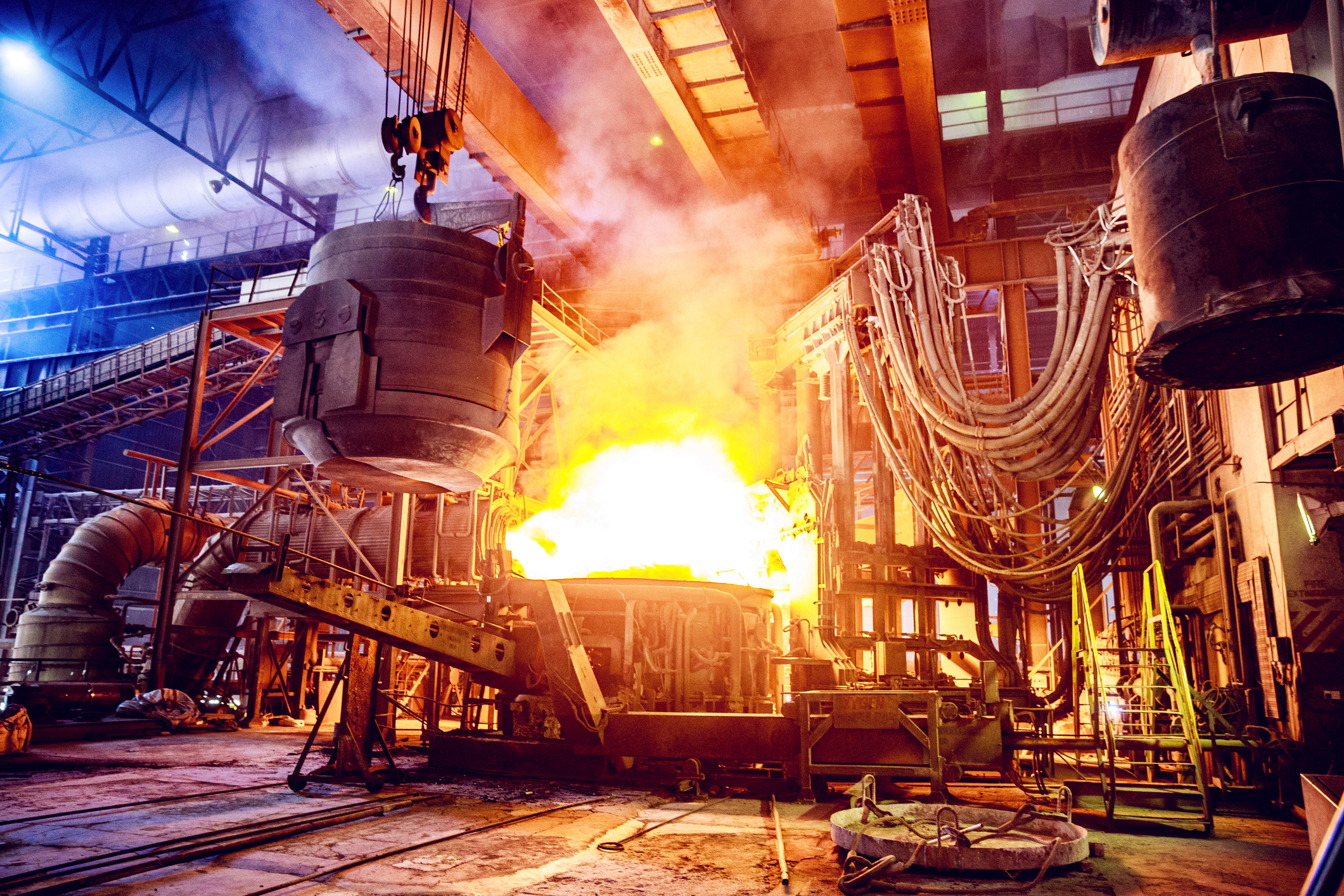
ASTM D2000: Elastomeric Materials
ASTM D2000 is a widely recognized standard that provides a classification system for elastomeric materials based on their performance properties, making it easier for manufacturers and engineers to specify the right elastomer for various applications. ASTM D2000 elastomeric materials are used in a broad range of industries, from automotive to industrial applications, due to their versatility and durability. This guide covers the features, common applications, and the pros and cons of ASTM D2000 elastomeric materials.
ASTM D2000 tested silicone, fluorosilicone, EPDM, CanRez® FFKM and Kalrez® O-rings, gasket rapid manufacturing, & custom molded parts are available now!
Check with one of Canyon’s helpful product engineers for an expert material and manufacturing recommendation.
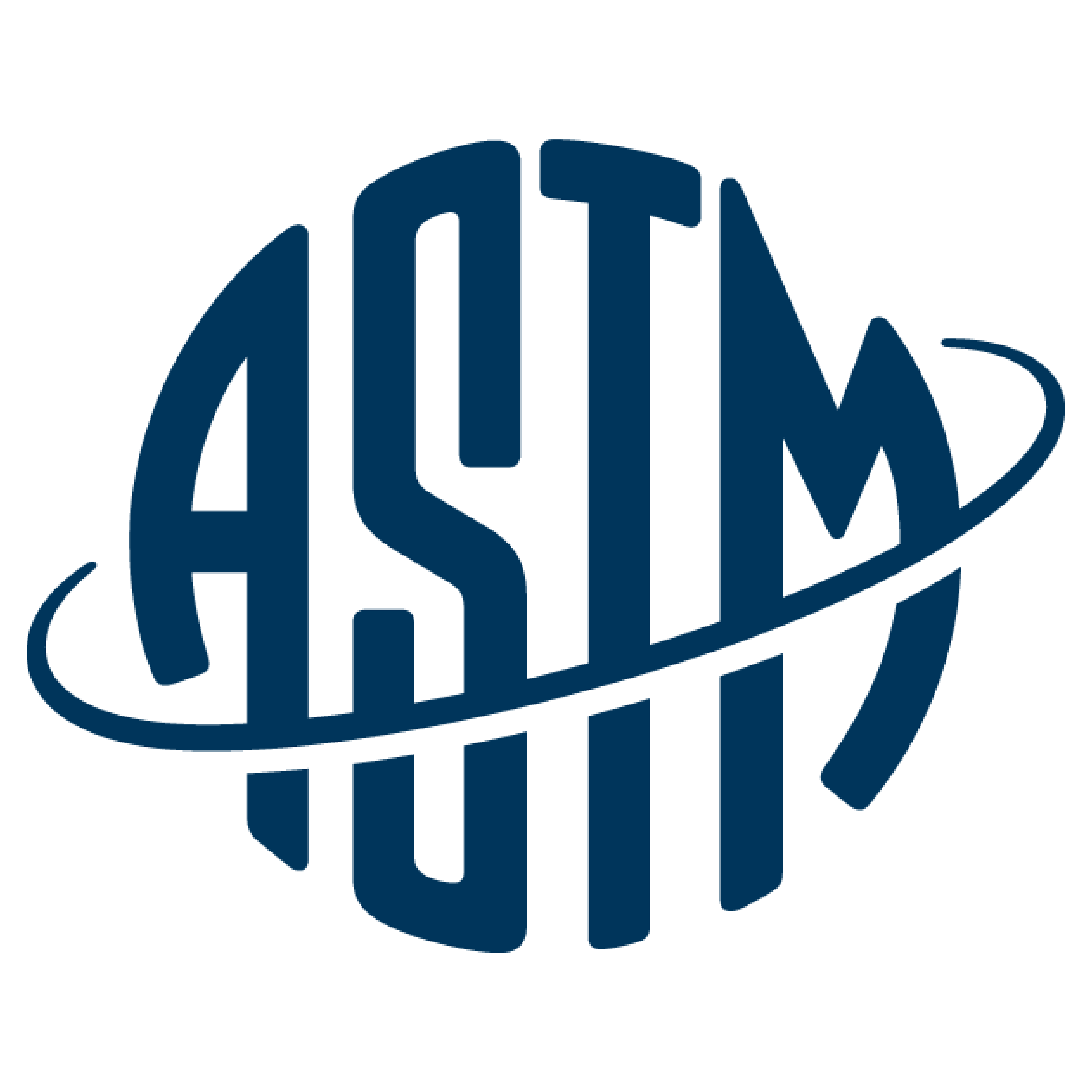
How to Read ASTM D 2000 Specifications
ASTM D2000 is a comprehensive standard used to classify and describe the properties of rubber and elastomeric materials. It's designed to help engineers, manufacturers, and quality assurance professionals identify suitable rubber compounds for various applications based on their performance characteristics. Understanding how to read and interpret ASTM D2000 is essential for selecting the right material for your specific requirements.
NOTE: This description is not all inclusive. For exact details of test requirements, it will be necessary to also review ASTM D2000 itself.
1. Understanding the Basic Format
The ASTM D 2000 specification format follows a structured sequence of letters and numbers that define the rubber's properties. A typical ASTM D2000 line might look like this:
ASTM D 2000 M2BC614 A14 B14 EO14 EO34 F17
For this guide on how to read ASTM D 2000, we will use this example spec as reference. Let's break down each part:
2. Breaking Down the Specification Line
ASTM D 2000 M2BC614 A14 B14 EO14 EO34 F17
ASTM D 2000: Indicates that the material follows the ASTM D2000 standard.
M: The optional "M" indicates metric units. If absent, it defaults to imperial (English) units.
Grade (2): The first digit following the M (in this case, "2") represents the grade of the material, indicating whether it meets specific requirements. Grades range from 1 to 9, with higher numbers meaning more stringent requirements or testing conditions.
Type & Class (BC): The next two letters indicate the type and class of the material. This defines the resistance of the material to swelling in ASTM Oil No. 3 after 70-h immersion at a temperature determined by the Type list below. Limits of swelling for each class are shown in the Class list below.
For example, a BC material would be one that is expected to have up to 120% swell when placed in ASTM Oil No. 3 for 70 hours at 100°C.
NOTE: A material being tested to BC does not mean that the material couldn't also be tested to another material specification. For example, an FKM material would typically be listed with the Type and Class of "HK" which would mean that it is being tested to the relatively stringent requirements of HK. That same FKM could also be tested to BC, DE, or any number of other ASTM D2000 specification Type/Classes and it may or may not pass. Just because a material has an ASTM D2000 specification does not mean that it couldn't be successfully tested to a different ASTM D2000 specification.
- Type is based on the temperature resistance of the elastomer:
- A: Up to 70°C
- B: Up to 100°C
- C: Up to 125°C
- D: Up to 150°C
- E: Up to 175°C
- F: Up to 200°C
- G: Up to 225°C
- H: Up to 250°C
- J: Up to 275°C
- K: Up to 300°C
- Class represents the oil resistance of the elastomer:
- A: No Requirement
- B: 140% Swell
- C: 120% Swell
- D: 100% Swell
- E: 80% Swell
- F: 60% Swell
- G: 40% Swell
- H: 30% Swell
- J: 20% Swell
- K: 10% Swell
Below is a list of the polymers most frequently used for each Type/Class designation.
- AA: Natural rubber, reclaimed rubber, SBR, butyl, EP polybutadiene, polyisoprene
- AK: Polysulfides
- BA: Ethylene propylene, high-temperature SBR and butyl compounds
- BC: Chloroprene polymers (neoprene), cm
- BE: Chloroprene polymers (neoprene), cm
- BF: NBR polymers
- BG: NBR polymers, urethanes
- BK: NBR
- CA: Ethylene propylene
- CE: Chlorosulfonated polyethylene (Hypalon), cm
- CH: NBR polymers, epichlorohydrin polymers
- DA: Ethylene propylene polymers
- DE: CM, CSM
- DF: Polyacrylic (butyl-acrylate type)
- DH: Polyacrylic polymers, HNBR
- EE: AEM
- EH: ACM
- EK: FZ
- FC: Silicones (high strength)
- FE: Silicones
- FK: Fluorinated silicones
- GE: Silicones
- HK: Fluorinated elastomers (Viton, Fluorel, etc.)
- KK: Perfluoroelastomers
3. Hardness and Tensile Strength (614)
ASTM D 2000 M2BC614 A14 B14 EO14 EO34 F17
Next comes a three-digit code specifying hardness and tensile strength:
- 6: This indicates the hardness of the material, measured in Shore A durometer. In this case, "6" means 60 Shore A hardness (add a "0" to convert it).
- 14: Represents the minimum tensile strength in megapascals (MPa). Multiply by 1.45 to convert to PSI (pounds per square inch). Here, "14" means the material has a tensile strength of 14 MPa (around 2030 psi).
- NOTE: If there was no metric "M" at the beginning of M2BC614, then the 14 would NOT be read in MPa. Instead, it would be displayed in approximate 100's of psi. In this case, 2030 psi is rounded to "20". Ultimately, that means that this material could be described in two ways: M2BC614 or _2BC620
4. Suffix Requirements (A14 B34 EA14 EF31 EO34 F17)
ASTM D 2000 M2BC614 A14 B14 EO14 EO34 F17
Suffixes provide additional information about the elastomer’s performance characteristics under specific conditions. Each suffix is made up of a letter followed by a number. Let's break down a part of our example material: A14 B14 EO14 EO34 F17
- A14:
- "A" refers to the suffix letter, which in this case means heat resistance.
- "14" refers to the specific test condition or requirement, which in this case is 70 hours at 100°C.
- B14:
- "B" refers to the suffix letter, which in this case mean compression set.
- "14" refers to the specific test condition or requirement, which in this case is 22 hours at 100°C.
- EO14:
- "EO" refers to the suffix letter, which in this case means fluid resistance.
- "14" refers to the specific test condition or requirement, which in this case is submersion in ASTM No. 1 Oil tested to 70 hours at 100°C.
- EO34:
- "EO" refers to the suffix letter, which in this case means fluid resistance.
- "34" refers to the specific test condition or requirement, which in this case is submersion in ASTM No. 3 Oil tested to 70 hours at 100°C.
- F17:
- "F" refers to the suffix letter, which in this case means low-temperature resistance.
- "17" refers to the specific test condition or requirement, which in this case is non-brittle after 3 minutes at -40°C.
Below is a complete list of the meaning of all of the Suffixes.
- A: Heat Resistance
- B: Compression Set
- C: Ozone or Weather Resistance
- D: Compression-Deflection Resistance
- EA: Fluid Resistance (Aqueous)
- EF: Fluid Resistance (Fuels)
- EO: Fluid Resistance (Oils and Lubricants)
- F: Low-Temperature Resistance
- G: Tear Resistance
- H: Flex Resistance
- J: Abrasion Resistance
- K: Adhesion
- M: Flammability Resistance
- N: Impact Resistance
- P: Staining Resistance
- R: Resilience
- Z: Any special requirement, which shall be specified in detail
NOTE: This description is not all inclusive. For exact details of test requirements, it will be necessary to also review ASTM D2000 itself.
5. Interpreting ASTM D2000 in Practice
Let’s summarize how to interpret our example specification:
ASTM D 2000 M2BC614 A14 B14 EO14 EO34 F17
- ASTM D 2000: This material is tested to ASTM D 2000. ASTM D 2000 should be referenced when determining the materials characteristics.
- M: Metric units
- Grade 2: Meets Grade 2 specifications
- Type B, Class C: Material is being tested as a "BC" tested material. All test requirements will be in the BC section of ASTM D2000.
- 614: Hardness 60 Shore A with a tensile strength of 14 MPa.
- Suffix Requirements:
- A14: Heat resistance under a specific condition.
- B14: Compression set requirement.
- EO14, EO34: Fluid resistance requirements.
- F17: Low-temperature resistance.
Additional Tips:
- Always Refer to the ASTM D2000 Table: This guide is a summary, but ASTM D2000 provides a detailed table listing all the possible types, classes, and suffix requirements.
- Cross-Check Material Specifications: The ASTM D2000 specification is broad. Ensure the material meets all the suffix requirements for your application.
Features & Applications of ASTM D 2000
Features of ASTM D2000 Elastomeric Materials
ASTM D2000 elastomeric materials offer several important features that make them suitable for diverse industrial applications:
- Performance-Based Classification: ASTM D2000 specifies the performance characteristics of elastomers, such as hardness, tensile strength, elongation, and compression set. This ensures that the material chosen will meet the specific requirements of the application.
- Wide Range of Elastomers: The ASTM D2000 standard applies to a broad spectrum of elastomer types, including nitrile rubber (NBR), silicone (VMQ), EPDM, fluorocarbon (FKM), and neoprene (CR), among others.
- Temperature and Chemical Resistance: Many ASTM D2000 materials are designed to withstand extreme temperatures and exposure to oils, chemicals, and solvents, making them highly versatile for harsh environments.
- Customizable Specifications: ASTM D2000 allows for customizable material grades to meet specific application needs, including resistance to compression, abrasion, and environmental factors.
- Long-Term Durability: Elastomers classified under ASTM D2000 are known for their long-lasting performance in demanding conditions, ensuring that components maintain their integrity over time.
Common Applications of ASTM D2000 Elastomeric Materials
ASTM D2000 elastomeric materials are used in a wide range of industries and applications where durability, flexibility, and resistance to environmental factors are critical:
- Automotive Industry: ASTM D2000 materials are commonly used in seals, gaskets, O-rings, and hoses in automotive applications, where resistance to heat, oil, and chemicals is essential for engine and transmission systems.
- Industrial Equipment: These elastomers are used in seals, gaskets, and diaphragms for industrial equipment, including pumps, compressors, and valves, providing reliable sealing performance in harsh environments.
- Aerospace Industry: ASTM D2000 materials are used in aerospace applications for seals, O-rings, and gaskets, where they must withstand extreme temperature variations, pressure, and exposure to aviation fuels and lubricants.
- Oil and Gas Industry: In oil and gas applications, ASTM D2000 elastomers are used for sealing components in drilling and production equipment, where resistance to harsh chemicals and extreme pressure is required.
- Consumer Products: These materials are also found in various consumer products, including kitchen appliances, HVAC systems, and medical devices, where flexibility and durability are important.
Please consult a Canyon Components Engineer about your specific application and we will use our decades of experience to formulate a solution that fits your need.
Get a Quote Now!
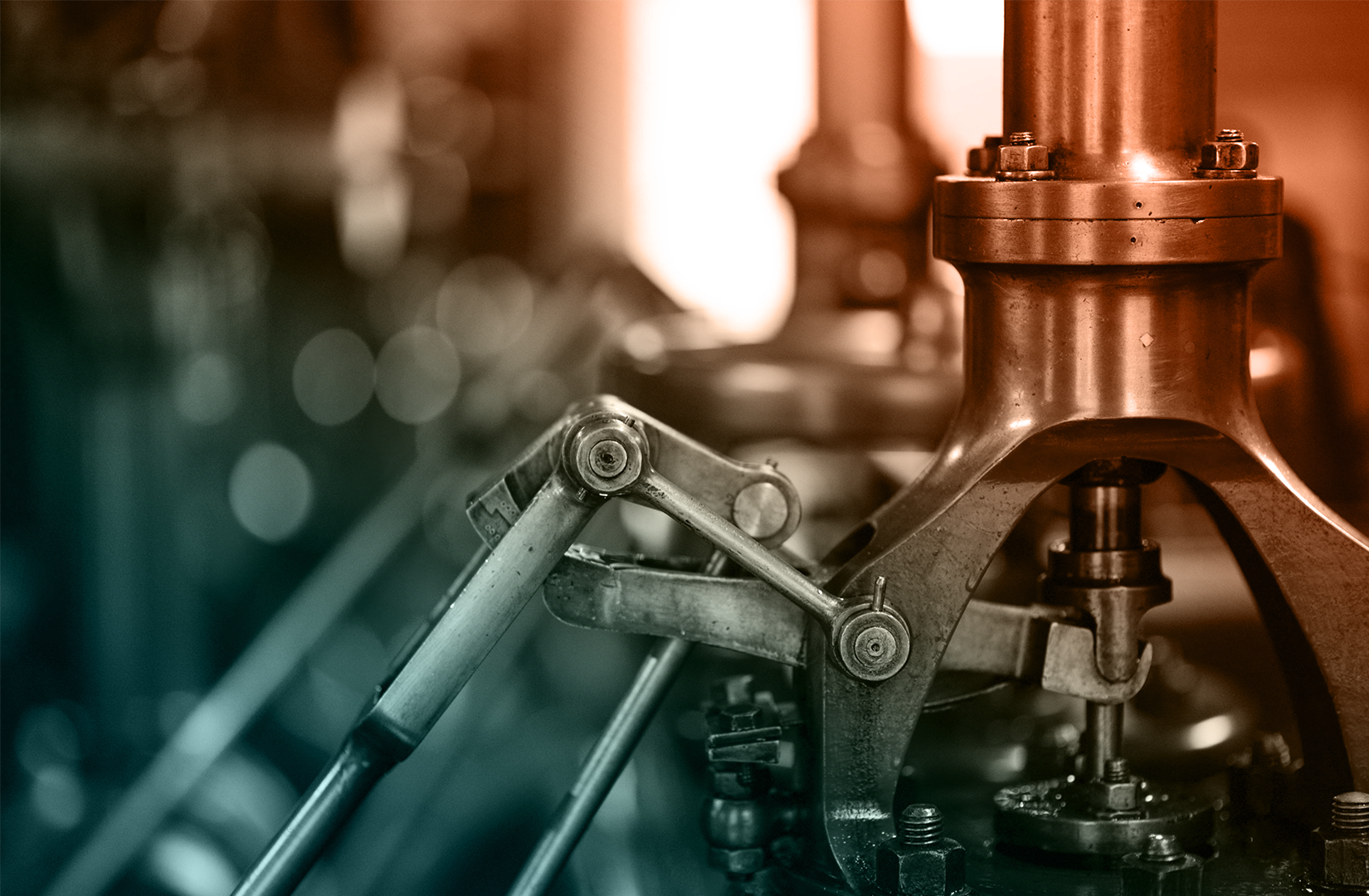
ASTM D2000 Tested Elastomers
CanRez™ FFKM Perfluoroelastomer
Extreme temperatures & chemicals require extreme solutions! ASTM D2000 Tested CanRez™ FFKM materials offer extreme reliability where you need it most! Thousands of sizes in stock now!
Kalrez® FFKM Perfluoroelastomer
Canyon Components offers ASTM D2000 Tested Kalrez® Perfluoroelastomer (FFKM) O-rings, gaskets, & custom molded parts at competitive prices and with great lead-times.
ASTM D2000 Tested Parker® O-rings, Parofluor parts, parker FKM Viton
Canyon Components offers ASTM D2000 Tested Parker Hannifin® O-rings, Gaskets, ASTM D2000 Tested Perfluoroelastomer (FFKM) parts, & custom molded parts at competitive prices and with great lead-times.
FKM (Viton®, Fluorocarbon)
ASTM D2000 Tested FKM compounds, O-rings, gaskets, & custom molded parts exhibit excellent mechanical attributes as well as excellent resistance to high temperatures, mineral oil, ozone, fuels, hydraulic fluids, and many other solvents and chemicals.
Aflas® (TFE/P)
ASTM D2000 Tested TFE/P (Aflas) compounds, O-rings, gaskets, & custom molded parts gives high resistance to steam, hot water, atmospheric wear, and many chemicals. TFE/P compounds provide superior performance in water, steam and virtually all caustic chemicals.
Fluorosilicone (FVMQ)
The mechanical and physical properties of ASTM D2000 Tested Fluorosilicone O-rings, gaskets, & custom molded parts are very similar to silicone. Fluorosilicone O-rings, gaskets, & custom molded parts offer improved flexibility and strength, better resistance to fuels and mineral oil, but reduced hot air resistance.
Silicone (VMQ, PVMQ)
ASTM D2000 Tested Silicone seals, O-rings, gaskets, & custom molded parts are excellent for extreme temperatures in static applications. Canyon Components carries a range of silicone materials, and we are happy to custom tailor a seal to meet your application requirements!
EPDM (Ethylene Propylene)
ASTM D2000 Tested EPDM materials, O-rings, gaskets, & custom molded parts can operate over a wide temperature range, and are compatible with glycol fluids that cause problems for most typical elastomeric seals.
NBR (Nitrile, Buna-N)
ASTM D2000 Tested Nitrile O-rings, gaskets, & custom molded parts are very oil-resistant, have strong mechanical properties, are resistant to wear, and are relatively inexpensive. These properties make Nitrile the most commonly used general purpose O-ring, gasket, & custom molded part material.
HNBR (Hydrogenated Nitrile)
ASTM D2000 Tested Hydrogenated Nitrile O-rings, gaskets, & custom molded parts offer higher strength and reduced degradation at high temperatures compared to conventional Nitrile materials. These properties make HNBR materials popular in the oil and gas industry, as well as many applications in the chemical industry.
XNBR (Carboxylated Nitrile)
ASTM D2000 Tested XNBR O-rings, gaskets, & custom molded parts are similar to Nitrile, but the backbone has been chemically modified with a Carboxylic Acid group. The resulting elastomer is a Nitrile rubber with outstanding abrasion and chemical resistance, superior to that of traditional Nitrile.
Neoprene (CR)
Chloroprene was the first synthetic rubber, and was developed commercially under the name Neoprene®. ASTM D2000 Tested Chloroprene rubbers, O-rings, gaskets, & custom molded parts contain Chlorine in the polymer to reduce the reactivity to many oxidizing agents, as well as to oil and flame.
Polyurethane (PU, AU)
ASTM D2000 Tested Polyurethane O-rings, gaskets, & custom molded parts generally have two or three times greater tensile strength and wear resistance than Nitrile and comparable polymers. Polyurethane also provides excellent permeation resistance when compared to most rubbers.
PTFE Encapsulated
ASTM D2000 Tested FEP and PFA encapsulated O-rings consist of an elastomeric core and a seamlessly closed casing of modified PTFE. The elastomer core of encapsulated O-rings is typically made of FKM (Viton) or VMQ (silicone) and guarantees a uniform pre-tensioning at the sealing point.
Specialty Materials & Compliances
Semiconductor Manufacturing Materials
Discover ASTM D2000 Tested materials, designed for use in the semiconductor manufacturing industry requiring the highest levels of purity and precision. Learn about their features, applications, and how they meet strict cleanliness standards in medical, pharmaceutical, and semiconductor environments.
Specialty Compliances
Canyon have materials available for O-rings, gaskets, & custom parts with compliances ranging from USP Class VI <87> & <88> for medical applications, to FDA CFR 21.177.2600 grades A through F for different food types, to the various drinking water specifications like KTW and NSF. Whether it's metal, rubber, or plastic, Canyon can meet your needs!
Custom Parts
Here at Canyon Components, we make sure to offer our customers any manufacturing technique they desire. Whether your ASTM D2000 O-rings, gaskets, & custom molded parts be rubber, plastic, or metal, rest assured that Canyon Components can make it!
Explore Plastic Materials
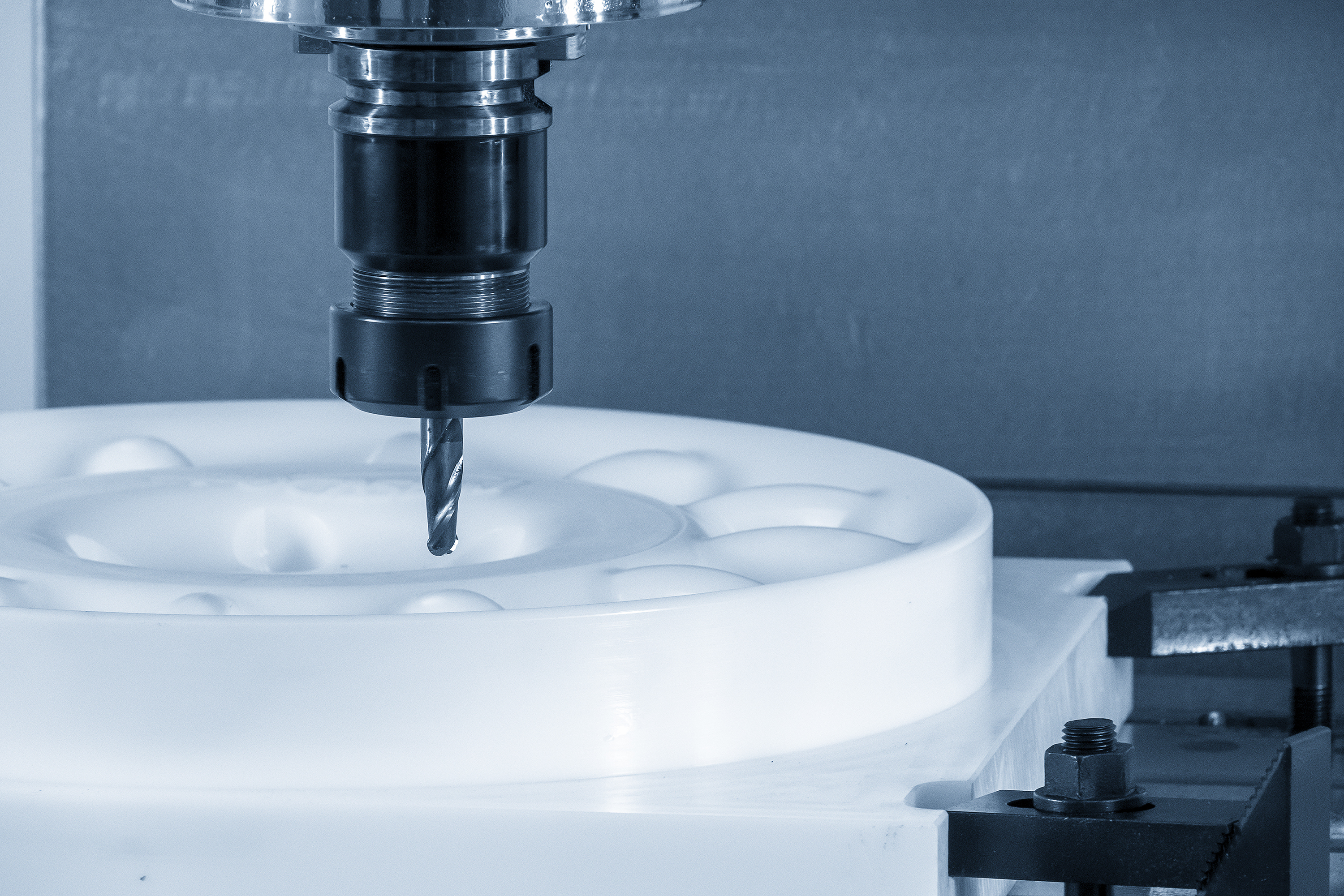
ASTM D2000 Tested Materials Pros & Cons
ASTM D2000 elastomeric materials provide a standardized, reliable solution for industries that require durable and versatile elastomers. With features like temperature and chemical resistance, performance standardization, and customizable material grades, these materials are widely used in automotive, aerospace, oil and gas, and industrial applications. While they offer significant advantages in terms of performance and durability, careful material selection is required to ensure they meet the specific demands of each application. Understanding the features, applications, and potential drawbacks of ASTM D2000 elastomeric materials will help you make informed decisions to ensure the success of your projects.
Canyon Components strives to meet all customer service requests. Feel free to contact Canyon Components engineering and let our knowledgeable staff help you design the perfect part for your needs.
Pros of ASTM D2000 Elastomeric Materials
ASTM D2000 elastomeric materials offer numerous advantages that make them ideal for industrial and commercial applications:
- Performance Standardization: The ASTM D2000 standard ensures consistency in material properties, making it easier to specify elastomers based on the required performance characteristics for the application.
- Versatility: The wide range of elastomer types covered by ASTM D2000 allows manufacturers to choose materials that are optimized for specific operating environments, such as high temperatures, chemical exposure, or mechanical stress.
- Chemical and Temperature Resistance: Many ASTM D2000 elastomers offer excellent resistance to oils, fuels, solvents, and extreme temperatures, ensuring long-lasting performance in harsh environments.
- Customizable Material Grades: ASTM D2000 provides flexibility in specifying material grades, allowing engineers to tailor elastomers to the exact requirements of their applications.
- Durability and Reliability: Elastomers meeting ASTM D2000 standards are designed for long-term use in demanding conditions, reducing the need for frequent replacements and lowering maintenance costs.
Cons of ASTM D2000 Elastomeric Materials
While ASTM D2000 elastomeric materials provide numerous benefits, there are also some potential drawbacks:
- Complex Material Selection: The wide range of elastomers and performance specifications under ASTM D2000 can make it challenging to select the right material for a specific application, requiring expert knowledge and analysis.
- Higher Cost for Specialized Elastomers: Some elastomers classified under ASTM D2000, such as fluorocarbon (FKM) or high-performance silicones, may come with higher costs due to their enhanced properties, such as extreme temperature or chemical resistance.
- Limited Performance Outside of Specifications: Elastomers designed to meet specific ASTM D2000 performance requirements may not perform well in environments outside of their intended specifications, requiring careful consideration during material selection.
- Material Degradation Over Time: While ASTM D2000 elastomers are generally durable, some materials may degrade over time due to environmental factors such as UV exposure, ozone, or oxidation, particularly in outdoor applications.
Relevant Compliances
USP Class VI Materials: Certified for Medical and Pharmaceutical Applications
Explore USP Class VI materials, certified for use in medical devices, pharmaceuticals, and food processing. Learn about their features, compliance standards, and how they ensure safety and purity in critical environments.
FDA Compliant Materials: Safe and Reliable Solutions for Food and Medical Applications
Discover FDA compliant materials, designed for use in food processing, medical devices, and pharmaceutical applications. Learn about their safety features, regulatory compliance, and how they meet stringent industry standards.
Materials for Semicon and Solar
Discover materials for semiconductor and solar applications: specialized for semiconductor manufacturing and durability in advanced energy systems.
Back to Compliance Hub
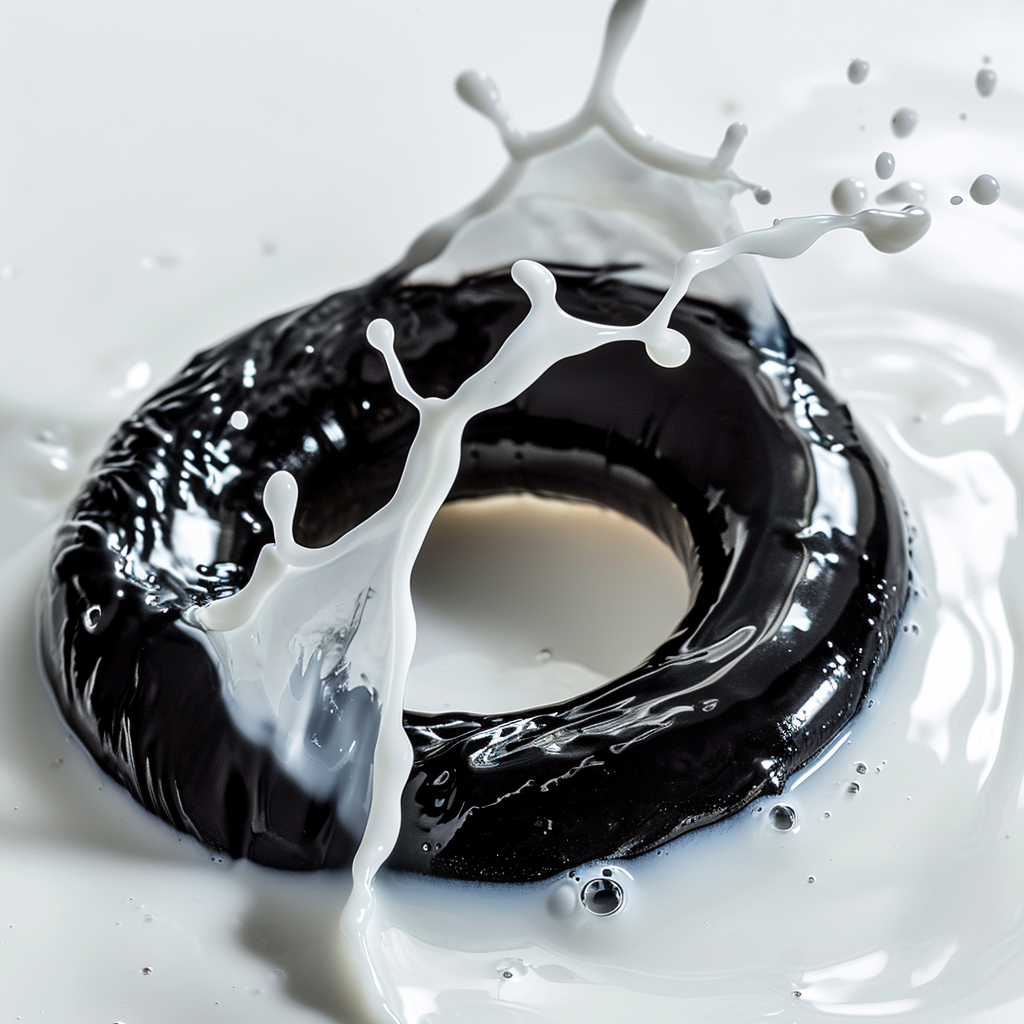
Get A Quote Now!
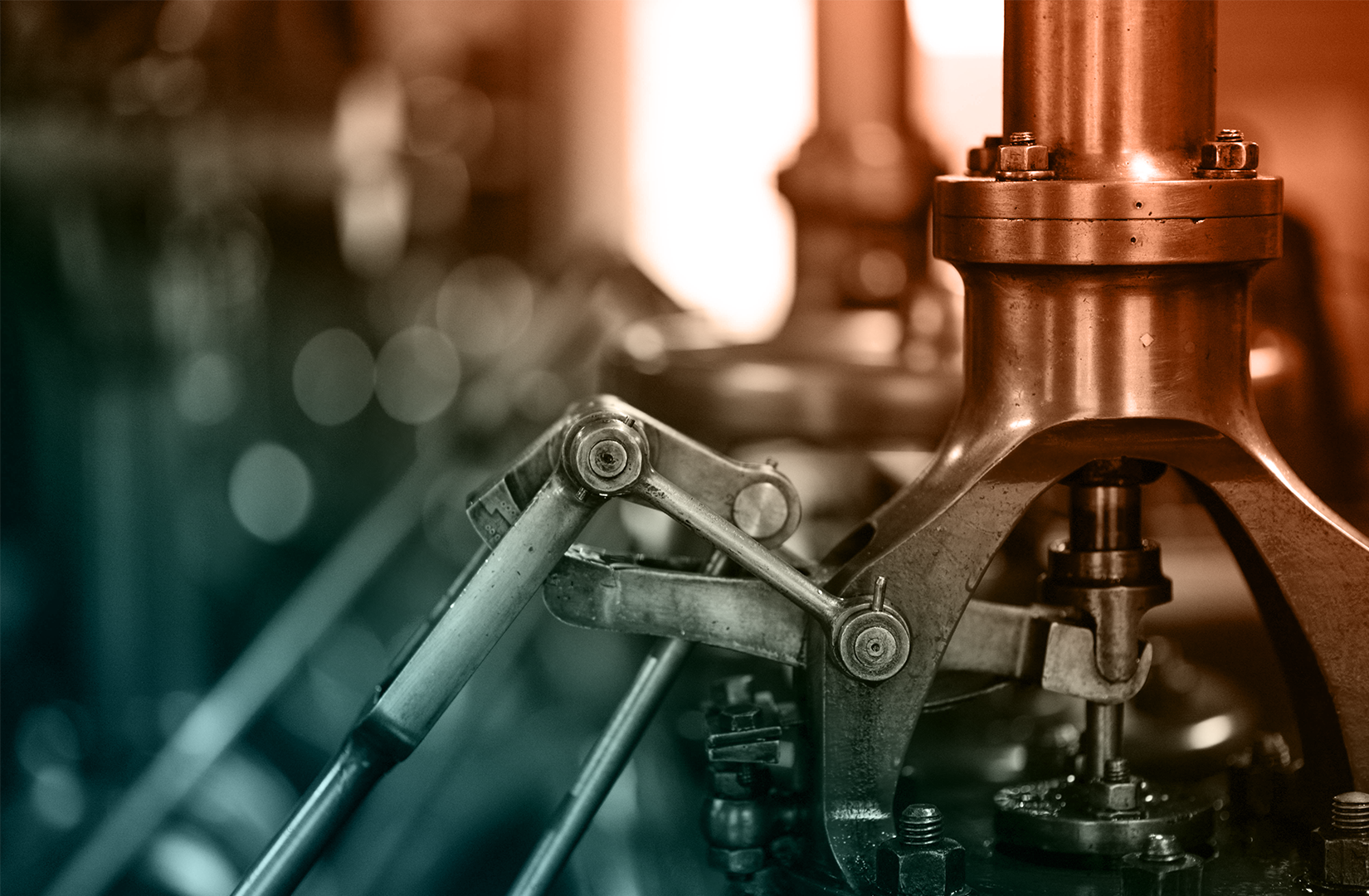