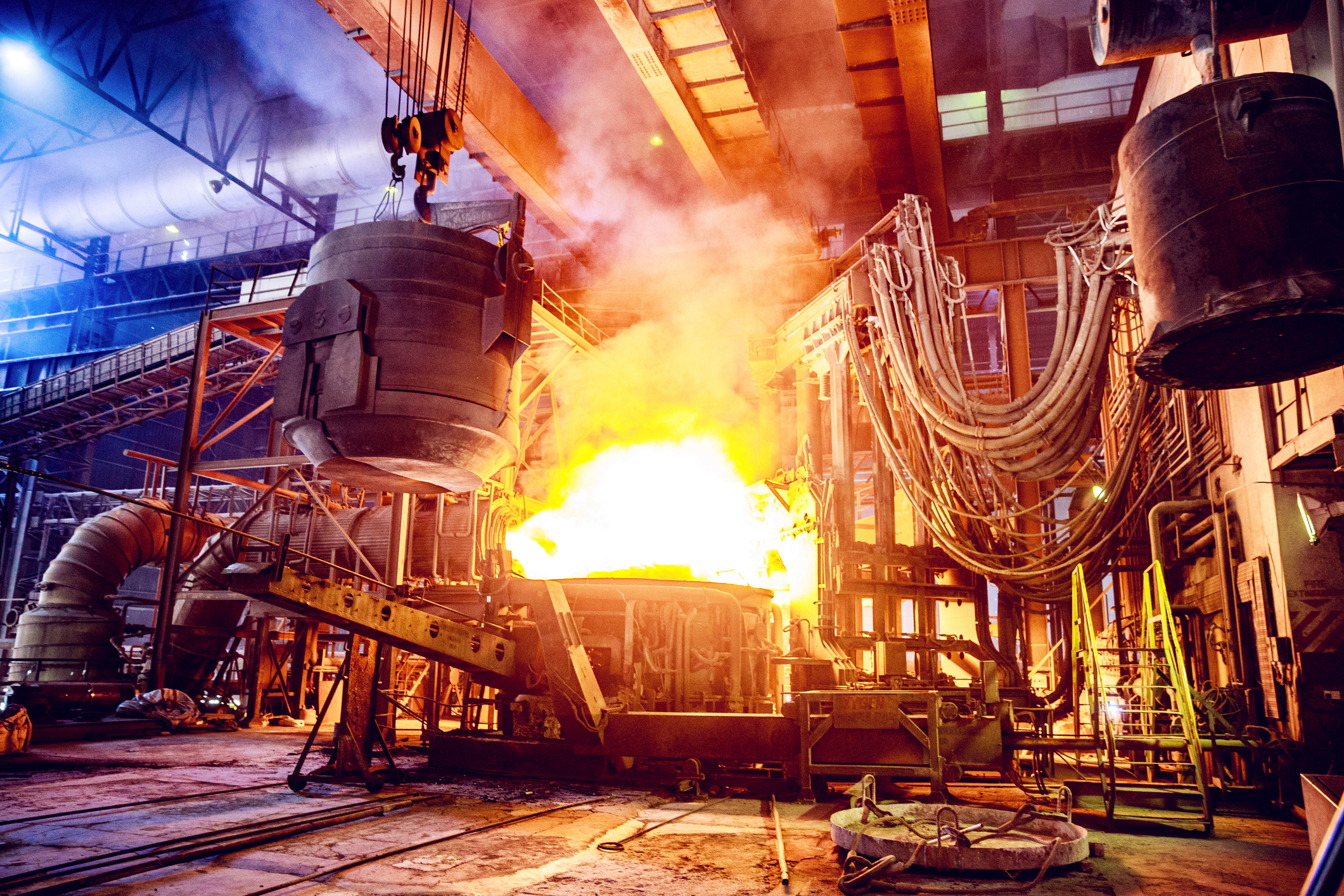
Magnesium Alloy Metal Selection Guide
Magnesium alloy metal is a group of lightweight, high-strength materials that are derived from magnesium and combined with various alloying elements. These alloys are known for their exceptional strength-to-weight ratio and are widely used in industries where weight reduction and structural integrity are crucial. In this web page, we will explore the different types of magnesium alloys, their numerous advantages and disadvantages, and the diverse industrial uses where magnesium alloy metals play a crucial role.
Magnesium Alloy rapid manufacturing, & machined parts are available now!
Check with one of Canyon’s helpful product engineers for an expert material and manufacturing recommendation.
Common names include: AZ31, AZ61, AZ80, AM50, AM60, ZK60, WE43, Elektron 675.
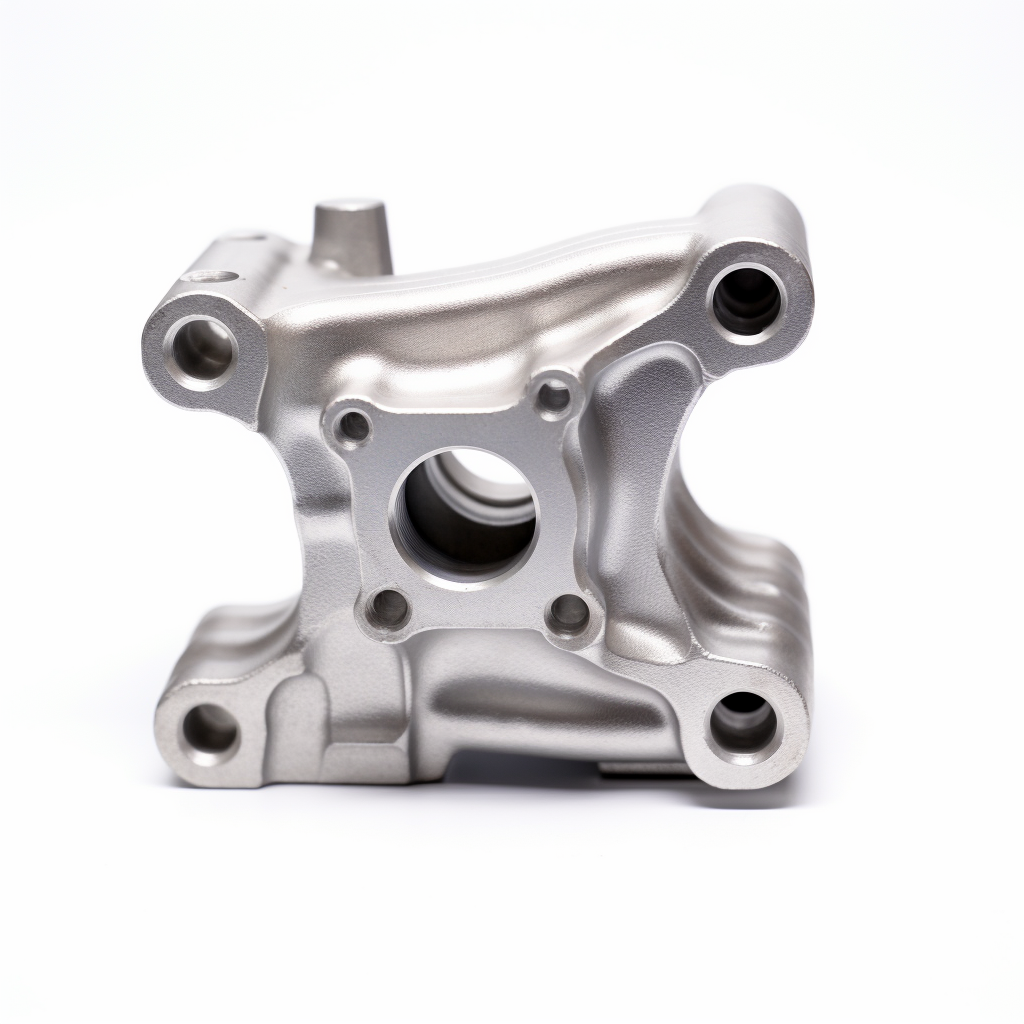
Advantages
- Lightweight: Magnesium alloys are some of the lightest structural materials available, making them ideal for applications where weight reduction is critical, such as in the aerospace and automotive industries.
- High Strength-to-Weight Ratio: Magnesium alloys provide exceptional strength-to-weight ratios, offering structural integrity while minimizing overall weight.
- Corrosion Resistance: Properly treated or alloyed magnesium alloys exhibit good corrosion resistance, making them suitable for outdoor and marine applications.
- High Thermal Conductivity: Magnesium alloys have high thermal conductivity, making them valuable in applications requiring effective heat dissipation, such as in electronics and heat sinks.
- Recyclability: Magnesium is highly recyclable, contributing to sustainability efforts and reducing environmental impact.
- Damping Capacity: Magnesium alloys possess good damping capacity, which helps reduce vibrations in machinery and structures.
Disadvantages
- Combustibility: Magnesium alloys are highly flammable and can ignite when exposed to heat or flame. Special precautions are necessary to prevent fires during handling.
- Corrosion Susceptibility: Some magnesium alloys can be susceptible to corrosion, particularly in harsh environments. Proper surface treatment or alloy selection is required to mitigate corrosion.
- Limited Strength at High Temperatures: Magnesium alloys may lose some of their strength at high temperatures, limiting their use in certain applications.
Common Applications of Magnesium Alloy
- Aerospace: Magnesium alloys are used in aerospace applications, including aircraft components, due to their lightweight properties and high strength-to-weight ratio.
- Automotive: Magnesium alloy metals are used in the automotive industry for components such as engine blocks, transmission cases, and steering wheels, contributing to weight reduction and fuel efficiency.
- Electronics: Magnesium alloys with high thermal conductivity are used in electronic devices, heat sinks, and enclosures to dissipate heat effectively.
- Construction: Magnesium-based cement and building materials are used in construction for their fire resistance and durability.
- Medical Devices: Magnesium alloys are used in medical implants and devices, including orthopedic implants and surgical instruments.
- Pyrotechnics: Magnesium powder is a key component in pyrotechnic devices, producing bright and white flames in fireworks and flares.
- Lightweight Structural Components: Magnesium alloys are used in the manufacturing of lightweight structural components for various industries, including sports equipment and consumer electronics.
- Chemical Industry: Magnesium alloy metals are used in the chemical industry for the production of magnesium-based compounds, such as magnesium hydroxide and magnesium chloride.
Please consult a Canyon Components Engineer about your specific application and we will use our decades of experience to formulate a solution that fits your need.
Types of Magnesium Alloy
Magnesium Alloy can come in different variations, depending on its composition and intended use. Some common types of Magnesium Alloy include the following.
Canyon Components strives to meet all customer service requests. Feel free to contact Canyon Components engineering and let our knowledgeable staff help you design the perfect part for your needs.
AZ31 Magnesium Alloy
This alloy, blending aluminum and zinc, is known for its good strength-to-weight ratio and weldability. AZ31 is commonly used in aerospace and automotive applications for components like gearbox casings and fuselage parts. It also finds use in portable electronic devices due to its light weight and strength.
AZ91D Magnesium Alloy
AZ91D is prized for its excellent corrosion resistance and high strength. It's extensively used in automotive applications, particularly for die-cast parts like transmission cases and engine blocks. This alloy also offers good castability, making it suitable for complex shapes.
AM60 Magnesium Alloy
AM60 is characterized by its high ductility and impact strength, making it ideal for safety-critical components such as automotive seat frames and steering wheel cores. It also provides good noise and vibration damping, enhancing comfort in vehicle design.
ZE41 Magnesium Alloy
ZE41 is notable for its excellent castability and resistance to high temperatures. It's used in aerospace applications, particularly for gearbox casings and helicopter transmissions. This alloy also has good damping capacities and is suitable for parts requiring a combination of lightweight and high-temperature performance.
WE43 Magnesium Alloy
WE43 is a high-strength alloy often used in aerospace, motorsport, and military applications where high-temperature performance is crucial. It retains its strength and stability even after long exposure to high temperatures, making it suitable for engine components, missiles, and helicopter transmissions.
Elektron 21 (EV31A)
This alloy is known for its excellent strength and corrosion resistance, along with good weldability and machinability. It's used in high-performance applications such as motorsport, aerospace, and defense industries. Elektron 21 is particularly suited for components that require lightweight and durability, like airframe structures and race car wheels.
Please consult a Canyon Components Engineer about your specific application and we will use our decades of experience to formulate a solution that fits your need.
Manufacturing Options for Magnesium Alloy
Magnesium Alloy parts can be manufactured using several methods, each suitable for different applications and part complexities.
Each of these methods has its own advantages, limitations, and cost implications. The choice of manufacturing technique usually depends on factors like the complexity of the design, required precision, material properties, and production volume.
Canyon Components strives to meet all customer service requests. Feel free to contact Canyon Components engineering and let our knowledgeable staff help you design the perfect part for your needs.
Back to Metals Hub
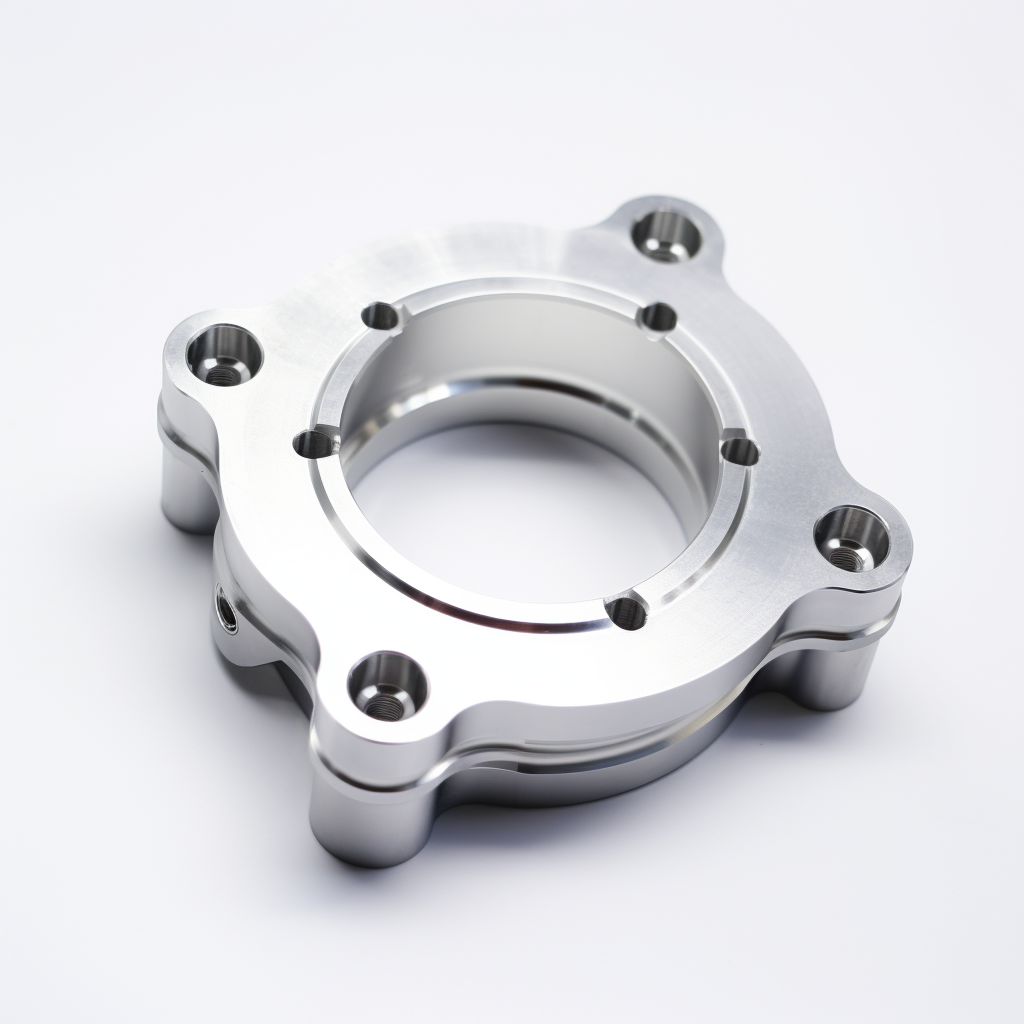
Get A Quote Now!
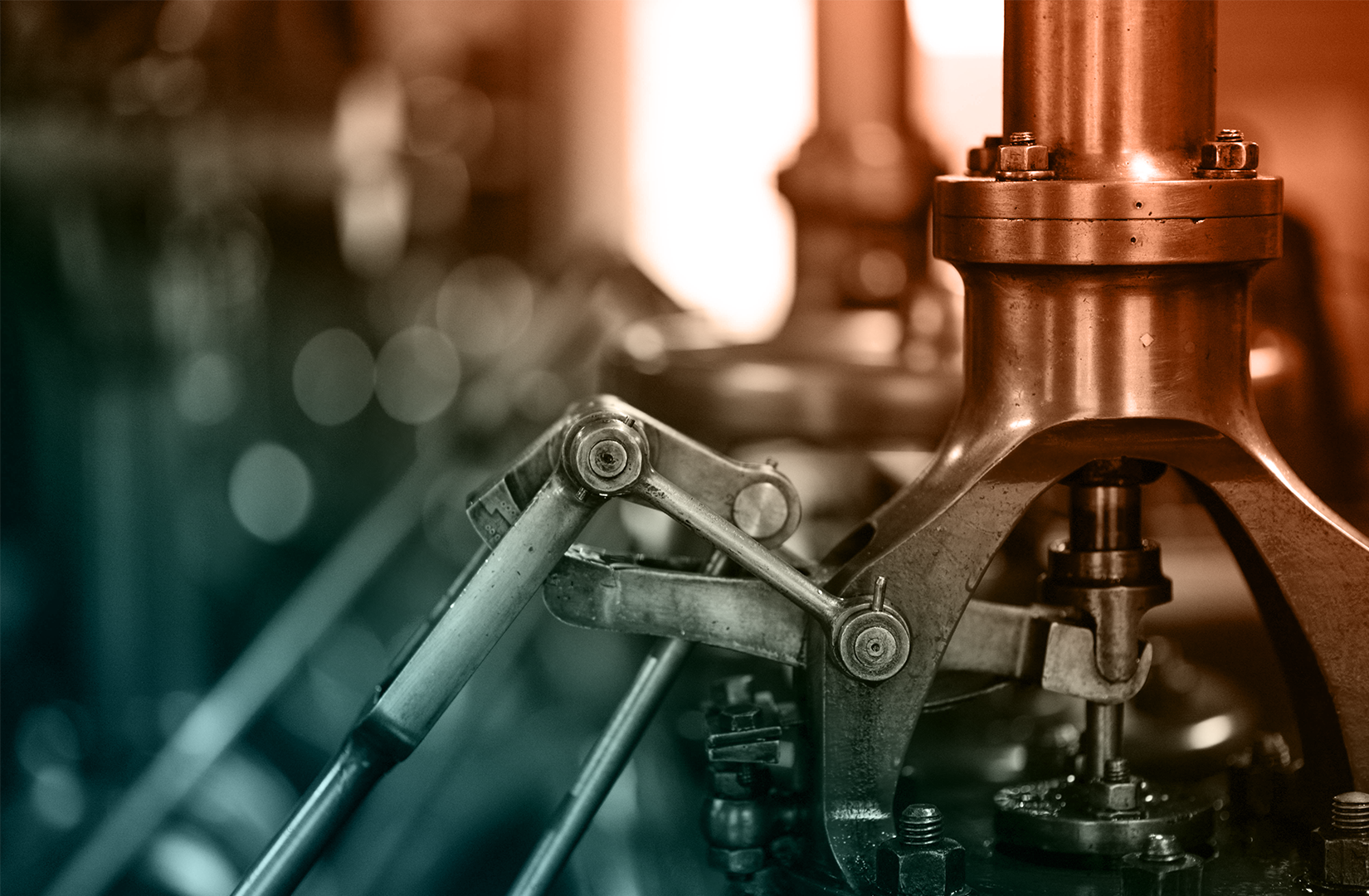
Groove Design References
Learn More
Coatings, Packaging, & Other Services
Learn More
Custom Parts & Custom O-rings
Learn More