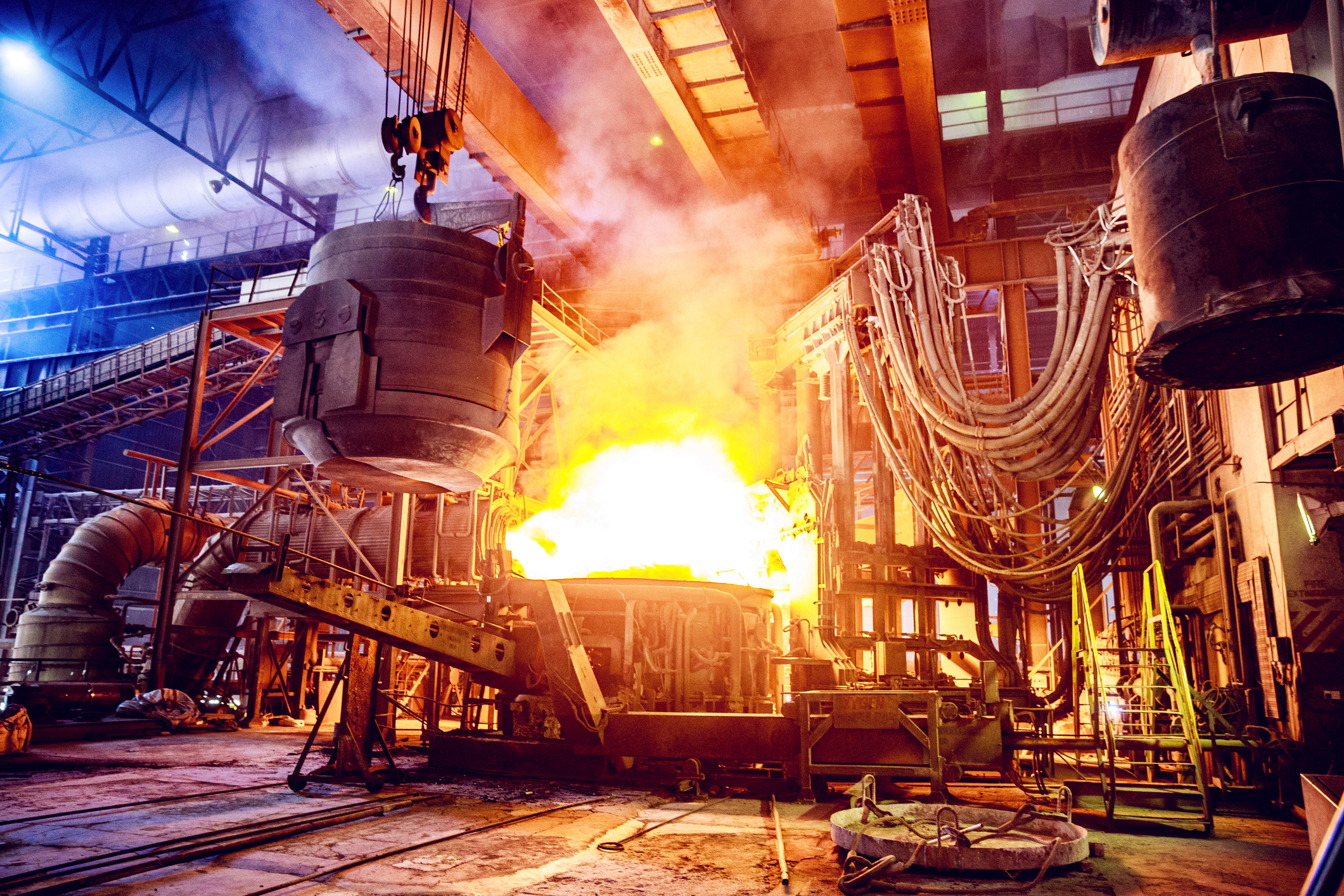
O-rings - Details, Selection, Installation, & Maintenance
O-rings are one of the most commonly used sealing components in various industries due to their simple yet effective design. These doughnut-shaped seals are used to block the passage of liquids or gases in various applications, making them indispensable in a wide range of mechanical systems. This page explores the features, common applications, types, and manufacturing options for O-rings, as well as essential guidelines for selection, installation, and maintenance.
Canrez® FFKM and Kalrez® O-rings, gasket rapid manufacturing, & custom molded parts are available now!
Check with one of Canyon’s helpful product engineers for an expert material and manufacturing recommendation.
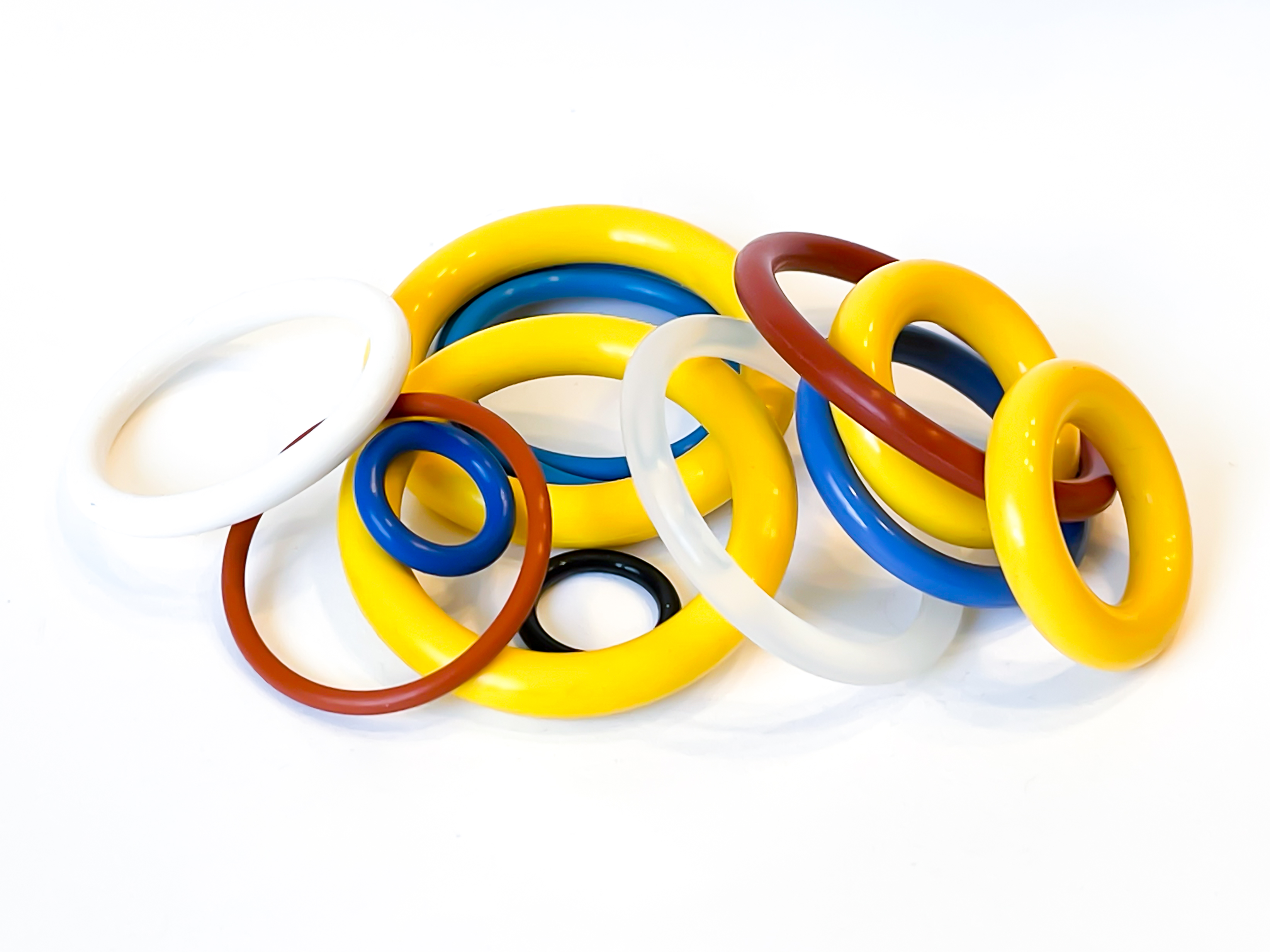
O-Ring Size Charts
USA AS568 O-ring Standard Size Chart
AS568 is one of the most common O-ring sizing standards.
Japanese JIS O-ring Standard Size Chart
JIS B 2401 is a common Japanese O-ring sizing standard.
International Metric O-ring Standard Size Chart
Metric is one of the most common O-ring sizing standards.
Materials Available
This table shows many of our standard materials and links out to our O-ring store. Get in touch with us if you need a custom gasket, custom molded part, or non-standard geometry!
Filter by
Temperature Search (°C)
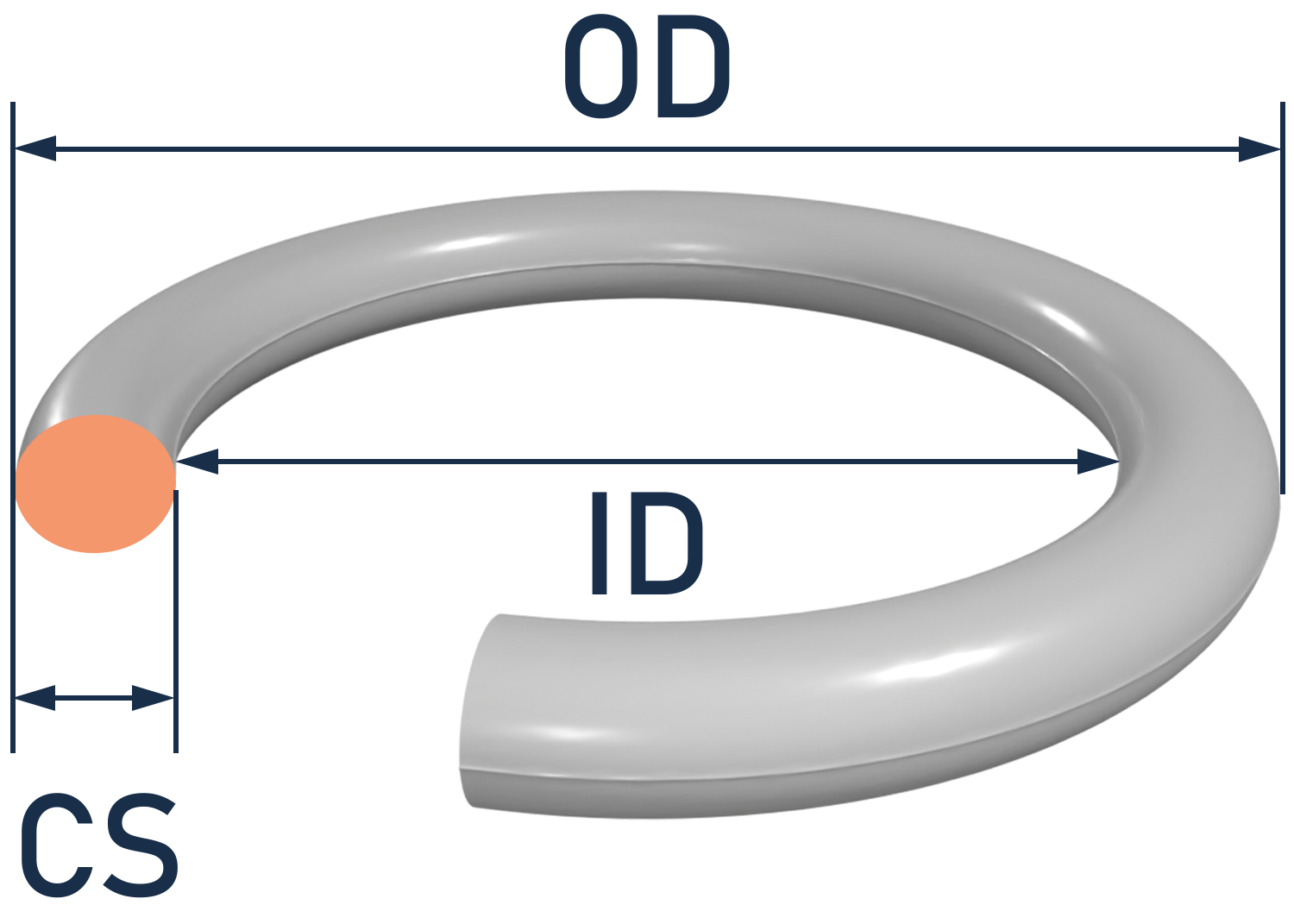
Features of O-Rings
O-rings offer several key features that make them popular in various industries:
- Versatility: O-rings can be used in both static and dynamic applications, making them suitable for a wide range of sealing needs.
- Durability: Made from robust materials, O-rings are designed to withstand extreme pressures, temperatures, and chemical exposure.
- Cost-Effective: Their simple design makes O-rings relatively inexpensive to produce, contributing to their widespread use.
- Easy Installation: O-rings are straightforward to install, often requiring minimal tools or expertise.
- Reliable Sealing: When properly installed, O-rings provide a highly reliable seal, reducing the risk of leaks and system failures.
Common Applications of O-Rings
O-rings are used across various industries due to their adaptability and effectiveness. Some of the most common applications include:
- Automotive Industry: O-rings are used in engines, transmissions, and other automotive systems to prevent fluid leaks and maintain pressure.
- Aerospace: In aircraft systems, O-rings help ensure the safe containment of fluids and gases under extreme conditions.
- Medical Devices: O-rings are found in medical equipment like syringes, pumps, and valves, ensuring the integrity of sensitive systems.
- Hydraulics and Pneumatics: These seals are essential in hydraulic cylinders, pumps, and pneumatic systems to prevent fluid or air leakage.
- Plumbing: O-rings are commonly used in faucets, pipes, and valves to provide a watertight seal.
Please consult a Canyon Components Engineer about your specific application and we will use our decades of experience to formulate a solution that fits your need.
Get a Quote Now!
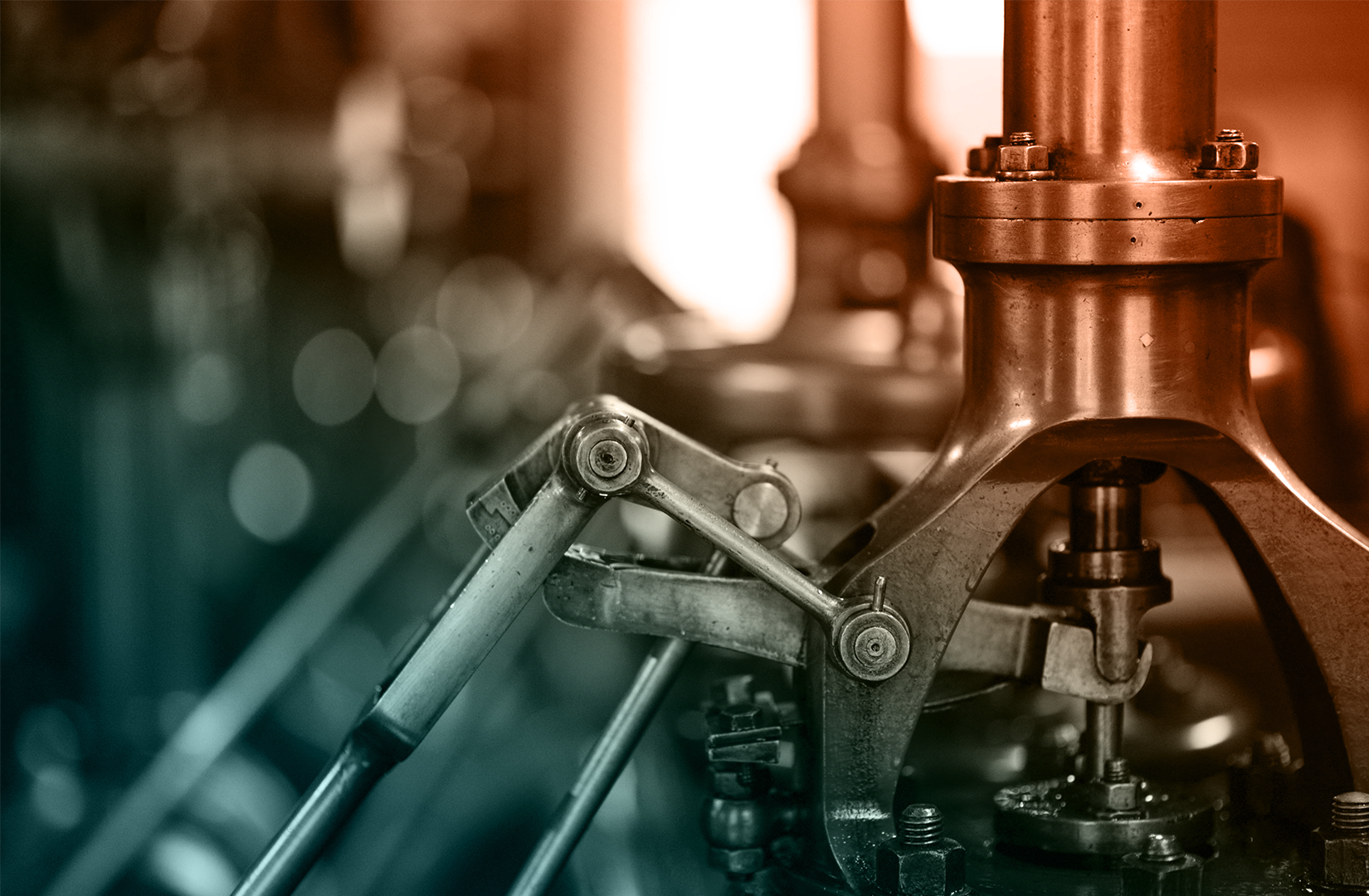
Types of O-Rings
Canrez® FFKM Perfluoroelastomer
Extreme temperatures & chemicals require extreme solutions! Canrez® FFKM materials offer extreme reliability where you need it most! Thousands of sizes in stock now!
CanGuard™ RFI & EMI Shielding Materials
CanGuard™ materials have been developed to offer superior sealing solutions with enhanced electromagnetic interference (EMI) shielding and radio frequency interference (RFI) shielding.
Kalrez® FFKM Perfluoroelastomer
Canyon Components offers Kalrez® Perfluoroelastomer (FFKM) O-rings, gaskets, & custom molded parts at competitive prices and with great lead-times.
Parker® O-rings, Parofluor parts, parker FKM Viton
Canyon Components offers Parker Hannifin® O-rings, Gaskets, Perfluoroelastomer (FFKM) parts, & custom molded parts at competitive prices and with great lead-times.
FKM (Viton®, Fluorocarbon)
FKM compounds, O-rings, gaskets, & custom molded parts exhibit excellent mechanical attributes as well as excellent resistance to high temperatures, mineral oil, ozone, fuels, hydraulic fluids, and many other solvents and chemicals.
Aflas® (TFE/P)
TFE/P (Aflas) compounds, O-rings, gaskets, & custom molded parts gives high resistance to steam, hot water, atmospheric wear, and many chemicals. TFE/P compounds provide superior performance in water, steam and virtually all caustic chemicals.
Fluorosilicone (FVMQ)
The mechanical and physical properties of Fluorosilicone O-rings, gaskets, & custom molded parts are very similar to silicone. Fluorosilicone O-rings, gaskets, & custom molded parts offer improved flexibility and strength, better resistance to fuels and mineral oil, but reduced hot air resistance.
Silicone (VMQ, PVMQ)
Silicone seals, O-rings, gaskets, & custom molded parts are excellent for extreme temperatures in static applications. Canyon Components carries a range of silicone materials, and we are happy to custom tailor a seal to meet your application requirements!
EPDM (Ethylene Propylene)
EPDM materials, O-rings, gaskets, & custom molded parts can operate over a wide temperature range, and are compatible with glycol fluids that cause problems for most typical elastomeric seals.
NBR (Nitrile, Buna-N)
Nitrile O-rings, gaskets, & custom molded parts are very oil-resistant, have strong mechanical properties, are resistant to wear, and are relatively inexpensive. These properties make Nitrile the most commonly used general purpose O-ring, gasket, & custom molded part material.
HNBR (Hydrogenated Nitrile)
Hydrogenated Nitrile O-rings, gaskets, & custom molded parts offer higher strength and reduced degradation at high temperatures compared to conventional Nitrile materials. These properties make HNBR materials popular in the oil and gas industry, as well as many applications in the chemical industry.
XNBR (Carboxylated Nitrile)
XNBR O-rings, gaskets, & custom molded parts are similar to Nitrile, but the backbone has been chemically modified with a Carboxylic Acid group. The resulting elastomer is a Nitrile rubber with outstanding abrasion and chemical resistance, superior to that of traditional Nitrile.
Neoprene (CR)
Chloroprene was the first synthetic rubber, and was developed commercially under the name Neoprene®. Chloroprene rubbers, O-rings, gaskets, & custom molded parts contain Chlorine in the polymer to reduce the reactivity to many oxidizing agents, as well as to oil and flame.
Polyurethane (PU, AU)
Polyurethane O-rings, gaskets, & custom molded parts generally have two or three times greater tensile strength and wear resistance than Nitrile and comparable polymers. Polyurethane also provides excellent permeation resistance when compared to most rubbers.
PTFE Encapsulated
FEP and PFA encapsulated O-rings consist of an elastomeric core and a seamlessly closed casing of modified PTFE. The elastomer core of encapsulated O-rings is typically made of FKM (Viton) or VMQ (silicone) and guarantees a uniform pre-tensioning at the sealing point.
PTFE O-Rings
The harshest environments require specialized solutions. Often times, a Canyon Components PTFE O-rings are used in harsh chemical environments. Polytetrafluoroethylene, commonly known as PTFE or Teflon®, is a high-performance fluoropolymer known for its exceptional chemical resistance, low friction, and non-stick properties.
Product Types
Custom Parts
Here at Canyon Components, we make sure to offer our customers any manufacturing technique they desire. Whether your O-rings, gaskets, & custom molded parts be rubber, plastic, or metal, rest assured that Canyon Components can make it!
Gaskets & Custom Cutting
Whether your custom cut parts be rubber, plastic, sponge, composite, or metal, rest assured that Canyon Components can make it! Canyon Components strives to meet all customer service requests. If you need something that isn't listed, feel free to contact a Canyon Components product and application consultant.
Infinite "Giant" Diameter O-Rings
By either Continuous Molding O-rings, or Splice & Vulcanizing O-rings, Canyon can provide mold-less, infinitely large O-rings at competitive prices!
Specialty Compliances
Canyon have materials available for O-rings, gaskets, & custom parts with compliances ranging from USP Class VI <87> & <88> for medical applications, to FDA CFR 21.177.2600 grades A through F for different food types, to the various drinking water specifications like KTW and NSF. Whether it's metal, rubber, or plastic, Canyon can meet your needs!
Please consult a Canyon Components Engineer about your specific application and we will use our decades of experience to formulate a solution that fits your need.
Manufacturing Options for O-Rings
O-rings can be manufactured through various methods, each offering different advantages depending on the application.
Canyon Components strives to meet all customer service requests. Feel free to contact Canyon Components engineering and let our knowledgeable staff help you design the perfect part for your needs.
Injection Molding
This process involves injecting molten material into a mold, making it ideal for producing large quantities of O-rings with consistent quality.
Compression Molding
Compression molding uses heat and pressure to shape O-rings from raw material, offering a cost-effective solution for smaller production runs.
Splice & Vulcanized
For custom-sized O-rings, extrusion followed by cutting to length and splice & vulcanization is a common method, allowing for a high degree of customization.
Transfer Molding
This method combines elements of both compression and injection molding, providing more precise control over the final product's shape and material distribution.
Die Cutting
For flat O-rings or gaskets, die-cutting from sheets of material can be an efficient and cost-effective manufacturing option.
O-Ring Selection, Installation, and Maintenance
O-rings are a fundamental component in various mechanical systems, providing reliable sealing solutions for a wide range of applications. By understanding the features, types, and manufacturing options available, along with proper selection, installation, and maintenance practices, you can ensure the optimal performance and longevity of O-rings in your specific application. Whether you're working in automotive, aerospace, medical, or industrial sectors, O-rings offer the versatility and durability required to keep systems running smoothly.
Canyon Components strives to meet all customer service requests. Feel free to contact Canyon Components engineering and let our knowledgeable staff help you design the perfect part for your needs.
Selection of O-Rings
Selecting the right O-ring for your application is crucial to ensure optimal performance and longevity. Consider the following factors during selection:
- Material Compatibility: Choose an O-ring material that is compatible with the fluids or gases it will encounter. For example, Nitrile is suitable for oil-based fluids, while Viton is better for high-temperature and chemical applications.
- Temperature Range: Ensure the O-ring material can withstand the operating temperature range of your system.
- Pressure Rating: Select an O-ring that can handle the pressure levels in your application to prevent deformation or failure.
- Size and Fit: Proper sizing is essential. An O-ring that is too large or too small can lead to leaks or premature wear.
- Application Type: Determine if the O-ring will be used in a static or dynamic application, as this will influence material and design choices.
Installation of O-Rings
Proper installation is critical to the effectiveness of O-rings. Follow these guidelines to ensure a correct installation:
- Inspect the O-Ring: Before installation, inspect the O-ring for any defects, such as nicks, cuts, or deformations.
- Use Lubrication: Apply a compatible lubricant to the O-ring to reduce friction during installation and prevent damage to the seal.
- Avoid Overstretching: Do not overstretch the O-ring during installation, as this can cause it to lose its shape and sealing effectiveness.
- Align Properly: Ensure the O-ring is properly seated in the groove and that it is not twisted or pinched.
- Use Installation Tools: When necessary, use specialized installation tools to avoid damaging the O-ring.
Maintenance of O-Rings
Regular maintenance of O-rings can extend their lifespan and prevent system failures. Consider the following maintenance practices:
- Regular Inspections: Periodically inspect O-rings for signs of wear, cracking, or deformation. Replace any O-rings that show signs of damage.
- Monitor Operating Conditions: Ensure that the system’s operating conditions, such as pressure, temperature, and chemical exposure, remain within the O-ring’s specified limits.
- Clean Regularly: Keep the O-rings and surrounding components clean to prevent debris from causing wear or damage.
- Use the Right Lubricants: Maintain proper lubrication to reduce friction and wear on the O-ring during operation.
- Replace as Needed: Even with proper maintenance, O-rings will eventually wear out. Replace them according to the manufacturer’s recommended intervals or when signs of failure are evident.
Back to Products Hub
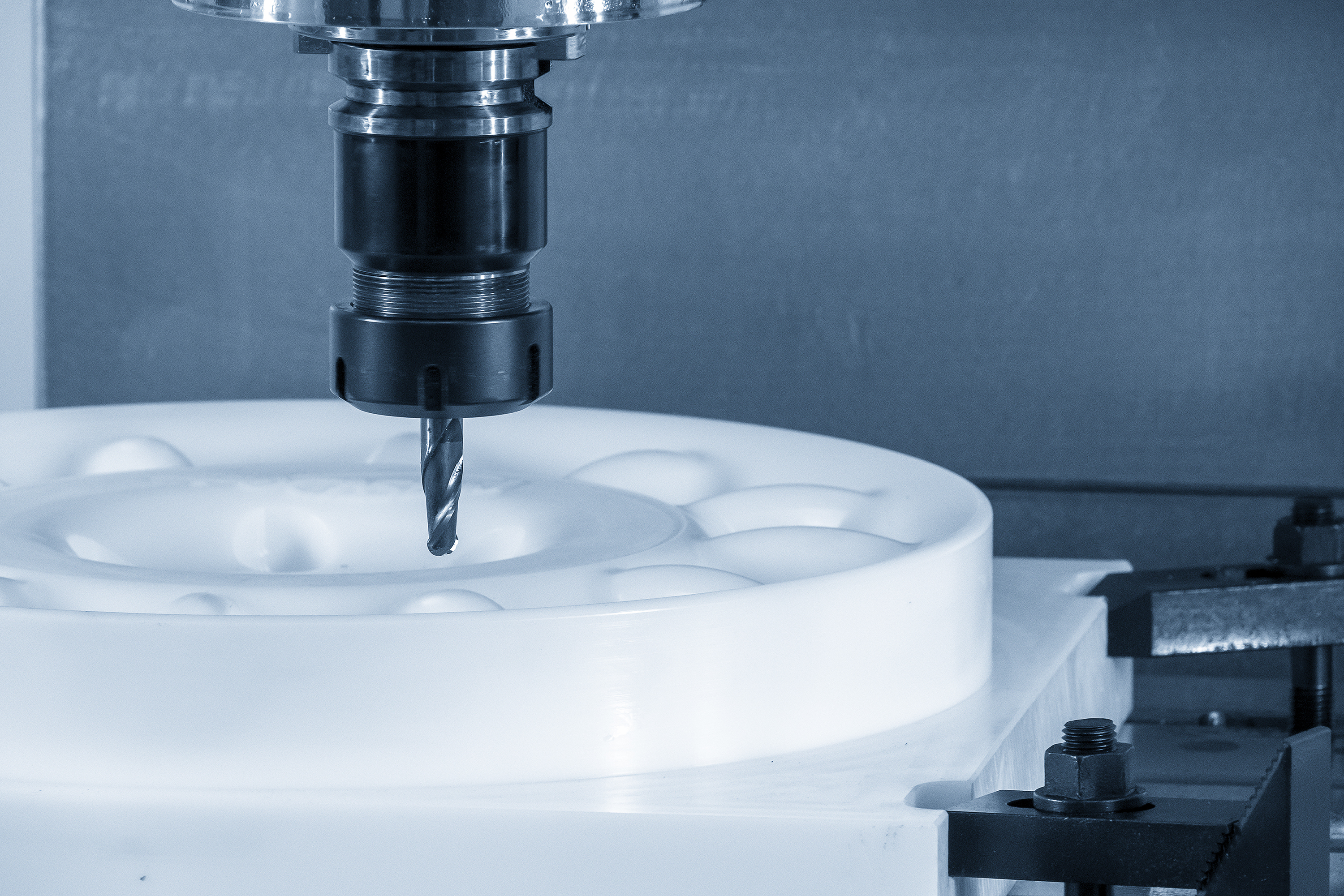
Get A Quote Now!
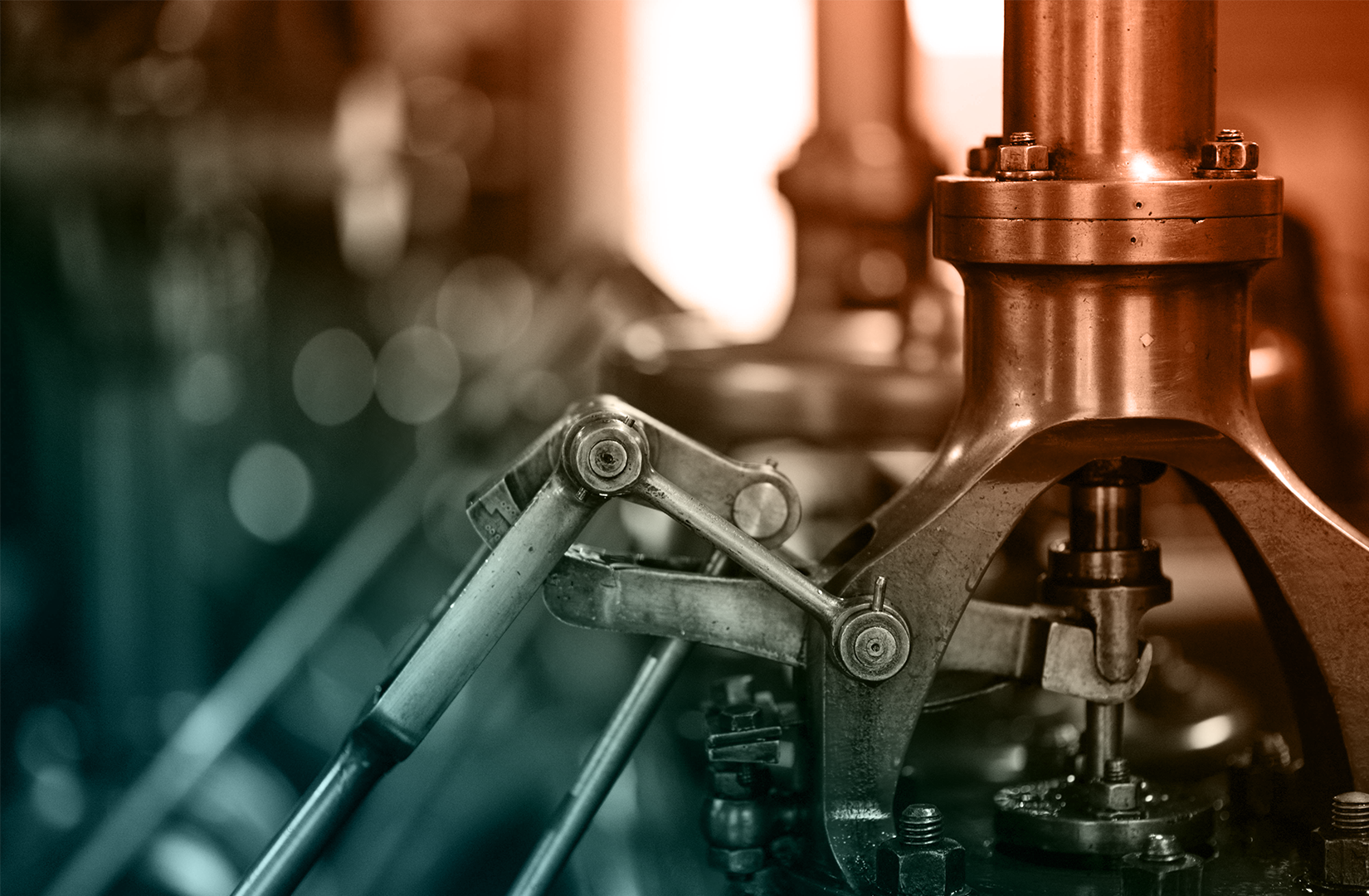