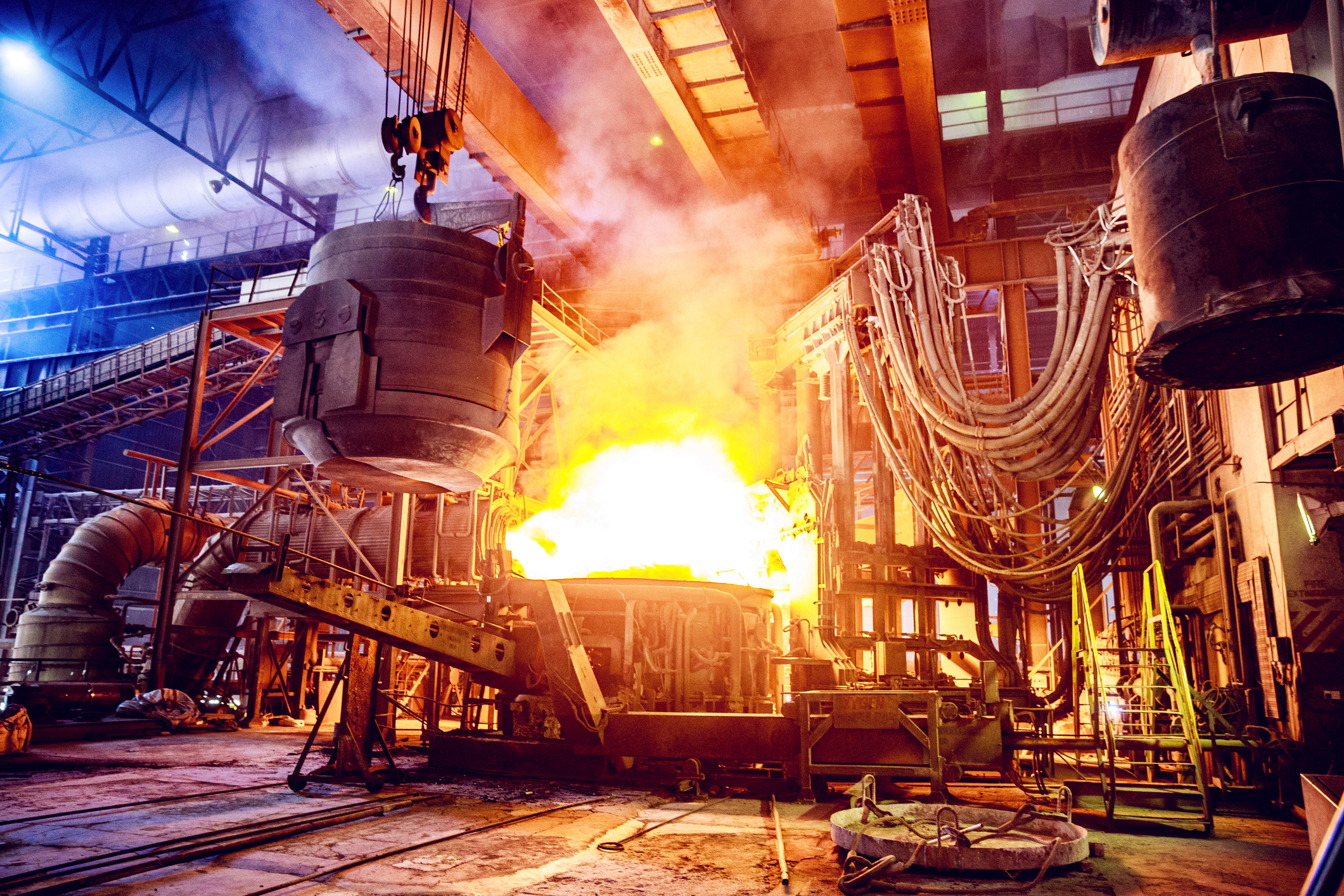
Packer Element Seals
Packer element seals are critical components used in the oil and gas industry to isolate zones in wellbores, ensuring effective sealing during drilling, completion, and production operations. These seals, located within packer tools, are designed to withstand high pressure, extreme temperatures, and exposure to aggressive downhole fluids. Packer element seals play a vital role in maintaining well integrity and ensuring the safe and efficient extraction of hydrocarbons from subsurface reservoirs.
CanRez® FFKM and Kalrez® packer element seals, grommets, O-rings, gasket rapid manufacturing, & custom molded parts are available now!
Check with one of Canyon’s helpful product engineers for an expert material and manufacturing recommendation.
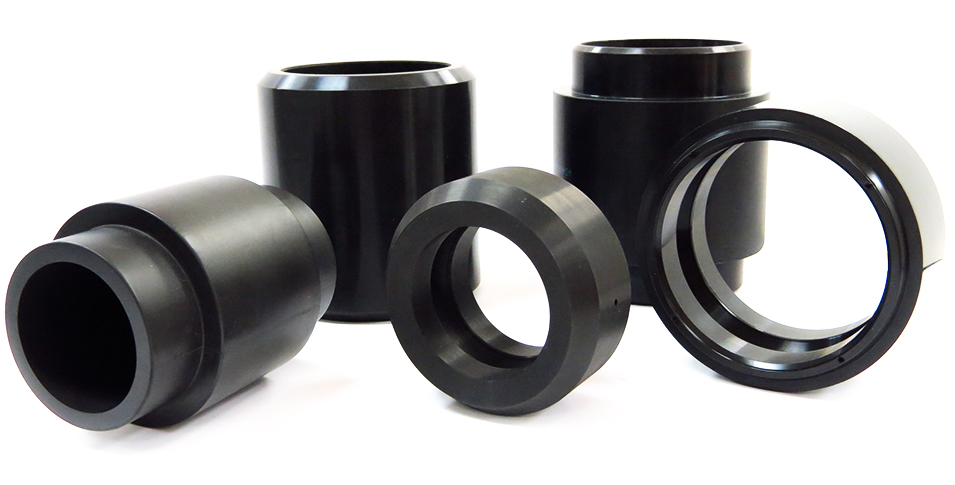
Features of Packer Element Seals
Packer element seals are designed to perform reliably under harsh wellbore conditions. Key features include:
- High Pressure Resistance: Depending on the material, packer seals are engineered to maintain their sealing integrity in environments with extreme pressures, ensuring reliable performance during downhole operations. If explosive decompression resistance and H2S sour gas resistance is needed, materials with NORSOK M-710, API and ISO 23936 certifications can be used.
- Temperature Tolerance: Depending on the material, these seals are capable of withstanding extreme temperature variations, from sub-zero temperatures in deepwater operations to high temperatures encountered in geothermal or deep wells, often ranging up to 350°F (175°C) or more.
- Chemical Resistance: Packer element seals are made from advanced elastomer compounds that provide resistance to harsh chemicals, gases, and fluids, including hydrocarbons, hydrogen sulfide (H₂S), and drilling muds.
- Elongation and Flexibility: The flexible nature of packer seals allows them to expand and contract as needed to form a reliable seal against the wellbore or casing, accommodating changes in pressure and fluid volumes.
- Abrasion Resistance: Packer seals are resistant to abrasion, ensuring long-lasting performance in environments where the seal is exposed to particulate matter or rough surfaces within the wellbore.
Common Applications of Packer Element Seals
Packer element seals are essential in various wellbore operations across the oil and gas industry. Their common applications include:
- Well Isolation: Packer seals are used to isolate different zones within a well, allowing operators to control fluid flow, pressure, and production from multiple reservoir zones.
- Zonal Isolation in Completions: During the well completion phase, packer element seals are employed to isolate sections of the wellbore for optimal production and to prevent cross-contamination between production zones.
- Hydraulic Fracturing: In hydraulic fracturing operations, packer element seals help contain the high-pressure fluids used to fracture rock formations and increase hydrocarbon recovery.
- Well Testing: Packer element seals are critical in well testing operations, where temporary seals are required to test pressure and fluid flow from different sections of the well.
- Enhanced Oil Recovery (EOR): In EOR methods like steam injection or gas injection, packer seals help isolate zones to ensure that injected fluids are confined to specific reservoir sections, improving recovery rates.
Please consult a Canyon Components Engineer about your specific application and we will use our decades of experience to formulate a solution that fits your need.
Get a Quote Now!
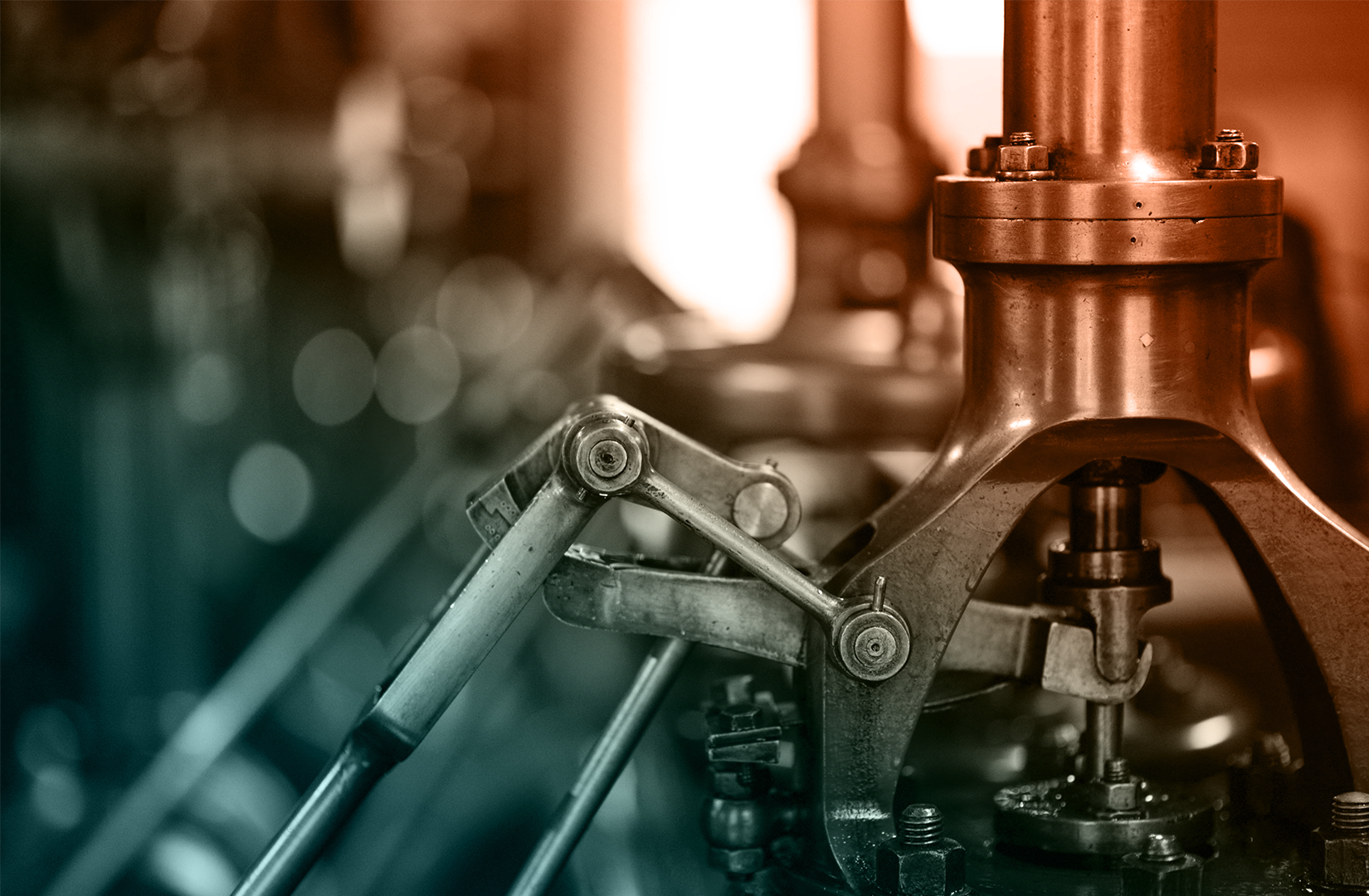
Packer Element Materials
CanRez™ FFKM Perfluoroelastomer
Extreme temperatures & chemicals require extreme solutions! CanRez™ FFKM packer element seal materials offer extreme reliability where you need it most! Thousands of sizes in stock now!
Kalrez® FFKM Perfluoroelastomer
Canyon Components offers Kalrez® Perfluoroelastomer (FFKM) packer element seals, O-rings, gaskets, & custom molded parts at competitive prices and with great lead-times.
Parker® Packer Element Seals, O-rings, Parofluor parts, parker FKM Viton
Canyon Components offers Parker Hannifin® packer element seals, O-rings, Gaskets, Perfluoroelastomer (FFKM) parts, & custom molded parts at competitive prices and with great lead-times.
FKM (Viton®, Fluorocarbon)
FKM packer element seals, compounds, O-rings, gaskets, & custom molded parts exhibit excellent mechanical attributes as well as excellent resistance to high temperatures, mineral oil, ozone, fuels, hydraulic fluids, and many other solvents and chemicals.
Aflas® (TFE/P)
TFE/P (Aflas) packer element seals, compounds, O-rings, gaskets, & custom molded parts gives high resistance to steam, hot water, atmospheric wear, and many chemicals. TFE/P compounds provide superior performance in water, steam and virtually all caustic chemicals.
EPDM (Ethylene Propylene)
EPDM packer element seals, materials, O-rings, gaskets, & custom molded parts can operate over a wide temperature range, and are compatible with glycol fluids that cause problems for most typical elastomeric seals.
NBR (Nitrile, Buna-N)
Nitrile packer element seals, O-rings, gaskets, & custom molded parts are very oil-resistant, have strong mechanical properties, are resistant to wear, and are relatively inexpensive. These properties make Nitrile the most commonly used general purpose O-ring, gasket, & custom molded part material.
HNBR (Hydrogenated Nitrile)
Hydrogenated Nitrile packer element seals, O-rings, gaskets, & custom molded parts offer higher strength and reduced degradation at high temperatures compared to conventional Nitrile materials. These properties make HNBR materials popular in the oil and gas industry, as well as many applications in the chemical industry.
XNBR (Carboxylated Nitrile)
XNBR packer element seals, O-rings, gaskets, & custom molded parts are similar to Nitrile, but the backbone has been chemically modified with a Carboxylic Acid group. The resulting elastomer is a Nitrile rubber with outstanding abrasion and chemical resistance, superior to that of traditional Nitrile.
Neoprene (CR)
Chloroprene was the first synthetic rubber, and was developed commercially under the name Neoprene®. Chloroprene packer element seals, rubbers, O-rings, gaskets, & custom molded parts contain Chlorine in the polymer to reduce the reactivity to many oxidizing agents, as well as to oil and flame.
Polyurethane (PU, AU)
Polyurethane packer element seals, O-rings, gaskets, & custom molded parts generally have two or three times greater tensile strength and wear resistance than Nitrile and comparable polymers. Polyurethane also provides excellent permeation resistance when compared to most rubbers.
PTFE (Teflon)
The harshest environments require specialized solutions. Often times, a Canyon Components PTFE packer element seals are used in harsh chemical environments. Polytetrafluoroethylene, commonly known as PTFE or Teflon®, is a high-performance fluoropolymer known for its exceptional chemical resistance, low friction, and non-stick properties.
Product Types
Custom Parts
Here at Canyon Components, we make sure to offer our customers any manufacturing technique they desire. Whether your O-rings, gaskets, & custom molded parts be rubber, plastic, or metal, rest assured that Canyon Components can make it!
Gaskets & Custom Cutting
Whether your custom cut parts be rubber, plastic, sponge, composite, or metal, rest assured that Canyon Components can make it! Canyon Components strives to meet all customer service requests. If you need something that isn't listed, feel free to contact a Canyon Components product and application consultant.
Infinite "Giant" Diameter O-Rings
By either Continuous Molding O-rings, or Splice & Vulcanizing O-rings, Canyon can provide mold-less, infinitely large O-rings at competitive prices!
Specialty Compliances
Canyon have materials available for O-rings, gaskets, & custom parts with compliances ranging from USP Class VI <87> & <88> for medical applications, to FDA CFR 21.177.2600 grades A through F for different food types, to the various drinking water specifications like KTW and NSF. Whether it's metal, rubber, or plastic, Canyon can meet your needs!
Packer Element Seals Pros & Cons
Packer element seals are indispensable for maintaining well integrity, ensuring zonal isolation, and optimizing production in the oil and gas industry. With their ability to withstand extreme pressures, temperatures, and chemical exposure, packer seals are critical for downhole operations, from well completion to enhanced oil recovery. While they may require careful selection and maintenance, the benefits they provide in terms of reliability, durability, and well control make them an essential component for any wellbore operation.
Canyon Components strives to meet all customer service requests. Feel free to contact Canyon Components engineering and let our knowledgeable staff help you design the perfect part for your needs.
Pros of Packer Element Seals
Packer element seals provide several advantages, making them indispensable in downhole applications:
- Durability in Harsh Environments: Packer seals are built to withstand the most challenging conditions, from extreme pressures to high temperatures and exposure to aggressive fluids, ensuring reliability and longevity in downhole operations.
- Reliable Sealing: These seals maintain their performance even under fluctuating wellbore conditions, providing a reliable barrier against fluid migration and maintaining well integrity.
- Versatility: Packer element seals are available in various sizes, configurations, and materials, allowing for customization based on wellbore conditions and the specific requirements of each operation.
- Enhanced Well Control: By isolating different sections of the well, packer seals enable operators to control production, fluid flow, and pressure more effectively, improving operational efficiency and safety.
- Cost Savings: By ensuring proper zonal isolation and preventing well integrity issues, packer seals can help reduce costly downtime, repairs, and maintenance in the long term.
Cons of Packer Element Seals
While packer element seals offer numerous benefits, there are some potential drawbacks:
- Material Degradation: Over time, packer seals can degrade due to prolonged exposure to high temperatures, chemicals, or mechanical stress, requiring regular inspection and replacement to maintain performance.
- Installation Complexity: Installing packer element seals in deep wells or highly deviated wellbores can be challenging, requiring specialized equipment and expertise.
- Cost of High-Performance Materials: While essential for extreme environments, high-performance elastomer compounds used in packer seals, such as HNBR or FKM, can increase the overall cost of the seals.
Back to Products Hub
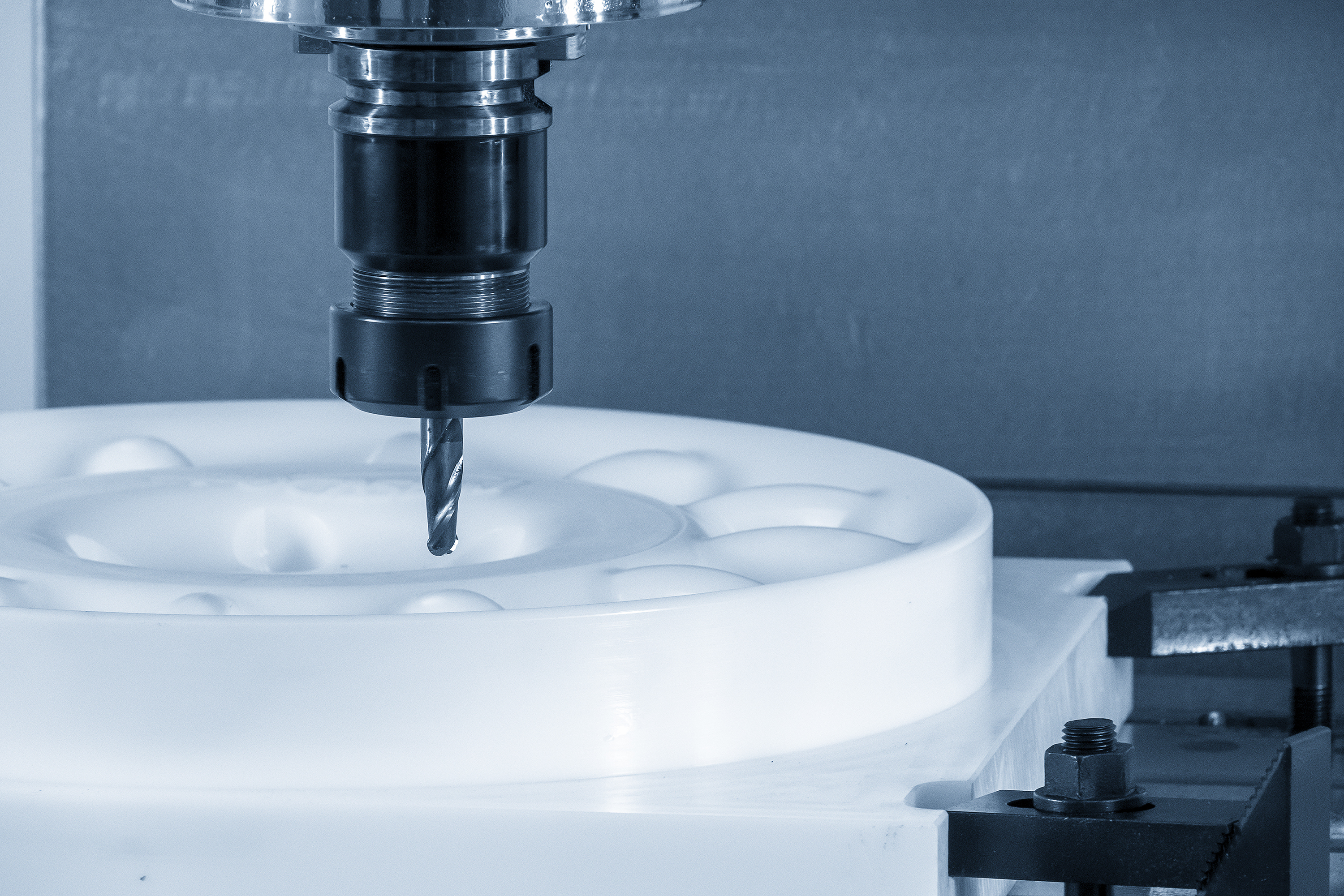
Get A Quote Now!
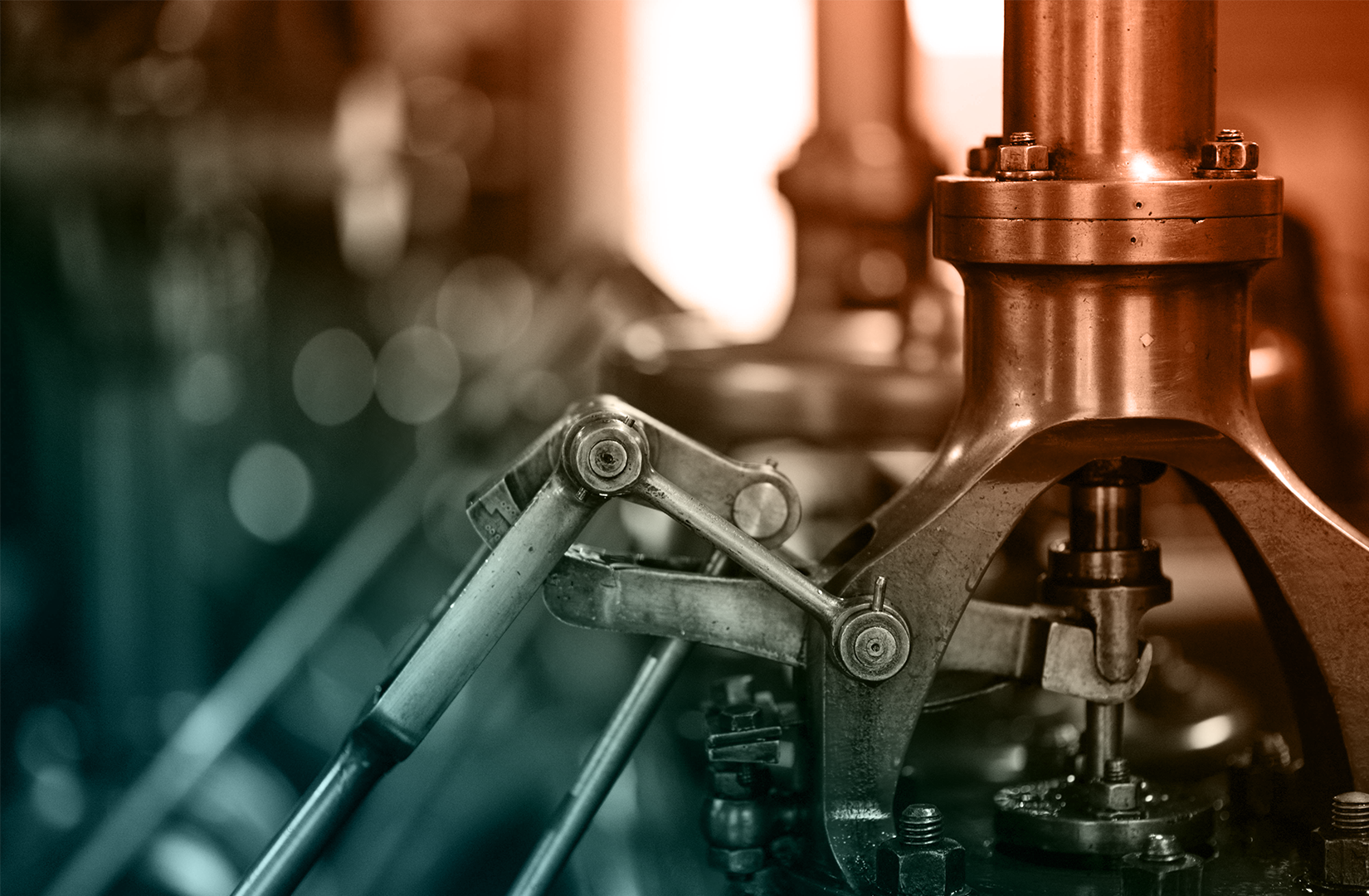