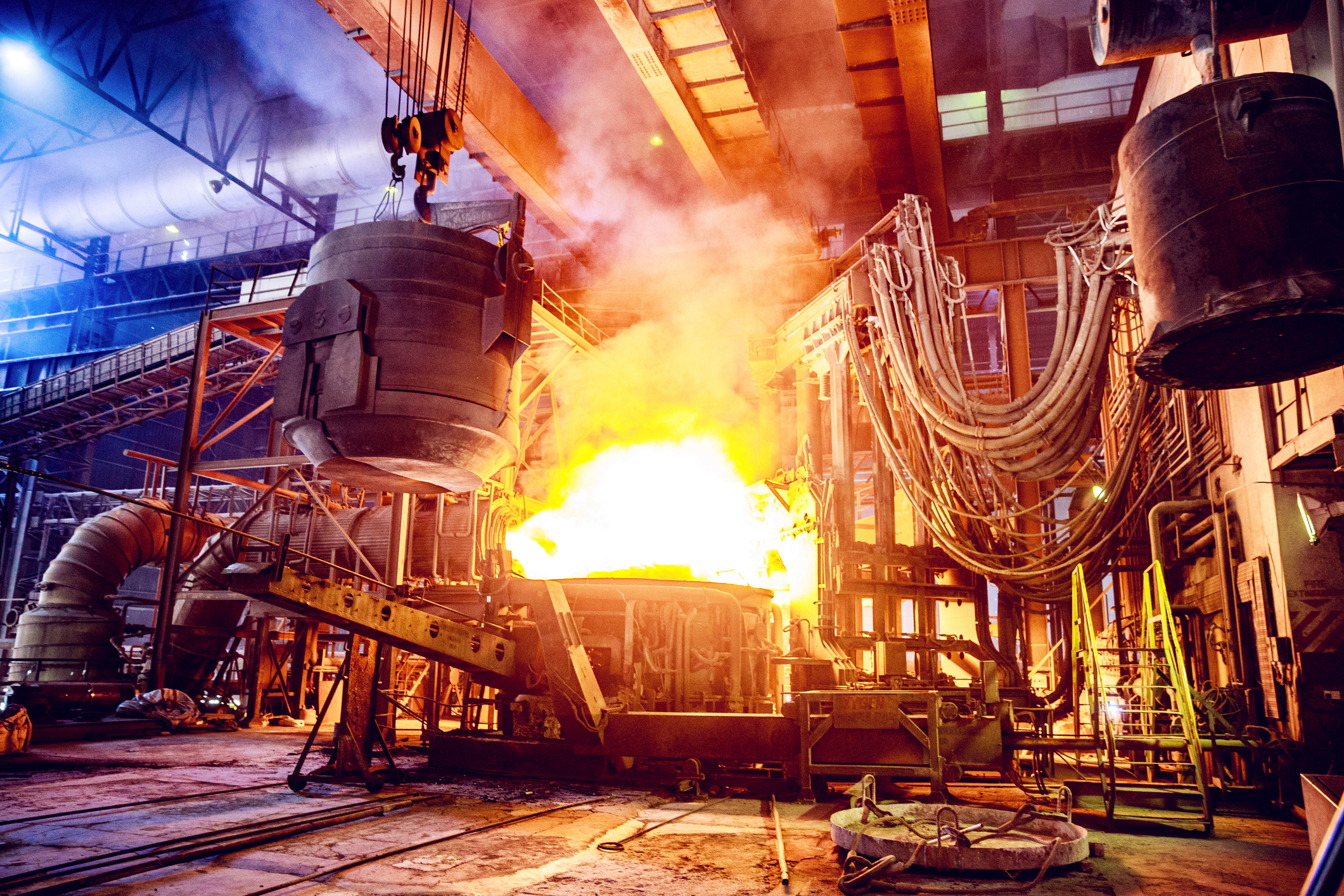
Custom Plastic Parts
Custom plastic parts are essential components in industries ranging from consumer goods to aerospace, offering flexibility, durability, and cost-effectiveness. Whether you're creating plastic enclosures, mechanical components, or intricate designs, custom plastic parts provide solutions for various applications. Understanding the different manufacturing processes and the common types of plastic parts can help you select the right method for your project while balancing performance, cost, and scalability.
Custom manufactured plastic parts with overmolded silicone, CanRez® FFKM and Kalrez® gaskets, rapid manufacturing, & custom molded parts are available now!
Check with one of Canyon’s helpful product engineers for an expert material and manufacturing recommendation.
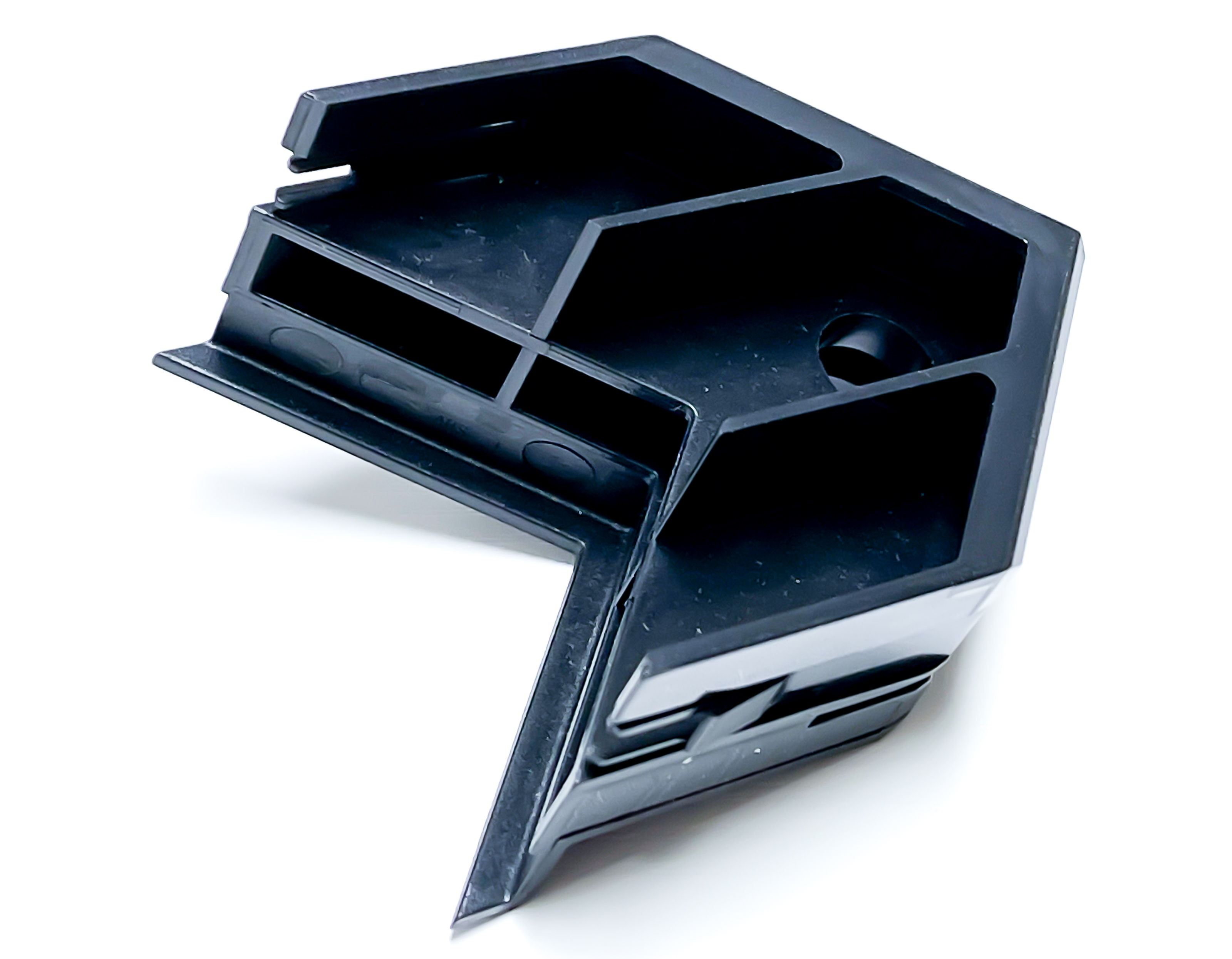
Manufacturing Types for Custom Plastic Parts
There are several manufacturing processes used to create custom plastic parts, each suited for different types of parts, production volumes, and materials.
- Injection Molding: One of the most common methods for producing custom plastic parts, injection molding involves injecting molten plastic into a mold to form the desired shape. This process is ideal for high-volume production and can create highly detailed parts with tight tolerances.
- 3D Printing (Additive Manufacturing): 3D printing allows for the creation of complex plastic parts by building them layer by layer. It’s especially useful for rapid prototyping and small production runs.
- CNC Machining: CNC machining is a subtractive process that involves cutting and shaping plastic from a solid block using computer-controlled machines. It’s ideal for creating precise parts from engineering-grade plastics.
- Blow Molding: Blow molding is used for making hollow plastic parts like bottles and containers. It involves inflating heated plastic into a mold to form the part’s shape.
- Thermoforming: Thermoforming involves heating plastic sheets until they are pliable and then forming them over a mold to create a part. This process is commonly used for large, lightweight parts.
Common Types of Custom Plastic Parts
Custom plastic parts can be found in a variety of industries, each requiring specific performance and aesthetic qualities.
- Enclosures and Housings: Custom plastic enclosures are used to protect sensitive electronics and electrical systems in industries like consumer electronics, telecommunications, and automotive.
- Gears and Bearings: Engineering-grade plastics are used to create gears and bearings that are lightweight, resistant to wear, and often self-lubricating, reducing the need for maintenance.
- Prototypes: Rapid prototyping with 3D printing or CNC machining is widely used to create functional plastic models for testing and design verification before mass production.
- Medical Components: Custom plastic parts are essential in the medical field, from surgical instruments to diagnostic devices, where precision and biocompatibility are critical.
- Consumer Products: Plastic parts are commonly used in everyday products like household items, packaging, and toys, offering durability and cost-effectiveness for mass production.
Please consult a Canyon Components Engineer about your specific application and we will use our decades of experience to formulate a solution that fits your need.
Get a Quote Now!
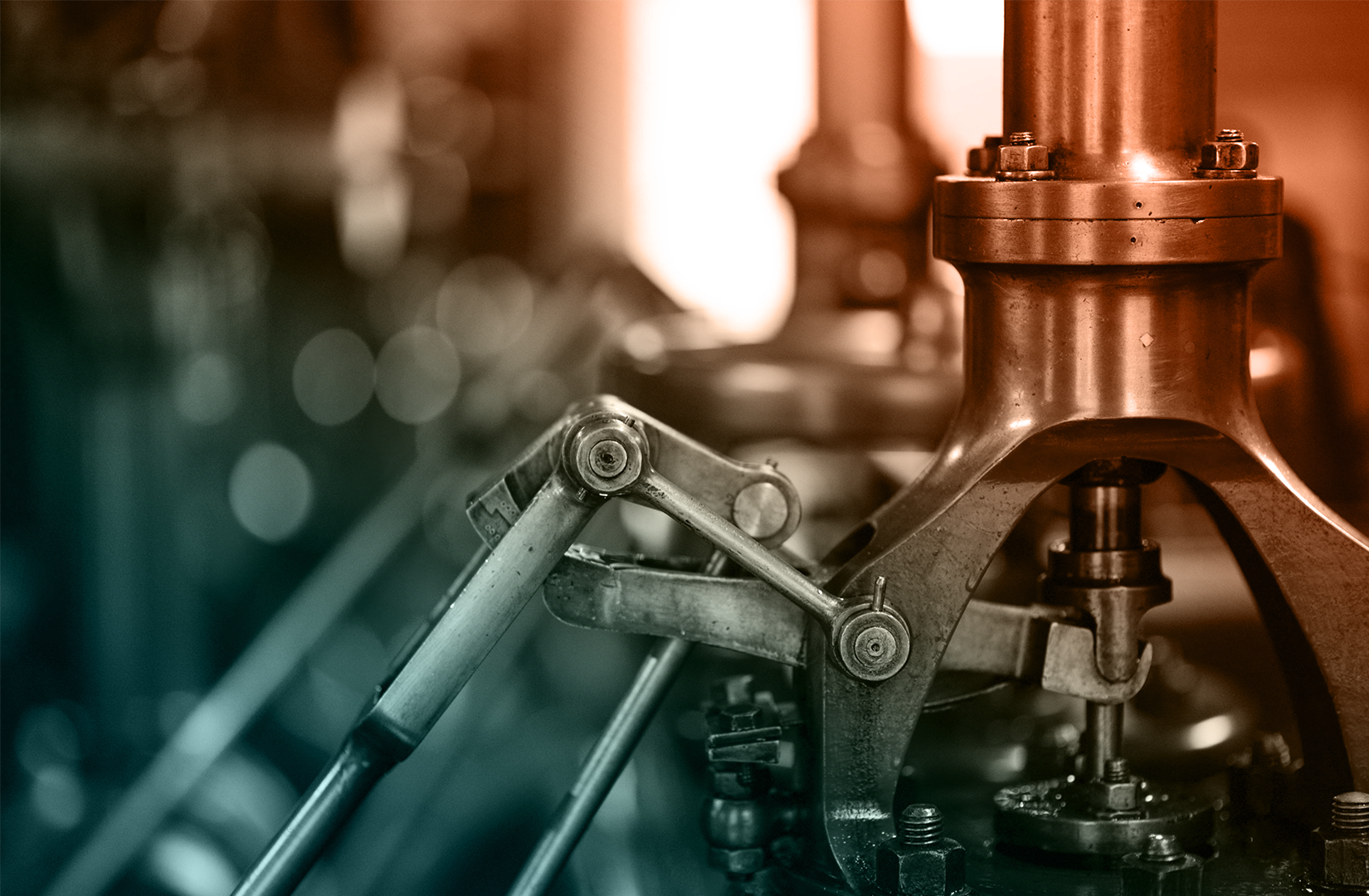
Materials
ABS (Acrylonitrile Butadiene Styrene)
ABS plastic, a thermoplastic polymer blend of acrylonitrile, butadiene, and styrene, is renowned for its toughness, impact resistance, and rigidity. It's easily machinable and ideal for automotive parts, consumer goods, and 3D printing due to its strength and versatility.
Nylon (Polyamide, PA)
Nylon, a synthetic thermoplastic polymer, is renowned for its high strength, elasticity, and abrasion resistance. It's versatile, easily dyeable, and used in a wide range of products from textiles and ropes to gears and automotive parts.
PBT (Polybutylene Terephthalate)
PBT (Polybutylene Terephthalate) is a durable, heat-resistant thermoplastic with excellent electrical properties. It's known for its strength, stiffness, and stability under heat, widely used in electrical components, automotive parts, and consumer goods.
PC (Polycarbonate)
Polycarbonate (PC) Plastic is a tough, transparent thermoplastic with exceptional impact resistance, heat tolerance, and optical clarity. Its versatility makes it ideal for bulletproof glass, eyewear lenses, medical devices, and protective gear, offering a unique balance of strength and lightweight properties.
PC/ABS (Polycarbonate ABS Blend)
PC/ABS (Polycarbonate/Acrylonitrile Butadiene Styrene) Plastic is a robust blend combining the heat resistance and mechanical strength of polycarbonate with the flexibility and high-quality finish of ABS. Ideal for automotive, electronics, and consumer goods, it offers excellent impact resistance and durability.
PC/ASA (Polycarbonate ASA Blend)
PC/ASA plastic, a blend of polycarbonate and acrylonitrile styrene acrylate, offers superior UV resistance, high heat stability, and excellent mechanical properties. Ideal for outdoor applications, it combines durability with aesthetic appeal and is widely used in automotive and electronics industries.
PEEK (Polyetheretherketone)
PEEK plastic, or polyether ether ketone, is a high-performance thermoplastic known for its exceptional heat resistance, chemical stability, and mechanical strength. It's widely used in aerospace, medical implants, and automotive industries for its durability and ability to withstand harsh environments.
PET (Polyethylene Terephthalate)
Polyethylene Terephthalate (PET) is a durable, lightweight thermoplastic, renowned for its clarity, strength, and recyclability. Widely used in beverage bottles, food packaging, and textiles, PET is also food-safe, resistant to water and many chemical solvents, and easily formed into various shapes.
PETG (Polyethylene Terephthalate Glycol)
PETG plastic, a glycol-modified version of polyethylene terephthalate, is valued for its clarity, excellent chemical resistance, and thermoformability. It's a popular choice for 3D printing, packaging, and medical devices due to its durability, impact resistance, and ease of fabrication.
PMMA (Polymethyl Methacrylate)
Polymethyl Methacrylate (PMMA) Plastic, commonly known as acrylic or Plexiglas, is a transparent thermoplastic with glass-like clarity and excellent light transmission. It's durable, shatter-resistant, and used in applications like lenses, aquariums, signage, and various architectural features due to its weather-resistant properties.
Polyethylene (PE)
Polyethylene (PE) plastic, renowned for its versatility, is a widely used thermoplastic. It's lightweight, impact-resistant, and has excellent chemical resistance. Commonly used in packaging, containers, and pipes, PE is available in varying densities for different applications, including high and low-density forms.
POM (Polyoxymethylene, Acetal)
Polyoxymethylene (POM) Plastic, also known as Acetal or Delrin, is a high-strength, low-friction thermoplastic. It's characterized by its dimensional stability, excellent wear resistance, and low moisture absorption, making it ideal for precision parts in automotive and consumer electronics.
PP (Polypropylene)
Polypropylene (PP) plastic, known for its exceptional chemical resistance and durability, is a lightweight thermoplastic. It's resilient against fatigue, has a high melting point, and is ideal for packaging, automotive parts, and textiles, thanks to its versatility and recyclability.
PPSU (Polyphenylsulfone)
Polyphenylsulfone (PPSU) Plastic is a high-performance thermoplastic known for its exceptional heat resistance, toughness, and stability under thermal stress. It's widely used in medical instruments, aerospace, and plumbing components due to its excellent chemical resistance and ability to withstand repeated sterilizations.
PS (Polystyrene)
Polystyrene (PS) plastic, a versatile and cost-effective thermoplastic, is known for its rigidity, clarity, and insulating properties. Widely used in packaging, disposable tableware, and insulation, PS is available in both solid and foam forms, catering to a broad range of applications.
PTFE (Polytetrafluoroethylene, Teflon)
Polytetrafluoroethylene (PTFE) Plastic, commonly known as Teflon, is a highly non-reactive and low-friction thermoplastic. Renowned for its outstanding chemical resistance, heat tolerance, and electrical insulation properties, it's extensively used in cookware coatings, electrical insulation, and various industrial applications.
PVC (Polyvinyl Chloride)
Polyvinyl Chloride (PVC) plastic, a widely utilized thermoplastic, is celebrated for its durability, chemical resistance, and versatility. It's commonly used in construction for pipes and fittings, medical devices, and window frames, and can be made more flexible with the addition of plasticizers.
SAN (Styrene Acrylonitrile)
Styrene Acrylonitrile (SAN) plastic is a copolymer blend known for its clarity, rigidity, and resistance to chemicals and heat. It combines the strength of polystyrene with the toughness of acrylonitrile, making it ideal for household and commercial items like containers and kitchenware.
Back to Custom Parts
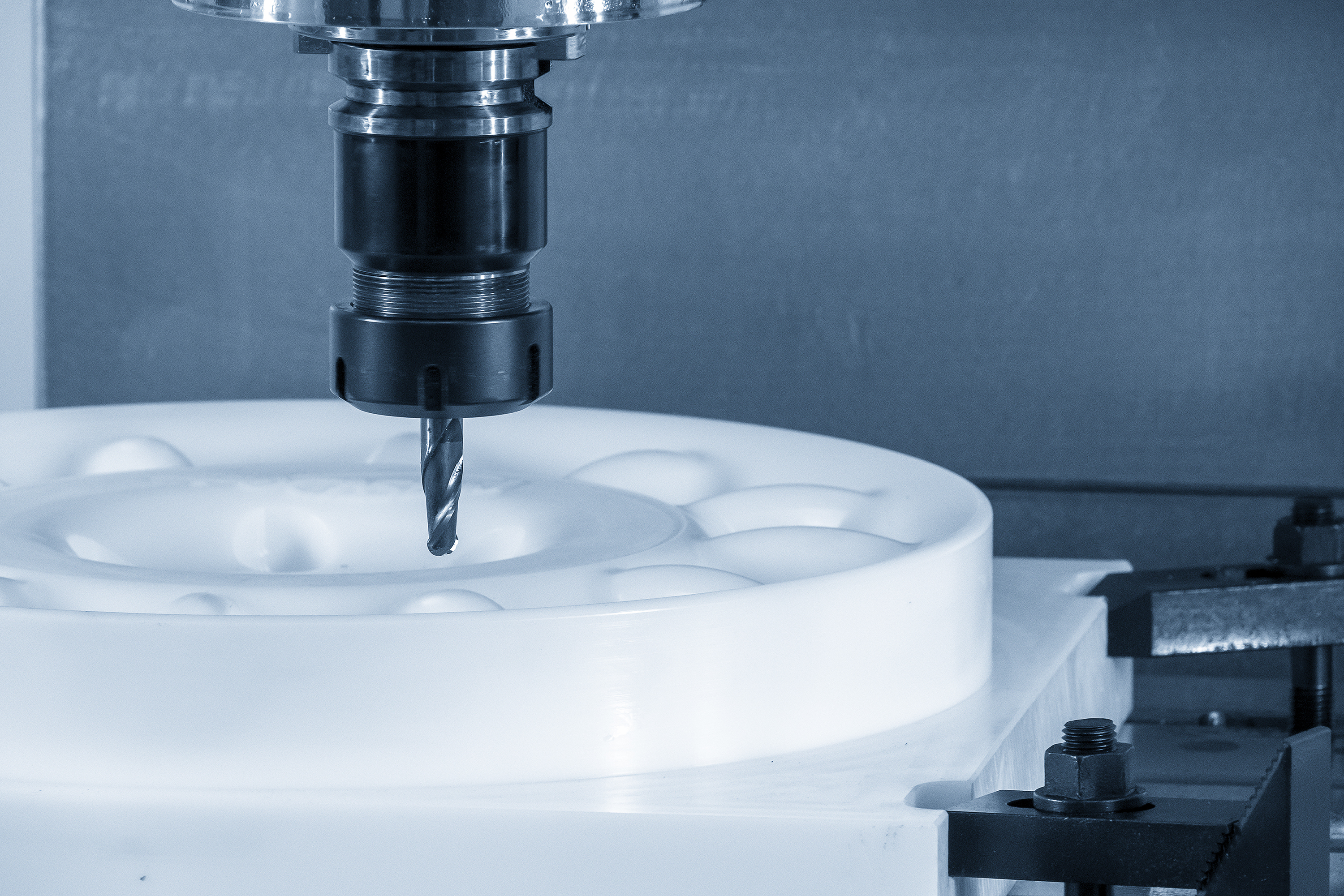
Custom Plastic Parts Pros & Cons
Custom plastic parts are integral to a wide array of industries, offering versatility, durability, and cost-effectiveness for mass production. With several manufacturing options available—including injection molding, CNC machining, and 3D printing—custom plastic parts can be designed to meet precise specifications, from lightweight consumer products to high-performance industrial components. By understanding the various manufacturing processes and material options, you can select the right method for your production needs, ensuring optimal performance and cost efficiency.
Canyon Components strives to meet all customer service requests. Feel free to contact Canyon Components engineering and let our knowledgeable staff help you design the perfect part for your needs.
Pros of Custom Plastic Parts
Custom plastic parts offer a range of benefits that make them ideal for a wide variety of applications:
- Cost-Effective for Mass Production: Once the mold is created, plastic parts can be produced in large volumes at a low cost per unit, making them highly economical for high-volume production.
- Lightweight and Durable: Plastic parts are often lighter than metal components while maintaining excellent durability, making them ideal for applications requiring lightweight materials.
- Versatility in Design: Plastic can be molded into complex shapes, allowing for intricate designs that may be difficult or costly to achieve with metal or other materials.
- Wide Range of Materials: From flexible, impact-resistant plastics to high-temperature-resistant engineering plastics, there is a wide variety of materials to choose from, each suited to specific applications.
- Corrosion Resistance: Plastics are inherently resistant to corrosion, making them a good choice for parts exposed to moisture, chemicals, or harsh environmental conditions.
Cons of Custom Plastic Parts
While custom plastic parts provide numerous advantages, there are some limitations:
- High Tooling Costs for Injection Molding: The initial cost of creating molds for injection molding can be high, making it less cost-effective for small production runs.
- Limited Strength Compared to Metals: While plastic parts are durable, they may not provide the same level of strength or heat resistance as metal components, limiting their use in high-stress or high-temperature applications.
- Environmental Concerns: Plastics can contribute to environmental pollution if not recycled properly, and some types of plastics are difficult to recycle.
- Material Limitations in 3D Printing: While 3D printing is excellent for rapid prototyping, the materials available for this process may not have the same mechanical properties as those used in injection molding or machining.
Other Custom Products
Custom Parts
Whether your O-rings, gaskets, & custom molded parts be rubber, plastic, or metal, rest assured that Canyon Components can make it!
Custom Metal Parts
Explore custom metal parts designed to meet specific requirements across industries. Learn about our manufacturing capabilities, material options, and how we deliver precision-engineered solutions for your projects.
Custom Rubber Parts
Explore custom rubber parts tailored to your exact specifications. Learn about our material options, manufacturing processes, and how we deliver durable and reliable rubber components for various industries.
Back to Custom Parts
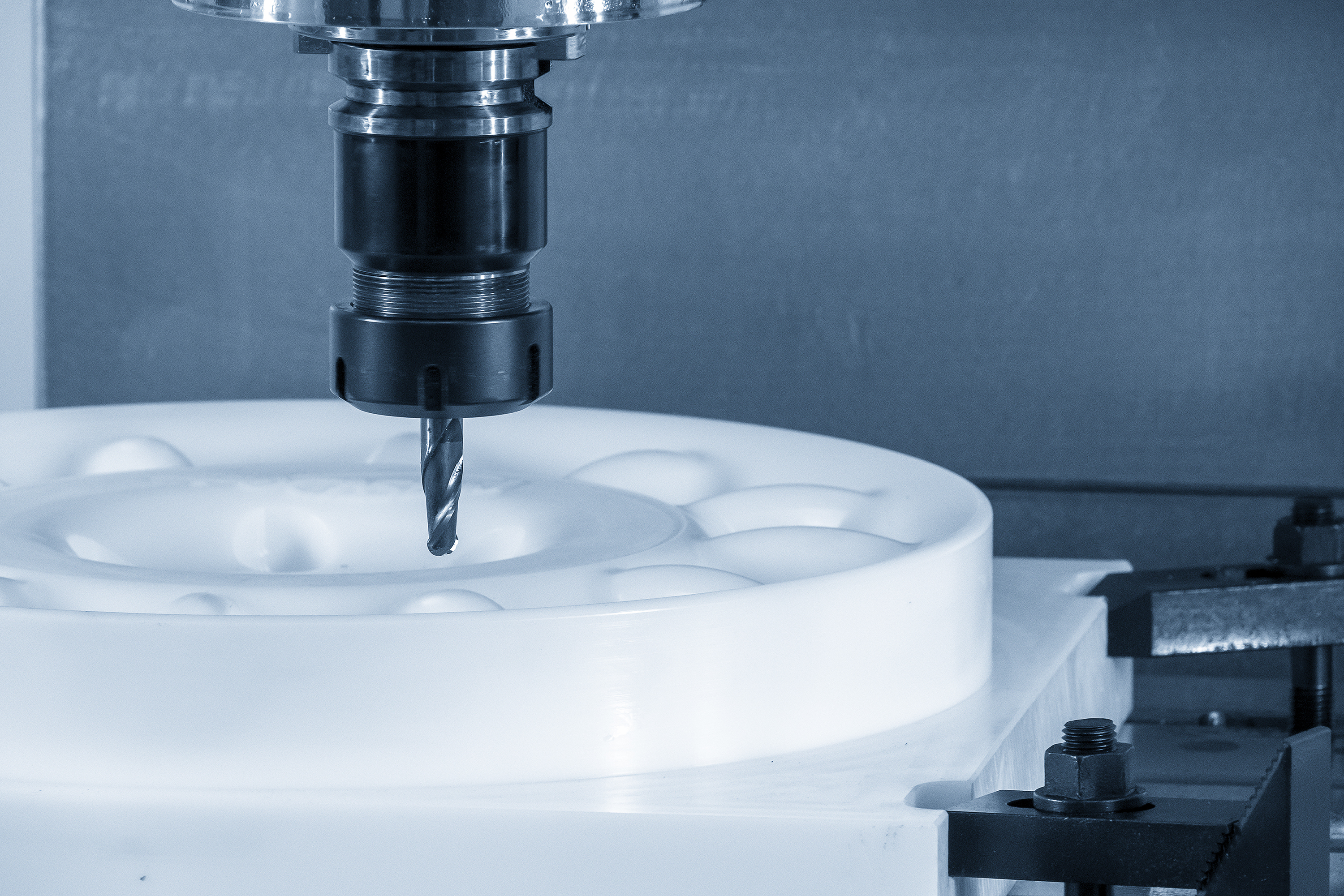
Get A Quote Now!
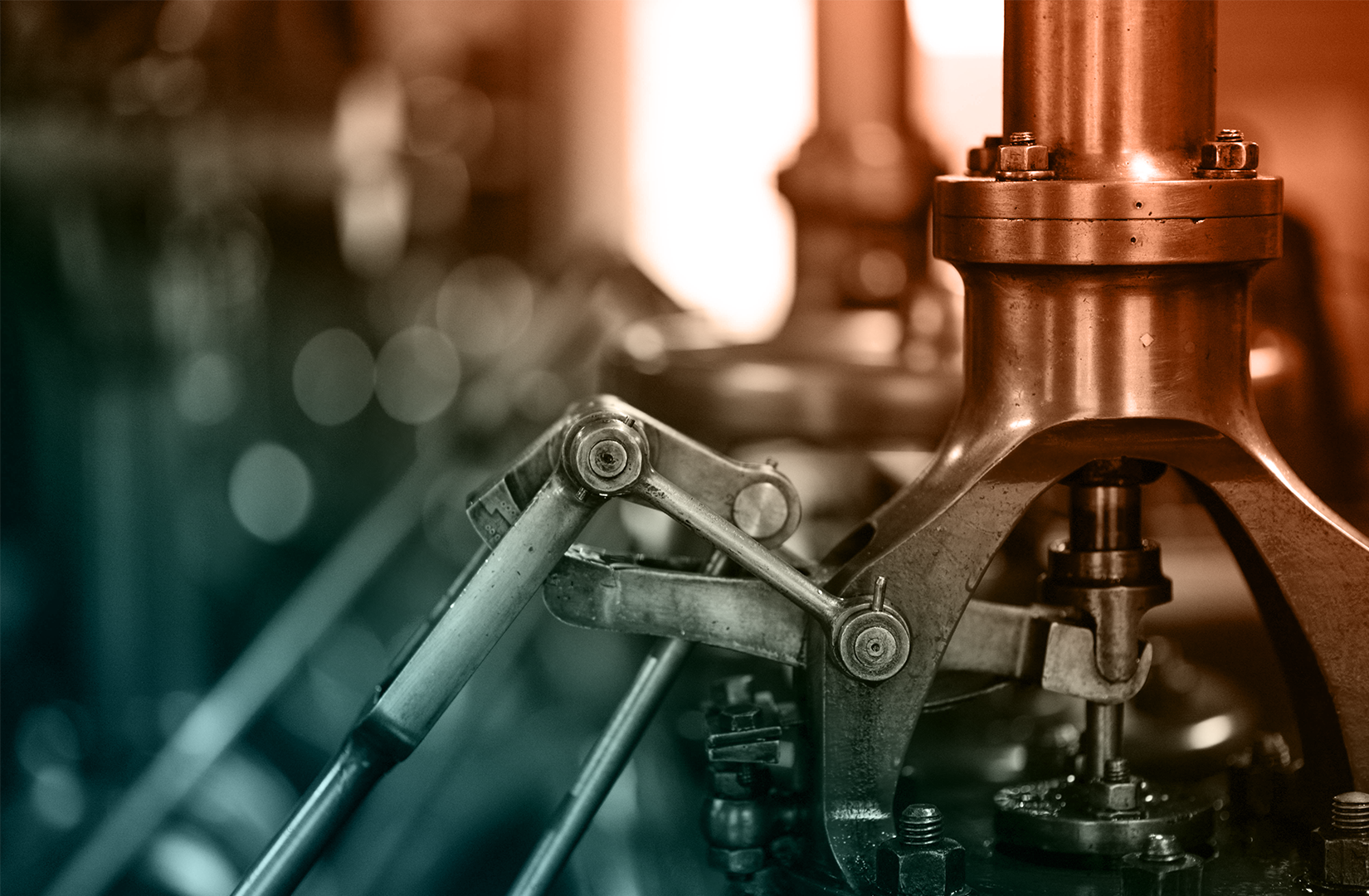