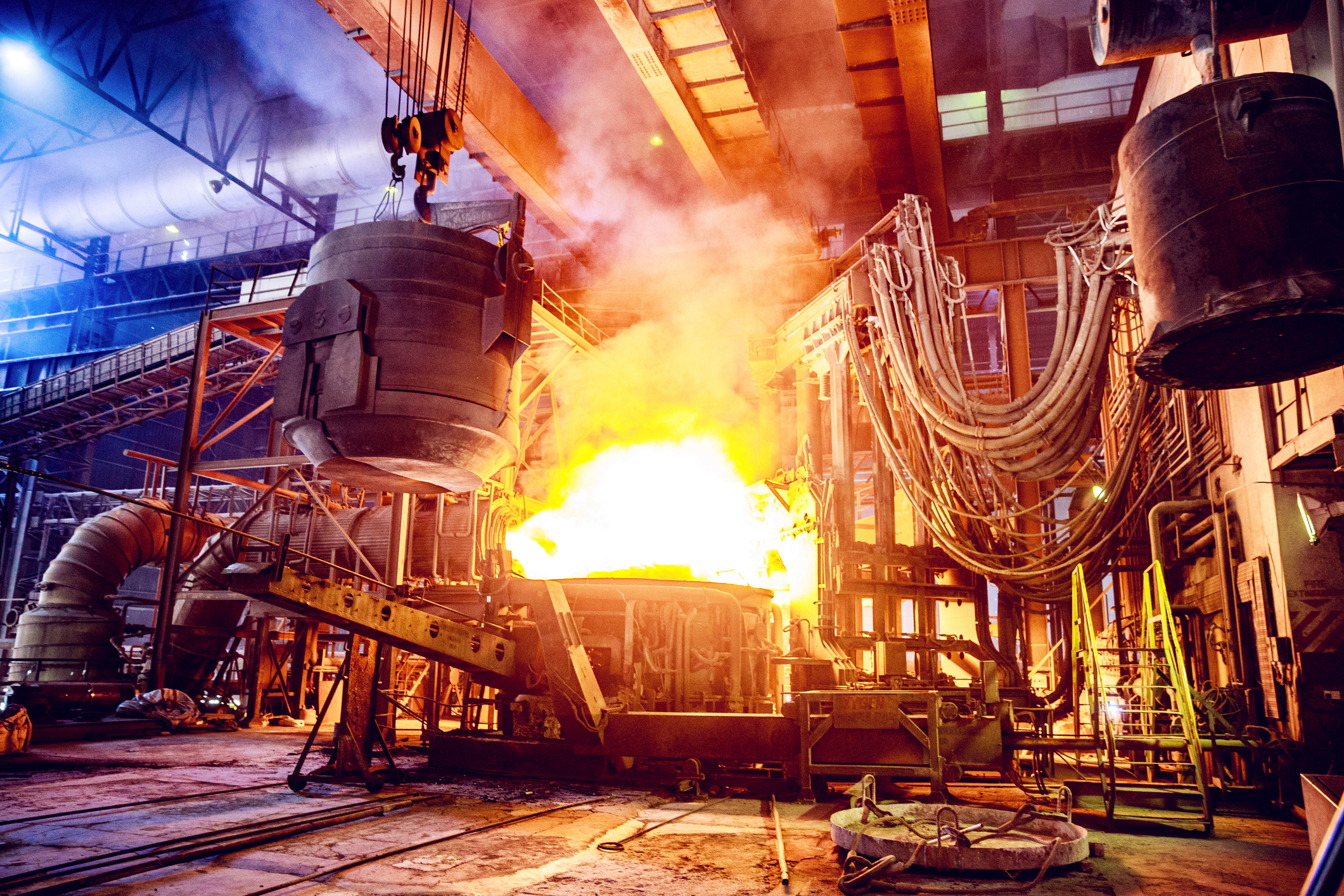
Cap Seals for Rod and Piston Applications
Cap seals for rod and piston applications are engineered to provide superior sealing performance in dynamic environments, where high pressures, extrusion resistance, and reliability are essential. These seals consist of an O-ring and a plastic cap, offering a combination of elasticity, flexibility, and durability. Widely used in machine tools, injection molding machines, and presses, cap seals are designed to handle the challenges of dynamic applications, such as reciprocating movements, pressure fluctuations, and high-speed operations.
CanRez® FFKM and Kalrez® with cap seals, grommets, O-rings, gasket rapid manufacturing, & custom molded parts are available now!
Check with one of Canyon’s helpful product engineers for an expert material and manufacturing recommendation.
Common names include: Turcon®, Stepseal®, Glyde Ring®, Hallite P54, Parker OE
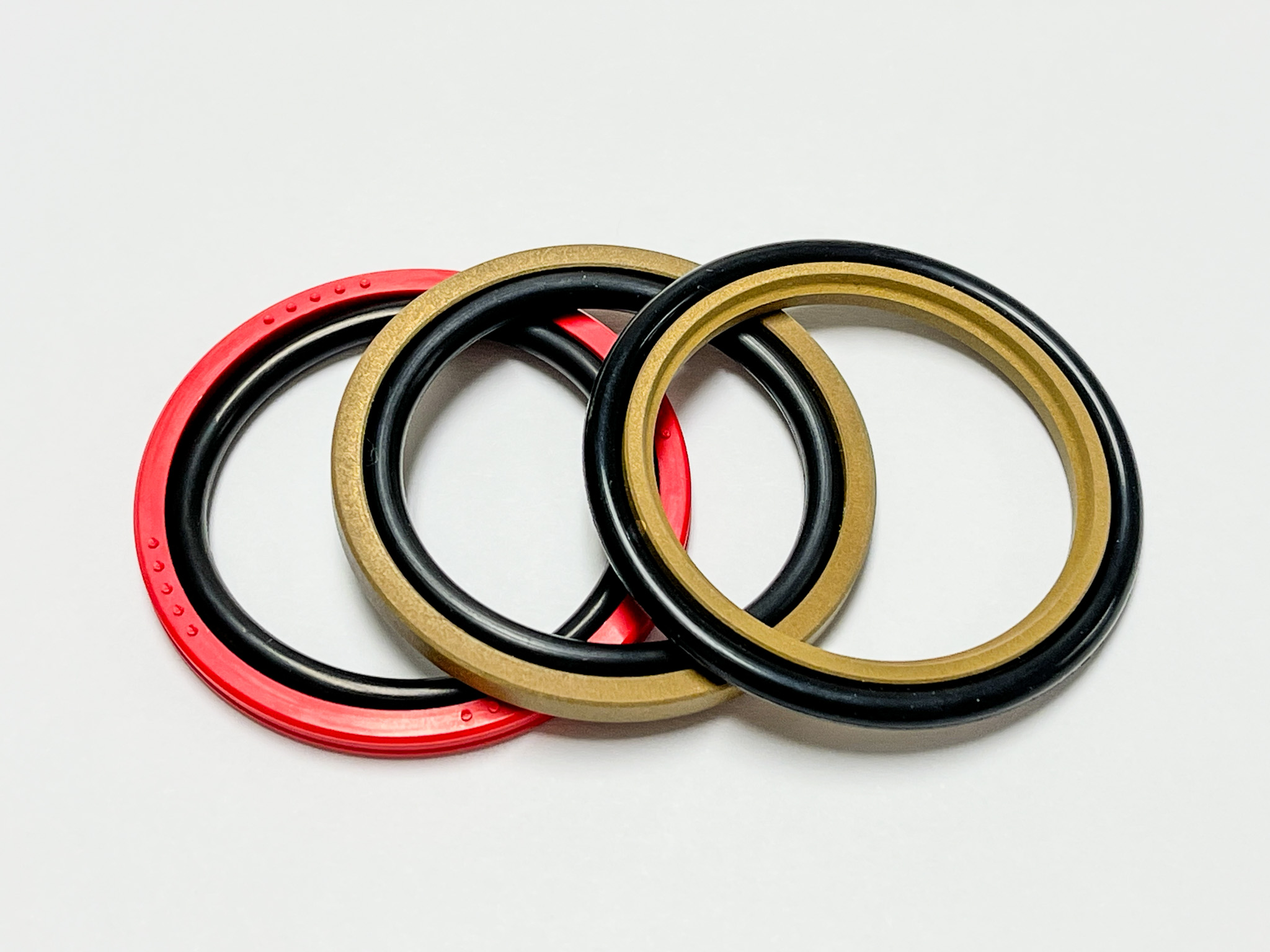
Features of Cap Seals for Rod and Piston Applications
Cap seals offer several key features that make them suitable for demanding dynamic applications:
- High Extrusion Resistance: The plastic cap component provides excellent extrusion resistance, ensuring the seal remains intact even under high pressures, preventing leakage and extending service life.
- Dynamic Sealing Performance: Cap seals are specifically designed for dynamic applications, providing reliable sealing in reciprocating and rotating movements, making them ideal for rod and piston applications.
- Low Friction: The combination of an O-ring and a low-friction plastic cap ensures smooth operation, reducing wear and tear on both the seal and the hardware, which is essential for high-speed applications.
- Broad Temperature Range: Cap seals can operate effectively across a wide range of temperatures, maintaining their sealing integrity in both high and low-temperature environments.
- Fluid Compatibility: These seals are resistant to a variety of fluids, including hydraulic oils, water, and some chemicals, ensuring long-lasting performance in diverse applications.
Common Applications of Cap Seals
Cap seals are widely used in industries that demand reliable, high-performance sealing solutions in dynamic environments:
- Machine Tools: Cap seals are frequently used in machine tools, where they provide reliable sealing in hydraulic cylinders and systems that operate under high pressures and dynamic movements.
- Injection Molding Machines: In injection molding machines, cap seals are used in hydraulic cylinders to ensure leak-free operation and resist extrusion, even under high-pressure cycles.
- Presses: Cap seals are ideal for hydraulic and pneumatic presses, where they handle the dynamic motion of rods and pistons, providing effective sealing and extrusion resistance.
- Hydraulic Cylinders: These seals are commonly used in hydraulic cylinders for construction, industrial, and agricultural equipment, providing dependable sealing in applications with reciprocating motion.
- Pneumatic Actuators: Cap seals are suitable for pneumatic systems where they maintain sealing integrity in applications that require dynamic movement and high-speed operation.
Please consult a Canyon Components Engineer about your specific application and we will use our decades of experience to formulate a solution that fits your need.
Get a Quote Now!
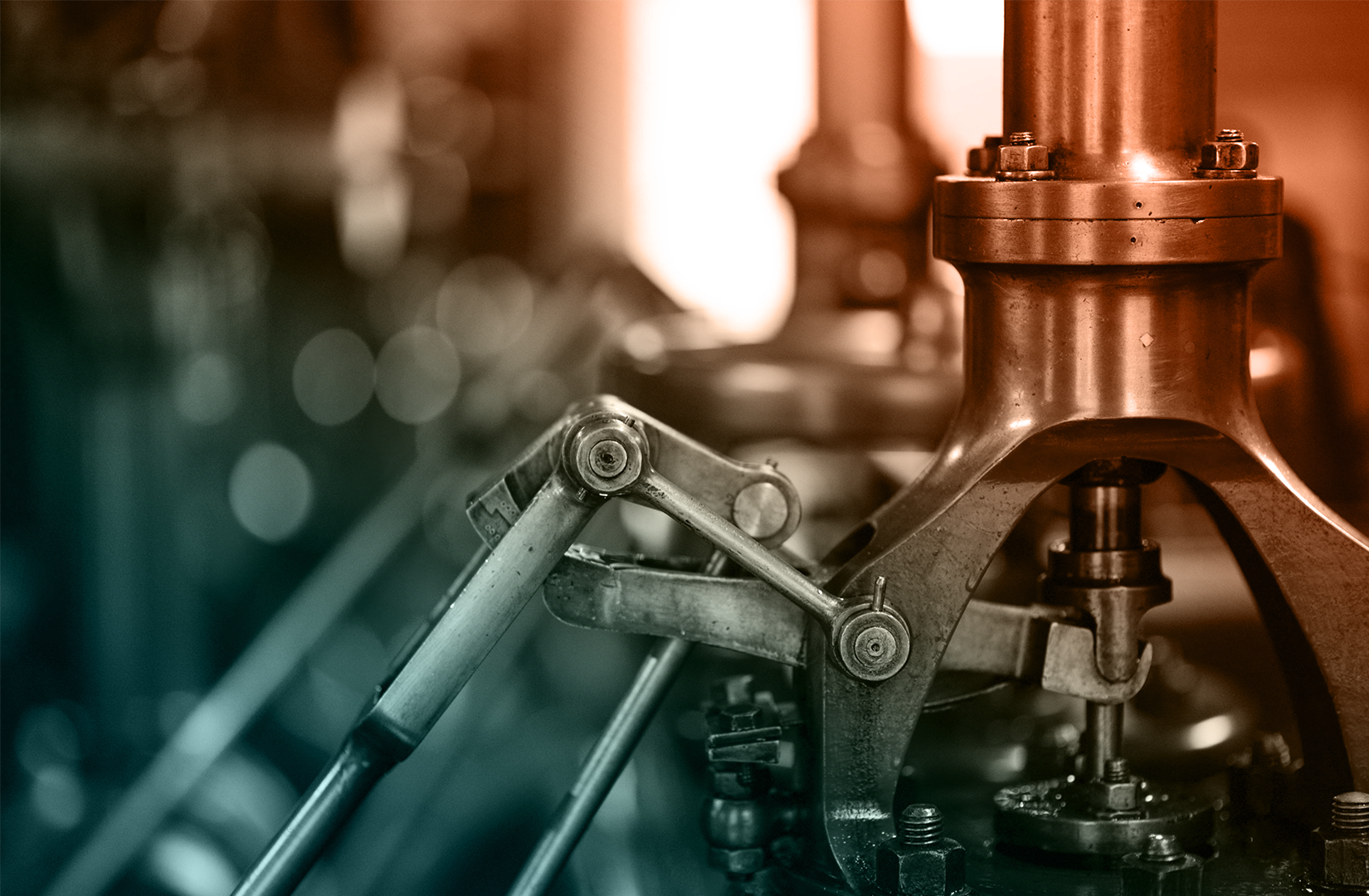
Common Materials Used in Cap Seals
Cap seals are typically made from a combination of materials to provide optimal performance in dynamic applications:
- PTFE (Polytetrafluoroethylene): The plastic cap is often made from PTFE, which offers excellent low-friction properties, high-temperature resistance, and chemical compatibility. This ensures smooth operation and minimizes wear. The cap can be filled with carbon, brass, bronze, or other materials to increase durability.
- Polyurethane (PU): Polyurethane caps provide excellent abrasion resistance and flexibility, making them suitable for applications where the seal is exposed to high pressures and dynamic movements.
- Nitrile (NBR) O-Rings: Nitrile O-rings offer good oil resistance, flexibility, and durability, making them ideal for hydraulic applications. They provide the elasticity needed to maintain a tight seal in dynamic applications.
- Viton® (FKM) O-Rings: For applications requiring high-temperature and chemical resistance, Viton O-rings are used. They provide excellent sealing performance in environments exposed to aggressive chemicals or elevated temperatures.
- EPDM O-Rings: EPDM O-rings are suitable for water-based hydraulic fluids and applications requiring resistance to heat, steam, and weathering, making them ideal for certain industrial environments.
Canyon Components strives to meet all customer service requests. Feel free to contact Canyon Components engineering and let our knowledgeable staff help you design the perfect part for your needs.
Cap Seal Materials
CanRez™ FFKM Perfluoroelastomer
Extreme temperatures & chemicals require extreme solutions! CanRez™ FFKM O-rings with cap seals offer extreme reliability where you need it most! Thousands of sizes in stock now!
CanGuard™ RFI & EMI Shielding Materials
CanGuard™ O-rings with cap seals have been developed to offer superior sealing solutions with enhanced electromagnetic interference (EMI) shielding and radio frequency interference (RFI) shielding.
Kalrez® FFKM Perfluoroelastomer
Canyon Components offers Kalrez® Perfluoroelastomer (FFKM) O-rings with cap seals, O-rings, gaskets, & custom molded parts at competitive prices and with great lead-times.
Parker® O-rings with cap seals, O-rings, Parofluor parts, parker FKM Viton
Canyon Components offers Parker Hannifin® O-rings with cap seals, O-rings, Gaskets, Perfluoroelastomer (FFKM) parts, & custom molded parts at competitive prices and with great lead-times.
FKM (Viton®, Fluorocarbon)
FKM O-rings with cap seals, compounds, O-rings, gaskets, & custom molded parts exhibit excellent mechanical attributes as well as excellent resistance to high temperatures, mineral oil, ozone, fuels, hydraulic fluids, and many other solvents and chemicals.
Aflas® (TFE/P)
TFE/P (Aflas) O-rings with cap seals, compounds, O-rings, gaskets, & custom molded parts gives high resistance to steam, hot water, atmospheric wear, and many chemicals. TFE/P compounds provide superior performance in water, steam and virtually all caustic chemicals.
Fluorosilicone (FVMQ)
The mechanical and physical properties of Fluorosilicone O-rings with cap seals, O-rings, gaskets, & custom molded parts are very similar to silicone. Fluorosilicone O-rings, gaskets, & custom molded parts offer improved flexibility and strength, better resistance to fuels and mineral oil, but reduced hot air resistance.
Silicone (VMQ, PVMQ)
Silicone O-rings with cap seals, seals, O-rings, gaskets, & custom molded parts are excellent for extreme temperatures in static applications. Canyon Components carries a range of silicone materials, and we are happy to custom tailor a seal to meet your application requirements!
EPDM (Ethylene Propylene)
EPDM O-rings with cap seals, materials, O-rings, gaskets, & custom molded parts can operate over a wide temperature range, and are compatible with glycol fluids that cause problems for most typical elastomeric seals.
NBR (Nitrile, Buna-N)
Nitrile O-rings with cap seals, O-rings, gaskets, & custom molded parts are very oil-resistant, have strong mechanical properties, are resistant to wear, and are relatively inexpensive. These properties make Nitrile the most commonly used general purpose O-ring, gasket, & custom molded part material.
HNBR (Hydrogenated Nitrile)
Hydrogenated Nitrile O-rings with cap seals, O-rings, gaskets, & custom molded parts offer higher strength and reduced degradation at high temperatures compared to conventional Nitrile materials. These properties make HNBR materials popular in the oil and gas industry, as well as many applications in the chemical industry.
XNBR (Carboxylated Nitrile)
XNBR O-rings with cap seals, O-rings, gaskets, & custom molded parts are similar to Nitrile, but the backbone has been chemically modified with a Carboxylic Acid group. The resulting elastomer is a Nitrile rubber with outstanding abrasion and chemical resistance, superior to that of traditional Nitrile.
Neoprene (CR)
Chloroprene was the first synthetic rubber, and was developed commercially under the name Neoprene®. Chloroprene O-rings with cap seals, rubbers, O-rings, gaskets, & custom molded parts contain Chlorine in the polymer to reduce the reactivity to many oxidizing agents, as well as to oil and flame.
Polyurethane (PU, AU)
Polyurethane O-rings with cap seals, O-rings, gaskets, & custom molded parts generally have two or three times greater tensile strength and wear resistance than Nitrile and comparable polymers. Polyurethane also provides excellent permeation resistance when compared to most rubbers.
PTFE (Teflon)
The harshest environments require specialized solutions. Often times, a Canyon Components PTFE cap seals are used in harsh chemical environments. Polytetrafluoroethylene, commonly known as PTFE or Teflon®, is a high-performance fluoropolymer known for its exceptional chemical resistance, low friction, and non-stick properties.
Product Types
Custom Parts
Here at Canyon Components, we make sure to offer our customers any manufacturing technique they desire. Whether your O-rings, gaskets, & custom molded parts be rubber, plastic, or metal, rest assured that Canyon Components can make it!
Gaskets & Custom Cutting
Whether your custom cut parts be rubber, plastic, sponge, composite, or metal, rest assured that Canyon Components can make it! Canyon Components strives to meet all customer service requests. If you need something that isn't listed, feel free to contact a Canyon Components product and application consultant.
Infinite "Giant" Diameter O-Rings
By either Continuous Molding O-rings, or Splice & Vulcanizing O-rings, Canyon can provide mold-less, infinitely large O-rings at competitive prices!
Specialty Compliances
Canyon have materials available for O-rings, gaskets, & custom parts with compliances ranging from USP Class VI <87> & <88> for medical applications, to FDA CFR 21.177.2600 grades A through F for different food types, to the various drinking water specifications like KTW and NSF. Whether it's metal, rubber, or plastic, Canyon can meet your needs!
Cap Seals Pros & Cons
Cap seals for rod and piston applications provide an effective and reliable sealing solution for dynamic environments, offering exceptional extrusion resistance, low friction, and compatibility with various fluids and temperatures. Their use in machine tools, injection molding machines, and presses highlights their suitability for high-pressure, high-speed applications where durability and performance are critical. While they may have some limitations in terms of cost and installation complexity, the benefits of cap seals make them an essential choice for ensuring leak-free, efficient operation in demanding industrial settings. Understanding the features, applications, and material options will help you select the right cap seal for your specific needs.
Canyon Components strives to meet all customer service requests. Feel free to contact Canyon Components engineering and let our knowledgeable staff help you design the perfect part for your needs.
Pros of Cap Seals for Rod and Piston Applications
Cap seals offer numerous advantages that make them suitable for high-performance dynamic applications:
- Exceptional Extrusion Resistance: The plastic cap provides high resistance to extrusion, ensuring the seal remains intact even under extreme pressures, which is crucial for applications involving heavy loads or high pressure.
- Low Friction and Wear: The low-friction properties of the plastic cap reduce wear on the seal and mating surfaces, resulting in longer service life and improved efficiency in dynamic applications.
- Wide Range of Material Compatibility: Cap seals can be tailored with different O-ring and cap materials to suit various fluids, temperatures, and pressure conditions, making them versatile for multiple applications.
- High-Speed Operation: Cap seals maintain sealing integrity in high-speed, reciprocating movements, making them ideal for use in machinery that requires rapid motion.
- Reliable Sealing in Dynamic Applications: The combination of an O-ring and cap ensures effective sealing, even in applications with frequent pressure changes, ensuring leak-free performance.
Cons of Cap Seals for Rod and Piston Applications
While cap seals provide many benefits, there are some potential drawbacks:
- Higher Cost: Cap seals can be more expensive than traditional O-rings or simple seals due to their advanced design and material composition, which may increase overall costs in some applications.
- Complex Installation: The installation process for cap seals may be more complex than standard seals, requiring careful handling to avoid damage, particularly to the plastic cap.
- Limited Availability in Certain Sizes: Cap seals may not be as widely available in all sizes or configurations, which can limit their use in specific applications or require custom manufacturing.
Back to Products Hub
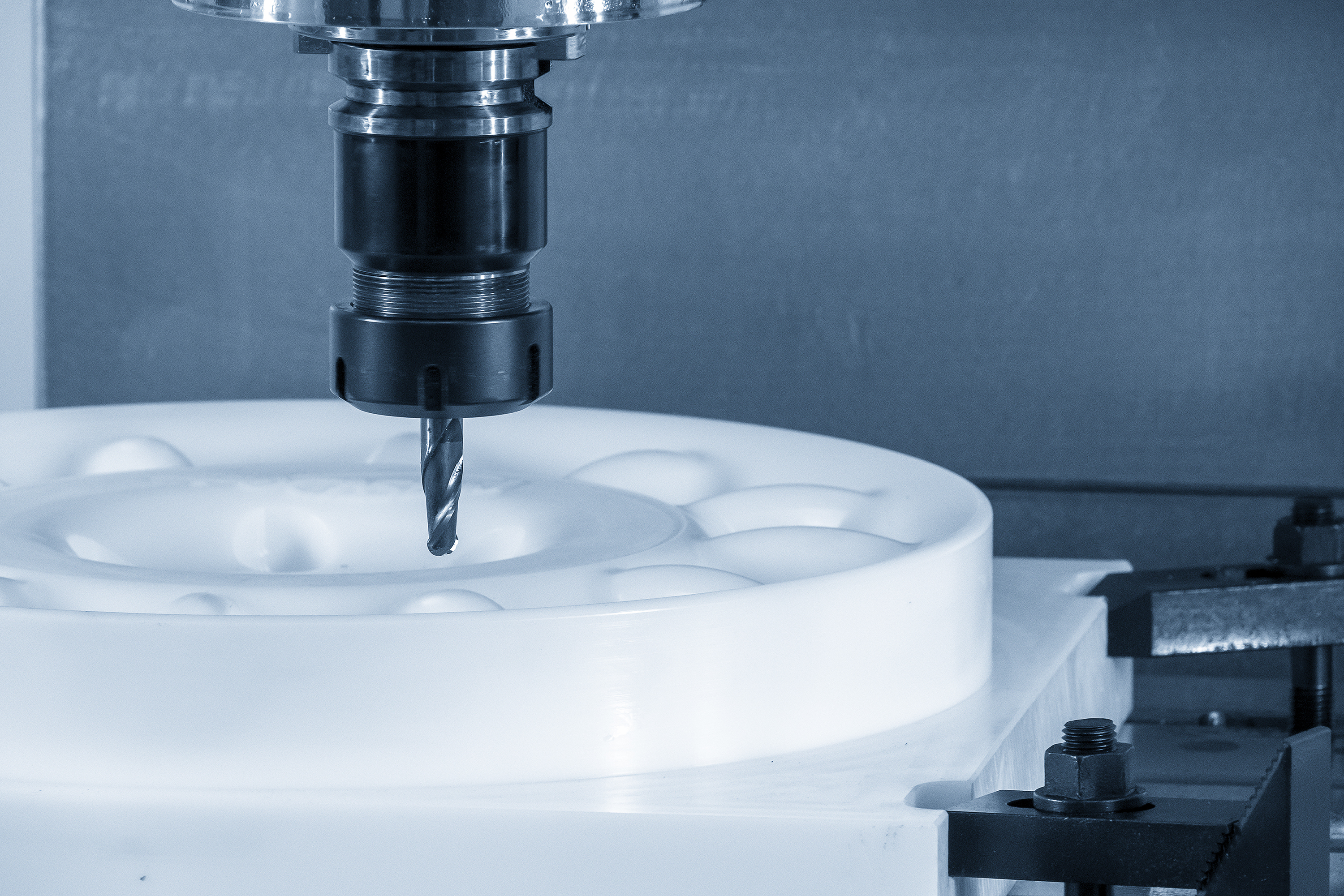
Get A Quote Now!
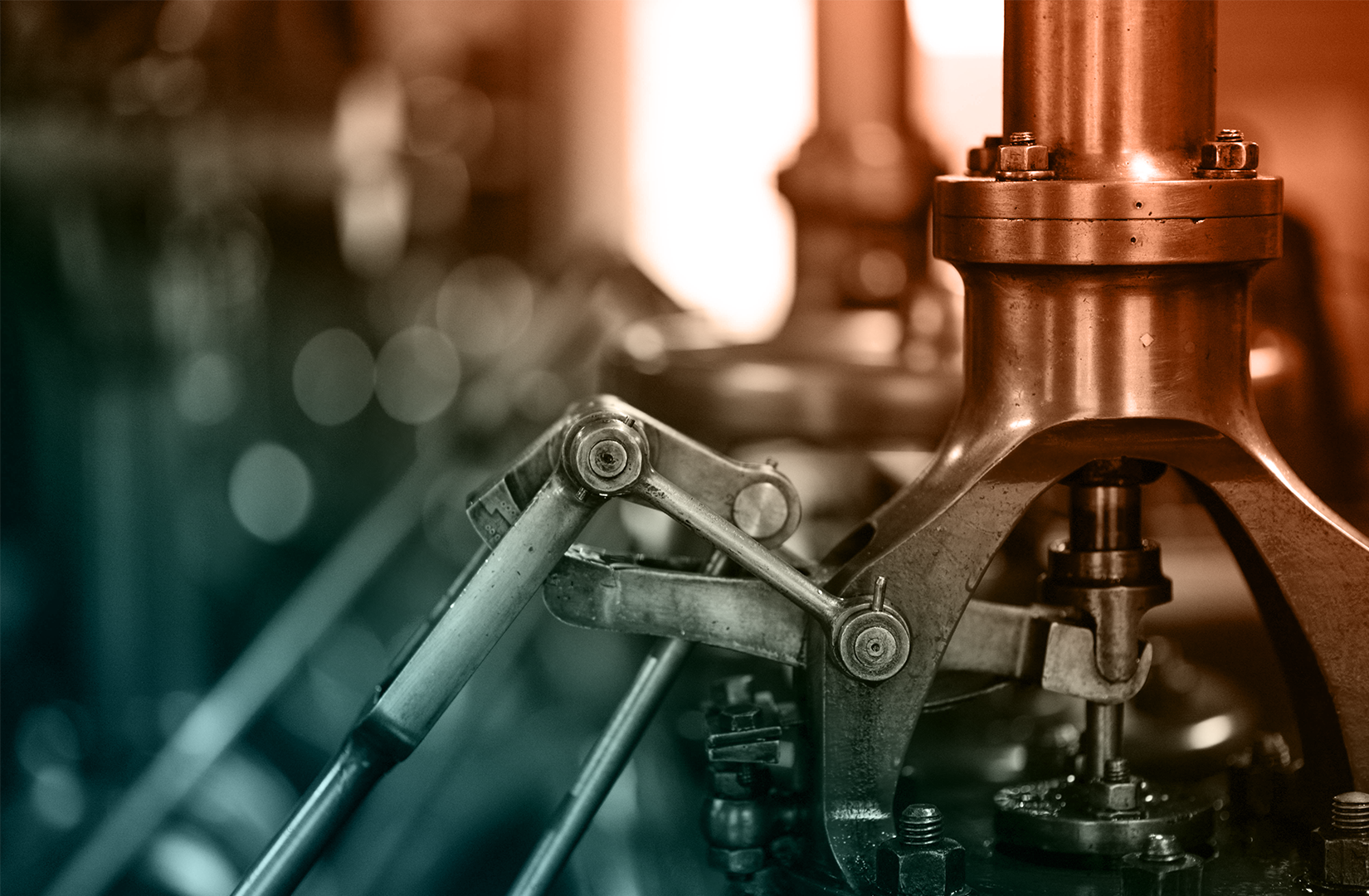