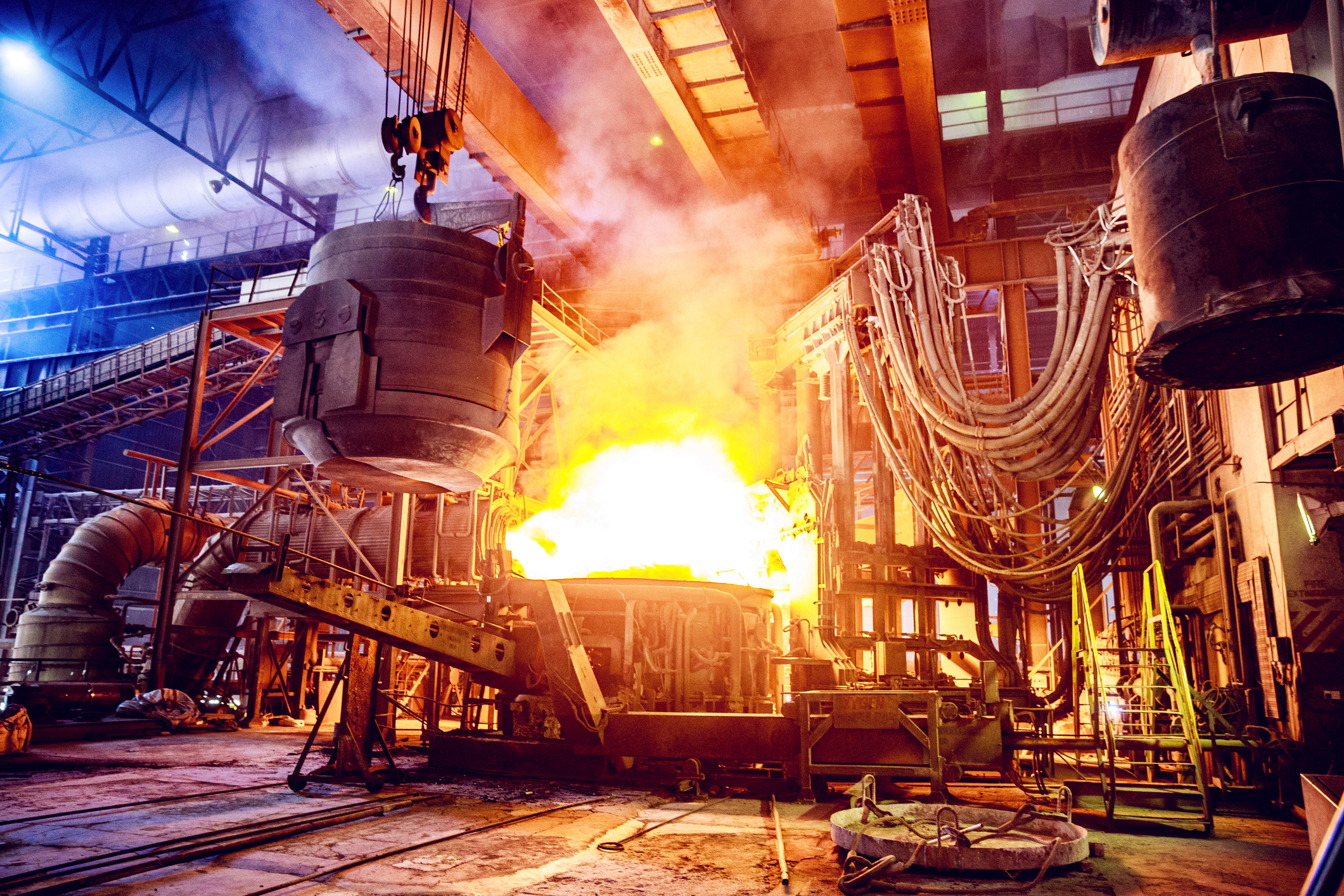
SAN Plastic (Styrene Acrylonitrile) Selection Guide
SAN (Styrene-Acrylonitrile) is a thermoplastic polymer known for its transparency, rigidity, and excellent chemical resistance. In this web page, we will explore the different types of SAN, its numerous advantages and disadvantages, and the diverse industrial applications where SAN plays a vital role.
SAN (Styrene Acrylonitrile) rapid manufacturing, & custom molded parts are available now!
Check with one of Canyon’s helpful product engineers for an expert material and manufacturing recommendation.
Common names include: SAN (Styrene Acrylonitrile), Trade Names: Lustran®, Tyril®, Kostil®, NAS®, Starex®.
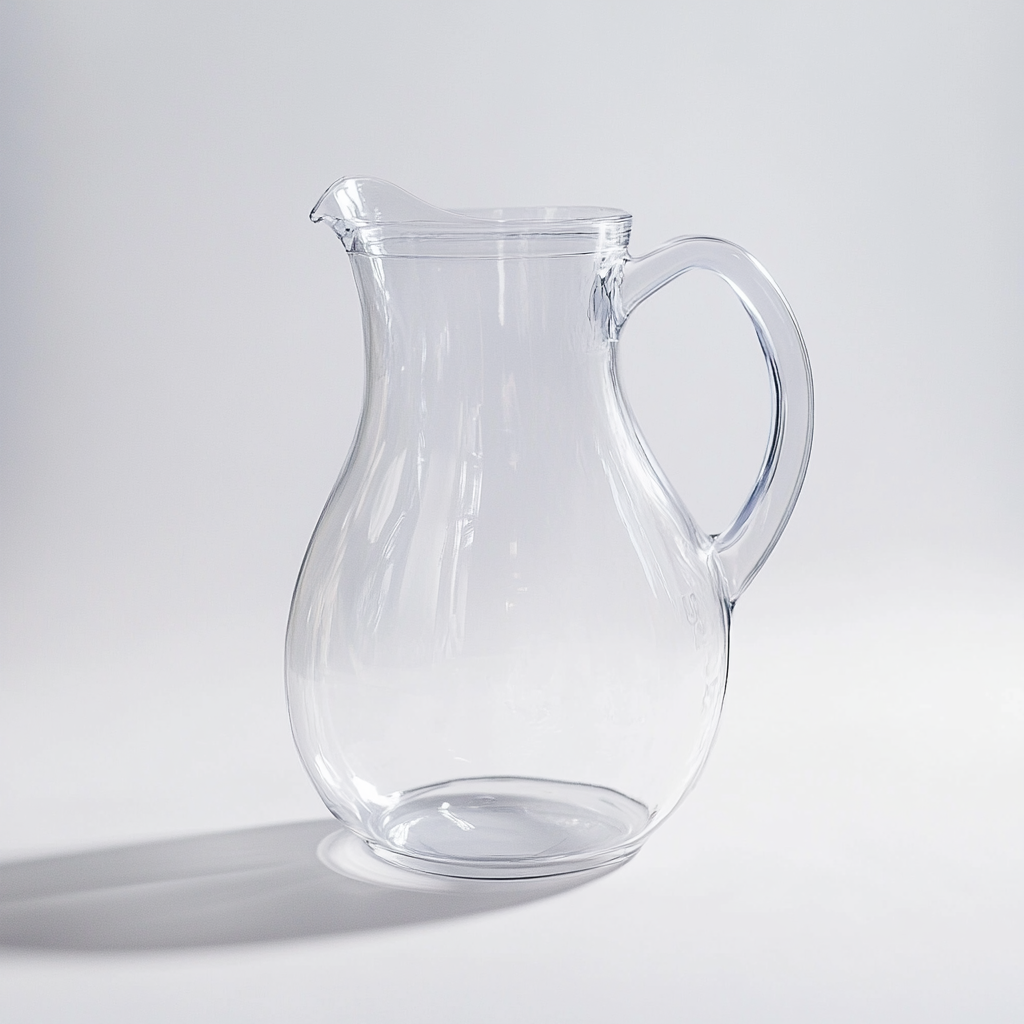
Advantages
- Transparency: SAN boasts exceptional optical clarity, making it an excellent choice for applications requiring visibility and aesthetics.
- Rigidity: It is a rigid material, providing structural integrity and stability to products, especially in thin-walled applications.
- Chemical Resistance: SAN is resistant to a wide range of chemicals, ensuring its stability in various industrial environments.
- Easy Processing: SAN is easy to process, including injection molding and extrusion, which makes it versatile for various manufacturing techniques.
- Good Surface Finish: SAN can be easily polished and post-processed to achieve a high-quality surface finish.
Disadvantages
- Brittleness: SAN can be relatively brittle, especially at low temperatures, which may limit its use in impact-critical applications.
- Not Suitable for High-Temperature Environments: SAN has a lower heat resistance compared to some other engineering plastics. It may soften or deform at elevated temperatures.
- Limited UV Resistance: Transparent SAN may degrade when exposed to prolonged UV radiation, so it may not be suitable for outdoor applications without UV stabilizers.
Common Applications of SAN
- Medical Devices: SAN is used in the production of various medical devices and equipment components due to its biocompatibility and resistance to chemicals used in healthcare settings.
- Automotive: SAN is employed in automotive interiors, including instrument panels, dashboards, and interior trim components due to its impact resistance and clarity.
- Consumer Goods: SAN is commonly used for manufacturing consumer goods such as kitchen appliances, consumer electronics, toys, and cosmetic containers due to its transparency and rigidity.
- Optical Components: Transparent SAN is used in optical lenses and light diffusers due to its exceptional optical properties.
- Packaging: SAN is used for packaging cosmetics, toiletries, and personal care products, where product visibility is important.
- Electrical and Electronics: SAN is used for manufacturing electrical enclosures, covers, and connectors due to its electrical insulating properties.
- Point-of-Purchase Displays: SAN is a favored material for creating attractive and durable point-of-purchase displays in retail environments.
- Household Appliances: SAN is used in the production of small household appliances and kitchenware due to its transparency and ease of processing.
Please consult a Canyon Components Engineer about your specific application and we will use our decades of experience to formulate a solution that fits your need.
Types of SAN
SAN can come in different variations, depending on its composition and intended use. Some common types of SAN include the following.
Canyon Components strives to meet all customer service requests. Feel free to contact Canyon Components engineering and let our knowledgeable staff help you design the perfect part for your needs.
General Purpose SAN
This standard type is known for its excellent clarity, rigidity, and resistance to chemicals. Widely used in household items like dishes and storage containers, it's also favored in cosmetic packaging due to its glossy finish and durability. General Purpose SAN offers a good balance of properties suitable for everyday consumer products.
High Flow SAN
Designed for ease of processing, High Flow SAN has a lower viscosity, allowing it to fill molds quickly and efficiently. Ideal for intricate and detailed components in consumer electronics and decorative items, it retains the strength and clarity of standard SAN while improving manufacturability.
Impact Modified SAN
This variant has enhanced impact resistance, making it suitable for more durable applications such as safety helmets, automotive components, and toys. It maintains the transparency and rigidity of SAN but is less brittle, making it more resistant to cracking under stress.
UV Stabilized SAN
UV Stabilized SAN is modified to resist degradation from UV light exposure, making it ideal for outdoor applications like garden furniture and automotive exterior parts. It retains the clarity and mechanical properties of SAN while preventing yellowing and loss of strength due to sunlight.
Flame Retardant SAN
This type of SAN includes flame retardant additives, making it suitable for applications with strict fire safety requirements, such as electrical and electronic housings. It maintains SAN’s clarity and rigidity while adding essential fire resistance characteristics.
Glass Fiber Reinforced SAN
By incorporating glass fibers, this SAN variant offers increased stiffness and dimensional stability. It's ideal for structural applications that require additional strength, such as mechanical parts and industrial components, without compromising the material’s inherent aesthetic qualities.
Please consult a Canyon Components Engineer about your specific application and we will use our decades of experience to formulate a solution that fits your need.
Manufacturing Options for SAN
SAN parts can be manufactured using several methods, each suitable for different applications and part complexities.
Each of these methods has its own advantages, limitations, and cost implications. The choice of manufacturing technique usually depends on factors like the complexity of the design, required precision, material properties, and production volume.
Canyon Components strives to meet all customer service requests. Feel free to contact Canyon Components engineering and let our knowledgeable staff help you design the perfect part for your needs.
Back to Plastics Hub
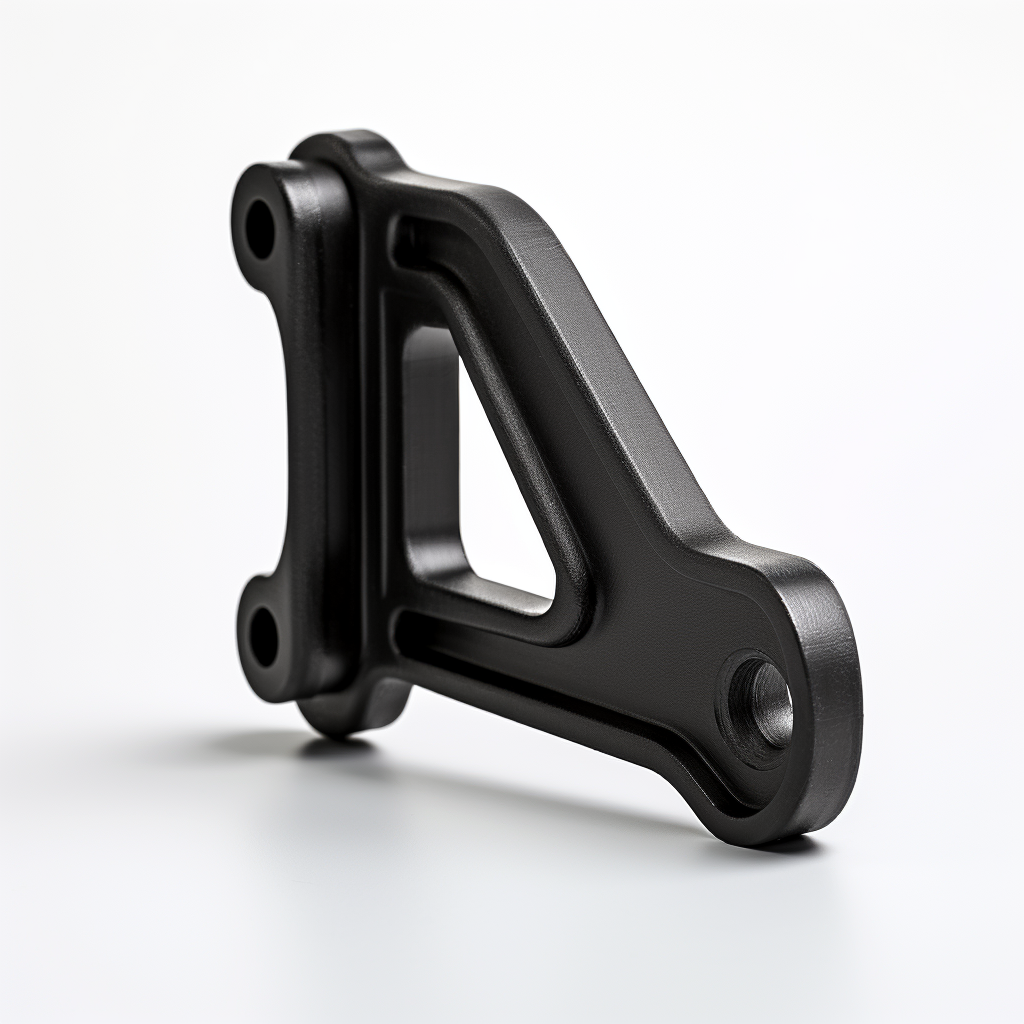
Get A Quote Now!
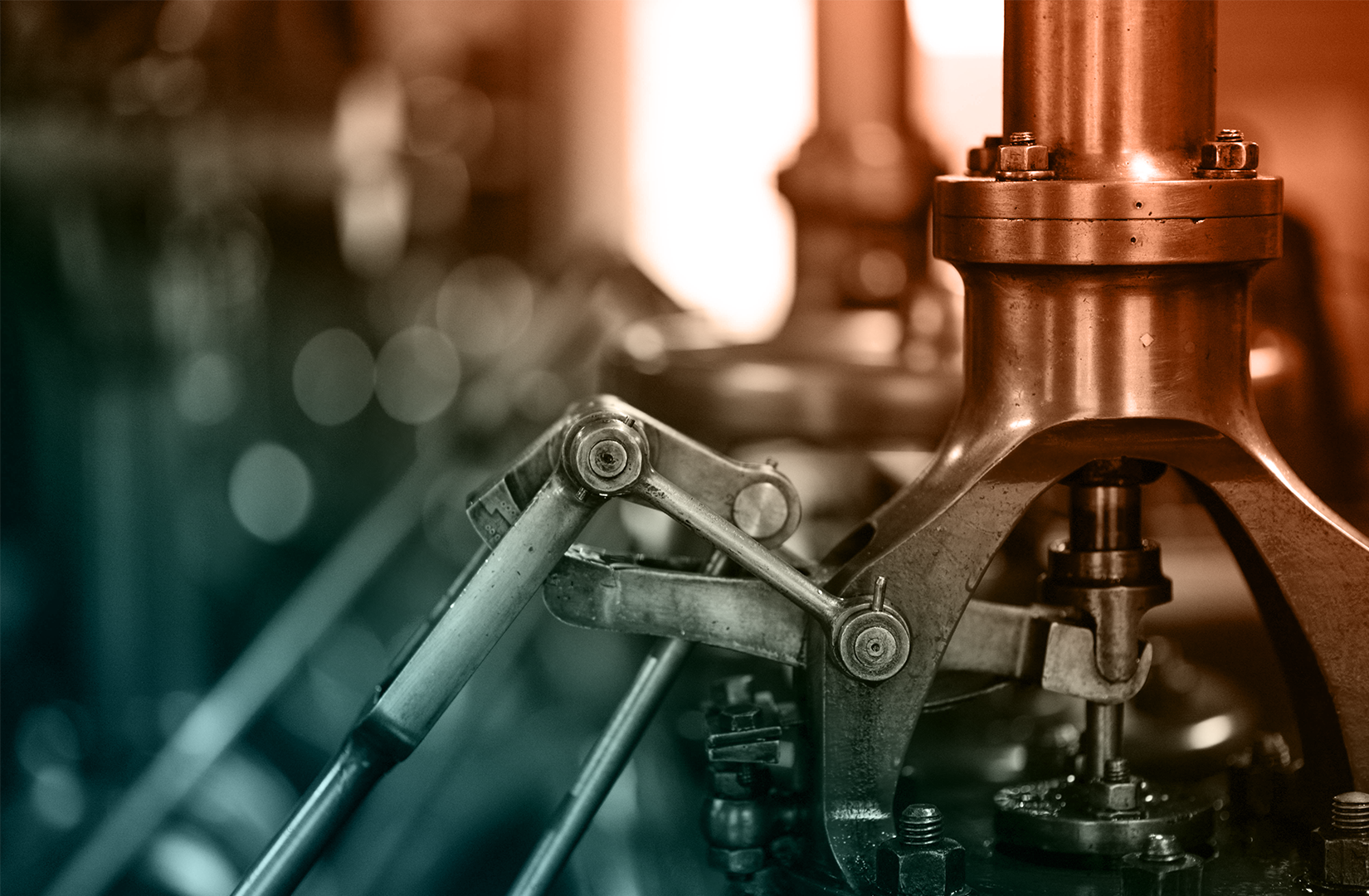
Groove Design References
Learn More
Coatings, Packaging, & Other Services
Learn More
Custom Parts & Custom O-rings
Learn More