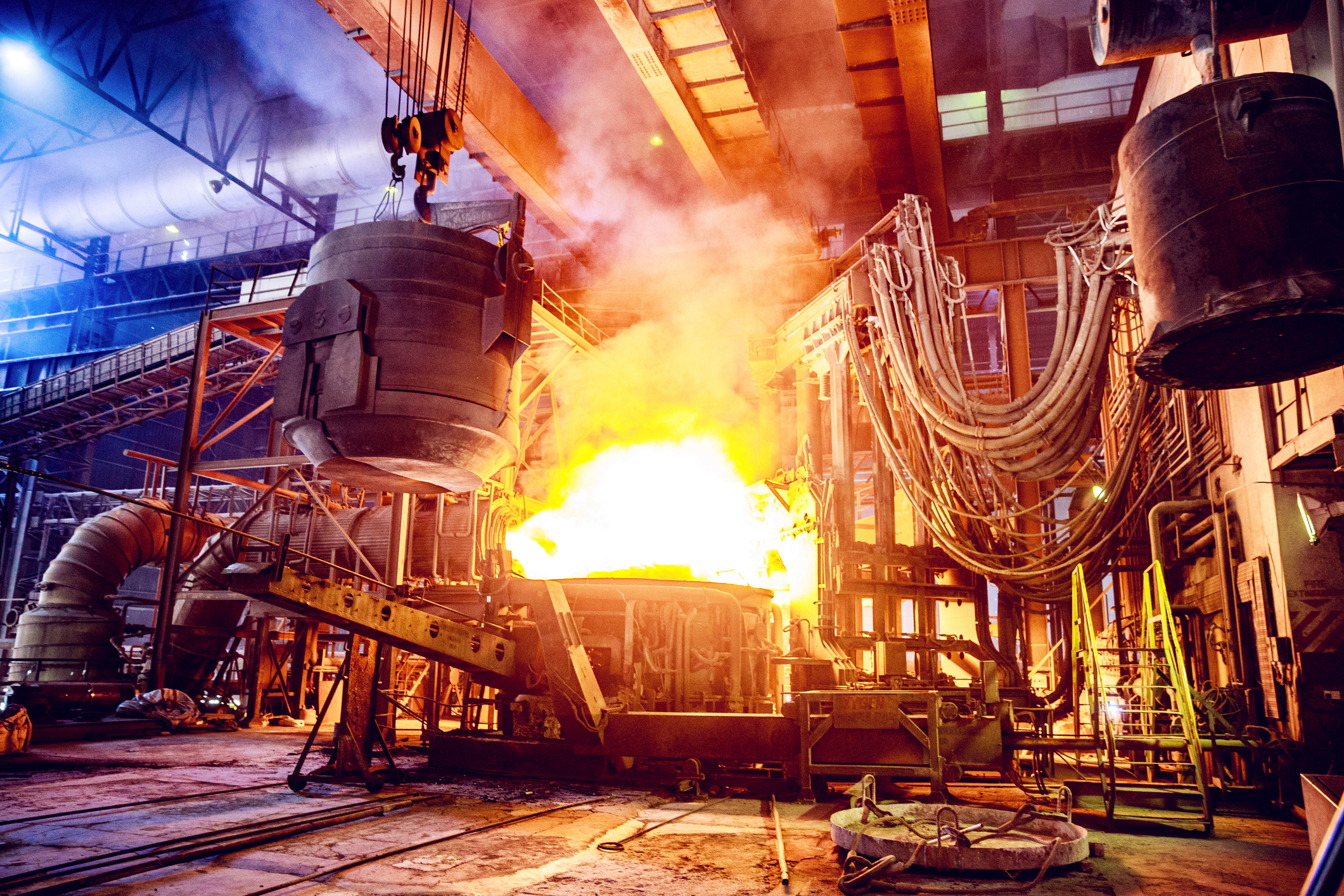
Liquid Silicone Rubber (LSR)
Liquid Silicone Rubber (LSR) is a versatile material widely used in manufacturing due to its exceptional properties, including flexibility, durability, and resistance to extreme environments. With its ability to be molded into intricate shapes, LSR is ideal for applications across medical, automotive, electronics, and consumer goods industries. This page delves into the features, common applications, and the pros and cons of LSR manufacturing, offering insight into why it’s a preferred material for a wide range of products.
Canyon Components carries a range of silicone O-rings, gaskets, & custom molded parts, and we are happy to custom tailor a seal to meet your application requirements! In addition to injection molded LSR (liquid silicone rubber), silicone can also be manufactured using standard compression molding. Silicone seals, O-rings, gaskets, & custom molded parts are popular in applications where extreme temperature fluctuations are common, such as the automotive and aerospace industries. Additionally, many silicone compounds, O-rings, gaskets, & custom molded parts are physiologically neutral making them ideal for the medical and food industries.
Common names include: VQM (Silicone), PVMQ Trade Name: Silastic®, Elastosil®, Thermoflex®, Wacker, DOW Corning, DOWSIL.
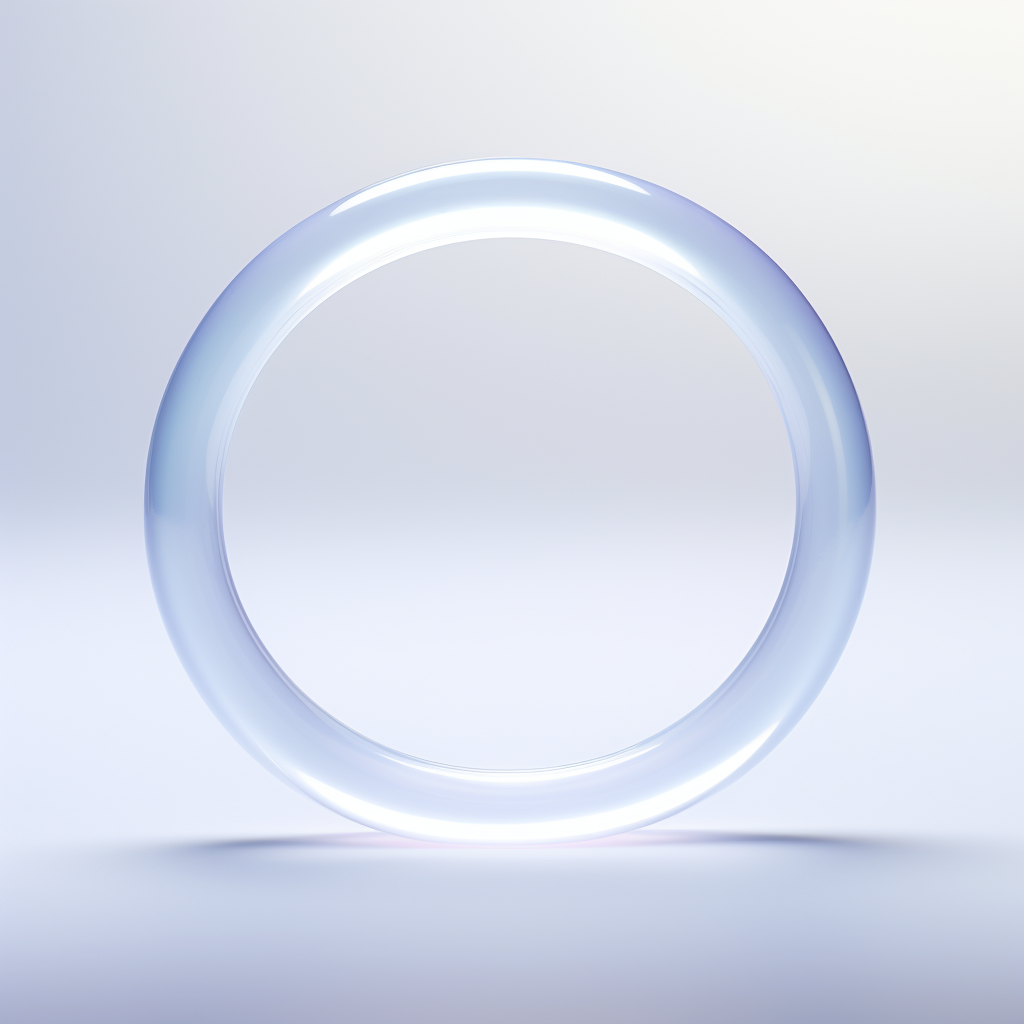
Features of LSR Manufacturing
- High Precision Molding: LSR is injected into molds with extreme precision, allowing for complex geometries and detailed features. This makes it suitable for parts requiring tight tolerances.
- Temperature Resistance: LSR can withstand a wide temperature range, from -90°F to 500°F (-68°C to 260°C) depending on the compound and application, making it ideal for both high-heat and cold environments.
- Biocompatibility: LSR is inherently biocompatible, making it safe for medical and food-grade applications. It meets stringent regulatory standards, including USP Class VI and FDA compliance.
- Durability: Resistant to UV light, ozone, and aging, LSR maintains its properties over time, even in harsh environments.
- Color Customization: LSR can be pigmented in a wide range of colors, allowing for aesthetic and functional customization.
- Short Cycle Times: LSR cures quickly, enabling efficient production with reduced lead times.
Common Applications of LSR
Medical and Healthcare:
- Catheters, seals, and gaskets
- Syringe components and wearable devices
- Implantable parts meeting biocompatibility requirements
Automotive:
- Gaskets, seals, and O-rings for high-temperature applications
- Keypads, connectors, and other interior components
- Noise-reducing and vibration-damping parts
Electronics:
- Waterproof seals for consumer electronics
- Keypads and buttons for devices
- Insulators and connectors in electrical systems
Consumer Products:
- Kitchenware, such as baking molds and utensils
- Infant products, including bottle nipples and pacifiers
- Wearable components for fitness and health monitoring devices
Industrial Applications:
- Seals for pumps and valves
- Custom parts for machinery exposed to extreme conditions
Please consult a Canyon Components Engineer about your specific application and we will use our decades of experience to formulate a solution that fits your need.
COMPOUND | COMPARABLE MATERIALS | ||||||
---|---|---|---|---|---|---|---|
Canyon™ VMQ | Color | Shore A | Temp (°C) | Description | Parker® | ||
SI70OR02 | Orange | 70 | -60 to +205 | FDA compliant for General Applications | S1138-70 | ||
SI50OR00 | Orange | 50 | -60 to +205 | Low durometer Orange silicone compliant | |||
SI50OR13 | Orange | 50 | -75 to +205 | Low durometer red silicone FDA compliant | S0383-70 | ||
SI30OR02 | Orange | 30 | -60 to +205 | Ultra low durometer orange silicone FDA compliant | |||
SI70RE04 | Red | 70 | -55 to +205 | FDA compliant and metal detectable for food processing equipment | |||
SI70TR37 | Clear | 70 | -55 to +205 | Translucent-Clear USP class VI silicone | |||
SI50TR35 | Clear | 50 | -55 to +205 | Low durometer Clear-Translucent silicone, FDA and USP class VI and ISO 10993-1 compliant | |||
SI30TR02 | Clear | 30 | -60 to +205 | Ultra Low duroemter Translucent Silicone FDA compliant | |||
SI80OR51 | Orange | 80 | -55 to +315 | Ultra High Temperature Orange Silicone | |||
SI70RE05 | Red | 70 | -60 to +205 | Externally Lubricated with Silicone oil for ease of installation and improved dynamic performance | |||
SI60BK15 | Black | 60 | -55 to +160 | Conductive Carbon filled for static dissipative black Silicone | |||
SI70YE00 | Yellow | 70 | -60 to +205 | General Purpose yellow silicone | |||
SI80TR00 | Clear | 80 | -60 to +205 | General Purpose higher durometer | |||
SI65TN11 | Tan | 65 | -45 to +125 | Silver plated copper filled silicone for EMI & RFI shielding, MIL-DTL-83528 Type A | Parker® Chomerics CHO-SEAL® 1215, 1273, 1270 | ||
SI65GY55 | Gray | 65 | -55 to +160 | Nickel plated aluminum filled silicone for EMI & RFI shielding, MIL-DTL-83528 |
LSR Manufacturing Pros & Cons
Liquid Silicone Rubber manufacturing offers unparalleled versatility, durability, and precision for a wide range of industries. Its unique properties make it a reliable choice for applications requiring biocompatibility, temperature resistance, and long-term performance. Whether for medical devices, automotive seals, or consumer goods, LSR provides a balance of functionality and efficiency, making it a cornerstone of modern manufacturing.
Canyon Components strives to meet all customer service requests. Feel free to contact Canyon Components engineering and let our knowledgeable staff help you design the perfect part for your needs.
Pros of LSR Manufacturing
- Versatility: LSR can be molded into intricate shapes, offering design flexibility for complex parts.
- Durability: Good resistance to chemicals, temperature, and environmental factors ensures long-lasting performance.
- Safety: Its non-toxic, biocompatible nature makes it suitable for sensitive applications, such as medical devices and food-contact products.
- Efficiency: The fast curing process reduces production time, enabling high-volume manufacturing.
- Aesthetic Options: Available in multiple colors and finishes, LSR components can meet functional and branding requirements.
Cons of LSR Manufacturing
- Initial Tooling Costs: The upfront investment in molds and tooling can be high, particularly for small production runs.
- Material Costs: LSR is more expensive than some alternatives, such as traditional rubbers, although its durability often offsets long-term costs.
- Limited Recyclability: While durable, LSR components are not easily recyclable, which may be a consideration for environmentally focused applications.
Get A Quote Now!
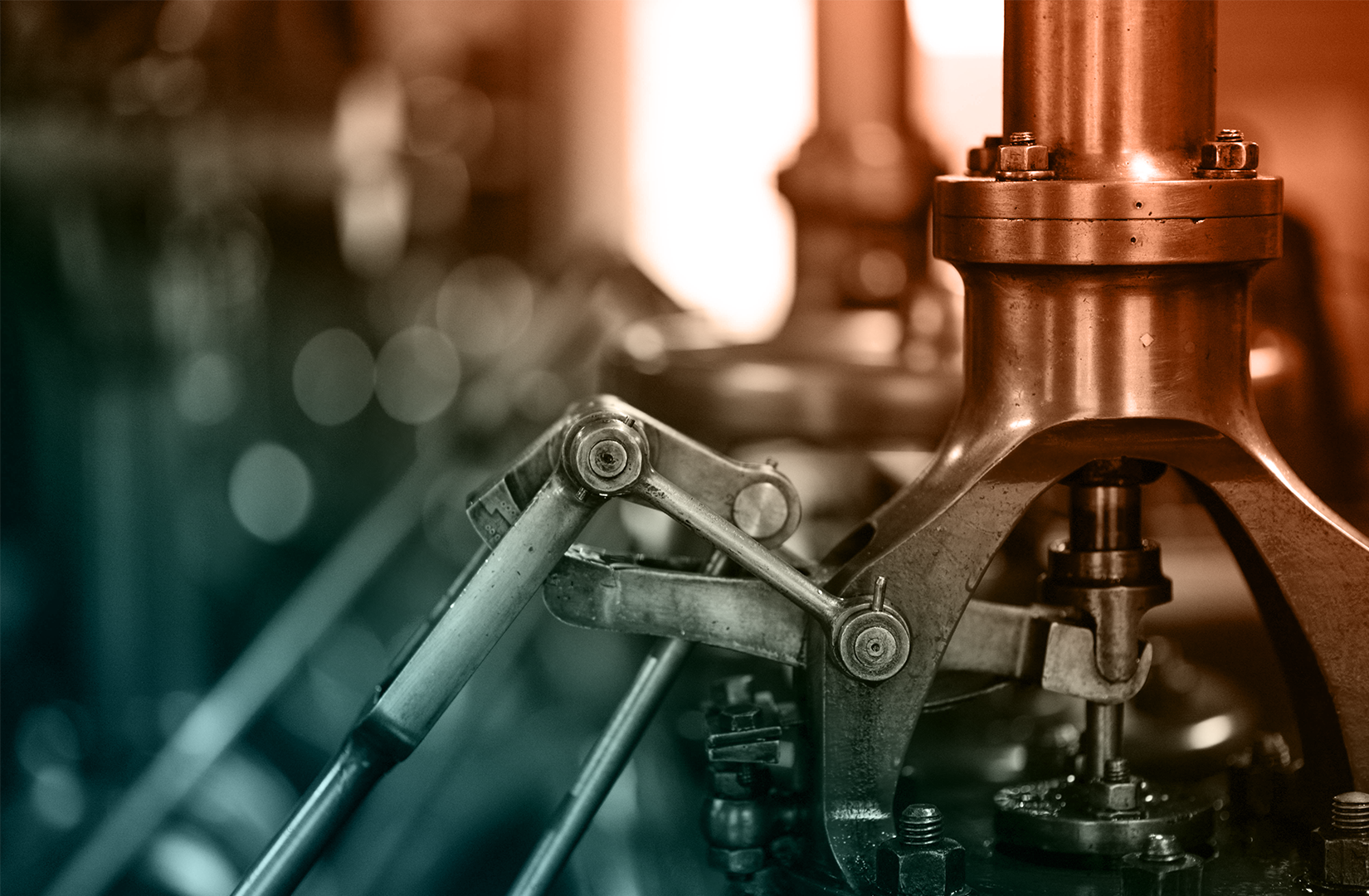
Groove Design References
Learn More
Coatings, Packaging, & Other Services
Learn More
Custom Parts & Custom O-rings
Learn More
Back to Elastomers Hub
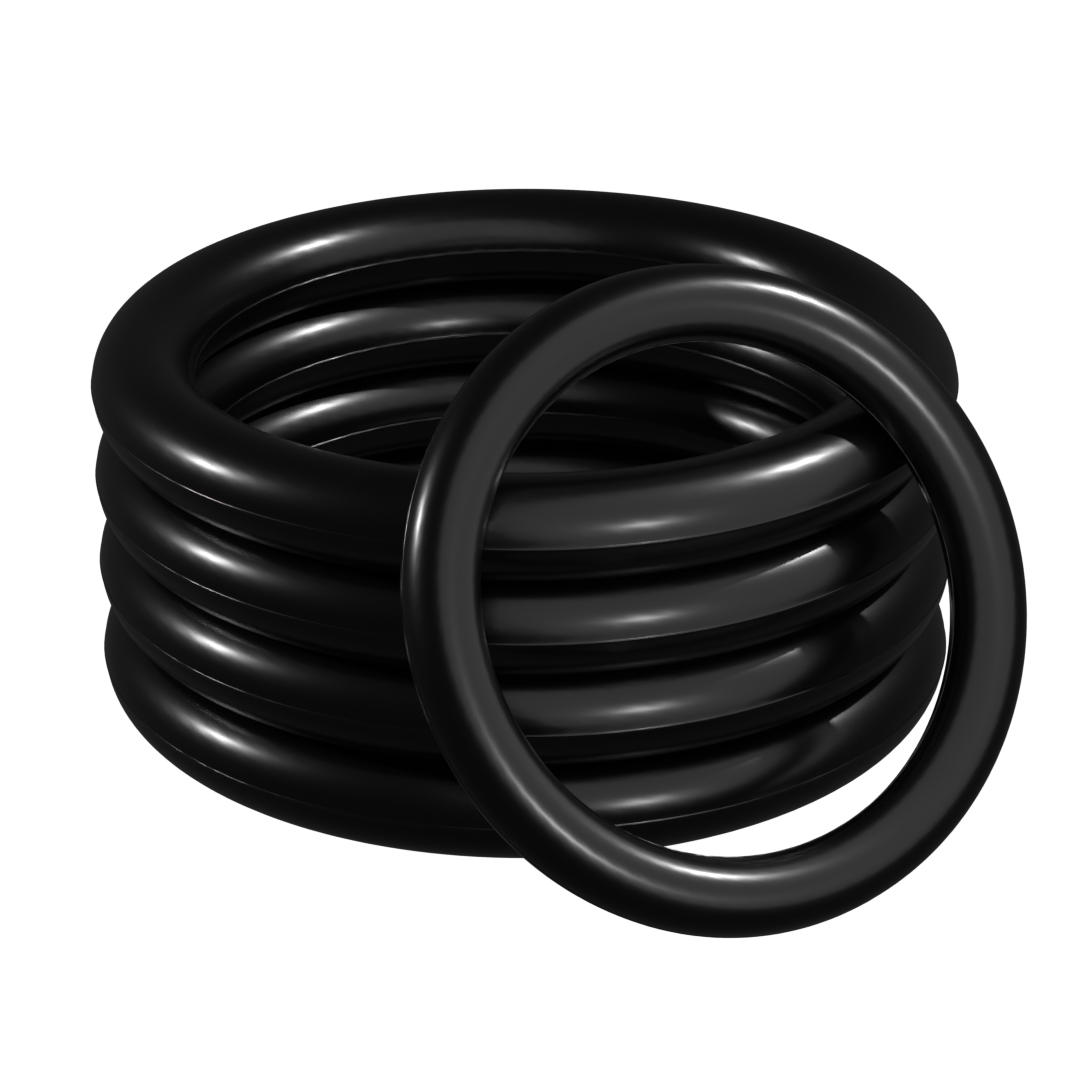