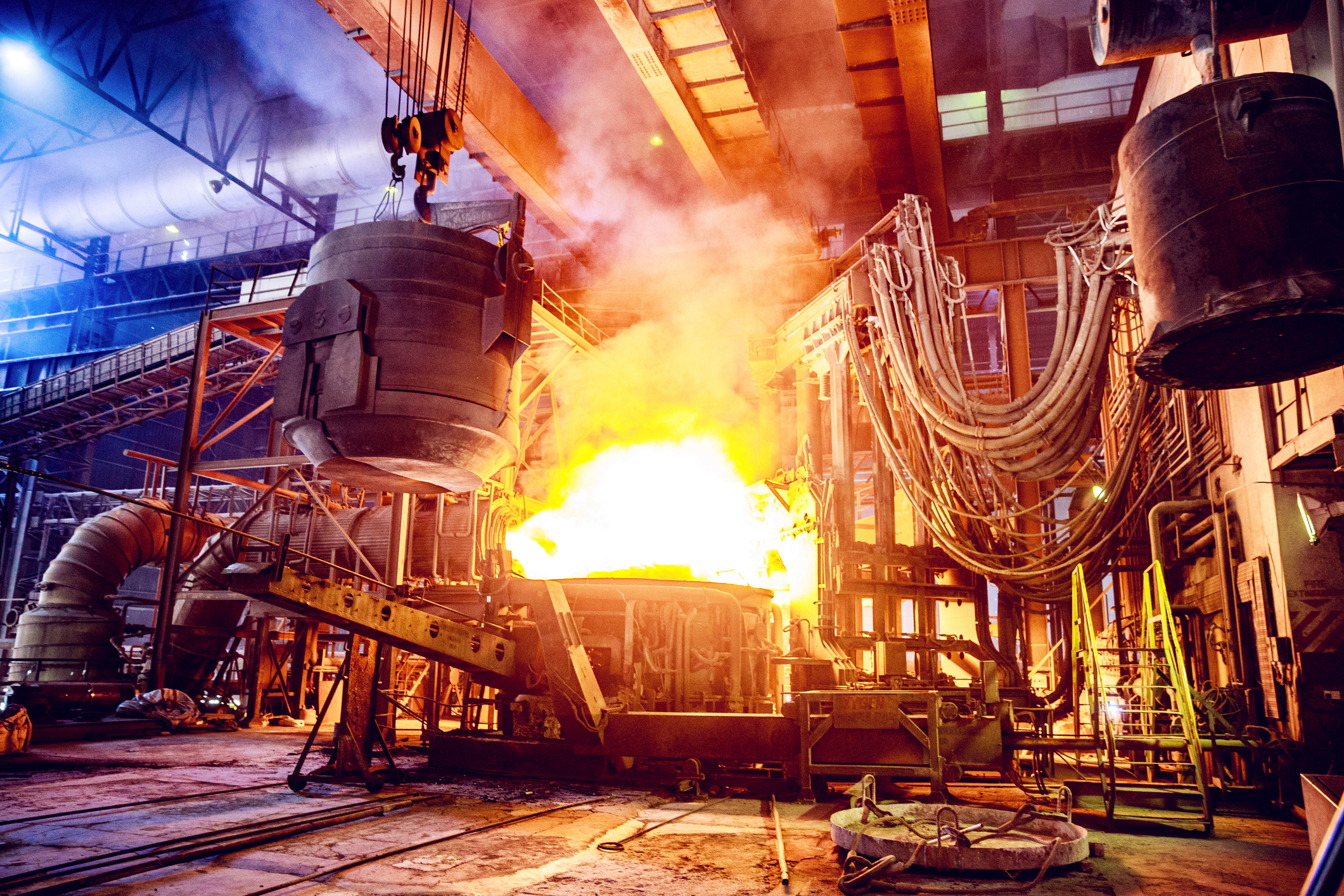
POM Plastic (Polyoxymethylene, Acetal) Selection Guide
POM (Polyoxymethylene), also known as acetal or polyacetal, is a high-performance engineering thermoplastic known for its excellent mechanical properties, low friction, and high stiffness. In this web page, we will explore the different types of POM, its numerous advantages and disadvantages, and the diverse industrial applications where POM plays a crucial role.
POM (Polyoxymethylene, Acetal) rapid manufacturing, & custom molded parts are available now!
Check with one of Canyon’s helpful product engineers for an expert material and manufacturing recommendation.
Common names include: POM (Polyoxymethylene, Acetal), Trade Names: Delrin®, Semitron® ESD, Ultraform®, Hostaform®/Celanex®, Ensital® SD, Duracon®, Kepital®, Tecaform®, Acetron®, Celcon®, Pomalux®, SUSTARIN®, TECAFORM®.
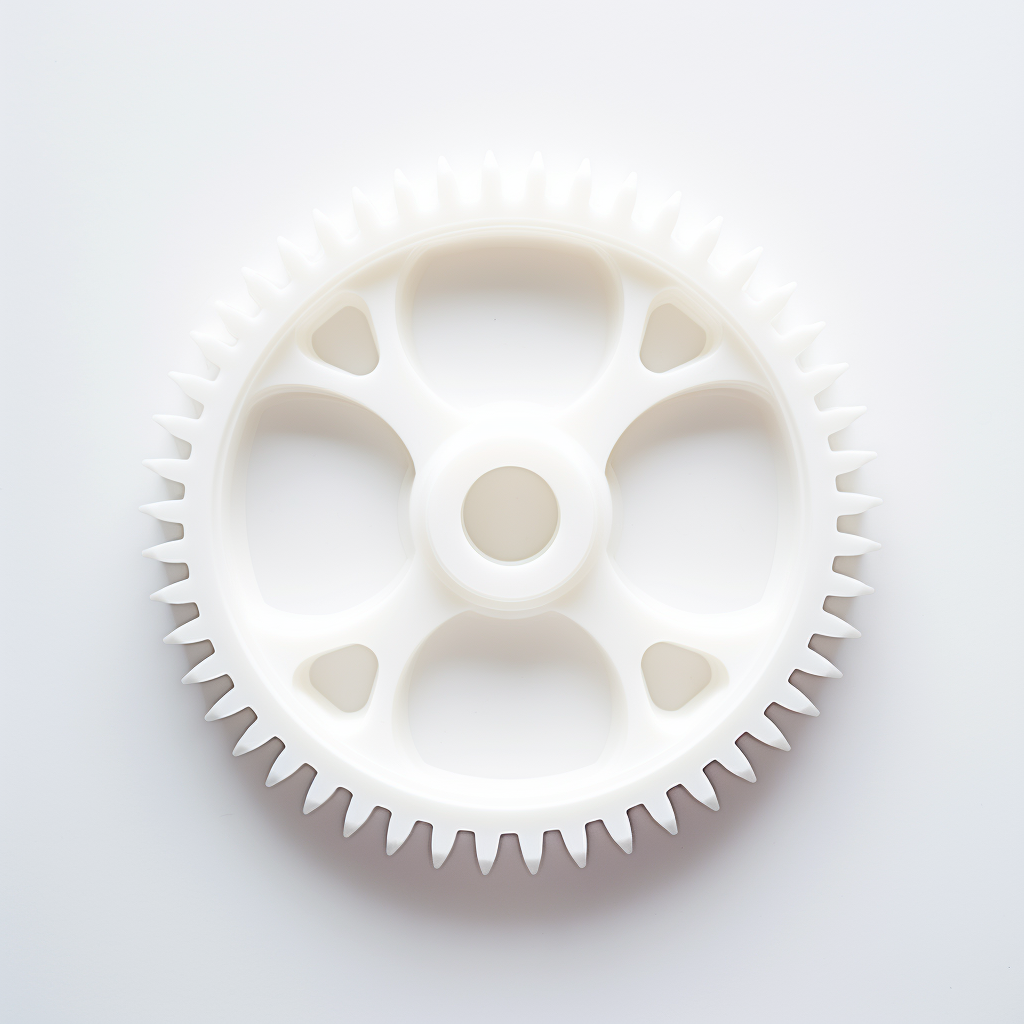
Advantages
- High Mechanical Strength: POM exhibits excellent mechanical properties, including high tensile strength and stiffness, making it suitable for load-bearing applications.
- Low Friction: POM has a low coefficient of friction, which reduces wear and ensures smooth operation in sliding or rotating applications.
- Dimensional Stability: POM has excellent dimensional stability, maintaining its shape and size over a wide temperature range.
- Chemical Resistance: POM is resistant to many chemicals, making it suitable for use in a variety of industrial environments.
- Low Moisture Absorption: POM has low water absorption, ensuring consistent performance in humid conditions.
- Easy Machinability: POM is easy to machine, allowing for the precise fabrication of intricate parts.
- Electrical Insulation: POM is a good electrical insulator, making it suitable for electrical and electronic applications.
Disadvantages
- Not Suitable for High-Temperature Environments: POM has a lower heat resistance compared to some other engineering plastics and may soften or deform at elevated temperatures.
- Flammability: POM is flammable and can release toxic fumes when burned. Flame-retardant grades are available to address this issue.
- Not Biodegradable: POM is not biodegradable, and its disposal in landfills contributes to plastic waste.
Common Applications of POM
- Automotive: POM is used in automotive applications for gears, bearings, bushings, fuel systems, and interior components due to its excellent mechanical properties and low friction.
- Aerospace: POM may find use in aircraft components such as control systems, hinges, and interior parts due to its lightweight nature and dimensional stability.
- Electrical and Electronics: POM is used for electrical connectors, insulators, and precision parts in electronic devices due to its electrical insulating properties and dimensional stability.
- Machinery and Equipment: POM is employed in industrial machinery for various components such as conveyor belts, couplings, valve bodies, and rollers due to its mechanical strength and low friction.
- Consumer Goods: POM is used in various consumer products like zippers, fasteners, and kitchen appliances due to its low friction and wear resistance.
- Medical Devices: POM is used in medical devices such as syringes, orthopedic implants, and dental components due to its biocompatibility and easy machinability.
- Sporting Goods: POM is used in sporting equipment such as ski bindings, gears, and firearm components due to its durability and low friction properties.
Please consult a Canyon Components Engineer about your specific application and we will use our decades of experience to formulate a solution that fits your need.
Types of POM
POM can come in different variations, depending on its composition and intended use. Some common types of POM include the following.
Canyon Components strives to meet all customer service requests. Feel free to contact Canyon Components engineering and let our knowledgeable staff help you design the perfect part for your needs.
Homopolymer POM (POM-H)
POM-H is known for its high mechanical strength and rigidity. Ideal for precision parts in high-load mechanical applications, such as gears, bearings, and automotive components. It offers excellent dimensional stability and resistance to solvents and chemicals, making it a popular choice in complex engineering applications.
Copolymer POM (POM-C)
POM-C provides better chemical resistance and is less prone to thermal degradation compared to POM-H. It's used in parts that require high stability and resistance to hot water and alkalis, such as pump and valve components. POM-C also exhibits lower moisture absorption, enhancing its dimensional stability.
Reinforced POM
This type includes additives like glass fibers or carbon to enhance mechanical properties like strength, stiffness, and thermal stability. It's suitable for more demanding applications that require additional structural integrity, such as high-performance industrial gears and automotive parts.
Impact Modified POM
Specifically designed for applications requiring high impact resistance, this variant of POM is perfect for products subjected to shock or impact, such as sports equipment and safety components. It retains the general characteristics of POM while offering increased toughness.
UV-Stabilized POM
This version includes UV stabilizers to resist degradation caused by prolonged exposure to sunlight. It’s ideal for outdoor applications, including gardening equipment and automotive exterior parts, where maintaining material integrity and color over time is essential.
POM with PTFE
Incorporating PTFE (Polytetrafluoroethylene) enhances the lubricity of POM, reducing friction and wear. This makes it ideal for applications where low friction is crucial, like in sliding bearings, gears, and moving mechanical parts. This combination results in components that operate more smoothly and have a longer service life.
Please consult a Canyon Components Engineer about your specific application and we will use our decades of experience to formulate a solution that fits your need.
Manufacturing Options for POM
POM parts can be manufactured using several methods, each suitable for different applications and part complexities.
Each of these methods has its own advantages, limitations, and cost implications. The choice of manufacturing technique usually depends on factors like the complexity of the design, required precision, material properties, and production volume.
Canyon Components strives to meet all customer service requests. Feel free to contact Canyon Components engineering and let our knowledgeable staff help you design the perfect part for your needs.
Back to Plastics Hub
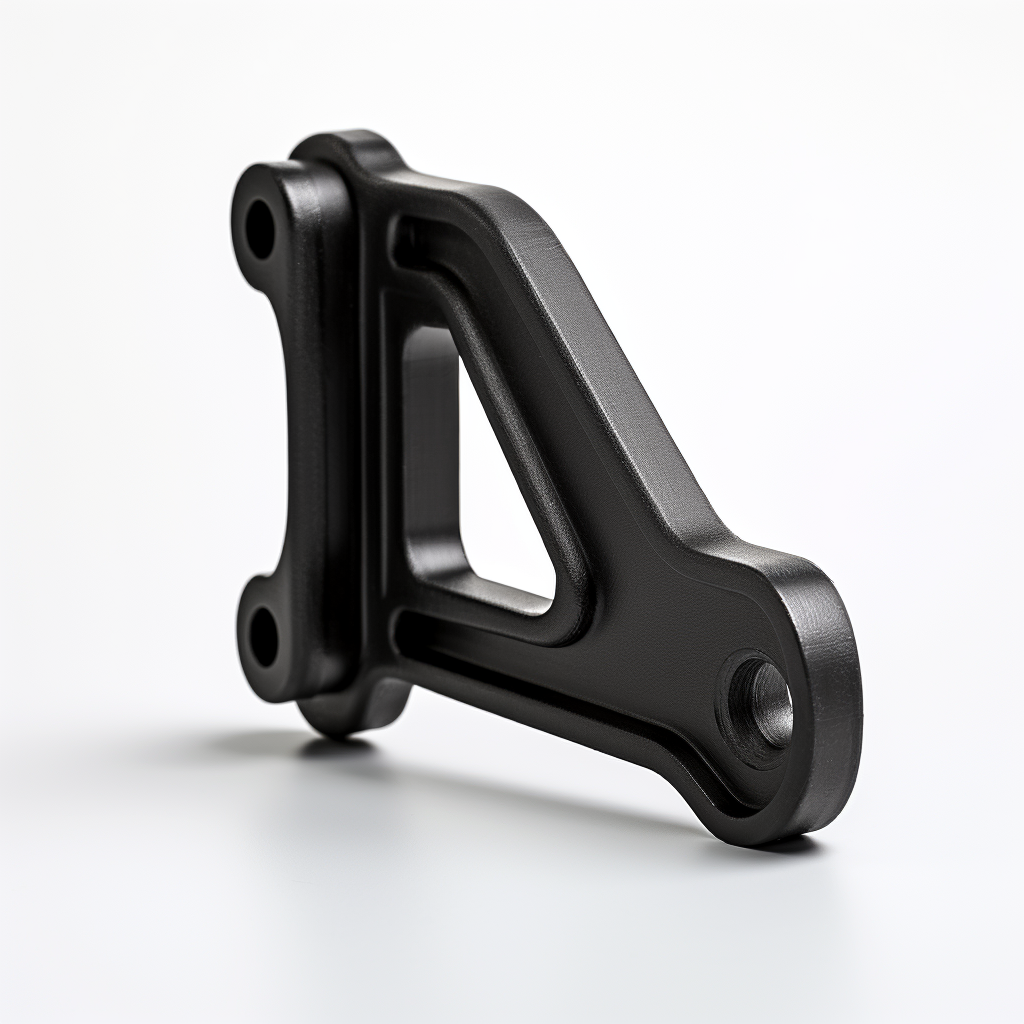
Get A Quote Now!
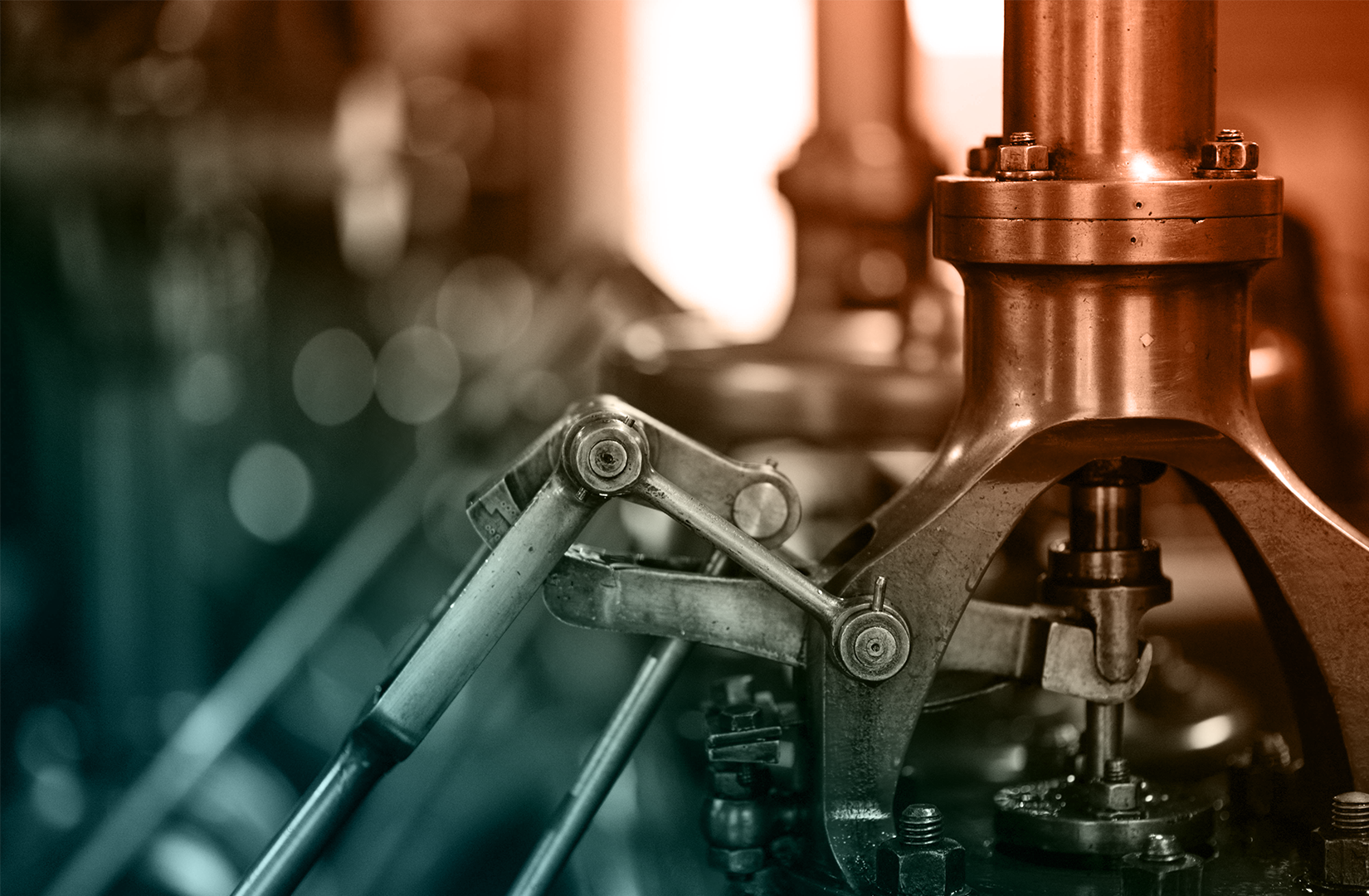
Groove Design References
Learn More
Coatings, Packaging, & Other Services
Learn More
Custom Parts & Custom O-rings
Learn More