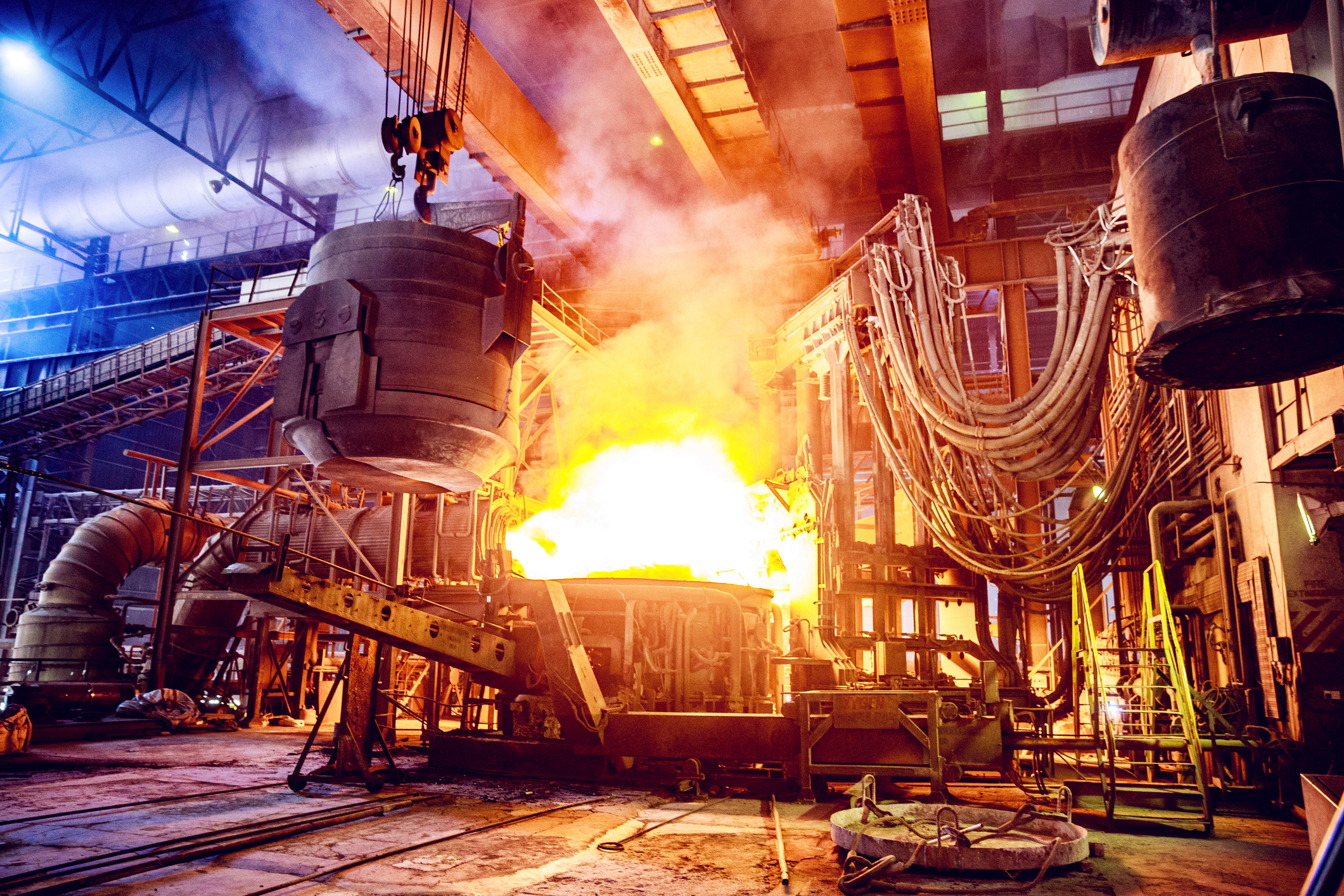
USP Class VI Materials
USP Class VI materials are essential for the manufacturing of components used in medical devices, pharmaceutical production, and biotechnology applications. These materials meet stringent biocompatibility and toxicity standards, ensuring that they are safe for use in environments that require the highest levels of cleanliness and reliability. This guide covers the key aspects of USP <88> and <87>, the types of rubbers and plastics used in these materials, common applications, and the pros and cons of using USP Class VI materials in medical and pharmaceutical settings.
USP Class VI CanRez® FFKM and Kalrez® O-rings, gasket rapid manufacturing, & custom molded parts for medical devices are available now!
Check with one of Canyon’s helpful product engineers for an expert material and manufacturing recommendation.
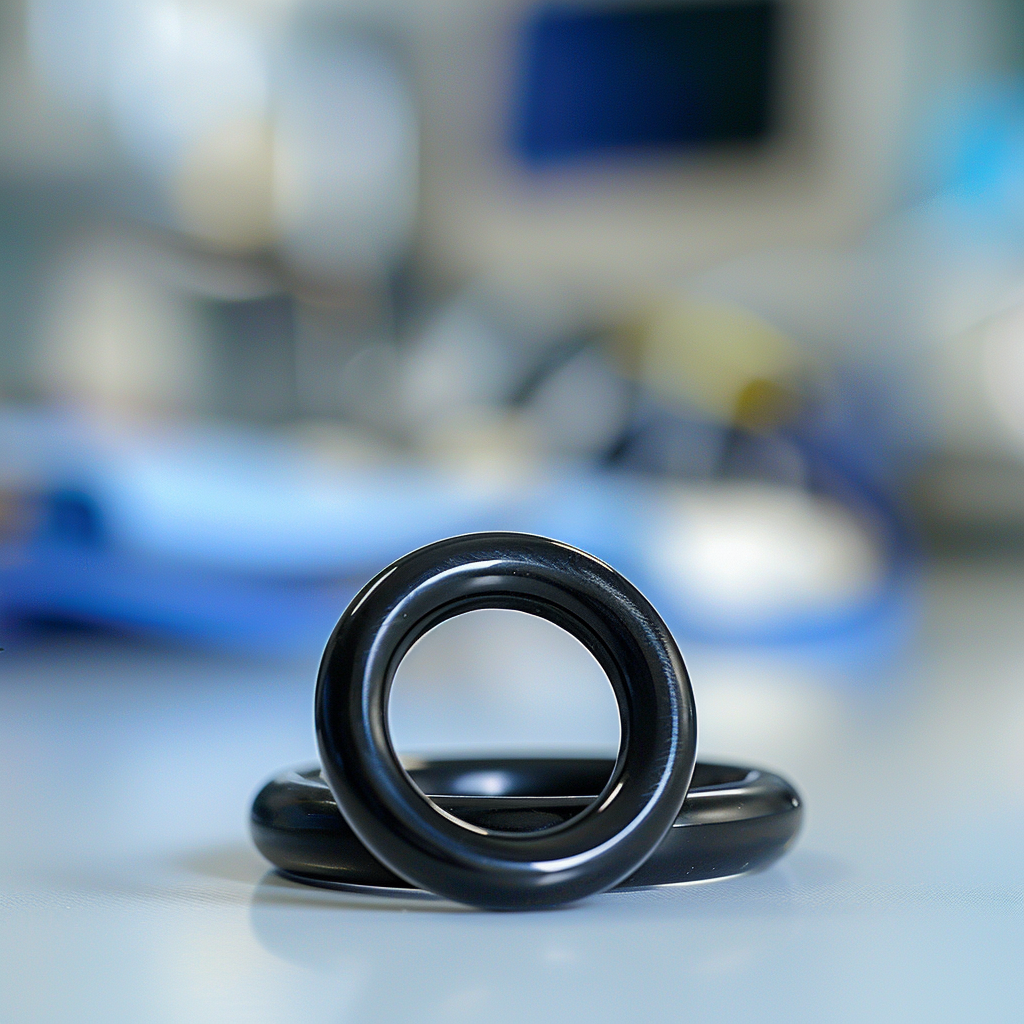
USP <88> and <87> Testing Standards
USP <88>: Biological Reactivity Tests
- USP <88> outlines a series of biological reactivity tests, both in vivo and in vitro, to ensure that the materials used in medical devices and pharmaceutical manufacturing are safe for direct or indirect contact with human tissue. These tests assess the potential toxicity, irritation, and inflammatory response of materials, ensuring they are safe for prolonged use in medical and pharmaceutical environments.
- In Vivo Testing: This includes systemic toxicity, intracutaneous, and implantation tests, which assess the biological response to the material when it comes into contact with living tissues.
- In Vitro Testing: These tests examine the cytotoxicity of the material in a controlled lab environment, ensuring it does not cause cell damage.
USP <87>: Biological Reactivity Tests, In Vitro
- USP <87> focuses primarily on in vitro cytotoxicity testing. It determines whether materials used in medical devices and pharmaceutical applications are toxic to living cells. This standard is critical for materials that come into contact with drugs, human tissue, or bodily fluids, such as tubing, seals, and other components used in medical devices and pharmaceutical manufacturing.
Common Applications of USP Class VI Materials
USP Class VI materials are essential in the manufacturing of medical devices and pharmaceutical equipment due to their safety and reliability. Common applications include:
- Medical Devices: Seals, gaskets, and tubing made from USP Class VI materials are used in critical medical devices such as catheters, infusion pumps, and implantable devices.
- Pharmaceutical Manufacturing: These materials are widely used in pharmaceutical processing equipment, including bioreactors, pumps, and valves, where contamination must be prevented.
- Biotechnology: In biotechnology applications, USP Class VI materials are used in filtration systems, tubing, and connectors to ensure the purity of biological products.
- Sterilization Equipment: Many USP Class VI materials are used in autoclaves and other sterilization equipment due to their ability to withstand extreme temperatures and chemical exposure.
Please consult a Canyon Components Engineer about your specific application and we will use our decades of experience to formulate a solution that fits your need.
USP Class VI Materials Available
This table shows many of our standard materials and links out to our O-ring store. Get in touch with us if you need a custom gasket, custom molded part, or non-standard geometry!
Filter by
Temperature Search (°C)
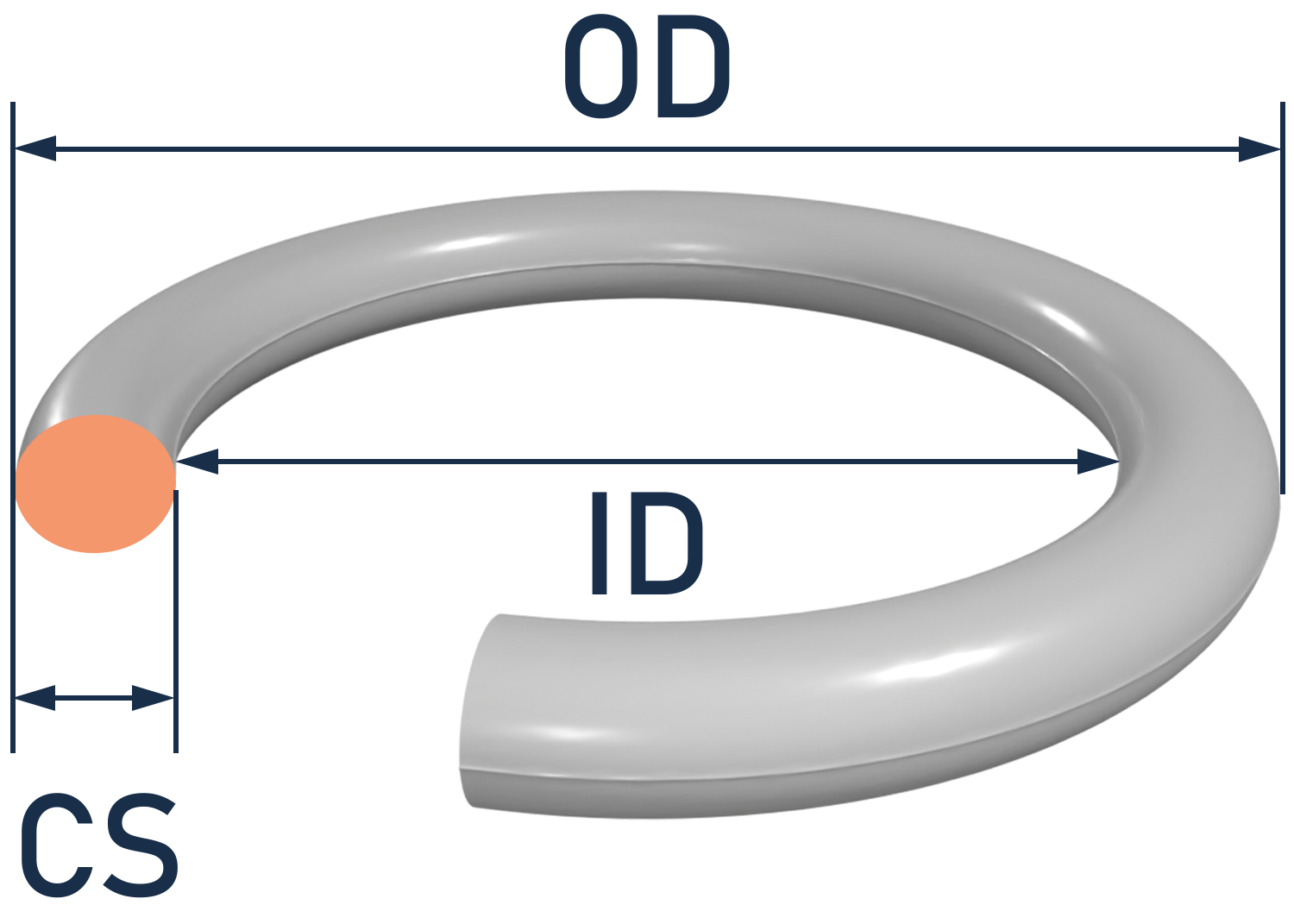
Get a Quote Now!
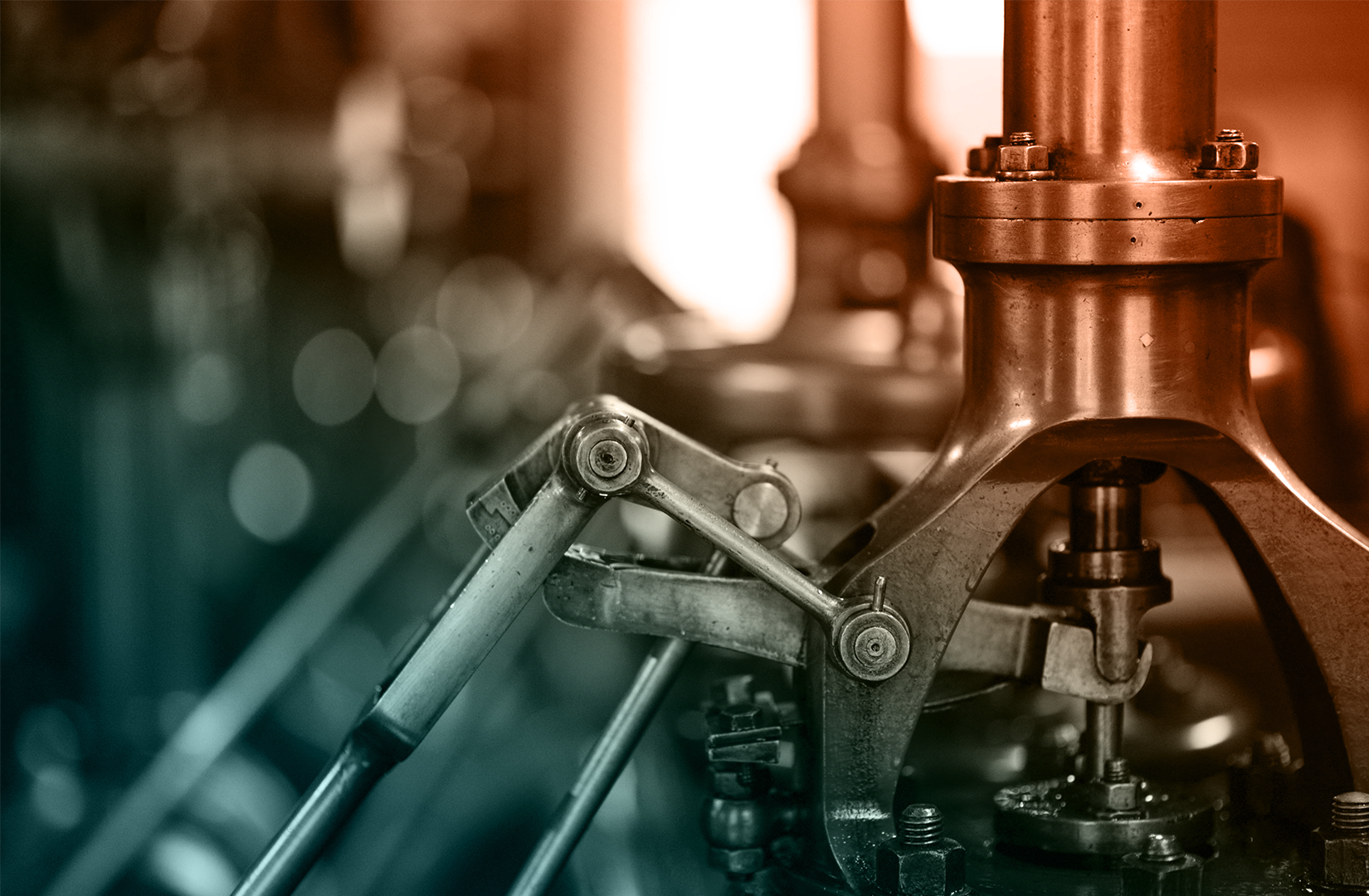
USP Class VI Elastomers
Medical Grade Materials
Explore USP Class VI materials, certified for use in medical devices, pharmaceuticals, and food processing. Learn about their features, compliance standards, and how they ensure safety and purity in critical environments.
Specialty Compliances
Canyon have materials available for O-rings, gaskets, & custom parts with compliances ranging from USP Class VI <87> & <88> for medical applications, to FDA CFR 21.177.2600 grades A through F for different food types, to the various drinking water specifications like KTW and NSF. Whether it's metal, rubber, or plastic, Canyon can meet your needs!
Custom Parts
Here at Canyon Components, we make sure to offer our customers any manufacturing technique they desire. Whether your USP Class VI O-rings, gaskets, & custom molded parts be rubber, plastic, or metal, rest assured that Canyon Components can make it!
CanRez™ FFKM Perfluoroelastomer
Extreme temperatures & chemicals require extreme solutions! USP Class VI CanRez™ FFKM materials offer extreme reliability where you need it most! Thousands of sizes in stock now!
Kalrez® FFKM Perfluoroelastomer
Canyon Components offers USP Class VI Kalrez® Perfluoroelastomer (FFKM) O-rings, gaskets, & custom molded parts at competitive prices and with great lead-times.
USP Class VI Parker® O-rings, Parofluor parts, parker FKM Viton
Canyon Components offers USP Class VI Parker Hannifin® O-rings, Gaskets, USP Class VI Perfluoroelastomer (FFKM) parts, & custom molded parts at competitive prices and with great lead-times.
FKM (Viton®, Fluorocarbon)
USP Class VI FKM compounds, O-rings, gaskets, & custom molded parts exhibit excellent mechanical attributes as well as excellent resistance to high temperatures, mineral oil, ozone, fuels, hydraulic fluids, and many other solvents and chemicals.
Fluorosilicone (FVMQ)
The mechanical and physical properties of USP Class VI Fluorosilicone O-rings, gaskets, & custom molded parts are very similar to silicone. Fluorosilicone O-rings, gaskets, & custom molded parts offer improved flexibility and strength, better resistance to fuels and mineral oil, but reduced hot air resistance.
Silicone (VMQ, PVMQ)
USP Class VI Silicone seals, O-rings, gaskets, & custom molded parts are excellent for extreme temperatures in static applications. Canyon Components carries a range of silicone materials, and we are happy to custom tailor a seal to meet your application requirements!
EPDM (Ethylene Propylene)
USP Class VI EPDM materials, O-rings, gaskets, & custom molded parts can operate over a wide temperature range, and are compatible with glycol fluids that cause problems for most typical elastomeric seals.
NBR (Nitrile, Buna-N)
USP Class VI Nitrile O-rings, gaskets, & custom molded parts are very oil-resistant, have strong mechanical properties, are resistant to wear, and are relatively inexpensive. These properties make Nitrile the most commonly used general purpose O-ring, gasket, & custom molded part material.
PTFE Encapsulated
USP Class VI FEP and PFA encapsulated O-rings consist of an elastomeric core and a seamlessly closed casing of modified PTFE. The elastomer core of encapsulated O-rings is typically made of FKM (Viton) or VMQ (silicone) and guarantees a uniform pre-tensioning at the sealing point.
PTFE (Teflon)
The harshest environments require specialized solutions. Often times, a Canyon Components USP Class VI PTFE O-rings are used in harsh chemical environments. Polytetrafluoroethylene, commonly known as PTFE or Teflon®, is a high-performance fluoropolymer known for its exceptional chemical resistance, low friction, and non-stick properties.
USP Class VI Plastics
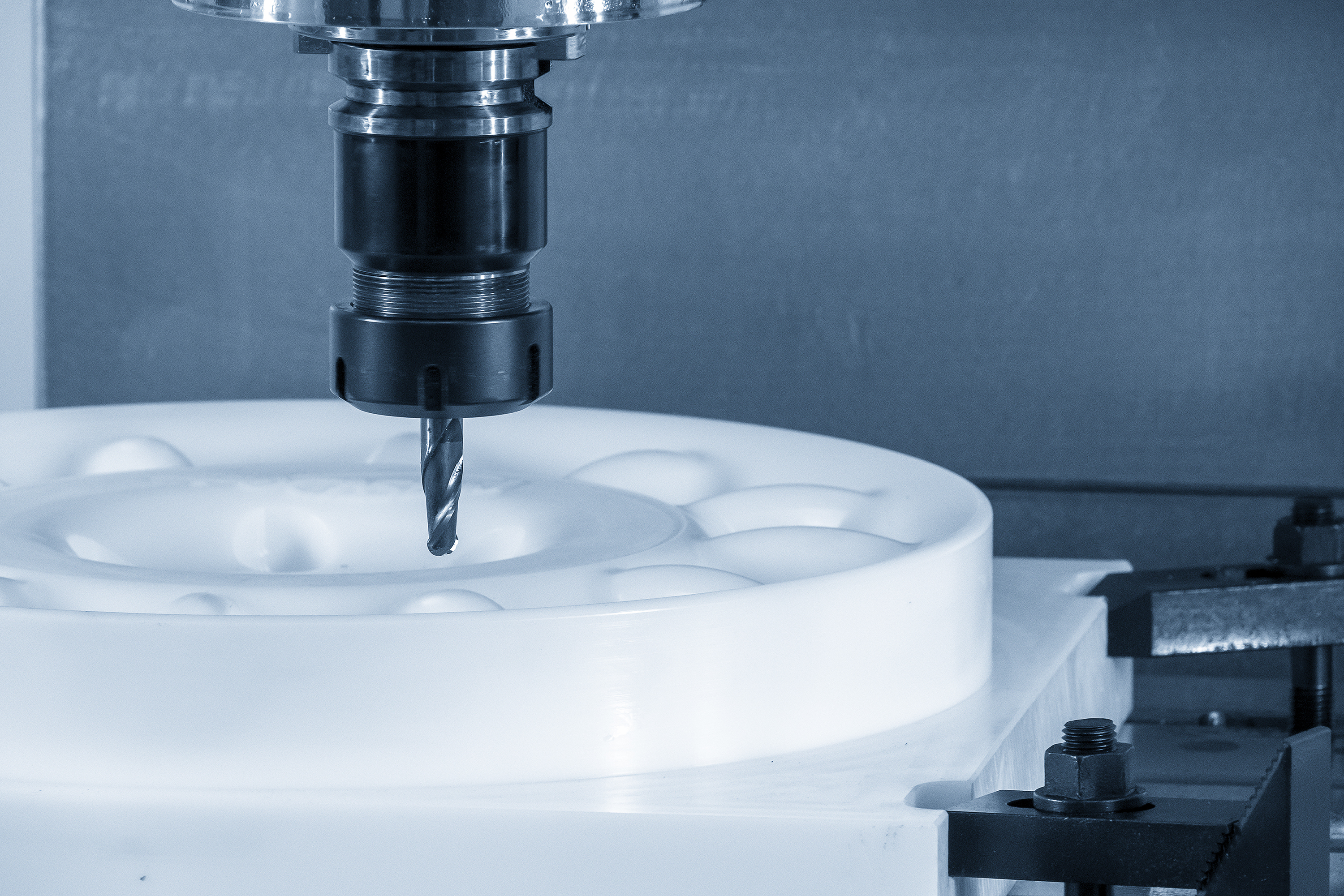
X-Ray and Metal Detectable Materials
In addition to their USP Class VI compliance, many materials are also available in x-ray and metal detectable versions. These additives significantly improve safety and quality control processes in medical device manufacturing, pharmaceutical production, and food-related applications:
- X-Ray Detectable Materials: These materials are formulated with additives that make them visible during x-ray inspections, allowing manufacturers to detect any foreign material contamination in products, such as medical devices or pharmaceutical components, ensuring product safety and purity.
- Metal Detectable Materials: Metal detectable USP Class VI materials contain metal particles that can be easily identified by standard metal detection systems. This provides an additional safeguard in environments such as medical device manufacturing and pharmaceutical production, ensuring that any material contamination is quickly identified and removed from the production line.
- Improved Quality Control: The incorporation of x-ray and metal detectable properties in USP Class VI materials enhances safety protocols and quality assurance. These materials help minimize the risk of contamination, product recalls, and regulatory non-compliance, ensuring that the highest standards are consistently met throughout the production process.
Canyon Components strives to meet all customer service requests. Feel free to contact Canyon Components engineering and let our knowledgeable staff help you design the perfect part for your needs.
USP Class VI Materials Pros & Cons
USP Class VI materials are a critical component in the medical device and pharmaceutical manufacturing industries. With their excellent biocompatibility, chemical resistance, and durability, these materials ensure that devices and equipment meet the highest standards of safety and performance. While the cost and processing requirements may be higher, the benefits of using USP Class VI materials, particularly in sensitive applications such as drug delivery systems and sterilization equipment, make them indispensable for manufacturers. Understanding the features, applications, and pros and cons of USP Class VI materials will help you make informed decisions to ensure the safety and reliability of your medical and pharmaceutical products.
Canyon Components strives to meet all customer service requests. Feel free to contact Canyon Components engineering and let our knowledgeable staff help you design the perfect part for your needs.
Pros of USP Class VI Materials
The use of USP Class VI materials in medical devices and pharmaceutical manufacturing offers several significant advantages:
- Biocompatibility: These materials are rigorously tested to ensure they are safe for direct contact with human tissues and fluids, making them ideal for use in medical devices and pharmaceutical equipment.
- Chemical Resistance: USP Class VI materials offer excellent resistance to a wide range of chemicals, ensuring they do not degrade or react with pharmaceutical products or sterilization chemicals.
- Durability: Whether exposed to high temperatures, chemicals, or repeated sterilization, USP Class VI materials maintain their performance and integrity over time, providing long-lasting reliability.
- Regulatory Compliance: By using USP Class VI materials, manufacturers ensure their products meet the highest regulatory standards for medical devices and pharmaceutical equipment.
Cons of USP Class VI Materials
While USP Class VI materials offer numerous benefits, there are also some potential drawbacks to consider:
- Higher Cost: The extensive testing and certification required for USP Class VI compliance can increase the cost of materials compared to non-certified alternatives.
- Material Limitations: Not all rubber and plastic materials can meet USP Class VI requirements, limiting the choice of materials for specific applications.
- Processing Complexity: The manufacturing processes for USP Class VI materials may be more complex, requiring specialized equipment and expertise to ensure compliance with testing standards.
Relevant Compliances
Clean Room Manufactured Materials: Precision and Purity for Critical Applications
Discover clean room manufactured materials, designed for use in industries requiring the highest levels of purity and precision. Learn about their features, applications, and how they meet strict cleanliness standards in medical, pharmaceutical, and semiconductor environments.
FDA Compliant Materials: Safe and Reliable Solutions for Food and Medical Applications
Discover FDA compliant materials, designed for use in food processing, medical devices, and pharmaceutical applications. Learn about their safety features, regulatory compliance, and how they meet stringent industry standards.
Medical and Pharmaceutical | Canyon Components
Discover Medical & Pharmaceutical Materials: designed for safety, compliance, and performance in medical devices, pharmaceutical manufacturing, and drug delivery.
Back to Compliance Hub
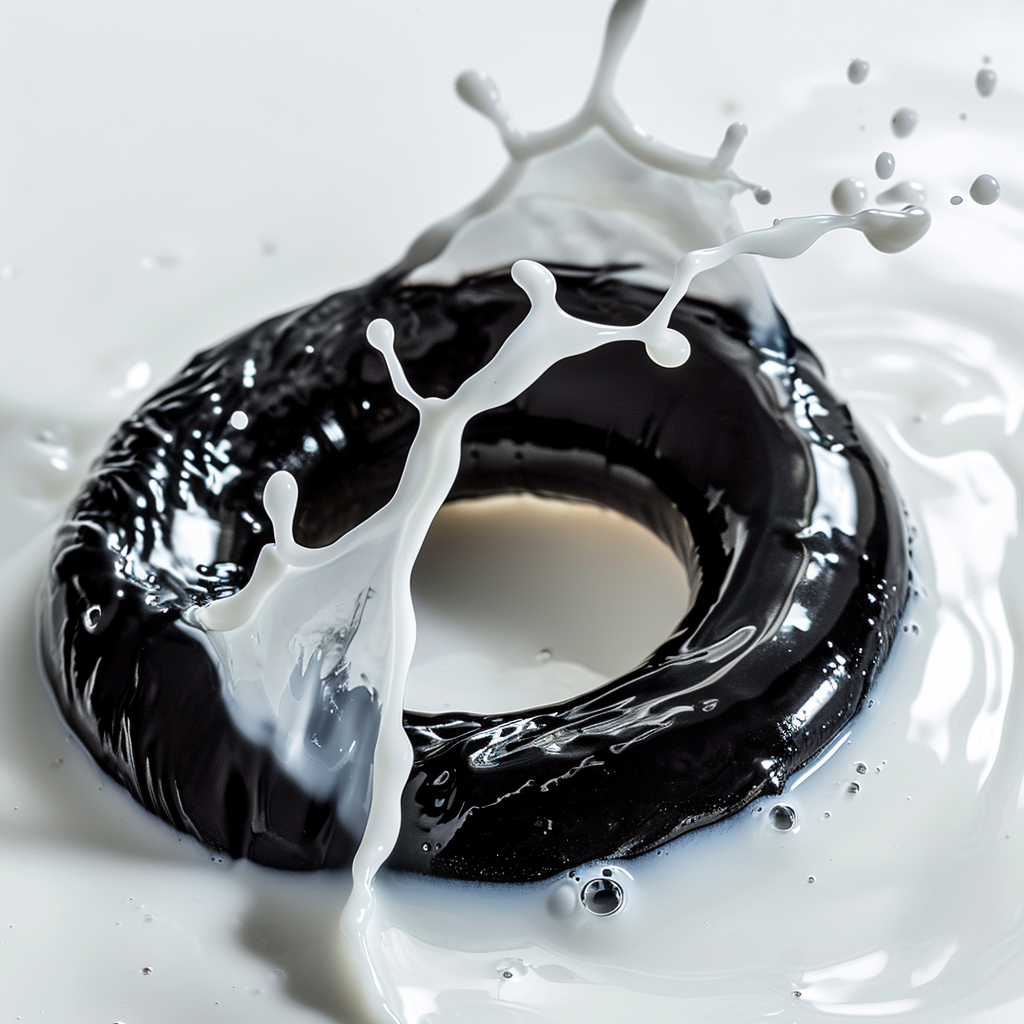
Get A Quote Now!
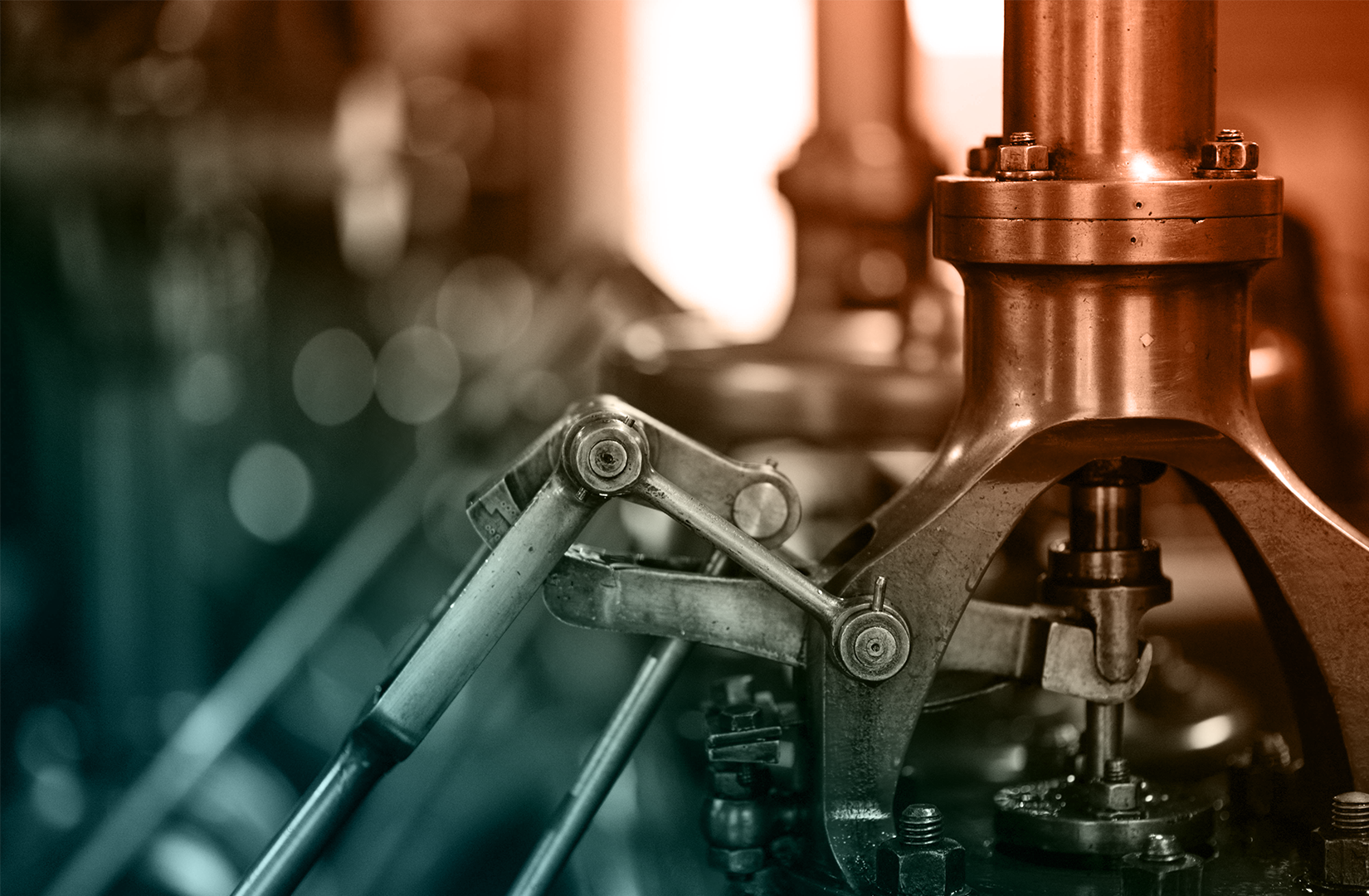