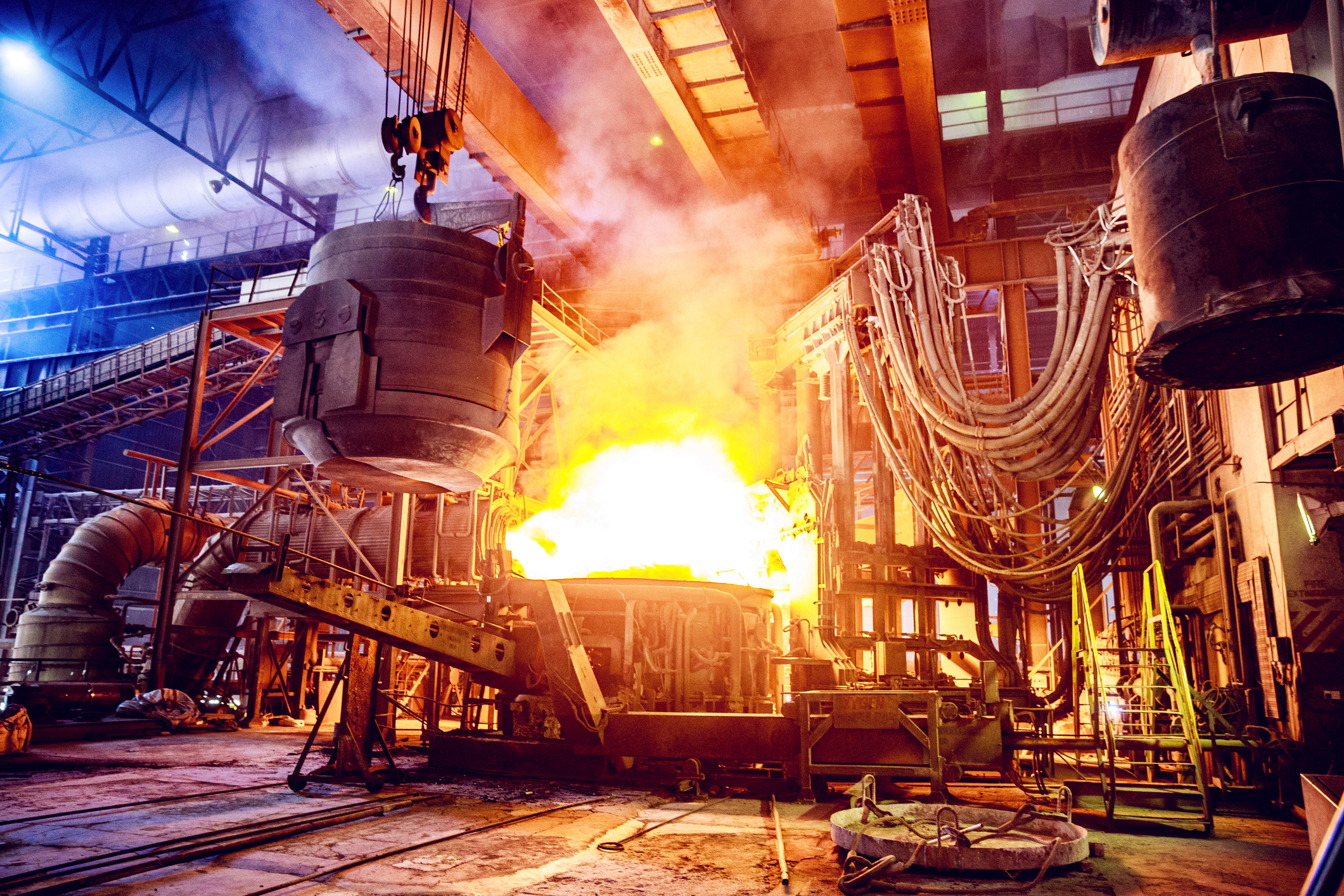
Tungsten Carbide Metal Selection Guide
Tungsten carbide, often referred to simply as carbide, is a remarkable and exceptionally hard material composed of tungsten (W) and carbon (C). It is renowned for its hardness, wear resistance, and high melting point, making it a crucial material in various industrial applications. In this web page, we will explore the different types of tungsten carbide, its numerous advantages and disadvantages, and the diverse industrial uses where tungsten carbide plays a crucial role.
Tungsten Carbide rapid manufacturing, & machined parts are available now!
Check with one of Canyon’s helpful product engineers for an expert material and manufacturing recommendation.
Common names include: Ultra-fine Grain Carbide, Fine Grain Carbide, Medium Grain Carbide, Coarse Grain Carbide, Submicron Carbide.
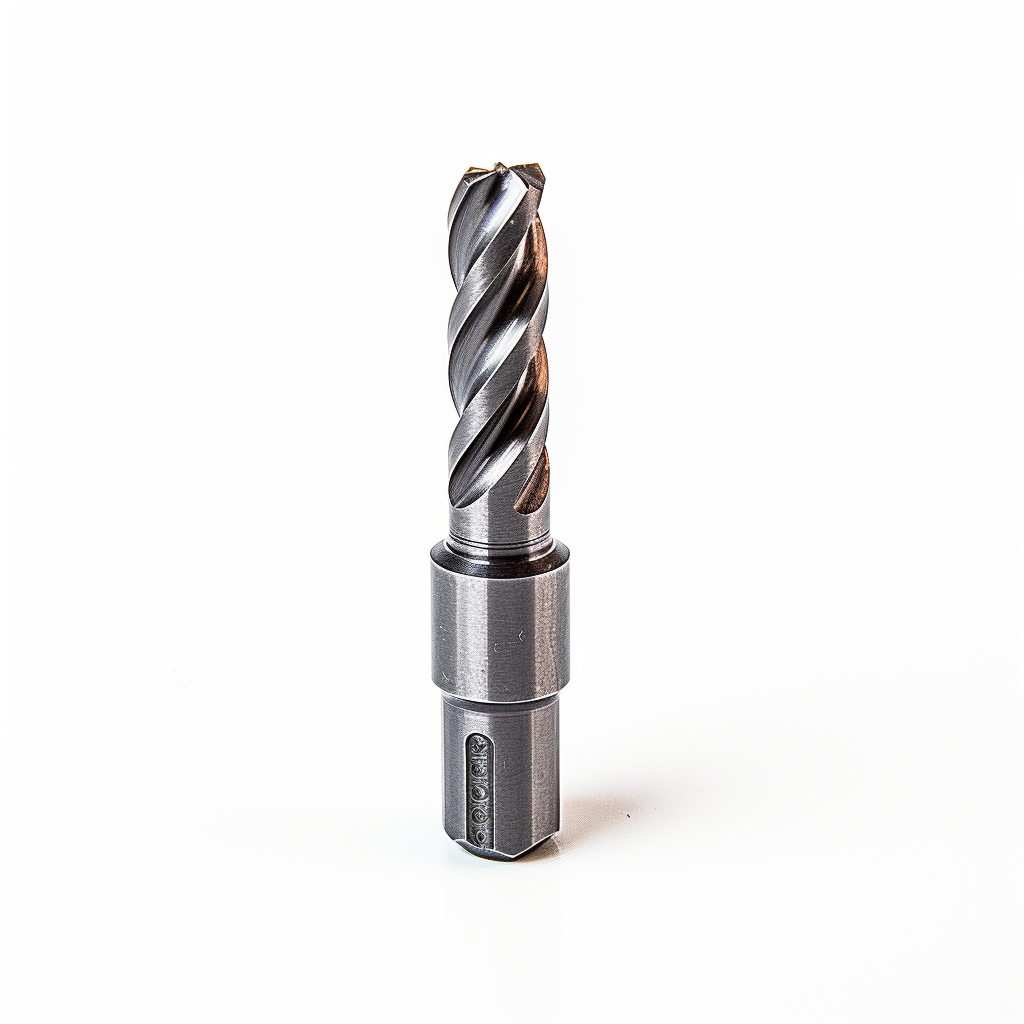
Advantages
- Exceptional Hardness: Tungsten carbide is one of the hardest materials known, making it highly resistant to wear and abrasion.
- High Melting Point: Tungsten carbide has a very high melting point, allowing it to maintain its properties at elevated temperatures.
- Excellent Wear Resistance: Tungsten carbide exhibits exceptional wear resistance, making it suitable for cutting, drilling, and grinding tools.
- Corrosion Resistance: Tungsten carbide is resistant to corrosion from acids and alkalis in many industrial environments.
- Strength and Toughness: Cemented carbide combines hardness with strength and toughness, allowing for efficient cutting and machining.
- Dimensional Stability: Tungsten carbide maintains its shape and dimensions under heavy loads and extreme conditions.
- Chemical Inertness: Tungsten carbide is chemically inert, making it suitable for use in aggressive chemical environments.
Disadvantages
- Brittleness: Tungsten carbide can be brittle and may fracture under heavy impact or shock loads.
- High Cost: The production and machining of tungsten carbide can be expensive, especially for complex shapes and precision components.
- Complex Manufacturing: Manufacturing tungsten carbide components often involves complex processes like sintering and grinding.
- Density: Tungsten carbide is denser than many other materials, which can be a drawback in weight-sensitive applications.
Common Applications of Tungsten Carbide
- Metalworking: Tungsten carbide is used for cutting tools, drills, end mills, and inserts, enhancing the efficiency and longevity of machining operations.
- Mining and Construction: Tungsten carbide is used in drill bits, rock drills, and wear parts for mining and construction equipment due to its wear resistance.
- Oil and Gas: Tungsten carbide is used for downhole drilling tools and wear-resistant components in the oil and gas industry.
- Aerospace: Tungsten carbide is used in aircraft components, including turbine blades and nozzles, due to its high-temperature stability.
- Medical: Tungsten carbide is used for surgical instruments and dental drills due to its biocompatibility and hardness.
- Automotive: Tungsten carbide is used in automotive cutting tools and wear-resistant components for engines and transmissions.
- Chemical Processing: Tungsten carbide is used in pumps, valves, and mixers for its resistance to corrosive chemicals.
- Woodworking: Tungsten carbide is employed in saw blades, router bits, and planer knives for woodworking applications.
- Jewelry: Tungsten carbide is used in the jewelry industry to create durable and scratch-resistant wedding bands and other accessories.
Please consult a Canyon Components Engineer about your specific application and we will use our decades of experience to formulate a solution that fits your need.
Types of Tungsten Carbide
Tungsten Carbide can come in different variations, depending on its composition and intended use. Some common types of Tungsten Carbide include the following.
Canyon Components strives to meet all customer service requests. Feel free to contact Canyon Components engineering and let our knowledgeable staff help you design the perfect part for your needs.
Fine Grain Tungsten Carbide
Characterized by small grain size, this type offers superior hardness and wear resistance. Ideal for precision cutting tools and surgical instruments, it ensures sharp edges and durability. Fine grain tungsten carbide is preferred in applications requiring detailed work and high precision.
Ultrafine Grain Tungsten Carbide
This variant, with even smaller grains than fine grain carbide, provides exceptional hardness and edge retention. It's used in micro-tools for electronics and jewelry making, where extreme precision is vital. Ultrafine grain carbide is also suitable for applications requiring high surface finishes.
Medium Grain Tungsten Carbide
Balancing hardness and toughness, medium grain carbide is used in a variety of cutting and drilling tools. It's suitable for general machining and mining tools, offering a good compromise between wear resistance and impact strength.
Coarse Grain Tungsten Carbide
With larger grain size, it offers increased toughness and shock resistance. Ideal for heavy-duty mining and drilling tools, it withstands high impact applications. Coarse grain carbide is also used in oil and gas drilling industries where robustness is key.
Submicron Tungsten Carbide
This type is known for its high wear resistance and good toughness. Suitable for high-speed cutting tools, it maintains sharpness over prolonged use. Submicron carbide is also used in applications where high-quality surface finishes are required.
Cemented Tungsten Carbide
Comprising tungsten carbide particles cemented with a metal binder, typically cobalt or nickel, it offers a balance of hardness, strength, and toughness. Widely used in cutting tools, wear parts, and molds, cemented carbide is versatile and can be tailored to various industrial applications.
Please consult a Canyon Components Engineer about your specific application and we will use our decades of experience to formulate a solution that fits your need.
Manufacturing Options for Tungsten Carbide
Tungsten Carbide parts can be manufactured using several methods, each suitable for different applications and part complexities.
Each of these methods has its own advantages, limitations, and cost implications. The choice of manufacturing technique usually depends on factors like the complexity of the design, required precision, material properties, and production volume.
Canyon Components strives to meet all customer service requests. Feel free to contact Canyon Components engineering and let our knowledgeable staff help you design the perfect part for your needs.
Back to Metals Hub
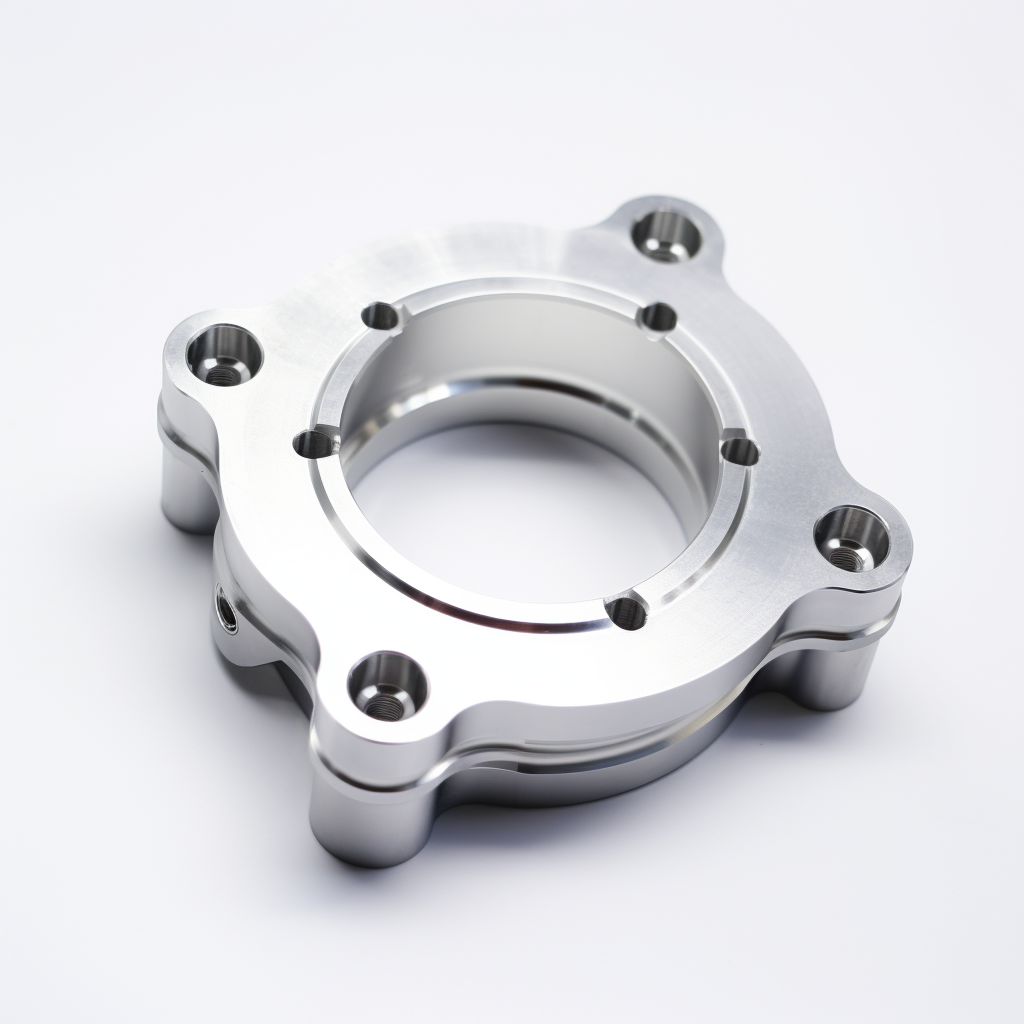
Get A Quote Now!
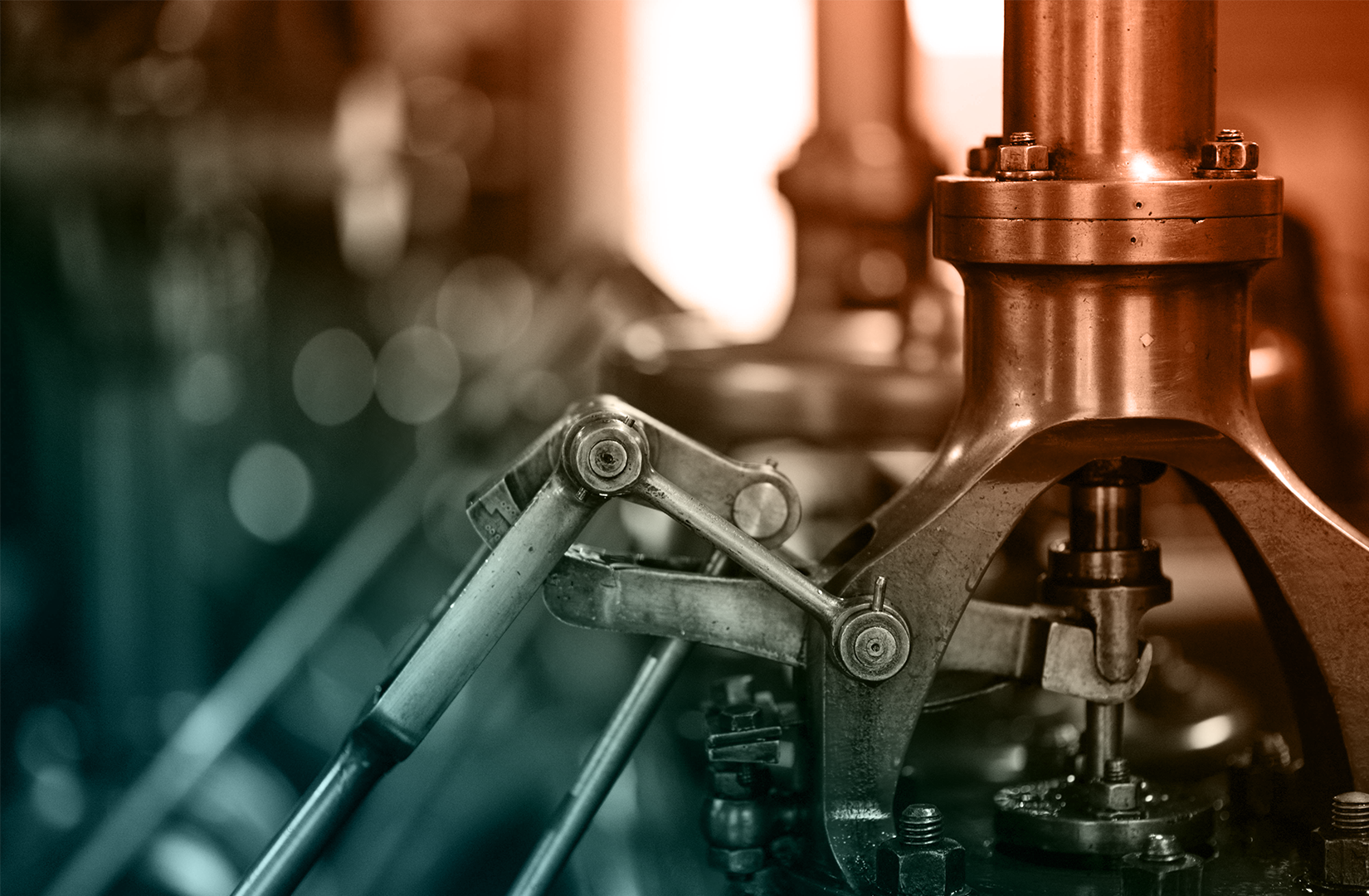
Groove Design References
Learn More
Coatings, Packaging, & Other Services
Learn More
Custom Parts & Custom O-rings
Learn More