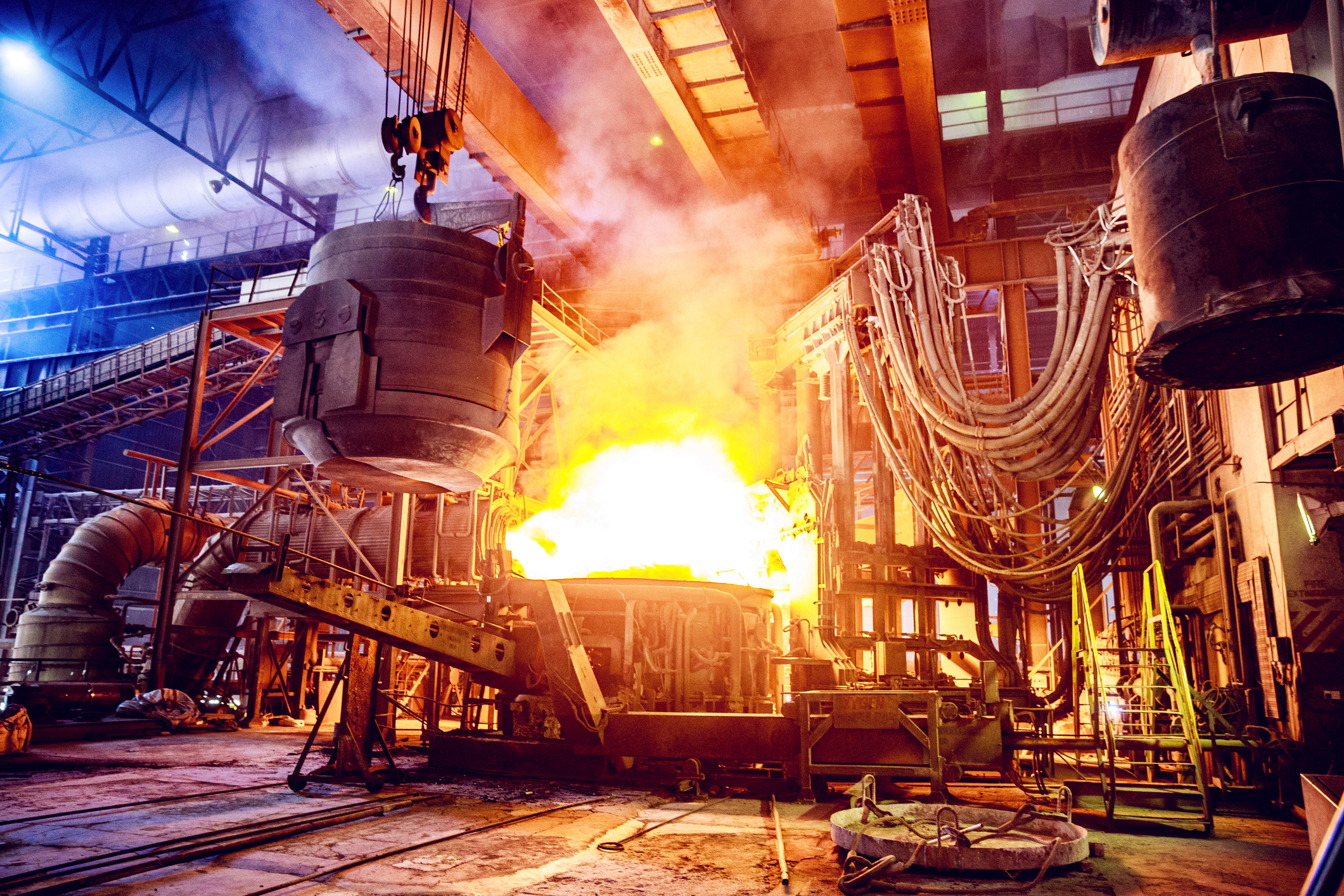
Rotational Molding
Rotational molding, also known as rotomolding, is a unique manufacturing process used to create hollow, seamless products with complex shapes. It involves rotating a mold while heating and melting a polymer to form the desired object. In this web page, we will explore the different types of rotational molding, their advantages and disadvantages, and the diverse range of industrial applications. Additionally, we'll provide a list of materials commonly used in rotational molding manufacturing. Custom Rotational Molded parts available now!
Check with one of Canyon’s helpful product engineers for an expert material and manufacturing recommendation.
Common terminology includes: Rock and roll rotational molding, clamshell rotational molding, shuttle rotational molding, swing arm rotational molding, carousel rotational molding, vertical rotational molding, multi-arm rotational molding, independent-arm rotational molding.
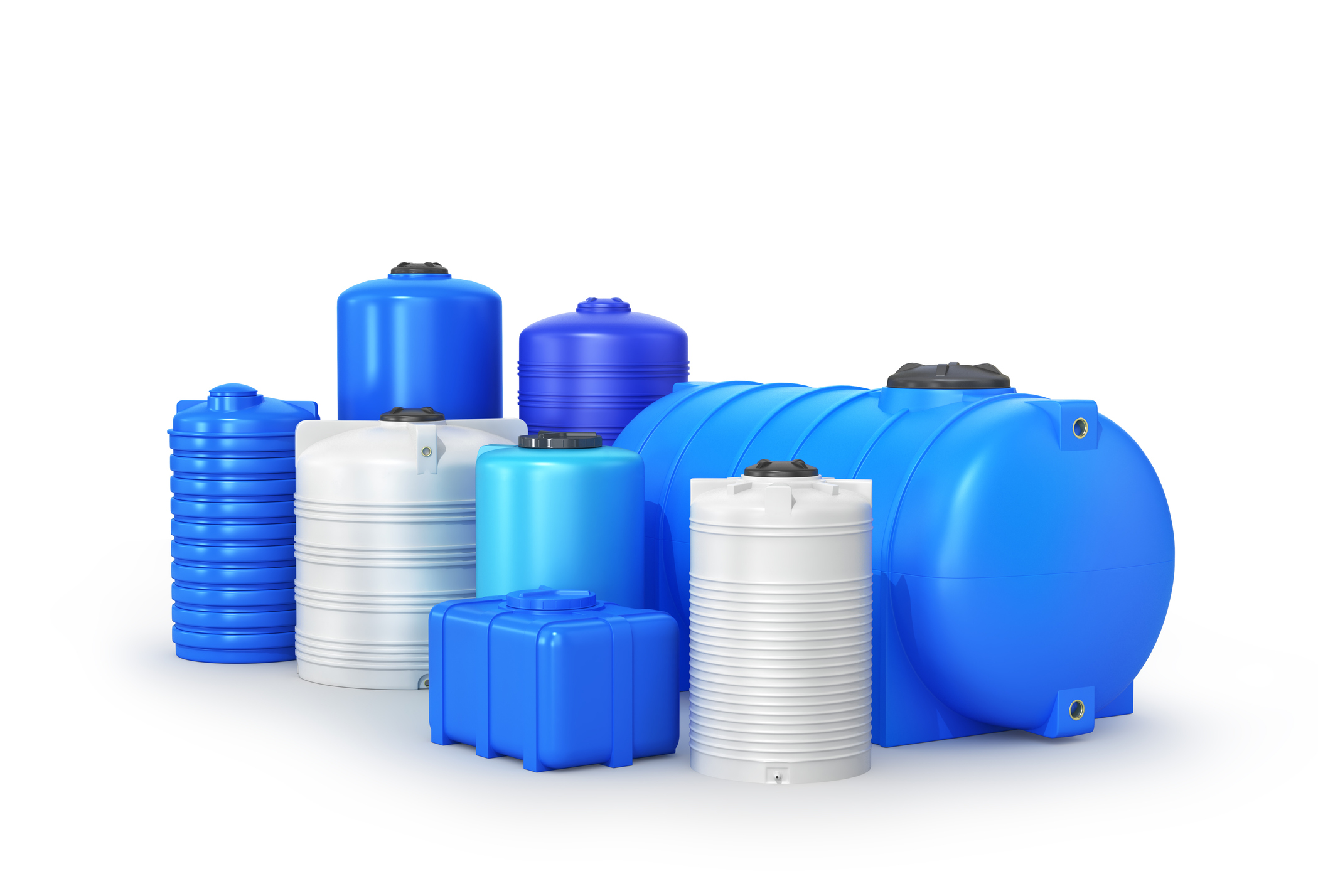
Advantages
- Complex Shapes: Allows for the production of intricate, seamless parts.
- Cost-Effective: Suitable for both small and large-scale production runs.
- Uniform Wall Thickness: Provides even material distribution, ensuring structural integrity.
- Design Flexibility: Easily incorporates features like textures and undercuts.
- Material Efficiency: Minimizes waste, as excess material can be recycled.
Disadvantages
- Limited Material Compatibility: Not all materials are suitable for rotational molding.
- Cycle Times: Longer cycle times compared to some other manufacturing methods.
- Surface Finish: Achieving a smooth surface may require additional processing steps.
Common Applications of Rotational Molding
- Plastics: Producing tanks, containers, toys, and playground equipment.
- Automotive: Creating automotive components like fuel tanks and air ducts.
- Agriculture: Manufacturing agricultural tanks, bins, and containers.
- Recreation: Producing kayaks, watercraft, and outdoor furniture.
- Construction: Fabricating septic tanks, mannequins, and decorative elements.
Please consult a Canyon Components Engineer about your specific application and we will use our decades of experience to formulate a solution that fits your need.
Types of Rotational Molding
Rotational Molding can be performed in a number of ways depending on the composition and intended use of the final product. Some variations available for Rotational Molding include the following.
Canyon Components strives to meet all customer service requests. Feel free to contact Canyon Components engineering and let our knowledgeable staff help you design the perfect part for your needs.
Rock and Roll Rotational Molding
Primarily used for long, narrow parts, this method rocks the mold back and forth while rotating it around one axis. Its advantage is the ability to produce large, hollow products with uniform wall thickness. However, it's limited in producing complex shapes and has longer cycle times compared to other methods.
Clamshell Rotational Molding
Involves a single arm that opens like a clamshell. It's effective for small to medium-sized parts and allows easy access to the mold. The advantage is simplicity and cost-effectiveness. The downside is limited production capacity and longer cycle times for each part.
Shuttle Rotational Molding
This method shuttles the mold between multiple heating and cooling stations. It's advantageous for producing multiple parts simultaneously, improving efficiency. However, it requires more space for equipment and is less suitable for very large or complex parts.
Swing Arm Rotational Molding
Uses arms that swing the mold into different heating and cooling stations. It's versatile for different product sizes and offers good control over the production process. The disadvantage is that it's not as efficient for high-volume production and requires significant floor space.
Carousel Rotational Molding
Features multiple arms that rotate and move molds through heating, cooling, and loading stations. It's efficient for high-volume production and can handle multiple molds simultaneously. However, it involves a higher initial investment and requires more operational space.
Vertical Rotational Molding
Molds rotate vertically, ideal for products requiring consistent wall thickness and quality. This method is beneficial for tall or deep parts. The disadvantage is the limitation in size and volume of products that can be produced, and it may not be as efficient for complex or intricate designs.
Please consult a Canyon Components Engineer about your specific application and we will use our decades of experience to formulate a solution that fits your need.
Request a Quote for Rotational Molded Parts
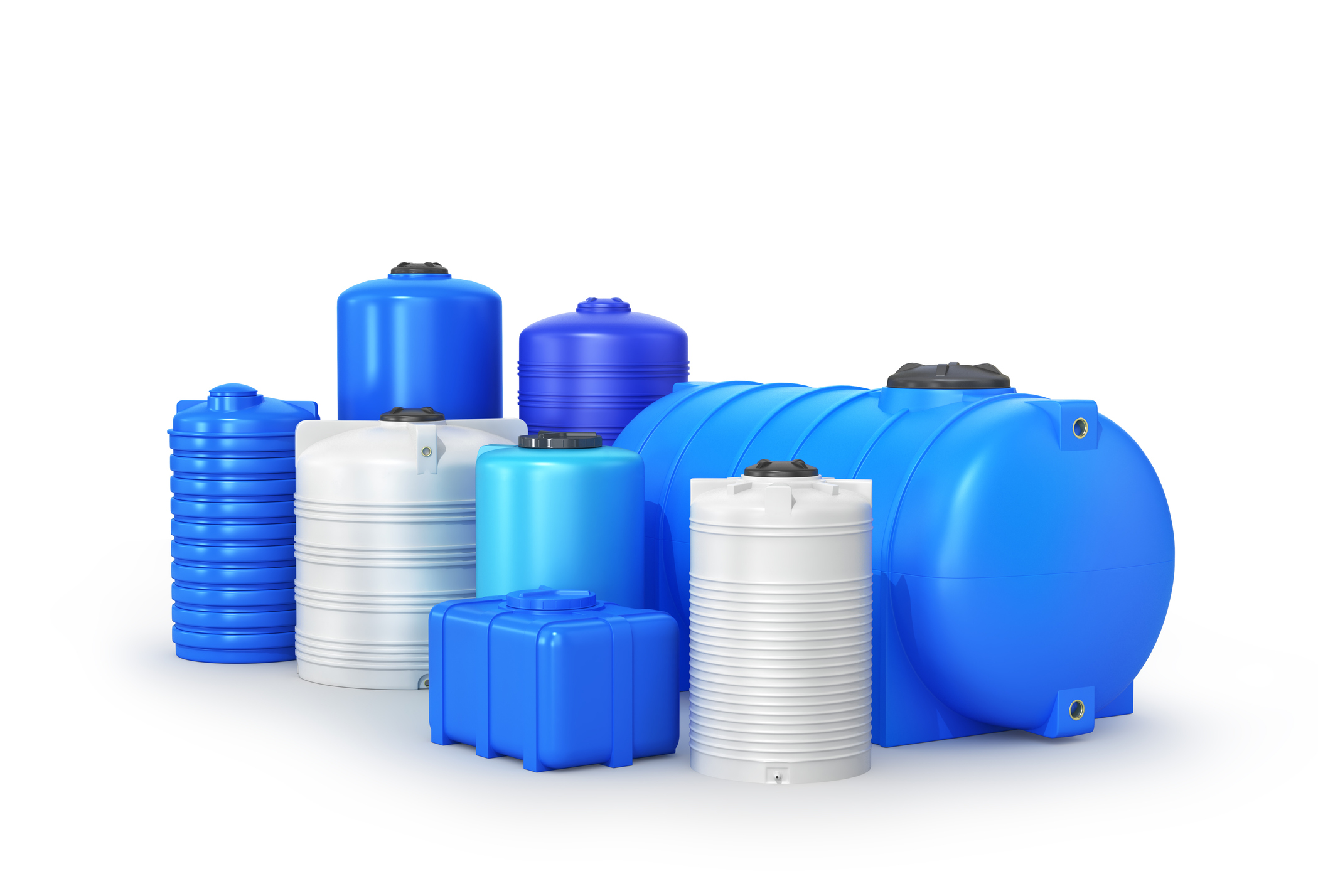
Rotational Molding Materials Available
Rotational Molding can be performed in a number of ways depending on the composition and intended use of the final product. Some common materials available for Rotational Molding include the following.
Each of these materials has its own advantages, limitations, and cost implications. The choice of material and manufacturing technique usually depends on factors like the complexity of the design, required precision, material properties, and production volume.
Canyon Components strives to meet all customer service requests. Feel free to contact Canyon Components engineering and let our knowledgeable staff help you design the perfect part for your needs.
Plastics
Plastics are a broad class of synthetic or semi-synthetic materials known for their versatility and moldability. They are crucial in numerous applications due to their ability to be shaped, lightweight nature, and resistance to chemicals and moisture.
Specialty Compliances
Canyon have materials available for O-rings, gaskets, & custom parts with compliances ranging from USP Class VI <87> & <88> for medical applications, to FDA CFR 21.177.2600 grades A through F for different food types, to the various drinking water specifications like KTW and NSF. Whether it's metal, rubber, or plastic, Canyon can meet your needs!
PP (Polypropylene)
Polypropylene (PP) plastic, known for its exceptional chemical resistance and durability, is a lightweight thermoplastic. It's resilient against fatigue, has a high melting point, and is ideal for packaging, automotive parts, and textiles, thanks to its versatility and recyclability.
Polyethylene (PE)
Polyethylene (PE) plastic, renowned for its versatility, is a widely used thermoplastic. It's lightweight, impact-resistant, and has excellent chemical resistance. Commonly used in packaging, containers, and pipes, PE is available in varying densities for different applications, including high and low-density forms.
PC (Polycarbonate)
Polycarbonate (PC) Plastic is a tough, transparent thermoplastic with exceptional impact resistance, heat tolerance, and optical clarity. Its versatility makes it ideal for bulletproof glass, eyewear lenses, medical devices, and protective gear, offering a unique balance of strength and lightweight properties.
Nylon (Polyamide, PA)
Nylon, a synthetic thermoplastic polymer, is renowned for its high strength, elasticity, and abrasion resistance. It's versatile, easily dyeable, and used in a wide range of products from textiles and ropes to gears and automotive parts.
Polyurethane (PU, AU)
Polyurethane O-rings, gaskets, & custom molded parts generally have two or three times greater tensile strength and wear resistance than Nitrile and comparable polymers. Polyurethane also provides excellent permeation resistance when compared to most rubbers.
ABS (Acrylonitrile Butadiene Styrene)
ABS plastic, a thermoplastic polymer blend of acrylonitrile, butadiene, and styrene, is renowned for its toughness, impact resistance, and rigidity. It's easily machinable and ideal for automotive parts, consumer goods, and 3D printing due to its strength and versatility.
PVC (Polyvinyl Chloride)
Polyvinyl Chloride (PVC) plastic, a widely utilized thermoplastic, is celebrated for its durability, chemical resistance, and versatility. It's commonly used in construction for pipes and fittings, medical devices, and window frames, and can be made more flexible with the addition of plasticizers.
PET (Polyethylene Terephthalate)
Polyethylene Terephthalate (PET) is a durable, lightweight thermoplastic, renowned for its clarity, strength, and recyclability. Widely used in beverage bottles, food packaging, and textiles, PET is also food-safe, resistant to water and many chemical solvents, and easily formed into various shapes.
PETG (Polyethylene Terephthalate Glycol)
PETG plastic, a glycol-modified version of polyethylene terephthalate, is valued for its clarity, excellent chemical resistance, and thermoformability. It's a popular choice for 3D printing, packaging, and medical devices due to its durability, impact resistance, and ease of fabrication.
PPSU (Polyphenylsulfone)
Polyphenylsulfone (PPSU) Plastic is a high-performance thermoplastic known for its exceptional heat resistance, toughness, and stability under thermal stress. It's widely used in medical instruments, aerospace, and plumbing components due to its excellent chemical resistance and ability to withstand repeated sterilizations.
Back to Manufacturing Hub
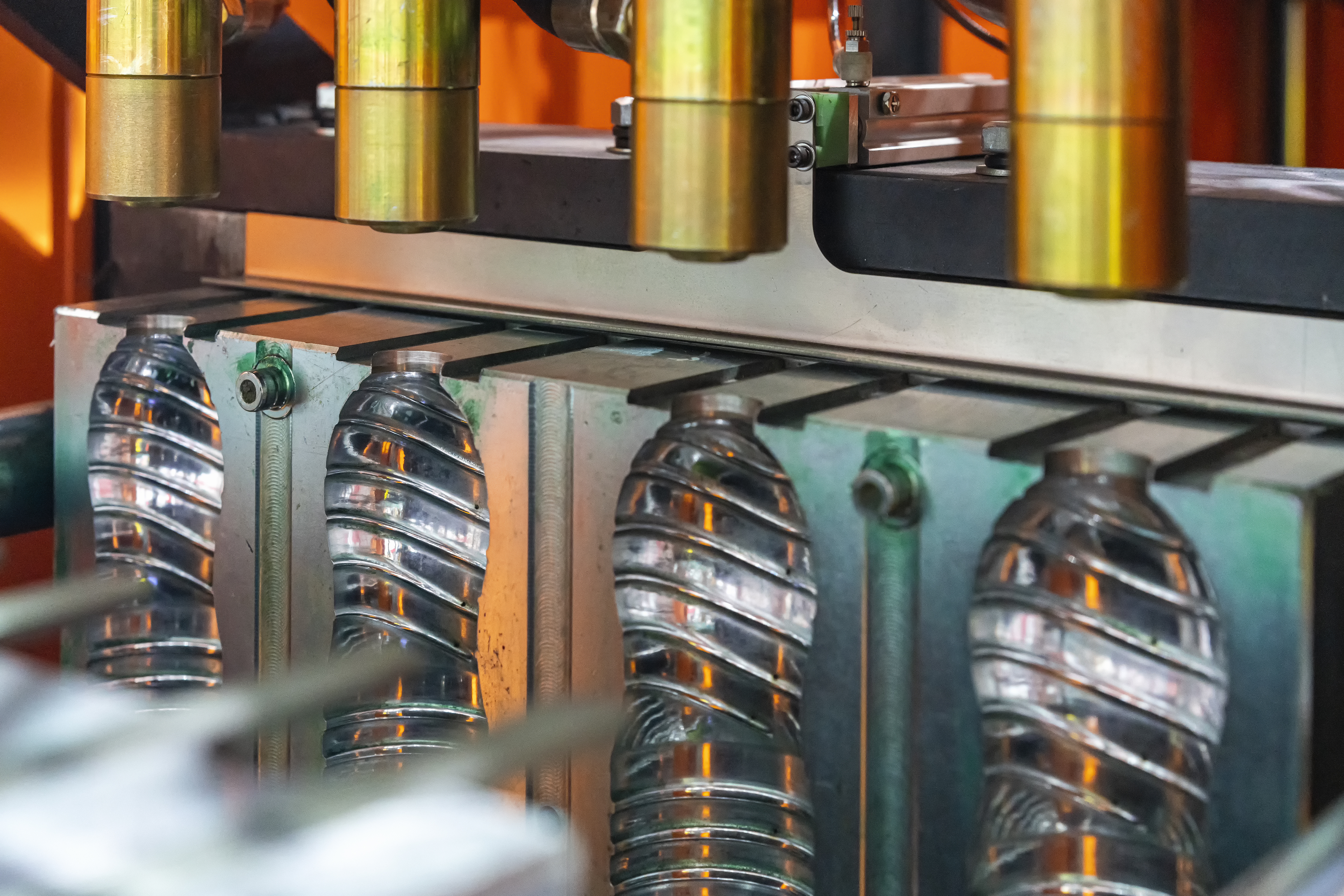
Get A Quote Now!
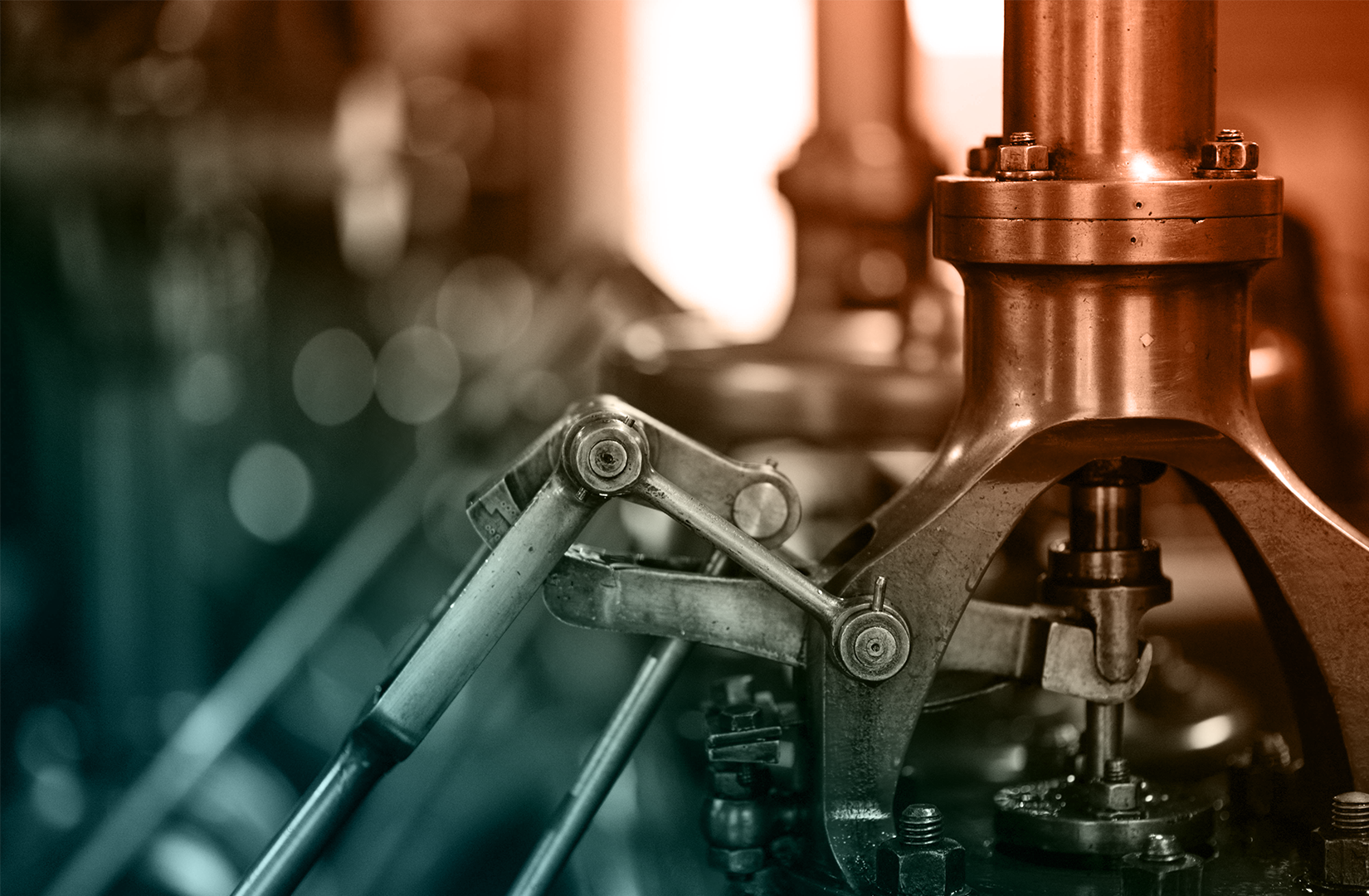
Groove Design References
Learn More
Coatings, Packaging, & Other Services
Learn More
Custom Parts & Custom O-rings
Learn More