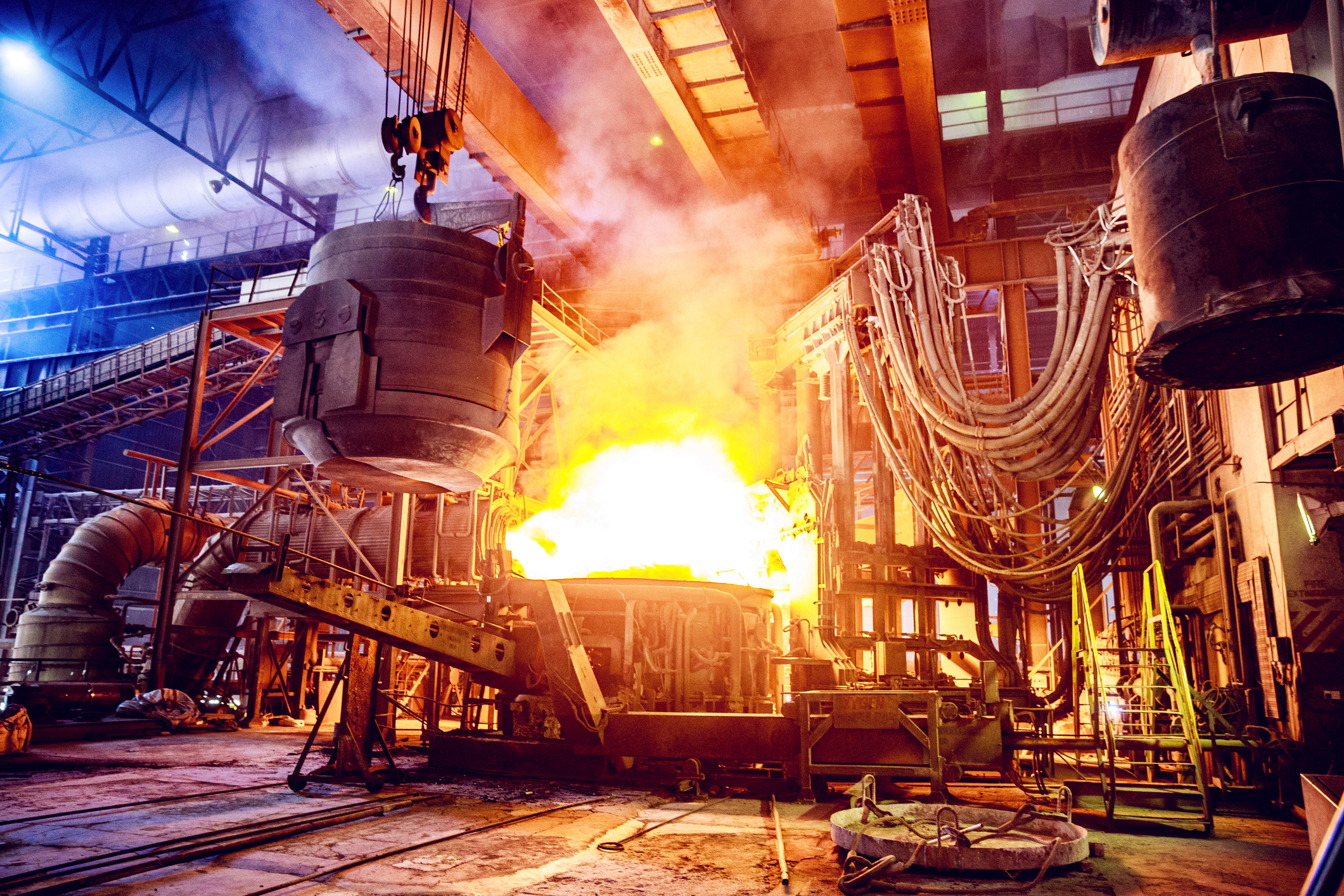
Zinc Alloy Metal Selection Guide
Zinc alloy metal is a group of materials created by combining zinc with other metallic elements to form alloys. These alloys are known for their versatility, corrosion resistance, and ease of casting, making them valuable in various industrial applications. In this web page, we will explore the different types of zinc alloys, their numerous advantages and disadvantages, and the diverse industrial uses where zinc alloy metals play a crucial role.
Zinc Alloy rapid manufacturing, & machined parts are available now!
Check with one of Canyon’s helpful product engineers for an expert material and manufacturing recommendation.
Common names include: Zamak 3, Zamak 5, Zamak 7, ZA-8, ZA-12, ZA-27, ACuZinc5.
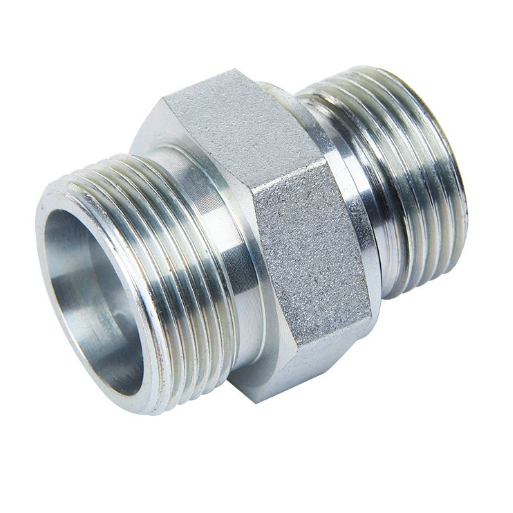
Advantages
- Corrosion Resistance: Zinc alloy metals are naturally corrosion-resistant, making them suitable for outdoor and marine applications.
- Ease of Casting: Zinc alloys have a low melting point and excellent fluidity, allowing for intricate and precise casting, making them ideal for die casting.
- Dimensional Stability: Zinc alloys exhibit minimal shrinkage during solidification, ensuring accurate and consistent parts.
- Recyclability: Zinc is highly recyclable, contributing to sustainability efforts and reducing environmental impact.
- Cost-Efficiency: Zinc alloys are cost-effective materials due to the abundance of zinc and the ease of processing.
- Low Environmental Impact: Zinc alloys have a low environmental footprint in terms of resource extraction and production emissions.
Disadvantages
- Low Melting Point: Zinc alloys have relatively low melting points, limiting their use in high-temperature applications.
- Brittleness: Some zinc alloys may exhibit lower impact resistance and ductility compared to other materials.
- Lead Content: Alloys containing lead may raise environmental and health concerns due to the toxicity of lead.
Common Applications of Zinc Alloy
- Automotive: Zinc alloys are used in automotive parts, including door handles, dashboard components, and brackets, due to their cost-efficiency and ease of casting.
- Electronics: Zinc alloys are used in electrical connectors, housings, and heat sinks due to their corrosion resistance and conductivity.
- Construction: Zinc alloy architectural hardware, such as door handles, locks, and window fittings, benefits from corrosion resistance and aesthetic appeal.
- Marine: Zinc alloys are used in marine components like boat fittings, propellers, and hardware due to their resistance to saltwater corrosion.
- Consumer Goods: Zinc alloy metals are used in various consumer goods, including jewelry, belt buckles, and zippers, for their affordability and casting capabilities.
- Die Casting: Zinc alloys are favored materials for die casting processes, producing intricate and precise parts for a wide range of industries.
- Soldering and Brazing: Zinc-tin alloys are used in soldering and brazing applications, providing reliable joining of electrical and plumbing components.
- Medical Devices: Some zinc alloys are used in medical devices and instruments due to their corrosion resistance and biocompatibility.
Please consult a Canyon Components Engineer about your specific application and we will use our decades of experience to formulate a solution that fits your need.
Types of Zinc Alloy
Zinc Alloy can come in different variations, depending on its composition and intended use. Some common types of Zinc Alloy include the following.
Canyon Components strives to meet all customer service requests. Feel free to contact Canyon Components engineering and let our knowledgeable staff help you design the perfect part for your needs.
Zamak 3
The most popular and widely used zinc alloy, known for its excellent balance of strength, ductility, and castability. It's ideal for die-casting applications, such as automotive parts, hardware, and toys. Zamak 3 offers good surface finish and dimensional stability.
Zamak 5
Similar to Zamak 3 but with higher copper content, which provides increased strength and hardness. This makes it suitable for mechanical components requiring extra durability, like gears and pump parts. Zamak 5 is also used in die-casting for decorative finishes.
Zamak 7
A variation of Zamak 3 with a lower magnesium content, resulting in improved ductility and fluidity. It's ideal for intricate die-castings, such as precision instruments and art objects, where fine detail and smooth surfaces are required.
ZA-8
A high-strength zinc-aluminum alloy, suitable for both die casting and permanent mold applications. ZA-8 is used when more strength than typical Zamak alloys is needed, such as in automotive safety components and electronic devices.
ZA-12
Offering a good balance between castability, strength, and cost-effectiveness, ZA-12 is used in various applications like engine components, business machines, and building hardware. It can be cast using various methods, including die, permanent mold, and sand casting.
ZA-27
The strongest of the ZA series, with the highest aluminum content. It's used in demanding applications that require high strength and low weight, such as high-speed machinery parts and aerospace components. ZA-27 has excellent bearing properties and is also used in high-load bearing applications.
Please consult a Canyon Components Engineer about your specific application and we will use our decades of experience to formulate a solution that fits your need.
Manufacturing Options for Zinc Alloy
Zinc Alloy parts can be manufactured using several methods, each suitable for different applications and part complexities.
Each of these methods has its own advantages, limitations, and cost implications. The choice of manufacturing technique usually depends on factors like the complexity of the design, required precision, material properties, and production volume.
Canyon Components strives to meet all customer service requests. Feel free to contact Canyon Components engineering and let our knowledgeable staff help you design the perfect part for your needs.
Back to Metals Hub
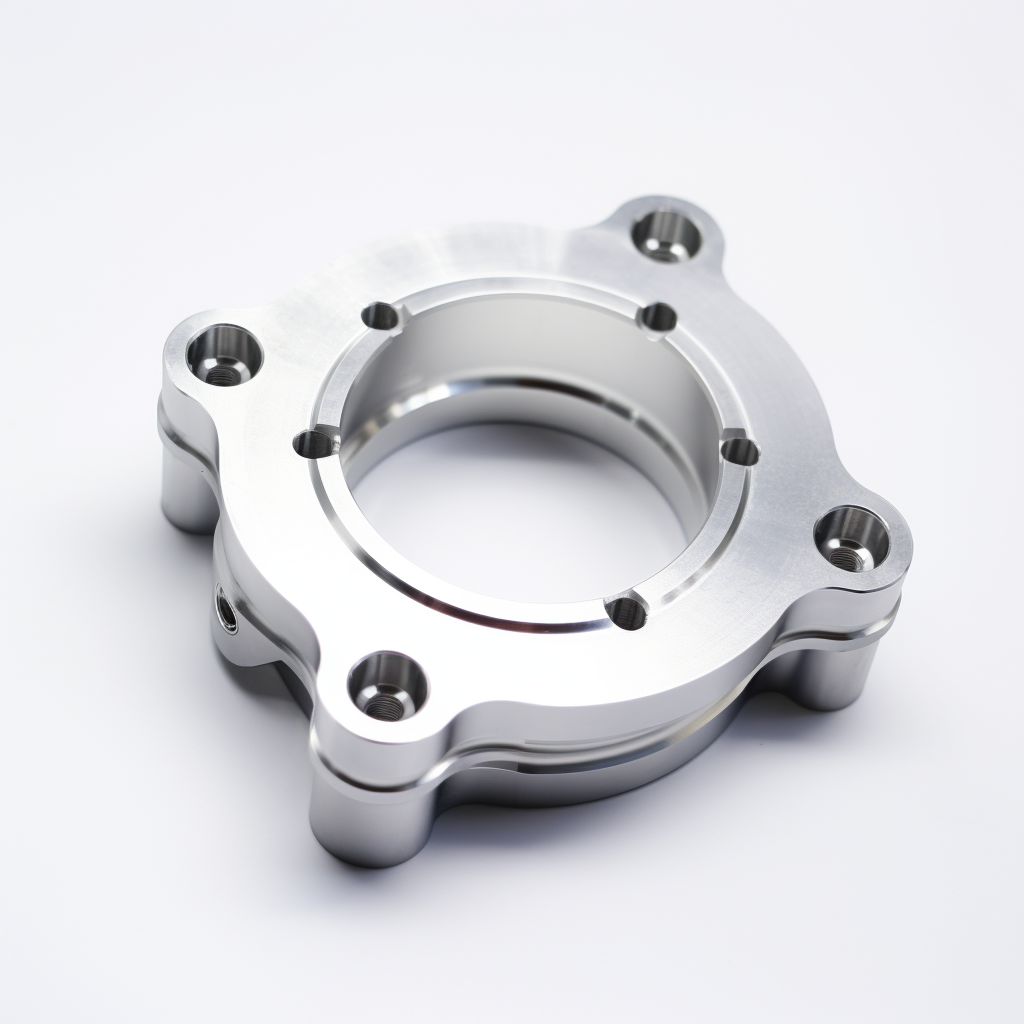
Get A Quote Now!
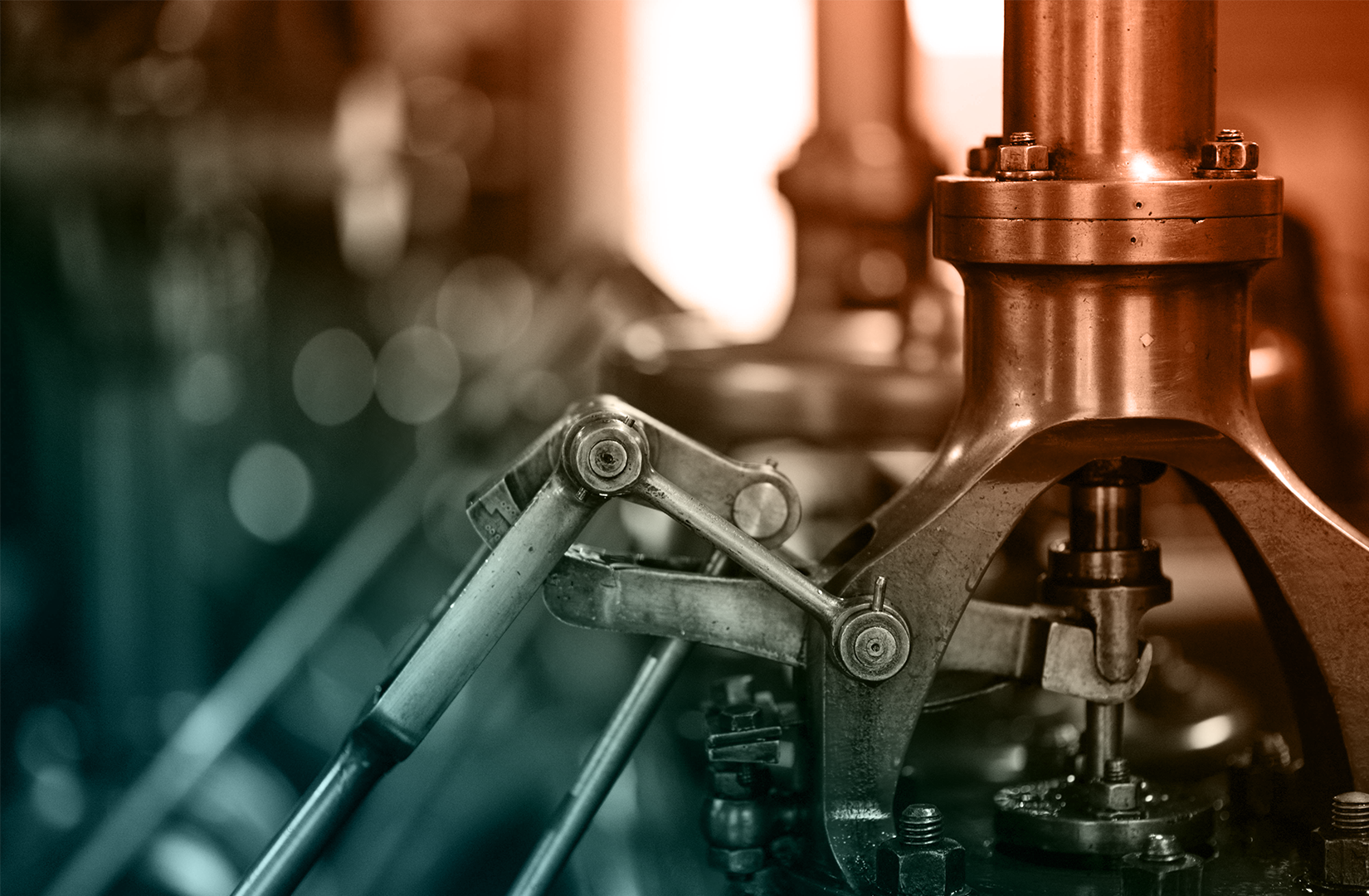
Groove Design References
Learn More
Coatings, Packaging, & Other Services
Learn More
Custom Parts & Custom O-rings
Learn More