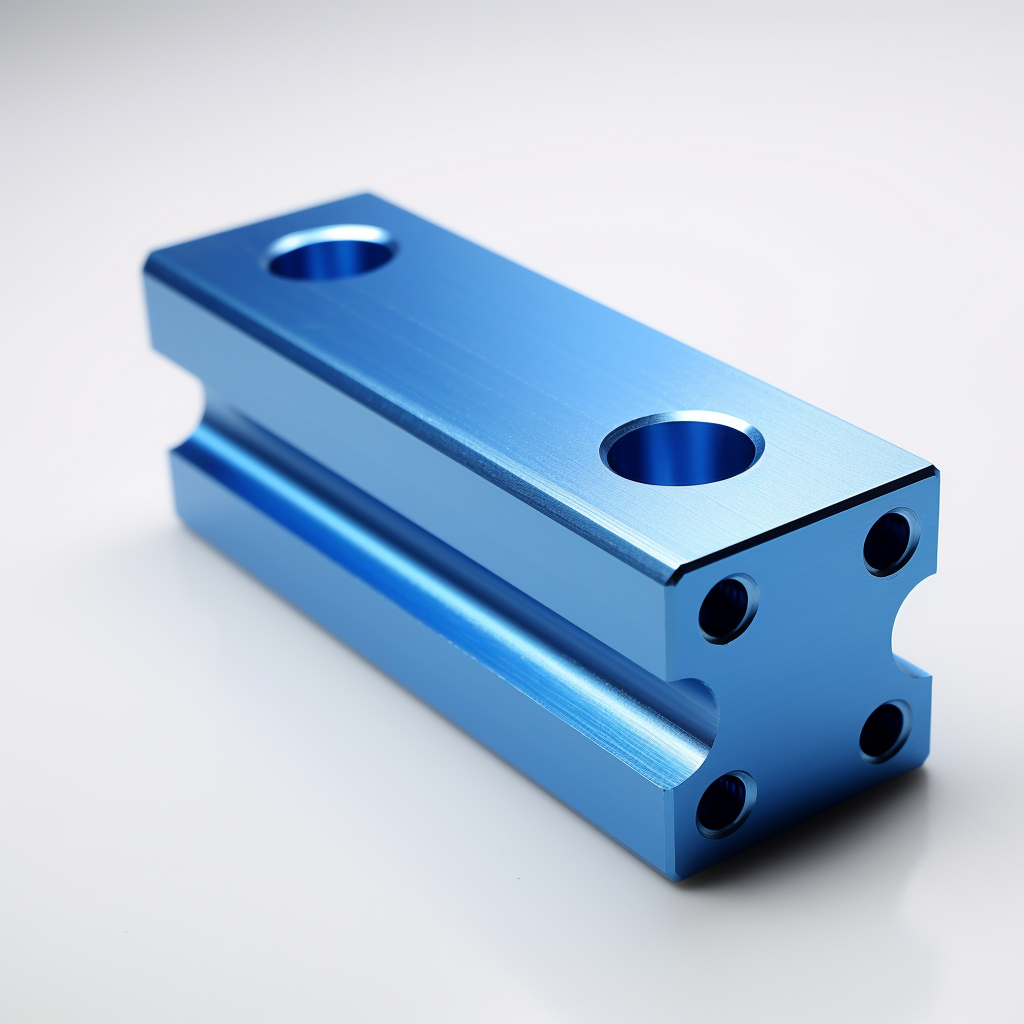
Advantages
- Low Density: Aluminum is lightweight, making it ideal for applications where weight reduction is crucial, such as in the aerospace and automotive industries.
- Corrosion Resistance: Aluminum naturally forms a protective oxide layer on its surface, providing excellent resistance to corrosion, especially in marine and outdoor environments.
- High Electrical Conductivity: Aluminum has good electrical conductivity, making it suitable for electrical transmission lines and conductors.
- Thermal Conductivity: Aluminum is an excellent thermal conductor, making it useful in heat exchangers and cooling systems.
- Recyclability: Aluminum is highly recyclable, and recycled aluminum retains its properties, contributing to sustainability efforts.
- Formability: Aluminum is easily shaped and formed through various processes, allowing for intricate designs and complex structures.
- Aesthetic Appeal: Aluminum's attractive appearance and ability to be anodized or coated for added aesthetics make it popular in architectural and decorative applications.
Disadvantages
- Lower Strength: Pure aluminum has lower tensile strength compared to steel, which may require the use of thicker sections or alloys to achieve the desired strength.
- Susceptibility to Stress Corrosion Cracking: Some aluminum alloys can be susceptible to stress corrosion cracking in specific environments, requiring proper material selection and protection.
- Higher Cost: Certain aluminum alloys, especially those with added alloying elements, can be more expensive than other materials like steel.
- Limited High-Temperature Performance: Aluminum's melting point is lower than that of steel, limiting its use in high-temperature applications.
Common Applications of Aluminum
- Aerospace: Aluminum is used extensively in aircraft structures, including wings, fuselages, and landing gear, due to its lightweight properties.
- Automotive: Aluminum is used in automotive components such as engine blocks, wheels, and body panels to reduce weight and improve fuel efficiency.
- Construction: Aluminum is used in architectural structures, windows, doors, roofing, and cladding due to its corrosion resistance and aesthetic appeal.
- Electrical and Electronics: Aluminum is used for electrical conductors, wiring, and heat sinks due to its electrical conductivity and thermal properties.
- Packaging: Aluminum is commonly used for beverage cans, food containers, and foil packaging due to its lightweight and corrosion-resistant properties.
- Transportation: Aluminum is used in ships, trains, and bicycles for its lightweight and corrosion resistance.
- Consumer Goods: Aluminum is used in a wide range of consumer products, including cookware, appliances, and sporting goods, due to its lightweight and aesthetic appeal.
- Power Transmission: Aluminum is used for overhead power transmission lines and cables due to its lightweight and electrical conductivity.
Please consult a Canyon Components Engineer about your specific application and we will use our decades of experience to formulate a solution that fits your need.
Types of Aluminum
Aluminum can come in different variations, depending on its composition and intended use. Some common types of Aluminum include the following.
Canyon Components strives to meet all customer service requests. Feel free to contact Canyon Components engineering and let our knowledgeable staff help you design the perfect part for your needs.
Series 1000 (Pure Aluminum)
This series is known for its high purity, excellent corrosion resistance, and high thermal and electrical conductivity. It's commonly used in chemical processing equipment, electrical components, and food industry applications. Its malleability makes it ideal for intricate shaping, but it has lower strength compared to other series.
Series 2000 (Aluminum-Copper Alloys)
These alloys are known for their high strength and are commonly used in aerospace applications. They offer good machinability and have excellent mechanical properties, but are less resistant to corrosion. Series 2000 is often heat-treated for added strength.
Series 3000 (Aluminum-Manganese Alloys)
Renowned for their good corrosion resistance, these alloys are commonly used in beverage cans, cooking utensils, and roofing sheets. They are not heat-treatable but can be work-hardened to increase strength, making them suitable for general-purpose applications.
Series 5000 (Aluminum-Magnesium Alloys)
These alloys are highly resistant to corrosion, especially in marine environments, and are often used in shipbuilding, tankers, and architectural applications. They are not heat-treatable but offer good weldability and moderate strength.
Series 6000 (Aluminum-Magnesium-Silicon Alloys)
Widely used in construction and automotive industries, these alloys are known for their balance of strength, corrosion resistance, and formability. They are heat-treatable and commonly used in extrusions, frames, and railings.
Series 7000 (Aluminum-Zinc Alloys)
Offering the highest strength of all aluminum alloys, they are extensively used in aerospace and sporting equipment. These alloys are heat-treatable and have good fatigue resistance, but their machinability and corrosion resistance are lower compared to other series.
Please consult a Canyon Components Engineer about your specific application and we will use our decades of experience to formulate a solution that fits your need.
Manufacturing Options for Aluminum
Aluminum parts can be manufactured using several methods, each suitable for different applications and part complexities.
Each of these methods has its own advantages, limitations, and cost implications. The choice of manufacturing technique usually depends on factors like the complexity of the design, required precision, material properties, and production volume.
Canyon Components strives to meet all customer service requests. Feel free to contact Canyon Components engineering and let our knowledgeable staff help you design the perfect part for your needs.
Back to Metals Hub
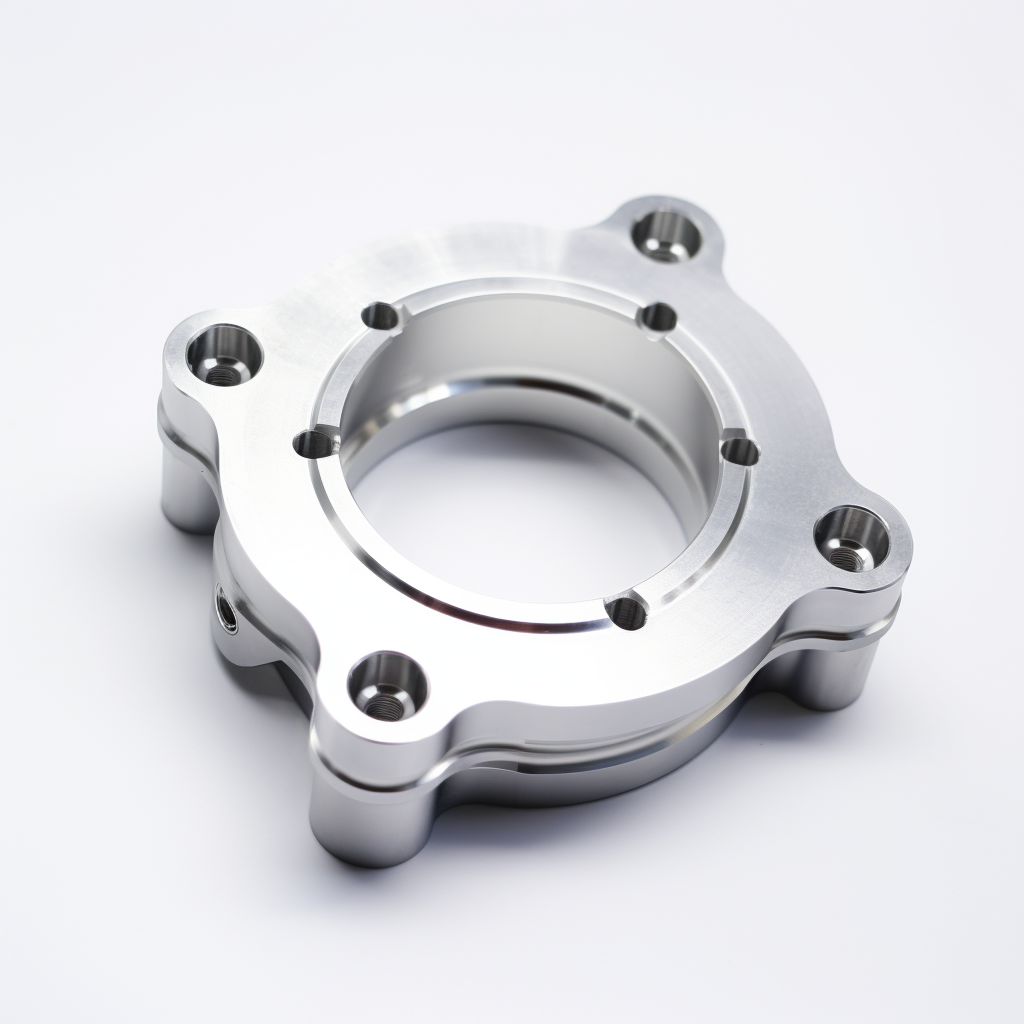
Get A Quote Now!
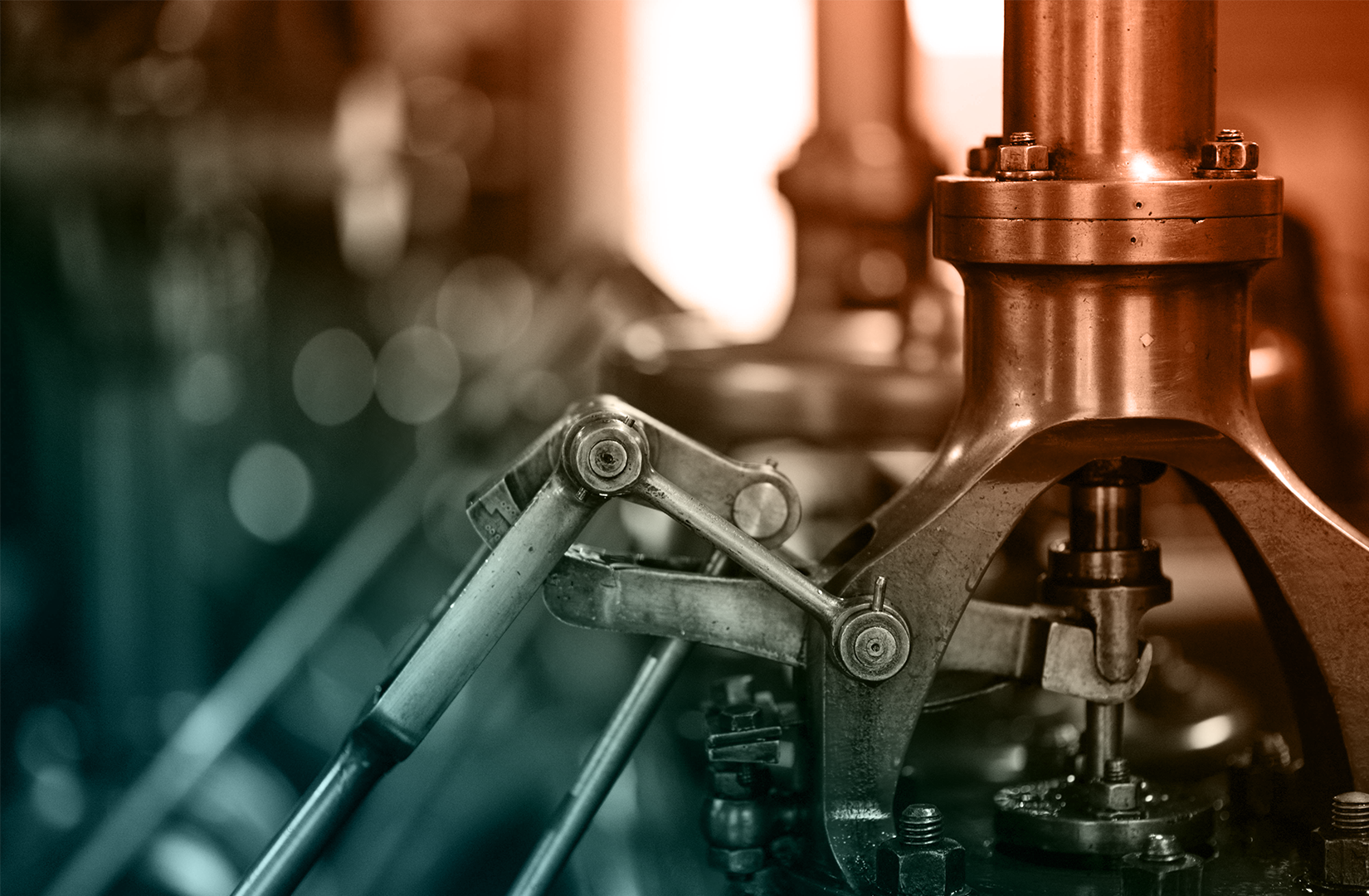
Groove Design References
Learn More
Coatings, Packaging, & Other Services
Learn More
Custom Parts & Custom O-rings
Learn More