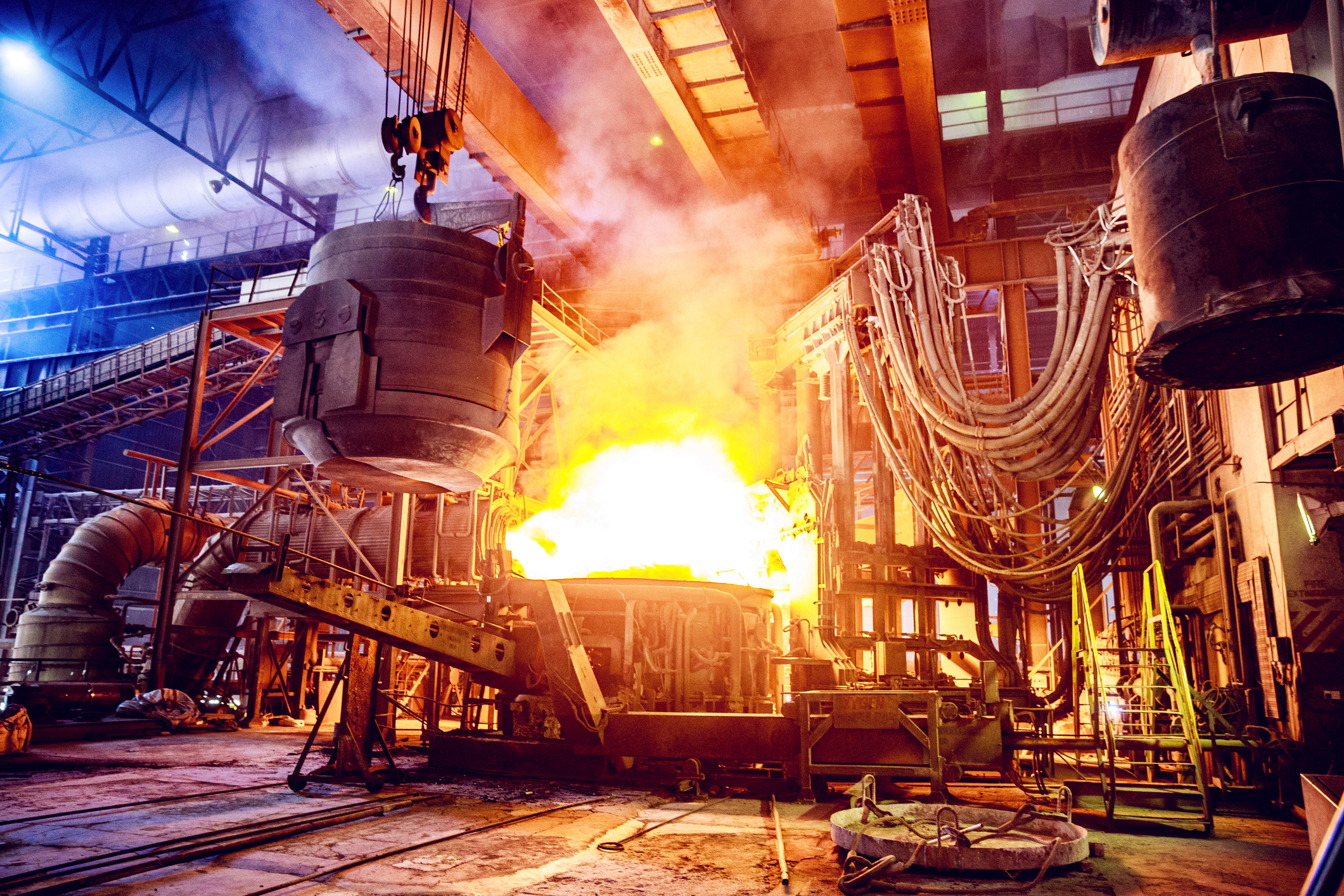
Nickel Metal Selection Guide
Nickel is a versatile and corrosion-resistant metallic element known for its distinctive silver color and excellent properties. It is commonly used in various industrial applications due to its ability to withstand harsh environments and its valuable alloying properties. In this web page, we will explore the different types of nickel, its numerous advantages and disadvantages, and the diverse industrial uses where nickel plays a crucial role.
Nickel rapid manufacturing, & machined parts are available now!
Check with one of Canyon’s helpful product engineers for an expert material and manufacturing recommendation.
Common names include: Nickel 200, Nickel 201, Monel (Nickel-Copper Alloy), Inconel (Nickel-Chromium Alloy), Incoloy (Nickel-Iron-Chromium Alloy), Nimonic (Nickel-Chromium-Cobalt Alloy), Hastelloy (Nickel-Molybdenum Alloy).
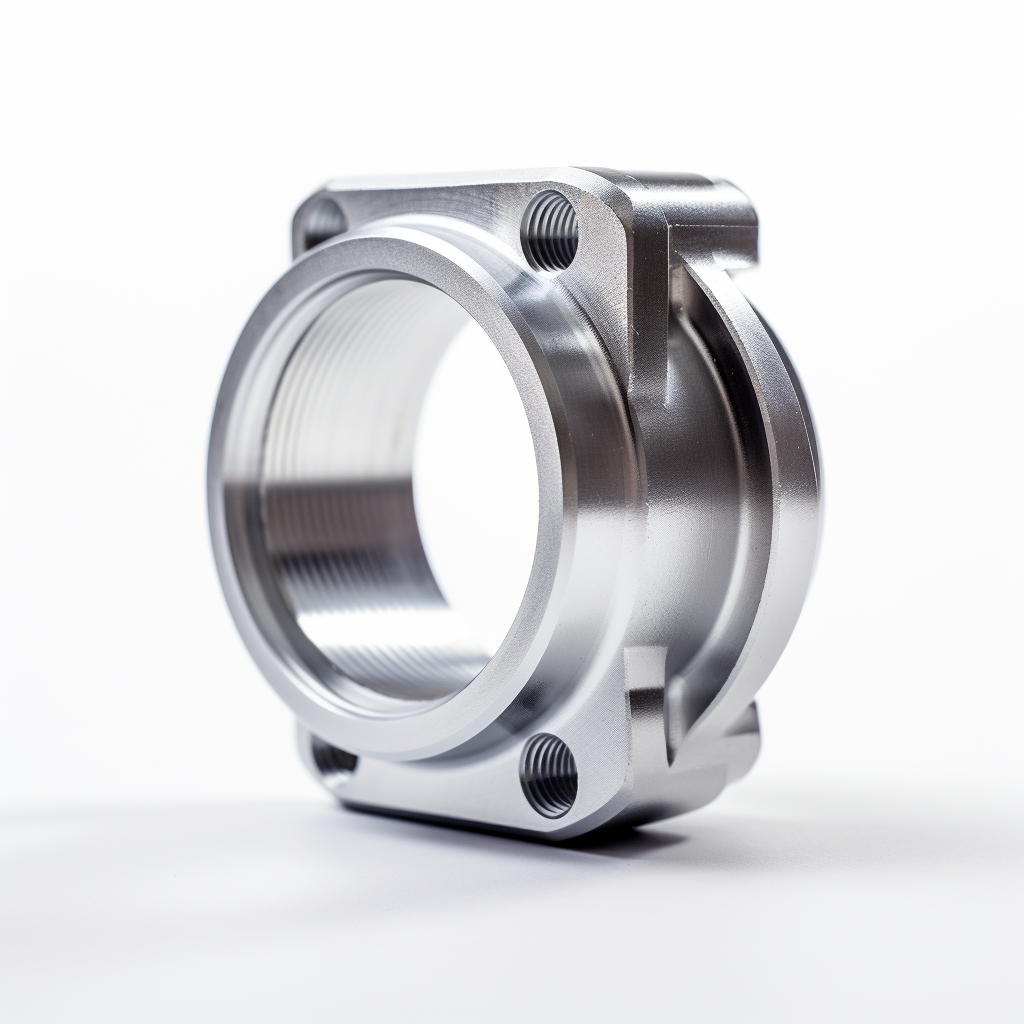
Advantages
- Corrosion Resistance: Nickel and its alloys exhibit outstanding resistance to corrosion, making them suitable for use in aggressive environments, including chemical processing and marine applications.
- High Temperature Resistance: Nickel-based alloys maintain their mechanical properties at elevated temperatures, making them ideal for applications in aerospace, power generation, and high-temperature processing.
- Strength and Toughness: Nickel alloys possess excellent mechanical properties, including strength, toughness, and ductility, allowing for reliable performance in demanding conditions.
- Electrical Conductivity: Nickel has good electrical conductivity, making it valuable in electrical components and wiring.
- Magnetic Properties: Certain nickel alloys, such as permalloy and mu-metal, exhibit high magnetic permeability and are used in electrical transformers and shielding applications.
- Low Thermal Expansion: Nickel alloys have low coefficients of thermal expansion, reducing the risk of distortion and cracking in high-temperature environments.
- Weldability: Nickel and its alloys are typically weldable, allowing for ease of fabrication and repair.
Disadvantages
- Cost: Nickel and its alloys can be more expensive than some other materials due to the cost of nickel and alloying elements.
- Allergic Reactions: Some individuals may experience allergic reactions to nickel, leading to skin irritation.
Common Applications of Nickel
- Chemical Processing: Nickel alloys are used in chemical processing equipment, such as reactors, pipes, and valves, due to their corrosion resistance.
- Aerospace: Nickel-based alloys are used in aircraft engines, turbine components, and exhaust systems due to their high-temperature resistance and strength.
- Electronics: Nickel is used in electronic components, including connectors and contacts, due to its electrical conductivity.
- Marine: Nickel alloys are used in marine components, such as seawater-resistant fasteners and valves.
- Oil and Gas: Nickel alloys are employed in oil and gas processing equipment, including heat exchangers and downhole components.
- Electroplating: Nickel plating is used to provide a protective and decorative coating on various materials, including jewelry, automotive parts, and household items.
- Power Generation: Nickel-based alloys are used in power generation equipment, such as gas turbines and heat exchangers, due to their high-temperature performance.
- Medical: Nickel is used in medical implants and devices due to its biocompatibility and corrosion resistance.
- Electromagnetic Shielding: Nickel alloys with high magnetic permeability are used in shielding applications to protect sensitive electronics from electromagnetic interference.
Please consult a Canyon Components Engineer about your specific application and we will use our decades of experience to formulate a solution that fits your need.
Types of Nickel
Nickel can come in different variations, depending on its composition and intended use. Some common types of Nickel include the following.
Canyon Components strives to meet all customer service requests. Feel free to contact Canyon Components engineering and let our knowledgeable staff help you design the perfect part for your needs.
Pure Nickel
Known for its corrosion resistance and magnetic properties, pure nickel is primarily used in the production of alloys, plating, and as a catalyst. Its high ductility and thermal conductivity make it suitable for various industrial applications, including electronics and specialty steels.
Nickel-Copper Alloys (Monel)
These alloys offer excellent corrosion resistance, especially in marine and chemical environments. Commonly used in marine engineering, chemical processing equipment, and coinage, their strength and durability in harsh conditions are highly valued.
Nickel-Chromium Alloys (Inconel)
Characterized by their high resistance to heat and corrosion, these alloys are ideal for extreme environments, such as aerospace engines, nuclear reactors, and chemical plants. They retain strength over a wide temperature range.
Nickel-Iron Alloys (Invar and Permalloy)
These alloys are known for their unique magnetic properties. Invar, with its low thermal expansion, is used in precision instruments, while Permalloy, with high magnetic permeability, is ideal for magnetic shielding and electrical transformers.
Nickel-Molybdenum Alloys (Hastelloy)
Offering excellent chemical resistance, especially to reducing acids, these alloys are used in chemical processing industries, pollution control, and waste treatment. They are known for their durability in corrosive environments.
Nickel-Titanium Alloys (Nitinol)
Famous for their shape memory and superelastic properties, these alloys are used in medical devices, including stents and orthodontic wires, and in actuators and sensors. Their ability to return to a predetermined shape after deformation is unique and valuable in various applications.
Please consult a Canyon Components Engineer about your specific application and we will use our decades of experience to formulate a solution that fits your need.
Manufacturing Options for Nickel
Nickel parts can be manufactured using several methods, each suitable for different applications and part complexities.
Each of these methods has its own advantages, limitations, and cost implications. The choice of manufacturing technique usually depends on factors like the complexity of the design, required precision, material properties, and production volume.
Canyon Components strives to meet all customer service requests. Feel free to contact Canyon Components engineering and let our knowledgeable staff help you design the perfect part for your needs.
Back to Metals Hub
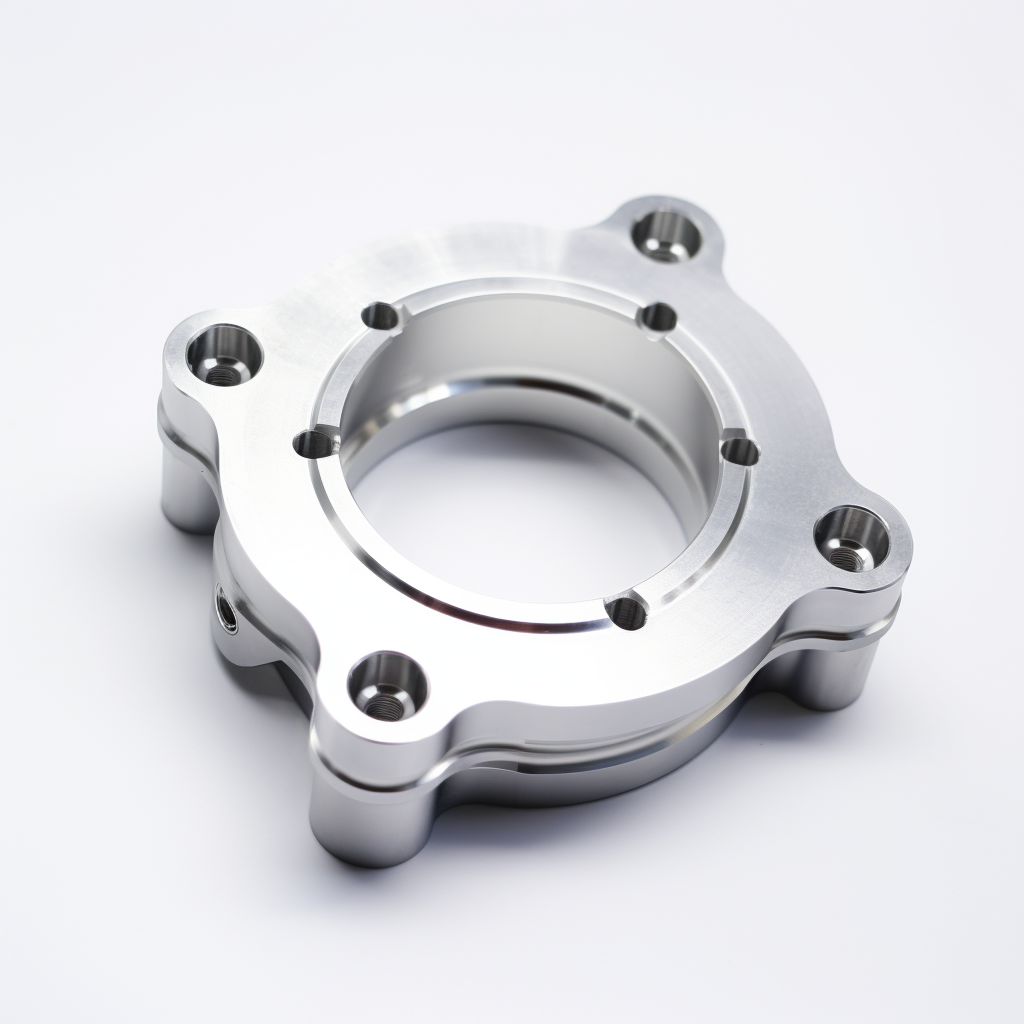
Get A Quote Now!
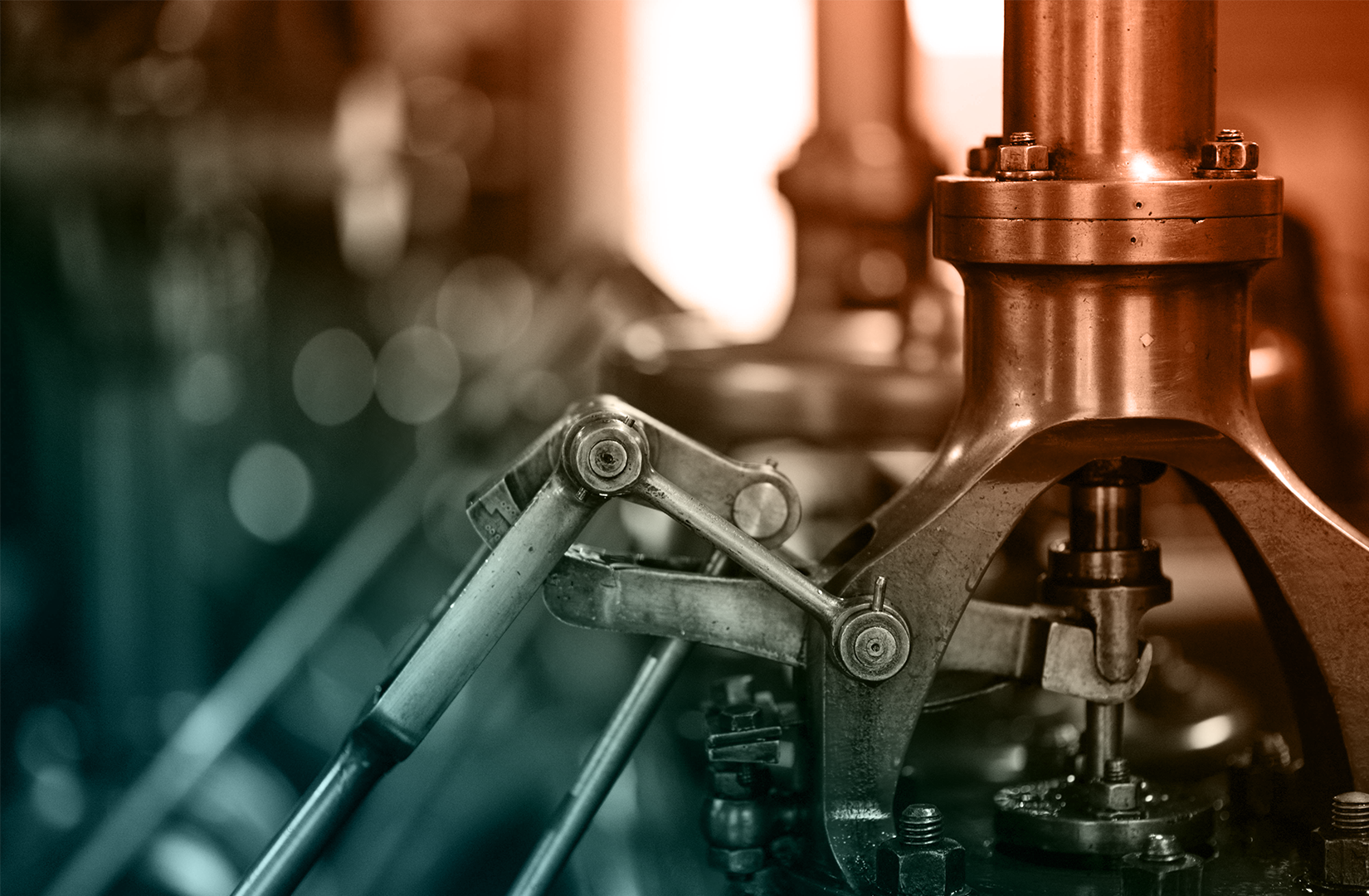
Groove Design References
Learn More
Coatings, Packaging, & Other Services
Learn More
Custom Parts & Custom O-rings
Learn More