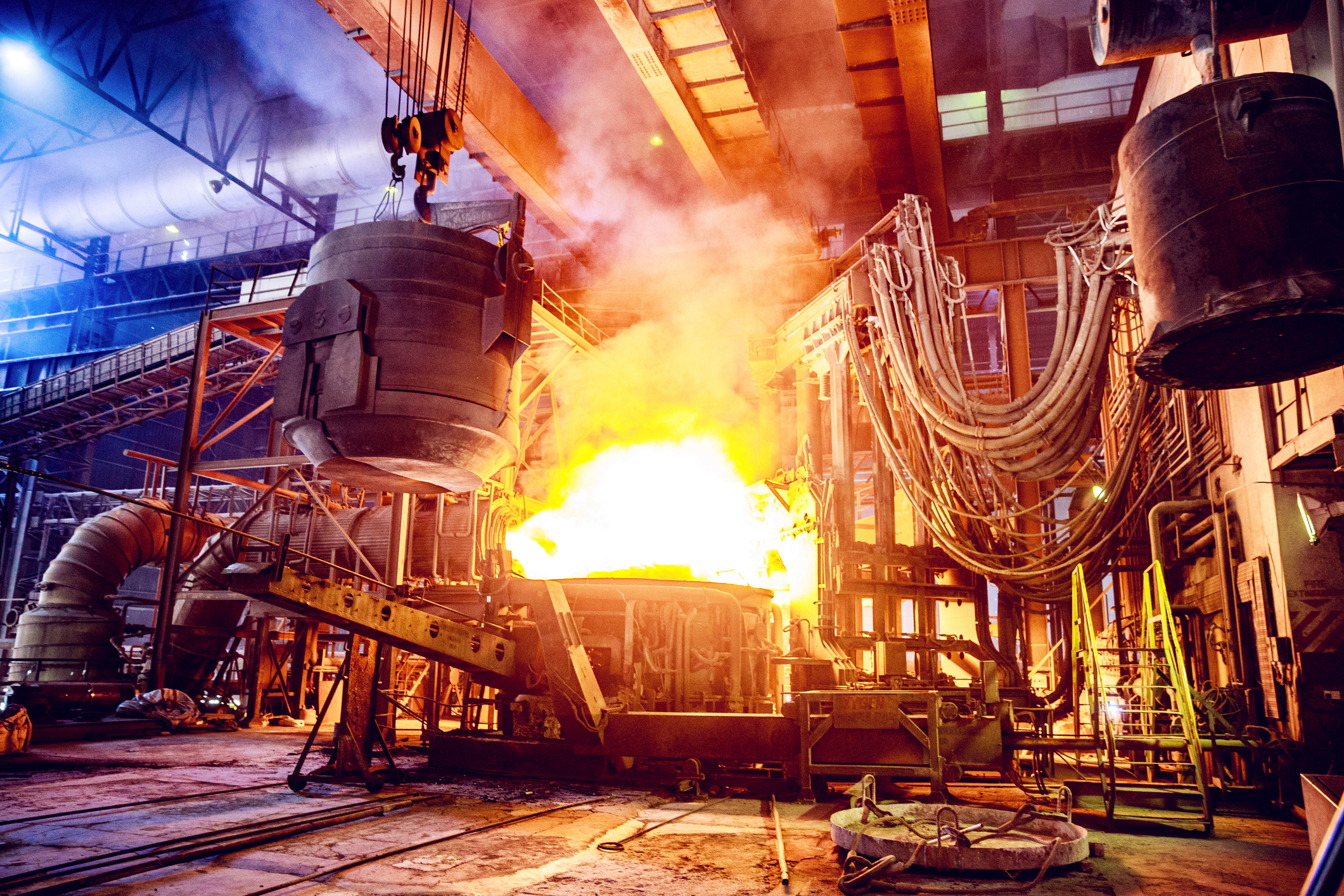
Diaphragms: Features, Applications, and Material Options
Elastomer diaphragms are flexible sealing components used in a variety of applications where precise control of fluids and gases is required. Made from rubber-like materials, these diaphragms provide reliable sealing and are essential in industries ranging from automotive to semiconductor manufacturing. This guide explores the features, common applications, pros and cons, and the specific role of diaphragms in the semiconductor manufacturing industry.
Silicone, Fluorosilicone, Viton, CanRez® FFKM and Kalrez® diaphragms, O-rings, micro gasket rapid manufacturing, & custom molded parts are available now!
Check with one of Canyon’s helpful product engineers for an expert material and manufacturing recommendation.
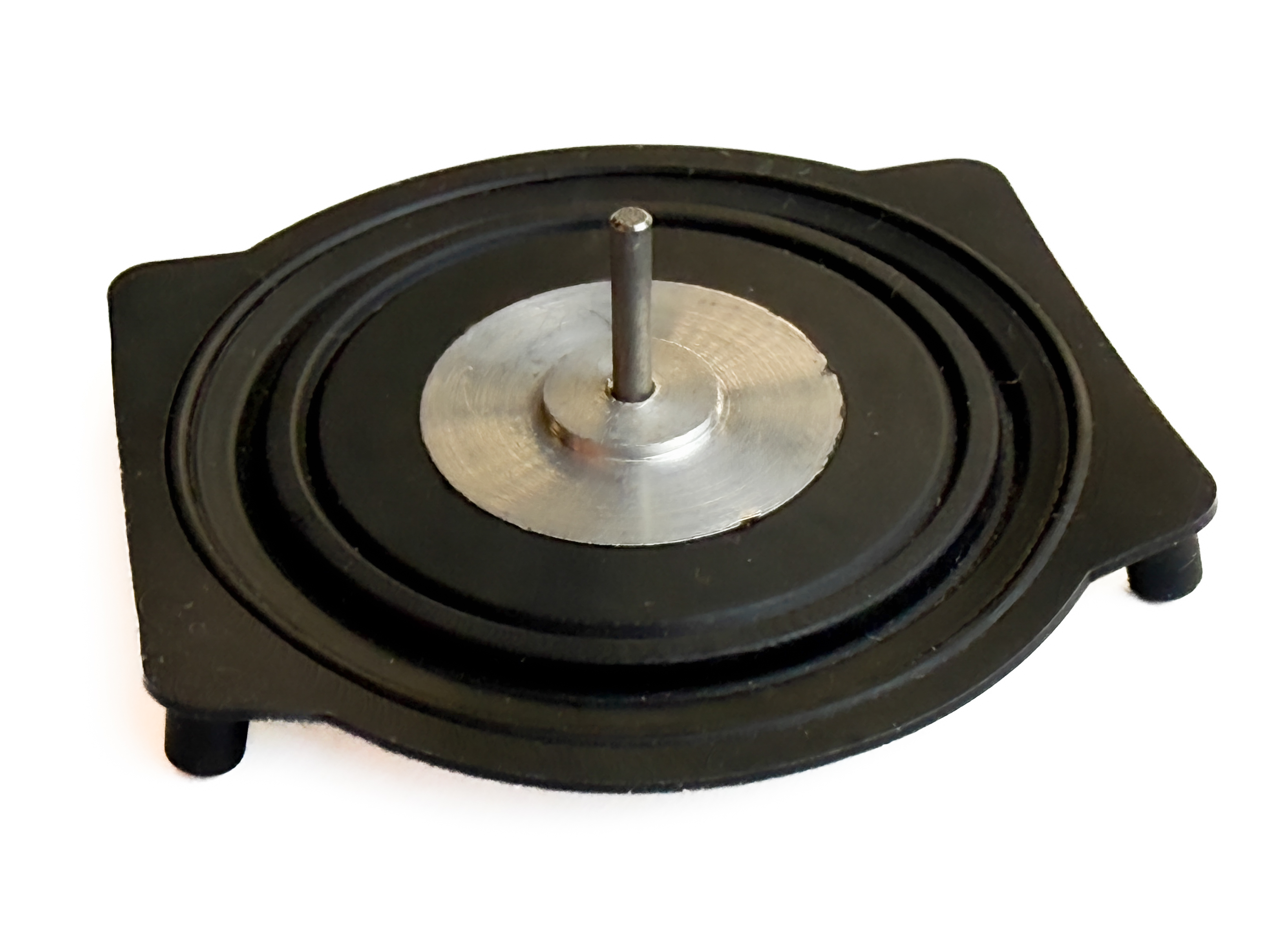
Features of Elastomer Diaphragms
Elastomer diaphragms offer several key features that make them an excellent choice for various sealing and control applications:
- Flexibility: Elastomer diaphragms are highly flexible, allowing them to respond to pressure changes and maintain a reliable seal in dynamic applications.
- Chemical Resistance: Depending on the material, elastomer diaphragms can resist a wide range of chemicals, making them suitable for aggressive environments.
- Temperature Range: Elastomer diaphragms can be engineered to withstand extreme temperatures, from low to high, ensuring reliable performance in various conditions.
- Low Permeability: These diaphragms are designed to have low permeability, preventing the passage of gases and liquids through the material.
- Durability: Elastomer diaphragms are built to withstand repeated cycles of movement, pressure, and environmental exposure, offering long service life in demanding applications.
Common Applications of Elastomer Diaphragms
Elastomer diaphragms are used in a wide range of industries due to their versatility and reliability. Common applications include:
- Pumps and Valves: Elastomer diaphragms are commonly used in diaphragm pumps and control valves to regulate fluid flow and pressure.
- Automotive: In automotive systems, elastomer diaphragms are used in fuel systems, braking systems, and emissions control devices to ensure precise control and sealing.
- Medical Devices: Elastomer diaphragms are found in medical equipment such as ventilators, blood pressure monitors, and fluid delivery systems, where they provide accurate control and sealing.
- Industrial Machinery: Elastomer diaphragms are used in compressors, actuators, and other machinery to control the flow of gases and liquids under varying pressure conditions.
- Aerospace: In aerospace applications, elastomer diaphragms are used in fuel control systems, environmental control systems, and hydraulic systems, where reliability and precision are critical.
Please consult a Canyon Components Engineer about your specific application and we will use our decades of experience to formulate a solution that fits your need.
Get a Quote Now!
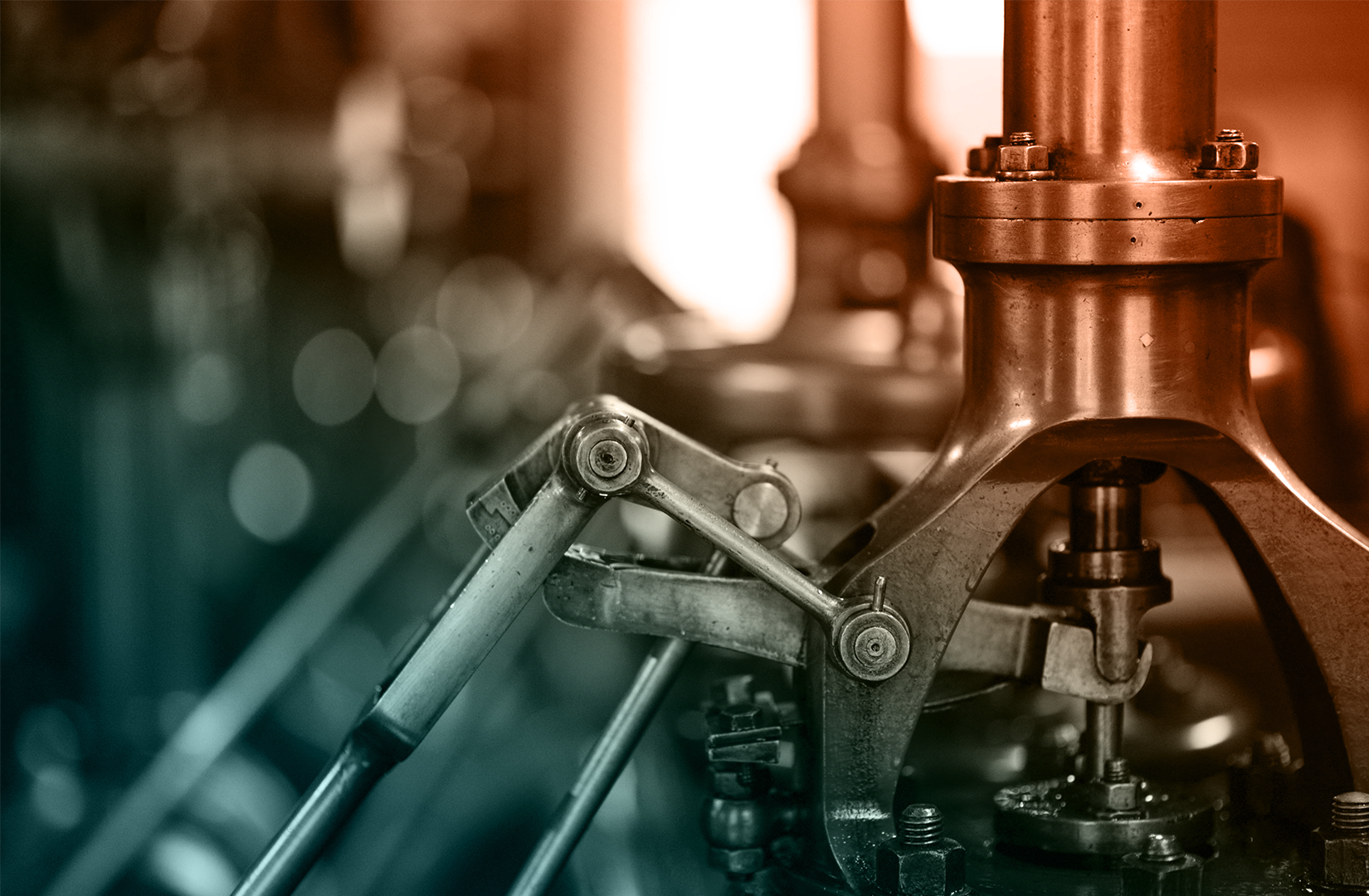
Elastomer Diaphragm Materials
CanRez® FFKM Perfluoroelastomer
Extreme temperatures & chemicals require extreme solutions! CanRez® FFKM diaphragms and materials offer extreme reliability where you need it most! Thousands of sizes in stock now!
CanGuard™ RFI & EMI Shielding Materials
CanGuard™ materials have been developed to offer superior sealing solutions with enhanced electromagnetic interference (EMI) shielding and radio frequency interference (RFI) shielding in a diaphragm format.
Kalrez® FFKM Perfluoroelastomer
Canyon Components offers Kalrez® Perfluoroelastomer (FFKM) diaphragms, gaskets, & custom molded parts at competitive prices and with great lead-times.
Parker® O-rings, Parofluor parts, parker FKM Viton
Canyon Components offers Parker Hannifin® diaphragms, Gaskets, Perfluoroelastomer (FFKM) parts, & custom molded parts at competitive prices and with great lead-times.
Silicone (VMQ, PVMQ)
Silicone diaphragms, seals, micro O-rings, gaskets, & custom molded parts are excellent for extreme temperatures in static applications. Canyon Components carries a range of silicone materials, and we are happy to custom tailor a seal to meet your application requirements!
Fluorosilicone (FVMQ)
The mechanical and physical properties of Fluorosilicone diaphragms, gaskets, & custom molded parts are very similar to silicone. Fluorosilicone O-rings, gaskets, & custom molded parts offer improved flexibility and strength, better resistance to fuels and mineral oil, but reduced hot air resistance.
FKM (Viton®, Fluorocarbon)
FKM compounds, diaphragms, & custom molded parts exhibit excellent mechanical attributes as well as excellent resistance to high temperatures, mineral oil, ozone, fuels, hydraulic fluids, and many other solvents and chemicals.
Aflas® (TFE/P)
TFE/P (Aflas) diaphragms, compounds, micro O-rings, gaskets, & custom molded parts gives high resistance to steam, hot water, atmospheric wear, and many chemicals. TFE/P compounds provide superior performance in water, steam and virtually all caustic chemicals.
EPDM (Ethylene Propylene)
EPDM diaphragms, materials, micro O-rings, gaskets, & custom molded parts can operate over a wide temperature range, and are compatible with glycol fluids that cause problems for most typical elastomeric seals.
NBR (Nitrile, Buna-N)
Nitrile diaphragms, micro O-rings, gaskets, & custom molded parts are very oil-resistant, have strong mechanical properties, are resistant to wear, and are relatively inexpensive. These properties make Nitrile the most commonly used general purpose O-ring, gasket, & custom molded part material.
HNBR (Hydrogenated Nitrile)
Hydrogenated Nitrile diaphragms, micro O-rings, gaskets, & custom molded parts offer higher strength and reduced degradation at high temperatures compared to conventional Nitrile materials. These properties make HNBR materials popular in the oil and gas industry, as well as many applications in the chemical industry.
XNBR (Carboxylated Nitrile)
XNBR diaphragms, micro O-rings, gaskets, & custom molded parts are similar to Nitrile, but the backbone has been chemically modified with a Carboxylic Acid group. The resulting elastomer is a Nitrile rubber with outstanding abrasion and chemical resistance, superior to that of traditional Nitrile.
Neoprene (CR)
Chloroprene was the first synthetic rubber, and was developed commercially under the name Neoprene®. Chloroprene diaphragms, rubbers, micro O-rings, gaskets, & custom molded parts contain Chlorine in the polymer to reduce the reactivity to many oxidizing agents, as well as to oil and flame.
Polyurethane (PU, AU)
Polyurethane diaphragms, micro O-rings, gaskets, & custom molded parts generally have two or three times greater tensile strength and wear resistance than Nitrile and comparable polymers. Polyurethane also provides excellent permeation resistance when compared to most rubbers.
PTFE (Teflon)
The harshest environments require specialized solutions. Often times, a Canyon Components PTFE diaphragms are used in harsh chemical environments. Polytetrafluoroethylene, commonly known as PTFE or Teflon®, is a high-performance fluoropolymer known for its exceptional chemical resistance, low friction, and non-stick properties.
Product Types
Custom Parts
Here at Canyon Components, we make sure to offer our customers any manufacturing technique they desire. Whether your micro O-rings, gaskets, & custom molded parts be rubber, plastic, or metal, rest assured that Canyon Components can make it!
Gaskets & Custom Cutting
Whether your custom cut parts be rubber, plastic, sponge, composite, or metal, rest assured that Canyon Components can make it! Canyon Components strives to meet all customer service requests. If you need something that isn't listed, feel free to contact a Canyon Components product and application consultant.
Specialty Compliances
Canyon have materials available for micro O-rings, gaskets, & custom parts with compliances ranging from USP Class VI <87> & <88> for medical applications, to FDA CFR 21.177.2600 grades A through F for different food types, to the various drinking water specifications like KTW and NSF. Whether it's metal, rubber, or plastic, Canyon can meet your needs!
Please consult a Canyon Components Engineer about your specific application and we will use our decades of experience to formulate a solution that fits your need.
Elastomer Diaphragms in the Semiconductor Manufacturing Industry
In the semiconductor manufacturing industry, elastomer diaphragms play a vital role in maintaining the precision and cleanliness required for producing advanced microchips and electronic components. Key uses include:
- Chemical Delivery Systems: Elastomer diaphragms are used in pumps and valves that control the delivery of ultra-pure chemicals to semiconductor manufacturing equipment. Their chemical resistance and low permeability help ensure the purity of the chemicals used in the production process.
- Vacuum Systems: Diaphragms are employed in vacuum systems that handle delicate wafer processing, where maintaining a contaminant-free environment is crucial.
- Pressure Regulation: Elastomer diaphragms help regulate pressure in critical processes, ensuring consistent flow rates and preventing contamination in the semiconductor manufacturing process.
- Cleanroom Compatibility: Elastomer diaphragms designed for semiconductor applications are often made from materials that meet strict cleanroom standards, ensuring they do not introduce particulates or contaminants into the manufacturing environment.
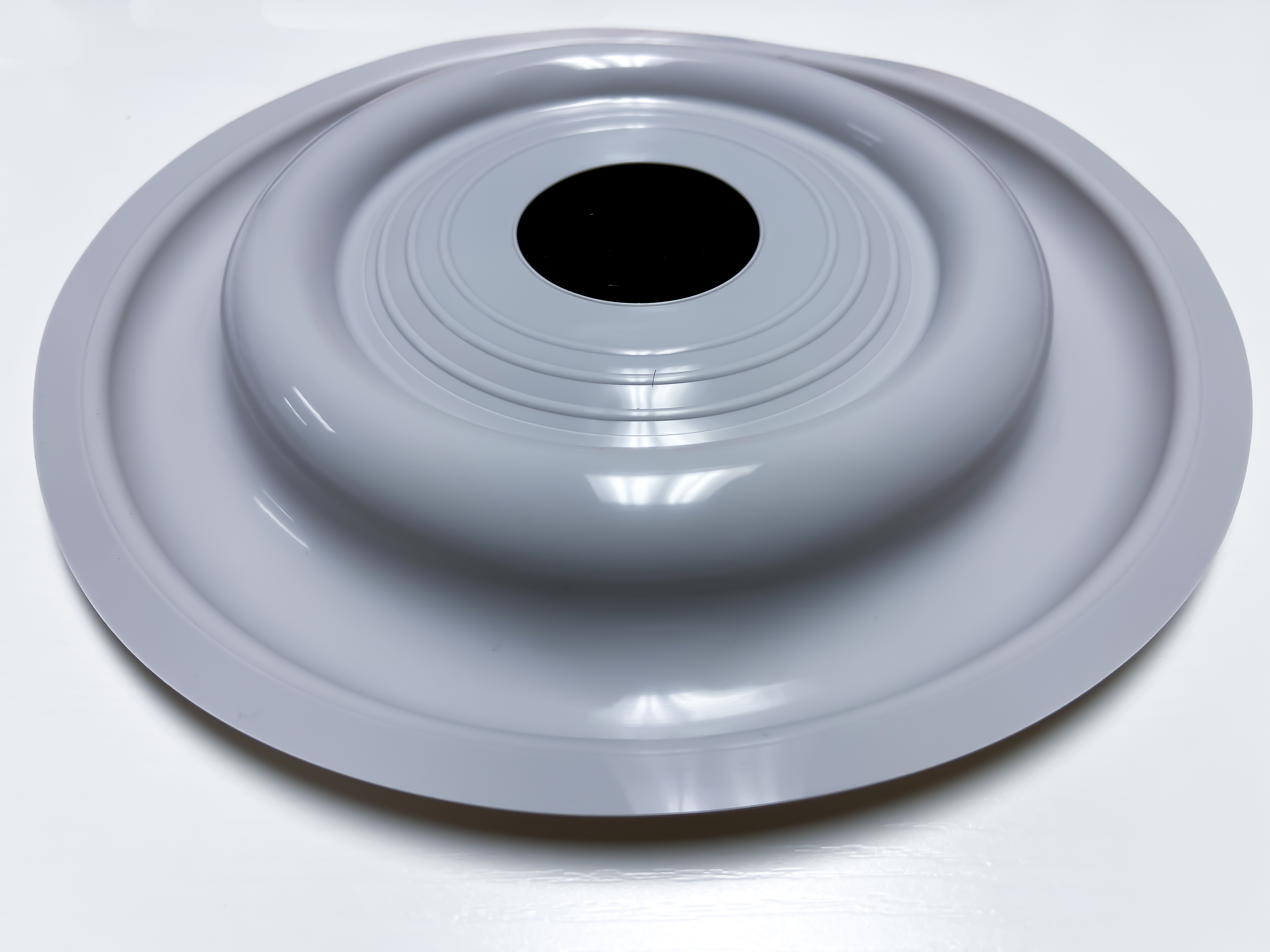
Elastomer Diaphragms Pros & Cons
Elastomer diaphragms are essential components in a wide range of industries, offering reliable sealing and precise control in dynamic applications. Their versatility, cost-effectiveness, and durability make them a popular choice for everything from automotive systems to semiconductor manufacturing. However, potential limitations in temperature resistance and material longevity should be considered when selecting elastomer diaphragms for specific applications. Understanding the features, applications, and potential drawbacks of elastomer diaphragms will help you make informed decisions to ensure optimal performance in your systems.
Canyon Components strives to meet all customer service requests. Feel free to contact Canyon Components engineering and let our knowledgeable staff help you design the perfect part for your needs.
Pros of Elastomer Diaphragms
Elastomer diaphragms offer several advantages that make them a preferred choice in many applications:
- Versatility: With a wide range of materials available, elastomer diaphragms can be tailored to meet specific chemical, temperature, and pressure requirements.
- Cost-Effective: Elastomer diaphragms are generally more affordable than metal or composite alternatives, making them a cost-effective solution for many applications.
- Precision: Elastomer diaphragms provide accurate control over fluid and gas flow, making them ideal for applications that require precise regulation.
- Durability: Built to withstand repeated use and harsh environments, elastomer diaphragms offer a long service life in demanding applications.
Cons of Elastomer Diaphragms
While elastomer diaphragms offer many benefits, there are also some potential drawbacks to consider:
- Limited Temperature Range: Although elastomer diaphragms can be engineered to withstand various temperatures, they may not be suitable for extremely high-temperature applications where metal or composite diaphragms would be more appropriate.
- Permeability: While elastomer diaphragms are designed to have low permeability, they may still allow some gases or liquids to pass through over time, which could be a concern in ultra-sensitive applications.
- Material Degradation: Depending on the environment and chemicals involved, elastomer diaphragms may degrade over time, leading to reduced performance or the need for replacement.
Back to Products Hub
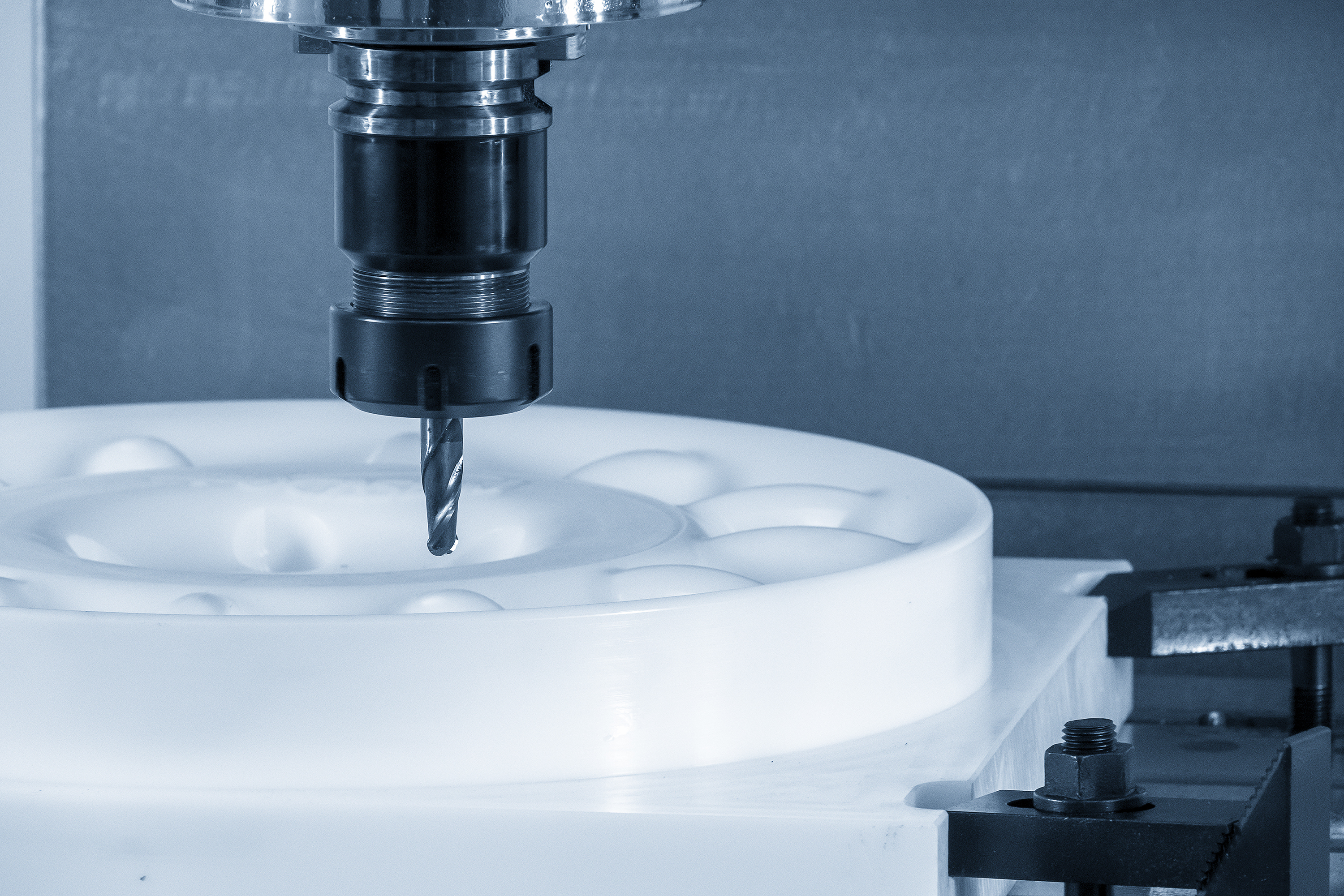
Get A Quote Now!
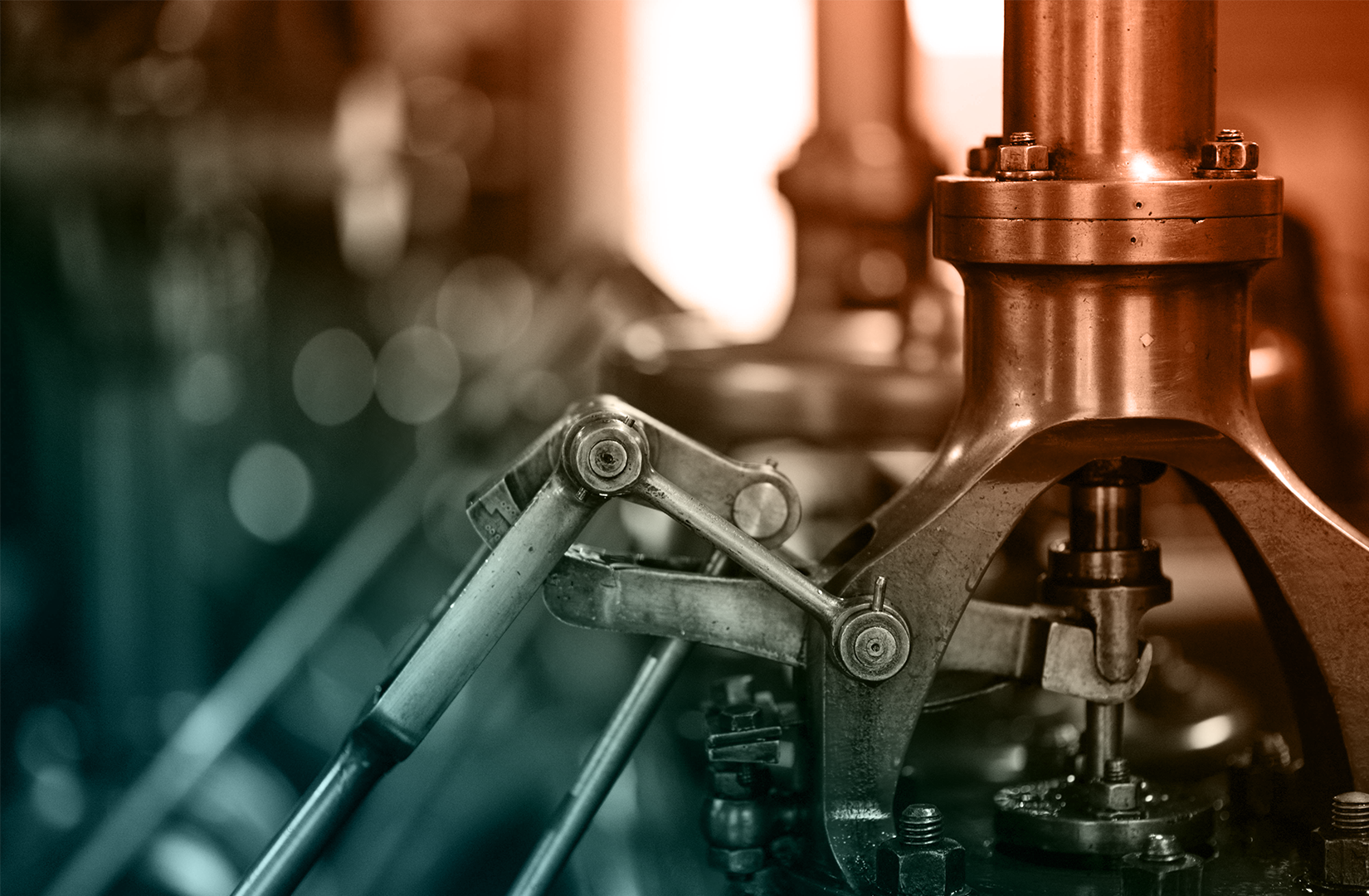