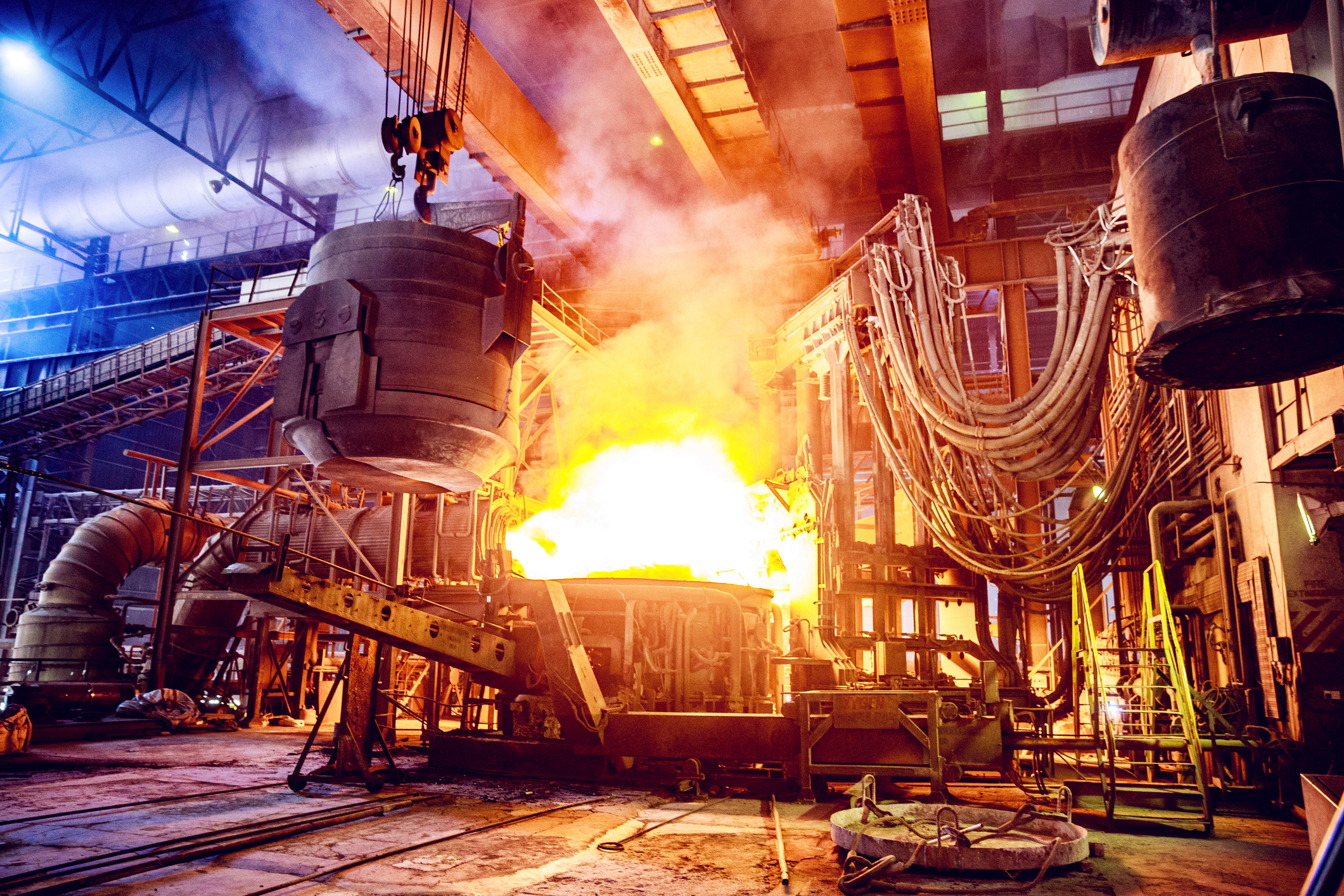
CNC Machining
Computer Numerical Control (CNC) manufacturing is a versatile and automated process that utilizes computer programs to control machining tools and equipment. It plays a pivotal role in modern manufacturing, offering precision, efficiency, and versatility. In this web page, we will explore the different types of CNC manufacturing, their advantages and disadvantages, and the diverse industrial applications. Additionally, we'll provide a list of materials commonly used in CNC manufacturing. Custom CNC Machined parts available now!
Check with one of Canyon’s helpful product engineers for an expert material and manufacturing recommendation.
Common terminology includes: CNC milling, CNC turning, CNC drilling, CNC grinding, 5-axis machining, 3-axis machining, 4-axis machining, CNC tapping, CNC boring, CNC reaming, CNC broaching, Swiss-style machining, CNC routing, CNC engraving, live tooling CNC machining.
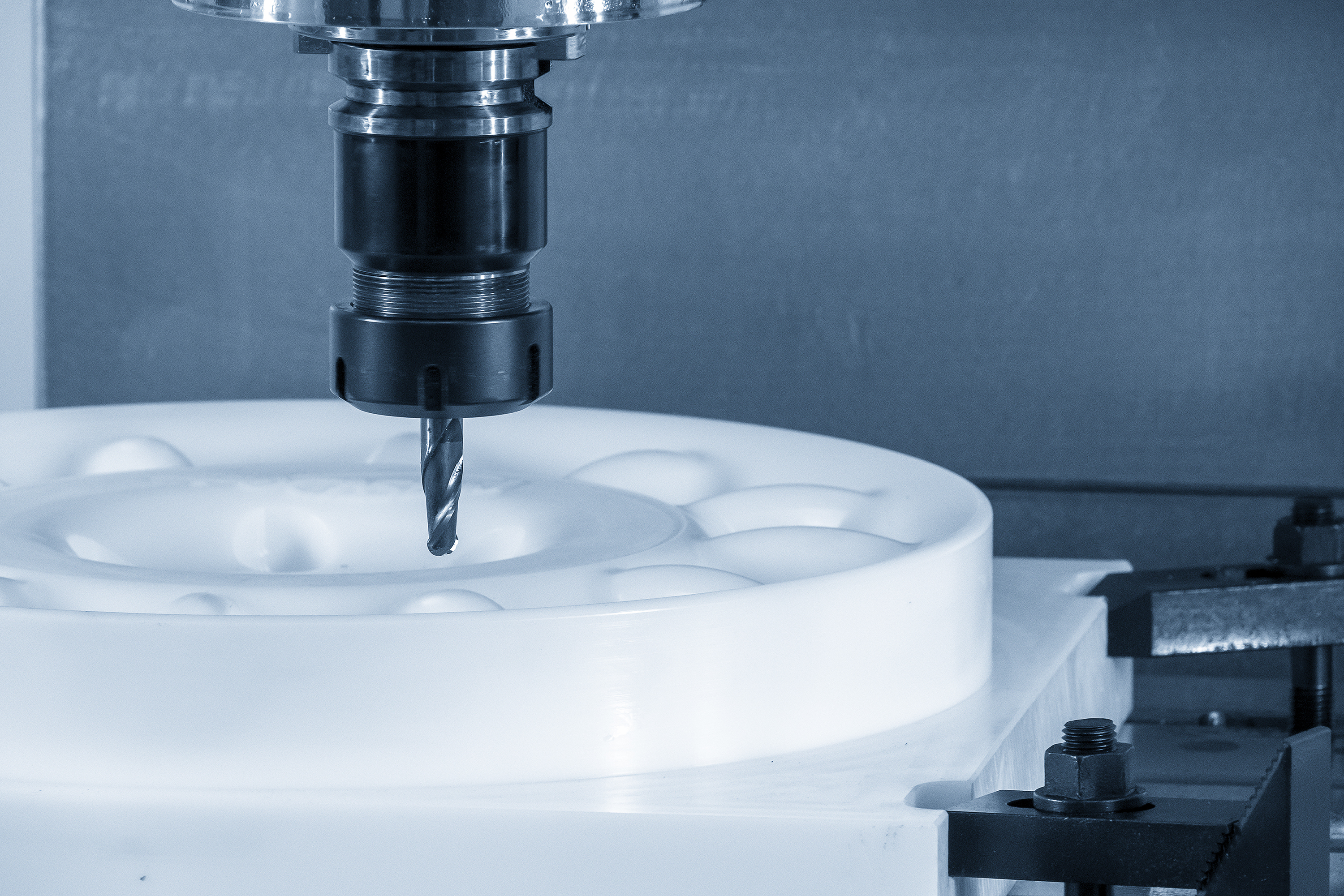
Advantages
- Precision: Achieves high levels of accuracy and repeatability.
- Automation: Reduces labor costs and increases production efficiency.
- Versatility: Suitable for a wide range of materials and complex geometries.
- Customization: Easily adapts to various designs and prototypes.
- Cost-Efficiency: Offers long-term cost savings through automation and reduced waste.
Disadvantages
- High Equipment Costs: Initial setup and equipment investment can be substantial.
- Operator Skill Requirement: Skilled operators are needed to program and operate CNC machines.
- Tool Wear and Maintenance: Tools require regular maintenance and replacement.
Common Applications of CNC Machining
- Aerospace: Precision machining of aircraft components and engine parts.
- Automotive: Producing engine components, chassis parts, and custom prototypes.
- Medical: Manufacturing surgical instruments, implants, and medical device components.
- Consumer Electronics: Fabricating custom parts for electronic devices.
- Custom Fabrication: Creating architectural components, signage, and custom machinery.
Please consult a Canyon Components Engineer about your specific application and we will use our decades of experience to formulate a solution that fits your need.
Types of CNC Machining
CNC Machining can be performed in a number of ways depending on the composition and intended use of the final product. Some variations available for CNC Machining include the following.
Canyon Components strives to meet all customer service requests. Feel free to contact Canyon Components engineering and let our knowledgeable staff help you design the perfect part for your needs.
CNC Milling
Involves cutting and drilling materials using a rotating cylindrical tool. Ideal for complex shapes and precision parts. Advantages include versatility and high precision. However, it's less efficient for round or hollow shapes and can be costly due to the need for multiple tooling setups.
CNC Turning
Uses a lathe to rotate the workpiece against a cutting tool. Best for cylindrical or round parts. The process is efficient and cost-effective for producing symmetrical components. The disadvantage is its limitation to primarily round or tubular shapes.
CNC Drilling
Involves creating holes in a workpiece using drill bits. It's highly precise and ideal for repetitive hole-making operations. While efficient and accurate for drilling, it's limited to hole-making operations and lacks the versatility of milling or turning.
CNC Grinding
Uses an abrasive wheel to remove material from a workpiece, achieving high surface quality and precise dimensions. It’s excellent for finishing operations. However, grinding is slower and more costly compared to other CNC processes, and it generates significant heat.
CNC Electrical Discharge Machining (EDM)
Utilizes electrical sparks to shape a workpiece. It excels in producing intricate, detailed parts from hard materials. The main advantage is its ability to machine complex shapes that would be challenging with other methods. The downside is slower processing speed and higher operational costs.
CNC Plasma Cutting
Employs a plasma torch to cut through metal. It's fast and cost-effective for cutting thick metal sheets. The advantage lies in its speed and ability to cut large sections of metal. However, it’s less precise than laser cutting and is limited to conductive materials.
Please consult a Canyon Components Engineer about your specific application and we will use our decades of experience to formulate a solution that fits your need.
Request a Quote for CNC Machined Parts
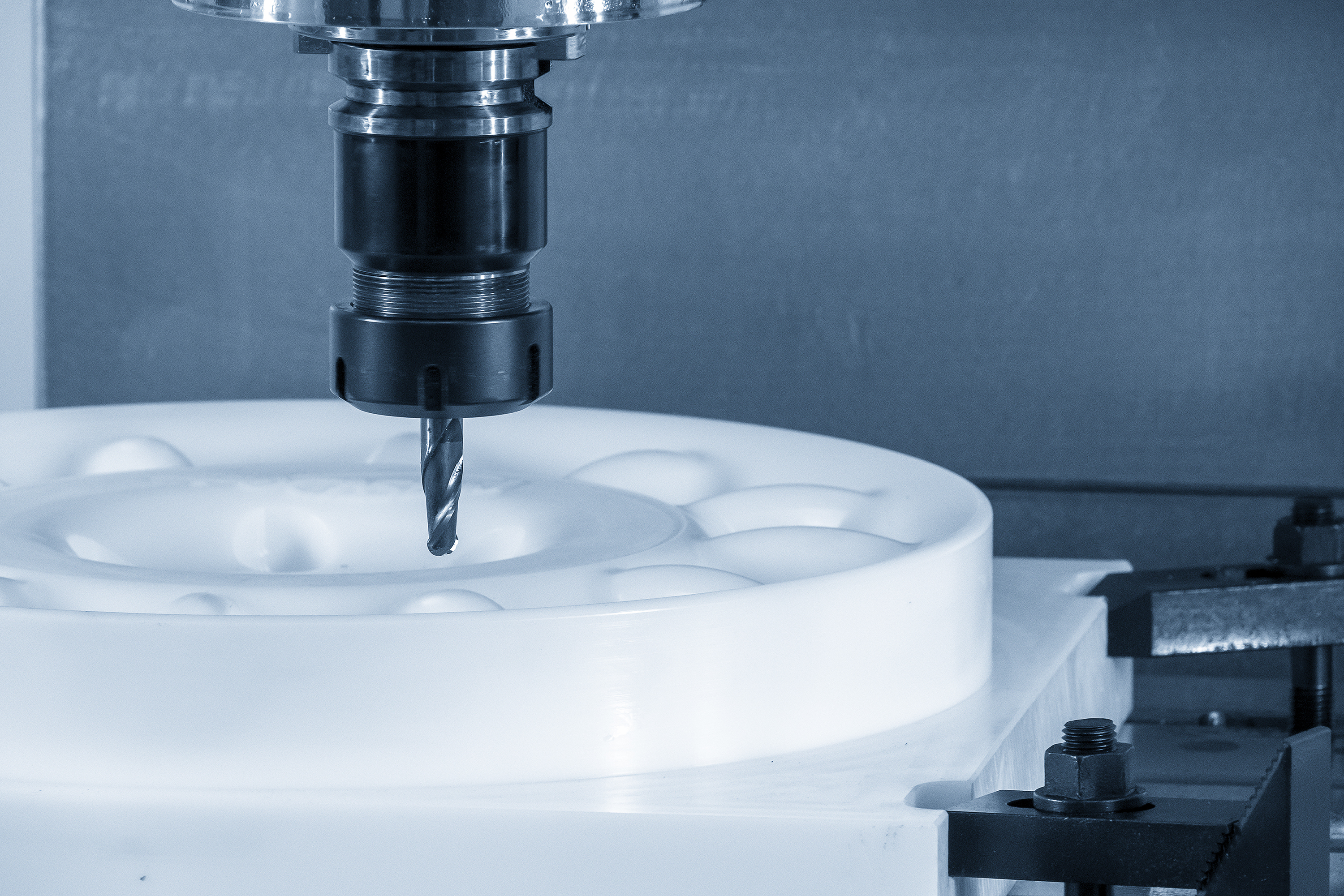
CNC Machining Materials Available
CNC Machining can be performed in a number of ways depending on the composition and intended use of the final product. Some common materials available for CNC Machining include the following.
Each of these materials has its own advantages, limitations, and cost implications. The choice of material and manufacturing technique usually depends on factors like the complexity of the design, required precision, material properties, and production volume.
Canyon Components strives to meet all customer service requests. Feel free to contact Canyon Components engineering and let our knowledgeable staff help you design the perfect part for your needs.
Perfluoroelastomers (FFKM, Kalrez, CanRez)
Extreme temperatures & chemicals require extreme solutions! CanRez™ FFKM materials offer extreme reliability where you need it most! Thousands of sizes in stock now!
Plastics
Plastics are a broad class of synthetic or semi-synthetic materials known for their versatility and moldability. They are crucial in numerous applications due to their ability to be shaped, lightweight nature, and resistance to chemicals and moisture.
PTFE (Polytetrafluoroethylene, Teflon)
Polytetrafluoroethylene (PTFE) Plastic, commonly known as Teflon, is a highly non-reactive and low-friction thermoplastic. Renowned for its outstanding chemical resistance, heat tolerance, and electrical insulation properties, it's extensively used in cookware coatings, electrical insulation, and various industrial applications.
PEEK (Polyetheretherketone)
PEEK plastic, or polyether ether ketone, is a high-performance thermoplastic known for its exceptional heat resistance, chemical stability, and mechanical strength. It's widely used in aerospace, medical implants, and automotive industries for its durability and ability to withstand harsh environments.
POM (Polyoxymethylene, Acetal)
Polyoxymethylene (POM) Plastic, also known as Acetal or Delrin, is a high-strength, low-friction thermoplastic. It's characterized by its dimensional stability, excellent wear resistance, and low moisture absorption, making it ideal for precision parts in automotive and consumer electronics.
Metals
Metals are a class of materials distinguished by their conductive, malleable, and ductile properties. They are fundamental in various applications due to their ability to conduct electricity and heat, resist corrosion, and form alloys with other metals.
Stainless Steel
Stainless steel, an alloy of iron, chromium, and often nickel, is renowned for its corrosion resistance and lustrous appearance. Its durability, easy maintenance, and hygienic qualities make it a popular choice in kitchenware, medical equipment, and architectural structures.
Titanium
Titanium is a lightweight, strong metal with a silvery-white appearance, known for its exceptional corrosion resistance and high strength-to-density ratio. Widely used in aerospace, medical implants, and sporting equipment, it forms alloys with elements like aluminum and vanadium.
Brass
Brass is a versatile alloy primarily composed of copper and zinc, known for its golden-yellow hue. It exhibits excellent malleability, acoustic properties, and resistance to corrosion, making it a popular choice for musical instruments, decorative items, and various fittings.
Zinc Alloy
Zinc alloy is a robust metal combination mainly composed of zinc, often blended with aluminum, copper, and magnesium. It's known for its high strength, good corrosion resistance, and ability to be cast into intricate shapes, commonly used in die-casting and automotive parts.
Nickel Alloy
Nickel alloy, a blend of nickel and other elements, is known for its exceptional corrosion resistance, heat resistance, and strength. It excels in harsh environments, making it ideal for aerospace, chemical processing, and power generation applications. Its silvery-white appearance adds to its appeal.
Bronze
Bronze, a copper-tin alloy, often contains small amounts of other elements like aluminum or nickel. It's known for its hardness, durability, and distinctive reddish-brown color. Widely used in sculpture, coins, and industrial applications, bronze resists corrosion and metal fatigue.
Tungsten Carbide
Tungsten carbide, a composite of tungsten and carbon, is exceptionally hard and wear-resistant. It has a high melting point and great rigidity, making it ideal for cutting tools, abrasives, and armor-piercing rounds. Its density and strength are comparable to those of diamond.
Back to Manufacturing Hub
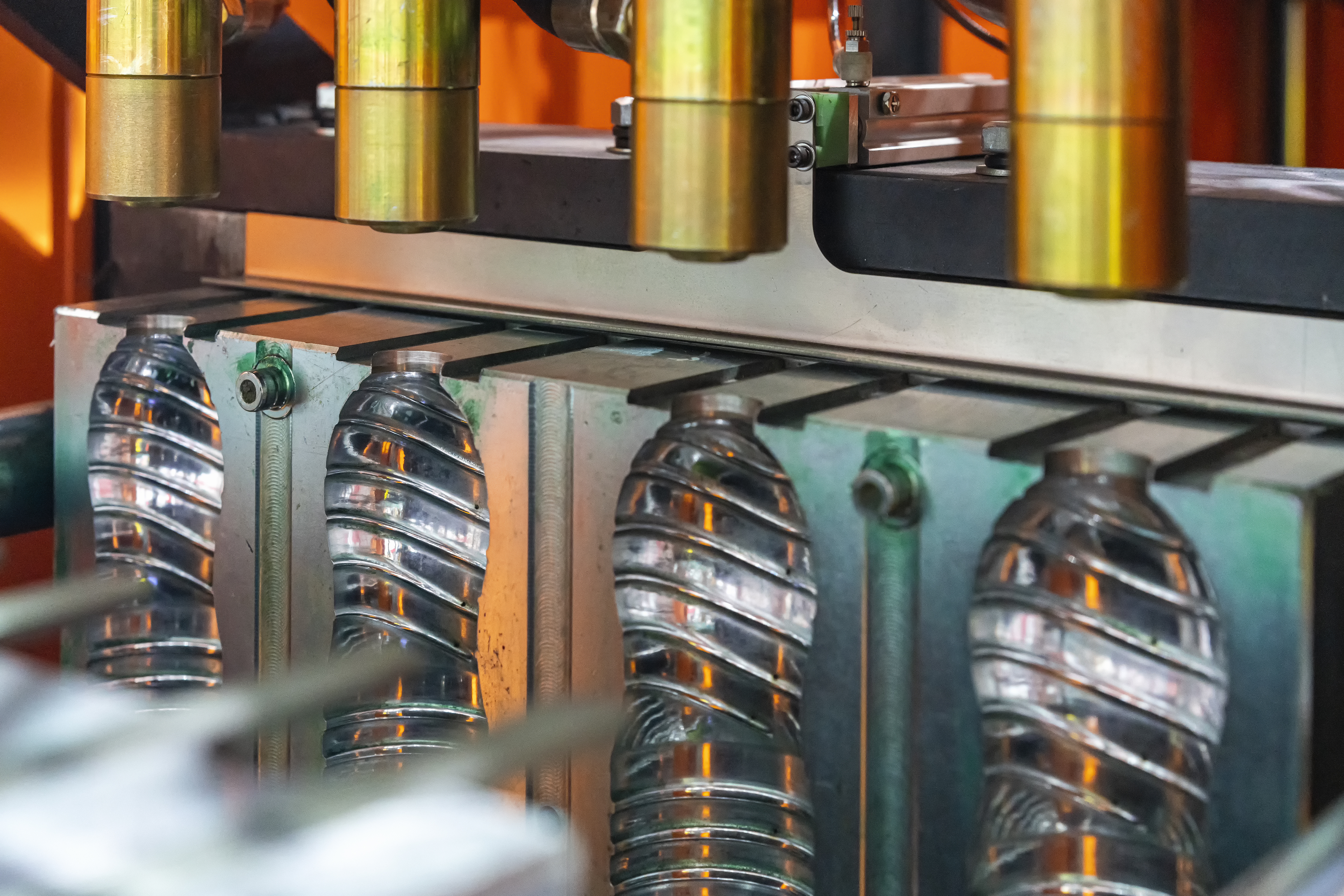
Get A Quote Now!
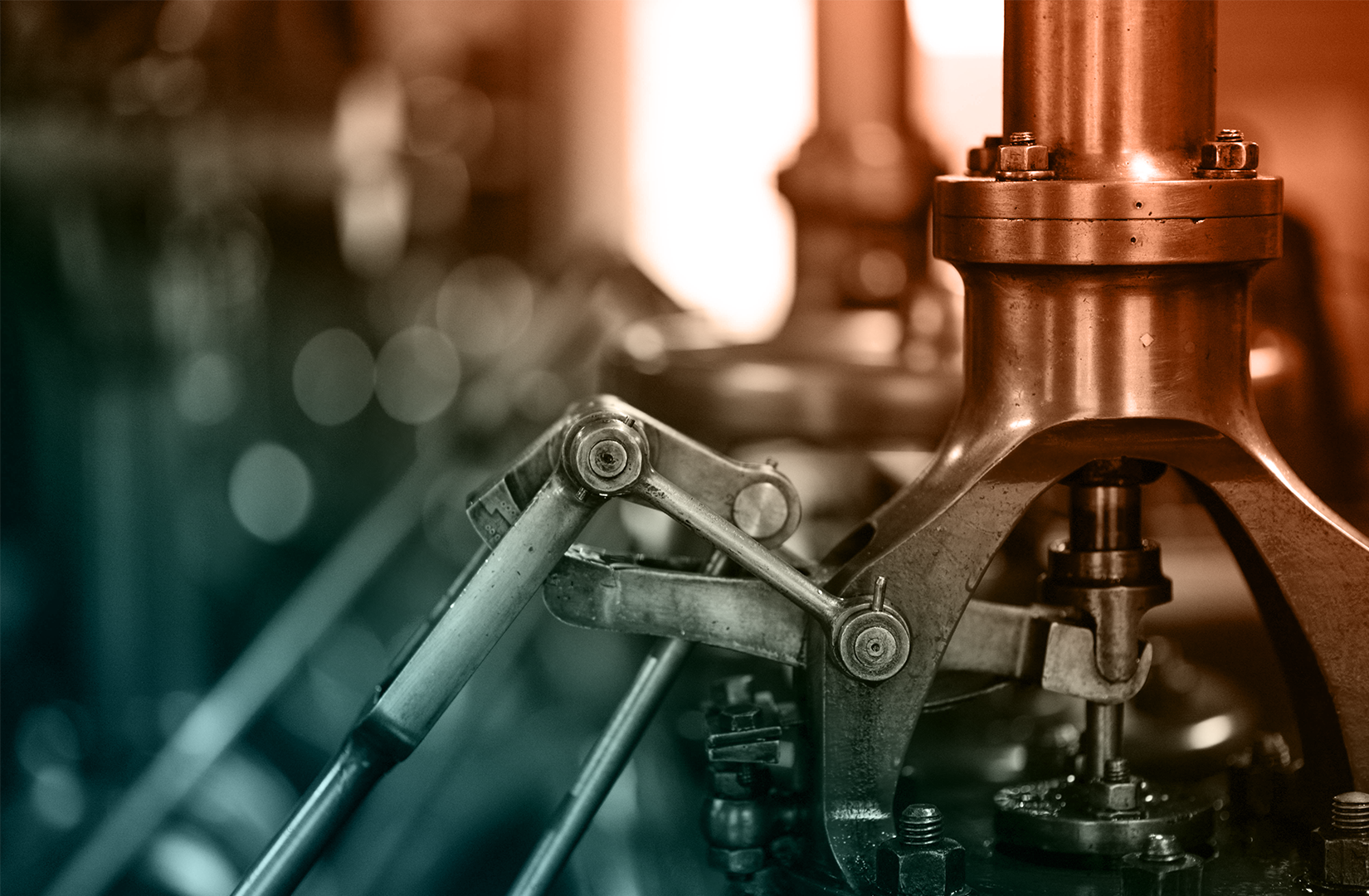
Groove Design References
Learn More
Coatings, Packaging, & Other Services
Learn More
Custom Parts & Custom O-rings
Learn More