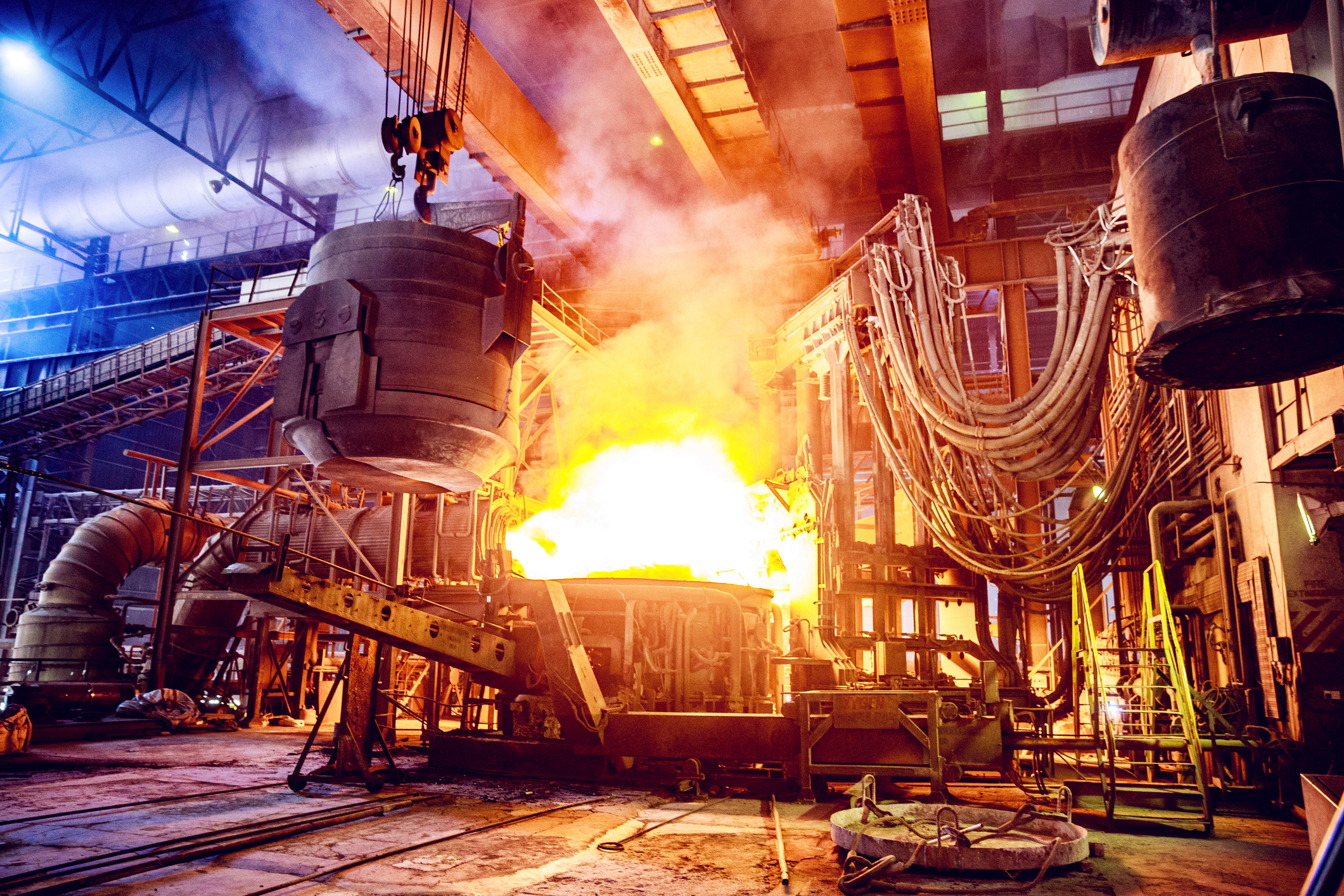
O-Ring Failures: Descriptions, Causes, and Prevention
O-ring failures can lead to leaks, equipment malfunctions, and costly downtime across various industries. Understanding the types of failures, their causes, and prevention methods is essential for ensuring long-lasting performance and optimal sealing in any application. This guide covers common O-ring failure modes, including abrasion, explosive decompression, chemical damage, compression set, extrusion, and more, offering insights into how to mitigate these issues.
Whatever your O-ring sizing requirements may be, Canyon Components can support you! If you can't find the O-ring size you need, or if you require something custom, feel free to get in touch with our engineers.
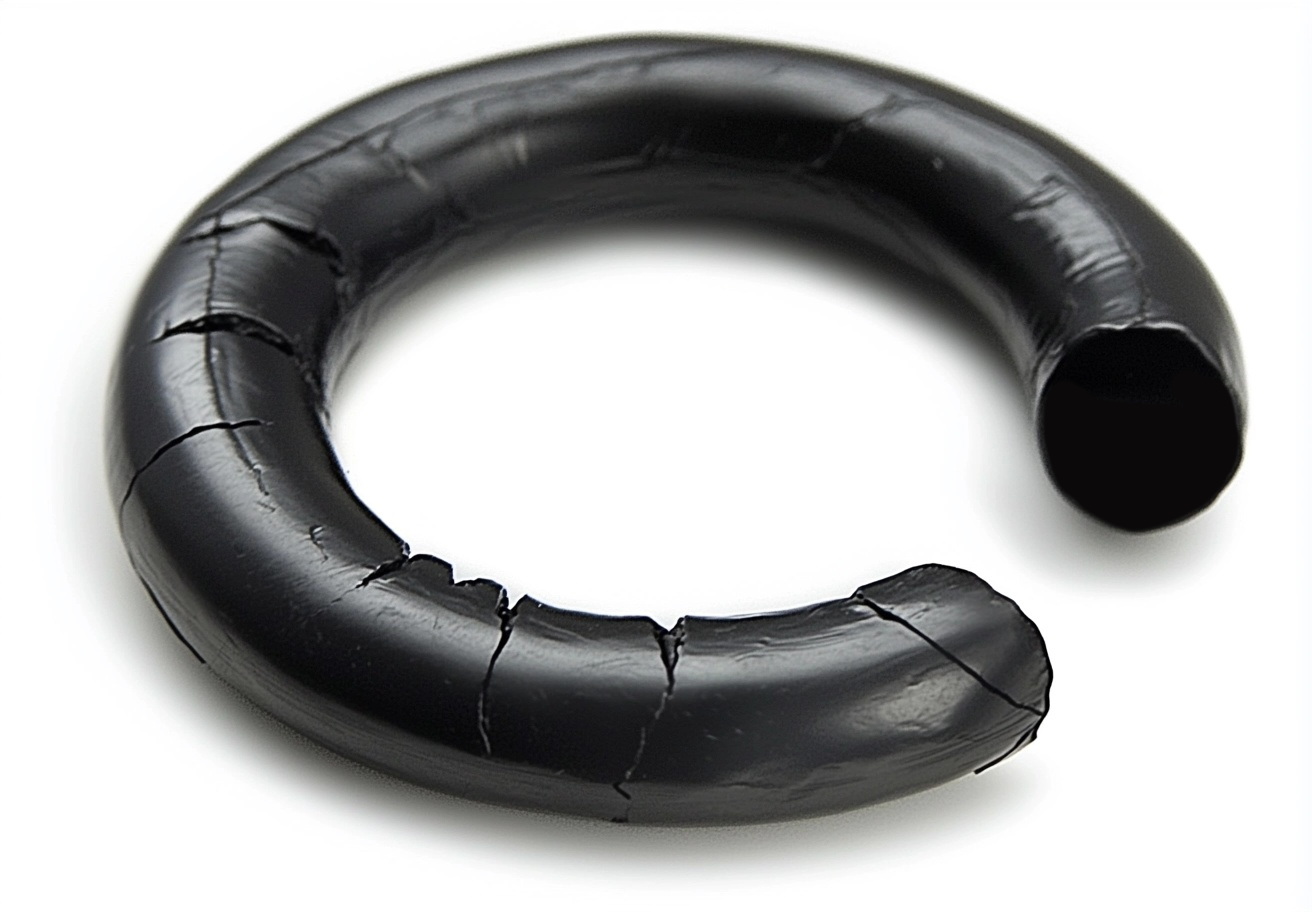
Table of Contents
Abrasion
Description:
Abrasion refers to the gradual wearing away or erosion of an O-ring's surface, usually caused by consistent rubbing, sliding, or friction against other surfaces. This type of damage manifests as visible surface wear or thinning, which can eventually lead to O-ring failure and leakage if not addressed.
If you have any questions, feel free to reach out to the Canyon Components engineering team.
Causes:
Abrasion commonly occurs in dynamic applications, like dynamic rod & piston applications or rotary applications, where the O-ring is in constant contact with moving parts, such as pistons, shafts, or other sliding components. Some primary causes include:
- Inadequate Lubrication: Insufficient lubrication increases friction, accelerating wear on the O-ring surface as it moves against metal or other materials.
- Rough or Damaged Surfaces: Surfaces with imperfections, burrs, or sharp edges can cause immediate damage and accelerated abrasion of the O-ring.
- Incorrect O-Ring Material Selection: Using an O-ring material with low abrasion resistance in high-friction applications leads to faster wear. Softer elastomers, for instance, are more susceptible to abrasion compared to materials engineered for durability.
- Misalignment: Misalignment between the moving and stationary parts increases uneven contact on the O-ring, leading to concentrated wear areas and eventual failure.
Signs of Abrasion:
- Visible surface wear, especially on the part of the O-ring in contact with other surfaces.
- Flaking, thinning, or pitted areas on the O-ring surface.
- Rough texture or reduced diameter where the O-ring makes contact.
Prevention:
Abrasion can be minimized by taking these precautions:
- Select Abrasion-Resistant Materials: Use elastomers with high abrasion resistance, such as Nitrile (NBR), polyurethane, or Viton, which can withstand dynamic friction better than softer materials.
- Proper Lubrication: Applying the correct external lubricant or using materials with internal lubrication reduces friction and prevents direct contact between the O-ring and other surfaces, extending the O-ring’s lifespan.
- Smooth Contact Surfaces: Ensure that surfaces in contact with the O-ring are smooth and free from rough edges, burrs, or sharp points that could damage the elastomer. Learn more about the surface finish recommendations for dynamic rod & piston applications and rotary applications.
- Correct Alignment: Verify alignment of moving parts to reduce uneven contact and wear on the O-ring.
- Regular Inspection and Maintenance: Routine checks for wear and tear help identify early signs of abrasion, enabling timely O-ring replacement before failure occurs.
Recommended Materials for Abrasion Resistance:
- Polyurethane (PU): Known for its exceptional resistance to wear and tear, polyurethane is ideal for dynamic applications with heavy-duty requirements.
- Nitrile (NBR): Often used in hydraulic systems, NBR offers good abrasion resistance and is compatible with oils and lubricants.
- FKM (Viton): Provides excellent resistance to wear, as well as chemical and high-temperature resilience, making it suitable for extreme environments.
Abrasion can be a significant factor in O-ring performance, particularly in dynamic applications where maintaining seal integrity is critical. By selecting appropriate materials, ensuring proper installation, and implementing preventive maintenance, O-ring abrasion can be effectively managed, resulting in longer-lasting seals and reduced downtime.
If you have any questions, feel free to reach out to the Canyon Components engineering team.
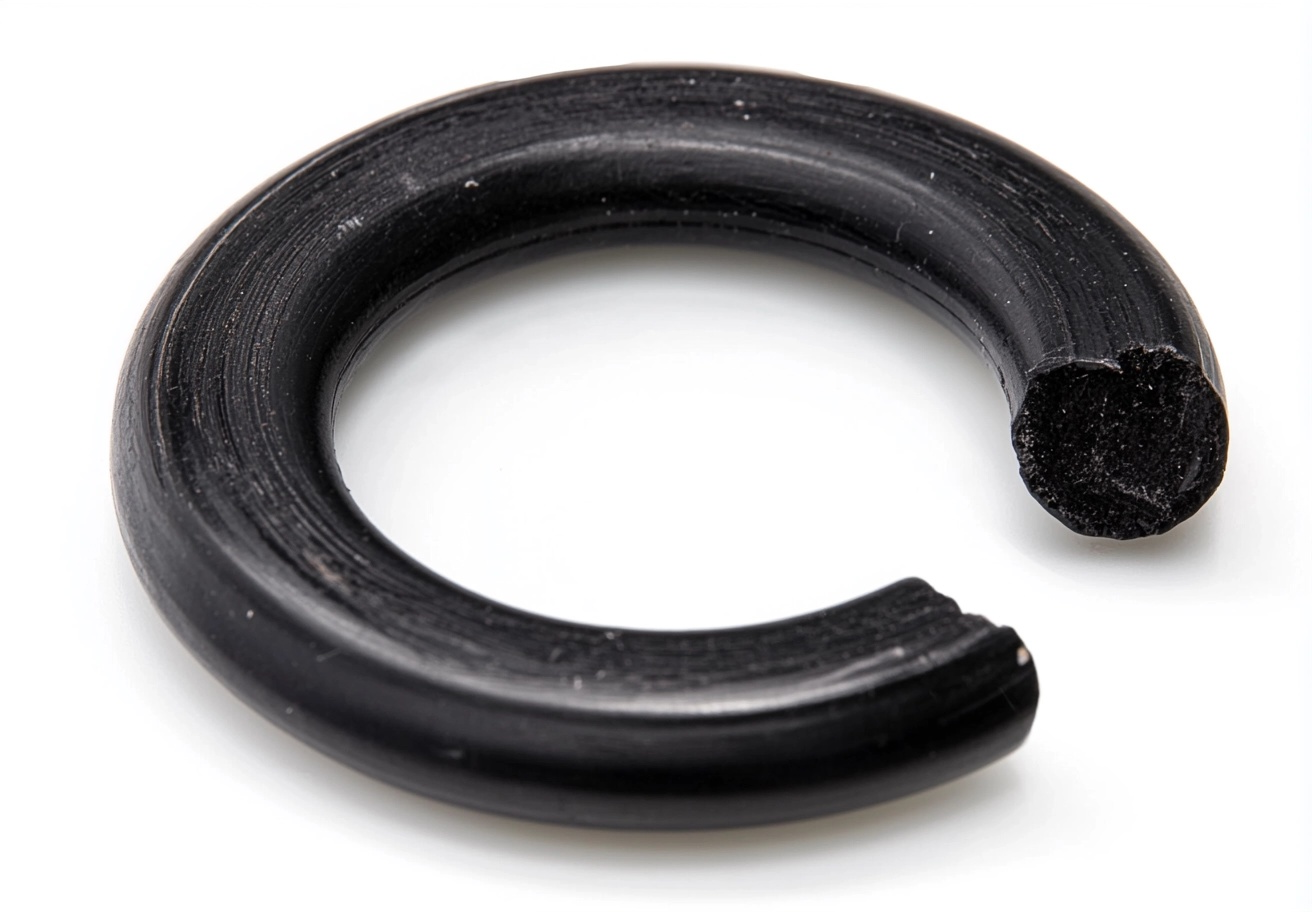
* The failure depicted in this image is intentionally exaggerated to highlight damage details, making it easy to recognize common O-ring failure modes for quick reference.
If you have any questions, feel free to reach out to the Canyon Components engineering team.
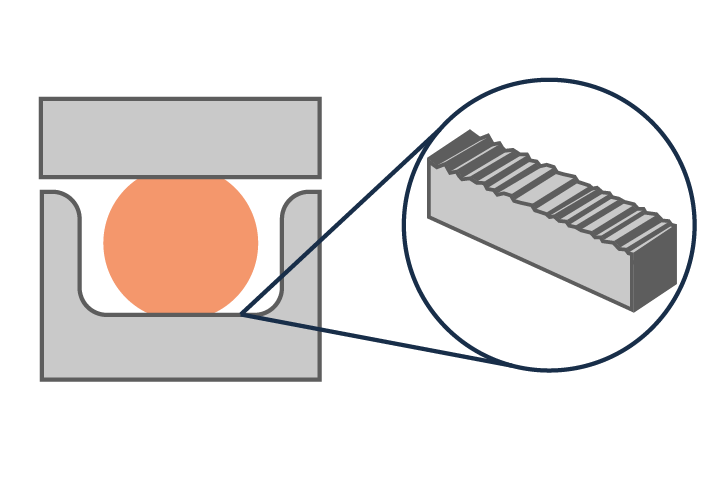
Chemical Damage
Description:
Chemical damage occurs when an O-ring is exposed to incompatible chemicals, causing the material to degrade, swell, crack, or soften. This degradation weakens the O-ring’s structure, compromising its ability to form an effective seal and eventually leading to leakage or complete failure. Chemical damage is often irreversible and, if left unchecked, can result in significant system issues and maintenance costs.
If you have any questions, feel free to reach out to the Canyon Components engineering team.
Causes:
Chemical damage arises when elastomer materials react with fluids, gases, or chemicals they are not resistant to. The most common causes include:
- Incompatibility with Chemical Environment: Each elastomer has specific chemical compatibilities; exposure to substances outside these limits can lead to rapid material breakdown.
- High Concentrations of Aggressive Chemicals: Strong acids, alkalis, or solvents can attack certain elastomers, breaking down their molecular structure.
- High-Temperature Reactions: Elevated temperatures often accelerate chemical reactions, intensifying the impact on O-ring materials.
- Absorption of Fluids: Some chemicals cause elastomers to swell by absorbing fluid, altering the O-ring’s shape and reducing its elasticity.
- Environmental Exposure: External factors, such as exposure to UV light, oxygen, or ozone, can chemically alter certain elastomers, increasing susceptibility to chemical attack.
Signs of Chemical Damage:
- Swelling or Expansion: The O-ring may expand, lose elasticity, or take on a gummy texture, making it difficult to fit within grooves.
- Cracking and Brittleness: The O-ring may become hard, brittle, and develop visible cracks or splits due to chemical exposure.
- Surface Erosion or Pitting: Chemicals may erode the O-ring surface, creating a rough or pitted texture that compromises sealing capabilities.
- Discoloration: Chemical reactions often change the color of the elastomer, indicating potential degradation.
Prevention:
Avoiding chemical damage involves careful material selection and preventive measures:
- Select Compatible Materials: Choose O-ring materials that match the chemical environment of the application. For instance, Canrez® FFKM (perfluoroelastomer) and FKM (Viton) offer excellent resistance to aggressive chemicals, while EPDM is suitable for water and steam applications.
- Consult Chemical Compatibility Charts: Use reference guides to verify the compatibility of specific elastomers with chemicals involved in the application.
- Avoid High-Temperature Chemical Exposure: Where possible, lower the temperature to slow down or prevent chemical reactions that degrade the O-ring material.
- Use Protective Coatings: Certain coatings, like parylene, can enhance chemical resistance and protect O-rings from aggressive substances, extending service life in challenging environments.
- Regular Inspection: Periodic checks for swelling, cracking, or discoloration help identify early signs of chemical damage, allowing for timely replacement.
Recommended Materials for Chemical Resistance:
- FFKM (Perfluoroelastomer): FFKM materials like Canrez®, Kalrez®, and Chemraz®, offer the highest chemical resistance, capable of withstanding exposure to strong acids, solvents, and other aggressive chemicals.
- FKM (Viton): Known for its resistance to hydrocarbons, oils, and many chemicals, FKM is widely used in demanding industrial applications.
- EPDM (Ethylene Propylene Diene Monomer): Resistant to water, steam, and many alkalis, EPDM is ideal for applications involving water-based chemicals.
- PTFE (Polytetrafluoroethylene): PTFE offers multiple types of sealing solutions, like spring energized seals and PTFE encapsulated seals. Though not a traditional elastomer, PTFE provides excellent chemical resistance and is often used in severe chemical environments.
- Aflas (TFE/P): Aflas combines resistance to heat, chemicals, and amines, making it suitable for applications involving aggressive chemicals and high-temperature environments.
- Fluorosilicone: Combines silicone’s flexibility with enhanced chemical resistance, making it ideal for applications requiring both UV and chemical resilience, especially in aerospace and fuel handling.
Chemical damage can severely impact O-ring performance and is one of the most challenging failure modes to address. By carefully selecting materials suited to the specific chemicals in the environment and regularly inspecting O-rings for early signs of damage, you can ensure reliable performance and longer service life for sealing components.
If you have any questions, feel free to reach out to the Canyon Components engineering team.
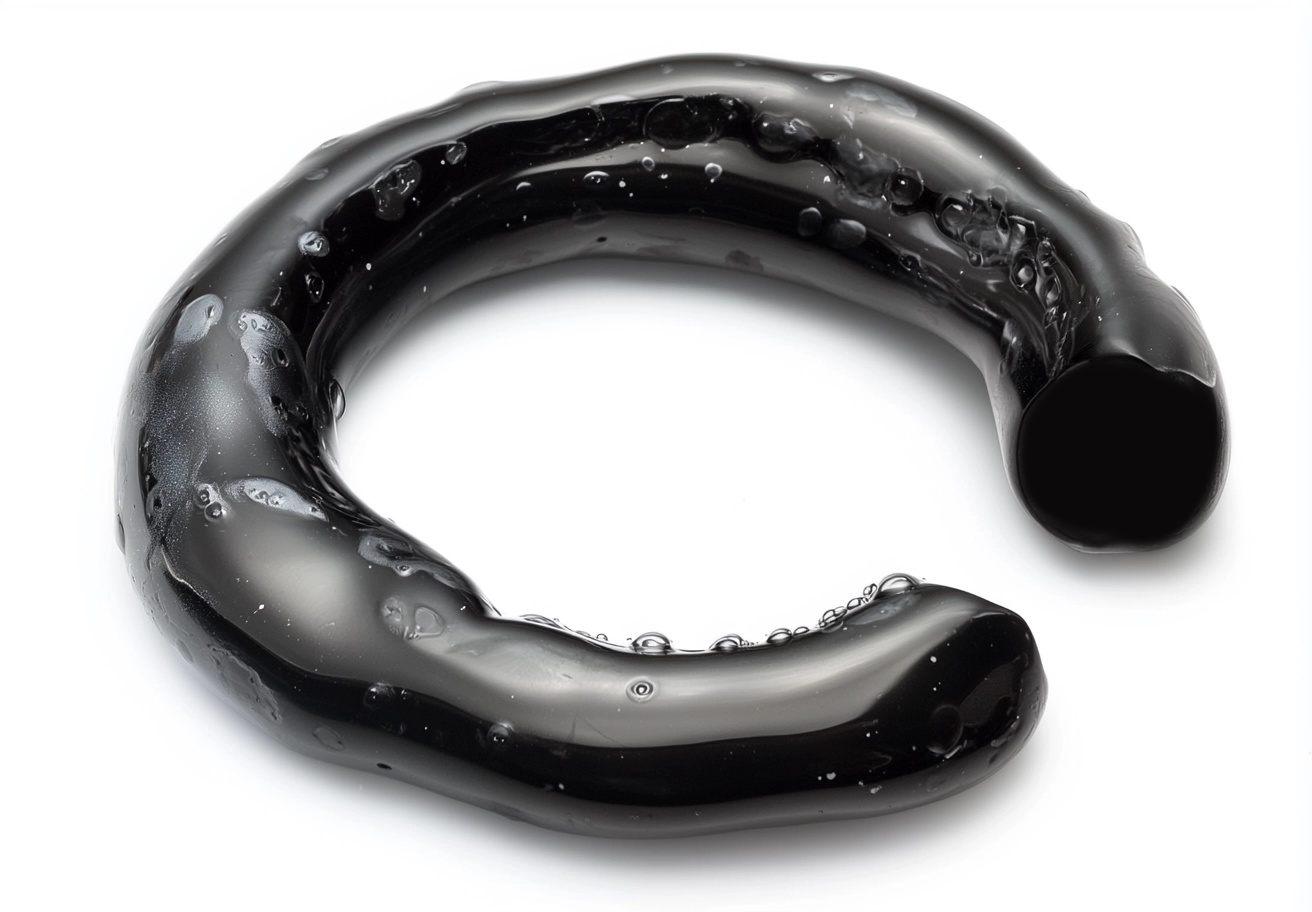
* The failure depicted in this image is intentionally exaggerated to highlight damage details, making it easy to recognize common O-ring failure modes for quick reference.
If you have any questions, feel free to reach out to the Canyon Components engineering team.
Compression Set
Description:
Compression set is the permanent deformation of an O-ring after prolonged compression, causing it to lose its original shape and elasticity. When an O-ring experiences compression set failure, it no longer fully rebounds to fill the sealing gap, leading to potential leaks and seal failure. This issue is especially critical in static seals, where the O-ring’s ability to maintain contact pressure is essential for reliable sealing.
If you have any questions, feel free to reach out to the Canyon Components engineering team.
Causes:
Compression set results from several factors, most often related to the O-ring’s material properties and operating environment:
- Extended Compression Time: O-rings compressed for long periods can take on a flattened shape, making it difficult for them to rebound when the load is released.
- High Temperatures: Heat accelerates the loss of elasticity in elastomers, making O-rings more susceptible to compression set.
- Chemical Exposure: Certain chemicals can alter the molecular structure of the elastomer, reducing its ability to rebound and increasing compression set risk.
- Material Hardness and Quality: Softer materials or those with poor resilience are more prone to compression set, particularly under prolonged or high-pressure conditions.
- Over-Compression: Applying too much force on an O-ring during installation or in operation can cause excessive flattening, leading to compression set over time.
- Aging and Material Fatigue: As elastomers age, they lose elasticity and become more prone to compression set, particularly when exposed to UV light, oxygen, or ozone.
Signs of Compression Set:
- Flattened Cross-Section: The O-ring may appear flattened or misshapen, particularly in the areas where it was compressed.
- Loss of Elasticity: The O-ring may not spring back to its original shape when removed, indicating a permanent deformation.
- Leaks and Seal Failure: In applications, compression set often leads to leaks as the O-ring can no longer effectively fill the sealing gap.
Prevention:
To minimize compression set and extend O-ring life, consider these preventive measures:
- Select Low Compression Set Materials: Use materials with low compression set properties, such as silicone, fluorocarbon (FKM), or certain grades of EPDM, especially in high-temperature or prolonged compression applications.
- Control Operating Temperature: Where possible, reduce the operating temperature, as heat is a major contributor to compression set. Alternatively, use heat-resistant materials to prevent deformation.
- Avoid Over-Compression: Ensure that O-rings are installed with the correct level of compression. Manufacturers typically recommend a compression range of 20-30% for most applications.
- Use Backup Rings in High-Pressure Applications: Backup rings help prevent over-compression and extrusion in high-pressure applications, especially in hydraulic systems.
- Periodic Inspection and Replacement: Regularly inspect O-rings in critical applications and replace them before compression set leads to failure, especially in high-pressure or high-temperature environments.
Recommended Materials for Low Compression Set:
- FFKM (Perfluoroelastomer): FFKM materials like Canrez®, Kalrez®, and Chemraz® are known for its outstanding resistance to both extreme temperatures and aggressive chemicals, FFKM provides superior compression set performance in high-demand environments such as chemical processing and aerospace.
- Silicone: Known for its low compression set and high-temperature resistance, silicone is ideal for applications requiring consistent elasticity over time.
- FKM (Viton): Viton has excellent compression set resistance, making it suitable for applications involving high temperatures and chemical exposure.
- HNBR (Hydrogenated Nitrile): HNBR combines excellent wear resistance with low compression set, particularly useful in oil and gas or automotive applications.
- EPDM: With its low compression set and resistance to water and steam, EPDM performs well in applications where temperature fluctuations occur.
Compression set is a common issue that can severely impact sealing performance, particularly in static applications where maintaining a reliable seal over time is critical. By selecting materials with low compression set characteristics, controlling compression levels, and performing routine maintenance, compression set can be effectively managed, ensuring that O-rings continue to perform reliably over their intended service life.
If you have any questions, feel free to reach out to the Canyon Components engineering team.
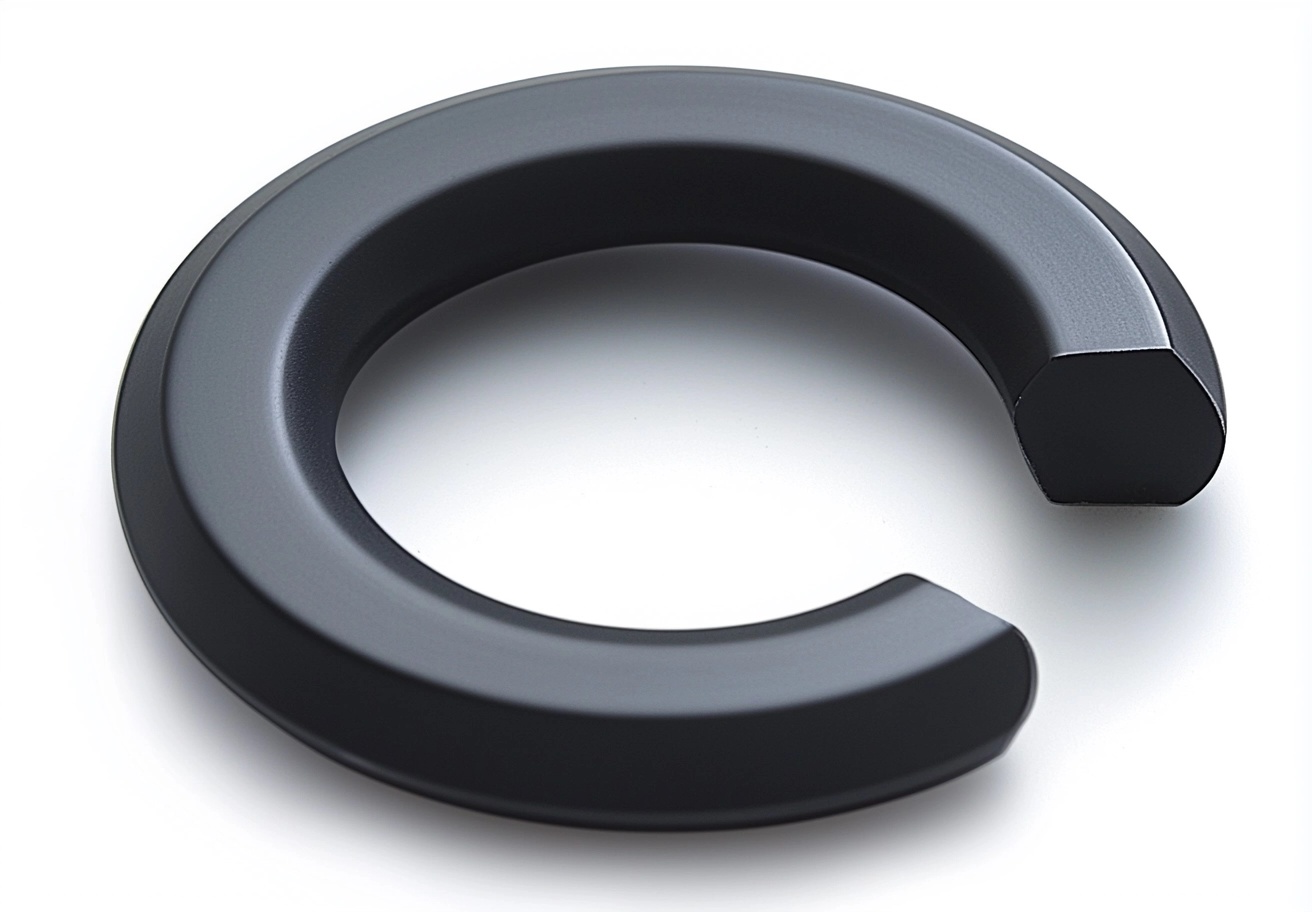
* The failure depicted in this image is intentionally exaggerated to highlight damage details, making it easy to recognize common O-ring failure modes for quick reference.
If you have any questions, feel free to reach out to the Canyon Components engineering team.
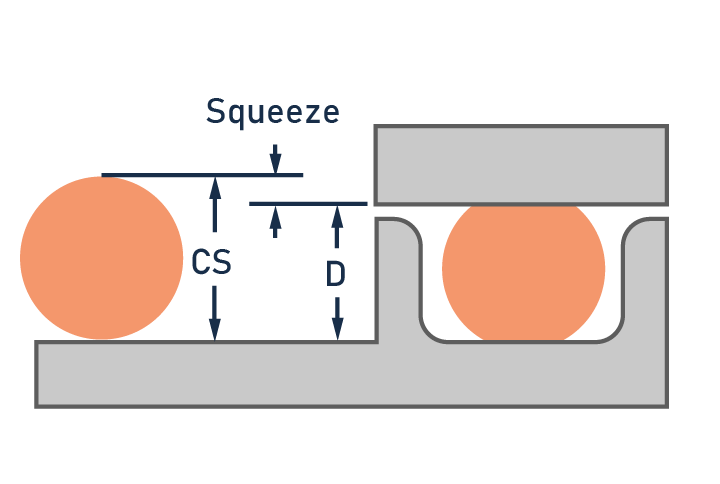
Explosive Decompression
Description:
Explosive decompression, also known as rapid gas decompression (RGD), occurs when an O-ring is exposed to high-pressure gas (frequently carbon dioxide (CO2)) that rapidly expands upon pressure release. When the pressure is suddenly lowered, gases trapped within the elastomer expand, creating internal stresses that cause the O-ring to blister, crack, or even rupture. This type of failure is common in high-pressure applications involving gas, such as in oil and gas, aerospace, and industrial equipment.
If you have any questions, feel free to reach out to the Canyon Components engineering team.
Causes:
Explosive decompression occurs due to a combination of high-pressure gas exposure, rapid decompression, and specific material properties:
- High-Pressure Gas Exposure: When O-rings are exposed to gases like nitrogen, carbon dioxide, or natural gas at high pressures, these gases permeate the elastomer over time.
- Rapid Pressure Drop: A sudden decrease in pressure forces the absorbed gases to expand quickly within the elastomer. If the gas cannot escape quickly enough, it creates internal ruptures or blisters.
Signs of Explosive Decompression:
- Surface Blistering: Visible blisters or bubbles appear on the O-ring surface, often accompanied by raised or pitted areas.
- Cracks and Ruptures: Internal cracks may form, leading to surface tears or complete breakage of the O-ring.
- Reduced Elasticity: The O-ring may lose its flexibility and become hard or brittle, making it more prone to additional mechanical failure.
Prevention:
Preventing explosive decompression requires careful material selection, pressure control, and operational practices:
- Select RGD-Resistant Materials: Choose elastomers specifically rated for resistance to rapid gas decompression (RGD), also known as anti-explosive decompression (AED). This includes materials tested to NORSOK M-710, NACE TM0297, and API 6A. Canyon offers many types of materials tested to these standards, such as HNBR (Hydrogenated Nitrile Butadiene Rubber), FKM (Viton), or certain perfluoroelastomers (FFKM), which are formulated to withstand high-pressure gas exposure.
- Control Pressure Release Rate: Implement gradual decompression protocols to allow gases to escape from the O-ring material slowly, reducing the chance of internal damage.
- Use Backup Rings: In certain applications, backup rings can help stabilize the O-ring, preventing excessive deformation during pressure fluctuations.
- Regular Inspection and Replacement: Periodically inspect O-rings in high-pressure gas environments and replace them if any signs of decompression damage are observed. Scheduled replacement can help avoid sudden failures.
- Material Hardness and Durometer: Use O-rings with a higher hardness rating (durometer), as these are often more resistant to gas permeation and explosive decompression.
Recommended Materials for Explosive Decompression Resistance:
- FFKM (Perfluoroelastomer): Certain RGD compounds of FFKM materials like Canrez®, Kalrez®, and Chemraz® offer outstanding resistance to explosive decompression and chemical exposure, making them suitable for extreme environments in oil and gas or chemical processing.
- HNBR (Hydrogenated Nitrile): Known for its high resistance to gases, RGD HNBR performs well in applications where RGD risk is high, such as oilfield equipment and high-pressure gas applications.
- FKM (Viton): With excellent chemical and thermal resistance, RGD Viton provides resilience against rapid decompression, particularly in high-temperature environments.
- Aflas®: RGD Aflas elastomers exhibit high resistance to explosive decompression, especially in applications involving amine-based gas sweetening and high-pressure conditions.
Industries and Applications Prone to Explosive Decompression:
- Oil and Gas Industry: RGD-resistant O-rings are used in downhole tools, blowout preventers, and wellhead equipment where rapid pressure fluctuations are common.
- Aerospace and Aviation: Components in fuel systems, cabin pressurization equipment, and oxygen systems often require RGD-resistant seals to handle pressure changes during ascent and descent.
- Compressed Gas Systems: Industrial equipment, such as compressors and valves, that handle high-pressure gas often require O-rings capable of withstanding explosive decompression.
- Hydraulic and Pneumatic Systems: High-pressure hydraulic and pneumatic systems that use gases or gas mixtures in control valves or actuators also face RGD risks.
Explosive decompression can significantly compromise sealing integrity, resulting in leaks or catastrophic failure. By selecting compatible, RGD-resistant materials, managing pressure release, and employing best practices in equipment design and operation, you can greatly reduce the risk of this type of O-ring failure and ensure more reliable, long-lasting sealing performance in high-pressure applications.
If you have any questions, feel free to reach out to the Canyon Components engineering team.
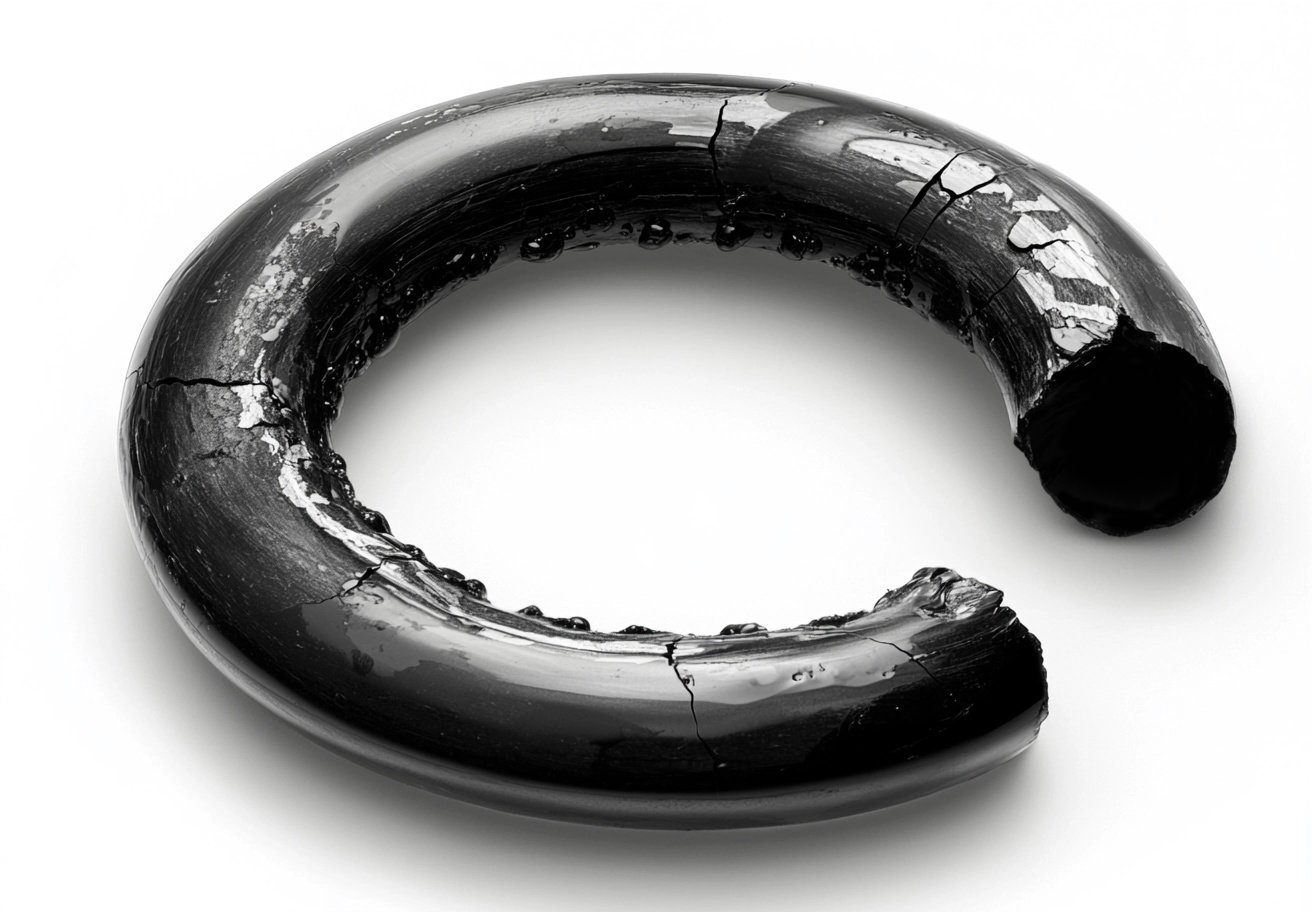
* The failure depicted in this image is intentionally exaggerated to highlight damage details, making it easy to recognize common O-ring failure modes for quick reference.
If you have any questions, feel free to reach out to the Canyon Components engineering team.
Extrusion Damage
Description:
Extrusion damage occurs when an O-ring is forced into the clearance gap between mating surfaces under high pressure, causing parts of the O-ring material to be pinched, torn, or even cut away. This issue is especially prevalent in high-pressure applications where O-rings are exposed to forces that push them out of their grooves. Over time, extrusion damage can lead to leaks, seal failure, and increased wear on system components.
If you have any questions, feel free to reach out to the Canyon Components engineering team.
Causes:
Extrusion damage results from a combination of factors, including high pressures, poor groove design, material incompatibility, and temperature fluctuations:
- High Operating Pressures: When pressure exceeds the O-ring’s ability to withstand deformation, it may push part of the O-ring into the clearance gap between components, leading to pinching or tearing.
- Excessive Clearance Gap: Large gaps between components provide space for the O-ring material to extrude. Clearance gaps should be minimized, especially in high-pressure systems, to reduce extrusion risk.
- Incorrect Material Selection: Soft or low-durometer materials are more prone to extrusion under pressure than harder compounds, making material choice critical for high-pressure applications.
- Temperature Variations: Heat can soften elastomers, making them more susceptible to extrusion. In extreme cold, elastomers may lose flexibility, leading to brittleness and increased risk of extrusion damage.
- Dynamic Applications: In applications with reciprocating or rotating motion, the O-ring may be subjected to additional stress, increasing the risk of extrusion and wear.
Signs of Extrusion Damage:
- Nibbling or Tearing on Edges: Extrusion damage is often visible as small, jagged tears or “nibbles” along the edges of the O-ring.
- Elongated or Distorted Shape: The O-ring may appear elongated, flattened, or distorted due to the repeated pressure that pushes it into the clearance gap.
- Localized Deformation: Extrusion damage is typically found on one side of the O-ring, where it makes contact with the gap, indicating that pressure has forced part of the material out.
Prevention:
Preventing extrusion damage involves careful attention to design, material selection, and system parameters:
- Use Backup Rings: Installing backup rings adjacent to the O-ring helps prevent extrusion by blocking the clearance gap. Backup rings are particularly useful in high-pressure applications and are commonly made from hard materials like PTFE.
- Minimize Clearance Gaps: Designing smaller clearance gaps reduces the space available for the O-ring to extrude into, especially in high-pressure systems. Precision machining can help achieve this tight tolerance.
- Select Harder O-Ring Materials: Materials with higher hardness ratings (durometer) are less likely to extrude. Choosing elastomers such as FKM, HNBR, or polyurethane can enhance extrusion resistance.
- Control Operating Temperatures: Using heat-resistant materials in high-temperature applications helps maintain O-ring integrity and minimizes the risk of extrusion due to material softening. FFKM materials like Canrez®, Kalrez®, and Chemraz® are the typically the most resistant to thermal degredation.
- Avoid Over-Pressurizing: Ensuring that the system operates within the O-ring’s pressure rating helps prevent material from being forced out. Over-pressurization can quickly lead to extrusion damage, so pressure control is key.
Recommended Materials for Extrusion Resistance:
- FFKM (Perfluoroelastomer): 90 shore A durometer FFKM materials like Canrez®, Kalrez®, and Chemraz® offer exceptional extrusion resistance and withstands extreme temperatures and aggressive chemicals, making it ideal for demanding applications in chemical processing and high-pressure environments.
- HNBR (Hydrogenated Nitrile): Known for its toughness and resilience, 90 shore A durometer HNBR resists extrusion and performs well in high-pressure, high-temperature environments.
- FKM (Viton): 90 shore A durometer Viton is an excellent choice for applications that require high extrusion resistance and compatibility with chemicals and high temperatures.
- Polyurethane (PU): With outstanding mechanical strength and abrasion resistance, 90 shore A durometer polyurethane is commonly used in dynamic applications that require high extrusion resistance.
- EPDM: While not as tough as some other materials, 90 shore A durometer EPDM provides good extrusion resistance in applications involving water and steam, especially in lower-pressure systems.
Industries and Applications Prone to Extrusion Damage:
- Hydraulic Systems: Hydraulic cylinders, valves, and pumps often operate under high pressures, increasing the likelihood of extrusion. Backup rings are frequently used in these systems to protect O-rings.
- Oil and Gas: In drilling and production equipment, extrusion-resistant seals are essential for high-pressure applications, such as in wellheads and blowout preventers.
- Pneumatics: In pneumatic equipment, especially where high-pressure gas is involved, O-rings can face extrusion risks, requiring tight clearance control and robust materials.
- Aerospace and Defense: Aircraft hydraulic systems and control valves are often exposed to extreme pressures and require O-rings with exceptional extrusion resistance.
Extrusion damage can have severe implications for O-ring performance, leading to premature failure and equipment malfunctions. By selecting the right material, using backup rings, and ensuring proper system design, extrusion damage can be effectively prevented, resulting in reliable sealing performance even in high-pressure applications.
If you have any questions, feel free to reach out to the Canyon Components engineering team.
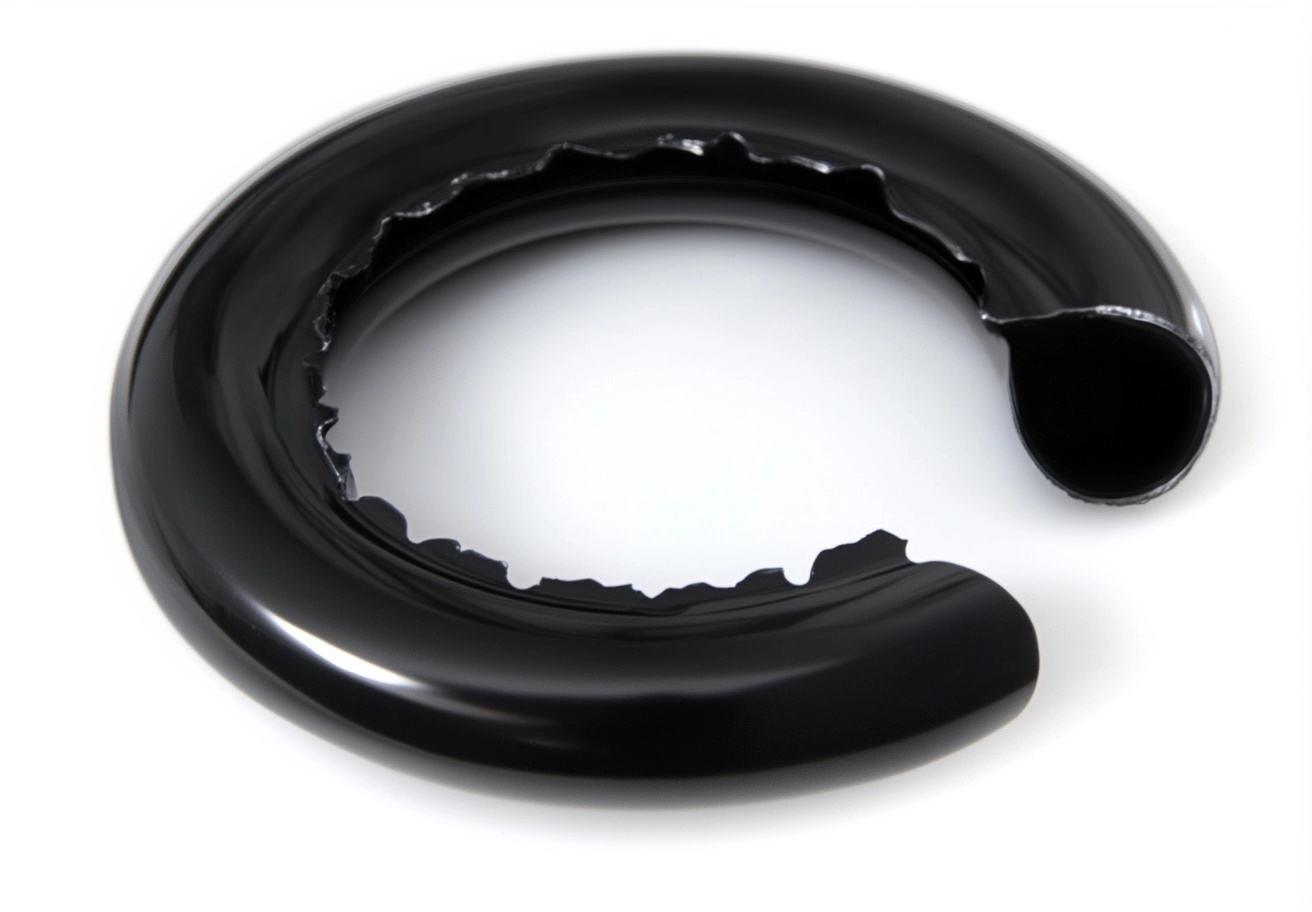
* The failure depicted in this image is intentionally exaggerated to highlight damage details, making it easy to recognize common O-ring failure modes for quick reference.
If you have any questions, feel free to reach out to the Canyon Components engineering team.
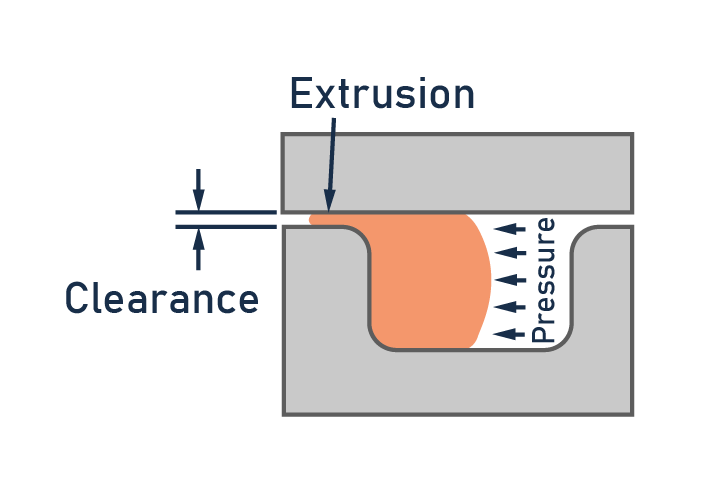
Installation Damage
Description:
Installation damage refers to physical harm that occurs to an O-ring during the process of installation, leading to cuts, nicks, overstretching, or distortion. Even minor installation damage can compromise an O-ring’s ability to create an effective seal, often resulting in leaks or early failure. Because O-rings are delicate components, especially when made from softer materials, careful handling during installation is crucial.
If you have any questions, feel free to reach out to the Canyon Components engineering team.
Causes:
Installation damage occurs due to a combination of handling errors, improper tools, and environmental factors. Key causes include:
- Improper Tooling: Sharp or pointed tools can cut or nick the O-ring during placement. Using the wrong tools can also increase the risk of overstretching or scratching.
- Overstretching: Elastomers have a limited stretch capacity, and pulling an O-ring too far can permanently deform or weaken the material, making it more prone to failure in use.
- Sharp Edges and Burrs: The presence of sharp edges, burrs, or rough surfaces on metal parts can tear or nick the O-ring as it’s installed, especially if it’s slid over threads or other irregular surfaces.
- Twisting or Spiraling: When installed improperly, an O-ring can twist or spiral within its groove, which can prevent it from sealing evenly and lead to premature wear or leaks.
- Insufficient Lubrication: Without adequate lubrication, friction during installation can stretch, twist, or damage the O-ring. Lubrication reduces resistance and helps the O-ring slide into place smoothly.
- Contamination: Dust, dirt, or oil contaminants can interfere with the installation process and potentially damage the O-ring surface, reducing its lifespan and effectiveness.
Signs of Installation Damage:
- Visible Cuts or Nicks: Small cuts, scratches, or nicks on the O-ring surface are often indicative of damage caused during installation.
- Deformation: An O-ring may show visible signs of deformation, such as elongation or flattening, which indicates that it was overstretched or twisted.
- Improper Fit: If the O-ring does not sit evenly in its groove or appears misaligned, it may have been damaged or distorted during installation.
- Leaks in Initial Operation: An O-ring damaged during installation may not seal effectively from the start, resulting in immediate leaks.
Prevention:
Preventing installation damage involves using proper techniques, tools, and materials to ensure that the O-ring is placed without harm:
- Use O-Ring-Specific Tools: Tools designed specifically for O-ring installation, such as plastic picks, blunt-ended tools, and angled tweezers, help prevent cutting or nicking the material.
- Avoid Overstretching: Only stretch the O-ring enough to fit over its groove or component and avoid pulling it more than necessary. As a rule of thumb, do not stretch an O-ring more than 50% of its inner diameter.
- Inspect Components for Sharp Edges: Smooth out any sharp edges, burrs, or threads that may come in contact with the O-ring during installation. This can be done with deburring tools or by adding a chamfered edge where the O-ring passes.
- Lubricate the O-Ring: Use materials with internal lubrication or apply a compatible external lubricant, such as a silicone or PTFE-based grease, to reduce friction and allow the O-ring to slide easily into place. Lubrication also helps to prevent twisting and increases the O-ring’s lifespan. Just be sure to utilize lubricant that is compatible with the O-ring material you are using.
- Implement Anti-Spiral Techniques: Ensure that the O-ring is not twisted or spiraled when placed in its groove. For dynamic applications, consider using X-rings or square rings, which resist spiral damage better than standard O-rings.
- Maintain a Clean Installation Environment: Keep the installation area and tools clean to avoid introducing dust or other contaminants onto the O-ring surface.
Recommended Materials for Damage Resistance:
- HNBR (Hydrogenated Nitrile): Known for its toughness and durability, HNBR is less prone to nicking or tearing, especially when properly lubricated.
- Silicone: Silicone is not relatively abrasion resistant. While softer and more delicate, silicone O-rings can be handled with care and benefit from lubrication during installation to avoid tearing.
- Polyurethane: With high resistance to cuts and abrasion, polyurethane is a durable choice for applications prone to handling and installation wear.
- Viton (FKM): Viton offers a good balance between flexibility and resistance to installation damage, performing well in high-temperature and chemical-resistant applications.
Industries and Applications Prone to Installation Damage:
- Automotive and Machinery Maintenance: Installing O-rings on threaded components or tight spaces in engines, pumps, and other machinery can lead to cuts or stretching if not done carefully.
- Hydraulics and Pneumatics: Hydraulic cylinders and pneumatic equipment often require precise seal installation. Any damage to the O-rings compromises the equipment’s pressure-handling capabilities.
- Oil and Gas: Applications involving high-pressure or chemically aggressive environments require careful installation to avoid damage, as these settings demand flawless sealing performance.
- Medical Devices: In medical equipment, where O-rings may be small and delicate, installation damage can impact the performance and longevity of the device, especially in fluid or pneumatic applications.
Proper handling and installation techniques are essential to prevent damage to O-rings, ensuring they maintain their sealing integrity and longevity. By selecting the right tools, using proper lubrication, and inspecting components before installation, you can effectively avoid installation damage and maximize the reliability and effectiveness of O-ring seals.
If you have any questions, feel free to reach out to the Canyon Components engineering team.
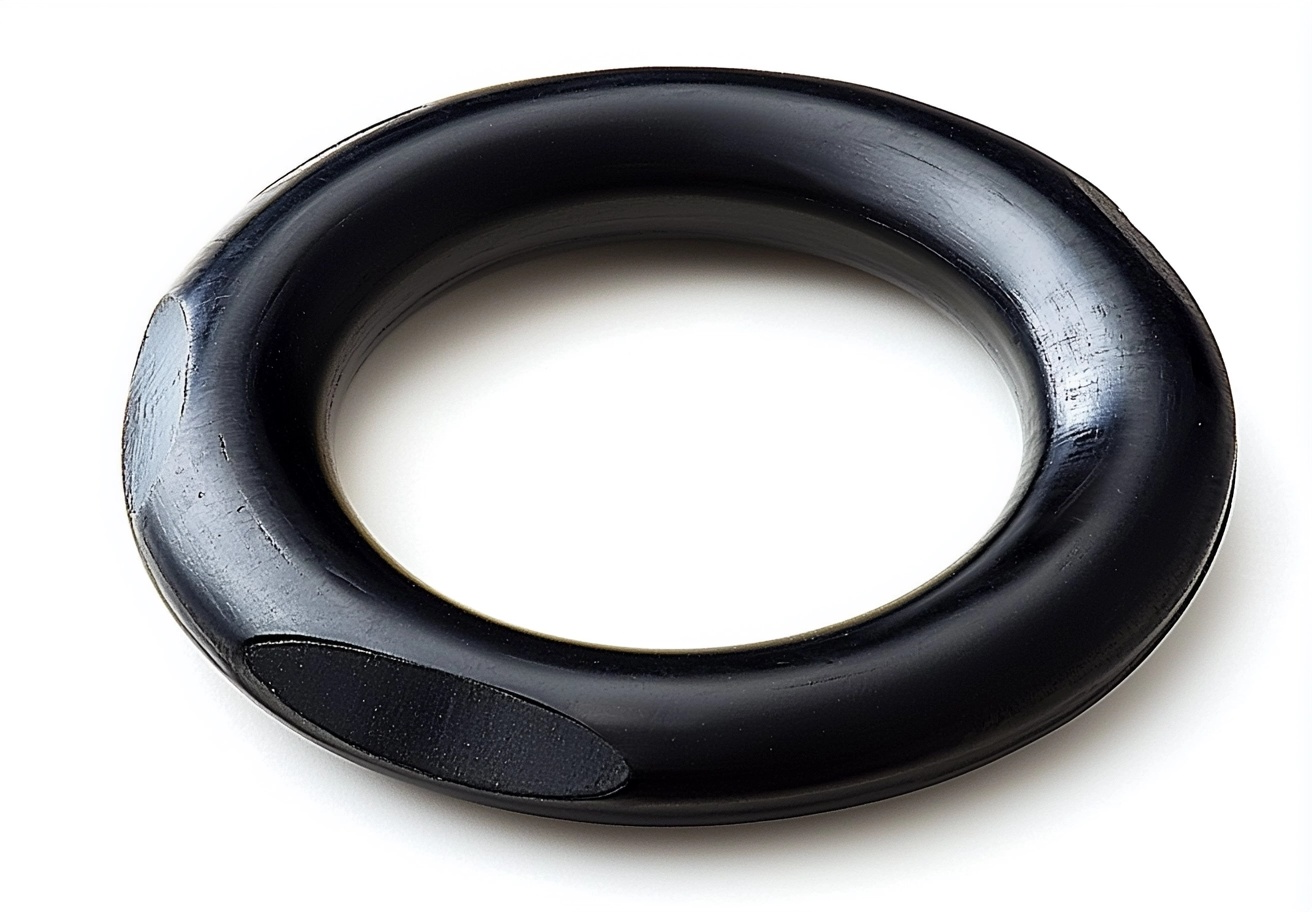
* The failure depicted in this image is intentionally exaggerated to highlight damage details, making it easy to recognize common O-ring failure modes for quick reference.
If you have any questions, feel free to reach out to the Canyon Components engineering team.
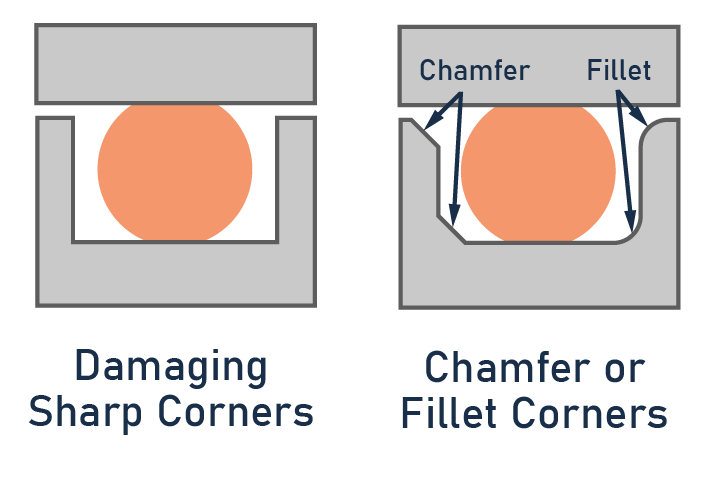
Outgassing
Description:
Outgassing is the release of volatile compounds trapped within an O-ring material, usually occurring in vacuum or high-temperature environments. These compounds, often byproducts from the curing or manufacturing process, gradually escape from the elastomer over time. In highly sanitary environments, outgassing can compromise the cleanliness of the surroundings, posing a significant risk in sensitive applications like aerospace, medical devices, electronics, and semiconductor manufacturing.
If you have any questions, feel free to reach out to the Canyon Components engineering team.
Causes:
Outgassing occurs due to environmental conditions and material composition, with several primary contributing factors:
- High Temperatures: Elevated temperatures accelerate the release of volatile compounds within the elastomer, increasing the outgassing rate.
- Vacuum Environments: In low-pressure or vacuum environments, outgassing is more pronounced as gases and volatiles escape more easily from the elastomer into the surrounding space.
- Material Formulation: Some elastomers contain plasticizers, curing agents, and additives that contribute to higher outgassing levels. Elastomers with lower cross-link density or less stable chemical bonds are more prone to outgassing.
- Manufacturing Residues: Volatile residues from the curing process or additives can remain in the elastomer if not adequately processed, releasing over time as the material ages or is exposed to extreme conditions.
- Moisture Saturation: It is also possible for moisture to permeate into microscopic voids within the molecular structure of elastomers. This moisture can then be pulled out of the material in vacuum environments, potentially causing contamination.
Signs of Outgassing:
- Film or Residue Buildup: Outgassing may produce a thin layer of residue on nearby components, compromising cleanliness, especially in optical or electronic applications.
- Loss of Seal Integrity: Outgassing can sometimes lead to slight volume loss in the O-ring, reducing its elasticity and compromising the seal over time.
- Presence of Particles or Bubbles: In some cases, small bubbles or particles may form on the O-ring’s surface, indicating volatile compound release.
Prevention:
Minimizing outgassing requires careful material selection, processing, and handling:
- Select Low-Outgassing Materials: Use materials specifically designed for low-outgassing properties, such as FKM (Viton), FFKM (perfluoroelastomers), and silicone formulations certified for low outgassing.
- Pre Vacuum Bake O-Rings: Pre vacuum baking O-rings at controlled temperatures helps release volatile compounds before installation, significantly reducing outgassing once the O-ring is in use. This is particularly useful for vacuum applications.
- Use Vacuum-Compatible Compounds: In applications like aerospace or semiconductor processing, select compounds that meet vacuum compatibility standards, as they are formulated to withstand low-pressure environments with minimal outgassing.
- Proper Storage and Handling: Store O-rings in a clean, controlled environment to avoid absorbing external contaminants, which can contribute to outgassing. Vacuum-sealed storage can help maintain cleanliness for applications requiring strict outgassing control.
- Avoid High-Temperature Exposures if Possible: For applications prone to outgassing, consider avoiding prolonged exposure to high temperatures and select materials that remain stable in such conditions.
Recommended Low-Outgassing Materials:
- FFKM (Perfluoroelastomer): FFKM materials like Canrez®, Kalrez®, and Chemraz® are engineered for ultra-low outgassing and high chemical resistance, making them ideal for high-purity applications in vacuums or high temperatures.
- FKM (Viton): Viton offers excellent outgassing resistance, particularly in high-temperature applications and environments where chemical resistance is required.
- Silicone: Certain low-outgassing silicone formulations, such as those approved by NASA or the European Space Agency, are ideal for aerospace and sensitive optical applications.
- EPDM: EPDM offers low outgassing properties, especially for water-based or low-pressure applications. It is a cost-effective alternative for less demanding low-outgassing applications.
Industries and Applications Prone to Outgassing:
- Aerospace and Vacuum Systems: In aerospace, vacuum systems, and space exploration, outgassing can interfere with sensitive instruments and cause contamination in low-pressure environments, affecting both equipment and data accuracy.
- Semiconductor Manufacturing: Outgassing is a major concern in semiconductor fabrication, where even minute contaminants can cause defects in chips or other components.
- Optics and Photonics: In optical applications, outgassing can lead to fogging or residue on lenses, mirrors, and other precision components, impacting optical performance.
- Electronics: Electronics require low-outgassing O-rings to avoid residue buildup on circuit boards and connections, which can disrupt performance and lead to short circuits.
- Medical Devices: Outgassing can release contaminants that affect sterilization processes or compromise the cleanliness of environments in medical devices and lab equipment.
Outgassing can significantly affect the performance and cleanliness of systems in sensitive applications, particularly those involving vacuums or high temperatures. By selecting low-outgassing materials, utilizing pre-baking, and following best practices for storage and installation, industries can minimize outgassing risks and ensure reliable, contamination-free performance of their O-ring seals.
If you have any questions, feel free to reach out to the Canyon Components engineering team.
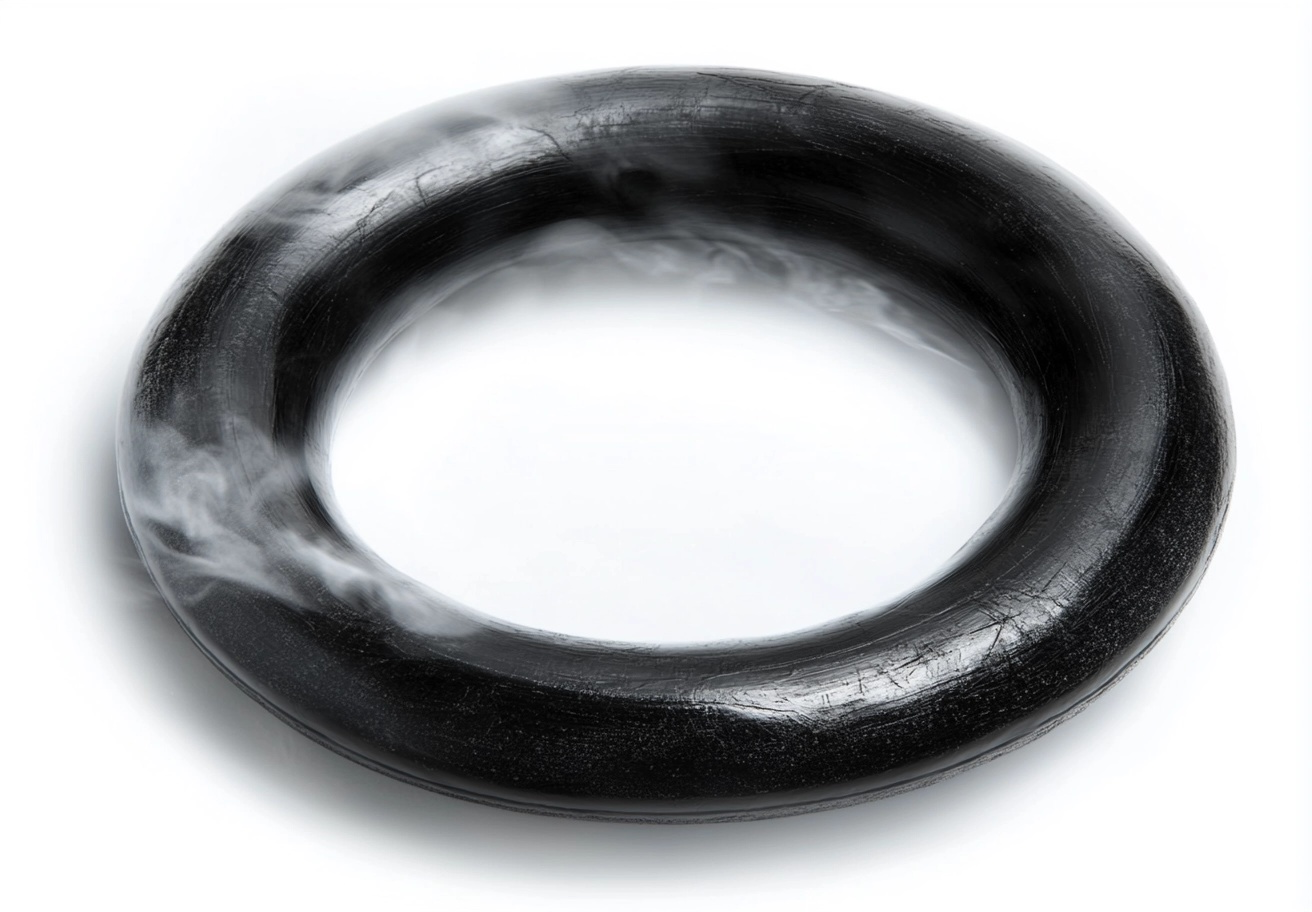
* The failure depicted in this image is intentionally exaggerated to highlight damage details, making it easy to recognize common O-ring failure modes for quick reference.
If you have any questions, feel free to reach out to the Canyon Components engineering team.
Over-Compression
Description:
Over-compression occurs when an O-ring is subjected to excessive compressive force, leading to permanent deformation, flattening, or even extrusion out of its groove. Over-compressed O-rings lose their elasticity, compromising their ability to maintain an effective seal and increasing the likelihood of leakage. This failure mode is common in both static and dynamic applications where improper compression or excessive tightening occurs.
If you have any questions, feel free to reach out to the Canyon Components engineering team.
Causes:
Over-compression can result from a range of installation and operational factors:
- Improper Installation: Excessive tightening of fasteners or applying more compression than recommended can flatten the O-ring, reducing its ability to maintain a proper seal.
- Incorrect Groove Design: Grooves that are too shallow or too narrow don’t provide enough space for the O-ring, leading to compression beyond the elastomer’s limits.
- Excessive Pressure: In high-pressure applications, the force exerted on the O-ring may cause it to deform beyond its capacity, especially if it’s not reinforced with backup rings.
- Wrong O-Ring Material: Some materials have limited resistance to deformation under compression. Using a softer or low-durometer elastomer in a high-pressure application can lead to over-compression.
- Thermal Expansion: Temperature fluctuations can cause materials to expand, increasing the compression force on the O-ring and potentially leading to over-compression if the O-ring is already compressed close to its maximum.
Signs of Over-Compression:
- Flattened Cross-Section: Over-compressed O-rings may appear flattened or squished, especially if they remain compressed for prolonged periods.
- Loss of Elasticity: The O-ring may lose its rebound ability, failing to return to its original shape when removed from the groove.
- Cracking and Hardening: Over-compression can cause some elastomers to harden and become brittle, resulting in cracks or splits over time.
- Leakage or Seal Failure: Over-compression often leads to seal failure, as the O-ring can no longer effectively seal against pressure changes or vibrations.
Prevention:
Avoiding over-compression requires careful attention to design specifications, installation practices, and material selection:
- Use the Correct Groove Dimensions: Ensure that groove depth and width are properly designed to accommodate the O-ring without excessive compression. Proper groove design prevents over-compression and provides room for the O-ring to expand under pressure without damage.
- Follow Compression Recommendations: Most O-ring manufacturers specify a recommended compression range. Sticking to these guidelines helps prevent over-compression and extends the O-ring’s life.
- Utilize Backup Rings for High-Pressure Applications: In high-pressure environments, backup rings support the O-ring and prevent it from deforming or extruding out of its groove.
- Choose the Right Material Hardness: Select a material with an appropriate durometer (hardness level) based on the application’s compression and pressure requirements. Harder materials withstand compression forces better, making them ideal for high-pressure scenarios.
- Avoid Over-Tightening: During installation, avoid overtightening bolts or fasteners, as this can increase compression forces on the O-ring beyond acceptable limits.
- Monitor Operating Temperature: For applications with temperature fluctuations, select materials that resist thermal expansion and maintain elasticity across temperature ranges. Thermal-resistant materials, such as FKM and EPDM, can help reduce the risk of over-compression caused by temperature changes.
Recommended Materials for Over-Compression Resistance:
- HNBR (Hydrogenated Nitrile): Known for its high strength and durability, HNBR performs well in high-pressure applications and maintains elasticity under compression.
- FKM (Viton): Viton has excellent compression resistance, making it suitable for high-temperature, high-pressure applications in industrial settings.
- EPDM: EPDM elastomers offer a balance of flexibility and resilience, performing well in both temperature-resistant and low-compression set applications.
- Polyurethane (PU): With high mechanical strength, polyurethane is particularly resistant to compression set, making it ideal for dynamic applications where high resistance to deformation is necessary.
Industries and Applications Prone to Over-Compression:
- Hydraulic Systems: Hydraulic systems that operate under high pressure, such as pumps and valves, often require precise compression control to prevent over-compression and seal failure.
- Automotive Sealing Applications: In automotive gaskets and seals, especially those exposed to high pressure and vibration, over-compression can lead to early failure. Following compression guidelines helps ensure durability in high-pressure automotive systems.
- Industrial Machinery: Heavy-duty machinery, especially in construction and mining, requires seals that withstand pressure and vibration without over-compressing, as it can lead to unexpected equipment downtime.
- Medical and Pharmaceutical Equipment: Equipment in sterile environments or applications requiring precise sealing faces risks of over-compression, especially in high-pressure fluid systems. Proper installation practices are crucial to prevent issues in these critical systems.
Over-compression significantly impacts O-ring reliability, often leading to premature failure and increased maintenance costs. By following installation guidelines, selecting appropriate materials, and adhering to groove and compression specifications, over-compression damage can be effectively avoided. These preventive measures help maintain the longevity and performance of O-rings in a wide range of applications.
If you have any questions, feel free to reach out to the Canyon Components engineering team.
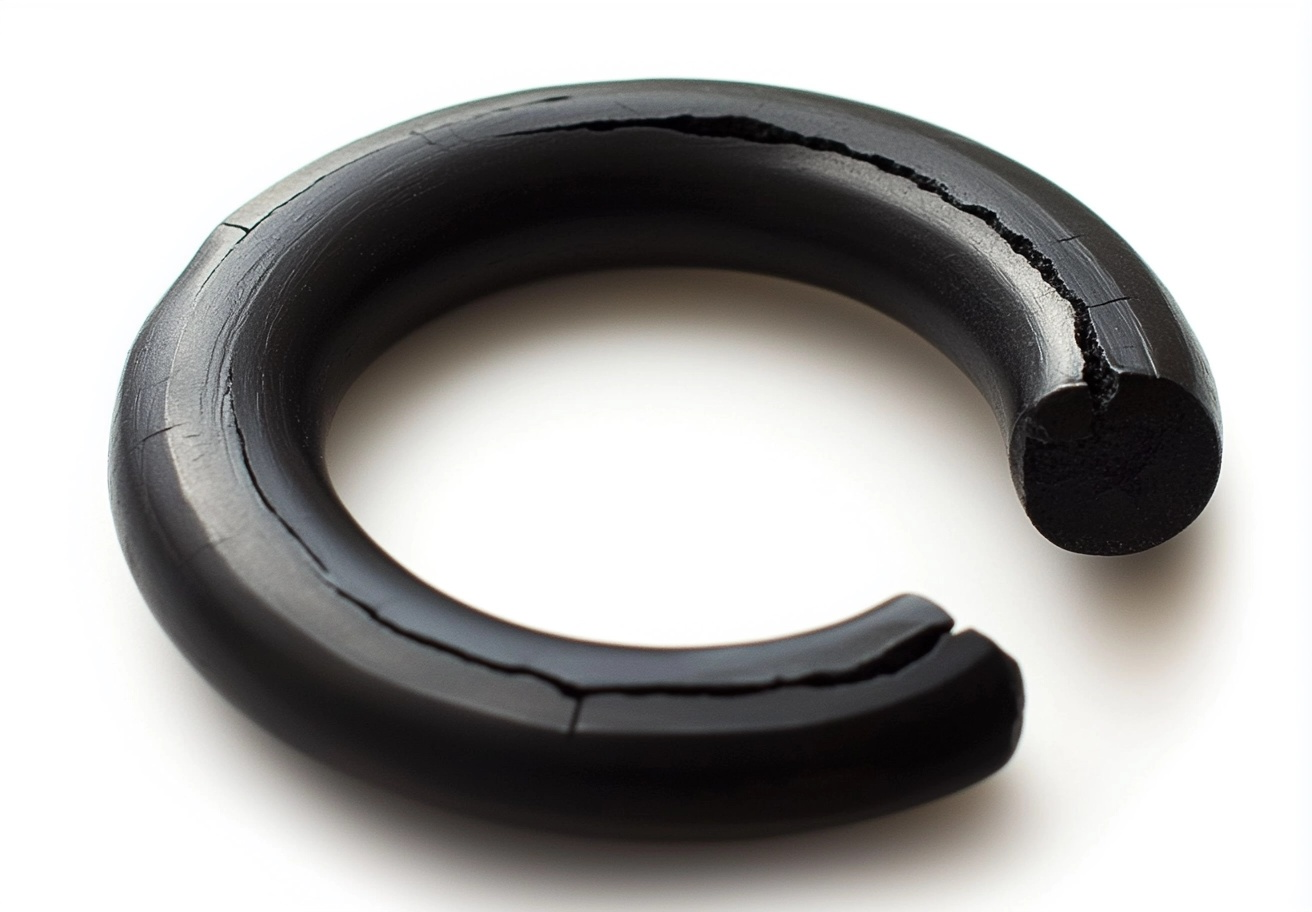
* The failure depicted in this image is intentionally exaggerated to highlight damage details, making it easy to recognize common O-ring failure modes for quick reference.
If you have any questions, feel free to reach out to the Canyon Components engineering team.
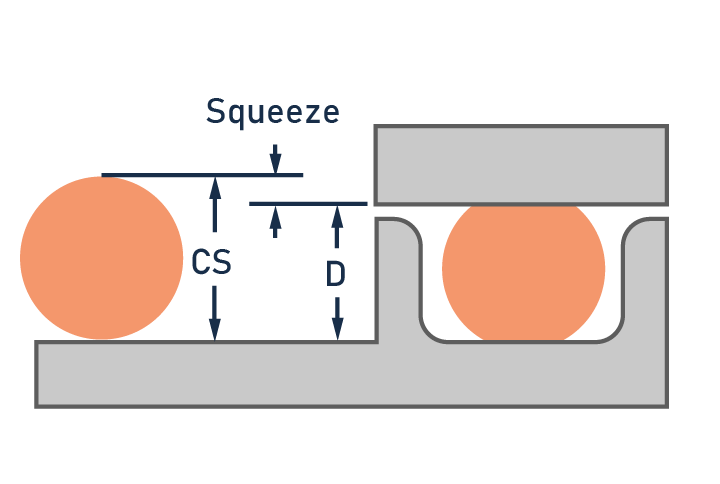
Plasma Damage
Description:
Plasma damage occurs when an O-ring is exposed to plasma, an ionized gas with high energy, resulting in surface erosion, chemical degradation, and structural weakening of the elastomer. Plasma exposure can degrade the O-ring's sealing properties and contaminate the surrounding environment with particulate matter from the damaged seal. Plasma damage is a common concern in industries requiring high-purity or vacuum environments, such as semiconductor manufacturing, electronics, and aerospace.
If you have any questions, feel free to reach out to the Canyon Components engineering team.
Causes:
Plasma damage occurs due to several factors associated with the plasma’s properties and its interaction with the O-ring material:
- Ionized Gas Exposure: Plasma consists of charged particles that bombard the O-ring surface, breaking down molecular bonds and causing erosion.
- Chemical Reactivity: Plasma environments often contain reactive gases like oxygen, fluorine, or chlorine. These gases can chemically attack the elastomer, especially under high energy conditions.
- High Temperature: The energy from plasma exposure generates heat, which can further degrade the O-ring material, accelerating chemical reactions and weakening the elastomer structure.
- UV Radiation: Plasma generates ultraviolet (UV) radiation, which can break down certain elastomers at a molecular level, leading to cracking and hardening.
- Vacuum and High-Purity Environments: Plasma is often used in controlled, low-pressure environments, such as vacuum chambers. The combination of low pressure and plasma exposure can accelerate elastomer degradation.
Signs of Plasma Damage:
- Surface Erosion: Plasma damage often appears as pitting, roughness, or small craters on the O-ring surface, caused by the ion bombardment.
- Cracking and Hardening: UV radiation and chemical attack can lead to surface cracking and hardening, reducing the O-ring’s elasticity and sealing capability.
- Discoloration or Chemical Burns: Chemical interactions between reactive plasma gases and the elastomer can lead to discoloration, indicating chemical changes or burns on the O-ring.
- Generation of Particulate Matter: Plasma-damaged O-rings can shed particles, contaminating sensitive environments like clean rooms or semiconductor fabrication areas.
Prevention:
Preventing plasma damage requires choosing suitable materials, implementing proper shielding, and controlling environmental factors:
- Select Plasma-Resistant Materials: Use materials known for their plasma resistance, such as FFKM (perfluoroelastomers), PTFE, or specific high-purity silicone compounds, as these are more resistant to chemical and physical plasma attack.
- Use Coatings for Added Protection: Plasma-resistant coatings, such as parylene or other fluoropolymer coatings, can be applied to enhance the O-ring's resistance to ionized gases and UV radiation.
- Implement Protective Shielding: In some setups, protective shields or barriers can help reduce direct plasma exposure to the O-ring, prolonging its lifespan.
- Control Temperature and UV Exposure: Minimizing temperature and UV radiation levels in the plasma environment can reduce the severity of plasma damage. Lower-energy plasma can achieve desired process results with less impact on the O-ring.
- Regular Inspection and Replacement: Periodically inspecting O-rings in plasma-prone environments for signs of wear, erosion, or contamination helps ensure timely replacement before damage affects performance.
Recommended Materials for Plasma Resistance:
- FFKM (Perfluoroelastomer): FFKM materials like Canrez®, Kalrez®, and Chemraz® offer high resistance to both plasma and chemical exposure, making them ideal for semiconductor and vacuum applications.
- PTFE (Polytetrafluoroethylene): PTFE, commonly known as Teflon, is highly resistant to ion bombardment and chemical interactions, and performs well in plasma environments.
- High-Purity Silicone: Special silicone grades designed for plasma resistance are used in applications where flexibility and sealing integrity are needed alongside plasma exposure.
- Aflas (TFE/P): Aflas elastomers resist chemical attack in environments with aggressive plasma gases like chlorine or fluorine, offering a good balance of resistance to plasma and high temperatures.
Industries and Applications Prone to Plasma Damage:
- Semiconductor Manufacturing: Plasma etching, wafer processing, and chemical vapor deposition (CVD) processes use plasma in vacuum environments, requiring O-rings that withstand plasma without contaminating sensitive equipment.
- Aerospace and Defense: In applications involving ionized gas propulsion or where seals encounter plasma, such as in spacecraft, high-resistance materials are crucial to prevent seal failure.
- Medical Device Sterilization: Plasma sterilization in medical devices uses ionized gases to sterilize surfaces, making plasma-resistant O-rings necessary to prevent contamination or degradation.
- Optics and Photonics: In high-vacuum optics applications, plasma-resistant O-rings prevent contamination of lenses and mirrors, essential for maintaining clarity and performance.
- High-Purity Processing: Industries requiring ultra-clean processing environments, such as pharmaceuticals and specialty chemical manufacturing, need plasma-resistant O-rings to prevent contamination and degradation in plasma cleaning processes.
Plasma damage poses significant risks to O-rings, especially in high-purity and vacuum environments where contamination is a concern. By selecting appropriate materials, adding protective coatings, and implementing regular inspection, plasma damage can be mitigated, helping ensure reliable, long-lasting sealing performance in challenging plasma-rich environments.
If you have any questions, feel free to reach out to the Canyon Components engineering team.
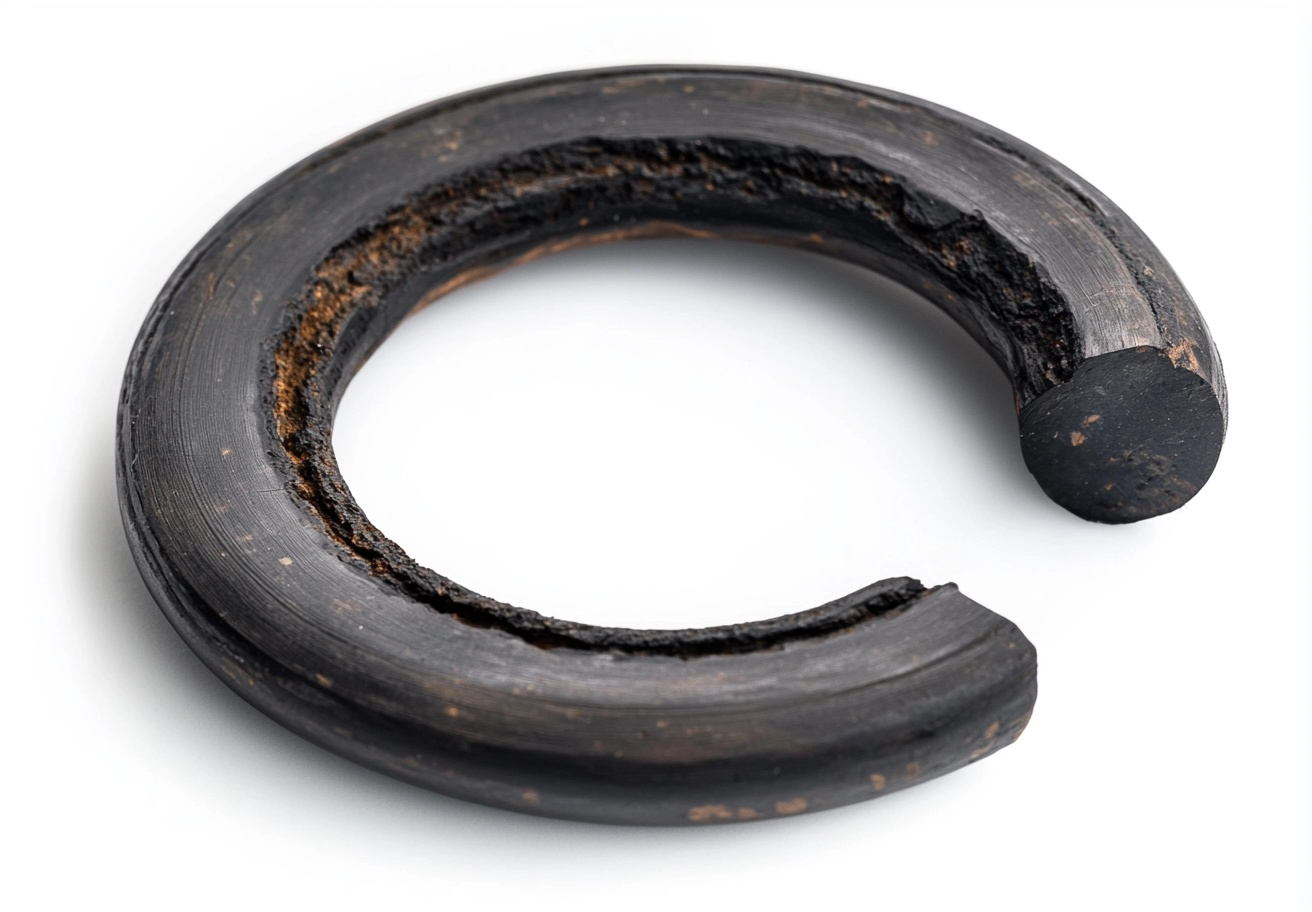
* The failure depicted in this image is intentionally exaggerated to highlight damage details, making it easy to recognize common O-ring failure modes for quick reference.
If you have any questions, feel free to reach out to the Canyon Components engineering team.
Spiral Failure
Description:
Spiral failure occurs when an O-ring twists or spirals within its groove during dynamic operation, leading to uneven wear, surface cuts, or tears. This failure mode is common in applications with reciprocating or oscillating motion, such as hydraulic cylinders or piston systems. Spiral failure prevents the O-ring from creating a consistent seal, often resulting in leaks, decreased efficiency, and frequent maintenance issues.
If you have any questions, feel free to reach out to the Canyon Components engineering team.
Causes:
Spiral failure results from the combination of dynamic movement, poor groove design, and specific material characteristics:
- Dynamic or Reciprocating Motion: In applications with back-and-forth or twisting movements, the O-ring is subjected to repeated friction against surfaces. This can cause the O-ring to twist or spiral within its groove rather than remaining stationary.
- Insufficient Lubrication: In some applications, if materials without internal lubrication or external lubrication are used, the O-ring experiences high friction, increasing the risk of twisting or spiraling as it moves along the sealing surface.
- Improper Groove Design: Grooves that are too wide, too shallow, or lack sufficient support for the O-ring can lead to uneven compression, allowing the O-ring to move more freely and twist.
- Low-Friction or High-Hardness Materials: Certain elastomers, particularly those with high hardness or low friction coefficients, may not grip the groove walls effectively, increasing the chance of spiral motion.
- Pressure Fluctuations: Rapid or uneven pressure changes can destabilize the O-ring’s position, causing it to twist or spiral.
Signs of Spiral Failure:
- Surface Cuts or Tearing: Spiral failure often creates diagonal cuts, abrasions, or tears along the O-ring’s surface, usually at a consistent angle.
- Twisting or Distortion: The O-ring may appear twisted or stretched unevenly when removed from the groove, indicating it rotated or spiraled during use.
- Leakage: Spiral failure prevents the O-ring from making full contact with sealing surfaces, leading to leaks or loss of system pressure.
- Visible Wear Pattern: A distinct wear pattern may appear along the O-ring where it made uneven contact with the groove or mating surface.
Prevention:
Preventing spiral failure involves selecting the right O-ring design, optimizing installation, and ensuring proper lubrication:
- Use Anti-Spiral O-Ring Designs: For applications prone to spiral failure, consider using an X-ring (Quad ring) or square ring instead of a standard round O-ring. These designs resist twisting and are better suited for reciprocating or oscillating motion.
- Optimize Groove Design: Ensure that the groove dimensions provide stable support for the O-ring, reducing the likelihood of spiral motion. Grooves should be deep and narrow enough to keep the O-ring firmly in place without excessive lateral movement.
- Ensure Adequate Lubrication: Use a material that has internal lubrication or by applying a compatible external lubrication to the O-ring and groove to reduce friction and help the O-ring glide smoothly without twisting. Silicone or PTFE-based lubricants are commonly used to lower friction in dynamic applications.
- Control Pressure and Motion Parameters: Avoid rapid, high-frequency reciprocating movements or extreme pressure fluctuations, as these conditions can increase the likelihood of spiral failure. Gradual pressure adjustments can help maintain the O-ring’s position.
Recommended Materials and Designs to Resist Spiral Failure:
- X-Rings (Quad Rings): With a unique four-lobed design, X-rings provide additional stability and resistance to spiral failure, making them ideal for reciprocating applications.
- Square Rings: Square rings have flat surfaces that prevent twisting and create a more secure fit within the groove, helping to avoid spiral failure in dynamic applications.
- HNBR and Nitrile (NBR): These materials offer good grip and resilience, making them suitable for high-pressure or high-friction environments where spiral failure is a risk.
- Polyurethane (PU): With high mechanical strength and abrasion resistance, polyurethane O-rings are durable and less likely to experience spiral failure in applications involving motion.
Industries and Applications Prone to Spiral Failure:
- Hydraulic and Pneumatic Systems: Applications with high-pressure pistons, such as hydraulic cylinders, are particularly prone to spiral failure due to the continuous reciprocating motion.
- Automotive and Machinery: In automotive engines or industrial machinery with reciprocating parts, O-rings may face repeated back-and-forth motion, increasing the risk of spiral failure.
- Aerospace and Aviation: In aircraft systems, where reciprocating motion is common, spiral failure prevention is critical to maintain reliable sealing in dynamic systems.
- Oil and Gas Equipment: Reciprocating pumps, compressors, and valves in the oil and gas industry often use O-rings in dynamic applications, where spiral failure can lead to operational disruptions.
Spiral failure can compromise sealing integrity, leading to leaks and reduced component life. By selecting the right O-ring shape, improving groove design, and ensuring proper lubrication, you can effectively prevent spiral failure and enhance the durability and reliability of O-rings in dynamic applications.
If you have any questions, feel free to reach out to the Canyon Components engineering team.
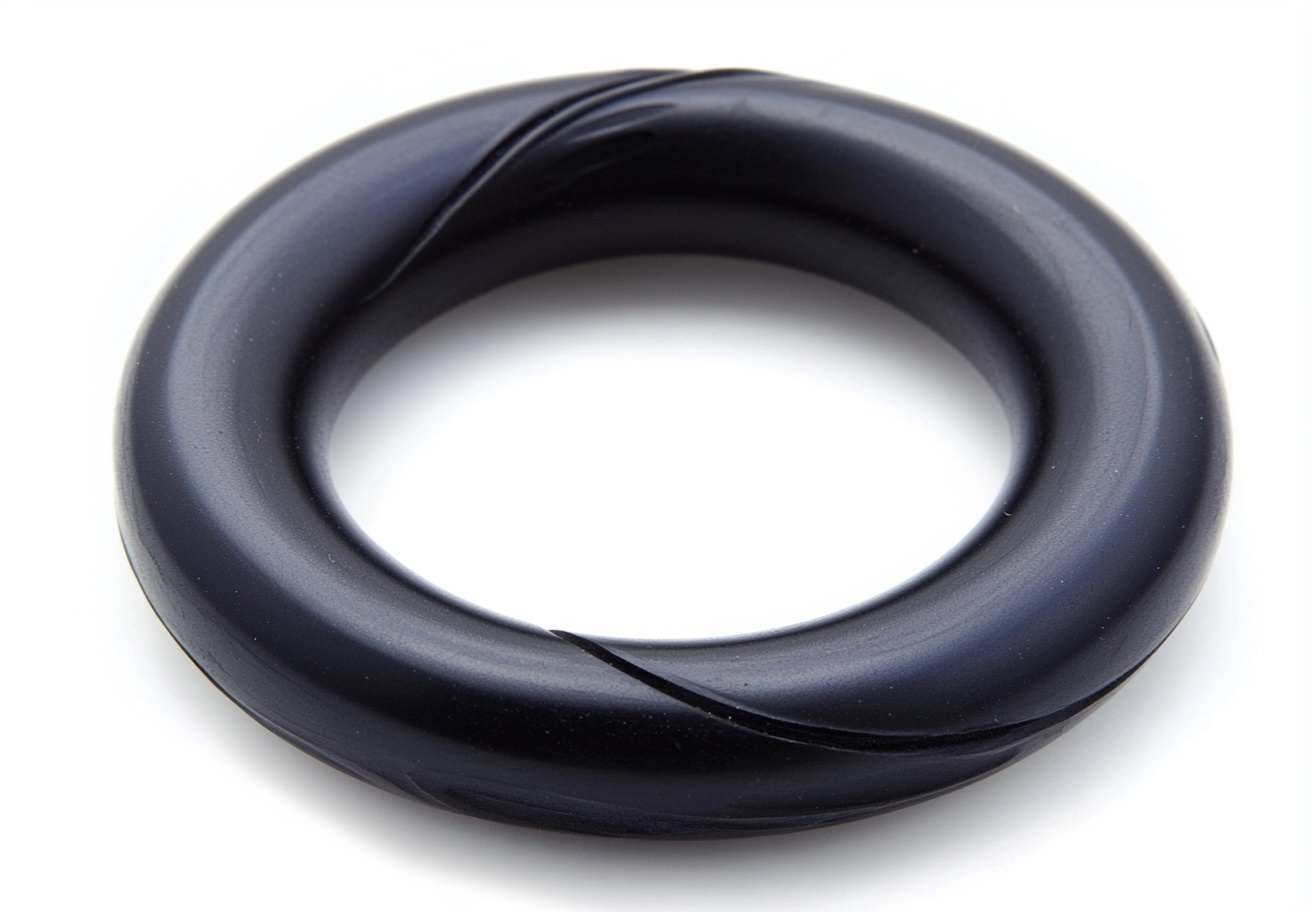
* The failure depicted in this image is intentionally exaggerated to highlight damage details, making it easy to recognize common O-ring failure modes for quick reference.
If you have any questions, feel free to reach out to the Canyon Components engineering team.
Thermal Damage
Description:
Thermal damage occurs when an O-ring is exposed to temperatures beyond its material’s tolerance range, resulting in hardening, cracking, embrittlement, or melting. High temperatures cause the elastomer to degrade chemically, losing its flexibility and resilience, while low temperatures can make it brittle and prone to cracking. Thermal damage compromises an O-ring’s ability to maintain an effective seal, leading to leaks and early failure.
If you have any questions, feel free to reach out to the Canyon Components engineering team.
Causes:
Thermal damage stems from exposure to extreme temperatures, either high or low, and can be influenced by several factors:
- High Operating Temperatures: Prolonged exposure to high temperatures accelerates the elastomer’s aging, breaking down molecular bonds and reducing its elasticity.
- Thermal Cycling: Continuous cycling between high and low temperatures puts additional stress on the O-ring, causing expansion and contraction that can lead to micro-cracks and material fatigue.
- Low-Temperature Brittleness: Elastomers harden at low temperatures, making them prone to cracking under stress or impact, especially in cold storage or outdoor applications.
- High-Friction Environments: Dynamic applications with high friction generate heat, which can elevate the O-ring’s temperature, especially if lubrication is insufficient.
- Incompatible Material Selection: Choosing an elastomer with low thermal resistance for a high-temperature application, or one without flexibility in cold environments, leads to premature thermal failure.
Signs of Thermal Damage:
- Hardening and Loss of Elasticity: High temperatures can cause the O-ring to harden, losing its natural flexibility and making it less effective at creating a seal.
- Cracking and Surface Degradation: Thermal damage often results in visible cracking or surface erosion, especially in low temperatures or high-temperature fluctuations.
- Glossy or Shiny Appearance: A glossy or shiny surface can indicate that the elastomer has experienced chemical changes due to heat, often seen as a result of high-temperature exposure.
- Discoloration: Exposure to excessive heat may change the color of the O-ring, which can signal thermal degradation or burning.
- Melting, Burning, or Softening: In extreme heat, certain elastomers may begin to soften, distort, burn, or melt, causing the O-ring to deform and lose its sealing capabilities.
Prevention:
Preventing thermal damage involves selecting appropriate materials, monitoring temperature, and controlling environmental conditions:
- Choose Temperature-Resistant Materials: Select O-rings made from materials known for their thermal stability, such as Canrez® FFKM Perfluoroelastomer and FKM (Viton) for high temperatures or silicone for both high and low-temperature applications.
- Use Thermal Insulators or Shields: In applications with localized high temperatures, consider using thermal insulation or shields to protect the O-ring from direct heat exposure.
- Control Friction and Ensure Lubrication: Proper lubrication reduces friction in dynamic applications, minimizing heat generation and protecting the O-ring from thermal damage. Use materials with internal lubrication or apply external lubrication.
- Avoid Excessive Thermal Cycling: Where possible, avoid rapid and extreme temperature changes, as these stress the elastomer and contribute to thermal fatigue.
- Inspect and Replace Periodically: Regularly inspect O-rings in high-temperature applications, as they may require more frequent replacement to maintain performance and prevent thermal failure.
Recommended Materials for Thermal Resistance:
- FFKM (Perfluoroelastomer): FFKM materials like Canrez®, Kalrez®, and Chemraz® have the highest thermal and chemical resistance, with certain blends tolerating extreme temperatures up to 660°F (350°C) or higher, making them ideal for demanding applications in oil and gas or chemical processing.
- FKM (Viton): Viton is known for its excellent high-temperature resistance, typically withstanding temperatures up to 437°F (225°C), making it suitable for harsh industrial environments. Certain Viton low temperature blends are also capable of handling temperatures as low as -55°F (-50°C).
- Silicone: Silicone offers flexibility in both high and low temperatures, with blends ranging from -80°F to 400°F (-62°C to 205°C), and is used in applications requiring thermal resilience. There are also high temp Silicone and low temp Silicone extreme blends available that expand the range to -112°F to 600°F (-80°C to 315°C).
- EPDM (Ethylene Propylene Diene Monomer): EPDM provides good resistance to moderate temperatures and is commonly used in applications with hot water or steam up to 300°F (150°C). There are also special ultra steam resistant EPDM blends that can handle temperatures of up to 600°F (315°C).
- Nitrile (NBR): Nitrile can handle moderate temperatures and is a cost-effective choice for applications up to 252°F (122°C).
Industries and Applications Prone to Thermal Damage:
- Automotive and Aerospace: Engines, exhaust systems, and aerospace components experience high temperatures and may undergo frequent temperature fluctuations, requiring heat-resistant seals to maintain reliability.
- Oil and Gas: Oil drilling, extraction, and processing equipment operate in high-temperature environments where thermal-resistant seals are essential for safe and continuous operation.
- Food and Beverage Processing: Equipment in the food industry often requires sterilization at high temperatures, demanding elastomers that can withstand steam and heat exposure.
- Semiconductor Manufacturing: High-purity seals in semiconductor equipment need to withstand both high temperatures and vacuums, requiring materials like FFKM or PTFE for thermal and chemical resilience.
- HVAC and Refrigeration: Low-temperature environments in HVAC systems, freezers, and refrigeration units necessitate O-rings that remain flexible and durable in subzero conditions.
Thermal damage can significantly impact the performance and longevity of O-rings, leading to leaks, wear, and increased maintenance costs. By choosing the appropriate materials, controlling friction, and implementing preventive measures for thermal stress, industries can minimize thermal damage and maintain reliable sealing performance in high and low-temperature applications.
If you have any questions, feel free to reach out to the Canyon Components engineering team.
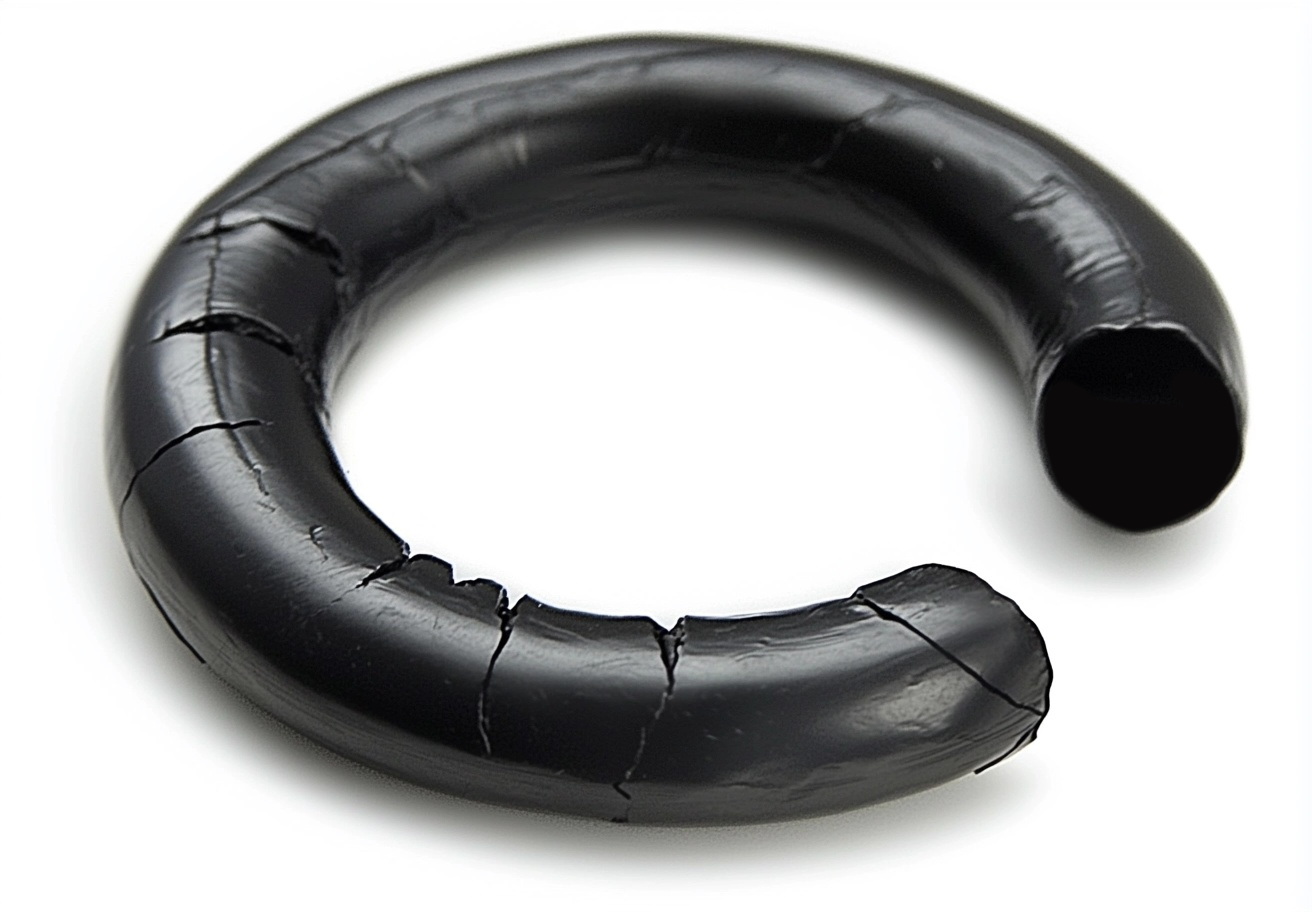
* The failure depicted in this image is intentionally exaggerated to highlight damage details, making it easy to recognize common O-ring failure modes for quick reference.
If you have any questions, feel free to reach out to the Canyon Components engineering team.
UV Damage
Description:
UV damage occurs when an O-ring is exposed to ultraviolet (UV) radiation, primarily from sunlight or artificial UV sources. UV rays break down the chemical bonds within the elastomer, leading to surface cracking, hardening, and eventual degradation of the O-ring’s structural integrity. This type of damage, also known as “ozone cracking” or “sun-checking,” reduces the O-ring’s flexibility and ability to create an effective seal, making it susceptible to leaks and early failure.
If you have any questions, feel free to reach out to the Canyon Components engineering team.
Causes:
UV damage results from prolonged exposure to UV light, which affects certain elastomers more severely than others:
- Direct Sunlight Exposure: Outdoor applications where O-rings are exposed to direct sunlight are particularly prone to UV damage, as continuous sunlight provides a consistent source of UV radiation.
- Artificial UV Light Sources: Some industrial environments use artificial UV light for curing, sterilization, or lighting, exposing nearby O-rings to UV radiation.
- Ozone and Environmental Factors: UV exposure creates ozone in the atmosphere, which further accelerates cracking and degradation of the elastomer.
- Temperature Variations: UV exposure can raise the temperature of the O-ring, amplifying the effects of heat aging and causing additional material weakening.
Signs of UV Damage:
- Surface Cracking or Crazing: UV damage often appears as fine cracks or “crazing” on the O-ring surface, especially along the areas exposed to light.
- Loss of Elasticity: The O-ring may lose flexibility, becoming brittle and less capable of creating a reliable seal, which makes it prone to cracking under pressure.
- Chalking or Discoloration: UV exposure can cause a chalky appearance, fading, or discoloration on the O-ring surface, often indicating molecular breakdown in the elastomer.
- Hardening and Surface Degradation: UV radiation can harden the O-ring surface, making it rigid and more likely to fracture or break when subjected to dynamic forces.
Prevention:
Minimizing UV damage involves selecting UV-resistant materials, applying protective coatings, and managing storage conditions:
- Choose UV-Resistant Materials: Use elastomers with natural UV resistance, such as EPDM, Viton (FKM), or silicone, especially in outdoor or high-exposure applications.
- Apply Protective Coatings: UV-blocking coatings or paints can be applied to O-rings exposed to sunlight, providing an additional layer of protection against radiation.
- Limit Sunlight Exposure: When feasible, install components with UV-exposed O-rings in shaded or sheltered areas to reduce direct sunlight exposure.
- Use UV-Resistant Storage Practices: For inventory storage, keep O-rings in opaque, UV-resistant packaging or containers to prevent UV exposure in storage rooms or warehouses.
- Regular Inspection and Replacement: For applications where UV exposure is unavoidable, inspect O-rings regularly for signs of cracking, hardening, or discoloration, and replace them as needed to maintain optimal sealing performance.
Recommended UV-Resistant Materials:
- EPDM (Ethylene Propylene Diene Monomer): Known for its excellent resistance to UV, ozone, and weathering, EPDM is commonly used in outdoor applications, such as automotive and HVAC systems.
- Viton (FKM): With strong UV and chemical resistance, Viton performs well in high-temperature and high-UV applications, making it suitable for aerospace and industrial settings.
- Silicone: Silicone elastomers resist UV radiation effectively and remain flexible at both high and low temperatures, making them ideal for outdoor and high-UV applications.
- Neoprene (CR): Neoprene provides moderate UV resistance and is used in weather-exposed applications, such as automotive and marine environments.
- Fluorosilicone: Fluorosilicone combines silicone’s UV resistance with added chemical resilience, making it ideal for aerospace and high-exposure environments.
Industries and Applications Prone to UV Damage:
- Automotive and Transportation: Vehicles and equipment with outdoor exposure, such as seals around windows, doors, or headlights, often use UV-resistant elastomers to withstand continuous sunlight.
- Construction and Outdoor Equipment: Seals in roofing, HVAC units, solar panels, and outdoor machinery are frequently exposed to sunlight, necessitating materials that resist UV degradation.
- Aerospace and Aviation: Aircraft and spacecraft have seals exposed to high levels of UV radiation at high altitudes, requiring O-rings with robust UV and ozone resistance.
- Agriculture and Irrigation: Irrigation systems, piping, and valves exposed to sunlight need UV-resistant O-rings to maintain long-lasting seals despite outdoor conditions.
- Marine and Offshore Applications: O-rings in marine environments face sunlight, saltwater, and ozone exposure, requiring UV-resistant materials to withstand these harsh conditions.
Understanding the Effect of UV Damage on O-Ring Performance:
UV damage weakens the molecular structure of elastomers, particularly on the surface, where cracks can develop and propagate over time. These cracks compromise the O-ring’s ability to maintain a seal, especially in dynamic applications where flexibility is key. In static applications, surface hardening and degradation can prevent the O-ring from properly filling its groove, leading to leaks over time.
By selecting UV-resistant materials, employing preventive measures like coatings, and regularly inspecting UV-exposed O-rings, industries can extend the life of their seals and maintain effective sealing in high-UV environments. These best practices help avoid premature failures, reduce maintenance costs, and improve overall reliability.
If you have any questions, feel free to reach out to the Canyon Components engineering team.
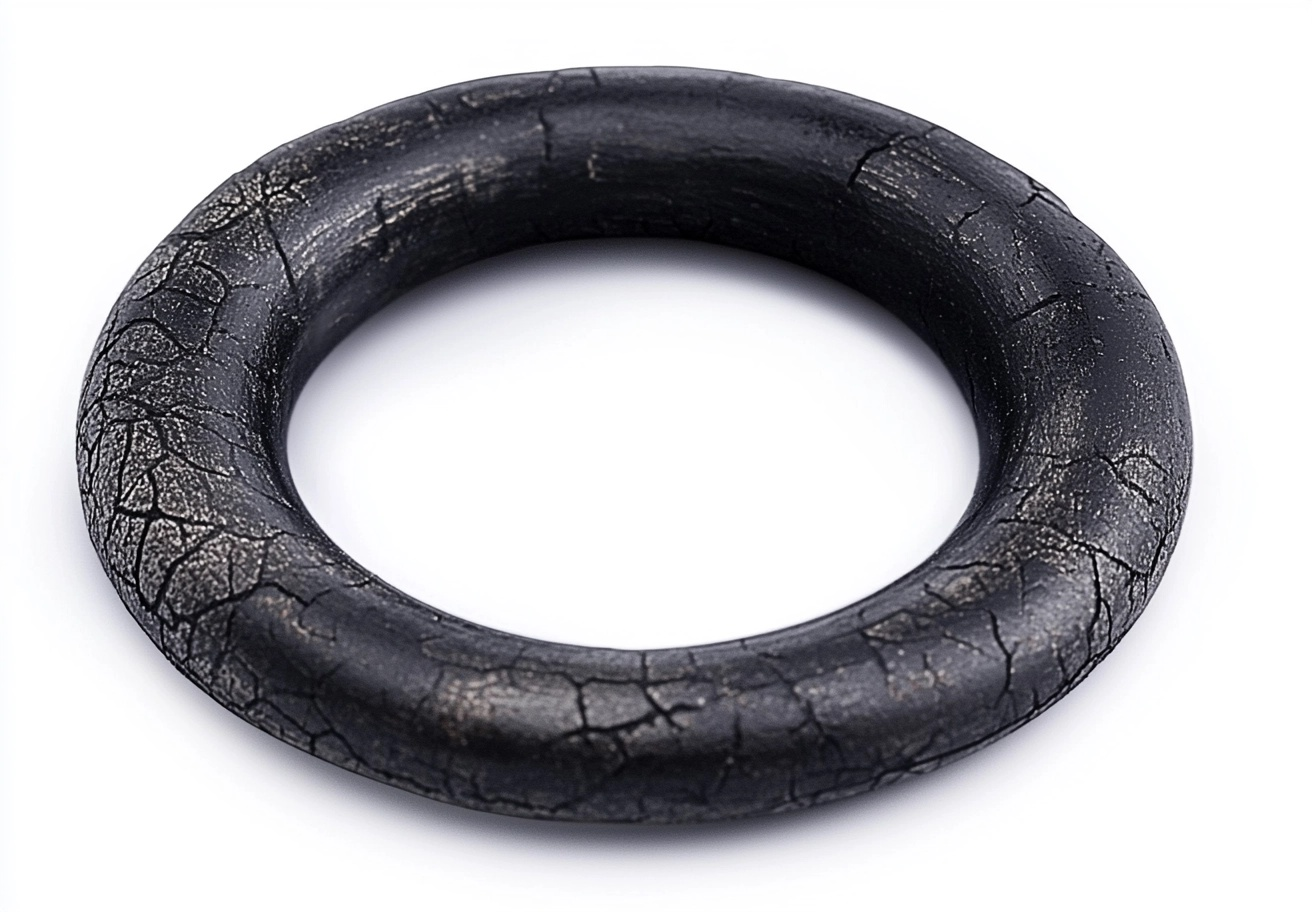
* The failure depicted in this image is intentionally exaggerated to highlight damage details, making it easy to recognize common O-ring failure modes for quick reference.
If you have any questions, feel free to reach out to the Canyon Components engineering team.
Back to Reference Hub
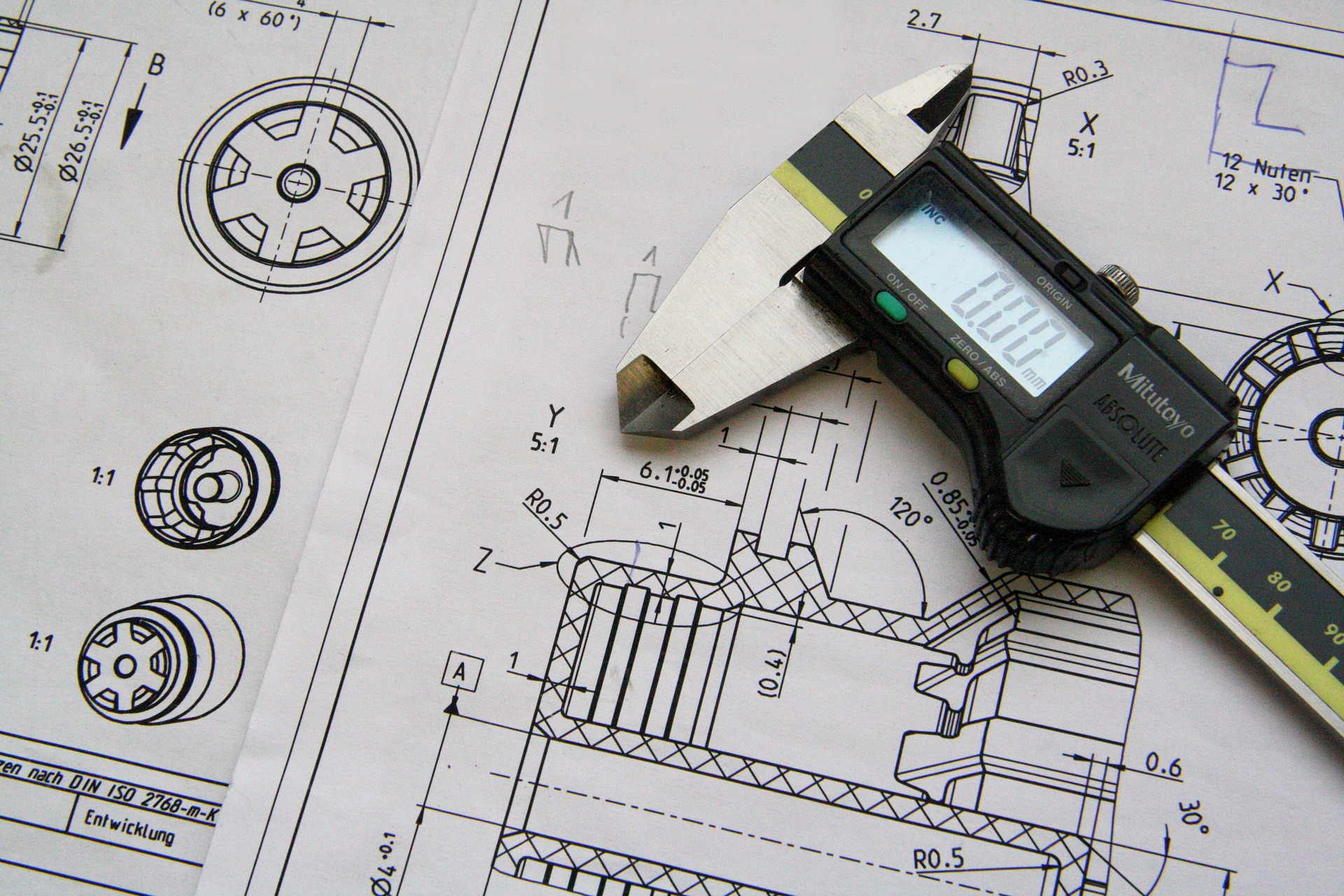
Get A Quote Now!
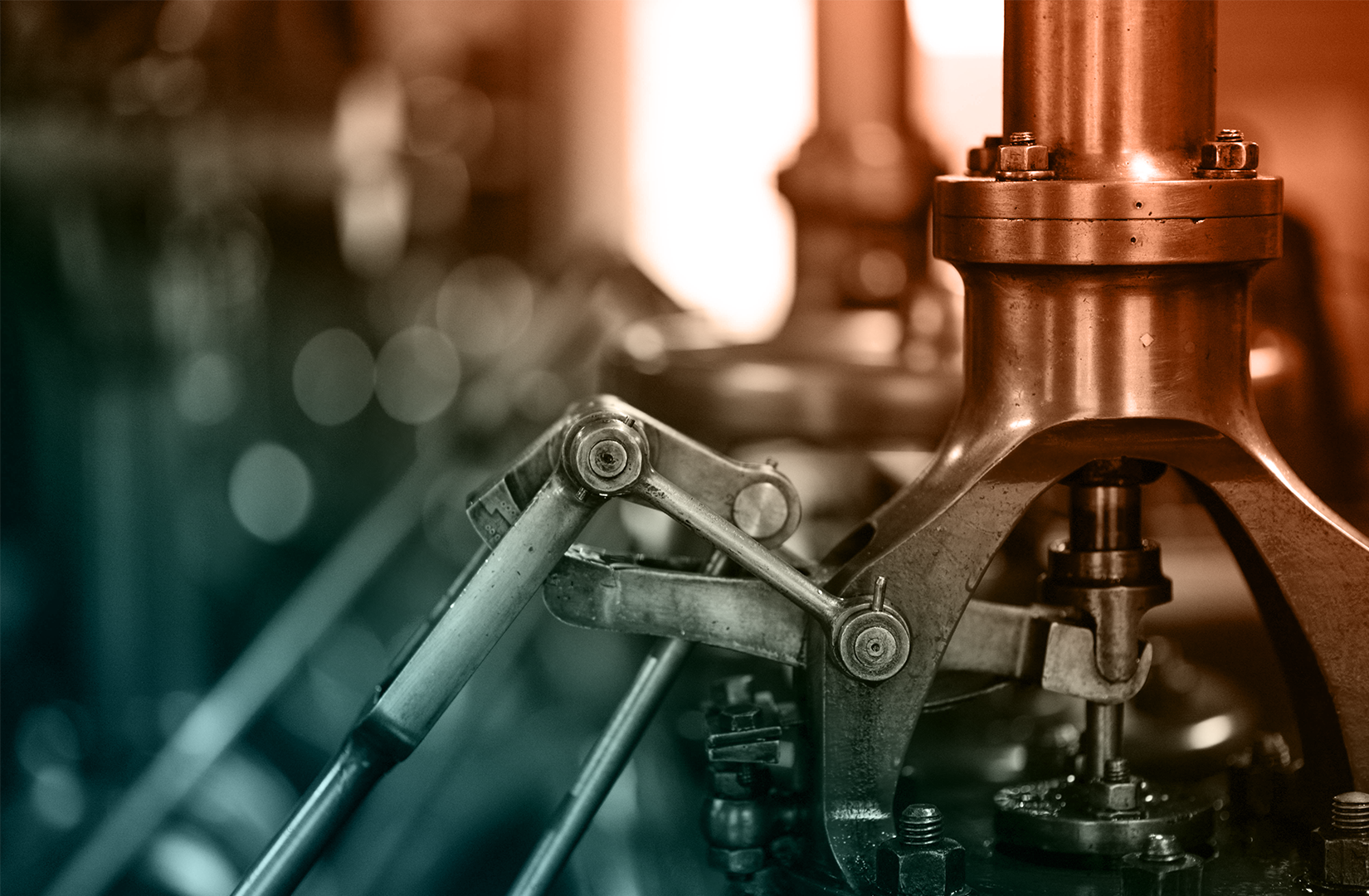
Groove Design References
Learn More
Coatings, Packaging, & Other Services
Learn More
Custom Parts & Custom O-rings
Learn More