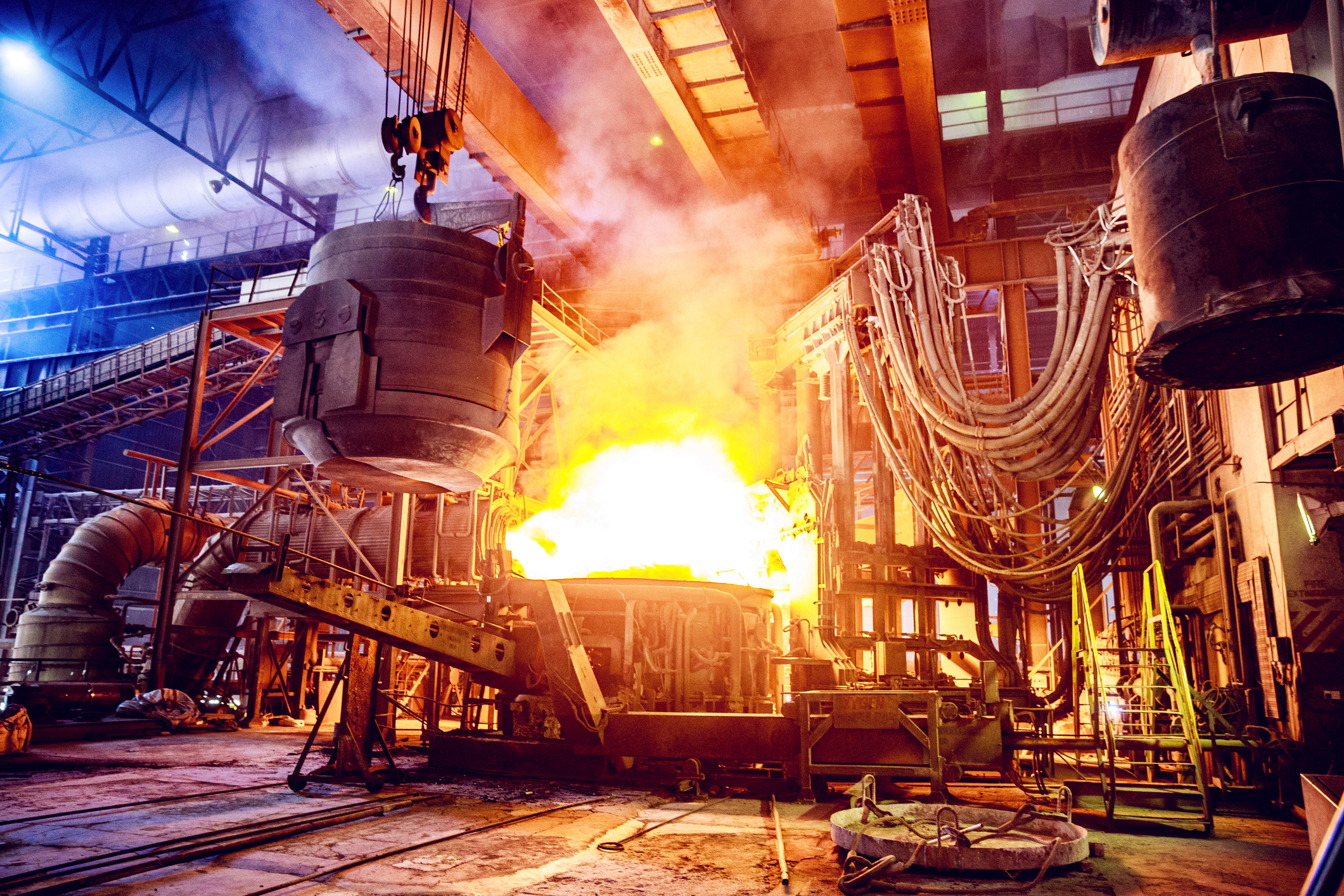
Backup Rings - Details, Selection, Installation, & Maintenance
Backup rings are essential components used in conjunction with O-rings, X-rings, or other sealing elements to prevent extrusion and enhance sealing performance in high-pressure applications. These rings provide additional support to the primary seal, extending its life and ensuring reliable operation in challenging conditions. This guide covers the features, common applications, types, manufacturing options, and essential guidelines for selection, installation, and maintenance of backup rings.
PTFE and PEEK Backup Rings available now! Use in conjunction with CanRez® FFKM and Kalrez® O-rings for the ultimate simple high pressure seal!
Check with one of Canyon’s helpful product engineers for an expert material and manufacturing recommendation.
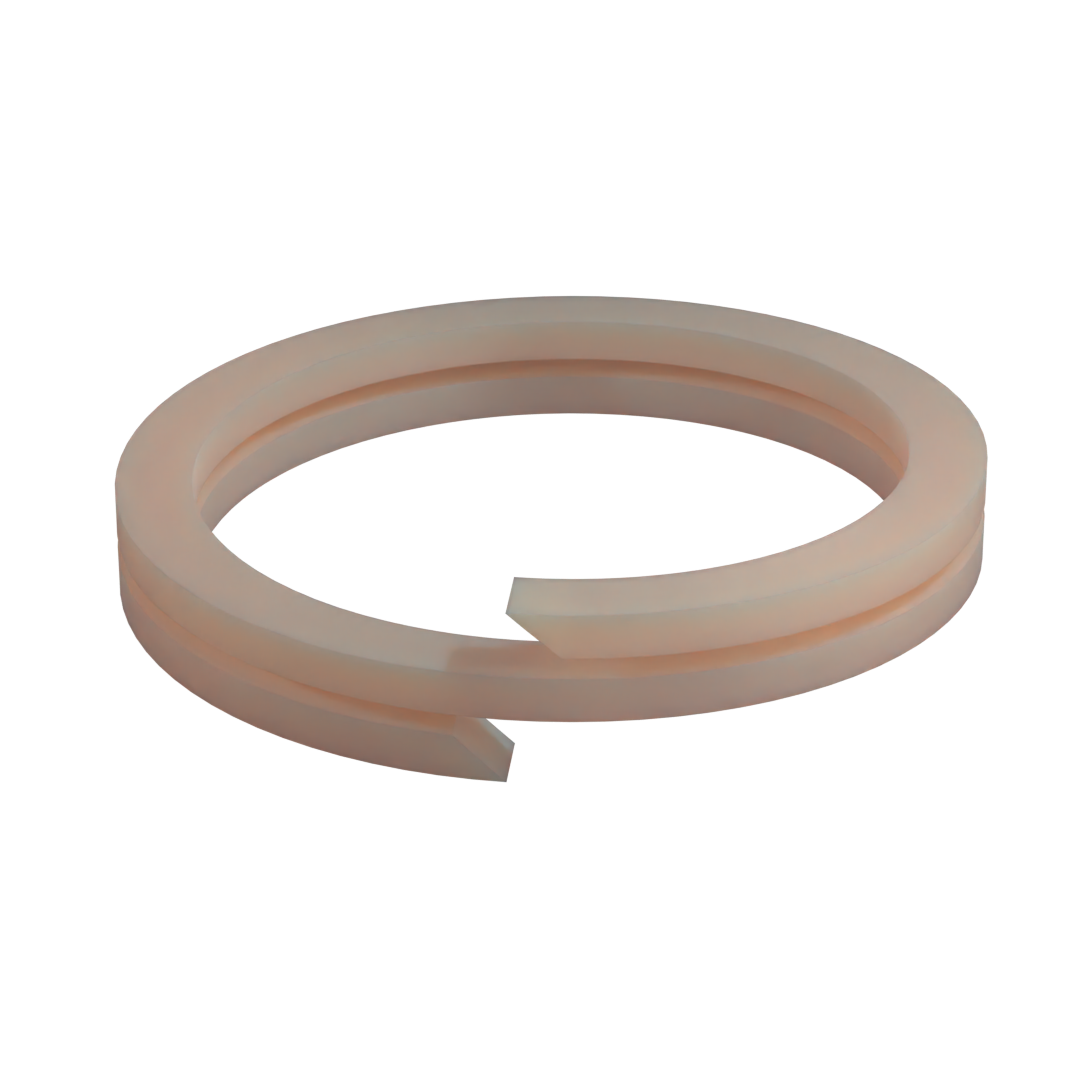
Backup rings play a vital role in sealing applications by providing essential support to primary seals, boosting their performance and extending their lifespan. Constructed from durable materials like PTFE (polytetrafluoroethylene), backup rings prevent the extrusion and deformation of seals when exposed to high pressures and temperatures. This reinforcement ensures the sealing system remains effective, minimizing the risk of leaks and system failures.
In high-pressure environments, seals can become distorted, displaced, or extruded through groove gaps, leading to reduced performance. Backup rings counteract these issues by serving as a sturdy barrier that keeps the seal in place and preserves its shape. This support is particularly crucial in dynamic applications where seals undergo constant movement and stress.
Additionally, backup rings reduce wear and tear on seals, lowering maintenance costs and decreasing downtime. They are indispensable in industries such as aerospace, automotive, and hydraulics, where dependable sealing solutions are critical for both safety and efficiency.
In conclusion, backup rings are essential for enhancing the performance, durability, and reliability of sealing systems. Their ability to prevent extrusion, maintain seal integrity, and prolong seal life makes them a valuable asset in any high-stress, high-pressure application.
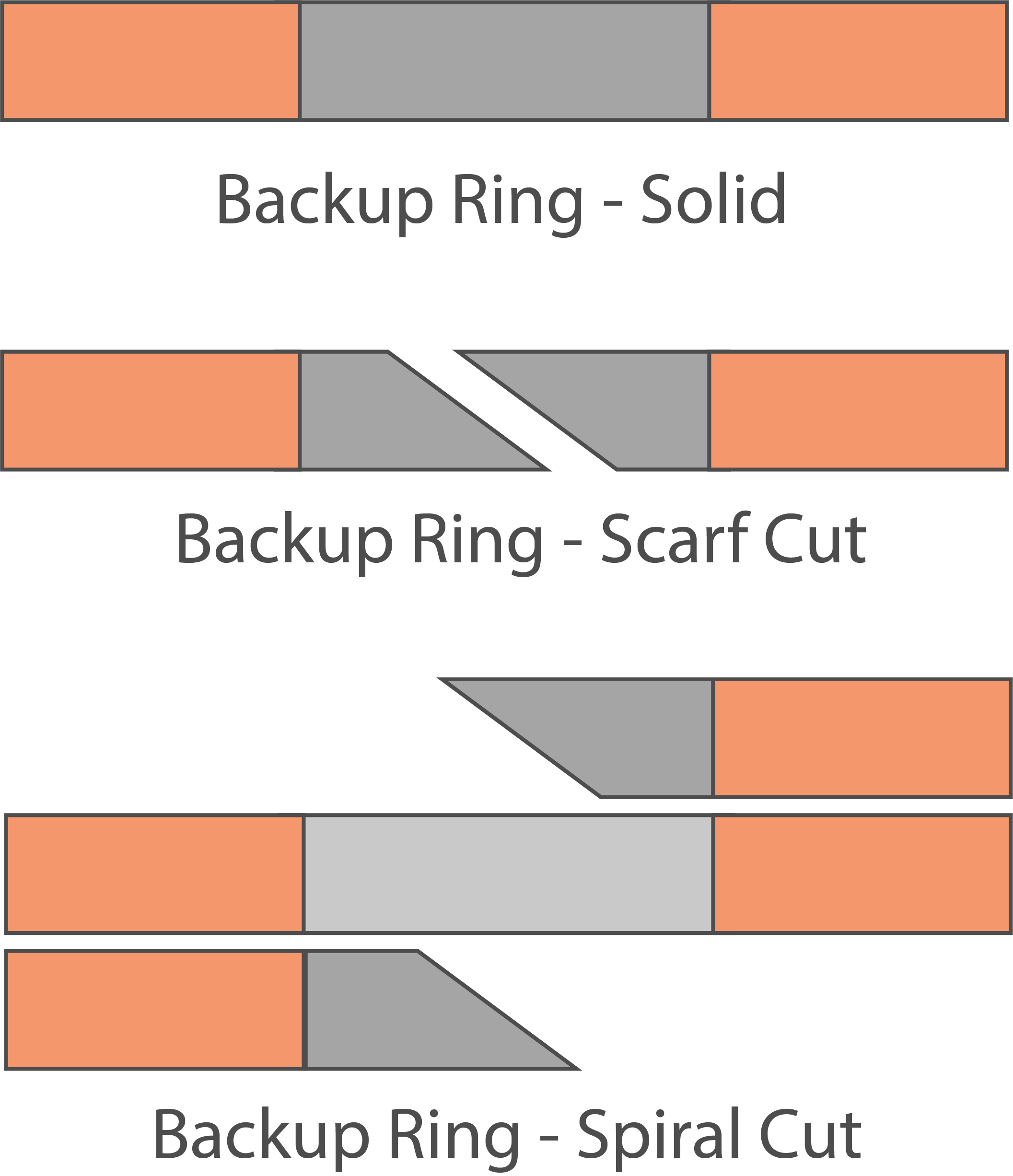
Features of Backup Rings
Backup rings offer several critical features that enhance the performance and durability of sealing systems:
- Extrusion Resistance: Backup rings prevent the extrusion of primary seals, especially in high-pressure environments, ensuring the integrity of the seal.
- Extended Seal Life: By reducing the risk of extrusion and wear, backup rings prolong the life of O-rings and other seals, leading to longer maintenance intervals.
- Enhanced Stability: Backup rings provide additional support to the sealing element, improving overall system stability and reliability.
- Versatility: Backup rings can be used with a variety of seals, including O-rings, X-rings, and other dynamic or static seals.
- Temperature and Chemical Resistance: Made from durable materials, backup rings can withstand extreme temperatures and exposure to aggressive chemicals, making them suitable for demanding applications.
Common Applications of Backup Rings
Backup rings are used across various industries where high pressures and demanding conditions require enhanced sealing performance. Common applications include:
- Hydraulic Systems: Backup rings are widely used in hydraulic cylinders, pumps, and valves to prevent O-ring extrusion in high-pressure environments.
- Pneumatic Systems: In pneumatic applications, backup rings help maintain seal integrity and prevent leaks in compressed air systems.
- Aerospace: Backup rings are used in aerospace systems to ensure reliable sealing under extreme pressures and temperatures.
- Oil and Gas: Backup rings provide critical support in oil and gas exploration and production equipment, where high-pressure conditions are common.
- Automotive: In automotive applications, backup rings are used in engines, transmissions, and braking systems to enhance sealing performance and reliability.
Please consult a Canyon Components Engineer about your specific application and we will use our decades of experience to formulate a solution that fits your need.
Get a Quote Now!
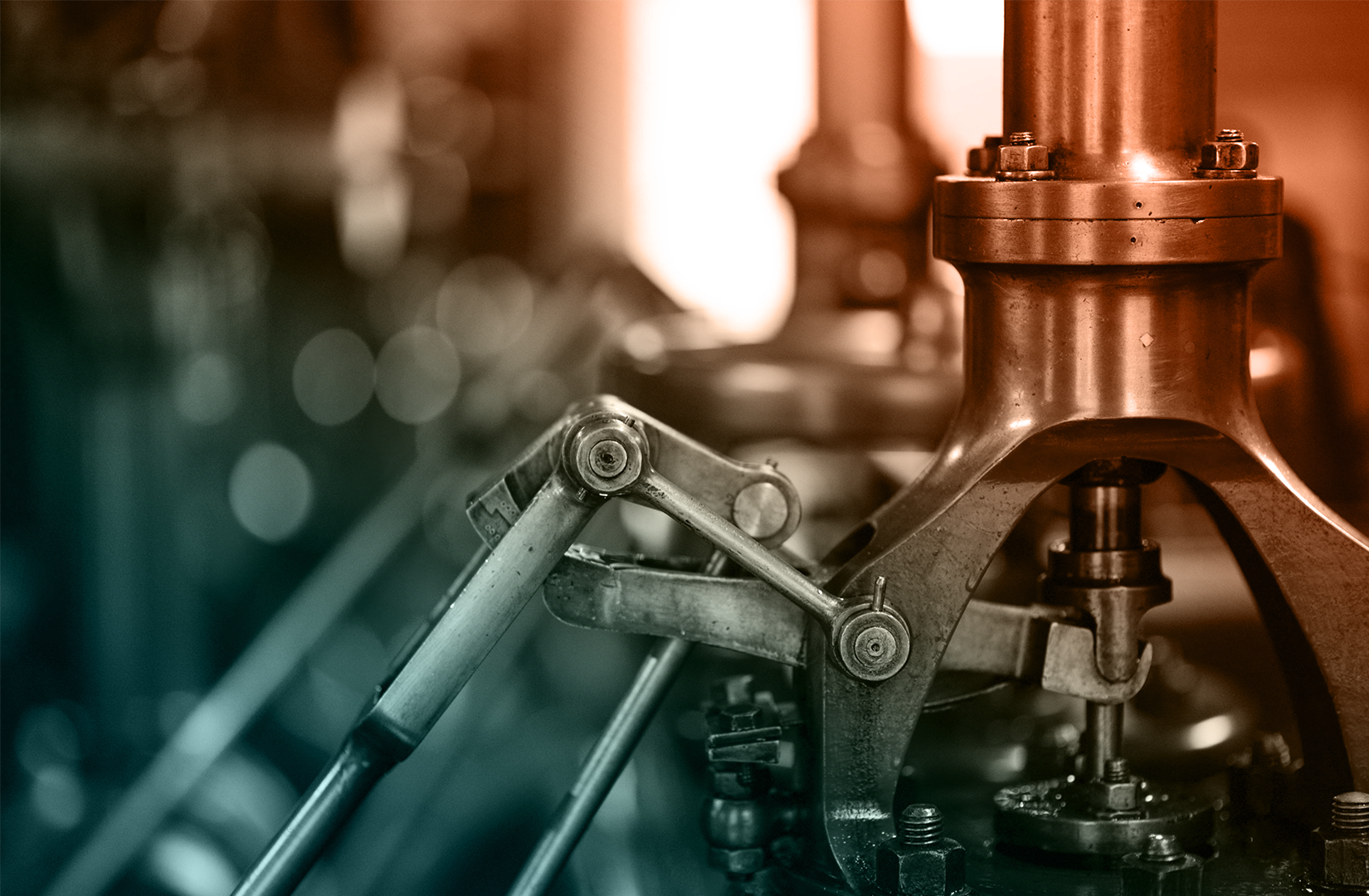
Backup Ring Materials
PTFE Backup Rings
Known for their excellent chemical resistance and low friction, PTFE backup rings are ideal for harsh environments and high-temperature applications.
PEEK Backup Rings
PEEK backup rings offer exceptional mechanical strength and chemical resistance, making them ideal for high-pressure, high-temperature environments, such as oil and gas, chemical processing, and aerospace applications.
Nylon Backup Rings
Nylon backup rings offer good mechanical strength and are often used in hydraulic and pneumatic systems.
Polyethylene Backup Rings
These backup rings provide good chemical resistance and are suitable for use in a wide range of applications.
Elastomeric Backup Rings
Made from rubber-like materials, these backup rings provide flexibility and are often used in lower-pressure applications where some elasticity is beneficial.
Please consult a Canyon Components Engineer about your specific application and we will use our decades of experience to formulate a solution that fits your need.
Solid PTFE Backup Rings
Solid backup rings are crafted from a single piece of material, providing robust and consistent support to primary seals. This design offers several key advantages:
- Reliable Seal Integrity: The solid construction ensures continuous, unwavering support, preventing seal extrusion and deformation, which is especially critical in high-pressure environments.
- Enhanced Durability: Without any cuts or gaps, solid backup rings are highly durable and resistant to wear, making them ideal for long-term use in static and dynamic sealing applications.
- Superior Performance in Extreme Conditions: Solid backup rings, often made from materials like PTFE or PEEK, are highly resistant to chemicals, extreme temperatures, and pressure variations, making them suitable for challenging environments such as chemical processing, aerospace, and hydraulic systems.
- Solid backup rings are a dependable solution for maintaining seal integrity and extending the lifespan of the entire sealing system, ensuring consistent performance even in the most demanding conditions.

Split (Scarf Cut) PTFE Backup Rings
Split PTFE backup rings, also known as Scarf Cut, feature a ring that is cut or split along its circumference. This design offers several advantages:
- Easy Installation and Removal: The split design allows for quick and hassle-free installation and removal without the need to disassemble equipment, making split backup rings ideal for retrofitting existing systems or situations where accessibility is limited.
- Convenience in Maintenance: Split rings facilitate easy access for maintenance and inspection, minimizing downtime and operational disruptions. They are particularly suitable for applications where efficiency and ease of use are prioritized.
- Versatility: Split backup rings can be used in a wide range of hydraulic and pneumatic systems, offering reliable sealing performance in various industrial applications.
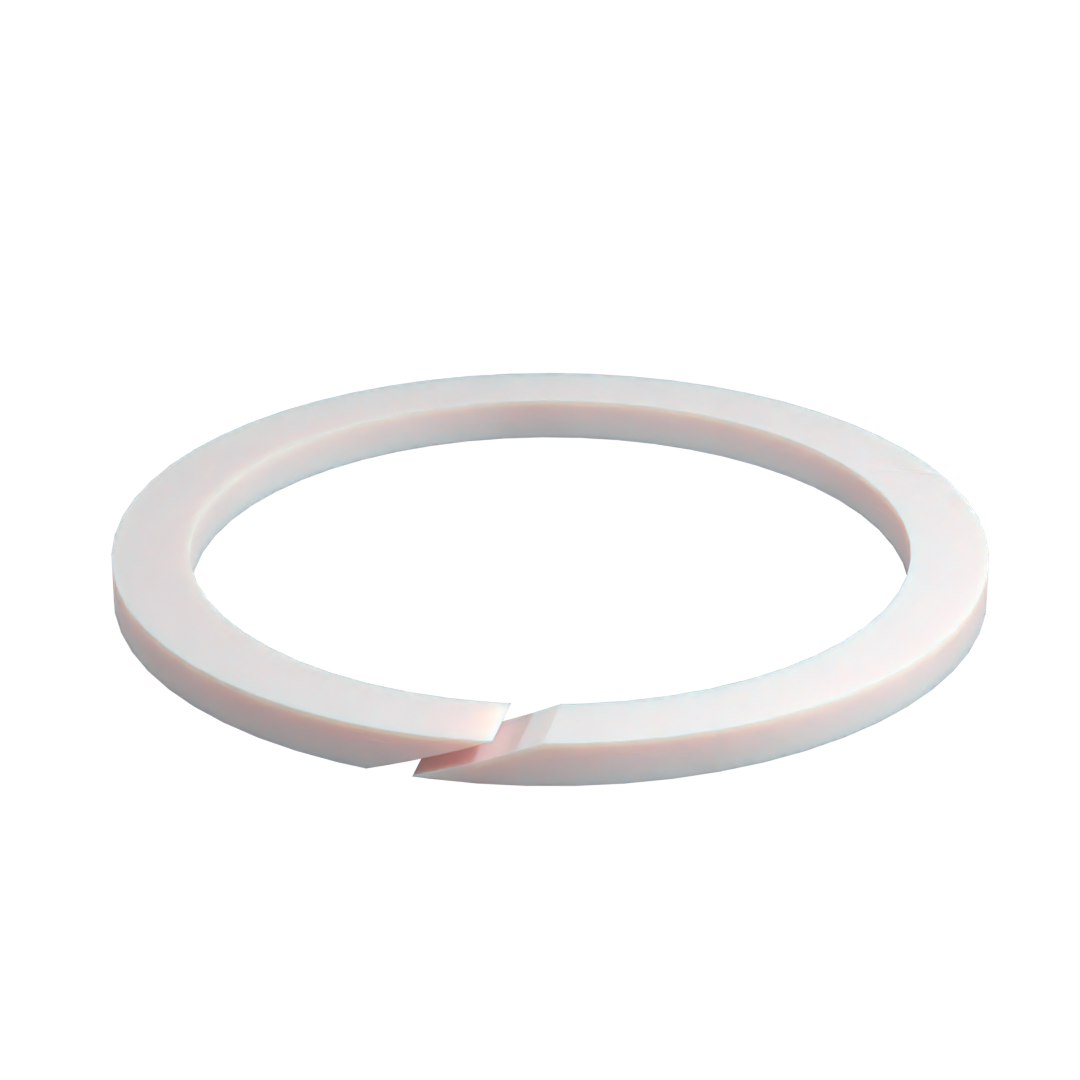
Spiral PTFE Backup Rings
Spiral PTFE backup rings are constructed from a continuous coil of PTFE material wound into a helical shape. This design provides several notable benefits:
- Uniform Pressure Distribution: The spiral construction ensures even pressure distribution along the sealing surface, reducing the risk of leakage and extending the lifespan of the primary seal.
- Flexibility and Resilience: The helical shape allows the ring to conform to the mating surfaces, even under dynamic motion and pressure differentials, making it suitable for demanding applications.
- Resistance to Harsh Conditions: PTFE material offers exceptional resistance to chemicals, high temperatures, and abrasive media, making spiral backup rings ideal for use in industries such as oil and gas, aerospace, and automotive manufacturing.
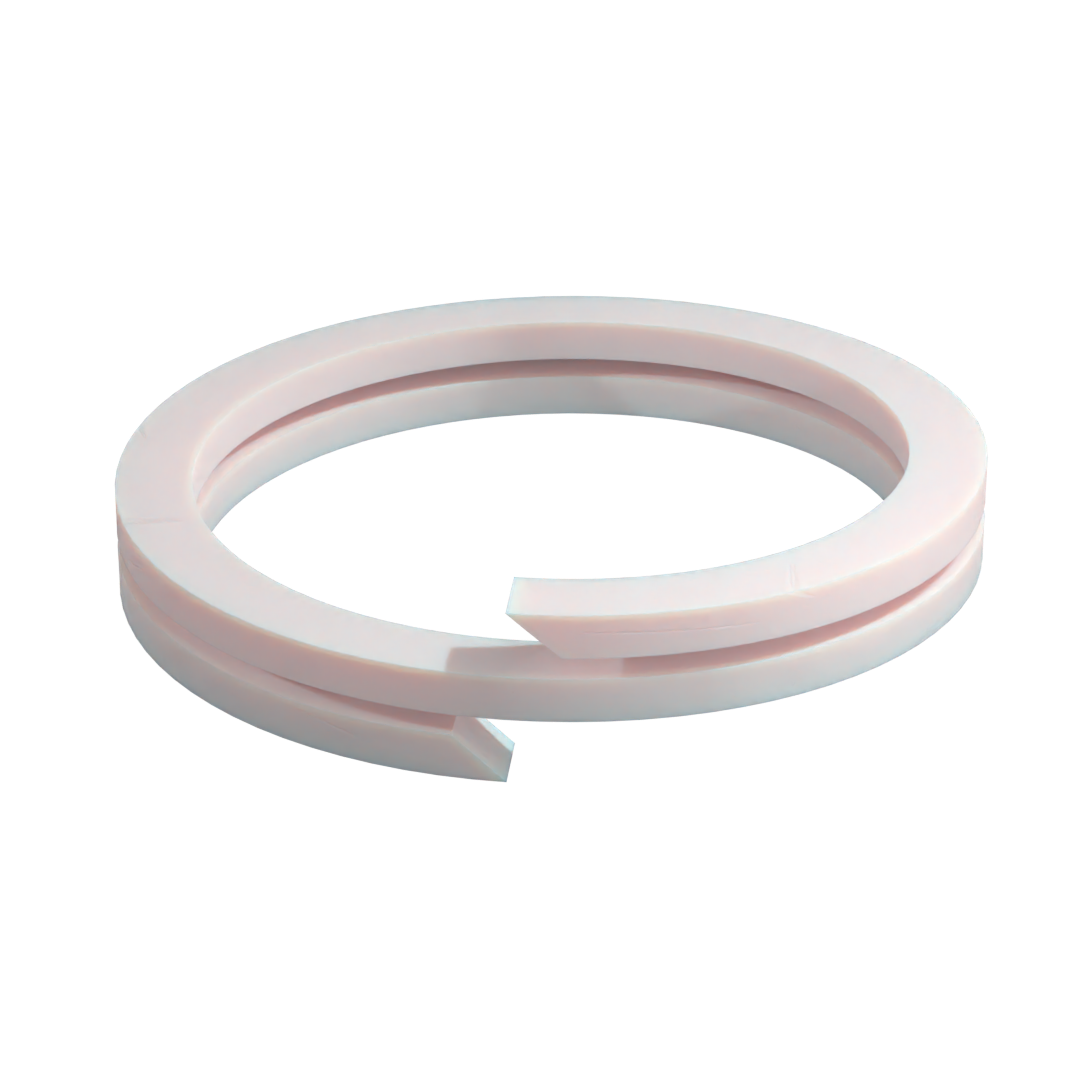
Manufacturing Options for Backup Rings
Backup rings can be manufactured using various methods, each offering unique benefits depending on the application:
Canyon Components strives to meet all customer service requests. Feel free to contact Canyon Components engineering and let our knowledgeable staff help you design the perfect part for your needs.
Machining
In some cases, backup rings are machined from solid materials, particularly when tight tolerances and specific dimensions are required.
Extrusion and Cutting
For custom-sized backup rings, extrusion followed by cutting to length is a common method, allowing for high customization and flexibility in production.
Injection Molding
Ideal for high-volume production, injection molding ensures consistent quality and precision in the final product.
Compression Molding
This method uses heat and pressure to shape backup rings from raw materials, making it suitable for producing strong and durable rings in lower quantities.
Die Cutting
Die-cutting from sheets of material is an efficient and cost-effective option for producing flat square rings or gaskets.
Square Ring Selection, Installation, and Maintenance
Backup rings are critical components that provide essential support to sealing systems in high-pressure and demanding applications. By understanding the features, types, and manufacturing options available, along with proper selection, installation, and maintenance practices, you can ensure the optimal performance and longevity of backup rings in your specific application. Whether you're working in hydraulic systems, aerospace, automotive, or industrial sectors, backup rings offer the reliability and durability required to maintain system integrity and prevent seal failure.
Canyon Components strives to meet all customer service requests. Feel free to contact Canyon Components engineering and let our knowledgeable staff help you design the perfect part for your needs.
Selection of Backup Rings
Selecting the right backup ring is crucial for ensuring optimal performance in your sealing system. Consider the following factors during selection:
- Material Compatibility: Ensure the backup ring material is compatible with the fluids, gases, and chemicals it will encounter. PTFE, for example, is ideal for chemically aggressive environments, while nylon is often used in hydraulic systems.
- Pressure Rating: Choose a backup ring that can handle the pressure levels in your application to prevent seal extrusion and failure.
- Temperature Range: Ensure the backup ring material can withstand the operating temperature of your system without degrading.
- Size and Fit: Proper sizing is essential for ensuring the backup ring provides adequate support to the primary seal without causing excessive compression or deformation.
- Application Type: Determine whether the backup ring will be used in a static or dynamic application, as this will influence material and design choices.
Installation of Backup Rings
Proper installation of backup rings is essential to ensure the effectiveness of the entire sealing system. Follow these guidelines for correct installation:
- Inspect the Backup Ring: Before installation, inspect the backup ring for any defects, such as nicks, cuts, or deformations.
- Use Lubrication: Apply a compatible lubricant to the backup ring to reduce friction during installation and prevent damage to the seal.
- Ensure Correct Placement: Install the backup ring on the low-pressure side of the primary seal (O-ring, X-ring, etc.) to provide effective support against extrusion.
- Align Properly: Ensure the backup ring is properly seated in the groove and that it is not twisted or pinched during installation.
- Use Installation Tools: When necessary, use specialized installation tools to avoid damaging the backup ring or the primary seal.
Maintenance of Backup Rings
Regular maintenance of backup rings and the associated sealing system can extend their lifespan and prevent system failures. Consider the following maintenance practices:
- Regular Inspections: Periodically inspect backup rings for signs of wear, cracking, or deformation. Replace any backup rings that show signs of damage or excessive wear.
- Monitor Operating Conditions: Ensure that the system’s operating conditions, such as pressure, temperature, and chemical exposure, remain within the specified limits for the backup rings.
- Clean Regularly: Keep the backup rings and surrounding components clean to prevent debris from causing wear or damage.
- Use the Right Lubricants: Maintain proper lubrication to reduce friction and wear on the backup rings during operation.
- Replace as Needed: Even with proper maintenance, backup rings will eventually wear out. Replace them according to the manufacturer’s recommended intervals or when signs of failure are evident.
Back to Products Hub
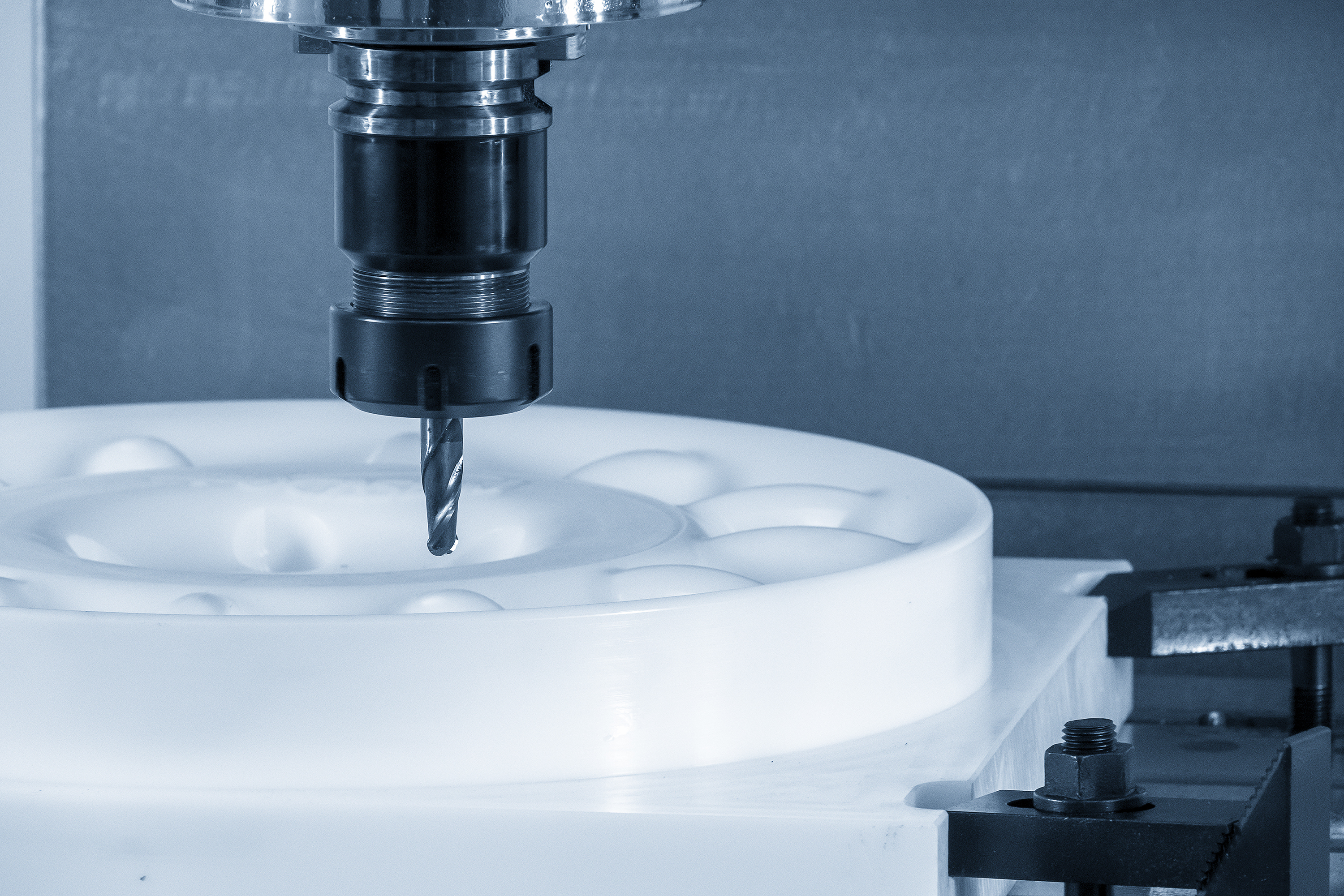
Get A Quote Now!
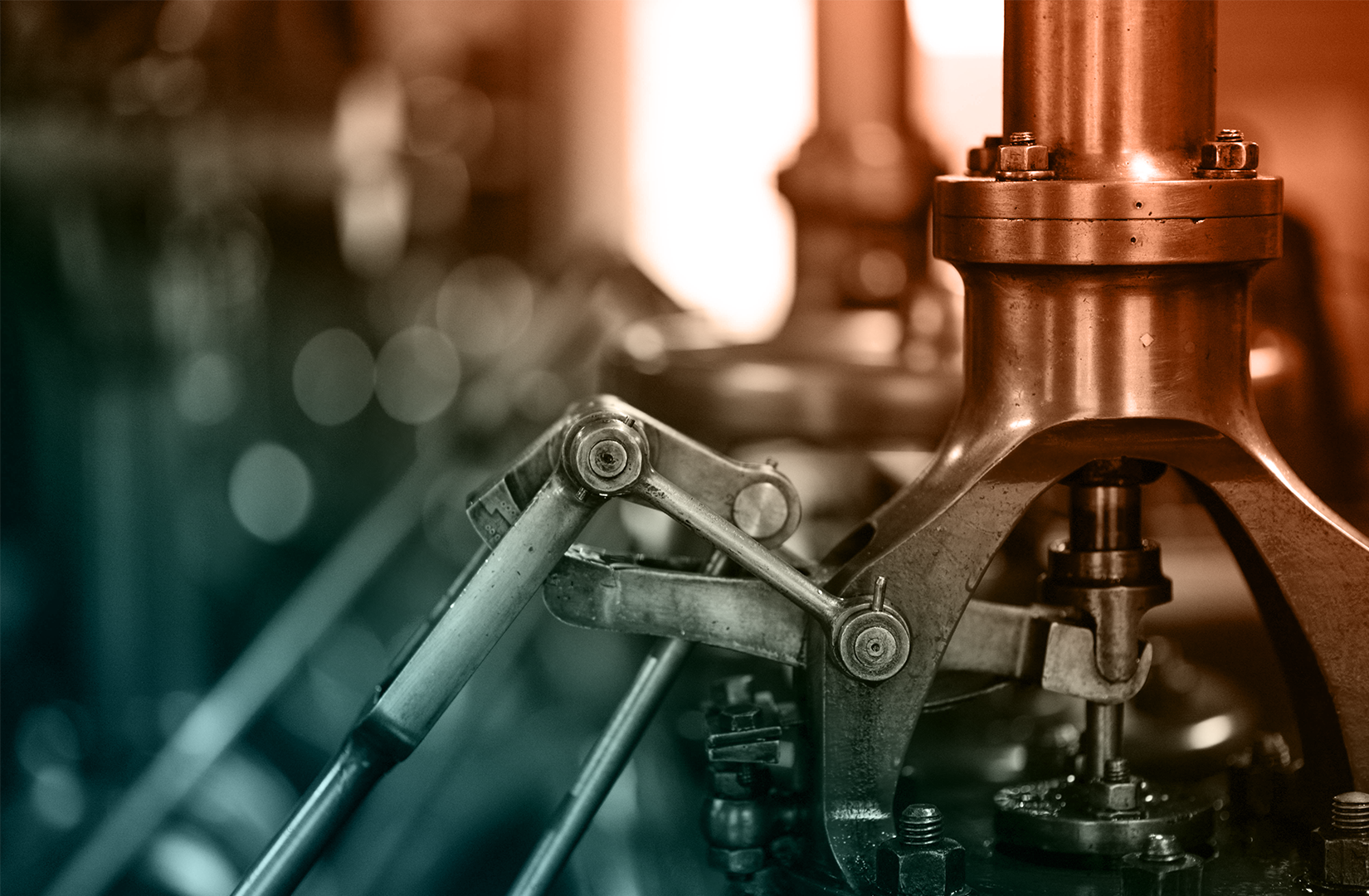