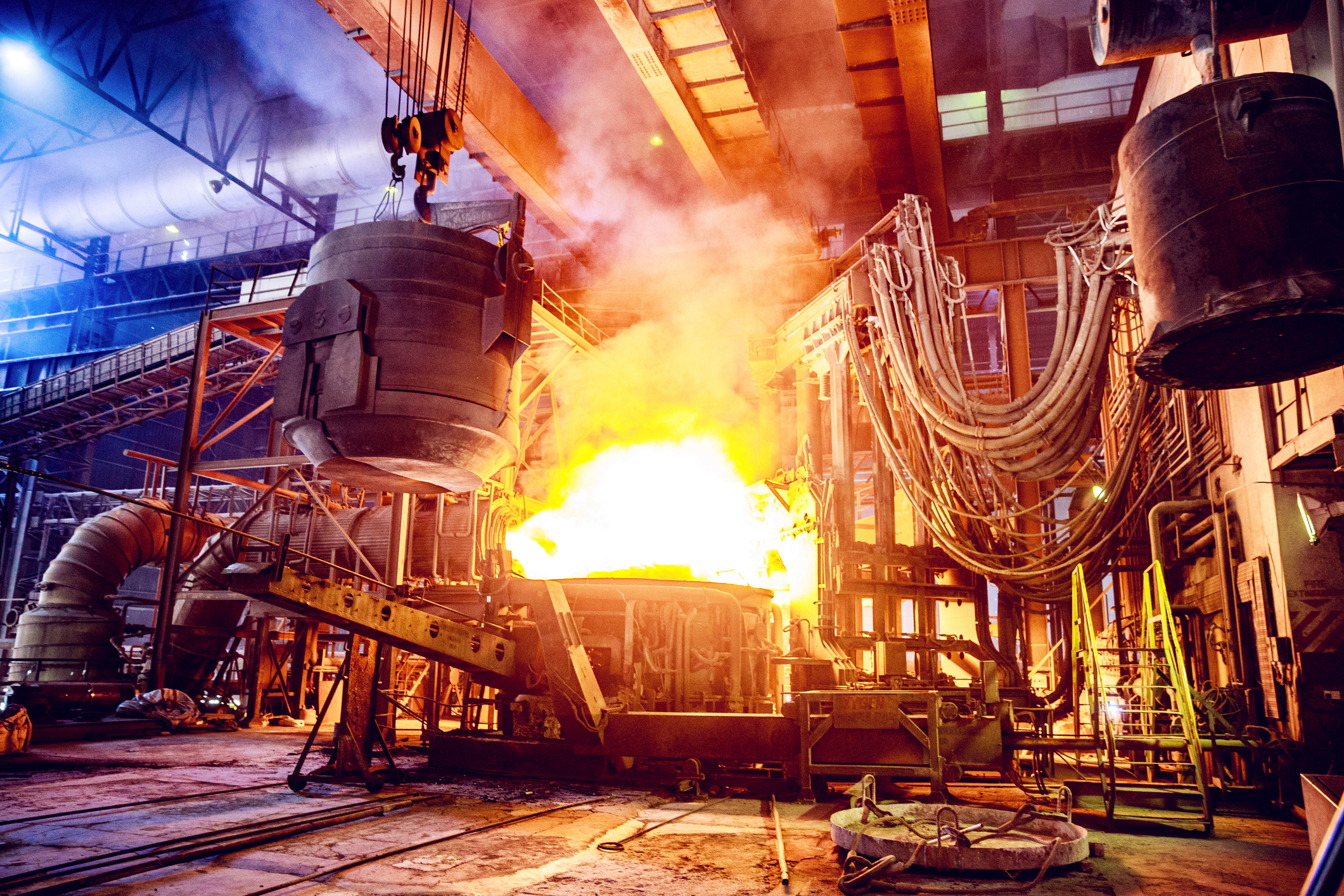
Bronze Alloy Metal Selection Guide
Bronze is a versatile and historically significant metal alloy composed primarily of copper, with varying amounts of tin and other elements. Known for its exceptional durability and resistance to corrosion, bronze has been used for thousands of years for a wide range of applications, from sculpture to weaponry. In this web page, we will explore the different types of bronze, its numerous advantages and disadvantages, and the diverse industrial uses where bronze plays a crucial role.
Bronze rapid manufacturing, & machined parts are available now!
Check with one of Canyon’s helpful product engineers for an expert material and manufacturing recommendation.
Common names include: Phosphor Bronze, Aluminum Bronze, Silicon Bronze, Manganese Bronze, Leaded Bronze, Nickel Bronze, Beryllium Bronze.
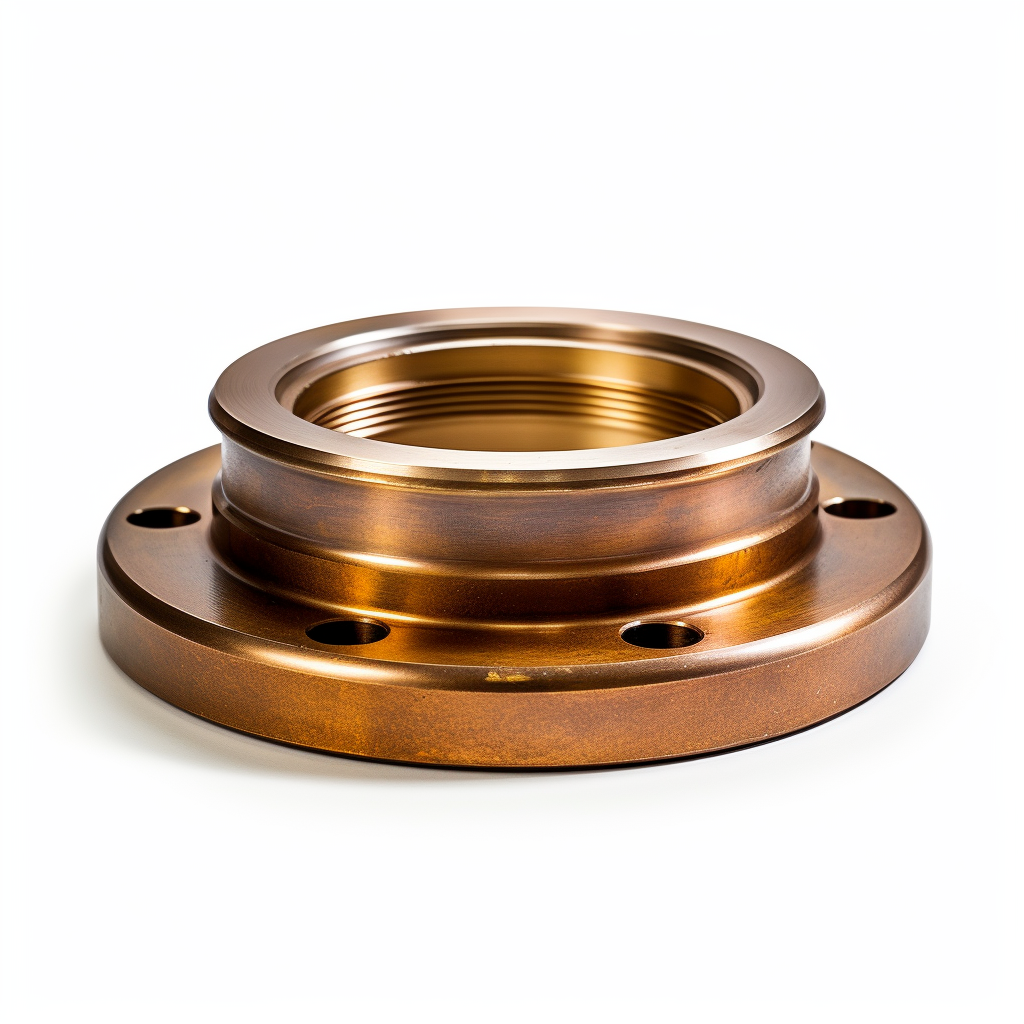
Advantages
- Corrosion Resistance: Bronze is highly resistant to corrosion, making it suitable for marine and outdoor applications.
- Strength: Bronze exhibits excellent strength and durability, making it ideal for load-bearing components.
- Malleability: Bronze can be easily cast, machined, and fabricated into various shapes and forms.
- Low Friction: Bronze alloys with lubricating properties, such as phosphor bronze, offer low friction, making them suitable for bearings and bushings.
- Historical Significance: Bronze has a rich history in art, sculpture, and cultural artifacts, adding to its value.
- Aesthetic Appeal: Bronze's warm and lustrous appearance makes it a popular choice for decorative elements and sculptures.
- Biocompatibility: Certain bronze alloys, such as phosphor bronze, are biocompatible and used in medical and dental applications.
Disadvantages
- Cost: Bronze can be more expensive than some other materials due to the cost of copper and tin.
- Weight: Bronze is denser than many materials, which can be a drawback in weight-sensitive applications.
- Machinability: Some bronze alloys can be challenging to machine, requiring specialized tools and techniques.
- Environmental Impact: Mining and processing copper and tin for bronze production can have environmental consequences.
Common Applications of Bronze
- Marine: Bronze is used in marine components, such as propellers, shafts, and valves, due to its corrosion resistance in seawater.
- Electrical and Electronics: Phosphor bronze is used in electrical connectors, switches, and springs due to its electrical conductivity and corrosion resistance.
- Aerospace: Bronze is used in aerospace applications for bearings, bushings, and components requiring high strength and corrosion resistance.
- Art and Sculpture: Bronze has a long history in art and sculpture due to its aesthetic appeal and durability.
- Architecture: Silicon bronze is used in architectural elements, including door hardware, fasteners, and decorative features, for its corrosion resistance and appearance.
- Automotive: Bronze bearings and bushings are used in automotive components such as engines and transmissions.
- Musical Instruments: Bronze is used in musical instruments, including cymbals and bells, for its resonance and tonal qualities.
- Plumbing and Fittings: Bronze is used in plumbing fittings and valves due to its corrosion resistance and low lead content.
- Jewelry: Bronze is used in jewelry making for its aesthetic qualities and affordability.
Please consult a Canyon Components Engineer about your specific application and we will use our decades of experience to formulate a solution that fits your need.
Types of Bronze
Bronze can come in different variations, depending on its composition and intended use. Some common types of Bronze include the following.
Canyon Components strives to meet all customer service requests. Feel free to contact Canyon Components engineering and let our knowledgeable staff help you design the perfect part for your needs.
Tin Bronze
Known for its excellent corrosion resistance and wear properties, tin bronze is widely used in bearings, bushings, and marine hardware. It typically contains about 12% tin, providing a balance of ductility and strength. This alloy is suitable for applications where resistance to fatigue, shock, and abrasion is essential.
Aluminum Bronze
Containing about 5-11% aluminum, this type offers high strength and excellent corrosion resistance, especially in marine environments. It's used in applications like aircraft parts, marine hardware, and pump components. Aluminum bronze also exhibits good wear resistance and can handle heavy loads.
Silicon Bronze
With a higher silicon content, this bronze variant is known for its good corrosion resistance, making it ideal for outdoor applications like architecture, art, and marine fittings. Silicon bronze is easy to weld and form, offering a combination of strength and ductility.
Phosphor Bronze
Phosphor bronze contains around 0.5-11% tin and a small amount of phosphorus. It's known for its fine grain, high fatigue resistance, and excellent formability. Common uses include electrical connectors, springs, and various types of industrial bearings.
Nickel Bronze
This alloy, enriched with nickel, offers enhanced strength and corrosion resistance. It’s commonly used in decorative applications for its appealing silver color, and in functional components such as valves, pump parts, and ship propellers that require durability in corrosive environments.
Leaded Bronze
Incorporating lead into bronze improves machinability and wear resistance, making it suitable for bearings, bushings, and similar components subject to high-speed and heavy-load applications. Leaded bronze also offers good corrosion resistance and is often used in plumbing and pipe fittings.
Please consult a Canyon Components Engineer about your specific application and we will use our decades of experience to formulate a solution that fits your need.
Manufacturing Options for Bronze
Bronze parts can be manufactured using several methods, each suitable for different applications and part complexities.
Each of these methods has its own advantages, limitations, and cost implications. The choice of manufacturing technique usually depends on factors like the complexity of the design, required precision, material properties, and production volume.
Canyon Components strives to meet all customer service requests. Feel free to contact Canyon Components engineering and let our knowledgeable staff help you design the perfect part for your needs.
Back to Metals Hub
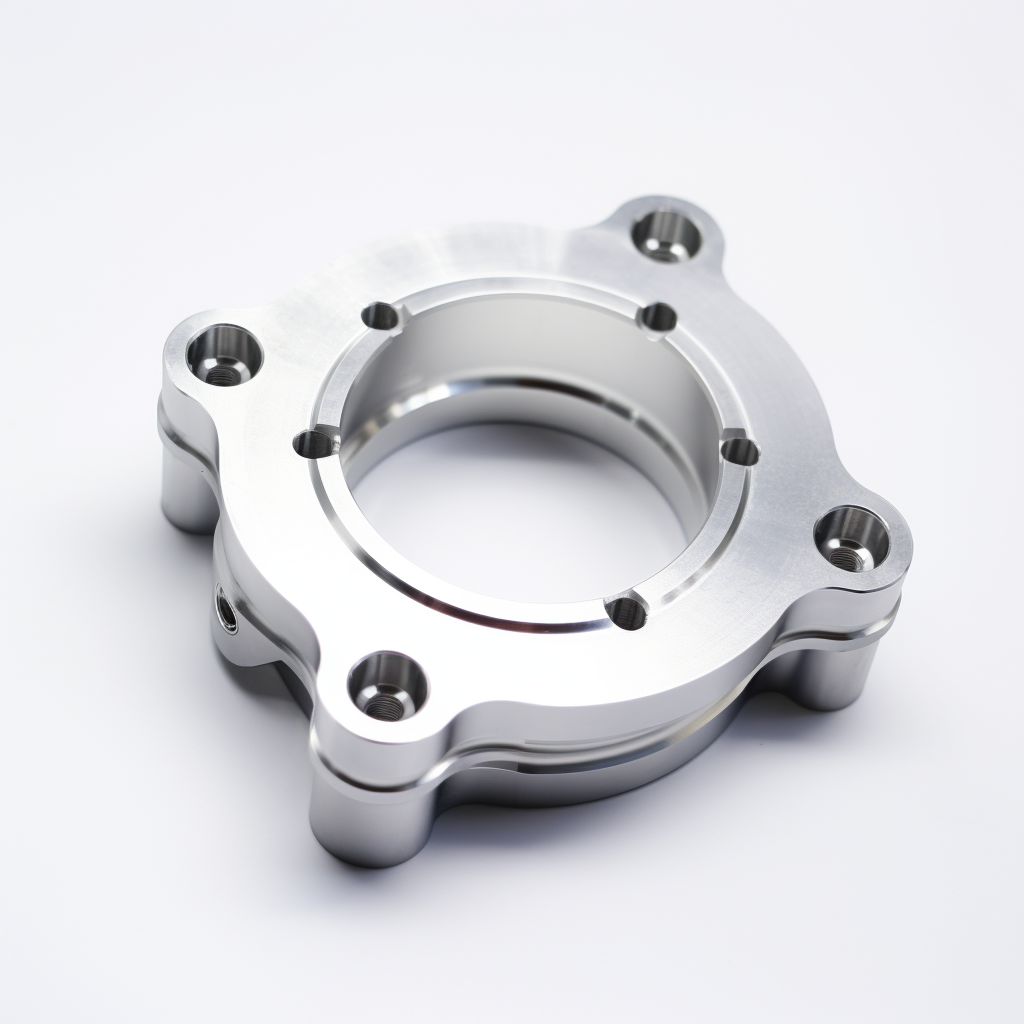
Get A Quote Now!
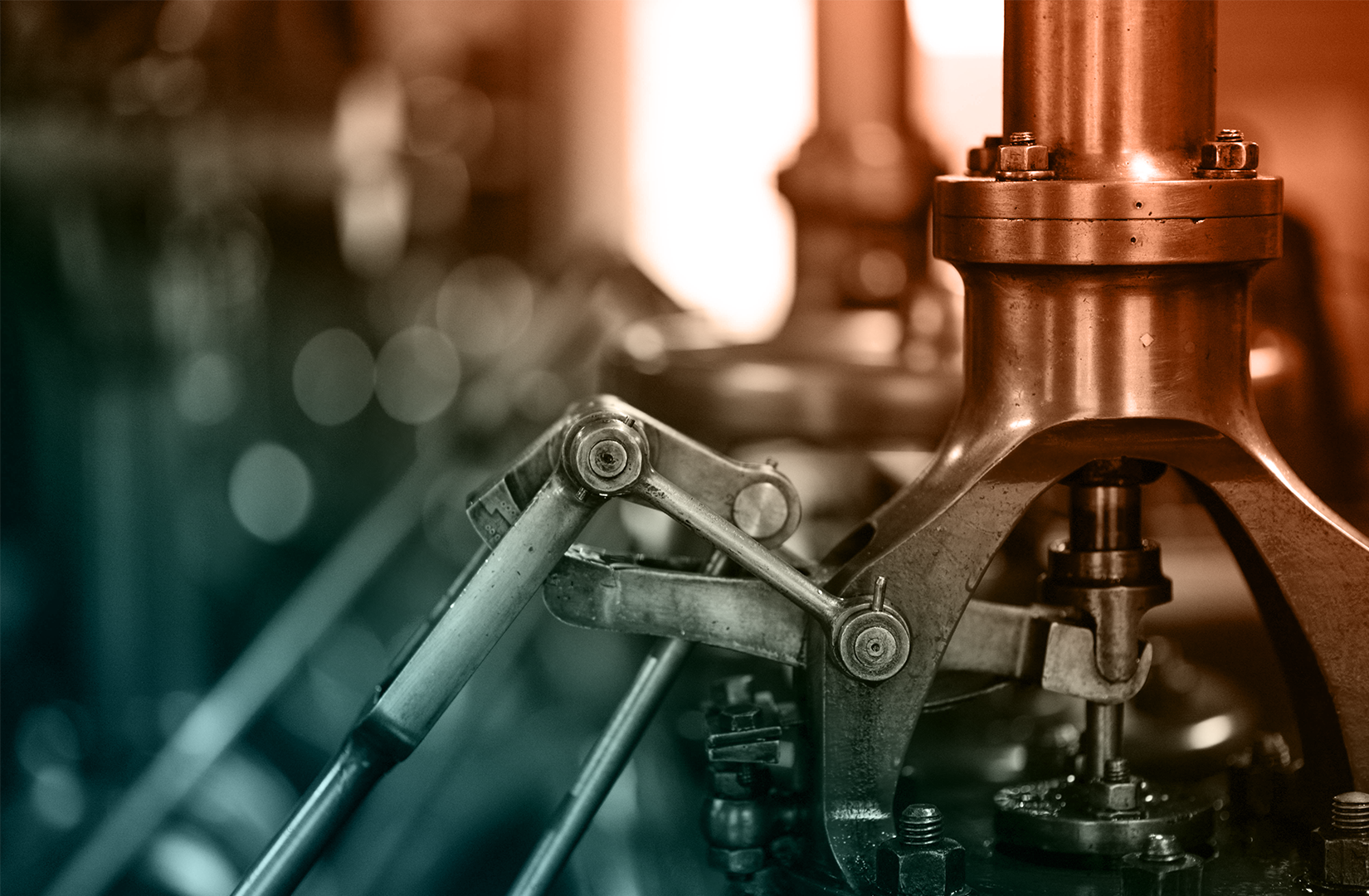
Groove Design References
Learn More
Coatings, Packaging, & Other Services
Learn More
Custom Parts & Custom O-rings
Learn More